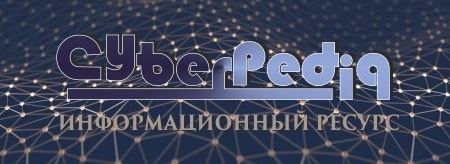
Общие условия выбора системы дренажа: Система дренажа выбирается в зависимости от характера защищаемого...
Эмиссия газов от очистных сооружений канализации: В последние годы внимание мирового сообщества сосредоточено на экологических проблемах...
Топ:
Генеалогическое древо Султанов Османской империи: Османские правители, вначале, будучи еще бейлербеями Анатолии, женились на дочерях византийских императоров...
Когда производится ограждение поезда, остановившегося на перегоне: Во всех случаях немедленно должно быть ограждено место препятствия для движения поездов на смежном пути двухпутного...
Интересное:
Уполаживание и террасирование склонов: Если глубина оврага более 5 м необходимо устройство берм. Варианты использования оврагов для градостроительных целей...
Распространение рака на другие отдаленные от желудка органы: Характерных симптомов рака желудка не существует. Выраженные симптомы появляются, когда опухоль...
Средства для ингаляционного наркоза: Наркоз наступает в результате вдыхания (ингаляции) средств, которое осуществляют или с помощью маски...
Дисциплины:
![]() |
![]() |
5.00
из
|
Заказать работу |
|
|
Для обеспечения высоких темпов добычи нефти и увеличения нефтеотдачи пласта широко применяют методы поддержания пластового давления путем нагнетания в пласт воды, воздуха или газа. Для закачки воды в пласт строят кустовые насосные станции, оборудованные мощными центробежными насосами. Для закачки в пласт воздуха или газа с целью поддержания пластового давления, а также в случае компрессорной эксплуатации нефтяных скважин, строят специальные компрессорные станции. Монтаж насосов и компрессоров является очень ответственной работой и поэтому его следует выполнять высококвалифицированными специалистами.
Общие технические положения и требования к монтажу нефтепромысловых насосов и компрессоров.
При монтажных работах должно быть обеспечено:
1) получение установленной технической характеристики;
2) отсутствие перекосов, перегревов, стуков, вибраций и сдвигов с фундамента;
3) надежность сальниковых уплотнений, охлаждения и точной регулировки;
4)выполнение требований по противопожарной технике и охране труда.
Содержание и последовательность операций по монтажу насосов и компрессоров различных типоразмеров изложены в заводских инструкциях, направляемых обычцо заводами-изготовителями вместе с машинами. В особых случаях (новизна машины, сложность и особая ответственность) заводы-изготовители руководят монтажом на месте установки машины. Поэтому достаточно изложить общие положения и рекомендации при подготовке и монтаже насосов и компрессоров.
Здания насосных и компрессорных станций следует проектировать в сборном железобетоне индустриального изготовления одноэтажными, бесфонарными, как правило, прямоугольной формы. Применение фонарей над отдельными зданиями насосных и компрессорных станций допускается только при соответствующем технико-экономическом обосновании.
|
Для монтажа и ремонта оборудования не следует применять мостовые краны, лучше заменять их наземными подъемно-транспортными средствами и подвесными такелажными приспособлениями. Грузоподъемность подъемно-транспортных средств следует определять по наиболее тяжелой сменной детали машины. В районах с расчетной наружной температурой ниже —5° С в зданиях следует располагать только компрессоры и насосы, не приспособленные для работы в условиях отрицательных температур, а также перекачивающие застывающие нефтепродукты и воду. Для насосов с приводом, приспособленных для работы при расчетной наружной температуре —40°С и работающих с перекачивающими незастывающими жидкостями, необходимо их только частично укрыть. При устройстве приточной механической вентиляции в насосных и компрессорных, воздух следует подавать в рабочую зону, а забирать его в местах, наиболее удаленных и защищенных от выброса вредных газов, паров и пыли.
В качестве источника теплоснабжения целесообразно в первую очередь использовать отходящее тепло производства или при его отсутствии применять перегретую воду или пар.
В производственных помещениях с автоматизированным технологическим процессом следует принимать внутреннюю температуру +5 С, а при периодическом обслуживании +10° С.
Подготовка к монтажу насосов и компрессоров включает в себя обеспечение транспортировки и складирование прибывшего оборудования, подготовку монтажных механизмов и устройств, мероприятия по технике безопасности и охране труда рабочих, проверку комплектности машины, выяснение типа и характеристики присоединительных фланцев машины, выявление возможных повреждений машины в процессе транспортировки.
Отдельный этап подготовки — сооружение фундаментов под монтируемые машины — рекомендуется завершить до окончания строительства здания или перекрытий. Это позволит использовать гусеничные самоходные краны для затаскивания и установки машин через раскрытое перекрытие здания.
|
Основные положения по производству монтажа насосов и компрессоров
Монтаж центробежных насосов ведется в описываемой ниже последовательности:
1) приемка под монтаж сооруженных фундаментов;
2) приемка под монтаж насосов и доставка их к месту установки;
3) установка монтажных механизмов и устройств;
4) подтаскивание, подъем и установка насоса на фундамент с последующей их выверкой и закреплением;
5) подливка цементным раствором фундаментных болтов и рамы насоса;
6) уборка монтажных механизмов и устройств;
7) разборка и сборка машины для проверки уплотняющих устройств, подшипников, регулировка системы смазки и охлаждения, точная центровка насоса и электродвигателя;
8) проверка правильности монтажа, испытание и обкатка установленного насоса.
Монтаж поршневых и плунжерных насосов отличается тем, что проводится разборка и сборка машины для проверки поршневых колец, регулировка вредного пространства, проверка и регулировка клапанов и системы смазки, набивка и регулировка сальников.
Вертикальный электроприводной компрессор монтируют в такой последовательности:
1) приемка под монтаж сооруженных фундаментов;
2) приемка под монтаж компрессора и доставка его к месту установки;
3) установка монтажных механизмов и устройств;
4) подтаскивание, подъем и установка компрессора на фундамент с последующей его выверкой и закреплением;
5) подливка цементным раствором фундаментных болтов и рамы компрессора;
6) уборка монтажных механизмов и устройств;
7) разборка и сборка машины для проверки, пригонки крейцкопфа к параллелям, а также пригонка крейцкопфного подшипника, сборка холодильников, проверка горизонтальности коленчатого вала с шабровкой вкладышей коренных и шатунных подшипников, проверка перпендикулярности осей шатуна и коленчатого вала и параллельности осей мотылевой и крейцкопфной головок шатуна, промывка керосином и смазка маслом шейки вала и вклады-
ей подшипников, монтаж масляного насоса, надевание маховика на вал и установка выносного подшипника;
8) проверка правильности монтажа, испытание и обкатка установленного компрессора.
|
Газомотокомпрессор монтируют в такой же последовательности. Монтаж ведут согласно заводской инструкции.
Как видно из изложенного, монтаж насосов и компрессоров имеет много общих элементов.
При приемке под монтаж сооруженных фундаментов проверяют соответствие выполненных фундаментов чертежам. Для приемки и доставки насосов и компрессоров на монтажный участок используют обычно автотранспорт. Содержание работ по установке монтажных механизмов и устройств зависит ют габаритных размеров и массы машин, а также от конкретных условий монтажной площадки (высота фундамента, трасса подтаскивания, возможность использования передвижных кранов и др.). Так, для затаскивания и установки машины на фундамент используют лебедки и полиспасты, передвижные краны, мачты, треноги и козлы, домкраты и наклонные площадки.
Смонтированные на фундаменте машины необходимо проверить в поперечном и продольном направлениях на горизонтальность установки, и, если необходимо, под станину рядом с фундаментными болтами подбить для выравнивания стальные клинья.
Подливка цементным раствором фундаментных болтов и рамы машины состоит в сборке опалубки, приготовлении раствора и его заливке под раму. Рекомендуется в процессе заливки все время проталкивать раствор под раму; заливка считается законченной только тогда, когда раствор появится со всех Сторон рамы. После твердения цемента, повторной проверки горизонтальности машины и окончательной подтяжки фундаментных болтов убирают монтажные механизмы и устройства и приступают к монтажу насосов или компрессоров согласно инструкции завода-изготовителя. Последняя операция монтажа — проверка его правильности, проведение испытаний и обкатка установленной машины. Обычно содержание, длительность и характер испытания и обкатки указываются в инструкции завода-изготовителя.
В настоящее время все больше применяют крупноблочный метод сооружения насосных и компрессорных станций, обеспечивающий значительное повышение качества и темпов строительства.
Монтаж оборудования для насосной эксплуатации нефтяных скважин
|
Для извлечения нефти из скважин при насосной эксплуатации чаще всего применяют:
1) поршневые глубинные насосы;
2) погружные центробежные насосы.
Поршневые глубинные насосы бывают двух разновидностей: трубные и вставные.
Цилиндр трубных насосов спускают в скважину на насосно-компрессорных трубах, продолжением которых он является. После этого на штангах спускают клапаны и плунжер насоса. Поэтому для подъема цилиндра трубного насоса из скважины приходится сперва поднять штоки с плунжером, клапанами и потом насосные трубы. Это занимает много времени. При использовании вставных насосов их опускают и извлекают на колонне штанг при стационарно подвешенных в скважине трубах, благодаря чему значительно сокращается время на смену насоса.
Вставной насос в скважину опускают в следующем порядке. Сперва спускают колонну насосных труб, на конце которой установлены замковая опора (рис.55) состоящая из переводника 1, кольца 2 и пружинного замка 3. Пружинный замок 3 представляет собой полый усеченный конус, имеющий в нижней части систему разрезов, благодаря которым он пружинит. Переводник 1 имеет в вержней части резьбу под насосно-компрессорную трубу, на которой замковая опора спускается в скважину. К нижней части замковой опоры присоединена рубашка 4 насоса с направляющей муфтой на конце, к которой, в свою очередь, можно присоединять различные защитные устройства (фильтры, сетки и др.). Затем в спущенные трубы спускают на штангах насос в собранном виде. Дойдя до пружинного замка, насос раздвигает его и проходит вниз до тех пор, пока пружина замка не зайдет за буртик упорного ниппеля, обеспечив тем самым прочное закрепление насоса. Закрепленный в замковой опоре вставной насос работает, как трубный насос.
Для приведения в движение плунжера глубинного насоса над устьем скважины устанавливают станок-качалку.
Станок-качалка является балансирным приводом глубиннонасосной установки, который преобразует вращательное движение вала двигателя в вертикальное возвратно-поступательное движение точки подвеса штанг. На нефтепромыслах эксплуатируют балансирные станки-качалки нескольких типов: так называемого нормального ряда (СКН), снабженные подшипниками качения, тормозом и роторным или комбинированным противовесом, приводом от электродвигателя при помощи клиноременной передачи, зубчатым редуктором и кривошипно-шатунным механизмом.
Станок-качалка СКНЗ-915 нормального ряда (рис. 56) состоит из.че-тырехопорной стойки 5, соединенной с рамой балансира 1, несущей набор грузовых плит 2. Траверса 4, состоящая из двух швеллеров, является соединительным звеном между редуктором 9 и балансиром 1; соединяется при помощи подвеса 3 и шатунно-
|
Рис. 55. Замковая опора насоса НГВ-1 кривошипных механизмов 6.
Кривошипы 8, закрепленные на ведомом валу редуктора 9, кроме шпоночных соединений дифференциальными стяжками 10 несут на себе по два перемещающихся дополнительных уравновешивающих груза 7. Таким образом, станок-качалка обеспечивается балансирным и роторным уравновешиванием. Тормоз 12 обеспечивает фиксацию положения балансира, а клиноременная передача 11 — передачу вращения вала электродвигателя 13 на редуктор 9. Остальные станки-качалки нормального ряда СКН2-615, СКН5-1812, СКН10-2165, СКН10-3012 отличаются от рассмотренного СКНЗ-915 размерами, длиной хода головки балансира, величиной
Рис. 56. Станок-качалка СКНЗ-915 максимальной нагрузки на головку балансира, мощностью электродвигателя, числом качаний в минуту и т. д.
Монтаж станка-качалки начинается с подготовки и планировки площадки и рытья котлована под фундамент.
Фундамент под станок-качалку состоит из двух частей: подземной, например, бутовой кладки и наземной (цокольной) - бутобетона, изготовляемого на месте, или бетонных блоков (что предпочтительнее), выполняемых в заводских условиях и соединяемых на фундаменте при помощи болтов.
По окончании сооружения фундамента начинается монтаж станка-качалки, который поступает на монтажную площадку в разобранном виде (кроме станка СКН-2, доставляемого в собранном виде), что облегчает его транспортировку на специальном лафете или грузовой платформе.
Разгружаемые части станка-качалки необходимо располагать на площадке с учетом последовательности его монтажа. Так, раму с редуктором укладывают возможно ближе к фундаменту. Значительно облегчает и ускоряет монтаж применение передвижных грузоподъемных кранов (автомобильных, тракторных и др.).
Для подтаскивания рамы на фундамент можно использовать также катки, которые предпочтительнее перекатывать по деревянному настилу. Раму, доставленную и установленную на фундаменте, проверяют при помощи уровня на горизонтальность установки в продольном и поперечном направлениях, при этом, если необходимо, под основание подкладывают металлические клинья. Стойки станка-качалки устанавливают на раму передвижным краном или при помощи каната, который пропускают через кронблок вышки или мачты и наматывают на барабан трактора-подъемника. Установленную стойку прикрепляют к раме болтами; горизонтальность положения ее верхней плиты проверяют в двух взаимно-перпендикулярных направлениях. Затем поднимают балансир и устанавливают его так, чтобы совпали болтовые отверстия корпусов подшипников балансирного вала с соответствующими отверстиями на плите опорной стойки. После этого подшипники прикрепляют к плите болтами и гайками. Правильность положения балансира относительно центра устья скважины определяют при помощи отвеса, прикрепленного к центру траверсы подвески. Если отвес не совпадает с центром скважины, то следует перемещать балансир до соответствующего положения. После этого его закрепляют скобами и болтами.
Далее при помощи серьги поперечную траверсу с двумя шатунами прикрепляют к хвосту балансира, собирают тормоз, устанавливают кривошипы в горизонтальное положение и надежно закрепляют на них роторные противовесы. При помощи кривошипных пальцев и гаек нижние головки шатунов присоединяют к кривошипам. На этом монтаж станка-качалки заканчивается.
Затем еще раз проверяют правильность установки станка-качалки, подливают цементный раствор под раму, а после его затвердения крепят гайками и контргайками фундаментные болты. Собранный станок-качалку оснащают металлической лестницей с перилами и металлической площадкой обкатывают и сдают персоналу промысла. В настоящее время широко применяют погружные центробежные электронасосы (ЭЦН).
Выбор типа насоса определяется характеристикой скважины и является задачей технологов. Задача механиков — правильно смонтировать насосную установку, наладить ее и обеспечить нормальную эксплуатацию в заданном технологами режиме. Все эти элементы установки доставляют на место эксплуатации раздельно и монтируют непосредственно на скважине. Для монтажа насосной установки применяют подъемник с вышкой или мачтой.
При монтаже электродвигатель подвешивают на специальном элеваторе над скважиной, подсоединяют кабель и прокручивают двигатель на холостом ходу, проверяя качество его работы и нужное направление вращения. Попутно размечают концы кабеля во избежание ошибки в направлении вращения вала насоса после монтажа. Затем электродвигатель устанавливают протектор и заполняют систему маловязким маслом, необходимым для защиты электродвигателя от попадания перекачиваемой жидкости. Электродвигатель с протектором опускают в скважину и устанавливают на фланце обсадной колонны на специальном хомуте-элеваторе. Затем устанавливают и закрепляют на протекторе насос. В таком виде агрегат готов к спуску в скважину.
Особое внимание при монтаже следует обратить на прочность и плотность всех соединений (прокладок, уплотнительных колец). Герметичность сборки агрегата проверяют его опрессовкой маловязким маслом при давлении 4 кгс/см2, нагнетаемым через обратный клапан в протекторе или в электродвигателе. После опрессовки важно выпустить из протектора часть масла (300—700 см3) в расчете на его расширение при нагреве во время работы агрегата (возможен нагрев до 100° С).
Очень важно обеспечить надежное соединение питающего кабеля с вводом в электродвигатель.
Из характеристик насосов известно, что центробежные насосы должны пускаться в ход при максимальном давлении на нагнетательной линии. Тогда мощность, затрачиваемая на запуск, будет минимальной. Для этого колонна насосных труб должна быть всегда заполнена жидкостью. Обратный шаровой клапан, смонтированный в головке насоса, исключает утечку жидкости из насосных труб после остановки насоса или при заливе.
Для выпуска жидкости из колонны насосных труб перед подъемом агрегата из скважины, для ремонта в одной из нижних муфт колонны монтируют спускной клапан.
Насосный агрегат в скважину спускают последовательным наращиванием колонны насосных труб с одновременным креплением к ним сбоку питающего кабеля. Весьма желательно обеспечить контролируемую затяжку резьбовых муфт. Кабель туго прижимается к насосным трубам специальными металлическими поясами на расстоянии 100—150 мм по обе стороны соединительных муфт.
Очень важно следить за параллельностью кабеля оси трубы по всей длине колонны, так как кабель, навитый на трубу по спирали, может заклинить колонну и вызвать тяжелые затруднения при демонтаже.
При спуске кабеля с колонной можно повредить его защитную оболочку о края фланца на входе в обсадную трубу. Чтобы избежать повреждений, на фланец обсадной трубы устанавливают подставку с боковым роликом, через который перекатывается кабель при спуске.
В процессе спуска колонны следует периодически проверять мегометром качество изоляции кабеля. Когда агрегат спущен на проектную глубину, монтажную подставку убирают, а на последнее звено колонны насосных труб монтируют мощную шайбу, на которой висит вся система во время эксплуатации. Затем оборудуют устье скважины в соответствии с заданием технологов и заливают колонну насосных труб жидкостью для облегчения запуска. Если в скважине возможно отложение парафина, на ее устье ставят приспособление для применения скребков. Из описания видно, что монтаж — демонтаж подземной части насосной установки является операцией длительной и трудоемкой, поэтому на тщательность выполнения всех работ и текущий контроль их качества должно быть обращено особое внимание, чтобы исключить необходимость преждевременного подъема насосного агрегата из скважины.
Станция управления дает возможность управлять работой установки вручную и автоматически по заданной программе. Станцию доставляют на место монтажа в собранном виде; остается лишь соединить кабель с вводами на станции, а главное, проверить и наладить электрическую часть установки на заданный режим. Станцию управления монтируют на некотором расстоянии от скважины и соединяют ее с кабелем,
Во время наладки электрической части тщательно проверяют схему, состояние приборов и аппаратуры, а также состояние изоляции и заземления. Все станции снабжают максимальным и минимальным реле для защиты установки от перегрузки и исключения возможности работы вхолостую при срыве подачи, которые необходимо отрегулировать: первое на максимальный ток перегрузки, второе — на минимальный ток холостого хода. В схеме станции имеется также реле самозапуска установки после перерыва подачи электроэнергии и реле времени для периодической работы установки по заданной технологами программе откачки нефти из скважины. Все электротехнические работы по монтажу, проверке и наладке насосной установки выполняют специалисты-электромеханики.
19.Система планово-предупредительного ремонта и структура ремонтных служб нефтепромысловых предприятий.
Нельзя считать правильным эксплуатацию машин или механизмов до полного выхода из строя, без своевременных остановок для замены быстроизнашивающихся деталей, необходимой
регулировки и ремонта. Эти мероприятия позволяют избежать более крупных затрат по ремонту, связанных с заменой дорогостоящих узлов и деталей.
Для сохранения нормальной работоспособности бурового и нефтепромыслового оборудования применяют систему планово-предупредительного ремонта (ППР), представляющую собой совокупность организационно-технических мероприятий по уходу, надзору и ремонту, проводимых в плановом порядке. Благодаря такой системе заранее планируется остановка машин на ремонт по графику, подготавливаются запасные части, материалы и т. д.
Система планово-предупредительного ремонта технологического оборудования характеризуется следующими основными особенностями.
1. Оборудование ремонтируется в плановом порядке, через определенное число отработанных машино-часов или установленную норму отработки в календарных днях.
2. Определенное число последовательно чередующихся плановых ремонтов соответствующего вида образует периодически повторяющийся ремонтный цикл.
3. Каждый плановый периодический ремонт осуществляется в объеме, восполняющем тот износ оборудования, который явился результатом его эксплуатации в предшествовавший ремонту период; он должен обеспечивать нормальную работу оборудования до следующего очередного планового ремонта, срок которого наступит через определенный, заранее установленный промежуток времени.
4. Между периодическими плановыми ремонтами каждая машина подвергается в плановом порядке техническим осмотрам, в процессе которых устраняются мелкие дефекты, производятся регулировка, очистка и смазка механизма, а также определяется номенклатура деталей, которые должны быть подготовлены для замены износившихся деталей.
Системой планово-предупредительного ремонта в зависимости от объема и сложности ремонтных работ предусматривается проведение текущего и капитального ремонтов.
Текущий ремонт — это минимальный по объему плановый ремонт, посредством которого оборудование поддерживается в работоспособном состоянии. Он выполняется непосредственно на месте установки оборудования.
При текущем ремонте проверяется состояние оборудования, заменяются быстроизнашивающиеся детали, меняется при необходимости смазка и устраняются дефекты, не требующие разборки сложных узлов оборудования. Те неисправности оборудования, которые не могут быть устранены силами службы технического обслуживания, устраняются силами выездных ремонтных бригад.
Перечень ремонтных работ при текущем ремонте определяется классификатором ремонта. После ремонта проверяется работа оборудования, регулируются узлы и механизмы.
Капитальный ремонт — наиболее сложный и трудоемкий вид планового ремонта, при котором производятся полная разборка оборудования с последующим ремонтом или заменой всех изношенных узлов или деталей, а также работы, входящие в объем текущего ремонта.
В результате капитального ремонта полностью восстанавливается техническая характеристика оборудования.
Капитальный ремонт, как правило, осуществляется на ремонтных заводах, но при необходимости в виде исключения выполняется силами ремонтных баз или мастерских. Оборудование отправляется в капитальный ремонт в соответствии с графиком ремонта, а также с учетом его технологического состояния.
Внеплановый ремонт — ремонт, вызванный аварией оборудования, или не предусмотренный планом. При надлежащей организации системы планово-предупредительного ремонта внеплановые ремонты, как правило, не должны иметь место.
Для поддержания оборудования в постоянной технической исправности и эксплуатационной готовности, а также с целью предупреждения аварий и поломок должна обеспечиваться система технического обслуживания. Техническое обслуживание включает в себя наблюдение за выполнением правил эксплуатации оборудования, указанных в технических условиях, паспортах на оборудование, и проводится с целью проверки технического состояния оборудования, устранения мелких неисправностей и выявления объема подготовительных работ, подлежащих выполнению при очередном плановом ремонте.
Для бурового и эксплуатационного оборудования устанавливают следующие виды технического обслуживания.
1. После завершения монтажа оборудования до начала проведения работ производят - проверку всех соединений, внешний осмотр, а также проверку работоспособности оборудования и приборов.
2. При кратковременных остановках, если по количеству отработанных часов оборудование не подлежит более сложному техническому обслуживанию, оборудование осматривают внешне в объеме технического обслуживания, а также устраняют неисправности, замеченные обслуживающим персоналом.
3.Периодические виды технического обслуживания осуществляют через определенное количество отработанных часов. Объемы одноименных периодических видов технического обслуживания равны друг другу, объем же каждого последующего вида обслуживания включает в себя объем предыдущего вида.
При периодических видах технического обслуживания выполняются трудоемкие работы, такие как промывка фильтров, смена смазки, замена шинно-пневматических муфт и т. п.
Межремонтное техническое обслуживание выполняет обслуживающий персонал, а в случае необходимости — дежурный персонал ремонтной службы. Результаты технического обслуживания заносят в специальный журнал.
Правильно организованное техническое обслуживание оборудования значительно сокращает его простои по причине поломок и выходов из строя узлов и деталей в межремонтный период. Межремонтным периодом называется период работы оборудования между двумя любыми очередными плановыми ремонтами.
Ремонтным циклом называется наименьший повторяющийся период работы оборудования, в течение которого выполняются в определенной последовательности установленные виды технического обслуживания и ремонта.
Структура ремонтного цикла представляет собой схему чередования видов ремонта, различающихся по объему работ, проводимых в определенной последовательности через определенные промежутки времени на всем протяжении ремонтного цикла.
По мере эксплуатации и ремонта для каждого оборудования наступает такой момент, когда в результате физического и морального износа его эксплуатация и ремонт становятся невозможными и экономически невыгодными.
Физический износ машины есть результат разрушения различных ее элементов, в связи с чем машина перестает удовлетворять предъявляемым к ней требованиям.
Моральным износом называется уменьшение стоимости действующей техники под влиянием технического прогресса. Различают две формы морального износа:
1. Утрата действующей стоимости, по мере того как машины такой же конструкции начинают воспроизводиться дешевле.
2. Обесценивание действующей техники вследствие появления более совершенных конструкций машин.
Период с начала введения машины в эксплуатацию до ее списания, измеряемый в годах календарного времени, называется сроком службы. Срок службы оборудования находится в тесной зависимости от норм амортизационных отчислений.
В основу системы ППР заложена плановость проведения ремонтных работ. Для этого перед началом каждого года на основе ремонтных нормативов на нефтепромысловых предприятиях составляются годовые, квартальные и месячные планы-графики ремонта на каждую единицу оборудования. При составлении планов-графиков необходимо выдерживать установленные системой ППР межремонтные периоды, а также обеспечивать примерно равный объем ремонтных работ по кварталам и месяцам с целью равномерной загрузки ремонтной службы.
Годовые планы-графики ремонта оборудования служат основанием для определения годового объема ремонтных работ, численности ремонтного персонала, потребности в запасных частях, материалах, денежных средствах и технологическом оборудовании, необходимых для выполнения ремонтных работ.
Годовые, квартальные и месячные планы-графики разрабатывает главный механик нефтепромыслового предприятия. Годовые планы капитального ремонта утверждаются руководителем предприятия.
Руководство работами по обеспечению правильного использования и поддержанию в работоспособном состоянии оборудования возлагается на главного механика предприятия. Он возглавляет отдел главного механика и осуществляет техническое и методическое руководство за деятельностью производственных единиц, предприятий и организаций в области хранения, эксплуатации и ремонта оборудования.
Прокатно-ремонтные цеха производят текущий ремонт оборудования; изготовляют и восстанавливают простые запасные части, а также изготовляют простые приспособления и устройства, применяемые при бурении или эксплуатации скважин. Руководит прокатно-ремонтным цехом начальник, который несет полную ответственность за выполнение плана по ремонту оборудования, изготовление запасных частей, качество выполнение работ и технику безопасности. В цехе оборудование ремонтируют бригады и звенья слесарей, возглавляемые квалифицированными слесарями-бригадирами. Техническое обслуживание оборудования и устранение мелких неисправностей в работе производит персонал, эксплуатирующий оборудование.
Капитальный ремонт нефтепромыслового оборудования осуществляют крупные ремонтные цеха, центральные базы производственного обслуживания и ремонтно-механические заводы.
Производственная структура ремонтного предприятия определяется составом производственных подразделений — цехов, участков, рабочих мест и вспомогательных служб.
Участок — основная производственная единица ремонтного предприятия, где выполняется определенная часть технологического процесса ремонта; он занимает обособленную производственную площадь предприятия и оснащается специальным оборудованием. Как правило, участок подразделяется на несколько рабочих мест. Различают основные, вспомогательные, обслуживающие и побочные участки ремонтных предприятий.
На основных участках выполняются все основные стадии производственного процесса по ремонту оборудования.
К вспомогательным участкам относятся те, которые создают условия для нормальной работы основных участков, например инструментальные.
К обслуживающим участкам и хозяйствам относятся транспортные и материально-технические склады.
Однотипные, взаимосвязанные участки крупного ремонтного предприятия, требующие единого руководства, объединяют в более крупные подразделения — цеха.
Классификация видов ремонтов и операций (для подземного ремонта).
Цикл эксплуатации нефтяной скважины состоит из следующих последовательно выполняемых процессов: а) отбор пластовой жидкости, т. е. эксплуатация скважин; б) поддерживание технологического режима эксплуатации скважин — подземный и капитальный ремонты, гидравлический разрыв, промывка, кислотная обработка призабойной зоны и т. д.
Подземный ремонт скважин подразделяется: текущий и капитальный. К текущему относятся работы, связанные с ремонтом извлекаемого подземного оборудования: колонны штанг, труб, насоса и т. д. Капитальный ремонт скважин включает сложные работы, связанные с ремонтом обсадной колонны и воздействием на пласт.
Все операции, составляющие процесс подземного и капитального ремонта скважин, выполняются при помощи подъемников, вышек или мачт, специализированного оборудования для очистки труб, промывки скважин, обработки призабойной зоны пласта, инструментов для выполнения ручных операций, а также средств механизации.
Рис. 57. Классификация операций подземного ремонта:
/— транспортные операции; 2 — подготовительные операции; 3 — спуско-подъемные операции;
4 — тартание и др.; 5 — депарафинизация; 6 — чистка пробок; 7 — закачка теплоносителя; 8 — закачка кислоты; 9 — закачка специальной жидкости; 10 — заливка цемента; 11 — цементирование ствола; 12 — разбуривание
При подземном ремонте проводятся следующие операции:
1) транспортные — доставка необходимого оборудования к устью скважины;
2) подготовительные — установка оборудования на площадке у скважины, подготовка его к работе;
3) спускоподъемные — извлечение из скважины насосного оборудования и спуск нового или отремонтированного;
4) подземный ремонт — смена скважинного насоса или его узлов, чистка пробки и т. п.;
5) заключительные — свертывание комплекта оборудования и подготовка его к транспортировке.
Все процессы подземного ремонта (рис.57) обязательно включают в себя транспортные, спускоподъемные и заключительные операции. В балансе времени примерно 80 % приходится на указанные операции и 20%—на остальные.
Подземный ремонт выполняется бригадами по подземному ремонту скважин
|
|
Двойное оплодотворение у цветковых растений: Оплодотворение - это процесс слияния мужской и женской половых клеток с образованием зиготы...
Автоматическое растормаживание колес: Тормозные устройства колес предназначены для уменьшения длины пробега и улучшения маневрирования ВС при...
Индивидуальные и групповые автопоилки: для животных. Схемы и конструкции...
История развития хранилищ для нефти: Первые склады нефти появились в XVII веке. Они представляли собой землянные ямы-амбара глубиной 4…5 м...
© cyberpedia.su 2017-2024 - Не является автором материалов. Исключительное право сохранено за автором текста.
Если вы не хотите, чтобы данный материал был у нас на сайте, перейдите по ссылке: Нарушение авторских прав. Мы поможем в написании вашей работы!