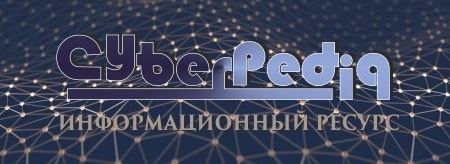
История развития пистолетов-пулеметов: Предпосылкой для возникновения пистолетов-пулеметов послужила давняя тенденция тяготения винтовок...
Историки об Елизавете Петровне: Елизавета попала между двумя встречными культурными течениями, воспитывалась среди новых европейских веяний и преданий...
Топ:
Отражение на счетах бухгалтерского учета процесса приобретения: Процесс заготовления представляет систему экономических событий, включающих приобретение организацией у поставщиков сырья...
Проблема типологии научных революций: Глобальные научные революции и типы научной рациональности...
Характеристика АТП и сварочно-жестяницкого участка: Транспорт в настоящее время является одной из важнейших отраслей народного хозяйства...
Интересное:
Наиболее распространенные виды рака: Раковая опухоль — это самостоятельное новообразование, которое может возникнуть и от повышенного давления...
Принципы управления денежными потоками: одним из методов контроля за состоянием денежной наличности является...
Что нужно делать при лейкемии: Прежде всего, необходимо выяснить, не страдаете ли вы каким-либо душевным недугом...
Дисциплины:
![]() |
![]() |
5.00
из
|
Заказать работу |
|
|
Механические свойства при растяжении, как и при других статических испытаниях, могут быть разделены на три основные группы: прочностные, пластические и характеристики вязкости. Прочностные свойства – это характеристики сопротивления материала образца деформации или разрушению. Большинство стандартных прочностных характеристик рассчитывают по положению определённых точек на диаграмме растяжения, в виде условных растягивающих напряжений.
Предел пропорциональности, пц – максимальное напряжение до которого наблюдается прямая пропорциональность между растягивающей нагрузкой Р и абсолютным удлинением ℓ (или между нормальным напряжением и относительной деформацией на условной диаграмме растяжения).
Предел текучести (физический), т – наименьшее напряжение, при котором образец деформируется без заметного увеличения растягивающей нагрузки (соответствует нагрузке Рт, на рис. 2 в, пунктир).
Предел текучести условный, 0,2 – напряжение, при котором остаточное удлинение достигает 0,2 % длины участка образца, удлинение которого принимается в расчет при определении указанной характеристики.
Временное сопротивление, вс – напряжение, соответствующее наибольшей нагрузке max предшествующей разрушению образца.
Истинное сопротивление разрыву, Sк – напряжение, определяемое отношением нагрузки Рк в момент разрыва к площади минимального поперечного сечения образца в момент разрыва Fк.
Относительное удлинение после разрыва, 10 – отношение приращения расчетной длины образца после разрыва к ее первоначальной величине.
Относительное сужение после разрыва, – отношение разности начальной площади и минимальной площади поперечного сечения образца после разрыва к начальной площади поперечного сечения образца.
|
2. Испытания на сжатие
Пластичные материалы на растяжение и на сжатие работают примерно одинаково и основным видом испытания для них является испытание на растяжение, а испытание на сжатие носит вспомогательный характер.
Хрупкие материалы (чугун, кирпич, раствор, бетон и др.) на сжатие работают значительно лучше, чем на растяжение (к примеру у бетона предел прочности на сжатие раз в 10 больше предела прочности на растяжение). В силу чего хрупкие материалы применяются в основном в сжатых элементах конструкций, поэтому основным видом испытаний хрупких материалов является испытание на сжатие.
Схема испытания на сжатие и геометрия используемых образцов показаны на рис. 5. Испытания проводят на тех же машинах, что и на растяжение. Образец устанавливают на опорную плиту в нижнем захвате и сжимают подвижным захватом. По мере сжатия на торцовых поверхностях образца возникают силы трения, направленные по радиусам к его центру и препятствующие деформации в горизонтальном направлении. В результате образец приобретает характерную бочкообразную форму, а схема напряжённого состояния усложняется и становится различной в разных точках. В точках 1 и 2, например, возникает схема объемного сжатия, а в точке 3 – равномерное плоское напряжённое состояние. Результаты испытаний на сжатие зависят от условий проведения эксперимента. Практически очень трудно добиться приложения сжимающей силы точно по оси образца. Поэтому образец будет не только сжиматься, но и изгибаться. Чем длиннее образец, тем больше влияние изгиба (попробуйте сжать длинный и тонкий прутик). Для уменьшения влияния изгиба рекомендуется применять образцы, длина которых не более чем в два раза превышает их поперечные размеры. Применение слишком коротких образцов тоже нежелательно. При сжатии образца продольные размеры уменьшаются, а поперечные увеличиваются (по закону Пуассона). Вследствие трения между торцами образца и опорными плитами машины увеличение поперечных размеров на середине и по краям образца неодинаковы (по краям меньше) и образец принимает бочкообразную форму, что у образцов из пластичных материалов видно невооруженным глазом.
|
Рис. 5 - Схема (а) и формы образцов (б-г) для испытания на сжатие
На рис. 6 приведены диаграммы, полученные при испытании на сжатие цилиндрических образцов из среднеуглеродистой стали одинакового диаметра d0, но с различным начальным отношением h0/d0.
Рис. 6 - Диаграммы сжатия цилиндрических образцов из стали 45
Как видно из этих данных, при переходе от относительно длинных образцов с начальным отношением h0/d0 = 2 к коротким образцам (h0/d0 = 0,5) сопротивление пластическому деформированию существенно возрастает.
Для пластичных материалов величины пределов текучести, определенные из опытов на растяжение и сжатие, оказываются близкими друг к другу.
При сжатии образцов из хрупкого материала, разрушение происходит по плоскостям, параллельным оси образца или по плоскостям, наклоненным к оси под углом 45°, совпадающим с направлением площадок, по которым действуют максимальные касательные напряжения. Поэтому испытанию на сжатие подвергают главным образом хрупкие материалы, которые, как правило, лучше сопротивляются сжатию, чем растяжению, и применяются для изготовления элементов, работающих на сжатие.
3. Испытания на изгиб
Испытание на изгиб — один из основных и широко распространенных видов испытания материалов — рекомендуется для определения механических свойств хрупких и малопластичных при растяжении металлов (чугунов, инструментальных сталей, литых сталей и сплавов), чувствительных к перекосу и требующих специальных мер его предотвращения при испытании на растяжение. Этот метод применяется, для оценки склонности к хрупкому разрушению высокопрочных сталей (метод «приборного изгиба»), а также при определении вязкости разрушения и чувствительности к острым трещинам.
Испытания на изгиб можно проводить на любой универсальной испытательной машине, используемой для испытаний на растяжение. Образец устанавливают на опорную плиту в нижнем захвате и деформируют изгибающим ножом, крепящемся в верхнем захвате машины. Образец изгибается при опускании верхнего или подъёме нижнего захвата. При этом на диаграммной ленте может быть записана диаграмма изгиба в координатах нагрузка Р – стрела прогиба f. Для пластичного материала диаграмма выглядит так, как показана на рис. 10. Если материал хрупкий, то кривая обрывается в точке b. Знание величины нагрузок Рпц, Рупр, Рт и Рb позволяет определить пределы пропорциональности упругости, текучести и прочности на изгибе.
|
Рис. 7 - Технологическая проба на изгиб: а – образец перед испытанием; б – загиб до определённого угла; в – загиб до параллельности сторон; г – загиб до соприкосновения сторон
Образцы для испытаний на изгиб не имеют головок. Это еще одно преимущество по сравнению с растяжением, так как изготовление образцов с головками, особенно из хрупких материалов, значительно сложнее. На изгиб испытывают прямоугольные или цилиндрические стержни. Для определения свойств отливок из чугуна используют цилиндрические образцы диаметром 30±1 и длиной 340 или 650 мм (при растяжении между опорами 300 и 600 мм соответственно). Для исследовательских целей испытания на изгиб обычно ведут на цилиндрических образцах с d0 = 2-10 мм и расстоянием между опорами l > d0 или плоских образцах с высотой b=1-3, шириной h=3-15 мм и t≥10h. Для оценки характеристик конструкционной прочности рекомендуется применять образцы большого сечения до 30×30 мм.
Сравнение полученных показателей дает возможность выбора стали, способной выдерживать больший изгиб и высокие нагрузки, а также обеспечить точность расчетов на прочность конструкций, работающих в условиях изгиба с растяжением.
Использование предлагаемого способа испытания позволяет получить достоверные значения механических характеристик и обеспечить повышение точности расчетов на прочность конструкций, работающих в условиях изгиба с растяжением, в том числе труб, эксплуатирующихся в условиях наклонных скважин, а также проволоки, профиля и труб при изготовлении с намоткой на барабан.
4. Испытания на кручение
Испытание на кручение является одним из основных методов определения механических свойств Материалов, используемых в деталях, работающих на кручение. Этим методом можно также оценивать пластичность материалов, хрупких при растяжении; Определение при испытании на кручение модуля сдвига G позволяет вычислить коэффициент Пуассона . В отличие от растяжения при кручении форма образца практически не изменяется даже при очень больших деформациях, что облегчает оценку напряжений и деформаций в этой области. Испытания на кручение позволяют наиболее строго в сравнении с другими видами механических испытаний дифференцировать характер разрушения.
|
На кручение испытываются, как правило, цилиндрические образцы сплошного круглого, реже — трубчатого сечения, иногда для специальных целей — квадратного или иной формы сечения. Головкам образцов придают квадратную форму или круглую с лысками.
При испытании к утолщенным головкам образца прикладываются два равных по величине и взаимно противоположных по направлению момента вращения, действующих в плоскостях, нормальных к оси. При этом в рабочей части образца создается плоское напряженное состояние чистого сдвига. В поперечных сечениях действуют только касательные напряжения, наибольшие у поверхности; такие же касательные напряжения действуют в продольных сечениях образца, проходящих через его ось. В сечениях, наклоненных к оси, возникают нормальные напряжения (растягивающие — в одном направлении и сжимающие - в перпендикулярном); наибольшие, главные (нормальные) напряжения действуют у поверхности по площадкам, наклоненным под углом 45° к оси, они равны по величине наибольшим касательным напряжениям.
Различно ориентированные при кручении плоскости действия наибольших касательных и нормальных напряжений позволяют отчетливо отличить разрушение от среза и от отрыва (рис. 8) и соответственно определить величины сопротивления срезу и сопротивления отрыву, как это сделано, например, при определении сопротивления разрушению (отрыву или срезу) в зависимости от содержания углерода в стали. Хрупкое состояние материала характеризуется появлением трещины и распространением разрушения по винтовой поверхности. Пластичные, материалы разрушаются от сдвига, как правило, в плоскости поперечного сечения образца. Дополнительные расслоения и разрушения по продольному направлению свидетельствуют о неоднородности структуры материала.
Рис. 8 - Типы разрушения при кручении: а – от среза; б – от отрыва;
в – при неоднородной структуре
Испытания на кручение осуществляется на машинах с механическим приводом, преимущественно с горизонтальным расположением образца, обеспечивающих надёжную центровку образца и гарантирующих отсутствие изгибающих усилий, возможность достаточно точного задания и измерения величины крутящего момента. Максимальный крутящий момент изменяется от 60Нм до 2МНм. В качестве меры деформации в процессе испытания фиксируется угол закручивания φ.
|
Рис. 9 - Схема горизонтальной машины для испытаний на кручение
На рис. 9 дана принципиальная схема горизонтальной испытательной машины с маятниковым силоизмерителем. Образец 13 крепится в захватах 4 и 5. Левый захват не связан с приводом и может перемещаться в горизонтальном направлении по направляющим 7 и 8. Правый захват устанавливается в неподвижном подшипнике 14 и получает вращение от червячного колеса 2, приводимого в движение электродвигателем через редуктор и вал 1. Число оборотов и угол закручивания активного захвата 45 можно определить по неподвижной круговой шкале с помощью указателя 3, который вращается вместе с захватом. второй захват 5 жестко связан с тяжелым маятником 11. Меняя груз или переставляя штангу 12 в вертикальное положение относительно захвата, можно менять масштаб шкалы силоизмерителя. Вращение захвата 5 вместе с маятником 11 создаёт крутящий момент, направленный противоположно этому вращению и равный моменту кручения, переданному на образец активным захватом 4. Отклонение маятника 11 от вертикального положения приводит к перемещению конца 6 штанги 12, затем стержня 9 и стрелки 10 силоизмерителя. Перемещение стрелки прямо пропорционально моменту кручения Мкр, который служит мерой сопротивления образца деформации, заменяя при кручении усилие Р, измерявшееся в других статических испытаниях.
3. Методы определения твёрдости материалов
Твердостью называется свойство материала оказывать сопротивление проникновению в него другого более твердого тела (индентора), не испытующего остаточной деформации. Внедряемый (вдавливаемый) индентор имеет определенную форму и размеры и не должен получать остаточную деформацию от действия прикладываемых к нему статических или динамических нагрузок. Измерение твердости является одним из самых распространенных и доступных методов механических испытаний, который широко используется в исследовательских целях и как средство (способ) контроля качества свойств материалов в производстве. В отличие от других испытания на твердость очень разнообразны и отличаются друг от друга по форме используемого индентора, условиям приложения нагрузки, способам расчета величины твердости, временем нагружения, твердости испытуемого материала, размеров детали (образца), толщины слоя, твердость которого нужно замерить и т. д. В зависимости от этих факторов твердость может характеризовать упругие и упруго-пластические свойства, сопротивление малым или большим деформациям, а также разрушению. Общим моментом для них является приложение нагрузки при контакте индентора и испытуемого материала. Условия определения твердости, требования к оборудованию, приборам и образцам и т. д. регламентируются государственными стандартами (ГОСТами).
Оценивается твердость так называемыми числами твердости, размерность которых определяется принципом измерения. Числа твердости являются вторичными, производными характеристиками механических свойств, зависящими от первичных, основных – модуля упругости, временного сопротивления и др., от продолжительности действия нагрузки, от способа испытаний и вычисления твердости. Поэтому сравнимые результаты, даже в пределах одного метода, получаются при строгой регламентации процедуры испытаний, которая часто определяется стандартом. Числа твердости для одного и того же материала, определяемые различными способами, получаются различным как по величине, так и по размерности. С помощью специальных таблиц, номограмм или эмпирических формул можно осуществлять пересчет чисел твердости.
В настоящее время существует около 30 разновидностей испытаний на твердость, но наибольшее распространение получили три из них – это методы измерения твердости по Брине́ллю, Рокве́ллу, Виккерсу, а также метод измерения микротвердости. Во всех случаях контакт осуществляется вдавливанием индентора определенной формы и размера со степенью деформации 30…40%. При этом реализуется состояние всестороннего неравномерного сжатия с коэффициентом “мягкости” α>2, что позволяет производить оценку твердости практически любых, в том числе и очень хрупких материалов.
Учитывая неизбежный разброс значений твердости, обусловленный как ошибками измерения, так и неоднородностью механических свойств материала, испытаниям подвергается обычно несколько образцов, а на каждом образце делают несколько вдавливаний индентора. Затем проводят статистическую обработку результатов испытаний, без которой нельзя делать достоверные выводы. При этом число измерений принято называть «выборкой».
Испытание на твердость – простой метод неразрушающего контроля. Экспериментально доказано, что его результаты коррелируют со статистическими характеристиками механических свойств, например, можно статистически достоверно, т.е. с определенной статистической погрешностью – стандартной ошибкой, определять временное сопротивление σв. Она также служит для косвенного суждения с определенной точностью о других характеристиках материала – пределе текучести, временном сопротивлении, склонности к ползучести и др.
Измерение твердости получило широкое распространение, как в заводской практике, так и при выполнении научных исследований. Такие испытания используются в следующих целях:
· для оценки твердости сплавов как характеристики, косвенно отражающей механические свойства;
· для контроля за качеством термических обработок, вызывающих изменение свойств в поверхностном слое, например, цементации, поверхностной закалки, электромеханической обработки и др.;
· для контроля за изменением механических свойств с течением времени эксплуатации (например, контроль за состоянием трубопроводов).
Испытания на твердость менее сложны и не дорогостоящи: они позволяют определять механические свойства и в небольших объемах, допускают текущий контроль изделий в процессе производства и эксплуатации, не влияют на их работоспособность и, что особенно ценно, относятся к неразрушающим методам механических испытаний.
|
|
Семя – орган полового размножения и расселения растений: наружи у семян имеется плотный покров – кожура...
Опора деревянной одностоечной и способы укрепление угловых опор: Опоры ВЛ - конструкции, предназначенные для поддерживания проводов на необходимой высоте над землей, водой...
Индивидуальные и групповые автопоилки: для животных. Схемы и конструкции...
Поперечные профили набережных и береговой полосы: На городских территориях берегоукрепление проектируют с учетом технических и экономических требований, но особое значение придают эстетическим...
© cyberpedia.su 2017-2024 - Не является автором материалов. Исключительное право сохранено за автором текста.
Если вы не хотите, чтобы данный материал был у нас на сайте, перейдите по ссылке: Нарушение авторских прав. Мы поможем в написании вашей работы!