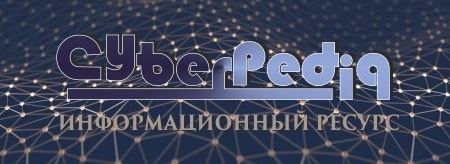
Автоматическое растормаживание колес: Тормозные устройства колес предназначены для уменьшения длины пробега и улучшения маневрирования ВС при...
Биохимия спиртового брожения: Основу технологии получения пива составляет спиртовое брожение, - при котором сахар превращается...
Топ:
Характеристика АТП и сварочно-жестяницкого участка: Транспорт в настоящее время является одной из важнейших отраслей народного...
Характеристика АТП и сварочно-жестяницкого участка: Транспорт в настоящее время является одной из важнейших отраслей народного хозяйства...
Методика измерений сопротивления растеканию тока анодного заземления: Анодный заземлитель (анод) – проводник, погруженный в электролитическую среду (грунт, раствор электролита) и подключенный к положительному...
Интересное:
Принципы управления денежными потоками: одним из методов контроля за состоянием денежной наличности является...
Лечение прогрессирующих форм рака: Одним из наиболее важных достижений экспериментальной химиотерапии опухолей, начатой в 60-х и реализованной в 70-х годах, является...
Аура как энергетическое поле: многослойную ауру человека можно представить себе подобным...
Дисциплины:
![]() |
![]() |
5.00
из
|
Заказать работу |
|
|
История развития отрасли.Роль русских ученых
Мельница всегда играла прогрессивную роль в развитии техники соответствующей эпохи. Маркс писал: ”... на их основе развивалась вся теория равномерных движений... Всю историю развития машин можно проследить по истории развития мукомольных мельниц”.
Корни возникновения ТОЗПП уходят в доисторические времена, к первым зернотеркам, жерновам, а затем водяным и ветряным мельницам.
Мукомольная промышленность России бурно развивается со второй половины ХIХ в., после отмены крепостного права. В 80-х годах ХIХ в. началось широкое строительство мельниц с паровыми двигателями. В 90-х годах ХIХ в. в России появились первые автоматические мельницы с широким использованием транспортных механизмов. В 1883 г. в Москве был открыт завод, производящий вальцовые станки, вентиляторы и трансмиссионное оборудование. В скором времени заводы по выпуску ТОЗПП появились в Нижнем Новгороде, Петербурге, Риге, Саратове, Киеве и в др. городах.
Характерными особенностями развития отрасли в советский период были переход на комплектные поставки всего технологического оборудования, повышение производительности машин, переход от трансмиссионного привода к индивидуальному, углубление процессов механизации и автоматизации работы предприятий.
Отечественные ученые являются основоположниками теории работы многих машин для переработки зерна. Своими капитальными работами они закрепили приоритет русской науки в этой отрасли. Еще в 1811 г. русский автор Василий Левшин опубликовал труд под названием “Полное наставление на гидродинамических правилах основанное о строении мельниц каждого рода - водяных, также ветром, горячими парами, скотскими и человеческими силами в действие приводимых”. В этой книге подробно освещены вопросы устройства водяных, ветряных и паровых мельниц.
|
Подлинными основоположниками теории мельничных машин являются: профессор Петербургского технологического института П. А. Афанасьев, который в 1876 г. издал книгу “Мукомольные мельницы”, где впервые привел подробные материалы о строении и химическом составе зерен, широко осветил устройство жернового постова - основной в ту пору измельчающей машины, разработал вопрос о наилучшей форме бороздок на поверхности жерновов и дал теоретические основы расчета этих машин; профессор Харьковского технологического института К. А. Зворыкин, написал в 1894 г. книгу “Курс по мукомольному производству”, в которой анализируются отдельные узлы вальцового станка, имеются данные о рациональных нагрузках на рабочие органы мельничных машин, о назначении и способах увлажнения зерна перед помолом, а также машинах для этой цели, приведено устройство различных типов рассевов и ситовеечных машин; профессор Московского высшего технического училища П. А. Козьмин, опубликовал в 1912 г. работу "Мукомольное производство - теоретическое и практическое пособие для техников", которая переведена на английский язык. Разработкой теории работы мельничных машин занимался великий русский ученый Н. Е. Жуковский, который еще в 1887 г. опубликовал исследования о движении продукта по ситу рассева с круговым поступательным движением.
В советский период значительный вклад в развитие науки и техники отрасли внесли профессора: Я. Н. Куприц, разработавший физико-химические основы процессов переработки зерна; Д. В. Шумский, обобщивший опыт строительства элеваторов и сформулировавший теорию, являющуюся основой для проектирования элеваторов; А. Я. Соколов, систематизировавший оборудование для хранения и переработки зерна и написавший серию учебников для подготовки специалистов отрасли; инженеры А. Ф. Григорович, А. П. Беспалов, И. И. Нестеров и др., разработавшие оригинальные конструкции машин для переработки зерна. Благодаря им и другим не менее известным авторам уровень науки и техники в России в этой отрасли поддерживается на достаточно высоком уровне и отечественная зерноперерабатывающая промышленность не выглядит хуже других передовых стран.
|
Рабочие органы машины
Машины могут иметь один или несколько рабочих органов, в том числе и основных. При этом, они (РО) могут быть все подвижными, одни подвижные, а другие неподвижные, все неподвижные. В последнем случае технологический эффект достигается в большинстве случаев за счет движения продукта. РО могут служить воздушные и водяные потоки, поля (магнитные, электрические, световые, температурные и др.), а также реакционные пространства (камеры), где создаются определенные условия для воздействия на обрабатываемый продукт. Воздействие осуществляется изменением влажности, давления (вакуума), температуры, химического состава окружающей среды или другим способом.
Приемно - питающие устройства. Требования к ним. Условие захвата про-та одновалк. РО
Приемно-питающие устройства в том или ином виде входят в состав любой технологической машины. При этом выполняемые ими функции различаются в зависимости от конкретной машины и вида перерабатываемого продукта. Однако к большинству из приемно-питающих устройств предъявляются следующие требования:
- непрерывно (равномерно во времени) и равномерно (по длине, ширине или площади рабочего органа) подавать продукт в рабочую зону;
- иметь возможность изменять (регулировать) количество подаваемого в машину продукта;
- обеспечивать герметизацию внутренних (рабочих) полостей машины.
Наибольшее распространение в зерноперерабатывающей отрасли получили барабанные, клапанные, тарельчатые, шнековые и вибрационные питатели рис. 5.1.
При одновалковом и барабанном рабочем органе важно обеспечить захват материала. В противном случае движение материала не будет иметь место, Q = 0. Для исключения проскальзывания валка (барабана) относительно материала необходимо соблюсти определенные соотношения между кинематическими параметрами и размерами РО. Размеры барабанного питателя и его кинематические параметры взаимосвязаны. Поэтому существуют ограничения на величину скорости или размер (диаметр) барабана. Для нахождения взаимосвязи между диаметром барабана и частотой (скоростью) его вращения следует рассмотреть силы, действующие на элементарный слой материала, находящегося на барабане, рис. 5.4. Для обеспечения движения продукта необходимо, чтобы сумма сил, действующих на слой продукта в направлении его движения, была больше суммы сил сопротивления, т. е.
|
G cosa + Fтр. б. ³ Fтр. к., (5.5)
где G - сила тяжести элементарного слоя продукта, G = mg;
Fтр. б. - сила трения продукта о барабан;
Fтр. к. - сила трения продукта о корпус.
Схема сил
Сила трения продукта о корпус возникает вследствие наличия силы инерции РИН при круговом движении продукта:
Fтр.к = Рин fк = m w2 R fк, (5.6)
где fк - коэффициент трения продукта о корпус.
Учитывая, что Fтр. б. = mg sina fб., выражение 5.5. преобразуется к виду:
m w2 R fк £ mg cosa fб. + mg sina, (5.7)
Поскольку коэффициент трения продукта о барабан fб и корпус fк обычно равны, так как изготавливаются из одного материала, а также имея в виду, что минимальное значение правая часть приобретает при a=00, после несложных преобразований получаем:
w2 £ R g, (5.8)
откуда получаем выражение, ограничивающее частоту вращения барабана
, (5.9)
или относительно линейной скорости поверхности барабана :
(5.10)
Выпускные устройства. Требования.. Произв-сть разл.видов ППУ и ВУ
Поскольку большинство зерноперерабатывающих машин непрерывного действия, то к их выпускным устройствам предъявляют следующие требования:
- обеспечивать непрерывный и беспрепятственный вывод продукта из машины;
- не допускать пылевыделения и потерь продукта;
- быть простыми и надежными в эксплуатации, удобными в обслуживании;
- зачастую выпускные устройства должны обеспечивать герметизацию машины, поскольку она находится под разряжением или избыточным давлением, поэтому они должны не допускать излишних подсосов или утечек воздуха, пара или др. газа.
|
Наиболее часто в зерноперерабатывающей отрасли используются выпускные устройства следующих типов: клапанные, барабанные (как правило, шлюзовые), шнековые, вибрационные. При этом, герметизацию для последних двух типов достигают путем образования так называемой “пробки” из продукта, например как показано на рис. 5.2. Иногда в качестве выпускных устройств используют комбинацию, например шнека и клапана, рис. 5.2 или вибролотка и клапана.
с герметизирующей “пробкой”.
1 - шнек; 2 - “пробка”; 3 - клапан.
Рис. 5.2. Схема шнекового выпускного устройства
В некоторых технологических машинах нашли применение эластичные герметизирующие элементы, которые совместно с патрубком выполняют функции выпускного устройства, рис. 5.3. Герметизация в этом случае достигается за счет деформации эластичного элемента под действием разряжения или избыточного давления.
1 - патрубок; 2 - эластичный элемент.
Рис. 5.3. Схема эластичного герметизирующего устройства.
Производительность ППУ и ВУ
Выражение для определения производительности того или иного приемно-питающего или выпускного устройства зависит от его типа.
Для шлюзового питателя (выпускного устройства) производительность Qшп определяется по выражению:
Qшл = V i w
, (5.1)
где V - объем ячейки;
i - количество ячеек;
w - частота вращения ротора;
- насыпная плотность продукта;
- коэффициент заполнения ротора.
Производительность Qшн шнекового питателя (выпускного устройства) можно найти по формуле:
(5.2)
где D - диаметр шнека;
t - шаг последнего витка шнека;
w1- частота вращения шнека;
- коэффициент заполнения продукта.
Коэффициент заполнения зависит как от физико-механических свойств продукта, так и от параметров дозатора (питателя, выпускного устройства, длины герметизирующей пробки, частоты вращения рабочего органа, формы, размеров и материала рабочих органов).
Производительность вибрационного питателя (выпускного устройства)Qв определяется по выражению:
(5.3)
где - скорость движения продукта;
F - площадь поперечного сечения продукта.
Скорость движения продукта по вибролотку зависит от частоты w и амплитуды А колебаний последнего, а также от направления колебаний относительно направления движения, которое можно задать углом b:
= К А w cosb, (5.4)
где К - коэффициент, зависящий от свойств продукта.
Производительность клапанно-грузовых, клапанно-пружинных и эластичных приемно-питающих и выпускных устройств рассчитывается по выражениям для самотечного транспорта. При этом следует учитывать уменьшение площади поперечного сечения потока и скорости его движения, вызванные наличием соответствующего герметизирующего элемента.
|
Сепаратор А1 - БСФ
Сепаратор А1 - БСФ предназначен для разделения зерна на фракции и очистки его от примесей.
Корпус сепаратора 1, рис. 8.11 представляет собой пространственную металлоконструкцию, соединенную с пакетами ситовых рам 2 зажимными устройствами 3. Ситовые рамы крепятся к балкам с помощью подвесок 4.
1 - корпус; 2 - ситовые рамки; 3 - зажимное устройство; 4 - подвески;
5 - ременная передача; 6 - груз; 7 - подшипник; 8 - штанга;
9 - приемный патрубок; 10 - рукав; 11 - выпускной патрубок.
Рис. 8.11 Схема сепаратора типа А1 – БСФ
Очистка сит осуществляется при помощи треугольных полиуретановых очистителей. Ситовая рамка имеет поддон для сбора проходовых фракций и каналы для передачи фракций на другие сита или выпускные патрубки в соответствии с технологической схемой. Самобалансный привод сепаратора обеспечивает круговое поступательное движение и размещен в центральной части. Привод осуществляется от электродвигателя через ременную передачу 5 балансирному механизму, представляющему собой вал, закрепленный в двух сферических подшипниках 7 и груз-дебаланс 6. Для регулирования амплитуды колебаний имеются сменные пластины. На штангах 8, присоединенных к потолочной раме, крепятся приемные патрубки 9, соединенные с пакетом сит с помощью матерчатых рукавов 10. Выпускные патрубки 11 соединены с напольными патрубками также с помощью рукавов.
Исходная смесь двумя потоками поступает на сита с продолговатыми отверстиями, ориентированными в различных (перпендикулярных) направлениях. Причем группы различно ориентированных отверстий чередуются между собой в шахматном порядке, как это показано на рис. 8.12. Схода с нижней пары сит объединяют в крупную фракцию зерна, направляемую на мукомольный завод. Проходы через сита с продолговатыми отверстиями просеиваются на ситах с отверстиями Æ= 2 мм, сходом с которых получается мелкая фракция зерна, а проходом - мелкие примеси.
Рис. 8.12 Схема расположения отверстий в приемных ситах.
После соответствующей переделки можно несколько изменить технологическую схему, а также получать при сепарировании другие фракции.
Рассев Р3 - БРБ
Основными принципиальными отличиями рассева Р3 - БРБ от сепаратора типа А1 - БСФ является устройство ситового кузова и применение кривошипного привода. Для уравновешивания используется груз-дебаланс. Схема рассева типа Р3-БРБ представлена на рис. 8.13.
Для обеспечения эксцентриситета между валками II и III применяется эксцентриковая муфта 3, груз-дебаланс 4 служит для уравновешивания системы. Массу груза можно изменять пластинами, что позволяет избежать веретенообразного движения вала II.
1 - электродвигатель; 2 - ременная передача; 3 - эксцентриковая муфта; 4 - груз; 5 - подшипник; 6 - подвеска; 7 - рама потолочная; 8 - рукав;
9 - патрубок выпускной; 10 - секция ситовая.
Рис. 8.13 Схема рассева типа Р3 – БРБ
Корпус представляет из себя шкаф с дверцами, в которые вставляются ситовые рамки. В дверцах помещены каналы для движения продукта. Каждая дверь шарнирно подвешена к корпусу и запирается винтовыми замками.
Классификация возд.сепараторов. Примеры конструкции
Пневмосепараторы на элеваторах, мельницах, крупяных и комбикормовых заводах применяют для очистки зерна от пыли и лёгких примесей, а также для разделения продуктов шелушения, контроля крупы и отходов.
По назначению все пневмосепараторы можно разделить на 3 группы:
- для очистки зерна от примесей;
- для отделения твёрдой фракции от газообразной (отделители);
- для фракционирования.
По структуре рабочего цикла пневмосепараторы различают:
- пневмосепараторы с замкнутым циклом движения воздуха (рис.9.2, а);
- пневмосепараторы с разомкнутым циклом движения воздуха (рис.9.2, б).
Последние обладают более высокой эффективностью очистки, однако менее экологичны, поскольку в окружающую среду выбрасывается запылённый воздух.
В зависимости от наличия источника гидравлической энергии пневмосепараторы могут быть с воздуходувной машиной (вентилятором) и без неё. В последнем случае используется внешний источник гидравлической энергии.
а) с замкнутым циклом движения воздуха;
б) с разомкнутым циклом движения воздуха, без вентилятора.
1 - приёмный патрубок; 2 - воздуховод; 3 - вентилятор; 4 – осадочная камера; 5 – грузовой клапан; 6 – выпускной патрубок; 7 – регулятор.
Рис.9.2 - Схемы пневмосепараторов.
В зависимости от направления движения воздушного потока в пневмоканале различают пневмосепараторы с вертикальным, горизонтальным и наклонными пневмоканалами.
На зерноперерабатывающих предприятиях широко применяют сепараторы Р3-БАБ и Р3-БСД.
Пневмосепаратор Р3 – БАБ (рис. 9.3) имеет разомкнутый цикл движения воздуха и не имеет воздуходувной машины
![]() |
- исходный продукт
-воздух;
- лёгкая фракция (примеси, относы);
![]() |
1 – вибратор; 2 – подвеска вибролотка; 3 – приёмный патрубок;
4 – подвижная стенка; 5 – воздуховод; 6 – дроссельная заслонка;
7, 8, 9 – штурвалы; 10 – жалюзи, 11 – светильник, 12 – смотровое
окно, 13 – выпускной конус; 14 – вибролоток.
Высокая эффективность очистки достигается благодаря предварительному расслоению смеси на вибролотке, равномерному распределению её по ширине пневмосепарирующего канала и возможности регулирования потоков воздуха.
Исходный продукт через приёмный патрубок 3 поступает на вибролоток 14. Вследствие вибраций смесь расслаивается (более плотные частицы попадают в нижние слои). Благодаря вибрациям продукт равномерно распределяется по ширине вибролотка. В зазоре между корпусом сепаратора и вибролотком образуется затвор, исключающий поступление значительного количества воздуха через приёмный патрубок. Основная часть воздуха поступает из – под вибролотка, проходя через слой материала, уносит лёгкие примеси в воздуховод 5. Очищенное зерно выводится из сепаратора через конус 13. Дополнительное количество воздуха поступает через жалюзи 10. Скорость воздуха в пневмоканале можно регулировать с помощью дроссельной заслонки 6 и положением подвижной стенки 4. Регулировки осуществляются штурвалами 7…9. Для наблюдения за процессом пневмосепарирования и более тонкой его настройки в стенке сепаратора предусмотрены смотровое окно 12 и светильник 11. Привод вибролотка осуществляется колебателем инерционного типа 1. При этом, меняя положение грузов на валу вибратора, можно изменять амплитуду колебаний вибролотка.
Сепаратор Р3 – БСД
Воздушный сепаратор Р3 – БСД (рис.9.4) предназначен для очистки зерновых смесей от легких примесей, а также для отделения твёрдой фазы от воздуха.
1 – приёмное устройство; 2 – отражатель; 3 – входной патрубок;
4 – колпак; 5 - смотровое окно; 6 - направляющее кольцо; 7 - внутренний кожух; 8 - патрубок для относов; 9 – патрубок отсасывающий;10 – патрубок для очищенного зерна; 11 – дроссельная заслонка;12 – сигнализатор; 13 – распределитель; 14 – воронка.
Смесь продукта с воздухом (аэросмесь) поступает в приёмный патрубок 3 и, ударяясь об отражатель 2, попадает в направляющую воронку 14, а затем на распределитель 13. Смесь, скатываясь с распределителя, попадает в первый пневмосепарирующий канал. Здесь встречным потоком воздуха смесь продувается и тяжёлая фракция (очищенное зерно) направляется в конус, а затем через патрубок 10 выводится из машины. Воздух с примесями попадает в пространство между внутренним кожухом 7 и распределителем 13, а затем во второй пневмосепарирующий канал, где отделяются более тяжёлые относы, которые выводятся через патрубок 8. Воздух с наиболее лёгкими примесями из пневмосепаратора отсасывается через патрубок 9.
Эффективность очистки в пневмосепараторе достигает 94% при производительности до 2 кг/с. При этом расход воздуха составляет около 1 м3/с.
Пневмосепаратор ПА-10.
Пневмосепаратор ПА-10 предназначен для выделения лёгких примесей из зерновой смеси; на нём достигается высокая эффективность очистки семян, в том числе и при выделении таких трудноотделимых примесей как овсюг, курай, карлык, вьюнок.
Сепаратор (рис. 9.5) представляет собой сварную (из стального листа) конструкцию.
- исходная смесь; - грубые примеси; - продукт без грубых примесей; - воздух; - тяжёлая фракция (зерно); - относы; - тяжёлые относы; - лёгкие относы.
1 – приёмный патрубок; 2 – решётка; 3,5 – вибролотки;4–вибратор;
6 – патрубок для тяжёлой фракции (зерна); 7,8 – патрубки для
тяжёлых и лёгких относов; 9,11 – осадочные камеры;
10 – всасывающий патрубок; 12 – жалюзи.
Внешний источник гидравлической энергии – вентилятор, соединяется со всасывающим патрубком 10.
Исходная смесь через приёмный патрубок поступает на решётку, которая улавливает грубые примеси. Смесь поступает последовательно на два вибролотка 3 и 5, где расслаивается и равномерно распределяется по ширине. Второй лоток заканчивается воздухопроницаемой решёткой, где смесь дополнительно расслаивается и лёгкие частицы уносятся в осадочные камеры 9 и 11. Тяжёлая фракция (зерно), скатываясь с вибролотка 5, выводится из сепаратора через патрубок 6, а относы, подхватываемые дополнительным количеством воздуха, поступившим через жалюзи 12, уносятся в осадочные камеры. Более тяжёлые относы выводятся через патрубок 7, а лёгкие – через патрубок 8.
Пневмосепаратор А1 - БВЗ.
Сепаратор А1 – БВЗ, схема которого показана на рис. 9.6, с замкнутым циклом движения воздуха предназначен для очистки зерна от лёгких примесей, для разделения продуктов шелушения и контроля крупы, относов лузги.
В сварном корпусе сепаратора находятся центробежный вентилятор 8, приёмный патрубок с каналом и рассекателем 2, рабочая камера с отражательными планками 3, осадочная камера 7, выпускные устройства для зерна 5 и лёгких относов 6. При этом для сбора и выпуска лёгких относов используется шнек, привод которого осуществляется от одного и того же с вентилятором электродвигателя.
Воздушный поток отсасывается вентилятором через щели дросселя 9 из осадочной и нагнетается в рабочую камеру. Гребёнки 4 позволяют равномерно распределить воздушный поток по длине рабочей камеры. Зерно, преодолевая сопротивление грузового клапана 10,
Рис. 9.6 - Схема сепаратора А1-БВЗ.
падает вниз с одной отражательной планки на другую, подвергаясь при этом воздействию воздушного потока.
Захваченные лёгкие примеси осаждаются в камере 7 и выводятся из машины шнеком 6. Очищенное зерно от легких примесей удаляется через патрубок 5.
- исходный продукт; - относы;
- тяжёлая фракция.
1 – приёмный патрубок; 2 – рассекатель; 3 – планки отражательные,
4 – гребёнка; 5,6 – соответственно выпускные устройства для тяжёлой
фракции (зерна) и лёгкой фракции (относов); 7- осадочная камера;
8 – вентилятор; 9-дроссель; 10-клапан грузовой.
Требования к эксплуатации воздушных сепараторов. Примеры конструкций(см 26)
Для достижения высокоэффективной работы пневмосепараторов необходимо выполнять ряд требований; некоторые из которых изложены ниже.
1. Внутренние полости пневмосепараторов должны быть изолированы от окружающей среды, для этого в свою очередь, необходимо:
- иметь над приёмными и выпускными патрубками надёжные противоприсосные (герметизирующие) устройства;
- обеспечить плотность закрывания лючков, смотровых окон, фланцевых и других соединений;
- не допускать наличие вмятин, трещин, отверстий в стенках осадочных камер, пневмоканалов и воздуховодов.
2. Величина скорости воздуха в пневмоканалах и осадочных камерах должна соответствовать номинальным значениям (рациональным режимам работы).
3. Подача продукта в машину по времени и по длине (ширине) пневмоканала должна быть равномерной.
4. Следует исключить попадание в пневмосепарационные каналы грубых примесей.
5. При эксплуатации следует не допускать разбалансировки вентилятора, следить за нормальным натяжением ремней.
Цилиндрический триер БТС
Триер БТС предназначен для очистки зерна от примесей, отличающихся от основной культуры (пшеницы) длиной (овсюг, овес, ячмень и др.). Рабочим органом машины, рис. 11.6, является цилиндрическая поверхность 2 с ячейками диаметром 8,5 мм.
1 – бандаж; 2 – цилиндр ячеистый; 3 – лоток; 4 – шнек для сбора короткой фракции; 5 – передача цепная; 6 – сборник овсюга; 7 – ворошитель; 8 – вал приводных роликов; 9 – вал промежуточный;
10 – электродвигатель; 11 – сборник короткой фракции; 12 – плужок; 13 – шнек питающий; 14 – приемник; 15 – ролик приводной.
По краям ячеистого цилиндра расположены бандажи 1, опирающиеся на ролики 15. Внутри цилиндра расположен питающий шнек 13 и шнек 4, служащий для сбора и вывода короткой фракции (пшеницы) из триера. Внутри цилиндра находится гребенка с плужками 12 служащими для перемещения длинной фракции вдоль цилиндра. Со стороны выпуска овсюга находится ворошитель 7. Цилиндр приводится в действие от электродвигателя 10 через ременные передачи, промежуточный вал 9, приводной вал 8 и ролики 15. Ролики за счет сил трения с бандажами передают движение ячеистому цилиндру. С вала 8 движение при помощи цепной передачи передается на шнеки 4, 13 и ворошитель 7.
Исходная смесь, поступающая на очистку питающим шнеком, распределяется тонким слоем примерно на 2/3 длины цилиндра. Зерна пшеницы, попадая в ячеи, поднимаются и выпадают в желоб шнека выводящий очищенное зерно в сборник. Овсюг и другие длинные примеси, не помещаясь в ячейки, скапливаются в цилиндре и при помощи плужков перемещаются вдоль его оси. Ворошитель разрыхляет зерновую массу, облегчая попадание пшеницы в ячеи. Овсюг через борт цилиндра поступает в сборник 6. Наибольшую эффективность очистки триер имеет при производительности 5 т/час и частоте вращения 38 об/мин.
Энтолейтор Р3 – БЭЗ
Энтолейтор Р3 – БЭЗ предназначен для уничтожения вредителей в зерне (стерилизации зерна). Функциональная схема машины представлена на рис. 14.2.
![]() | |||
![]() |
- исходный продукт; - обеззараженный продукт.
1-корпус; 2-отражательное кольцо; 3-втулки; 4-приёмный патрубок;
5-диски; 6-выпускной патрубок, 7-ремённая передача,
8-электродвигатель.
Рис.14.2 - Схема энтолейтора Р3 – БЭЗ.
Исходный продукт попадает на вращающийся диск 5 и под воздействием сил инерции отбрасывается на закреплённые между дисками втулки 3. В результате ударов продукта о втулки и отражательное кольцо 2 происходит уничтожение вредителей. Обеззараженный продукт выводится из машины через выпускной патрубок 6. Привод ротора осуществляется от электродвигателя 8 через ремённую передачу 7.
Вертикальная обоечная машина Р3 – БМО
Вертикальная обоечная машина Р3 – БМОпредназначена для очистки поверхности зерна от пыли и частичного удаления оболочек, зародыша и бородки.
Зерно из приёмного патрубка 1(рис. 14.3) направляется на два
- исходный продукт; , - продукты обработки.
![]() |
Рис. 14.3 - Схема обоечной машины типа Р3 – БМО.
конуса 4 и 5, а из них на диск 13, который направляет зерно на крестовину 11, а затем на бичи 12 и сетчатый барабан 7. В зазоре между ситовым барабаном и бичевым ротором зерно движется по спиральной траектории, подвергаясь воздействию ударов и трения. В результате этого от зерна отделяются пыль, частицы оболочек, зародыш и бородка. Продукты обработки собираются в конусе 8 и выводятся из машины через патрубок 9. Два конуса 4 и 5, а также подпружиненный диск 13 обеспечивают равномерность поступления зерна. Привод ротора осуществляется от электродвигателя через ремённую передачу. Выпускают два типоразмера таких машин Р3 – БМО – 6 и Р3 – БМО – 12, главными отличительными особенностями Р3 – БМО – 12 от Р3 – БМО – 6 является в два раза большая производительность и раздельный выпуск полученных фракций.
Ситовеечные машины. Конструкции. Техн.эфф-сть работы.Параметры.Требования к эксп-ции.
После сортирования продуктов измельчения зерна на ситах (в рассевах) получают фракции однородные по размерам, но неоднородные по качеству (соотношение эндосперма и оболочки в частицах различно). Дальнейшая переработка таких продуктов для получения сортовой муки становится невозможной без их разделения по качеству. Эту задачу на мельзаводах выполняют ситовеечные машины.
Ситовеечные машины относятся к классу вибропневмопневматических машин с просеивающими делительными плоскостями. Сортирование в ситовеечных машинах происходит по совокупности аэродинамических и геометрических свойств; причём значительная роль отводится процессу стратификации (самосортированию).
Технологическую эффективность работы ситовеечной машины оценивают выходом обогащённых продуктов (ВОБ) и перераспределением зольности (DZ).
, (13.17)
где Gi - масса i-той фракции проходовых частиц в единицу времени;
GИСХ - масса исходного продукта, поступившего на машину за то же время;
n - число фракций.
, (13.18)
где Z1 и Z2 - зольность i - той фракции продукта до поступления на машину и полученной после неё.
На эффективность процесса обогащения главным образом влияют:
- гранулометрический состав исходного продукта (крупность и однородность);
- удельная нагрузка;
- скорость воздуха;
- равномерность распределения продукта по ситу;
- кинематические параметры движения кузова;
- размеры установленных сит;
- направление колебаний.
В последнее время наибольшее распространение на мельзаводах получила ситовеечная машина А1-БСО (рис. 13.10). Она состоит из
- воздух; - исходный продукт; - промежуточные
продукты; - проходовые продукты; - сходовые продукты.
1-станина; 2-преобразователь эксцентриковый; 3-подвеска передняя;4-приёмно-питающее устройство; 5-секция аспирационная;
6-регулятор расхода воздуха; 7-аспирационный патрубок; 8-подвеска задняя; 9-камера сходов; 10-патрубок выпуска проходовых фракций; 11-сборник; 12-ситовая рамка; 13-очиститель сит; 14-салазки.
Рис. 13.10 – Схема ситовеечной машины.
![]() |
Проходовые фракции поступают в сборник 11, а сходовые - в камеру сходов 9, где формируются в соответствии с технологической схемой и выводятся из машины.
Для нормальной эксплуатации ситовеечной машины необходимо выполнять ряд правил и учитывать некоторые особенности:
а) следить за равномерностью распределения продукта по ширине сита; при нарушении равномерности большая часть воздуха будет проходить через оголённые места; регулирование равномерности загрузки осуществляют клапанным устройством и длиной подвесок;
б) не допускать порывов сита; последние должны быть туго натянуты на рамки, а ситовые рамки должны плотно прилегать к корпусу и не иметь “порогов” между собой;
в) щётки - очистители должны свободно перемещаться под ситами и обеспечивать их надёжную очистку;
г) не допускать излишних присосов; герметичность устройств, находящихся под разряжением, должна быть обеспечена;
д) угол направления и амплитуда колебаний регулируют соответственно передними, задними подвесками и массой грузов - дебалансов;
е) изменение расхода и скорости воздуха осуществляется дроссельной заслонкой, а в каждой секции - с помощью двух горизонтальных решёток, нижняя из которых имеет возможность двигаться;
ж) частоту колебаний можно изменить путём замены шкива на электродвигателе.
Рис.10.2 - Схема сепаратора А1-БИС.
Исходная смесь через патрубок 2 попадает на сортировочное сито 3, на котором отделяются крупные примеси. Последние выводятся из сепаратора через лоток 14. Проход с сортировочного сита попадает на подсевное сито 16, на котором проходом отделяется мелкая примесь. Она вследствие вибраций ситового кузова направляется по поддону 18 в выпускной патрубок15. Очищенное зерно с подсевного сита попадает на вибролоток 12, где оно предварительно расслаивается по плотности (лёгкие частицы «всплывают» вверх) и направляются в воздушный канал. Процесс отделения лёгких примесей осуществляется как в пневмосепараторе Р3-БАБ, поскольку конструкция пневмосепарирующих элементов сепаратора А1-БИС представляет собой воздушный сепаратор Р3-БАБ.
Привод ситового кузова сепаратора осуществляется от инерционного колебателя 17, включающего в себя: электродвигатель, ременную передачу и шкив с валом, закреплённые в подшипниковом узле ситового кузова. При этом груз - дебаланс непосредственно закреплён на шкиве ременной передачи.
Сита очищаются с помощью инерционного шарикового очистителя 4. Ситовой кузов соединён с корпусом 1 подвесками 19. Аспирация сепаратора осуществляется через аспирационный патрубок 6. Для уменьшения вероятности попадания зерна в крупную фракцию (в лоток 14) служит фартук 5.
Особенности конструкции и эксплуатации
сепараторов А1- БИС и А1- БЛС
Отличительными особенностями сепараторов А1- БИС и А1- БЛС являются:
- отсутствие осадочных камер, что позволяет уменьшить их габариты и массу;
- использование регулируемой перегородки 9 (рис. 10.2), с помощью которой возможно изменять скорость воздуха в пневмосепарационном канале, а значит и качество пневмосепарирования;
- закрепление сит к ситовому кузову осуществлено с помощью эксцентриковых зажимных устройств, что обеспечивает простоту и удобство в обслуживании;
- применение гнутых тонкостенных профилей позволяет снизить массу сепаратора;
- для ограничения амплитуды колебаний в периоды пуска и остановки предусмотрены резиновые амортизаторы;
- использование подсветки в пневмоканале и смотрового окна
|
|
Механическое удерживание земляных масс: Механическое удерживание земляных масс на склоне обеспечивают контрфорсными сооружениями различных конструкций...
Двойное оплодотворение у цветковых растений: Оплодотворение - это процесс слияния мужской и женской половых клеток с образованием зиготы...
Адаптации растений и животных к жизни в горах: Большое значение для жизни организмов в горах имеют степень расчленения, крутизна и экспозиционные различия склонов...
Биохимия спиртового брожения: Основу технологии получения пива составляет спиртовое брожение, - при котором сахар превращается...
© cyberpedia.su 2017-2024 - Не является автором материалов. Исключительное право сохранено за автором текста.
Если вы не хотите, чтобы данный материал был у нас на сайте, перейдите по ссылке: Нарушение авторских прав. Мы поможем в написании вашей работы!