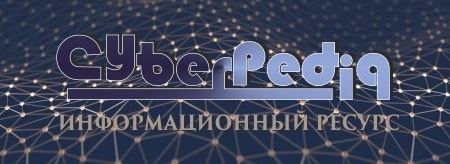
Типы оградительных сооружений в морском порту: По расположению оградительных сооружений в плане различают волноломы, обе оконечности...
Семя – орган полового размножения и расселения растений: наружи у семян имеется плотный покров – кожура...
Топ:
Характеристика АТП и сварочно-жестяницкого участка: Транспорт в настоящее время является одной из важнейших отраслей народного хозяйства...
Теоретическая значимость работы: Описание теоретической значимости (ценности) результатов исследования должно присутствовать во введении...
Проблема типологии научных революций: Глобальные научные революции и типы научной рациональности...
Интересное:
Искусственное повышение поверхности территории: Варианты искусственного повышения поверхности территории необходимо выбирать на основе анализа следующих характеристик защищаемой территории...
Принципы управления денежными потоками: одним из методов контроля за состоянием денежной наличности является...
Средства для ингаляционного наркоза: Наркоз наступает в результате вдыхания (ингаляции) средств, которое осуществляют или с помощью маски...
Дисциплины:
![]() |
![]() |
5.00
из
|
Заказать работу |
|
|
Пуском руководит и несет ответственность один человек из трех указанных выше.
Аппаратчики производства формалина находятся на своих рабочих местах, действуют в соответствии с инструкцией на рабочее место и выполняют все распоряжения ответственного за пуск.
Во время пуска на этажерке кроме аппаратчика должны присутствовать: электрослесарь, который собирает схему электрозапала и включает его по указанию ответственного за пуск. Регулирование и контроль за работой электрозапала производится с пульта управления.
Подготовка системы к пуску.
Загрузка катализатора производится следующим образом: на трубную решетку подконтактного холодильника помещается круг, составленный из перфорированных медных сегментов и диска, обжимной латунной сеткой N2 ГОСТ 3826-82. Сегменты и диск (толщиной 8-10 мм с отверстиями диаметром 8 мм), если поставлены вновь обжигаются при температуре не ниже 8000 С, во избежании их коробления. После установки сегментов на подконтактный холодильник ставится царга подконтактного аппарата. Свободное пространство между решеткой и царгой заделывается латунной сеткой заподлицо с решеткой. После такой подготовки на латунную сетку засыпается контактная масса.
При загрузке катализатора необходимо следить за равномерным распределением массы по сечению контактного аппарата для обеспечения равномерного прохождения контактных газов через контактную массу. Засыпается масса и уплотняется вручную осторожно с помощью специальной трамбовки, горизонтальность слоя проверяется по уровню. На уплотненную массу накладывается специальная сетка, ставятся салазки с электрозапалом, верхний конус и контактный аппарат закрывается. Перед установкой конусной крышки для проверки следует включить электрозапал под напряжение на 3-5 минут.
|
Примечание:
1. При загрузке контактной массы необходимо следить, чтобы термопары располагались в середине слоя.
2. Чем лучше уплотняется слой контактной массы, тем быстрее осуществляется процесс розжига и выхода процесса концентрирования на нормальный режим.
После проверки герметичности оборудования проверяется исправность коммуникаций подачи технологической воды к точкам потребления:
1) на заполнение систем рециркуляции;
2) на подпитку систем абсорбции.
В зимнее время линия подачи технологической воды на приготовление спиртоводного раствора должна быть свободной во избежании ее замораживания.
Проверяется наличие необходимого давления пара не менее (3,5 кгс/см2) 0,35 МПа на вводе в мастерскую, исправность коммуникаций подачи пара к теплообменникам (промежуточным подогревателям воды, перегревателям спиртовоздушной смеси), а также подачи острого пара на подогрев циркулирующей воды.
Заполняется технологической водой (паровым конденсатом), система рециркуляции воды охлаждения-подогрева контактного узла. заполнение ведется с помощью ц/б или поршневого насосов.
Система считается заполненной когда уровень воды в расширительном бачке на этажерке достигает установленного уровня в пределах контрольных отметок по мерному стеклу и по сигнальным лампочкам установленным на щите. По окончании заполнения включаются насосы циркуляции и проверяется исправность работы каждого и безотказность автоматического переключения с одного насоса на другой.
Проверяется наличие метанола в расходном хранилище и исправность коммуникаций подачи спирта на смешение, безотказность автоматического переключения с одного насоса на другой.
Проверяется исправность коммуникаций и центробежных насосов орошения барботажного холодильника и абсорбционных башен или поглотительной колонны системы №3. Газоход перед барботажным холодильником должен быть свободен от конденсата, который спускается в сборник во время остановки, а также при работе производства. Уровень жидкости в сборнике при пуске должен быть не менее 30см. Для уменьшения количества пускового (нестандартного) формалина уровень жидкости по башням при пуске должен быть минимальным (1-2 см по мерному стеклу). В этом случае, когда во время остановки раствор формальдегида с башен спущен, заполняются технологической водой только последние башни 2-я, 4-я, 6-я до минимального уровня (по мерному стеклу или до появления перетока в 1-ую, 3-ую и 5-ю башни). Проверяется исправность КИПиА, наличие сжатого воздуха в системе контроля и автоматики с давлением не ниже (1,6 атм) 0,16 МПа. Проверяется правильность перекрытия всей запорной арматуры на местах.
|
После указанной подготовки и при температуре циркуляционной воды около 50-540 С (при температуре спирта в испарителе около 35-380 С) включается турбовоздуходувка, при этом закрывается воздушник на буферном аппарате и открывается электрозадвижка на обводном газоходе (задвижки до и после контактного аппарата закрыты). Таким образом спиртовоздушная смесь, минуя аппарат поступает на абсорбцию. Расход воздуха при пуске устанавливается 900-2000 м3 /час при сопротивлении в системе не более (0,25кгс/см2) 0,025 МПа. Вместе с включением турбовоздуходувки дается пар в пароперегреватель буферного аппарата. Температура перегрева спиртовоздушной смеси при пуске должна быть не ниже 700 С.
Перед началом розжига контактной массы спирт из спиртоиспарителя отбирается на анализ в лабораторию.
Массовая доля его должна быть не ниже 97 %. Тщательно контролируется температура испарения спирта по прибору и ртутному термометру, расположенному в газоходе над зеркалом испарителя жидкости. Ртутный термометр для контроля температуры испарения должен иметь цену деления 0,50 С и перед пуском обязательно проверяется контрольной лабораторией, где выдается поправка на показание.
Розжиг контактной массы продувка контактного аппарата, включение электрозапала проводится при температуре испарения спирта 45-460 С по ртутному термометру ГОСТ 28498-90, со шкалой (0-100)0 С, погр.изм. 1%.
Розжиг контактной массы осуществляется следующим образом:
1) полностью открывается (с пульта управления) задвижка на входе в контактный аппарат;
|
2)открывается задвижка на выходе из контактного аппарата и одновременно закрывается задвижка на обводной линии;
3) рукой на ощупь проверяется равномерность прогрева царги контактного аппарата. Если спиртовоздушная смесь через сечение контактной массы проходит равномерно, то царга контактного аппарата прогревается тоже равномерно. Продувка контактного аппарата спиртовоздушной смесью необходима для вытеснения из него воздуха во избежание образования взрывоопасной концентрации спиртовоздушной смеси перед включением электрозапала;
4) через 1-2 минуты продувки и равномерного прогрева царги аппарата и верхнего конуса включается электрозапал.
На пульте управления имеется сигнальная лампочка работы электрозапала. Ведется непрерывное наблюдение за состоянием контактной массы через смотровое стекло на конусе контактного аппарата;
5) появление местного свечения контактной массы означает начало реакции образования формальдегида. При температуре в зоне контактирования 400-5000 С электрозапал выключается и дальнейший розжиг контактной массы идет за счет тепла реакции;
6) при нормальном розжиге могут наблюдаться голубоватые всполохи над поверхностью контактной массы. При поступлении в контактный аппарат обедненной спиртовоздушной смеси происходят слабые вспышки с толчками и с изменением свечения. В этом случае температуру в спиртоиспарителе следует поднять на 1-20 С до прекращения ненормального горения. При сильно обедненной смеси горение сопровождается резкими хлопками и вспышками. В этом случае электрозапал выключается, перекрываются задвижки до и после контактного аппарата и открывается задвижка на обводной линии.
При поступлении богатой смеси контактная масса не разжигается. В этом случае температуру в испарителе следует понизить на 1-20 С и следить за продолжением розжига.
По мере розжига контактной массы температура циркулирующей воды, а следовательно, и температуре в испарителе возрастают. Для поддержания температурного режима испарения постепенно уменьшается подача пара в регулировочный подогреватель циркулирующей воды и в случае необходимости дается охлаждающая вода в регулировочный холодильник. Регулировка температуры осуществляется со щита через регулировочный клапан или вручную по обводным линиям.
|
После разогревания всей контактной массы и достижения температуры контактирования в пределах 630-6900 С подача воздуха увеличивается до 1600-2000 м3/час.
С увеличением подачи воздуха включается орошение барботажного холодильника.
При расходе воздуха 1600-2000 м3 /час осуществляется переход к подаче в испаритель спиртоводного раствора концентрации 60-68% по метанолу (40-32% воды). Для этого соответственно расходу метанола устанавливается расход технологической воды и подключается корректировка по плотности. Раствор спирта концентрацией 60-68% подается на испарение до выхода испарителя на рабочий режим. Снижение концентрации метанола в испарителе до нормального рабочего раствора 15-20% осуществляется постепенно. Проба на анализ отбирается в зависимости от обстановки, но не реже чем 2 часа.
По окончании разбавления метанола в спиртоиспарителе включается орошение на башни № 4.
По мере разбавления метанола увеличивается температура испарения и регулируется с таким расчетом, чтобы заданная температура контактирования держалась постоянно. При этом соответственно увеличивается температура циркуляционной воды.
Во время выхода спиртоиспарителя на рабочий режим концентрация спиртовоздушной смеси нестабильна, поэтому необходимо особенно внимательно следить за температурой контактирования и держать ее в пределах 630-6900 С не допуская повышения ("скачков") более 300 С.
После выхода спиртоиспарителя на рабочий режим увеличивают нагрузку на контактный аппарат. Увеличение нагрузки производится прибавлением подачи воздуха на 250 м3 с интервалом через 1-2 часа работы до выхода системы на заданную производительность.
После увеличения расхода воздуха увеличивается орошение барботажного холодильника. При этом по системе абсорбции поддерживается следующий температурный режим:
1) барботажный холодильник.
Температура газа не более 850 С.
Температура орошающей жидкости фактически;
2) 3 абсорбционная башня.
Температура газа летом не более 600 С,
зимой не более 550 С.
Температура орошающей жидкости в пределах, обеспечивающих заданную температуру газа
3) 4 абсорбционная башня.
Температура газа летом не более 400 С, зимой не более 200С.
Температура орошающей жидкости в пределах, обеспечивающих заданную температуру газа.
После выхода спиртоиспарителя на режим, концентрация спиртовоздушной смеси устанавливается стабильной.
После вывода системы на получение стандартного формалина в сборнике температура контактирования постепенно снижается до оптимальной 650-6900С. По достижении оптимальной температуры в зоне контактирования можно увеличить нагрузку на катализатор (увеличивать расход воздуха) и давать по мере возможности на 4-ю и 2-ю башни абсорбции подпитку технологической воды.
|
Пуск поглотительной колонны агрегата №3
Включение в работу поглотительной колонны производится после обеспечения работоспособности смежных систем и оборудования: сборника процессного конденсата, хранилищ формалина с их насосами и коммуникациями, систем деминерализованной, оборотной (технической) воды, а так же проверки работоспособности и включению в работу всех приборов КИПиА, сигнализаций и блокировок.
Закрыть клапан на сливе жидкости со сборника верхнего циркуляционного контура поглотительной колонны в сборник процессного конденсата, установив задание регулятора на клапан L-5-16 на ''0''. Закрыть откачку с куба колонны в хранилище формалина. Открыть подачу деминерализованной воды на 30 тарелку колонны (в режиме ручного управления).
Подача деминерализованной воды на приготовление спиртоводной смеси ведется через сборник процессного конденсата в режиме автоматического включения-выключения клапана на подаче деминерализованной воды в пределах уровня 30÷50%.
Деминерализованная вода, сливаясь по тарелкам санитарной, а затем верхней циркуляционной зоны, попадает в сборник, расположенный между 15 и 16 тарелками, заполняет насосы поз.23/3,4 (вентили на всасе и нагнетании насосов, а так же воздушники насосов открыты), трубопроводы и сам сборник до уровня переливного порога. Достигнув уровня переливного порога сборника, деминерализованная вода по переливу поступает на тарелки среднего контура и сливается в сборник, расположенный между 5 и 6 тарелками.
Заполнив насосы 23/1,2 (вентили на всасе и нагнетании насосов, а так же воздушники насосов открыты), трубопроводы и сам сборник до уровня переливного порога, деминерализованная вода через перелив, по тарелкам нижнего контура перетекает вкуб колонны, заполняет насосы поз.18/1,2 (вентили на всасе и нагнетании насосов, а так же воздушники насосов открыты) трубопроводы и куб колонны до заданного уровня - 50÷60%. После достижения указанного уровня в кубе и проверки заполнения насосов поз. 18,23, вентили на нагнетании и воздушниках последних закрываются, включаются в работу по одному насосу на циркуляционный контур и устанавливаются заданные расходы жидкости на циркуляцию (на насосах поз.18 ≈ 60 м3/час, нанасосах поз.23/1,2 ≈ 30 м3/час; на насосах поз. 23/3,4 ≈ 10 м3/час). Поскольку сборники жидкости представляют собой глухие тарелки и переток жидкости на нижерасположенные тарелки возможен только через переливы при переполнении сборников, в циркуляционных контурах всегда обеспечен необходимый запас жидкости для пуска насосов.
После включения циркуляционных насосов, за счет заполнения оборудования и трубопроводов циркуляционных контуров, находящихся выше соответствующих сборников, уровень жидкости в кубе колонны и сборниках жидкости между 5 и 6 и между 15 и 16 тарелками снизится. Возобновляется подача деминерализованной воды на 30 тарелку, сборники вновь заполняются до верхнего перелива, а уровень в кубе колонны начинает повышаться. При достижении уровня в кубе колонны значения 50÷80% подача воды на 30 тарелку прекращается. Включается подача охлаждающей воды в теплообменники циркуляционных контуров. Если колонна сообщалась с атмосферой через воздушник – закрыть его. Поглотительная система готова к приему газа со стадии окислительного дегидрирования метанола.
После пуска стадии окислительного дегидрирования и подачи газа в колонну тарелки вступают в работу. При этом уровень жидкости в сборниках и в кубе колонны вновь упадет на величину запаса жидкости на ситчатых тарелках. Возобновляется подача деминерализованной воды на 30-ю тарелку, при этом сборники последовательно заполняются жидкостью до уровня переливов. При достижении уровня жидкости в кубе колонны значения 50%подача воды на 30тарелку прекращается.
Открывается вентиль на сливе в сборник поз.16 из сборника верхнего циркуляционного контура. При этом произойдет падение уровня во внутреннем сборнике до уровня расположения штуцера слива в сборник поз.16. Перевести регулирование уровня в сборнике процессного конденсата на автоматическое. Подача деминерализованной воды в сборник поз.16 автоматически прекращается после превышения уровня выше 50%.
За счет конденсации и поглощения жидкостью из газа формальдегида и метанола, а так же паров воды будет происходить увеличение количества жидкости, циркулирующей в контурах колонны. При росте уровня в кубе колонны более 70% открывается откачка из куба колонны в хранилище.
До установления концентрации формалина 37% поддержание уровня в сборнике поз.16 ведется в автоматическом режиме по подаче деминерализованной воды на 30 тарелку колонны (клапан на сливе с глухой тарелки в сборник поз.16 полностью открыт). После достижения концентрации формалина 37,2% поддержание уровня в сборнике поз.16 переключается на клапан отбора с глухой тарелки, а подача деминерализованной воды на 30 тарелку увеличивается. Прием из колонны переводится в другое хранилище.
Поглотительная система включена в работу и выведена на режим.
Пуск системы сжигания хвостовых газов абсорбционного отделения.
Пуск установки сжигания хвостовых газов абсорбционного отделения осуществляется под руководством лица ответственного запуск.
Руководить пуском имеют право:
1) первый заместитель директора по производству;
2) технолог цеха;
3)начальник производства формалина.
Пуск установки сжигания производится после вывода систем производства формалина на рабочий режим.
Подготовка установки сжигания хвостовых газов абсорбционного отделения к пуску.
Подготовка установки для приема хвостовых абсорбционных газов на сжигание состоит из подготовки котла-утилизатора и подготовки газового хозяйства.
За 4-6 часов перед пуском установки сжигания подготавливается к работе котел-утилизатор КУ-40:
1) проверяется исправность арматуры котла, водомерных стекол, предохранительных клапанов, манометров, всех спускных и запорных вентилей арматуры и регулятора питания.
Рычаги предохранительных клапанов не должны быть заклинены и не должны иметь дополнительных грузов. Контрольный рычаг клапана на барабане должен быть заключен в кожух и запломбирован или закрыт на замок;
2) после осмотра и проверки готовности котла к пуску производится заполнение котла водой или подпитка его, если вода из него не спускалась. Заполнение котла водой производить следует в течение 1,0-1,5 часов, а в холодное время года заполнение водой удлиняется до 2-х часов. Температура воды при заполнении котла должна быть в пределах 20-5000 С. Котел наполняется только до низшего уровня воды в барабане во избежание переполнения воды вверх водоуказательного прибора при повышении её температуры при подогреве котла.
Во время заполнения котла проверяется плотность лазов, фланцев, спускной и продувочной арматуры. После прекращения питания котла водой необходимо проверить, сохраняется ли в котле неподвижный уровень воды.
Если уровень воды опускается или поднимается, необходимо еще раз осмотреть, выявить неплотности в арматуре и устранить их.
Если котел был уже заполнен водой (обессоленной или паровым конденсатом), следует подпитать или спустить часть воды. Проверить исправность водоуказательных колонок и довести уровень до положения "низшего";
3) после заполнения котла водой включить устройство для обогрева, предварительно прогрев паровую линию. Включать следует медленно, начиная от ближнего к котлу.
Подогрев воды острым паром производится при закрытом выходном паровом вентиле до тех пор, пока давление в котле не поднимается до (2,5-3,0) кгс/см2 0,25-0,3 МПа, после чего могут быть допущены дымовые газы в котел. При достижении давления пара в котле (1,5-2,0кгс/см2) 0,15-0,2 МПа, а также перед включением котла в паровую магистраль производится продувка водомерных стекол. Общая продолжительность разогрева котла от холодного состояния до полного давления должно быть не менее 2,5-3,0 часов.
Если при нагревании воды в котел уровень ее повышается за верхний допустимый предел, необходимо часть воды спустить через продувочный штуцер;
4) для подготовки газопровода необходимо заполнить гидрозатворы водой и отрегулировать постоянный небольшой перелив ее в канализацию;
5) проверяется исправность коммуникаций, вентиляторов, газодувок;
6) проверяется исправность системы КИП и автоматики, наличие сжатого воздуха в системе контроля и автоматике с давлением не ниже (1,6 кгс/ см2) 0,16 МПа;
7) проверяется правильность перекрытия всей запорной арматуры;
8) проверяется разряжение в топке. Разряжение должно быть не менее (2-3 мм. вод. ст.) 20-30 Па.
|
|
Кормораздатчик мобильный электрифицированный: схема и процесс работы устройства...
Особенности сооружения опор в сложных условиях: Сооружение ВЛ в районах с суровыми климатическими и тяжелыми геологическими условиями...
Механическое удерживание земляных масс: Механическое удерживание земляных масс на склоне обеспечивают контрфорсными сооружениями различных конструкций...
Типы оградительных сооружений в морском порту: По расположению оградительных сооружений в плане различают волноломы, обе оконечности...
© cyberpedia.su 2017-2024 - Не является автором материалов. Исключительное право сохранено за автором текста.
Если вы не хотите, чтобы данный материал был у нас на сайте, перейдите по ссылке: Нарушение авторских прав. Мы поможем в написании вашей работы!