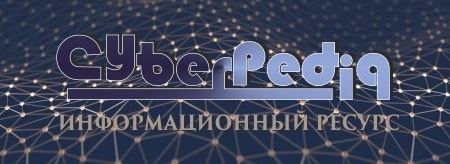
Двойное оплодотворение у цветковых растений: Оплодотворение - это процесс слияния мужской и женской половых клеток с образованием зиготы...
Историки об Елизавете Петровне: Елизавета попала между двумя встречными культурными течениями, воспитывалась среди новых европейских веяний и преданий...
Топ:
Оснащения врачебно-сестринской бригады.
Методика измерений сопротивления растеканию тока анодного заземления: Анодный заземлитель (анод) – проводник, погруженный в электролитическую среду (грунт, раствор электролита) и подключенный к положительному...
Процедура выполнения команд. Рабочий цикл процессора: Функционирование процессора в основном состоит из повторяющихся рабочих циклов, каждый из которых соответствует...
Интересное:
Инженерная защита территорий, зданий и сооружений от опасных геологических процессов: Изучение оползневых явлений, оценка устойчивости склонов и проектирование противооползневых сооружений — актуальнейшие задачи, стоящие перед отечественными...
Средства для ингаляционного наркоза: Наркоз наступает в результате вдыхания (ингаляции) средств, которое осуществляют или с помощью маски...
Берегоукрепление оползневых склонов: На прибрежных склонах основной причиной развития оползневых процессов является подмыв водами рек естественных склонов...
Дисциплины:
![]() |
![]() |
5.00
из
|
Заказать работу |
|
|
Потребляемую пусковую мощность электродвигателя привода винтового компрессора понижают путем установки золотника регулятора холодопроизводительности в положение минимальной холодопроизводительности.
При отсутствии байпасного клапана и регулятора мощности пуск ротационного компрессора осуществляют с закрытым всасывающим клапаном.
Во избежание аварии время работы маслозаполненных винтовых и ротационных компрессоров с закрытыми всасывающими клапанами не должно превышать 30…60с.
После пуска винтового насоса золотник регулятора холодильной мощности перемещается в положение номинальной мощности постепенно.
Всасывающий клапан также открывается постепенно, во избежание гидравлического удара. Влажный ход винтового компрессора не вызывает классический гидравлический удар, однако он не желателен из-за повышения потребляемой мощности и ухудшения условий смазки, вызывающих интенсивный износ опорных и упорных подшипников, а также сальниковых уплотнений компрессора.
Величину потребляемой мощности электродвигателя при пуске ротационного и винтового компрессоров определяют по показаниям амперметра.
Последовательность пуска ротационного компрессора такая же, как у одноступенчатого поршневого компрессора без байпасного клапана, всасывающий клапан открывается только после установления необходимой подачи масла для компрессоров с лубрикаторной смазкой или циркуляции масла для компрессоров с циркуляционной системой смазки. За циркуляцией масла наблюдают через смотровое стекло на напорном масляном трубопроводе. Пуск винтового компрессора осуществляют следующим образом:
— золотник регулятора производительности устанавливают на минимальное значение (положение);
|
— открывают нагнетательный клапан, приоткрывают всасывающий клапан компрессора на 1,5…2 оборота и включают электродвигатель привода масляного насоса;
— пускают электродвигатель привода компрессора, при этом включается привод встроенного в компрессор масляного насоса;
— медленно открывают всасывающий клапан;
— постепенно перемещая золотник регулятора холодопроизводительности, повышают холодопроизводительность компрессора до 100% и наблюдают за показаниями амперметра.
После прогрева маслоотделителя (примерно через 10…15 минут) и выпаривания из него жидкого хладагента открывают клапан возврата масла в картер компрессора, после этого вводят маслоотделитель в работу.
При пуске поршневых, ротационных и винтовых компрессоров возможны следующие неисправности:
— отсутствие давления масла в масляной системе;
— чрезмерное повышение давления нагнетания (силы тока);
— появление посторонних шумов, резких ударов;
— утечка масла через сальник (допускается утечка не более шести капель в минуту);
— резкое снижение уровня масла в картере или маслоохладителе;
— повышенный нагрев цилиндров, подшипников, сальников;
— отсутствие протока охлаждающей воды через полости охлаждения цилиндров.
При обнаружении любой из них компрессор останавливают. Повторный пуск компрессора производят только после выявления и устранения неисправности. Охлаждающую воду в полость охлаждения цилиндров компрессора после устранения неисправности можно подавать только после их естественного охлаждения во избежание резкого перепада температур и возможной аварии компрессора из-за термических напряжений.
3.5. Пуск циркуляционного насоса хладагента
Осуществляют после охлаждения его до температуры хладагента в циркуляционном ресивере. При наличии байпаса приоткрывают его клапан и запускают насос, после установления потока жидкого хладагента, приоткрывают нагнетательный клапан насоса и регулируют необходимую разность давлений нагнетания и всасывания.
|
При отсутствии байпаса запуск насоса производят с приоткрытым нагнетательным клапаном. При установившемся режиме работы насоса разность давлений нагнетания и всасывания достигают регулировкой открытия нагнетательного клапана. При понижении разности давлений нагнетания и всасывания увеличивается подача насоса и растёт потребляемая мощность его электродвигателя. Однако равные показания мановакуумметра на всасывании и манометра на нагнетании свидетельствуют о прекращении подачи жидкости насосом. Работу насоса контролируют по показаниям манометра, мановакуумметра, амперметра и уровню жидкого хладагента в циркуляционном ресивере. При появлении дефектов в работе насоса (посторонние шумы, прекращение движения жидкости, чрезмерный нагрев) его останавливают, выявляют причину неполадки и устраняют её.
3.6. П ризнаки нормальной и оптимальной работы СХУ
Нормальной называется такая работа СХУ, которая обеспечивает поддержание требуемых температурных условий в охлаждаемых помещениях.
Оптимальный режим работы СХУ – это наиболее экономичный и безопасный режим работы, который определяется перепадом температур в теплообменных аппаратах и температурным режимом работы компрессора. Общие признаки оптимальной работы СХУ:
— отсутствие пропусков хладагента через сальники запорной и регулировочной арматуры, фланцевые соединения, сальники насосов хладагента;
— отсутствие пропусков рассола и воды из рассольной и водяной систем;
— наличие равномерного слоя инея на батареях охлаждающих приборов, расположенных в охлаждаемых помещениях.
При нормальной работе КИП их стрелки неподвижны или колеблются незначительно. Нагрев трущихся частей компрессоров, насосов и вентиляторов не превышает температуру в рефрижераторном помещении более чем на 30ºС, а максимальный нагрев не должен быть больше 60…70ºС.
Мощность, потребляемая компрессором и определяемая по показанию амперметра, должна соответствовать спецификационной для данного режима работы компрессора. Мощность, потребляемая рассольным и водяным насосами, не должна превышать максимально допустимую. Уровень жидкого хладагента в:
– циркуляционном ресивере
|
– кожухотрубном испарителе
– промсосуде
– линейном ресивере (или ресиверной части конденсатора),
при установившемся режиме работы установки, не изменяется.
О нормальной работе СХУ судят по показаниям КИП и температурным перепадам в теплообменных аппаратах. Для аммиачных компрессоров признаки нормальной работы следующие:
– на 5…15ºС;
– перегрев паров аммиака, выходящих из промсосуда до ступени высокого давления находится в пределах 5…7ºС;
– в насосно-циркуляционной схеме подачи хладагента в приборы охлаждения перегрев паров на всасывании в компрессор составляет 2…6ºС за счет внешних теплопритоков к всасывающему трубопроводу от ресивера до компрессора;
– при расположении змеевика в сухопарнике кожухотрубного испарителя общий нагрев паров на всасывании в ступень низкого давления составляет 20…25ºС.
В испарителях хладоновых систем для обеспечения нормального возврата масла поддерживается минимально возможный перегрев выходящих паров. Так в кожухотрубных испарителях перегрев паров в установках, работающих
– на R12 составляет 1…2ºС
– на R22 — 5…10ºС.
В воздухоохладителях пар хладагентов R12 и R22 перегревают на 3…5ºС. Общий перегрев паров R12 на всасывании в компрессор с учетом перегрева в регенеративном теплообменнике поддерживается в пределах 10…30ºС. Для R22 при аналогичных условиях перегрев составляет 10…20ºС. Температура паров, нагнетаемых компрессором, должна соответствовать температуре конца сжатия, определённой по h, p диагpамме.
Превышение фактической температуры, измеренной термометром, над теоретической, определенной по таблицам и/или диаграммам, для поршневых компрессоров и ротационных (с лубрикаторной смазкой) допускается не более 25ºС.
Фактическая температура нагнетания винтового и ротационного компрессоров должна быть ниже теоретической на 20…60ºС в зависимости от температуры и массы впрыскиваемого масла.
В зависимости от марки компрессора максимально допустимая температура нагнетания составляет для
– поршневых компрессоров (работающих на R717 или R22) от 120 до 160ºС
– винтовых компрессоров (работающих на R717) от 80 до 105ºС
|
– винтовых компрессоров (работающих на хладоне) от 80 до 90ºС
– ротационных компрессоров от 100 до 130ºС.
В сальниковых компрессорах допускается пропуск масла через сальник компрессора не более одной капли за 2 минуты.
Признаки нормальной работы системы охлаждающей воды:
– нагрев воды в конденсаторе составляет 1…3ºС;
– температура конденсации хладагента должна быть больше средней температуры входящей и выходящей воды из конденсатора на 5…7ºС;
– при наличии водорегулирующего клапана разность температур входящей и выходящей из конденсатора воды зависит от поддерживаемого давления конденсации.
В воздушных конденсаторах нагрев воздуха составляет 8…12ºС, а его средняя температура ниже температуры конденсации на 3…8ºС. Водяной насос (вентилятор) обеспечивает необходимую подачу и напор воды (воздуха) в системе.
Рассольная система имеет следующие признаки нормальной работы:
– охлаждение рассола в испарителе составляет 2…3ºС;
– температура кипения хладагента ниже средней температуры рассола на 5…7ºС;
– рассольный насос обеспечивает необходимую подачу и напор рассола в системе;
– достаточен уровень рассола в расширительном бачке;
– отсутствует воздух в системах.
Воздушная система охлаждения имеет следующие признаки нормальной работы:
– температура кипения хладагента в воздухоохладителе на 7…10ºС ниже средней температуры воздуха в охлаждаемом помещении;
– температура рассола на входе в воздухоохладитель ниже средней температуры в охлаждаемом помещении на 7…10ºС;
– вентиляторы обеспечивают необходимую циркуляцию воздуха в охлаждаемом помещении;
– охлаждение воздуха в воздухоохладителе составляет 2…3ºС;
– шиберы находятся в положениях, обеспечивающих необходимый режим перевозки и хранения рефрижераторного груза.
Для циркуляционного насоса хладагента признаки нормальной работы следующие:
– насос работает устойчиво, срывов потока жидкости на всасывании не наблюдается;
– поддерживается необходимая разность давлений на всасывании и нагнетании;
– в смотровом стекле трубопровода подвода жидкого хладагента для смазки подшипников и охлаждения статора электродвигателя пузырьков пара не наблюдается.
Батарейная система охлаждения имеет следующие признаки нормальной работы:
– температура кипения хладагента в приборах охлаждения (или температура рассола на входе в приборы охлаждения) ниже средней температуры воздуха в рефрижераторном помещении на 10…12ºС (для ребристых или гладкотрубных батарей) или на 7…10ºС – для панельных;
– температура хладагента перед регулирующим клапаном должна быть на 1…3ºС выше температуры воды, выходящей из конденсатора и на 5…8ºС выше температуры хладагента в промсосуде;
|
– поверхности труб батарейной системы охлаждения должны иметь равномерное обмерзание.
При непосредственной системе охлаждения верхние ряды труб могут не обмерзать.
3.7. Техническое обслуживание СХУ
Техобслуживание холодильной установки включает:
– контроль работы холодильного оборудования;
– поддержание холодильной установки в надлежащем порядке и чистоте;
– обеспечение экономичной и безопасной работы СХУ. Все работы по техобслуживанию СХУ выполняет персонал, несущий вахту и действующий в соответствии с инструкциями по эксплуатации СХУ.
При ежедневном техобслуживании СХУ проверяют:
– отсутствие пропусков хладагента, масла, воды и рассола;
– исправность (плотность) предохранительных клапанов;
– рабочий уровень и давление хладагента в циркуляционном ресивере, испарителе и в промсосуде;
– уровень рассола в расширительном баке;
– визуальным осмотром проверяют исправность:
– оборудования СХУ;
– КИП;
– приборов автоматики.
– отсутствие вибрации из-за ослабления фундаментных болтов или центровки валов;
– состояние крепления оборудования и трубопроводов;
– исправность вентиляционных систем;
– целостность защитных и изоляционных покрытий.
При техобслуживании СХУ:
– протирают указательные и смотровые стекла на компрессорах, аппаратах и приборах автоматики;
– очищают таблички и надписи на оборудовании;
– на ощупь определяют нагрев узлов трения: допускается до 50…60ºС (такую температуру рука человека выдерживает примерно 10 секунд).
Обязательным для СХУ являются техобслуживания, проводимые согласно графика с целью контроля технического состояния холодильной установки и предупреждения возможных отказов в работе. Периодические техобслуживания включают также работы по устранению ранее выявленных неисправностей. Например, очистку фильтров рассольной, водяной, масляной систем и системы хладагента производят через 10 суток; более частая очистка возможна при явных признаках их загрязнения. В первый месяц работы новой СХУ или после её ремонта очистку фильтров производят через 100 часов их работы. Техобслуживание системы хладагента состоит в выявлении и устранении неплотностей, а также в проверке состояния влагопоглотителя в осушителе.
В аммиачных СХУ утечки определяют с помощью специальных химических индикаторов, или газоанализаторов. Специальным образом приготовленная индикаторная бумага в присутствии аммиака окрашивается в малиновый цвет. Места утечек в хладоновых установках определяют путем обмыливания, а также галоидными лампами или течеискателями. Масляные пятна и подтеки являются признаками утечки хладагента из системы.
Для обнаружения утечек хладагента наиболее часто применяют пропановые и спиртовые галоидные лампы. Принцип действия галоидных ламп заключается в том, что галоидные элементы (F, Cl), входящие в состав хладагента, в присутствии меди, раскаленной до температуры 660…700ºС, образуют соединения хлористого и фтористого водорода, которые окрашивают пламя лампы в зеленоватый цвет.
При концентрации хладона примерно 0,1 % цвет пламени становится темно-зеленым, а при концентрации 1 % – зелено-синим. Пропановая лампа реагирует на утечки, составляющие 5…7 грамм хладона в год.
Более надежными приборами для определения утечек хладона являются электронные галоидные течеискатели типов ВАГТИ – 3, ГТИ – 6, БГТИ – 5.
Принцип работы течеискателей основан на изменении ионной эмиссии раскаленной платиновой поверхности при наличии галоидов в соприкасающемся воздухе. Чувствительность ГТИ-6 составляет 0,2 грамма хладона в год. Перед использованием ламп и течеискателей помещение необходимо проветрить.
В систему хладагента холодильной установки, работающей на R22, при ее эксплуатации и ремонте, а также в аварийных ситуациях могут попасть:
– вода;
– воздух;
– механические загрязнения.
Вода попадает в систему хладагента при заполнении её недостаточно осушенным хладагентом, или при коррозионном разрушении трубок конденсаторов и маслоохладителей. При высоких температурах и каталитическом действии металлов образуются слабые кислоты и основания, которые вызывают коррозию деталей механизмов и трубопроводов. Продукты коррозии засоряют фильтры и отверстия дроссельных устройств. В дроссельных устройствах вода образует ледяные пробки.
Для удаления влаги устанавливают фильтры-осушители. Фильтры-осушители устанавливают также на линии заправки системы хладагентом. В некоторых осушителях имеются индикаторы влаги. В качестве сорбентов используются технический силикагель и синтетический цеолит. В процессе эксплуатации для исключения попадания влаги в систему необходимо:
– заправлять систему тщательно осушенным хладагентом;
– смазочное масло хранить в герметичных емкостях;
– проводить регулярный анализ масла на наличие в нем влаги.
Проверку влагопоглотителя (адсорбента) в осушительном патроне проводят в течение первых 2-х…3-х суток после монтажа или ремонта СХУ ежедневно. Силикагель, насыщенный влагой, тускнеет. При увеличении массы ≈ на 10 % силикагель заменяют или регенерируют (прокаливают) при температуре 140…170ºС. Перед заполнением осушительный патрон фильтра нагревают до 120…150ºС.
Цеолит также восстанавливают прокаливанием при температуре 450…500ºС в течение двух с половиной часов. Тщательно промытый спиртом, уайт-спиритом или бензином корпус осушительного патрона нагревают перед засыпкой цеолита до 150…200ºС.
Воздух, попавший в систему хладагента, собирается в конденсаторе или линейном ресивере. Присутствие воздуха в конденсаторе даже при небольшой концентрации (0,1…5 % по объему) снижает коэффициент теплопередачи «» и нивелирует положительный эффект от накатки трубок конденсатора. Поэтому в процессе эксплуатации СХУ следует своевременно удалять воздух из конденсаторов и ресиверов. Повышенная текучесть хладагентов R12 и R 22 предъявляет высокие требования к герметичности системы и аппаратов холодильной техники.
Для уменьшения расхода хладагентов при эксплуатации СХУ необходимо:
– обеспечивать защиту трубок конденсатора от коррозии;
– наносить защитные покрытия на эпоксидной основе на соединения трубопроводов из разнородных металлов, чтобы исключить попадание влаги в места их контакта;
– исключать использование разнородных металлов в соприкасающихся деталях;
– устанавливать для понижения вибрации дополнительные крепления трубопроводов и демпферные кольца на трубках КИП и приборах автоматики;
– так как R12 и R 22 при своем движении способны захватывать загрязнение (окалину, шлам, продукты коррозии), поэтому необходимо внутренние полости системы хладагента поддерживать в чистоте.
3.8. Регулирование режимов работы СХУ. Наблюдение за показаниями КИП
Каждая СХУ оборудуется необходимым набором КИП, за показаниями которых ведут непрерывное наблюдение для оценки работы:
– компрессоров;
– конденсаторов;
– испарителей;
– воздухоохладителей;
– насосов и др.
По показаниям манометров и мановакуумметров определяют значения давлений:
– всасывания и нагнетания компрессора;
– в системе смазки и в картере компрессора;
– кипения и конденсации;
– в промежуточном сосуде;
– всасывания и нагнетания циркуляционных насосов хладагента;
– рассольного насоса и охлаждающей воды.
При этом используются манометры и мановакуумметры, имеющие класс точности 1,5 или 2,5. Ежегодно и после каждого ремонта установки манометры проверяются Госконтрольной организацией (лабораторией). Один раз в полгода рабочие манометры проверяют по контрольному манометру.
Для измерения температуры используют жидкостно-стеклянные термометры, манометрические термометры, термометры сопротивления и двухшкальные манометры и мановакуумметры.
Во время работы СХУ ведут наблюдение за значениями температур:
– всасывания и нагнетания компрессоров;
– масла в системе смазки компрессора;
– кипения и конденсации.
При отсутствии двухшкальных приборов температуру определяют по таблицам насыщенных паров хладагента в зависимости от давления, измеренного манометром или мановакуумметром (с учетом атмосферного):
– жидкого хладагента перед регулирующим клапаном;
– воды на входе и выходе из конденсатора;
– рассола на входе и выходе из испарителя;
– хладагента в промежуточном сосуде;
– жидкого хладагента на входе и выходе из приборов охлаждения (при насосной схеме подачи хладагента в приборы охлаждения). По данным указателей уровня или визуально по смотровым стёклам контролируют уровни:
– масла в картере компрессора (маслоотделителе);
– жидкого хладагента в испарителе;
– жидкого хладагента циркуляционном, линейном и дренажном ресиверах;
– рассола в расширительном бачке.
Потребляемую мощность электродвигателей, используемых для привода компрессоров, насосов и вентиляторов определяют по показаниям амперметров.
3.9. О становка СХУ
Остановку СХУ осуществляют в такой последовательности:
– прекращают подачу жидкого хладагента в испаритель, циркуляционный ресивер, промсосуд и останавливают циркуляционный насос хладагента;
– компрессором отсасывают пары хладагента из испарителя до давления ниже атмосферного;
– останавливают:
– компрессор;
– вентиляторы;
– насосы (рассольные, циркуляционные).
– закрывают запорные клапаны на:
– системе хладагента;
– рассола;
– охлаждающей воды.
– снимают питание с отключенных механизмов, щитов, пультов.
Для остановки циркуляционного насоса хладагента необходимо отключить электродвигатель насоса, а затем закрыть нагнетательный клапан. Всасывающий клапан при отсутствии предохранительного клапана на насосе оставляют открытым. Таким образом, насос сообщается с циркуляционным ресивером и исключается повышение давления в насосе при его подогреве.
Остановку поршневого, винтового или ротационного компрессоров осуществляют следующим образом:
– устанавливают минимально возможную холодопроизводительность компрессора (для компрессоров с регулируемой подачей);
– закрывают всасывающий клапан компрессора;
– отключают электродвигатель привода компрессора;
– закрывают нагнетательный клапан компрессора (после прекращения вращения вала компрессора);
– закрывают клапан подачи воды на охлаждение компрессора, и/или хладагента на маслоохладитель;
– закрывают клапаны на трубопроводах спуска масла в картер, а также всасывающий и нагнетательный клапаны;
– в вахтенном журнале записывают время и причину остановки компрессора.
При остановке двухступенчатого компрессора сначала закрывают всасывающий клапан ступени низкого давления, а после снижения давления в промсосуде и картере компрессора высокого давления до 0,02 МПа (по манометру) закрывают всасывающий клапан ступени высокого давления. При остановке двухступенчатого агрегата, состоящего из двух одноступенчатых компрессоров, сначала останавливают компрессор низкого давления, а затем — компрессор высокого давления.
В картере остановленных на длительное время хладоновых компрессоров поддерживается давление 0,03…0,05 МПа (по манометру) во избежание насыщения масла парами хладагента. Пуск компрессора с маслом, насыщенным хладагентом, приводит к вспениванию масла и нарушению смазки компрессора.
При остановке холодильной установки с рассольной системой охлаждения закрывают клапан на трубопроводе подачи рассола в систему охлаждения (после испарителя) и оставляют открытым клапан на трубопроводе возврата рассола в испаритель. Это предотвращает нарушение плотности в рассольной системе (выдавливание прокладок, сальников и т. п.) при повышении давления в ней в результате расширения рассола при его отеплении.
При отрицательных температурах в рефрижераторном отделении после остановки СХУ спускают воду из систем охлаждения компрессоров, маслоохладителей, конденсаторов и другого оборудования.
3.10. Техобслуживание компрессоров
При обслуживании компрессоров наибольшее внимание следует уделять:
– температуре перегрева паров на всасывании в ступень низкого и высокого давления;
– не допускать влажного хода компрессора;
– контролировать температуру и давление после компрессора.
Оптимальный перегрев всасываемого пара вызывает сухой ход компрессора, при этом температуры крышек компрессора, нагнетательного патрубка и нагнетательного трубопровода примерно одинаковы. Всасывающий патрубок компрессора при ‹ 0ºС покрывается инеем.
При влажном ходе компрессора:
– отсутствует легкий стук клапанов;
– появляется иней на крышке компрессора;
– температура на нагнетательной стороне компрессора снижается;
– в прямоточном компрессоре инеем покрывается картер компрессора.
Влажный ход винтового компрессора не вызывает явного гидравлического удара, но отрицательно влияет на условия его работы.
При нормальной работе компрессора посторонний шум отсутствует, прослушивается только работа его клапанов. При резком повышении давления нагнетания или при внезапном появлении шума – компрессор необходимо быстро остановить. Посторонние шумы в компрессоре могут быть вызваны:
– увеличением зазора в подшипниках верхней или нижней головках шатуна или в коренных подшипниках коленвала;
– поломкой пластин, пружин клапанов;
– ослаблением буферных пружин ложных крышек.
При техобслуживании компрессора проверяют паровой фильтр на всасывающем коллекторе компрессора.
Признаки засорения фильтра компрессора:
– повышенное давление всасывания до фильтра и пониженное после фильтра;
– пониженное давление в картере компрессора;
– пониженное давление нагнетания.
В результате засорения фильтра подача компрессора уменьшается. Падение давления определяется с помощью мановакуумметров, установленных на всасывающей магистрали до фильтра и на картере компрессора.
Периодически проверяют срабатывание защитной автоматики:
– защиту компрессора по давлению нагнетания;
– защиту компрессора по температуре нагнетания;
– защиту компрессора по давлению масла в системе смазки.
Нормальная работа сальника компрессора характеризуется пропуском масла по валу не более 1 капли за 2 минуты. Пропуск хладагента через сальник компрессора и насоса хладагента устраняют сразу же после их обнаружения.
Плотность закрытия предохранительных и байпасных клапанов определяют по разности температур трубопроводов, соединяющих их с нагнетательной и всасывающей стороной компрессора.
Температура картера, сальника, блока цилиндров нормально работающего компрессора не должна превышать температуру воздуха в рефрижераторном помещении более чем на 25…30ºС.
Нормальная (надежная и безопасная) работа компрессора зависит от условий смазки трущихся пар и свойств масла. Применяемое масло должно обладать хорошими смазочными свойствами как при низкой, так и при высокой температуре (+120ºС). Температура помутнения масла (выпадения парафинов) должна быть значительно ниже температуры испарения. Для смазки компрессора используют специальные холодильные масла, указываемые в технической документации на холодильную установку.
При растворении хладагента в масле снижается его вязкость (смазочные свойства), что может привести к нарушению смазки трущихся поверхностей. Если масло гигроскопично, то влага, попадая с маслом на трущиеся пары, вызывает коррозию и возникновение густых масляных осадков в:
– колонках указателей уровня хладагента в ресиверах;
– фильтрах;
– дроссельных клапанах.
Длительное использование масла (без замены на свежее) приводит к появлению слоя темных смолянистых веществ на деталях сальника, регулятора подачи, разгрузочного поршня винтового компрессора, что нарушает нормальную работу этих узлов. Поэтому после 5…6 тыс. часов работы СХУ рекомендуется проводить лабораторный анализ масла на соответствие его физико-химических характеристик паспортным данным. Для каждого сорта масла имеются свои браковочные показатели:
– изменение вязкости;
– кислотное число;
– плотность при 20ºС;
– содержание механических примесей.
Отработавшее масло для экономии может быть использовано вторично в качестве добавки только после регенерации (очистки), но не более 30…40% к свежему маслу. Добавление регенерированного масла к свежему для смазки винтовых компрессоров не допускается.
Очистку масла осуществляют путем:
– отстоя;
– фильтрации;
– сепарации.
На сепарацию масло поступает только после отстоя и фильтрации. Для ускорения отстоя масло подогревают. Для фильтрации применяют фильтры грубой (металлические сетки) и тонкой (ткани, войлок, бумага) очистки. Сепарированием достигается очистка масла от воды и механических примесей.
Максимальная температура масла:
– в картере поршневого компрессора + 50ºС;
– после маслоохладителя винтового компрессора → 45…50ºС;
– после маслоохладителя ротационного компрессора→ 55ºС.
Количество масла в компрессоре поддерживается по указателю уровня. Уровень масла в фреоновом компрессоре может понизиться из-за переноса фреона в испарительную систему. Для возврата масла в картер компрессора увеличивают подачу хладагента в испаритель, создавая тем самым режим работы компрессора с минимальным перегревом. При угрозе гидравлического удара, прикрывают всасывающий клапан перед компрессором и регулирующий клапан подачи жидкости в испаритель. При стабилизации уровня масла в картере принудительный возврат масла из испарительной системы прекращают.
Давление масла должно превышать давление в картере поршневого компрессора или давление нагнетания винтовых или ротационных компрессоров на 0,08…0,6 МПа. Давление масла в поршневых компрессорах должно быть на 0,05…0,15 МПа больше давления всасывания.
Регулируют давление масла с помощью ручного перепускного клапана.
Работа масляной системы зависит от качества масла и степени загрязнения фильтров. Очистку и промывку фильтров выполняют при смене масла, которую производят при профилактическом техобслуживании СХУ:
– для поршневых и ротационных компрессоров через 1500…2000 часов;
– для винтовых – через 2500…5000 часов работы.
В начальный период работы СХУ и после её капитального ремонта смену масла производят через 200…500 часов работы до полной очистки системы.
Промывку фильтров и очистку масляных полостей производят чистым маслом. Элементы фильтров тонкой очистки заменяют. Для очистки фильтров применяют льняную ткань или кисти; хлопчатобумажная ткань или шерстяная ветошь могут засорить фильтр и нарушить работу системы смазки.
Профилактическое техобслуживание компрессоров включает:
– осмотр;
– промывку;
– очистку;
– регулировку;
– замену изношенных деталей;
– проверку крепежа:
-фундамента;
-соединительных муфт.
– проверку соосности электродвигателя и вала компрессора.
В винтовых компрессорах через каждые 2500 часов работы проверяют:
– величину осевого зазора спаренных радиально-упорных подшипников;
– осевое смещение роторов;
– касание поверхностей роторов и корпуса (это приводит к повышенному износу и заклиниванию ротора).
Плотность всасывающих и нагнетательных клапанов проверяют при пуске компрессора не реже одного раза в месяц. Исправность всасывающих клапанов определяют по отклонению стрелки при повороте вала компрессора вручную. О неплотности нагнетательных клапанов судят по тому, как быстро повышается давление в картере компрессора при закрытых запорных всасывающих и нагнетательных клапанах остановленного компрессора.
На неплотности всасывающих и нагнетательных клапанов указывает значительный нагрев цилиндровых крышек компрессора.
Предохранительные клапана компрессора проверяют не реже двух раз в год путем прикрытия нагнетательного запорного клапана.
В компрессорах, холодопроизводительность которых регулируется с помощью электромагнитных устройств, не реже одного раза в год проверяют оммичное сопротивление катушек и изоляции проводов, а также контактов.
3.11. Техобслуживание теплообменных аппаратов
Техобслуживание теплообменных аппаратов (конденсаторов, испарителей, воздухоохладителей, батарей) сводится к поддержанию их герметичности и эффективному использованию теплопередающих поверхностей.
Герметичность наружных поверхностей теплообменных аппаратов проверяют ежедневно, а внутренних (трубок и трубных решеток) – один раз в неделю.
Плотность аммиачного конденсатора проверяют путем анализа воды, выходящей из конденсатора: в пробу, взятую через 5…6 часов после вывода конденсатора из работы, добавляют несколько капель реактива Несслера
(). В присутствии аммиака проба окрашивается в желтый цвет, а при большой концентрации аммиака – выпадает красно-бурый осадок. Для обнаружения большой утечки аммиака может использоваться индикаторная бумага, помещаемая в пробу воды.
При обнаружении в воде аммиака – конденсатор отключают. Выпустив воду, снимают крышки и при помощи индикаторной бумаги уточняют места утечки аммиака. Причинами неплотности может быть нарушение герметичности развальцовки или прорыв 1…2 трубок из-за коррозийного и/или эрозийного их износа.
Наличие хладона в воде определяют следующим образом: из водяной полости конденсатора спускают частично воду, через воздуховыпускной кран вводят конец гибкого шланга галоидной лампы или щуп течеискателя, включают прибор. При обнаружении утечек, снимают крышки, протирают ветошью трубные доски и устанавливают места пропуска хладагента.
Проверку производят течеискателем или обмыливанием. При проверке герметичности трубок их закрывают с одной стороны резиновой пробкой. Трубка считается плотной, если мыльная пена по диаметру трубки не разрывается в течение одной минуты. Обнаруженные неплотности устраняют только после освобождения аппарата от хладагента.
Нарушение развальцовки трубок устраняют их подвальцовкой, а вышедшие из строя трубки заменяют новыми. Глушение трубок конусными пробками допускается как исключение только в рейсе (до 10% теплообменных трубок).
В процессе эксплуатации в конденсаторе поддерживают минимальный уровень жидкого хладагента. Техобслуживание конденсатора сводится к поддержанию постоянным давления p k= f (t k) путем регулирования подачи охлаждающей воды в конденсатор. Увеличение подачи воды в конденсатор уменьшает значение p k, но вызывает ускоренный износ трубок и трубных решеток.
Как правило, при движении судна температура забортной воды все время меняется, что приводит к изменению давления конденсации p k= f (t k), а это отрицательно влияет на работу холодильной установки:
– уменьшение p k вызывает уменьшение разности давлений конденсации и испарения: Δ p = p k – p и, что приводит к понижению подачи хладагента в испаритель через ТРВ. Постоянство давления конденсации p k= f (t k) поддерживают, регулируя подачу воды в конденсатор.
Нижние трубки конденсатора, утопленные в жидком хладагенте, в теплообмене не участвуют, что вызывает повышение p k. Давление конденсации повышается также при загрязнении теплообменной поверхности конденсатора и при наличии в системе хладагента воздуха.
Трубки конденсатора со стороны забортной воды загрязняются минеральными отложениями (водяным камнем), биологическими (ракушками), механическими (песком) загрязнениями и ржавчиной, а со стороны хладагента замасливаются.
Загрязненные трубки не реже одного раза в течение шести месяцев очищают специальными шарошками, вводимыми в трубки с помощью гибкого вала с электрическим или пневматическим приводом, а затем промывают водой. Медные трубки очищают мягкими резиновыми пробками. Наружную поверхность трубок (внутреннюю поверхность конденсатора – межтрубное пространство) очищают путем продувки сжатым воздухом.
Повышению давления кон
|
|
Адаптации растений и животных к жизни в горах: Большое значение для жизни организмов в горах имеют степень расчленения, крутизна и экспозиционные различия склонов...
Опора деревянной одностоечной и способы укрепление угловых опор: Опоры ВЛ - конструкции, предназначенные для поддерживания проводов на необходимой высоте над землей, водой...
Состав сооружений: решетки и песколовки: Решетки – это первое устройство в схеме очистных сооружений. Они представляют...
Индивидуальные и групповые автопоилки: для животных. Схемы и конструкции...
© cyberpedia.su 2017-2024 - Не является автором материалов. Исключительное право сохранено за автором текста.
Если вы не хотите, чтобы данный материал был у нас на сайте, перейдите по ссылке: Нарушение авторских прав. Мы поможем в написании вашей работы!