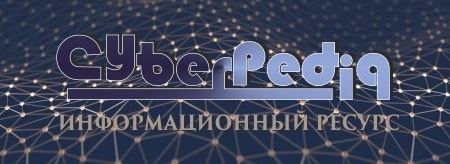
Архитектура электронного правительства: Единая архитектура – это методологический подход при создании системы управления государства, который строится...
Археология об основании Рима: Новые раскопки проясняют и такой острый дискуссионный вопрос, как дата самого возникновения Рима...
Топ:
Процедура выполнения команд. Рабочий цикл процессора: Функционирование процессора в основном состоит из повторяющихся рабочих циклов, каждый из которых соответствует...
Особенности труда и отдыха в условиях низких температур: К работам при низких температурах на открытом воздухе и в не отапливаемых помещениях допускаются лица не моложе 18 лет, прошедшие...
Методика измерений сопротивления растеканию тока анодного заземления: Анодный заземлитель (анод) – проводник, погруженный в электролитическую среду (грунт, раствор электролита) и подключенный к положительному...
Интересное:
Что нужно делать при лейкемии: Прежде всего, необходимо выяснить, не страдаете ли вы каким-либо душевным недугом...
Уполаживание и террасирование склонов: Если глубина оврага более 5 м необходимо устройство берм. Варианты использования оврагов для градостроительных целей...
Принципы управления денежными потоками: одним из методов контроля за состоянием денежной наличности является...
Дисциплины:
![]() |
![]() |
5.00
из
|
Заказать работу |
|
|
Содержание
Введение...........................................................................................................................2
1. Технологический процесс ремонта автоматического регулятора
торможения усл.№ 574Б.................................................................................................6
2. Технологическая карта ремонта автоматического регулятора торможения
усл. №574Б....................................................................................................................18
3. Правила техники безопасности, охраны труда и организации рабочего
места при ремонте автоматического регулятора торможения усл. № 574.........21
Заключение....................................................................................................................24
Список используемых источников..............................................................................26
Введение
Основной вид транспорта в Российской Федерации - железнодорожный. На его долю приходится более 45% и около 27% всего объема соответственно грузовых и пассажирских перевозок (без учёта трубопроводного транспорта - 87 %), выполняемых транспортом общего пользования. Железные дороги, будучи основной транспортной системы Российской Федерации, имеют чрезвычайно важное государственное, экономическое, социальное и оборонное значение. От них требуется своевременное, качественное и полное удовлетворение потребностей населения, грузоотправителей и грузополучателей в перевозках.
Железные дороги располагают различными инженерными сооружениями, техническими устройствами и средствами, основными из которых являются железные пути, подвижной состав (локомотивы и вагоны), локомотивное и вагонное хозяйства, сооружения и устройства сигнализации, связи, электро- и водоснабжения, железнодорожные станции и узлы.
Бесперебойная и безаварийная работа многоотраслевого хозяйства железнодорожного транспорта требует согласованного функционирования всех его звеньев. Для того чтобы с наибольшей эффективностью направить свои усилия на совершенствование перевозочного процесса, каждому специалисту необходимо не только быть профессионалом в своей области, но и обладать знаниями по вопросам, связанным с другими, смежными отраслями железнодорожного транспорта.
|
Условия эксплуатации вагонов связаны со значительными статистическими и динамическими нагрузками, повышенной влажности, агрессивных средств на конструкцию вагонов. Сложная конструкция подвижного состава определяет необходимость его регулярного квалификационного обслуживания. Передовые методы своевременного выявления дефектов подвижного состава является основой предупреждения аварий и крушений.
Эффективность эксплуатации подвижного состава во многом зависит от квалификации осмотрщиков вагонов, их знаний передовой технологии и прогрессивных методов труда. Осмотрщики-ремонтники обязаны обеспечивать включение в поезд только технически исправных вагонов, а также контролировать выполнение необходимого объёма текущего безотцепного ремонта с высоким качеством.
Профессия слесаря подвижного состава интересная и познавательная, а многочисленные размеры и инструменты, для выявления неисправностей деталей, говорят о высоком классе точности и качестве осмотра и ремонта частей и приборов подвижного состава.
Вагономпринято называть не самодвижущуюся единицу подвижного состава, предназначенную для перевозки пассажиров или грузов. Современный парк вагонов состоит из разнообразных их типов и конструкций, которые обусловлены необходимостью удовлетворять основные требования при перевозке: комфорт для пассажиров, сохранность грузов, защита некоторых из них от атмосферных осадков, возможность механизации погрузочно-разгрузочных работ, движение с высокими скоростями, а также обеспечивать минимальные расходы на создание, эксплуатацию и ремонт.
|
Парк грузовых вагонов состоит из полувагонов, платформ, цистерн, крытых, изотермических (ледников и рефрижераторных) вагонов и вагонов специального назначения. Полувагоны - наиболее массовый тип вагонов грузового парка. Они предназначены для перевозки всех сыпучих и навалочных грузов, не требующие защиты от атмосферных осадков, а также длинномерных грузов, машин, контейнеров, строительных конструкций и др. В крытых вагонах перевозят грузы, которые требуют защиты от атмосферных осадков. Платформы используют для перевозки длинных и громоздких грузов, разных машин, в том числе на колесном и гусеничном ходу, и контейнеров; цистерны - для редких и газообразных, изотермические вагоны - для скоропортящихся грузов. Вагоны специального назначения предназначены для перевозки только одного или нескольких родственных грузов, к которым предъявляются единые требования и которые не требуют специального очищения грузового помещения: цементовозы, окатышевозы, для перевозки минеральных удобрений, агломерата, сажи, муки, хопперы-дозаторы и др.
Несмотря на разнообразие типов и конструкций, каждый вагон состоит из кузова, рамы, ходовых частей, автосцепных устройств и тормозов. Кузов предназначен для размещения грузов. Он состоит из боковых н торцевых стен, пола и крыши (у закрытых кузовов). Устройство кузова зависит от типа вагона. Рама воспринимает усилие, которые действуют на вагон. Она состоит из продольных и поперечных балок, жестко соединенных между собой, и является основой кузова, а во многих современных конструкциях вместе с кузовом представляет единую несущую конструкцию. На раме размещенные автосцепные устройства, тормозное оборудование и узлы соединения кузова с кодовыми частями.
Ходовые части служат для плавного движения вагона по рельсовой колее с расчетной скоростью и минимальным сопротивлением. К ним относятся колесные пары, буксы и рессорное подвешивание. Если у вагонов четыре и больше колесные пары, ходовые части объединяются в самостоятельные узлы - тележки. В зависимости от количества колесных пар тележки подразделяют на двух-, трех-, четырех- и многоосные.
Автосцепное устройство предназначено для сцепления вагонов между собой и с локомотивом, а также для передачи и смягчение действия продольных усилий от локомотива до вагона и от одного вагона к другому. Современное автосцепное устройство состоит из автосцепки и поглощающего аппарата. Установлено они из каждой торцевой стороны вагона. Тормоз служит для замедления движения или полной остановки вагона и содержание его на месте. Он состоит из тормозного воздухораспределителя, системы труб, резервуара для сжатого воздуха и рычажной передачи. Все вагоны дорог СНГ оборудованы автоматическими тормозами, а часть дополнительно и ручными тормозами; некоторые пассажирские вагоны - электропневматическими тормозами. Все снова строящиеся вагоны на подшипниках катания оборудуют стояночным тормозом.
|
Основное назначение вагонного хозяйства – обеспечение перевозки пассажиров и грузов, содержание вагонов в исправном состоянии, подготовка их к перевозкам, обслуживанию пассажирских поездов и рефрижераторных вагонов в колее прохождения. Важнейшим требованием при этом есть обеспечения безопасности движения и сохранности перевезенных грузов.
Для бесперебойной эксплуатации вагонного парка и содержания его в исправном состоянии установлена система технического обслуживания и ремонта грузовых вагонов.
Посты испытания автотормозов обосновываются на станциях, где делают испытание автоматических тормозов, при отсутствии на этих станциях ПКТО и ПТО вагонов. Предназначенные для производства пробы тормозов, замены и ремонта тормозного оборудования.
Технология обслуживания вагонов на колеях станций непрерывно совершенствуется; необходимо постоянно согласовывать ее с вопросами улучшения и облегчение условий работы работников пунктов технического обслуживания вагонов (ПТО).
Заключение
Эффективная работа ремонтного персонала во многом зависит от рациональной и экономически выгодной организации ремонтного производства, т.е. широко внедрения прогрессивной техники и технологии, улучшения условий труда, повышения его качества и производительности, распространения и обобщения опыта передовых депо.
Основной проблемой, стоящей перед железнодорожными компаниями, является сокращение эксплуатационных расходов. Одна из наиболее значимых статей этих расходов - затраты на техническое обслуживание и ремонт подвижного состава, которые включают много трудоемких операций, зачастую выполняемых в неблагоприятных условиях. Положение усугубляется недостатком рабочей силы, так как ремонтно-эксплуатационный персонал постепенно "стареет" и выходит на пенсию, а для новых, более молодых рабочих такие работы непривлекательны (судя по своему опыту). Поэтому в последнее время механизации и автоматизации технологического процесса обслуживания и ремонта нужно уделять особое внимание. К числу операций, входящих в процесс ремонта, относятся разборочные.
|
Эти операции имеют свою специфику и практически не встречаются в современном машиностроительном производстве. Кроме того, подлежащие разборке узлы и агрегаты после длительной эксплуатации загрязнены, изношены, крепежные соединения труднодоступны и разнохарактерны, после снятия креплений следует обеспечить целостность высвобождаемых деталей. Все это осложняет разборочные работы и ставит их на одно из последних мест по технико-социальному уровню. Для преодоления указанных затруднений необходимо создать и использовать при разборке подвижного состава устройства, требующие минимально возможных затрат ручного труда.
Нарушение технологии изготовления деталей, сборки, испытаний приводит к своевременному их износу и возможным неисправностям. Для предупреждения неисправностей применяют различные измерительные приборы и бортовые (встроенные) или стационарные устройства диагностики, которые в установленные сроки подвергают плановым осмотрам, ревизиям и проверкам.
Ремонт узла в зависимости от его технического состояния разрешается производить частичной или полной разборкой согласно Правилам ремонта и технологическим инструкциям. Правилами ремонта и технической документацией, предусматривают ряд однотипных проверок и испытаний, позволяющих применять одно и то же оборудование, станки, стенды, инструменты и приспособления, что приводит к увеличению производительности труда, уменьшению времени простоя и, следовательно, к уменьшению себестоимости ремонта.
Велико влияние исправного состояния автотормозных устройств на безопасность подвижного состава. Не выявленные своевременно износы приводят к аварийным ситуациям, вызывая угрозу схода подвижного состава с рельсов.
Учитывая особенности эксплуатации вагонов, современный слесарь должен обладать и применять современные методы объективной оценки фактического технического состояния оборудования вагонов. Уметь диагностировать и прогнозировать оставшийся ресурс, что является ключевым моментом в увеличении межремонтного срока службы вагонов, сокращения простоя их в плановых видах ремонта и ликвидации текущих ремонтов с изъятием вагонов из эксплуатации, что равносильно увеличению масштабов производства заводов – изготовителей без дополнительных затрат на их расширение.
|
Содержание
Введение...........................................................................................................................2
1. Технологический процесс ремонта автоматического регулятора
торможения усл.№ 574Б.................................................................................................6
2. Технологическая карта ремонта автоматического регулятора торможения
усл. №574Б....................................................................................................................18
3. Правила техники безопасности, охраны труда и организации рабочего
места при ремонте автоматического регулятора торможения усл. № 574.........21
Заключение....................................................................................................................24
Список используемых источников..............................................................................26
Введение
Основной вид транспорта в Российской Федерации - железнодорожный. На его долю приходится более 45% и около 27% всего объема соответственно грузовых и пассажирских перевозок (без учёта трубопроводного транспорта - 87 %), выполняемых транспортом общего пользования. Железные дороги, будучи основной транспортной системы Российской Федерации, имеют чрезвычайно важное государственное, экономическое, социальное и оборонное значение. От них требуется своевременное, качественное и полное удовлетворение потребностей населения, грузоотправителей и грузополучателей в перевозках.
Железные дороги располагают различными инженерными сооружениями, техническими устройствами и средствами, основными из которых являются железные пути, подвижной состав (локомотивы и вагоны), локомотивное и вагонное хозяйства, сооружения и устройства сигнализации, связи, электро- и водоснабжения, железнодорожные станции и узлы.
Бесперебойная и безаварийная работа многоотраслевого хозяйства железнодорожного транспорта требует согласованного функционирования всех его звеньев. Для того чтобы с наибольшей эффективностью направить свои усилия на совершенствование перевозочного процесса, каждому специалисту необходимо не только быть профессионалом в своей области, но и обладать знаниями по вопросам, связанным с другими, смежными отраслями железнодорожного транспорта.
Условия эксплуатации вагонов связаны со значительными статистическими и динамическими нагрузками, повышенной влажности, агрессивных средств на конструкцию вагонов. Сложная конструкция подвижного состава определяет необходимость его регулярного квалификационного обслуживания. Передовые методы своевременного выявления дефектов подвижного состава является основой предупреждения аварий и крушений.
Эффективность эксплуатации подвижного состава во многом зависит от квалификации осмотрщиков вагонов, их знаний передовой технологии и прогрессивных методов труда. Осмотрщики-ремонтники обязаны обеспечивать включение в поезд только технически исправных вагонов, а также контролировать выполнение необходимого объёма текущего безотцепного ремонта с высоким качеством.
Профессия слесаря подвижного состава интересная и познавательная, а многочисленные размеры и инструменты, для выявления неисправностей деталей, говорят о высоком классе точности и качестве осмотра и ремонта частей и приборов подвижного состава.
Вагономпринято называть не самодвижущуюся единицу подвижного состава, предназначенную для перевозки пассажиров или грузов. Современный парк вагонов состоит из разнообразных их типов и конструкций, которые обусловлены необходимостью удовлетворять основные требования при перевозке: комфорт для пассажиров, сохранность грузов, защита некоторых из них от атмосферных осадков, возможность механизации погрузочно-разгрузочных работ, движение с высокими скоростями, а также обеспечивать минимальные расходы на создание, эксплуатацию и ремонт.
Парк грузовых вагонов состоит из полувагонов, платформ, цистерн, крытых, изотермических (ледников и рефрижераторных) вагонов и вагонов специального назначения. Полувагоны - наиболее массовый тип вагонов грузового парка. Они предназначены для перевозки всех сыпучих и навалочных грузов, не требующие защиты от атмосферных осадков, а также длинномерных грузов, машин, контейнеров, строительных конструкций и др. В крытых вагонах перевозят грузы, которые требуют защиты от атмосферных осадков. Платформы используют для перевозки длинных и громоздких грузов, разных машин, в том числе на колесном и гусеничном ходу, и контейнеров; цистерны - для редких и газообразных, изотермические вагоны - для скоропортящихся грузов. Вагоны специального назначения предназначены для перевозки только одного или нескольких родственных грузов, к которым предъявляются единые требования и которые не требуют специального очищения грузового помещения: цементовозы, окатышевозы, для перевозки минеральных удобрений, агломерата, сажи, муки, хопперы-дозаторы и др.
Несмотря на разнообразие типов и конструкций, каждый вагон состоит из кузова, рамы, ходовых частей, автосцепных устройств и тормозов. Кузов предназначен для размещения грузов. Он состоит из боковых н торцевых стен, пола и крыши (у закрытых кузовов). Устройство кузова зависит от типа вагона. Рама воспринимает усилие, которые действуют на вагон. Она состоит из продольных и поперечных балок, жестко соединенных между собой, и является основой кузова, а во многих современных конструкциях вместе с кузовом представляет единую несущую конструкцию. На раме размещенные автосцепные устройства, тормозное оборудование и узлы соединения кузова с кодовыми частями.
Ходовые части служат для плавного движения вагона по рельсовой колее с расчетной скоростью и минимальным сопротивлением. К ним относятся колесные пары, буксы и рессорное подвешивание. Если у вагонов четыре и больше колесные пары, ходовые части объединяются в самостоятельные узлы - тележки. В зависимости от количества колесных пар тележки подразделяют на двух-, трех-, четырех- и многоосные.
Автосцепное устройство предназначено для сцепления вагонов между собой и с локомотивом, а также для передачи и смягчение действия продольных усилий от локомотива до вагона и от одного вагона к другому. Современное автосцепное устройство состоит из автосцепки и поглощающего аппарата. Установлено они из каждой торцевой стороны вагона. Тормоз служит для замедления движения или полной остановки вагона и содержание его на месте. Он состоит из тормозного воздухораспределителя, системы труб, резервуара для сжатого воздуха и рычажной передачи. Все вагоны дорог СНГ оборудованы автоматическими тормозами, а часть дополнительно и ручными тормозами; некоторые пассажирские вагоны - электропневматическими тормозами. Все снова строящиеся вагоны на подшипниках катания оборудуют стояночным тормозом.
Основное назначение вагонного хозяйства – обеспечение перевозки пассажиров и грузов, содержание вагонов в исправном состоянии, подготовка их к перевозкам, обслуживанию пассажирских поездов и рефрижераторных вагонов в колее прохождения. Важнейшим требованием при этом есть обеспечения безопасности движения и сохранности перевезенных грузов.
Для бесперебойной эксплуатации вагонного парка и содержания его в исправном состоянии установлена система технического обслуживания и ремонта грузовых вагонов.
Посты испытания автотормозов обосновываются на станциях, где делают испытание автоматических тормозов, при отсутствии на этих станциях ПКТО и ПТО вагонов. Предназначенные для производства пробы тормозов, замены и ремонта тормозного оборудования.
Технология обслуживания вагонов на колеях станций непрерывно совершенствуется; необходимо постоянно согласовывать ее с вопросами улучшения и облегчение условий работы работников пунктов технического обслуживания вагонов (ПТО).
Технологический процесс ремонта автоматического регулятора торможения усл. № 574Б
Авторегулятор служит для автоматического поддержания заданного выхода штока по мере износа колодок. Установлен на тяге ТРП.
В основном на грузовых и пассажирских вагонах применяется авторегулятор 574 Б, который за одно торможение стягивает ТРП на 11мм.
На вагонах, используемых в эксплуатации на крутых затяжных спусках применяются авторегуляторы РТРП – 675, который стягивает ТРП за одно торможение на 20мм.
Оба авторегулятора одинаковой конструкции у РТРП – 675 удлинённый корпус с крышкой. Имеет корпус в виде цилиндра “12” (рис.1). С одной стороны у него ввернута головка “4”, которая фиксируется болтом “5”, с другой стороны развальцована крышка “13”, на наружной поверхности крышки и головки шестигранник под ключ. Через осевое отверстие головки входит регулировочный винт “1”, с этой стороны он имеет двухходовую прямоугольную резьбу, ее наружный участок закрыт защитной трубой “3”. На конце этого винта метрическая резьба под муфту “2”.
Рис.1 Авторегулятор.
Через осевое отверстие крышки входит полый тяговый стержень “14”, внутри в него входит винт “1”. Внутри корпуса расположен стакан “9”, в него с одной стороны ввернута тяговая втулка “10”, а с другой стороны крышка “6”. Они фиксируются винтами. На тяговую втулку действует усилие возвратной пружины “11”, которая установлена с предварительной затяжкой. Внутри стакана регулировочная “8” и вспомогательная гайка “7”, навернутая на регулировочный винт, на эти гайки действуют усилия пружин “18” и “19” через упорные шарикоподшипники. Внутренняя полость заполняется густой смазкой. Ушко регулятора соединяется со штоком ТЦ приводом.
Авторегулятор имеет привод: на грузовых вагонах рычажный (Рис. 2), на пассажирских - стержневой (Рис. 3) и рычажный.
Рис. 2. Стержневой привод регулятора.
Рис. 3. Рычажный привод регулятора.
Для авторегулятора согласно инструкции устанавливают два контрольных зазора:
А – зазор между крышкой корпуса и рычагом (упором). От этого размера зависит выход штока, который будет поддерживать авторегулятор, устанавливается согласно инструкции при постановке на вагон (для грузовых вагонов при чугунных колодках - 40 - 60 мм, а при композиционных - 35-50мм).
а – зазор между торцом защитной трубы и началом резьбы под муфту на регулировочном винте, этот размер наибольший при постановке новых колодок. По мере износа колодок авторегулятор стягивает ТРП и он уменьшается. Согласно инструкции минимальный допустимый размер «а», в грузовых вагонах 150мм, пассажирских 250мм.
Принцип работы. Авторегулятор механического действия, если выход штока в норме, то авторегулятор работает как жесткая тяга:
При торможении шток ТЦ выходит, а через рычаг “8” вправо перемещается стержень “14” регулятора, откуда усилие через головку “4” и вспомогательную гайку “7” передается на регулировочный винт “1”.
По мере износа колодок, выход штока увеличивается. Когда выход будет больше нормы, в момент прижатия крышки корпуса в упор, колодки еще не прижмутся к колесам, поэтому шток выходит дальше. Стержень продолжает перемещаться вправо, а корпус стоит на месте. При этом пружина “11” внутри корпуса сжимается, между головкой и вспомогательной гайкой “7” образуется зазор. Под действием пружины “19” вспомогательная гайка наворачивается на винт и образуется зазор между вспомогательной и регулировочной гайками. В результате - тяга стягивается и размер “а” - уменьшается.
При отпуске тормозов шток уходит в ТЦ, стержень перемещается влево, а за ним, под действием пружины “11” и стакан “9”. Освобождается регулировочная гайка, которая под действием пружины “18” наворачивается на винт до упора во вспомогательную гайку.
За одно торможение ТРП стягивается примерно на 10мм. При этом уменьшается зазор между колодками и колесами и соответственно выход штока.
Снятый с вагона регулятор направляется для очистки, дальнейшей разборки и ремонта в отведенное для этого место отделения автоконтрольного пункта (АКП).
Разборка авторегулятора. Ввиду того что установленная в корпусе регулятора возвратная пружина сжата с силой около 150 кгс, запрещается разбирать и собирать авторегулятор без специального приспособления.
Проектно-конструкторское бюро ПКБ ЦВ МПС разработало технологическую оснастку для разборки, ремонта и сборки бескулисных регуляторов усл. № 536М. В комплект оснастки входят стенд для испытания регуляторов, а также приспособления и инструменты для разборки и сборки регуляторов; весь комплект можно использовать при ремонте регулятора усл. № 574Б.
Комбинированное приспособление для разборки и сборки основных узлов бескулисного авторегулятора (рис. 4) является быстродействующим устройством с пневматическим приводом.
Рис. 4. Комбинированное устройство для разборки и сборки регулятора усл. № 574Б
Приспособление смонтировано на опорной раме, которая устанавливается на стол-верстак, имеющий соответствующие вырезы для размещения силового горизонтального цилиндра 20 и вертикального цилиндра, расположенных ниже опорной плиты 21.
Силовой цилиндр 20 предназначен для сжатия возвратной пружины 7 регулятора. На шток 19 цилиндра свободно насажена серьга 18, которая удерживается двумя гайками 17. В верхнее отверстие серьги вставлен натяжной винт 15 с маховиком 16. Конец натяжного винта имеет резьбу, соответствующую резьбе тягового стержня авторегуляторов усл. 536М и 574Б. Горизонтальный цилиндр 20 приварен к ребрам опорной плиты.
Вертикальный цилиндр (на рисунке не показан) служит для перемещения прижима 6, закрепляющего корпус 4 регулятора на ребрах опорной плиты. Цилиндр 20 имеет двусторонний впуск сжатого воздуха, вертикальный цилиндр -- односторонний.
В ряде случаев можно пользоваться более простым приспособлением для сжатия возвратной пружины (рис. 5). Это приспособление состоит из винта 5, гайки 4 с ленточной двухзаходной резьбой, подшипника 3 и трубы 1 с втулкой 2. Винт на одном конце имеет такую же нарезку, как и ушко регулятора, а на другом- квадрат для удобства ввинчивания в тяговый стержень регулятора. К гайке 4 приварены рукоятки-стержни.
Рис. 5. Приспособление для сжатия возвратной пружины регулятора.
Перед установкой на комбинированное приспособление каждый поступивший в ремонт регулятор должен быть очищен от грязи и проверен на стенде с целью определения предстоящего объема работ.
При разборке корпус авторегулятора устанавливается на У-образных ребрах опорной плиты приспособления таким образом, чтобы его торец упирался во фланец 12 горизонтального цилиндра, как это показано на рис. 2. Затем включают вертикальный силовой цилиндр прижима 6, и корпус регулятора надежно зажимается в приспособлении.
В начале разборки выбивают заклепку 13, вывертывают ушко регулятора 14 и снимают упор 11 привода с тягового стержня 10. Затем регулирующий винт ввертывают в регулятор до тех пор, пока предохранительная гайка 8 не выйдет из тягового стержня 10 со стороны ушка. После этого снимают предохранительную гайку 8, предварительно выбив штифт 9, и полностью вывертывают регулирующий винт из регулятора.
Далее с помощью маховика 16 в тяговый стержень 10 регулятора ввертывают натяжной винт 15, причем нарезанная часть винта должна полностью войти в тяговый стержень во избежание несчастных случаев при последующем сжатии пружины. Из корпуса 4 регулятора вывертывается стопорный болт 3, соединяющий головку 2 с корпусом.
Поворотом трехходового крана впускают сжатый воздух в левую полость горизонтального цилиндра 20. В результате этого поршень вместе со штоком 19, серьгой 18 и винтом 15 перемещается вправо, вытаскивая стержень 10 вместе с узлом стакана 5 и тем самым сжимая возвратную пружину 7. Таким образом, головка 2 регулятора освобождается от нагрузки возвратной пружины 7 и может быть выведена из корпуса 4.
Затем с помощью трехходового крана выпускают сжатый воздух из левой полости горизонтального цилиндра и впускают его в правую полость. Возвратная пружина 7, постепенно разжимаясь, переместит стакан 5 влево до выхода его из корпуса регулятора, после чего тяговый стержень 10 освобождают от натяжного винта 15 приспособления, а стакан 5 со всеми собранными в нем деталями и возвратную пружину 7 вынимают из корпуса регулятора. После этого начинают разборку стакана.
После чего вывертывают крышку 13, предварительно вывернув стопорный винт 12 (М6Х8). Вынимают вспомогательную гайку 10 с подшипником 11 и пружиной 9.
На этом разборка регулятора заканчивается. Все детали промывают в керосине, протирают насухо и подвергают тщательному осмотру и проверке.
Ремонт основных деталей авторегулятора. Головку авторегулятора осматривают с проверкой основных размеров. При наличии трещин, изломов, а также износа резьбы М95Х2 по шагу и диаметру более чем на 0,4 мм или срыва резьбы общей длиной более 1,5 нитки головка регулятора к дальнейшей эксплуатации не допускается. Заусенцы на гранях резьбы разрешается удалять напильником или шабером, а местные забоины и срывы прорезать на токарно-винторезном станке. Забитую резьбу М8 можно прорезать метчиком.
Если на конусной поверхности появляется местный износ глубиной до 0,6 мм, поверхность следует проточить с сохранением конусности 30°. Мелкие риски на этой поверхности удаляются протиркой с пастой ГОИ.
Регулирующий винт, вспомогательная и регулирующая гайки осматривают, их основные размеры проверяют. При наличии трещин, изломов и изношенной резьбы, когда гайки имеют продольное перемещение более 1 мм, детали бракуют.
Заусенцы, задиры, забоины на резьбе должны быть зачищены. Равномерный износ конусной поверхности регулирующей гайки допускается глубиной не более 0,6 мм; при большем износе разрешается поверхность обточить с сохранением конусности 45°.
Пружины, имеющие излом, трещины и другие поверхностные дефекты, бракуют. Заменяют новыми также пружины, имеющие по сравнению с установленными минимальными допусками просадку: возвратная пружина - более чем на 4 м; пружина роспуска - более чем на 1 мм; пружина регулирующей гайки - более чем на 1,5 мм. Проверка высоты пружин выполняется на специальном приспособлении, показанном на рис. 6. Остальные детали регулятора при ремонте также осматриваются и проверяются специальными шаблонами. Задиры и заусенцы на деталях зачищаются, а их рабочие размеры доводятся до чертежных.
Рис. 6. Приспособление для измерения высоты пружины.
Сборка авторегулятора. Сборка регулятора производится по узлам в последовательности, обратной разборке. При сборке все трущиеся поверхности деталей и подшипники смазывают смазкой ЖТКЗ ВТУ ЦТУ № 13-66 или ЦИАТИМ-201 ГОСТ 6267--59.
Вначале в корпус регулятора вставляется возвратная пружина, а затем собирают узел тягового стакана. Корпус стакана зажимают в тисках в вертикальном положении. В него последовательно вставляют пружину 9, подшипник 11, вспомогательную гайку 10 и поджимают эти детали крышкой 13, завертывая ее до совпадения отверстий в ней и в корпус стакана под стопорный винт 12 (М6Х8). Затем ослабляют тиски, переворачивают стакан, вновь закрепляют его в тисках и последовательно вставляют регулирующую гайку 8, подшипник 2, пружину 3, втулку 4, тяговый стержень 6. Все эти детали поджимают гильзой 5, которую завертывают до совпадения отверстий в ней ив корпусе стакана под стопорный винт 7 (М6Х8). После того как собран узел тягового стакана, производят окончательную сборку регулятора на комбинированном приспособлении (см. рис. 2). Корпус 4 регулятора со вставленной в него возвратной пружиной 7 устанавливают на опорную плиту 21 приспособления и закрепляют прижимом 6.
На регулирующий винт навертывают собранные узлы головки и стакана, при этом необходимо убедиться, что они при вертикальном положении винта свободно, без заеданий навинчиваются под собственным весом. Затем комплект этих узлов вставляют в корпус 4, в отверстие тягового стержня 10 ввертывают натяжной винт 15 приспособления; впуская воздух в силовой цилиндр 20, сжимают возвратную пружину 7, ключом ввертывают головку 2 и закрепляют ее болтом М8 х 12.
Далее выпускают воздух из силового цилиндра приспособления, отпуская возвратную пружину, и вывертывают натяжной винт приспособления из тягового стержня 10. Регулирующий винт ввертывают в головку до выхода его конца из тягового стержня, после, этого на винт навертывают предохранительную гайку 8, совмещают отверстия в винте и гайке и вставляют штифт 9.
После сборки регулятор снимают с приспособления и устанавливают на стенд для испытания.
Испытание авторегулятора на стенде. Стенд для испытания авторегуляторов (рис. 7) представляет собой сварной каркас, на котором установлен тормозной цилиндр диаметром 14". Шток поршня цилиндра шарнирно соединен с рычагом 2, верхний конец которого валиком 3 соединяется с ушком 4 регулятора. Специальное упорное устройство 5 предназначено для закрепления упора привода 6.
На стенде имеется механизм, позволяющий имитировать износ тормозных колодок (увеличение или уменьшение зазора между колодкой и колесом). Вращением маховика 18 уменьшается или увеличивается расстояние между упором 16 и колодкой 17, шарнирно подвешенной на вертикальном рычаге 15. На верхнем шарнире вертикального рычага установлен поворотный демпфер 14 пружинного типа, имитирующий упругие деформации рычажной передачи. На шток демпфера навинчена тяговая муфта 13 с быстродействующим захватом.
Воздух поступает в тормозной цилиндр по трубе 9 через кран 8 вспомогательного тормоза локомотива усл. № 4ВК. Давление в тормозном цилиндре при испытании контролируется по манометру 7 ',
Рис. 7. Стенд для испытания регуляторов.
а величину выхода штока можно определить по указателю 20, закрепленному на штоке поршня тормозного цилиндра, и масштабной линейке 19, установленной на: каркасе стенда.
Механизм регулировки зазоров между колодкой и упором и демпферное устройство позволяют проверить работу автоматического регулятора в условиях, близких к эксплуатационным.
При испытании авторегулятора на стенде проверяется его работа на стабильность действия и стягивание рычажной передачи при различной величине износа тормозных колодок.
Устанавливая регулятор 10 на стенд, его ушко 4 соединяют с вертикальным рычагом 2 при помощи валика 3 со шплинтом. С противоположной стороны регулирующий винт 12- соединяют муфтой 13 с поворотным демпфером 14.
Проверка работы автоматического регулятора на стабильность позволяет определить способность регулятора при нормальных зазорах между колодками и колесами сохранять постоянную величину выхода штока поршня тормозного цилиндра. Для этого вращением маховика 18 против часовой стрелки устанавливают зазор между упором 16 и колодкой 17 вертикального рычага, обеспечивающий определенную величину хода штока, тормозного цилиндра, например 100 мм при полном служебном торможении. Затем поворотом ручки крана 8 производят полное служебное торможение. Исправный авторегулятор должен установить выход штока в пределах 100 мм. Далее, поворачивая ручку крана 8, выпускают воздух из цилиндра, рычажная передача стенда возвращается в исходное положение, а между упором 16 и колодкой 17. образуется зазор.
Чтобы проверить стабильность работы регулятора, наносят продольную и поперечную меловые риски на конец защитной трубы 11 я регулирующий винт 12 и производят одно-два регулировочных торможения с последующим отпуском. У исправного авторегулятора меловые риски не должны сместиться. Если же они сместились, значит, регулятор неисправен и его необходимо вернуть в ремонтное отделение АКП.
Во время эксплуатации регулятор должен надежно стягивать рычажную передачу в зависимости от увеличения выхода штока поршня тормозного цилиндра, поддерживая постоянные зазоры между колодками и колесами.
Проверяя на стенде действие регулятора на стягивание рычажной, передачи, необходимо маховик 18 повернуть по часовой стрелке на один-два оборота, чтобы между упором 16 и колодкой 17 образовался зазор 8-16 мм. Затем производят при помощи крана 8 полное служебное торможение с последующим отпуском, в результате чего регулятор должен сократиться по длине на ве
|
|
Состав сооружений: решетки и песколовки: Решетки – это первое устройство в схеме очистных сооружений. Они представляют...
Общие условия выбора системы дренажа: Система дренажа выбирается в зависимости от характера защищаемого...
Механическое удерживание земляных масс: Механическое удерживание земляных масс на склоне обеспечивают контрфорсными сооружениями различных конструкций...
Историки об Елизавете Петровне: Елизавета попала между двумя встречными культурными течениями, воспитывалась среди новых европейских веяний и преданий...
© cyberpedia.su 2017-2024 - Не является автором материалов. Исключительное право сохранено за автором текста.
Если вы не хотите, чтобы данный материал был у нас на сайте, перейдите по ссылке: Нарушение авторских прав. Мы поможем в написании вашей работы!