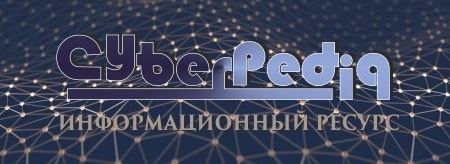
Индивидуальные и групповые автопоилки: для животных. Схемы и конструкции...
Кормораздатчик мобильный электрифицированный: схема и процесс работы устройства...
Топ:
Теоретическая значимость работы: Описание теоретической значимости (ценности) результатов исследования должно присутствовать во введении...
Определение места расположения распределительного центра: Фирма реализует продукцию на рынках сбыта и имеет постоянных поставщиков в разных регионах. Увеличение объема продаж...
История развития методов оптимизации: теорема Куна-Таккера, метод Лагранжа, роль выпуклости в оптимизации...
Интересное:
Наиболее распространенные виды рака: Раковая опухоль — это самостоятельное новообразование, которое может возникнуть и от повышенного давления...
Что нужно делать при лейкемии: Прежде всего, необходимо выяснить, не страдаете ли вы каким-либо душевным недугом...
Берегоукрепление оползневых склонов: На прибрежных склонах основной причиной развития оползневых процессов является подмыв водами рек естественных склонов...
Дисциплины:
![]() |
![]() |
5.00
из
|
Заказать работу |
|
|
Характеристика шлицевых соединений
Шлицевое соединение образуют выступы (зубья) на валу (рис. 1, 2, 3), входящие в соответствующие впадины (шлицы) в ступице.
Рабочими поверхностями являются боковые стороны выступов.
Выступы на валу выполняют фрезерованием, строганием или накатыванием в холодном состоянии профильными роликами по методу продольной накатки. Впадины в отверстии ступицы изготовляют протягиванием или долблением.
Условно можно представить шлицевое соединение, как многошпоночное соединение, у которого шпонки выполнены как одно целое с валом.
Основное назначение шлицевых соединений - передача вращающего момента между валом и ступицей. При этом ступица может быть закреплена на колесе, фланце, шкиве, ролике или другом валу (карданный вал).
Шлицевые соединения стандартизованы и широко распространены в машиностроении.
Достоинства шлицевых соединений по сравнению со шпоночными:
· Способность точно центрировать соединяемые детали или точно выдерживать направление при их относительном осевом перемещении.
· Меньшее число деталей соединения (шлицевое соединение образуют две детали, шпоночное – три).
· Большая несущая способность вследствие большей суммарной площади контакта.
· Взаимозаменяемость (нет необходимости в ручной пригонке).
· Большая усталостная прочность вследствие меньшей концентрации напряжений изгиба, особенно для эвольвентных шлицев.
· Меньшая длина ступицы и меньшие радиальные зазоры.
· Большая надежность при динамических нагрузках.
Недостатки шлицевых соединений - более сложная технология изготовления (зубофрезерование, протягивание, шлифование), а следовательно, более высокая стоимость.
|
***
Классификация шлицевых соединений
Шлицевые соединения различают:
· по характеру соединения - неподвижные для закрепления детали на валу; подвижные, допускающие перемещение вдоль вала (например, блока шестерен коробки передач; шпинделя сверлильного станка, карданного вала автомобиля);
· по форме выступов - прямобочные, эвольвентные, треугольные.
Шлицевые соединения с эвольвентным профилем
Соединения с эвольвентным профилем (рис. 1,б) применяют в неподвижных и подвижных соединениях. Боковая поверхность выступа очерчена по эвольвенте (как профиль зубьев зубчатых колес).
Эвольвентный профиль отличается от прямобочного повышенной прочностью в связи с утолщением выступа к основанию и плавным переходом в основании.
Соединения обеспечивают высокую точность центрирования; они стандартизованы - за номинальный диаметр соединения принят наружный диаметр D.
По сравнению с прямобочным, соединение с эвольвентным профилем характеризует большая нагрузочная способность вследствие большей площади контакта, большего количества зубьев и их повышенной прочности. Применяют для передачи больших вращающих моментов. Шлицевые соединения с эвольвентным профилем шлицев считаются наиболее перспективными.
Применяют центрирование по боковым поверхностям S зубьев, реже - по наружному диаметру D.
Шлицевые соединения с треугольным профилем
Соединения с треугольным профилем (рис. 1,в) изготовляют по отраслевым нормалям. Применяют в неподвижных соединениях. Имеют большое число мелких выступов–зубьев ( z = 20...70; т = 0,2...1,5мм). Угол β профиля зуба ступицы составляет 30°, 36° или 45°. Применяют центрирование только по боковым поверхностям, точность центрирования невысокая.
Применяют для передачи небольших вращающих моментов тонкостенными ступицами, пустотелыми валами, а также в соединениях торсионных валов, стальных валов со ступицами из легких сплавов, в приводах управления (например, привод стеклоочистителя автомобиля).
|
Соединения с треугольным профилем применяют также при необходимости малых относительных регулировочных поворотов деталей. Шлицевые валы и ступицы изготовляют из среднеуглеродистых и легированных сталей с временным сопротивлением σв > 500МПа.
***
Материалы и допускаемые напряжения смятия
Шлицевые валы и ступицы изготовляют из среднеуглеродистых и легированных сталей с временным сопротивлением σв > 500 Н/мм2 (МПа).
В Таблице 1 приведены значения [σ]см, принятые с учетом опыта эксплуатации при длительном сроке службы. Большие значения [σ]см принимают при легких режимах работы, когда соединение большую часть времени нагружено моментами, значительно меньшими максимально длительно действующего вращающего момента.
Таблица 1. Допускаемые напряжения смятия при средних условиях эксплуатации
Тип соединения | [σ]см, Н/мм2 | |
≤ 350 HB | > 40 HRC | |
Неподвижное | 60... 100 | 100... 140 |
Подвижное | 20... 30 | 30... 60 |
Подвижное под нагрузкой | - | 5... 15 |
Примечание: допускаемые напряжения приведены для средних условий эксплуатации: знакопостоянная переменная нагрузка с амплитудой ≤ 10% от постоянной, соединение смазывается.
***
Пример расчета шлицевого соединения
Задача
Подобрать шлицевое неподвижное соединение зубчатого колеса с валом.
Соединение передает вращающий момент Т = 210 Нм.
Условия эксплуатации средние, режим работы – тяжелый.
Диаметр вала d = 45 мм, материал колеса и вала – сталь марки 45 с термической обработкой – улучшение, твердость H = 290 HB.
Решение
Проектировочный расчет
1. Выбор соединения. Принимаем наиболее распространенное прямобочное соединение с центрированием по наружному диаметру.
2. Размеры соединения. По Таблице 2 находим параметры зубьев легкой серии.
Для диаметра вала d = 45 мм:
z × d × D = 8 × 46 × 50, f = 0,4 мм.
Средний диаметр dср и рабочая высота зуба h:
dср = 0,5(D + d) = 0,5(50 + 46) = 48 мм;
h = 0,5(D – d) – 2f = 0,5(50 – 46) - 2×0,4 = 1,2 мм.
3. Допускаемые напряжения. Для неподвижного соединения при средних условиях эксплуатации, тяжелом режиме работы и твердости материала H < 350 HB по Таблице 1 принимаем [σ]см = 60 Н/мм2.
4. Расчетная длина зубьев. Из формулы (1) при Кз = 1,3, получаем:
lр = 2×103ТКз / dсрzh[σ]см = (2000×210×1,3) / (48×8×1,2×60) = 19,7 мм.
5. Длина ступицы колеса:
|
lст = lр + 6 мм = 19,7 + 6 = 25,7 мм.
Принимаем для длины ступицы ближайшее большее значение из ряда нормальных линейных размеров:
lст = 26 мм.
***
Рекомендации по конструированию шлицевых соединений
При проектировании и конструировании шлицевых соединений следует учитывать изложенные ниже рекомендации, основанные на опыте эксплуатации и аналитических выводах:
1. Для подвижных соединений рекомендуется рабочую длину ступицы принимать не меньше диаметра вала, т. е. lр ≥ d.
При коротких ступицах при перемещении их вдоль вала возможно защемление от перекоса.
2. В длинных ступицах ( lст > 1,5 d ) необходима расточка отверстия для выхода стружки при протягивании.
3. Для облегчения входа протяжки и сборки соединения в отверстии ступицы выполняют фаски f.
4. В соединениях, воспринимающих радиальные нагрузки (зубчатые и червячные колеса, звездочки, шкивы и т. п.), зубья соединения желательно располагать симметрично относительно венцов колес, звездочек и т. д.
5. Для уменьшения изнашивания следует уменьшать зазоры в соединении, повышать точность изготовления и твердость рабочих поверхностей.
15. Назначение и разновидности механических передач. Основные силовые энергетические и кинематические соотношения для механических передач вращательного движения.
Механические передачи.
Назначение и роль передач в механизмах и машинах. Классификация меха-нических передач. Передачи трением (с непосредственным контактом и с гибкой связью) и зацеплением. Основные кинематические и энергетические соотношения для передач вращательного движения. Материал изготовления зубчатых колес.
Большинство современных машин создается по схеме двигатель– передача–исполнительный орган машины (рис. 2.1).
Двигатель
Передача
Рабочий орган машины
Рис. 2.1. Схема машины
Как правило, двигатели для уменьшения массы и габаритов выполняют быстроходными с узким диапазоном регулирования скоростей. Непосред-ственное соединение двигателя с рабочим органом применяется редко (вен-тиляторы); как правило, между ними устанавливают промежуточный меха-низм – передачу.
|
Передачами называют механизмы, служащие для передачи механиче-ской энергии на расстояние.
Функции передачи энергии совмещают с решением следующих основ-ных задач:
согласование угловых скоростей исполнительных органов машин дви-гателей(двигатели имеют большие скорости, исполнительные органы ма-шины для выполнения своих функций часто требуют больших моментов при относительно малых скоростях);
регулирование и реверсирование (изменение направления) скорости исполнительного органа машины при постоянной угловой скорости двигате-ля; преобразование вращательного движения двигателя в поступательное или другое движение исполнительного органа машины;
приведение в движение нескольких исполнительных органов (с раз-личными скоростями движения) от данного двигателя.
Наиболее распространены механические передачи вращательного дви-жения, что связано с возможностью обеспечения его непрерывности и рав-номерности при малых потерях на трение.
По принципу движения от ведущего звена к ведомому передачи делят-ся на две группы: 1) передачи трением, имеющие непосредственный контакт жестких тел (фрикционные) или гибкую связь (ременные); 2) передачи за-
цеплением, имеющие непосредственный контакт твердых тел (зубчатые, вин-товые и червячные) или гибкую связь (цепные, зубчатые ременные).
ЗУБЧАТЫЕ ПЕРЕДАЧИ
Зубчатая передача относится к передачам зацеплением с непосред-ственным контактом пары зубчатых колес и предназначена в основном для передачи вращательного движения. Меньшее зубчатое колесо принято назы-вать шестерней, большее – колесом. Термин «зубчатое колесо» относится как
к шестерне, так и к колесу. Зубчатые передачи – самый распространенный вид механических передач, так как могут надежно передавать мощности от долей ватт до десятков тысяч киловатт при окружных скоростях до 150 м/с.
Достоинства:
высокая нагрузочная способность; малые габариты (рис. 4.1);
большая надежность и долговечность (до 40 000 ч);
постоянство передаточного числа;
высокий КПД (до 0.97-0.98 в одной ступени);
сравнительно малые нагрузки на валы и подшипники;
простота обслуживания.
3000
0 | |||
3 | |||
0 | |||
цепная | 1 | ||
∅700 | |||
0 | |||
5 | |||
0 | |||
2 | |||
∅ | 0 | ||
7 | |||
6 | |||
∅ |
плоскоременная
клиноременная | зубчатая |
Рис. 2.1. Габариты передач
Недостатки:
высокие требования к точности изготовления и монтажа;
шум при больших скоростях;
|
высокая жесткость, не позволяющая гасить динамические нагрузки.
НИЯ
В зубчатых передачах вращение от одного колеса к другому передается си-лами в точках контакта боковых поверхностей зубьев. Поверхности взаимо-действующих зубьев, обеспечивающие постоянное передаточное число, называют сопряженными поверхностями. Для получения таких поверхностей профили зубьев должны быть очерчены кривыми, подчиняющимися опреде-ленным законам. Эти законы вытекают из основной теоремы эвольвентно-го зацепления: общая нормальNNк профилям зубьев,проведенная черезточку их касания S (рис. 4.3а), в момент прохождения через полюс зацепле-нияП делит межосевое расстояние О1О2 на отрезки обратно пропорциональ-но угловым скоростям.
Для доказательства теоремы рассмотрим пару сопряженных зубьев в зацеп-лении (см. рис. 4.3б). Профили зубьев касаются в точке S. Расстояние аw между центрами вращения О1О2 неизменно. Проведем через точку касания S общие для обоих профилей касательную ТТ и нормаль NN. Окружные скоро-сти точки S относительно центров v1 = O1S·ω1 и v2 = O2S·ω2.
Характеристика шлицевых соединений
Шлицевое соединение образуют выступы (зубья) на валу (рис. 1, 2, 3), входящие в соответствующие впадины (шлицы) в ступице.
Рабочими поверхностями являются боковые стороны выступов.
Выступы на валу выполняют фрезерованием, строганием или накатыванием в холодном состоянии профильными роликами по методу продольной накатки. Впадины в отверстии ступицы изготовляют протягиванием или долблением.
Условно можно представить шлицевое соединение, как многошпоночное соединение, у которого шпонки выполнены как одно целое с валом.
Основное назначение шлицевых соединений - передача вращающего момента между валом и ступицей. При этом ступица может быть закреплена на колесе, фланце, шкиве, ролике или другом валу (карданный вал).
Шлицевые соединения стандартизованы и широко распространены в машиностроении.
Достоинства шлицевых соединений по сравнению со шпоночными:
· Способность точно центрировать соединяемые детали или точно выдерживать направление при их относительном осевом перемещении.
· Меньшее число деталей соединения (шлицевое соединение образуют две детали, шпоночное – три).
· Большая несущая способность вследствие большей суммарной площади контакта.
· Взаимозаменяемость (нет необходимости в ручной пригонке).
· Большая усталостная прочность вследствие меньшей концентрации напряжений изгиба, особенно для эвольвентных шлицев.
· Меньшая длина ступицы и меньшие радиальные зазоры.
· Большая надежность при динамических нагрузках.
Недостатки шлицевых соединений - более сложная технология изготовления (зубофрезерование, протягивание, шлифование), а следовательно, более высокая стоимость.
***
|
|
История создания датчика движения: Первый прибор для обнаружения движения был изобретен немецким физиком Генрихом Герцем...
Адаптации растений и животных к жизни в горах: Большое значение для жизни организмов в горах имеют степень расчленения, крутизна и экспозиционные различия склонов...
Опора деревянной одностоечной и способы укрепление угловых опор: Опоры ВЛ - конструкции, предназначенные для поддерживания проводов на необходимой высоте над землей, водой...
Поперечные профили набережных и береговой полосы: На городских территориях берегоукрепление проектируют с учетом технических и экономических требований, но особое значение придают эстетическим...
© cyberpedia.su 2017-2024 - Не является автором материалов. Исключительное право сохранено за автором текста.
Если вы не хотите, чтобы данный материал был у нас на сайте, перейдите по ссылке: Нарушение авторских прав. Мы поможем в написании вашей работы!