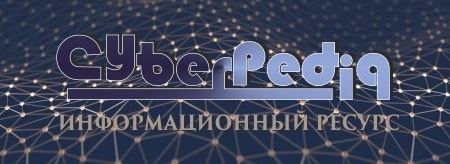
Опора деревянной одностоечной и способы укрепление угловых опор: Опоры ВЛ - конструкции, предназначенные для поддерживания проводов на необходимой высоте над землей, водой...
Особенности сооружения опор в сложных условиях: Сооружение ВЛ в районах с суровыми климатическими и тяжелыми геологическими условиями...
Топ:
Характеристика АТП и сварочно-жестяницкого участка: Транспорт в настоящее время является одной из важнейших отраслей народного хозяйства...
Оснащения врачебно-сестринской бригады.
Когда производится ограждение поезда, остановившегося на перегоне: Во всех случаях немедленно должно быть ограждено место препятствия для движения поездов на смежном пути двухпутного...
Интересное:
Что нужно делать при лейкемии: Прежде всего, необходимо выяснить, не страдаете ли вы каким-либо душевным недугом...
Наиболее распространенные виды рака: Раковая опухоль — это самостоятельное новообразование, которое может возникнуть и от повышенного давления...
Мероприятия для защиты от морозного пучения грунтов: Инженерная защита от морозного (криогенного) пучения грунтов необходима для легких малоэтажных зданий и других сооружений...
Дисциплины:
![]() |
![]() |
5.00
из
|
Заказать работу |
|
|
Составляющие баланса | Расчетное уравнение | Приход | Составляющие баланса | Расчетное уравнение | Приход | |||
кДж | % | кДж | % | |||||
Q эл | (9) | Q разл | (11) | |||||
Q ан | (10) | Q мет | (12) | |||||
Q газ | (13) | |||||||
Q п | ||||||||
Итого | 100 | 100 | ||||||
Приход тепла от сгорания угольных анодов
, (10)
где и
– соответственно число киломолей СО2 и СО, выделяющихся за 1 ч;
и
– тепловые эффекты реакций полного и неполного горения углерода при температуре поверхности анода.
Число киломолей продуктов горения можно определить из материального баланса (см. табл.1):
и
,
где и
– массовая концентрация СО2 и СО в газе соответственно; 44 и 28 – молекулярная масса СО2 и СО соответственно, кмоль/кг.
Тепловые эффекты реакций горения с образованием СО2 и СО в первом приближении соответственно
кДж/моль;
кДж/моль,
где T – температура поверхности анода, К.
Расход тепла на разложение глинозема
, (11)
где 1,89 Р – теоретический расход глинозема, кг/ч; – тепловой эффект реакции окисления алюминия, при температуре электролиза с учетом теплоты плавления алюминия
=1725722 – 61,71(Т – 298) + 31,82(Т – 932) кДж/моль,
где T – температура электролита, К.
Потери тепла с выливаемым из ванны алюминием рассчитываются, исходя из условия, что количество вылитого алюминия соответствует количеству наработанного в то же время металла. При температуре выливаемого алюминия 960 °С энтальпия алюминия составляет 43982 кДж/кмоль, а при 25 °С – 6717 кДж/кмоль. Тогда потери тепла с выливаемым алюминием
|
кДж. (12)
Унос тепла с газами рассчитываем, принимая, что разбавление газов за счет подсоса воздуха в систему отсутствует. Температура отходящих газов, по данным практики 550 °С. Потери тепла с газами
кДж, (13)
где 40488 и 16446 – рассчитанные по справочным данным энтальпии диоксида углерода соответственно при 550 и 25 °С, кДж/кмоль; 24860 и 8816 – то же для оксида углерода, кДж/кмоль.
Тепловые потери с поверхности электролизера Q п, связанные с конвективным теплообменом и излучением, наиболее трудоемки для определения. Эти расчеты осложняются также различием в условиях теплопередачи для отдельных поверхностей и тепловых зон электролизера. Считая модельный электролизер сбалансированным, тепловые потери можно определить по разности статей прихода и расхода в тепловом балансе.
Лабораторное оборудование. Модель алюминиевого электролизера, изготовленная в масштабе 1:20 в отделе макетного проектирования института ВАМИ.
Содержание задания. Данные по анодной плотности тока, выход по току алюминия, состав анодных газов, температура электролита и другие сведения технологического характера.
Порядок работы
1. Ознакомиться на макете электролизера с конструкцией алюминиевого электролизера типа ОА. Дать краткое описание отличительных особенностей этой конструкции, ее достоинств и недостатков.
2. Выполнить необходимые геометрические измерения и с учетом масштаба модели произвести балансовый расчет реального промышленного электролизера указанного типа, сводя результаты расчетов в табл.1-3.
3. Дать анализ полученных результатов в соответствии с заводской практикой эксплуатации алюминиевых электролизеров.
|
Цель работы. Знакомство с теорией и практикой металлотермического производства магния.
Основные определения, теория и технология
Способы получения металлов, в которых восстановитель также металл, называются металлотермическими. Они широко применяются в металлургии легких и редких металлов. В общем виде реакция металлотермического восстановления выражается уравнением
|
Me'nAm + nMe" = nMe' + Me"nAm,
где Me' и Me" – соответственно металлы, выполняющие роль окислителя и восстановителя (в данном случае с равной валентностью); A – анион (кислород, хлор и др.).
Восстановителями магния из его оксида служат такие элементы, которые образуют с кислородом термодинамически более прочные соединения, чем МgО. Мерой химической прочности оксида является энергия Гиббса для образования оксида из элементов – сродство к кислороду. Чем более положительное значение имеет энергия Гиббса, тем менее устойчив оксид, тем легче из него может быть восстановлен металл другим элементом, оксид которого характеризуется более отрицательным значением энергии Гиббса его образования.
На рис.1 приведены температурные зависимости стандартных значений энергии Гиббса образования оксидов из элементов (в расчете на 1 моль кислорода), откуда видно, что наибольшим сродством к кислороду обладает кальций. Следовательно, он способен восстанавливать из оксидов все металлы, характеризующиеся меньшей абсолютной величиной
при данной температуре. Точки пересечения графиков
= f (Т) для двух оксидов указывают температуру, при которой восстановление, т.е. замена магния в оксиде другим элементом, становится термодинамически равновероятной. Из такой очень приближенной оценки следует, что восстановление магния алюминием начинается при 1500 °С, а кремнием лишь выше 2300 °С. Но реакция может быть осуществлена при более низких температурах, если, во-первых, путем вакуумирования понижать давление паров магния над реакционной смесью, во-вторых, связать оксид восстановителя в иное, термодинамически более устойчивое соединение, например, SiO2 – в двухкальциевый силикат 2CaO×SiO2, Al2O3 – в алюминат кальция 5CaO×3Al2O3 и т.д. Количественная оценка влияния давления на установление равновесия возможна с помощью уравнения изотермы химической реакции (изотермы Вант-Гоффа).
|
Применительно к металлотермическому восстановлению магния по реакции
2MgO + Si = 2Mgгаз + SiO2
уравнение изотермы приобретает вид:
, (1)
|
где и
– неравновесное и равновесное давления магния при данной температуре.
С кинетической точки зрения, развитие реакции, протекающей с выделением газообразных продуктов, обусловлено скоростью их удаления. Достаточная для практики скорость реакции достигается тогда, когда равновесное парциальное давление паров магния станет хотя бы равным давлению остаточных, не участвующих в реакции газов. Для исключения лимитирующей роли диффузии паров и достижения возможно более высокой скорости процесса за счет повышения температуры необходимо соблюдение условия >
.
Конденсация паров магния наступает при их давлении, превышающем упругость насыщенного пара магния в конденсаторе. Возможность конденсации магния в твердом или жидком состоянии зависит от температуры и давления в конденсаторе. Если давление не превысит величины, отвечающей тройной точке (2,63 мм рт.ст. при t = 651 °С), то магний будет конденсироваться только в твердом состоянии.
Термическая технология магния – это радикальная альтернатива электролитическому методу, который достаточно сложен и потому рентабелен лишь при организации крупномасштабного производства (мощностью около 30000 т/год). К недостаткам электролитического способа следует отнести трудно решаемые проблемы коррозионной стойкости аппаратуры и загрязнения окружающей среды. Следует сказать, что термические способы в значительной степени свободны от этих недостатков.
Вакуумное восстановление обожженного доломита кремнием (с использованием ферросилиция, содержащего более 75 % Si) требует меньших капитальных затрат, чем электролитический метод. Кроме того, вакуумное восстановление легче приспособить к требованиям конъюнктуры, оборудование быстрее выходит на проектную мощность. Эта технология не требует длительного обучения персонала и, наконец, является менее опасной для окружающей среды.
|
Распространенный ранее метод Пиджена – восстановление обожженного доломита из брикетированной смеси с ферросилицием в вакуумированных до 0,1-0,01 кПа ретортах из нержавеющей стали – в настоящее время применяется достаточно редко. На остальных предприятиях термического профиля, а также на вновь проектируемых применяется технология Magneterm (рис.2), включающая: кальцинацию доломита и боксита, восстановление магния ферросилицием в вакуумной печи с внутренним электрообогревом, переплавку, рафинирование и отливку слитков. В этом случае восстановление доломита кремнием подчиняется следующей стехиометрии:
|
2(СаО + MgO) + Si = 2CaO×SiO2 + 2Mg. (2)
Однако при температуре реального процесса (1300 °С) реакция идет ступенчато, через стадию образования летучего монооксида кремния:
MgO + Si = Mg(г) + SiO(г);
3CaO + SiO(г) = Ca(г) + 2CaO×SiO2;
Сa(г) + MgO = Mg(г) + СаО.
Замена ферросилиция на алюмокремниевые сплавы позволяет более полно использовать их восстановительную способность, связанную с участием в реакциях алюминия:
2(CaO + MgO) + Al = 2Mg +
(5CaO×3Al2O3) +
CaO. (3)
Лабораторное оборудование Весы, гидравлический пресс и специализированная высокотемпературная установка, обеспечивающая возможность физического моделирования основных технологических процессов и операций для металлотермического получения магния, включая шихтовку, брикетирование и вакуумное восстановление.
Содержание задания. Требования к составу и количеству шихты, режиму шихтоподготовки и металлотермического восстановления.
Порядок работы
1. Рассчитать шихту для металлотермического восстановления доломита по реакциям (2) и (3) с учетом заданного избытка восстановителя от его стехиометрического количества, состава используемого сырья и количества вводимого минерализатора (флюорита).
2. Брикетированную шихту после взвешивания загрузить в реторту. Взвесить разъемную часть реторты для конденсации паров магния. Реторту собрать и установить в трубчатую печь. Ознакомиться с устройством термоустановки и методами контроля технологического режима. Зарисовать схему установки.
3. Включить вакуум-насос и при достижении величины остаточного давления в системе (0,1 мм рт.ст.) начать разогрев трубчатой печи до заданной температуры (1050-1200 °С) со скоростью около 20 °С/мин. Регулировка скорости обеспечивается изменением электрической нагрузки подаваемой на печь от автотрансформатора в пределах 0-180 В. Каждые 10 мин вести запись режимных показателей процесса (см. таблицу). По достижении максимальной температуры процесса произвести изотермическую выдержку в течение 40-60 мин.
Режим восстановления
t, мин | Р, мм рт.ст. | t, °С | D t /Dt, °С/мин |
0 | |||
10 | |||
... |
4. После завершения процесса в присутствии преподавателя отключить нагрев; кварцевую трубку с ретортой переместить в низкотемпературную зону и охладить под вакуумом в течение 15 мин. Затем заполнить систему воздухом и отключить вакуум-насос.
|
Взвесить конденсатор и твердый остаток, определить извлечение магния и выход огарка в процентах по формулам соответственно
;
,
где – масса брикетированной шихты;
– масса огарка;
– изменение массы конденсатора;
– масса магния в брикетированной навеске (по данным о количестве и составе магнийсодержащего компонента).
5. Используя графики = f (Т) для образования оксидов (см. рис.1) выполнить термодинамические расчеты:
· Определить термодинамическую вероятность протекания реакции при температурах 1100, 1400, 1600, 2000 °С по данным о стандартном сродстве к кислороду магния и кремния при этих температурах.
· По аналогии дать термодинамическую оценку реакции
2MgO + Al = 2Mg +
Al2O3.
· Для указанного температурного диапазона дать термодинамическую характеристику возможности протекания реакций (2) и (3). Вычислить константы равновесия и равновесные давления паров магния при этих температурах:
;
.
· Для реакций (2) и (3) по уравнению изотермы (1) определить возможность их протекания при температуре 1100 °С и давлении паров магния , равном 0,5; 0,1; 0,01; 0,001; 10-4 ат.
6. Дать анализ вероятности протекания приведенных реакций в условиях лабораторного опыта. Объяснить результаты эксперимента.
|
Цель работы. Знакомство с теоретическими и технологическими основами производства магния электролизом расплавленных хлоридов. Приобретение практических навыков проведения электролиза расплавленных сред. Выполнение термодинамических и технологических расчетов.
Основные определения, теория и технология
Впервые магний был выделен при восстановлении MgO парами калия английским физиком Х.Дэви в 1800 г. Французский химик С.-К.Девиль в середине XIX в. получил магний, восстанавливая MgCl2 парами калия и натрия. К концу XIX в. во Франции, Германии и США работали небольшие заводы, использующие этот процесс, остававшийся, однако, мало эффективным. В 1830 г. М.Фарадей впервые получил магний электролизом расплава MgCl2. В последующем этот способ был усовершенствован Матиссеном и С.-К.Девилем и в настоящее время является наиболее распространенным в производстве металлического магния.
Обладая низкой плотностью (1,745 г/см3), высокой коррозионной стойкостью и химической активностью, магний находит применение в автомобиле- и самолетостроении, в производстве космической техники, в металлургии коррозионно-устойчивых сплавов, в производстве тугоплавких редких металлов. Этим объясняется неизменный рост производства магния, чему способствует неисчерпаемые ресурсы природного сырья и высокое (2,4 %) содержание магния в земной коре.
Главным сырьевым источником для получения магния электролитическим методом служат его хлориды: бишофит MgCl2×6H2O и карналлит KCl×MgCl2×6H2O.
Технико-экономические показатели электролитического получения магния в значительной мере определяются физико-химическими свойствами электролита и обусловливаются его составом. При питании электролизеров расплавом карналлита содержание основных компонентов в электролите устанавливается самопроизвольно, исходя из их содержания в исходном обогащенном карналлите. Состав такого электролита не является оптимальным. Содержание, например, NaCl в нем не превышает 14 %.
|
Сопоставление физико-химических свойств различных электролитов и их технологических показателуй, показало, что наиболее благоприятным сочетанием свойств обладает натриево-калиевый электролит, содержащий 8-18 % MgCl2, и по 38-42 % NaCl и КС1. Однако в таком электролите MgCl2 имеет повышенную активность способствующую интенсивному шламообразованию, что, в свою очередь, приводит к пассивации катодов и снижению выхода магния по току.
К магниевому электролиту предъявляются высокие требования по чистоте и постоянству состава, поэтому природную карналлитовую руду после дробления и отделения пустой породы направляют на производство так называемого искусственного карналлита, (рис.1). Искусственный карналлит имеет примерно следующий состав, % по массе: MgCl2 31-32,5, КС1 25-26, NaCl 5-6, Н2О 34-36. При производстве магния в электролизер периодически вводят хлорид магния или карналлит, которые должны быть предварительно тщательно обезвожены.
При нагревании MgCl2×6H2O ступенчато теряет кристаллизационную воду, переходя с повышением температуры от одной формы кристаллогидрата к другой:
MgCl2×6H2O ® MgCl2×4H2O (более 117 °C);
MgCl2×4H2O ® MgCl2×2H2O (более 182 °C);
MgCl2×2H2O ® MgCl2×H2O (более 242 °C).
Однако уже при температуре выше 184 °С идет образование гидроксохлорида магния по реакции
MgCl2×2H2O = MgOHCl + HCl + H2O.
При температуре выше 554 °С происходит распад гидроксохлорида магния по реакции
MgOHCl = MgO + HCl.
Таким образом, полного обезвоживания гидратов хлорида магния простым нагреванием на воздухе достигнуть невозможно, так как повышение температуры сверх 150-260 °С приводит только к их гидролизу с образованием в конечном счете МgО и НСl. Для предотвращения гидролиза необходимо, чтобы в газовой фазе над гидратом хлорида магния существовало избыточное парциальное давление НСl.
Обезвоживание КС1×MgCl2×6H2O протекает с меньшими осложнениями, так как активность МgСl2 в двойной соли ниже. Это ведет к уменьшению гидролиза солей и позволяет вести процесс в воздушной среде.
Дегидратация карналлита протекает только в две ступени:
KCl×MgCl2×6H2O ® KCl×MgCl2×2H2O (более 90 °C);
KCl×MgCl2×2H2O ® KCl×MgCl2 (более 150 °C).
В промышленности им соответствуют две стадии обезвоживания, (рис.2). Обезвоживание карналлита на первой стадии проходит во вращающихся печах (старая технология) или в печах кипящего слоя, на второй стадии – в электрических печах непрерывного действия (СКН). Затем карналлит сливается в миксеры и нагревается до 750-850 °С с целью почти полного удаления воды, разложения
![]() |
гидроксихлоридов магния и для удаления из расплава оксида магния, который оседает в шлам. Полученный безводный карналлит с содержанием 49-52 % MgCl2, 0,5-0,8 % MgO направляется на электролиз. При хлорировании в хлораторах электролит плавится в интервале температур 500-550 °С, затем расплав поступает в хлорирующие камеры для дальнейшего обезвоживания и хлорирования MgO, и в миксер, где он отстаивается от непрохлорированного MgO и углерода. Осветленный расплав сливается в ковши и поступает на серии электролизеров.
Термодинамической основой электролиза MgCl2 в расплаве хлоридов служит возможность протекания следующих электродных процессов:
Mg2+ + 2 e = Mg; 2Cl– – 2 e = Cl2.
При этом теоретическое напряжение разложения MgCl2 численно равно ЭДС гальванической пары, образованной магниевым и хлорным электродами,
,
где j – электродный потенциал соответствующей пары.
Используя уравнение Нернста, можно записать
,
где jо – стандартный электродный потенциал соответствующей пары; R – универсальная газовая постоянная; Т – температура, К; n – число зарядов, участвующих в процессе; F – число Фарадея; а – активность соответствующего иона.
С учетом средней ионной активности при постоянстве
в расплаве получим
.
Здесь – число молей соответствующих ионов, образующихся при диссоциации MgCl2; Е о – напряжение разложения чистого MgCl2 в стандартных условиях.
Напряжение разложения чистого MgCl2, экспериментально найденное различными методами, E о = 2,499¸2,521 В при температуре 714-718 °С, а температурный коэффициет dE / dT = –(0,66¸1,21)×10-3 В/К.
В электролите, содержащем 13 % MgCl2, 3 % CaCl2 и хлориды калия и натрия в равных долях, при температуре 704 °С активность = 0,00102, и для E о = 2,544 В напряжение разложения MgCl2 составляет 2,613 В. Так как оно меньше напряжения разложения NaCl, KCl и CaCl2, для которых Е о соответственно равно 3,15, 3,29 и 3,32 В, то данные компоненты электролита остаются устойчивыми при разложении MgCl2. В то же время в электролите нежелательно наличие примесей с низкими напряжениями разложения. К ним, в первую очередь, относятся FeCl3 (E о = 0,780 В), FeCl2 (E о = 1,163 В), AlCl3 (E о = 1,730 В) и ряд других хлоридов.
Приведенные данные по напряжению разложения относятся к равновесным условиям при плотности тока на электродах, близкой к нулю. С повышением плотности тока напряжение разложения растет и на промышленных электролизерах при плотности тока 0,22-0,25 А/см2 составляет 2,70-2,75 В.
В процессе электролиза концентрация MgCl2 в электролите снижается, его напряжение разложения увеличивается, соответственно повышается вероятность совместного разряда ионов магния и щелочных металлов.
При повышенных, начиная с 20 %, концентрациях MgCl2 равновесие реакции
MgCl2 + Mg = 2MgCl
сдвигается вправо с образованием одновалентных ионов магния, легко подверженных окислению в объеме расплава растворенным хлором и кислородом, так как = -3,24 В.
Для достижения максимальных выходов по току подбираются наиболее оптимальные условия (параметры) циркуляции электролита, снижающие возможность соприкосновения выделяющегося хлора с плавающими корольками магния. Повышение температуры при электролизе магния сверх оптимальной (720-730 °С) приводит к быстрому падению выхода по току. Это объясняется более интенсивным окислением магния хлором, кислородом и влагой, а также уменьшением разницы между плотностью электролита и магния.
Чистая поверхность катода хорошо смачивается магнием и на ней образуются крупные капли осаждаемого металла. Образование пассивирующей пленки на катоде, состоящей, в основном, из оксида магния и дисперсного железа, способствует образованию мелких корольков магния. Покрытые оксидом магния корольки уносятся в анодную зону, где постепенно окисляются хлором. Добавки CaF2 или NaF благоприятствуют образованию более крупных капель магния за счет десорбции МgО с мелких частиц металла. Пассивную пленку в настоящее время очищают механически или посредством выделения щелочного металла на катоде при электролизе обедненного электролита. После очистки катода и добавки свежей порции хорошо обезвоженного электролита выделяющийся магний вновь смачивает поверхность катода.
В отечественной магниевой промышленности в разные периоды ее развития нашли применение электролизеры с боковым, нижним и верхним вводом анодов. Каждый из этих электролизеров имеет свои конструктивные особенности, преимущества и недостатки. На карналлитовой схеме питания (рис.2) работают обычно электролизеры с боковым и нижним вводом анодов, на расплаве хлористого магния – более мощные с верхним вводом анодов. Для каждого типа электролизеров применимы определенные способы интенсификации. Для электролизеров с боковым и нижним вводом анодов следует изыскать пути снижения степени разрушения анодов, футеровки. На электролизерах с верхним вводом анодов более важным является полное и своевременное удаление из электролита примесей. Однако проблемами, общими для всех типов электролизеров, являются минимизация или исключение шламообразования в электролизере, удаление пассивирующего осадка с катода, активизация рабочей поверхности катода. Без решения этих задач невозможно создать автоматизированный безотходный электролизер с высокими показателями.
В связи с технологическими особенности поточной линии (рис.3) главными факторами интенсификации процесса электролиза являются герметизация электролизеров и переточных каналов, тщательная очистка сырья от примесей в голове технологической линии и создание герметичного безотходного проточного электролизера. Количество твердых отходов сводится к минимуму при установке над головным агрегатом бесшламового плавильника карналлита. Срок службы проточных электролизеров можно повысить до 4-5 лет.
|
Лабораторное оборудование. Электролитическая ячейка для получения магния, представляющая собой тигель (стакан) из термо- и коррозионно-стойких материалов (фарфор, кварц, алунд), установленный в электрической печи сопротивления, обеспечивающей заданный температурный режим электролиза.
Электроды смонтированы на подвижном штативе, допускающем их вертикальное перемещение, а также изменение межполюсного расстояния. Анод выполнен из графита, катод – из стали. Электродные пространства разделены керамической перегородкой.
Источником постоянного поляризующего напряжения является селеновый выпрямитель с измерительными приборами, установленными на выходе (вольтметр, амперметр). Регулировка выходного напряжения осуществляется изменением питающего напряжения, подаваемого от автотрансформатора. Точная регулировка выходного напряжения производится потенциометрически включенным реостатом.
Поддержание температуры в электрической печи производится с помощью регулирующего пирометрического милливольтметра ХА-группы, обеспечивающего включение (отключение) силовой цепи печного нагревателя.
Содержание задания. Сведения о составе и количестве магниевого электролита, реактивах, используемых для его приготовления, технологическом режиме электролиза (температура, сила тока, продолжительность и др.) и рекомендации по выполняемым расчетам и обработке экспериментальных данных.
Порядок работы
1. Рассчитать и приготовить необходимые навески солей. Загрузить в плавильный тигель навеску смеси предварительно просушенных хлоридов натрия и калия, обезвоженных хлоридов магния и кальция. Включить печь на нагрев. После расплавления навески и достижения температуры в печи 720-730 °С выдержать расплав при данной температуре 20-30 мин. Затем аккуратно вылить расплав в предварительно прогретую стальную изложницу, чтобы отделить электролит от шлама, остающегося на дне тигля.
2. Плав солей загрузить в электролитическую ячейку и разогреть до температуры электролиза.
3. Под наблюдением преподавателя ввести в расплав и зафиксировать анод. Тщательно очищенный и взвешенный катод опустить в электролит в поляризованном состоянии (при напряжении около 2 В) и сразу же установить требуемую силу тока, чтобы поверхность катода не успела окислиться.
4. Провести электролиз в течение 1-1,5 ч. По ходу электролиза записывать регистрируемые величины каждые 10-15 мин (см. таблицу). Корректировку тока I эл на ванне до заданной величины производить по мере изменения путем регулировки напряжения U эл. Обратную ЭДС (E) определить методом отключения электролитической ячейки. Изменения в характере работы печного агрегата должны быть зафиксированы в таблице. Обязательно также регистрировать время работы печи при той или иной нагрузке.
|
|
История развития хранилищ для нефти: Первые склады нефти появились в XVII веке. Они представляли собой землянные ямы-амбара глубиной 4…5 м...
История создания датчика движения: Первый прибор для обнаружения движения был изобретен немецким физиком Генрихом Герцем...
Своеобразие русской архитектуры: Основной материал – дерево – быстрота постройки, но недолговечность и необходимость деления...
Эмиссия газов от очистных сооружений канализации: В последние годы внимание мирового сообщества сосредоточено на экологических проблемах...
© cyberpedia.su 2017-2024 - Не является автором материалов. Исключительное право сохранено за автором текста.
Если вы не хотите, чтобы данный материал был у нас на сайте, перейдите по ссылке: Нарушение авторских прав. Мы поможем в написании вашей работы!