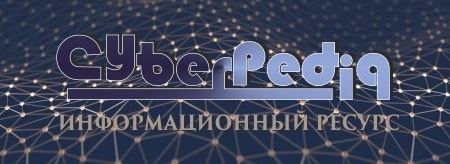
Биохимия спиртового брожения: Основу технологии получения пива составляет спиртовое брожение, - при котором сахар превращается...
Архитектура электронного правительства: Единая архитектура – это методологический подход при создании системы управления государства, который строится...
Топ:
Техника безопасности при работе на пароконвектомате: К обслуживанию пароконвектомата допускаются лица, прошедшие технический минимум по эксплуатации оборудования...
Проблема типологии научных революций: Глобальные научные революции и типы научной рациональности...
Интересное:
Искусственное повышение поверхности территории: Варианты искусственного повышения поверхности территории необходимо выбирать на основе анализа следующих характеристик защищаемой территории...
Инженерная защита территорий, зданий и сооружений от опасных геологических процессов: Изучение оползневых явлений, оценка устойчивости склонов и проектирование противооползневых сооружений — актуальнейшие задачи, стоящие перед отечественными...
Финансовый рынок и его значение в управлении денежными потоками на современном этапе: любому предприятию для расширения производства и увеличения прибыли нужны...
Дисциплины:
![]() |
![]() |
5.00
из
|
Заказать работу |
|
|
Основной дефект вала привода инжектора установки МК20Т – износ трущихся посадочных поверхностей, в первую очередь шлицевых и поверхностей, предназначенных для посадок подшипников. Изношенные посадочные места под подшипники качения восстанавливают электродуговой наплавкой, виброконтактной или полуавтоматической наплавкой под слоем флюса, а также осталиванием.
Рисунок 2.5 - Шлицевой вал привода установки МК20Т.
Выбор способа ремонта зависит от характера соединения сопрягаемых, деталей и величины износа. Износ шеек валов, сопрягаемых с внутренними кольцами подшипников качения по скользящей или неподвижной посадкам, обычно не превышает 0,08—0,15 мм. Такой слой металла можно восстановить осталиванием.
Шейки валов, вращающиеся в подшипниках скольжения, изнашиваются на большой площади по всей длине контакта вала с подшипником. Сильно изношенные шейки часто восстанавливают электродуговой наплавкой, а иногда (в хорошо оборудованных мастерских) виброконтактной или полуавтоматической наплавкой под слоем флюса. Толщина наплавленного слоя металла после обработки должна быть не меньше 1,0—2 мм. Поэтому валы с износом 0,5—0,6 мм по диаметру предварительно протачивают на 1—2 мм по диаметру, затем наплавляют, предусматривая припуск на обработку 3—4 мм. Перед наплавкой изношенную поверхность зачищают стальной щеткой. При наплавке применяют электроды Э-42, Э-50, ОЗН-250, ОЗН-300 и др. Для получения весьма твердой износостойкой поверхности шейки валов наваривают специальными электродам с высококачественной обмазкой.
При автоматической вибродуговой наплавке, вал с изношенными шлицевыми зубьями отжигают при температуре 850 – 900 С. Под одной из впадин зуба ставится метка для правильной установки вала при последующем фрезеровании. затем вал устанавливается горизонтально – фрезерный станок и ставится на равномерную подачу со скоростью примерно 0,2 – 0,3 м/мин и толщиной наплавляемого слоя 3 – 4 мм, включая 2 – 3 мм на последующую обработку. Зубья наплавляются сплошным слоем, в качестве присадочного материала используются стали 35Х, 40Х, У10, У20 и другие легированные или высокоуглеродистые инструментальные стали. После завершения наплавки со шлицев на фрезерном станке пальцевой фрезой снимается припуск на боковой стороне зубьев, затем на токарном станке вал обтачивается до номинального диаметра вершин зубьев. После завершения механической обработки вал нормализуется при температуре
|
850 – 900 С и шлифуется.
Технология механической обработки
Сварка
Сваркой называют технологический процесс получения неразъемных соединений из металлов (или пластмасс), осуществляемый установлением межатомных (у пластмасс — межмолекулярных) связей между свариваемыми частями изделия при их местном или общем нагреве, или пластическом деформировании, или при совместном действии этих двух факторов. Между свариваемыми частями изделия образуется сварной шов.
Сварка является одной из распространенных технологических операций, широко применяемой в машиностроении, на транспорте и в строительстве. Объясняется это значительной экономией металлов по сравнению с болтовыми и заклепочными соединениями, высокой прочностью и низкой стоимостью сварных конструкций.
В зависимости от состояния металла в сварочной зоне все виды сварки можно разделить на две группы: по способу соединения свариваемых частей изделия и по виду используемой энергии. В первом случае различают сварку плавлением и сварку давлением. При сварке плавлением сварной шов образуется из общей сварочной ванны расплавленных металлов соединяемых частей изделия. При сварке давлением, для повышения пластичности металла в зоне сварки, соединяемые части изделия нагревают и сдавливают.
|
По виду используемой энергии сварку подразделяют на термическую (сварка дуговая, плазменная, газовая и др.), термомеханическую (сварка контактная, диффузионная и др.) и механическую (сварка взрывом, трением, ультразвуковая и др.).
При сварке плавлением образуется литой сварной шов с характерным дендритным строением. При сварке давлением образуется шов, представляющий собой зону сросшихся кристаллитов металла соединяемых частей изделия. Зону, непосредственно примыкающую к сварному шву, называют зоной термического влияния.
Пайка
Пайка — это процесс получения неразъемных соединений в результате расплавления припоя, смачивания им металла, растекания припоя по поверхности металла и заполнения зазора между соединяемыми заготовками (деталями) и, наконец, затвердевания припоя.
В отличие от сварки при пайке не требуется расплавления основного металла, что позволяет производить распай деталей. Наиболее широко пайку применяют в электро- и радиотехнике и приборостроении. В этих отраслях промышленности пайку производят для создания механически прочного, иногда герметичного, шва или для получения постоянного (нескользящего или разрывного) электрического контакта с небольшим переходным сопротивлением.
|
|
Семя – орган полового размножения и расселения растений: наружи у семян имеется плотный покров – кожура...
Таксономические единицы (категории) растений: Каждая система классификации состоит из определённых соподчиненных друг другу...
Своеобразие русской архитектуры: Основной материал – дерево – быстрота постройки, но недолговечность и необходимость деления...
Общие условия выбора системы дренажа: Система дренажа выбирается в зависимости от характера защищаемого...
© cyberpedia.su 2017-2024 - Не является автором материалов. Исключительное право сохранено за автором текста.
Если вы не хотите, чтобы данный материал был у нас на сайте, перейдите по ссылке: Нарушение авторских прав. Мы поможем в написании вашей работы!