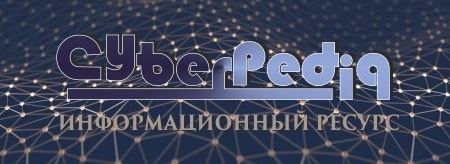
Поперечные профили набережных и береговой полосы: На городских территориях берегоукрепление проектируют с учетом технических и экономических требований, но особое значение придают эстетическим...
История развития хранилищ для нефти: Первые склады нефти появились в XVII веке. Они представляли собой землянные ямы-амбара глубиной 4…5 м...
Топ:
Характеристика АТП и сварочно-жестяницкого участка: Транспорт в настоящее время является одной из важнейших отраслей народного...
Установка замедленного коксования: Чем выше температура и ниже давление, тем место разрыва углеродной цепи всё больше смещается к её концу и значительно возрастает...
Интересное:
Как мы говорим и как мы слушаем: общение можно сравнить с огромным зонтиком, под которым скрыто все...
Национальное богатство страны и его составляющие: для оценки элементов национального богатства используются...
Берегоукрепление оползневых склонов: На прибрежных склонах основной причиной развития оползневых процессов является подмыв водами рек естественных склонов...
Дисциплины:
![]() |
![]() |
5.00
из
|
Заказать работу |
|
|
ОТЧЕТ ПО МОДУЛЮ 3
по дисциплине «Эксплуатация, ремонт и монтаж машин и оборудования
для добычи нефти и газа»
Тема: Технологические основы и технологические процессы ремонта, эксплуатации и монтажа оборудования
Творческий коллектив гр. НГ 10-04 в составе:
Руководитель раздел 3,4 общая редакция Д.Е. Латышев
Исполнитель раздел 1,2,5И.С. Зингер
Преподаватель доцент, к.т.н. В.Н. Конов
Красноярск 2014
Содержание
Введение.......................................................................................................................3
1 Технологические основы ремонта оборудования….............................................5
1.1 Система технического обслуживания и ремонта
оборудования...............................................................................................................5
1.2 Виды технического обслуживания и ремонта оборудования....................7
1.3 Структура производственного процесса ремонта
оборудования.............................................................................................................10
2 Методы восстановления поверхностей и неразъемных соединений ремонтируемых деталей............................................................................................14
2.1 Восстановление поверхностей наплавкой..................................................15
2.2 Восстановление поверхностей металлизацией..........................................17
2.3 Наплавка шлицевого вала привода…………………….............................20
2.4 Технология механической обработки………………………….................22
2.4.1 Сварка………………………………………………………………22
2.4.2 Пайка………………………………………………………………..23
2.4.3 Обработка металлов давлением……………………………….…..23
2.4.4 Обработка металлов резанием…………………………………….23
|
3 Технологические маршруты и процессы восстановления изделий...................25
3.1 Общие сведения............................................................................................25
3.2Проектирование технологического маршрута и механической
обработкиштока бурового насоса...........................................................................28
3.3Закалка ТВЧ и ВИЗ.......................................................................................30
4 Основы монтажа оборудования.............................................................................35
4.1 Общие сведения............................................................................................35
4.2 Монтаж СВП TescoECI 900 HP, 500 тонн.................................................40
4.3 Методы испытания технических объектов………………………………47
4.4 Контроль технического состояния..............................................................48
4.5 Экспертное заключение промышленной экспертизы о результатах
приемки оборудования..............................................................................................50
5 Показатели надежности изделий НГП.................................................................51
Заключение………………………………………………………………………….53
Список использованных источников.......................................................................54
Введение
Техническое обслуживание и ремонт (ТОиР) — комплекс операций по поддержанию работоспособности или исправности производственного оборудования при использовании по назначению, ожидании, хранении и транспортировке.
Монтаж – это последовательный процесс сборки, установки оборудования и механизмов, включающий общие подготовительные, монтажные, механические и технические действия квалифицированных специалистов, для последующего запуска оборудования.
Основная цель, достигаемая комплексом технического обслуживания и ремонта — устранение отказов оборудования.
Наибольшее число отказов обусловлено износом рабочих органов и узлов трения, а также другими видами разрушений, связанных с взаимодействием сопрягаемых деталей в узлах и механизмах машины.
На ремонтных предприятиях применяют различные способы восстановления изношенных поверхностей деталей: механическая и слесарная обработка, сварка, наплавка, металлизация, хромирование, никелирование, осталивание, склеивание, упрочнение поверхности деталей и восстановление их формы под давлением.
|
Выбор способа восстановления поверхностей деталей определяется характером дефекта, материалом детали, особенностями ее конструкции и технологии изготовления, условиями работы.
Модуль 3 состоит из 5-ти глав:
v Технологические основы ремонта оборудования;
v Методы восстановления поверхностей и неразъемных соединений ремонтируемых деталей;
v Технологические маршруты и процессы восстановления изделий
обработки ступенчатого вала;
v Основы монтажа оборудования;
v Показатели надежности изделий НГП.
В главе 1 рассмотрены:
o Система технического обслуживания и ремонта оборудования;
o Виды технического обслуживания и ремонта оборудования;
o Структура производственного процесса ремонта оборудования.
В главе 2 рассмотрены:
o Восстановление поверхностей наплавкой;
o Восстановление поверхностей металлизацией;
o Наплавка шлицевого вала привода установки МК20Т;
o Технология механической обработки.
В главе 3 рассмотрены:
o Общие сведения;
o Проектирование технологического маршрута и механической обработки штока бурового насоса;
o Закалка ТВЧ и ВИЗ.
В главе 4 рассмотрены:
o Общие сведения;
o Монтаж колтюбинговой установки МК20Т;
o Методы испытания технических объектов;
o Контроль технического состояния;
o Экспертное заключение промышленной экспертизы о результатах.
В главе 5рассмотрены:
o Показатели надежности изделий НГП.
Технологические основы ремонта оборудования НГП
Структура производственного процесса ремонта
Оборудования
Производственный процесс ремонта представляет комплекс технологических и вспомогательных операций по восстановлению работоспособности оборудования, выполняемых в определенной последовательности, и включает приемку оборудования в ремонт, моечно-очистные операции, разборку оборудования на агрегаты, сборочные единицы и детали, контроль, сортировку и ремонт деталей, их комплектацию, сборку сборочных единиц, агрегатов и оборудования в целом, обкатку и испытание оборудования после сборки, окраску и сдачу оборудования из ремонта.
|
Степень расчлененности производственного процесса во многом зависит от конструкции машины и программы ремонтно-обслуживающего предприятия. Правильно расчлененный технологический процесс ремонта той или иной машины или агрегата создает наиболее благоприятные условия для его рациональной организации, снижения себестоимости и оснащения рабочих мест высокопроизводительными технологическим оборудованием и оснасткой.
На ремонтных предприятиях нефтегазовой отрасли в зависимости от количества однотипного оборудования и условий ремонта применяют два основных метода ремонта: индивидуальный и агрегатный. В зависимости от применяемого метода изменяются содержание и последовательность операций технологического процесса ремонта.
При индивидуальном методе ремонта детали, сборочные единицы и агрегаты оборудования маркируют и после ремонта устанавливают на том же оборудовании. Следовательно, сборку оборудования начинают только тогда, когда отремонтированы все детали, что значительно удлиняет общее время ремонта.
Рисунок 1.5 – Схема технологического процесса ремонта оборудования индивидуальным методом
Индивидуальный метод ремонта применяется в тех случаях, когда на ремонтное предприятие поступает мало однотипного оборудования. При индивидуальном методе ремонта машину или механизм ремонтирует одна комплексная бригада, состоящая из рабочих высокой квалификации.
Индивидуальный метод ремонта имеет следующие недостатки:
· отсутствует специализация ремонтных работ и ограничена возможность внедрения механизации, что значительно снижает производительность труда;
· оборудование длительно находится в ремонте, так как готовые детали простаивают, пока все детали не будут отремонтированы;
· требуется высокая квалификация рабочих.
Особенность индивидуального метода ремонта заключается втом, что сборочные единицы и детали машины в процессе ремонта не обезличиваются и заказчик получает ту же машину, которую сдал в ремонт.
При агрегатном ремонте все детали, сборочные единицы и агрегаты машины обезличиваются, за исключением базовой детали. Наличие склада оборотных агрегатов, постоянно пополняемого отремонтированными обезличенными агрегатами поступающего в ремонт оборудования, позволяет начинать сборку машин немедленно после ремонта базовой детали.
|
Агрегатный метод ремонта обычно применяют в ЦБ ПО и на специализированных ремонтных заводах, т.е. когда на ремонт поступает значительное количество однотипного оборудования.
Организация ремонта оборудования для бурения скважин и нефтегазодобычи агрегатным методом должна быть такой, чтобы заказчик получал отремонтированную машину в кратчайший срок.
Основными преимуществами агрегатного метода ремонта являются:
· специализация рабочих по отдельным видам работ, что повышает производительность труда;
· более совершенная технология ремонта с использованием специального технологического оборудования и оснастки;
· широкое внедрение механизации работ;
· улучшение качества и снижение стоимости ремонтных работ;
· сокращение продолжительности ремонта.
Рисунок 1.5 – Схема технологического процесса ремонта оборудования агрегатным методом
Недостаток агрегатного метода ремонта - необходимость в оборотном фонде агрегатов.
Разновидностью агрегатного метода ремонта является так называемый узловой метод, который часто применяется при ремонте оборудования непосредственно на месте эксплуатации. В этом случае изношенная сборочная единица заменяется отремонтированной на базе производственного обслуживания. По такому методу обычно ремонтируют тяжелое оборудование, транспортировка которого затруднена.
Сварка
Сваркой называют технологический процесс получения неразъемных соединений из металлов (или пластмасс), осуществляемый установлением межатомных (у пластмасс — межмолекулярных) связей между свариваемыми частями изделия при их местном или общем нагреве, или пластическом деформировании, или при совместном действии этих двух факторов. Между свариваемыми частями изделия образуется сварной шов.
Сварка является одной из распространенных технологических операций, широко применяемой в машиностроении, на транспорте и в строительстве. Объясняется это значительной экономией металлов по сравнению с болтовыми и заклепочными соединениями, высокой прочностью и низкой стоимостью сварных конструкций.
В зависимости от состояния металла в сварочной зоне все виды сварки можно разделить на две группы: по способу соединения свариваемых частей изделия и по виду используемой энергии. В первом случае различают сварку плавлением и сварку давлением. При сварке плавлением сварной шов образуется из общей сварочной ванны расплавленных металлов соединяемых частей изделия. При сварке давлением, для повышения пластичности металла в зоне сварки, соединяемые части изделия нагревают и сдавливают.
|
По виду используемой энергии сварку подразделяют на термическую (сварка дуговая, плазменная, газовая и др.), термомеханическую (сварка контактная, диффузионная и др.) и механическую (сварка взрывом, трением, ультразвуковая и др.).
При сварке плавлением образуется литой сварной шов с характерным дендритным строением. При сварке давлением образуется шов, представляющий собой зону сросшихся кристаллитов металла соединяемых частей изделия. Зону, непосредственно примыкающую к сварному шву, называют зоной термического влияния.
Пайка
Пайка — это процесс получения неразъемных соединений в результате расплавления припоя, смачивания им металла, растекания припоя по поверхности металла и заполнения зазора между соединяемыми заготовками (деталями) и, наконец, затвердевания припоя.
В отличие от сварки при пайке не требуется расплавления основного металла, что позволяет производить распай деталей. Наиболее широко пайку применяют в электро- и радиотехнике и приборостроении. В этих отраслях промышленности пайку производят для создания механически прочного, иногда герметичного, шва или для получения постоянного (нескользящего или разрывного) электрического контакта с небольшим переходным сопротивлением.
Обработка металлов резанием
Обработка металлов резанием заключается в срезании с поверхности заготовки слоя металла, называемого припуском, с целью получения изделия требуемых геометрической формы, размеров и шероховатости поверхностей. Срезание припуска производят с помощью режущего инструмента.
В большинстве случаев изделия, полученные литьем, прокаткой, ковкой, штамповкой, сваркой и другими методами, подвергают обработке резанием. Удаляемый при этом припуск превращается в стружку, которая является характерным признаком всех процессов обработки металлов резанием (ОМР). ОМР бывает механической, когда припуск срезают на металлорежущих стенках, и слесарной, когда припуск удаляют вручную с помощью соответствующего слесарного инструмента. ОМР применяют и как самостоятельный способ изготовления деталей.
Основными видами механической ОМР являются: точение; строгание; долбление; сверление (зенкерование, развертывание и зенкование); фрезерование и шлифование, — производимые на металлорежущих стенках соответствующей группы. Станки различают токарной группы, строгальной и долбежной, сверлильной и расточной, фрезерной, шлифовальной и др. При ОМР используют различный режущий инструмент: резцы, сверла, зенкера, развертки, фрезы, которые имеют специально заточенную режущую часть, а также применяют шлифовальные абразивные круги, зерна которых обладают острыми гранями и углами. Режущий инструмент изготавливают из У7, У10 У13, ХВГ, 9ХС, Р9, Р18 материала повышенной твердости 60-66 HRC, прочности т 2600 4000 Мпа, термо- и износостойкостиt=600 C, различных форм и размеров.
3 Технологические маршруты и процессы восстановления изделий
Общие сведения
Технологический процесс — это часть производственного процесса, содержащая целенаправленные действия по изменению и (или) определению состояния предмета труда.
Технологический маршрут – совокупность взаимосвязанных операций по реализации технологического процесса на оборудовании цеха во время обработки деталей и сборочных единиц, входящих в изделие.
Составление технологического маршрута - это решение сложной многовариантной задачи, в результате которого принимают общий план обработки изделия, намечают содержание технологических операций, определяют состав технологического оснащения.
При этом надо учитывать, что различные детали машин образуются сочетанием разнообразных поверхностей.
По ГОСТ 21495-76 все поверхности деталей изделий машиностроения можно разделить на четыре вида:
1) Исполнительные поверхности - поверхности, с помощью которых деталь выполняет свое служебное назначение;
2) Основные поверхности - поверхности, с помощью которых определяют положение данной детали в изделии;
3) Вспомогательные поверхности - поверхности, с помощью которых определяют положение присоединяемых деталей относительно данной;
4) Свободные поверхности - поверхности, не соприкасающиеся с поверхностями других деталей.
Обеспечение заданной точности и качества поверхностей основной группы с наименьшими затратами труда и издержками производства является главнейшей задачей технологического процесса.
Заданные точность и качество основной группы поверхностиразмеры, масса и форма детали дают возможность определить, необходимые методы окончательной обработки этих поверхностей, что предопределяет выбор средств технологического оснащения (СТО). Каждому методу окончательной обработки предшествуют промежуточные методы и соответствующие СТО. При этом исходят из того, что каждый последующий метод должен быть точнее предыдущего.
Решение задачи по выбору методов обработки всех поверхностей детали сводится к определению содержание технологического процесса, выявлению необходимости осуществления трех стадий обработки: черновой, чистовой и отделочной.
На первой стадии выполняют операции черновой обработки всех поверхностей. На этой стадии удаляется основная масса материала. Обработка сопровождается интенсивным нагревом заготовки и инструмента, большими силами резания, которые требуют соответствующих сил закрепления заготовки и приводят к значительным деформациям технологической системы - источниками образования погрешностей обработки. После черновой обработки возникают деформации заготовки в результате перераспределения остаточных напряжений в ее материале, которое наиболее интенсивно происходит при снятии с заготовки наружных слоев материала.
На второй стадии осуществляются операции чистовой обработки, в результате которых завершается обработка одних поверхностей или происходит подготовка других поверхностей к последующей, более точной обработке.
Третья стадия - отделочная обработка. На этой стадии обрабатывают поверхности с точностью по 6…7-му квалитету.
B маршрутной технологии механической обработки предусматривается технический контроль соответствия параметров требованиям, заданным чертежом и техническими условиями.
Выбор способа восстановления поверхностей деталей определяется характером дефекта, материалом детали, особенностями ее конструкции и технологии изготовления, условиями работы. На выбор способа восстановления существенное влияние оказывают технико-экономические показатели, которые определяются производительностью процесса ремонта детали, стоимостью применяемых материалов и оборудования, серийностью ремонтного производства, степенью повышения долговечности детали в результате ремонта, а также санитарно-гигиеническими условиями труда.
Анализ технологических возможностей различных способов восстановления поверхностей деталей машин показывает, что значительная часть поврежденных поверхностей может быть не только восстановлена, но и упрочнена с повышением ресурса по сравнению с ресурсом новых деталей.
Закалка ТВЧ и ВИЗ
Метод закалки ТВЧ разработан советским ученым Вологдиным В.П.
Основан на том, что если в переменное магнитное поле, создаваемое проводником-индуктором, поместить металлическую деталь, то в ней будут индуцироваться вихревые токи, вызывающие нагрев металла. Чем больше частота тока, тем тоньше получается закаленный слой.
Обычно используются машинные генераторы с частотой 50…15000 Гц и ламповые генераторы с частотой больше 106 Гц. Глубина закаленного слоя – до 2 мм.
Индукторы изготавливаются из медных трубок, внутри которых циркулирует вода, благодаря чему они не нагреваются. Форма индуктора соответствует внешней форме изделия, при этом необходимо постоянство зазора между индуктором и поверхностью изделия.
1 – закаливаемая деталь; 2 – индуктор; 3 – спрейер.
Рисунок 3. - Схема технологического процесса закалки ТВЧ
После нагрева в течение 3…5 с индуктора 2 деталь 1 быстро перемещается в специальное охлаждающее устройство – спрейер 3, через отверстия которого на нагретую поверхность разбрызгивается закалочная жидкость.
Высокая скорость нагрева смещает фазовые превращения в область более высоких температур. Температура закалки при нагреве токами высокой частоты должна быть выше, чем при обычном нагреве.
При правильных режимах нагрева после охлаждения получается структура мелкоигольчатого мартенсита. Твердость повышается на 2…4 HRC по сравнению с обычной закалкой, возрастает износостойкость и предел выносливости.
Перед закалкой ТВЧ изделие подвергают нормализации, а после закалки низкому отпуску при температуре 150…200oС (самоотпуск).
Наиболее целесообразно использовать этот метод для изделий из сталей с содержанием углерода более 0,4 %.
Закалка индукционная – ТВЧ (токами высокой частоты) характеризуется двумя параметрами: глубиной и твердостью закаленного слоя детали. Для получения тонкого слоя у закаливаемой детали используются индукционные нагреватели (ТВЧ установки) мощностью от 40 кВА до 160 кВА и частотой 20 - 40 кГц либо 40 - 70 кГц. Если осуществляется закалка более глубоких слоев, то используется диапазон частот 6 - 20 кГц.
У поверхностной закалки токами высокой частоты есть ряд преимуществ:
· высокая твердость
· высокая производительность;
· любой уровень глубины закаленного слоя детали;
· отсутствие окалины;
· возможность закалки деталей любых форм;
· возможность внедрения полной автоматизации закалки.
Недостатки:
· в мелкосерийном и единичном производстве изготовление индуктора и разработка технологического процесса могут быть нерентабельными.
· Во-вторых, для некоторых деталей сложной формы изготовление индуктора затруднительно или даже невозможно.
· В-третьих, на деталях, имеющих глубокие впадины, выступы, резкие переходы, острые углы и т. д., не удается получить равномерной толщины закаленного слоя.
Хотя это ограничивает возможность применения высокочастотной закалки, тем не менее в массовом и крупносерийном производстве для таких деталей, как коленчатые валы, шестерни, втулки, шпиндели, борштанги, валки холодной прокатки и др., поверхностная закалка ТВЧ находит все большее применение.
Высокочастотная импульсная закалка (ВИЗ) предназначена для поверхностного упрочнения стальных и чугунных деталей машин.
Сущность процесса заключается в скоростном нагреве поверхности детали мощным импульсным ВЧ полем и последующей быстрой автозакалке нагретого слоя теплосбросом в глубину металла. Образование высокодисперсных упрочняющих структур (мартенсит, карбиды и др.) повышает твердость, износостойкость и другие свойства металла, увеличивает ресурс работы такой детали в несколько раз.
Для получения тока высокой частоты применяются машинные и ламповые генераторы.
В зависимости от формы, размеров закаливаемых деталей и предъявляемых к ним требований различают три способа высокочастотной закалки.
Для закалки небольших деталей применяют способ одновременной закалки: вся поверхность закаливаемой детали находится в зоне действия индуктора и нагревается одновременно. Деталь в индукторе должна вращаться. После нагрева реле времени отключает индуктор от генератора и включается водяной душ, который одновременно охлаждает всю деталь.
а – одновременный; б – непрерывно – последовательный; в – последовательный; 1 – деталь; 2 – индуктор; 3 – закалочное устройство; 4 – шланг.
Рисунок 3 – Способы ВИЗ
Детали значительной длины закаливают непрерывно-последовательным способом. Вал 1 вращается вокруг вертикальной оси и перемещается внутри индуктора 2 сверху вниз, последовательно проходя через зону нагрева и зону охлаждения закалочного устройства 3, к которому по шлангу 4 подается вода. Непрерывно-последовательную закалку стальных плит выполняют при помощи плоских индукторов.
Для закалки отдельных участков детали применяют способ последовательной закалки: поверхность нагревается и охлаждается по частям.
Максимальная глубина ВИЗ – 3.5 мм.
Достоинства ВИЗ:
· Снижение хрупкости за счет пластичной сердцевины и диспергирования зерна;
· Возможность упрочнения внутренних и наружных поверхностей;
· Возможность локального упрочнения;
· Снижение затрат энергии на нагрев;
· Технологическая простота метода, легкость автоматизации процесса.
Основы монтажа оборудования
Общие сведения
Монтаж – это последовательный процесс сборки, установки оборудования и механизмов, включающий общие подготовительные, монтажные, механические и технические действия квалифицированных специалистов, для последующего запуска оборудования.
При монтаже оборудования следует выполнять следующие правила:
- монтаж оборудования проводят чаще всего днем;
- монтаж нельзя проводить на открытых площадках при ветре более шести баллов, при дожде, снегопаде, гололеде;
- подъем груза должен доводиться до проектного положения, если это не удалось сделать до конца смены, то груз должен быть опущен на нулевую отметку;
- груз при подъеме должен быть надежно застропован, т.е. стропы налагаются равномерно без узлов и перекруток и угол между ветвями строп не должен быть больше 90°;
расстроповку груза проводят только после его установки и надежного закрепления
Создавая промышленное производство, стремятся снизить удельные капитальные вложения, эксплуатационные расходы и себестоимость продукции. Данные показатели во многом зависят от качества монтажных и ремонтных работ. Уже на стадии проектирования оборудования и изготовления его необходимо предусматривать методы монтажа и ремонтопригодность технологических машин и аппаратов.
Монтаж оборудования, как правило, состоит из следующих этапов:
· организационно-техническая подготовка монтажа;
· производство монтажных работ;
· пуско-наладочные работы.
Организационно-техническая подготовка монтажа состоит из следующих мероприятий:
· получение монтажной организацией от заказчика технической документации;
· организация монтажной площадки;
· обеспечение строительной готовности объекта;
· организация поставки оборудования;
· оснащение участка монтажным оборудованием;
· разработка и создание безопасных условий труда;
· организация контроля качества работ, подготовка кадров.
1.Техническая документация содержит: планы расположения строящихся объектов; планы и разрезы цехов; чертежи на фундаменты и монтаж оборудования; чертежи на трубопроводы и металлоконструкции; смету на производство монтажных работ; дополнительную документацию на монтаж отдельных узлов.
Монтажная организация составляет план производства работ (ППР), который содержит основные принципиальные решения по монтажу. ППР оформляется в виде пояснительной записки, к которой прикладывается генеральный план, график производства работ, ведомость трудовых затрат и график движения рабочей силы, монтажные чертежи.
Следует отметить, что график движения рабочей силы должен иметь плавный характер (рис. 4.1).
Рисунок 4.1 - График движения рабочей силы
2.Площадка для складирования является составной частью монтажной площадки ирасполагается по возможности вблизи монтируемого объекта.
Размеры площадки П, м2 определяются по формуле:
,
где М - общий вес оборудования, т;
К - коэффициент одновременности поступления (0,5... 0,9);
В - удельная загрузка, т/м2.
Удельная загрузка зависит от вида оборудования и материалов.
3. Строительная готовность объекта. Под этим термином понимают такое состояние строительной части возводимого объекта, когда можно вести монтаж в безопасных условиях и обеспечивать сохранность оборудования и рациональные методы его монтажа. В перекрытиях и стенах должны быть предусмотрены монтажные проемы для транспортировки оборудования.
4.Фундаменты под технологическое оборудование. Фундаменты бывают групповые и индивидуальные.
Групповые фундаменты представляют собой бетонное или железобетонное полотно толщиной до 300 мм, с аппаратами весом до 2 т.
Индивидуальные фундаменты используются для установки тяжелого оборудования, а также оборудования, работающего с большими динамическими нагрузками.
5. Поставка и прием оборудования. Для рациональной организации монтажа необходима комплектная поставка оборудования. Правила поставки оборудования следующие.
Малогабаритное оборудование должно поставляться в собранном виде, на подкладках, с установленными внутренними устройствами и деталями для строповки. Защитные покрытия свинцом, медью, лаком, эмалью выполняются на заводе-изготовителе, а футеровка кирпичом и плиткой на месте монтажа.
Крупногабаритное оборудование поставляется максимально укрупненными блоками с соответствующей маркировкой.
Поставляемое оборудование должно иметь ответные фланцы нам штуцерах, а также крепежные детали и анкерные болты.
Порядок транспортировки оборудования по железной дороге и реке следующий:
- по железной дороге допускается перевозка машин и аппаратов по согласованию с Министерством путей сообщения весом до 240 т, диаметром 4 ми длиной 30 м;
- по рекам на судах: диаметром до 8 ми длиной 55 м, ас буксировкой на плаву: диаметром до 10 ми длиной до 100 м по согласованию с Министерством речного флота.
Прием оборудования в монтаж производится на складе путем осмотра без разборки на узлы и детали. При этом проверяют:
- соответствие оборудования чертежам и проектной спецификации;
- комплектность оборудования по упаковочным ведомостям;
- наличие и полноту технической документации завода-изготовителя;
- отсутствие трещин, поломок и т.п.
Для обеспечения нормальной работоспособности оборудования и технологической схемы в целом необходимо точно установить и выверить это оборудование в плане и по высоте. Оборудование, как правило, устанавливается на фундаменте (рис. 4.2), и суммарная жесткость системы "станина оборудования - фундамент" во многом определяет надежность работы технологической схемы. Оборудование устанавливается в основном двумя способами:
- непосредственно на фундамент или бетонную подливку на фундаменте;
- с применением пакетов плоских металлических подкладок.
Для компенсации неточности размеров фундаментов применяются пакеты подкладок, установочные болты, упругие шайбы, фундаментные болты.
1 - оборудование; 2 - пакет пластин; 3 - подливка; 4 - фундамент
Рисунок 4.2 - Установка оборудования на фундаменте
До установки аппаратов на фундамент укладывают подкладки или приспособления для выверки оборудования. При выверке аппаратов на фундаменте проверяют соблюдение требований горизонтальности, соосности, параллельности, вертикальности и привязки осей аппарата к осям здания и строительных конструкций.
Выверку горизонтального положения оборудования следует производить по базовым поверхностям (плоскостям разъема и расточкам под вкладыши подшипников или по контрольным площадкам).
Проверку соосности валов машин и агрегатов, соединяемых муфтами, следует производить в два приема:
1) предварительная проверка при помощи линейки и щупа - это делается до затяжки фундаментных болтов и подливки бетоном плит, рам;
2) окончательная проверка при помощи специальных скоб, устанавливаемых на полумуфтах.
Заключение
Опыт работы машиностроительных предприятий свидетельствует о том, что сдерживающим фактором развития технологии ремонта изношенных деталей машин является отсутствие эффективныхметодик не только повторного использования большинства деталей после восстановления, но и самого изделия.
Восстановление изношенных поверхностей деталей является одним из важнейших показателей хозяйственной деятельности ремонтных предприятий. Современная восстановительная технология располагает достаточным объемом средств и методов, с помощью которых изношенным деталям машин практически полностью возвращаются свойства новой детали.
В технологии машиностроения при ремонте деталей машин нашли применение технологические методы, которые можно разделить на две группы:
1) методы восстановления изношенных поверхностей металлов покрытиями;
2) восстановление изношенных поверхностей деталей без добавленногометалла.
В данном модуле были рассмотрены наиболее эффективные и широко используемые методы восстановления поверхностей деталей, которые позволяют полностью восстановить работоспособность изделия.
Приведена классификация методов обработки деталей, а также разработан полный технологический маршрут восстановления работоспособности деталей изделий НГП с помощью методов восстановления поверхностей и металлообработки в комплексе, который используется на базах производственного обеспечения и ремонтных – механических цехах компаний нефтегазового сектора.
Рассмотрены основа монтажа оборудования НГП и основные показатели его надежности.
Список использованных источников
1. ГОСТ Р 53480-09 Надежность в технике. Термины и определения. Дата введ. 01.01.2011. М.: Стандартинформ, 2010. 28 с.
2. СТО 4.2 – 07 – 2014 Система менеджмента качества. Общие требования к построению, изложению и оформлению документов учебной деятельности. Введ. взамен СТО 4.2 – 07 – 2012; дата введ. 27. 02.2014. Красноярск: ИПК СФУ, 2012. - 60 с.
3. Анурьев В.И. Справочник конструктора-машиностроителя. В 3-х т. Т.2.–8-е изд., перераб. и доп. – М.: Машиностроение, 2001 – 912 с.
4. Всемирная инициатива CDIO. Стандарты: информационно методическое издание/ Пер. с анг. и ред. А.И. Чучалина, Т.С. Петровской, Е.С. Кулюкиной; Томский политехнический университет. – Томск: Изд-во Томского политехнического университета, 2011. – 17 с.
5. ДемьяненкоН.А, ШемлейР.В., БутовЮ.А., БогаткоА.Н.. Перспективы развития колтюбингового бурения в РУП «Производственное объединение «Белоруснефть». Журнал «Время колтюбинга» №33 Сентябрь 2010 – 186 с.
6. Дунаев П.Ф. Конструирование деталей узлов и деталей машин: Учеб. пособие для студ. техн. спец. вузов / П.Ф.Дунаев, О.П.Леликов. – 8-е изд., перераб. и доп.-М: Академия, 2006г.- 496.:ил.
7. Инструкция по монтажу СВП ECI 900 HP, Корпорация TESCO, 2006 г. – 124 с.
8. Конов В.Н. Основы отраслевых технологий. Учебное пособие для студентов экономических специальностей всех форм обучения. /Сост.: Конов В.Н., - Красноярск. - Красноярский филиал МЭСИ, 2005. -107с.
9. Машиностроение. Энциклопедия. Надежность машин. Т. VI – 3/ В.В. Клюев, В.В. Болотин, Ф.Р. Соснин и др.; общ. ред. В.В. Клюева. 2003. – 596 с.: ил.
10. МолчановА.Г., ВайнштокС.М., НекрасовВ.И.,ЧернобровкинВ.И.. Подземный ремонт и бурение скважин с применением гибких труб.224 с., ил. 2000 г.
11. Новочихина Л.И. Справочник по техническому черчению/Л.И.Новочихина. -3-е изд., стереотип. Мн.;Книжный дом, 2008. – 320 с.
Протасов В.Н. Эксплуатация оборудования для бурения скважин и нефтегазодобычи. Учебник для вузов / В.Н.Протасов, Б.З.Султанов, С.В.Кривенков под общей редакцией В.Н.Протасова - М.: Недра, 2004. – 691 с.
Приложение А
ОТЧЕТ ПО МОДУЛЮ 3
по дисциплине «Эксплуатация, ремонт и монтаж машин и оборудования
для добычи нефти и газа»
Тема: Технологические основы и технологические процессы ремонта, эксплуатации и монтажа оборудования
Творческий коллектив гр. НГ 10-04 в составе:
Руководитель раздел 3,4 общая редакция Д.Е. Латышев
Исполнитель раздел 1,2,5И.С. Зингер
Преподаватель доцент, к.т.н. В.Н. Конов
Красноярск 2014
Содержание
Введение.......................................................................................................................3
1 Технологические основы ремонта оборудования….............................................5
1.1 Система технического обслуживания и ремонта
оборудования.........
|
|
Эмиссия газов от очистных сооружений канализации: В последние годы внимание мирового сообщества сосредоточено на экологических проблемах...
Кормораздатчик мобильный электрифицированный: схема и процесс работы устройства...
Общие условия выбора системы дренажа: Система дренажа выбирается в зависимости от характера защищаемого...
Состав сооружений: решетки и песколовки: Решетки – это первое устройство в схеме очистных сооружений. Они представляют...
© cyberpedia.su 2017-2024 - Не является автором материалов. Исключительное право сохранено за автором текста.
Если вы не хотите, чтобы данный материал был у нас на сайте, перейдите по ссылке: Нарушение авторских прав. Мы поможем в написании вашей работы!