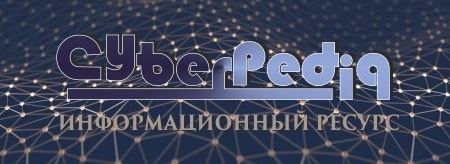
Семя – орган полового размножения и расселения растений: наружи у семян имеется плотный покров – кожура...
Типы сооружений для обработки осадков: Септиками называются сооружения, в которых одновременно происходят осветление сточной жидкости...
Топ:
Комплексной системы оценки состояния охраны труда на производственном объекте (КСОТ-П): Цели и задачи Комплексной системы оценки состояния охраны труда и определению факторов рисков по охране труда...
Устройство и оснащение процедурного кабинета: Решающая роль в обеспечении правильного лечения пациентов отводится процедурной медсестре...
Проблема типологии научных революций: Глобальные научные революции и типы научной рациональности...
Интересное:
Уполаживание и террасирование склонов: Если глубина оврага более 5 м необходимо устройство берм. Варианты использования оврагов для градостроительных целей...
Распространение рака на другие отдаленные от желудка органы: Характерных симптомов рака желудка не существует. Выраженные симптомы появляются, когда опухоль...
Как мы говорим и как мы слушаем: общение можно сравнить с огромным зонтиком, под которым скрыто все...
Дисциплины:
![]() |
![]() |
5.00
из
|
Заказать работу |
|
|
Химико – термической обработкой называют технологические процессы, приводящие к диффузионному насыщению поверхностного слоя деталей различными элементами, с последующей их закалкой в большинстве случаев.
Химико-термическую обработку применяют для повышения твердости, износостойкости, сопротивления усталости и контактной выносливости, а также для защиты от электрохимической и газовой коррозии.
Различают три стадии процесса химико – термической обработки.
На первой стадии протекают химические реакции в исходной (окружающей) среде, в результате которых образуются активные диффундирующие элементы, по-видимому, в ионизированном состоянии.
На второй стадии процесса они усваиваются насыщаемой поверхностью металла - происходит адсорбция диффундирующих элементов, в результате чего тончайший поверхностный слой насыщается диффундирующим элементом (абсорбция), возникает градиент концентрации – движущая сила для следующей стадии процесса.
Третья стадия – диффузионное проникновение элемента в глубь насыщаемого металла, которое сопровождается образованием твердых растворов, химических соединений или фазовой перекристаллизацией.
Первая и вторая стадии процесса химико – термической обработки протекают значительно быстрее третьей – диффузионной стадии, где формируются структура и свойства диффузионной зоны. Третья стадия определяет скорость процесса химико-термической обработки. Диффузионное насыщение стали углеродом, азотом и совместно этими элементами – наиболее распространенные в промышленности процессы химико – термической обработки.
Углерод и азот легко усваиваются поверхностью стали, образуют с железом твердые растворы внедрения, химические соединения – нитриды, карбиды и сравнительно быстро диффундируют в стали, образуя слои значительной толщины.
|
Цементация стали. Технологический процесс диффузионного насыщения углеродом называется цементацией. Обычно после цементации сталь подвергают закалке и низкому отпуску. После такого комплексного процесса концентрация углерода на поверхности стальной детали доводится до 0,8 – 1% и выше, структура низкоотпущенного мартенсита с мелкими сфероидальными карбидами хорошо сопротивляется износу. Твердость на поверхности деталей достигает Н V 7500 – 9500. Сердцевина детали, содержащая 0,08 – 0,25% С, остается вязкой.
Цементации обычно подвергают такие детали машин, которые должны иметь износостойкую рабочую поверхность и вязкую сердцевину: зубчатые колеса, валы и пальцы, распределительные валики, кулачки, червяки и т. д.
Карбюризаторы. Исходную среду для цементации (науглероживания) принято называть карбюризатором. В основном применяют два способа цементации: в твердом и в газовом карбюризаторе. Несмотря на различные названия, процесс цементации в твердом и газовом карбюризаторе идет через газовую фазу. Наиболее распространенный твердый карбюризатор состоит в основном из древесного угля с добавкой 20 – 25% углекислого бария для интенсификации процесса и 3 – 5% СаСО3 для предотвращения спекания частиц карбюризатора. Детали, подлежащие цементации и карбюризатор упаковываются в контейнер (стальной ящик) и нагреваются в печи до 910 – 930 0С. При нагреве уголь взаимодействует с кислородом остаточного воздуха контейнера по реакции
2С + О2 = 2СО.
Кроме того, оксид углерода образуется в результате реакции
ВаСО3 + С = ВаО + 2СО
Разложение соединения СО приводит к образованию активного атомарного углерода:
2СО СО2+Сат
На поверхности деталей протекает ведущая процесс цементации реакция диспропорционирования, в результате которой активный углерод адсорбируется насыщаемой поверхностью, находящейся в аустенитном состоянии, а СО2 взаимодействует с углем, образуя новые порции СО. Таким образом, в результате обратимой реакции диспропорционирования углерод переносится на насыщаемую поверхность.
|
При газовой цементации в качестве карбюризатора используют разбавленный природный газ (состоящий почти полностью из метана), контролируемые атмосферы, получаемые в специальных генераторах, а также жидкие углеводороды (керосин, бензол и др.), каплями подаваемые в герметичное рабочее пространство печи, где они образуют активную газовую среду. Основная ведущая реакция при наличии метана:
СН4 = 2Н2 + Сат
В зависимости от состава газовой смеси и содержания углерода в стали атмосфера в рабочем пространстве печи может быть науглероживающей, обезуглероживающей и нейтральной. Нейтральному составу газовой смеси соответствует определенная равновесная концентрация углерода на поверхности стальной детали. Эту концентрацию углерода принято называть углеродным потенциалом контролируемой атмосферы. Следовательно, науглероживание будет происходить в том случае, если концентрация углерода на поверхности стали будет меньше углеродного потенциала газовой смеси при данной температуре.
Структура цементованного слоя. Типичная структура цементованного слоя на поверхности низкоуглеродистой стали после медленного охлаждения от температуры цементации показана на рис. 1. Наружная часть слоя, содержащая больше 0,8% С, имеет структуру заэвтектоидных сталей – перлит и вторичный цементит, который при медленном охлаждении выделяется на границах аустенитных зерен в виде оболочек (на шлифе сетка). Средняя часть слоя, имеющая эвтектоидную концентрацию, состоит из перлита. Далее по направлению к сердцевине концентрация углерода уменьшается, структура соответствует доэвтектоидной стали, причем количество перлита уменьшается при приближении к сердцевине.
![]() | Принято различать полную и эффективную толщину цементованного слоя. За эффективную толщину принимают сумму заэвтектоидной, эвтектоидной и половины доэвтектоидной зоны слоя. Эффективная толщина цементованного слоя обычно составляет 0,5-1,8 мм и в исключительных случаях достигает 6 мм. Структура после цементации получается крупнозернистой в связи с длительной выдержкой деталей при температуре науглероживания. Длительность изотермической выдержки при цементации зависит от заданной толщины слоя и марки цементируемой стали. Процесс газовой цементации идет быстрее, так как не приходится нагревать ящик с карбюри- |
затором. Кроме того, процесс газовой цементации легко регулируется и автоматизируется. На заводах работают автоматизированные агрегаты для цементации, которые регулируют процесс по углеродному потенциалу.
|
Термическая обработка после цементации. Для получения заданного комплекса механических свойств после цементации необходима дополнительная термическая обработка деталей.
В зависимости от условий работы, а также от выбранной для изготовления детали стали, режим упрочняющей термической обработки может быть различен. Для тяжелонагруженных трущихся деталей машин, испытывающих в условиях работы динамическое нагружение, в результате термической обработки нужно получить не только высокую поверхностную твердость, но и высокую прочность (например, для зубчатых колес - высокую прочность на изгиб) и высокую ударную вязкость. Для обеспечения указанных свойств требуется получить мелкое зерно, как на поверхности детали, так и в сердцевине. В таких ответственных случаях цементованные детали подвергают сложной термической обработке, состоящей из двух последовательно проводимых закалок и низкого отпуска.
При первой закалке деталь нагревают до температуры на 30-50 °С выше температуры Ас3 цементируемой стали. При таком нагреве во всем объеме детали установится аустенитное состояние. Нагрев до температур, лишь немного превышающих Ас3, вызывает перекристаллизацию сердцевины детали с образованием мелкого аустенитного зерна, что обеспечит мелкозернистость продуктов распада. При этой температуре весь диффузионный слой переходит в аустенитное состояние, поэтому, чтобы предотвратить выделение цементита, проводят закалку.
|
При второй закалке деталь нагревают до температуры t с превышением на 30-50 °С температуры Ас1. В процессе нагрева мартенсит, полученный в результате первой закалки, отпускается, что сопровождается образованием глобулярных карбидов, которые в определенном количестве сохраняются после неполной закалки в поверхностной заэвтектоидной части слоя, увеличивая его твердость и другие показатели работоспособности, за счет уменьшения концентрации напряжения при шаровидной форме включений карбида.
Окончательной операцией термической обработки является низкий отпуск при 160-200° С, уменьшающий остаточные напряжения и не снижающий твердость и прочности стали.
Азотирование стали. Азотированием называют процесс диффузионного насыщения азотом поверхностной зоны деталей. Азотирование применяют для повышения износостойкости и предела выносливости деталей машин (коленчатые валы, гильзы цилиндров, червяки, валики и др.).
До азотирования детали подвергают закалке и высокому отпуску (улучшению) и чистовой обработке. После азотирования детали шлифуют или полируют.
Обычное азотирование проводят притемпературе 500-600° С в муфелях или контейнерах, через которые пропускается диссоциирующий аммиак. Длительность процесса зависит от требуемой толщины азотированного слоя. Чем выше температура азотирования, тем ниже твердость азотированного слоя и больше толщина слоя. Обычно при азотировании желательно иметь слой толщиной 0,3-0,6 мм. Процесс азотирования является продолжительным и составляет 24 – 90 ч. Для ускорения процесса азотирования нередко применяют двухступенчатый процесс: сначала азотирование проводят при 500 – 520 0С, а затем при 540 – 600 0С. При двухступенчатом процессе сокращается продолжительность процесса, при этом сохраняется высокая твердость азотированного слоя. Охлаждение после азотирования производят вместе с печью в потоке аммиака.
Азотированию подвергают среднеуглеродистые стали, содержащие хром, алюминий и молибден. С этими элементами азот образует очень твердые и износостойкие нитриды. Твердость азотированного слоя в 1,5...2 раза выше твердости цементированного слоя. Кроме того, азотирование повышает сопротивляемость поверхностного слоя коррозии. Азотирование применяют для упрочнения гильз цилиндров, шестерен и др. В структуре азотированной легированной стали 38ХМЮА на поверхности (рис. 2) расположен тонкий нетравящийся белый слой, состоящий из ε + γ' – фазы. Затем следует серый слой, представляющий собой смесь γ'+ά – фаз. Далее располагается ά-фаза. Фазы γ' и ε представляют собой соответственно карбонитриды Fе4(N,С) и Fе2(N,С), а ά-фаза является азотистым ферритом. В поверхностном слое располагаются также нитриды легирующих элементов. Микроструктура сердцевины состоит из сорбита отпуска, который получают термообработкой, проведенной до азотирования. Формирование структуры азотированной зоны в углеродистых сталях происходит примерно так же, как при азотировании железа.
|
Рисунок 8.2 – Микроструктура стали 38 ХМЮА после азотирования
Поэтому, пользуясь диаграммой Fe-N можно предсказать структуру азотированной зоны низкоуглеродистых сталей. По мере насыщения железа азотом при температуре ниже 590 0С сначала образуется ά-твердый раствор внедрения азота в железо, затем слой γ'-фазы с ГЦК решеткой и упорядоченным расположением атомов азота в центрах элементарных ячеек.
Цианирование и нитроцементация – процесс одновременного насыщения поверхности стали углеродом и азотом. Цианирование может быть жидким или газовым (нитроцементация), а в зависимости от температуры нагрева – высокотемпературным (750...900 0С) или низкотемпературным (530...560 0С).
Жидкое цианирование осуществляется в расплавленных цианистых солях (NаСN, КСN и др.), газовое – в смеси науглероживающего газа и аммиака. Чаще применяют газовое высокотемпературное цианирование, которое более безопасно, отличается экономичностью и возможностью механизации процесса.
Высокотемпературное цианирование, при котором преобладает насыщение стали углеродом, применяют для деталей, изготовленных из среднеуглеродистых сталей (шестерни, пальцы, валики, гайки и др.). После цианирования детали подвергают закалке и низкому отпуску. После высокотемпературного цианирования детали имеют примерно такую же структуру, как и цементированные (тонкая поверхностная корка состоит из карбонитридов, затем следует слой азотистого мартенсита см. рис.8.3). По сравнению с цементированными, цианированный слой обладает более высоким сопротивлением износу, лучшим сопротивлением коррозии.
Низкотемпературное цианирование характеризуется насыщением поверхности стали преимущественно азотом, и применяется для повышения режущих свойств инструмента из быстрорежущей стали.
Поверхностное насыщение стали алюминием, хромом, бором и другими элементами называют диффузионным насыщением металлами.
Изделие, поверхность которого обогащена этими элементами, приобретает ценные свойства, к числу которых относятся высокая жаростойкость, коррозионная стойкость, повышенная износостойкость и твердость.
![]() | Поверхностное насыщение стали металлами, а также таким элементом, как кремний, можно осуществлять при 900 – 1050 0С упаковкой изделия в порошкообразную среду, погружением в расплавленный металл, если диффундирующий элемент имеет невысокую температуру плавления (например, цинк; алюминий), или насыщением из газовой среды. При газовом методе используют летучие галогениды, хлориды металлов. Алитирование.Алитированием называют насыщение поверхности стали алюминием. Чаще применяют алитирование в порошкообразных смесях. Детали упаковывают в ящик, заполненный |
рабочей смесью, в состав которой входят: алюминиевый порошок (25 – 50%) или ферроалюминий (50 – 75%), окись алюминия (25 – 75%) и хлористый аммоний (~ 1,0%). Процесс ведут при 900 – 1050 0С в течение 3 – 12 ч. Нередко применяют алитирование в ваннах с расплавленным алюминием. Алитируемые детали погружают в расплавленный алюминий, содержащий 6 – 8% Fе (железо добавляют для того, чтобы исключить растворение обрабатываемых деталей в алюминии), процесс ведут при 700 – 800 0С в течение 45 – 90 мин.
Структура алитированного слоя представляет собой твердый раствор алюминия в ά -железе (рис 8.4 а). Концентрация алюминия в поверхностной части слоя составляет ~30%. Увеличение содержания в стали углерода и легирующих элементов тормозит диффузию алюминия. Глубина алитированного слоя чаще всего составляет 0,2 – 1,0 мм. Алитированию подвергают топливники газогенераторных машин, чехлы термопар, детали разливочных ковшей, клапаны и другие детали, работающие при высоких температурах.
Хромирование стали – насыщение поверхности стальных изделий хромом. Этот процесс обеспечивает повышенную устойчивость стали против газовой коррозии, высокую коррозионную стойкость в таких средах, как вода, морская вода и азотная кислота. Хромирование сталей, содержащих более 0,3 – 0,4% С, повышает также твердость и износостойкость.
Хромирование чаще ведут в порошкообразных смесях (например, 50% феррохрома, 49% окиси алюминия и 1% хлористого аммония).
а) б) в) г) д)
а) алитированный слой в железе; б) хромированный слой в железе; в) хромированный слой в стали; г) силицированный слой на стали; д) борированный слой на железе
Рисунок 8.4 – Микроструктура диффузионных слоев
Некоторое применение нашло газовое хромирование (нагрев в среде, содержащей СгСl2) и в вакууме. При хромировании в вакууме изделия засыпают порошком хрома в стальном или керамическом тигле и помещают в вакуумную камеру. При высокой температуре хром испаряется и диффундирует в железо. Хромирование ведут при 1000 – 1050° С несколько часов.
Диффузионный слой, получаемый при хромировании технического железа, состоит из твердого раствора хрома в а – железе (рис. 8.4 б). Слой, получаемый при хромировании стали, содержащий углерод, состоит из карбидов хрома. На рис. 8.4 в,показана структура хромированного слоя, полученного на стали с 0,45% С. Слой состоит из карбидов хрома, под слоем карбидов находится переходной слой с высоким содержанием углерода (0,8%). Такие слои образуются в результате диффузии углерода из внутренних слоев к поверхности навстречу хрому. Углерод обладает большей скоростью диффузии, чем хром, поэтому для образования карбидного слоя используется не весь углерод. Часть его составляет переходный слой с высоким содержанием углерода. Карбидный слой обладает высокой твердостью. Твердость слоя при хромировании стали – НV 1200 – 1300. Глубина хромированного слоя обычно не превышает 0,15 – 0,20 мм. Хромирование используют для деталей паросилового оборудования, пароводяной арматуры, клапанов, вентилей, патрубков, а также деталей, работающих на износ в агрессивных средах.
Силицирование - насыщение поверхности стали кремнием. Силицирование придает стали высокую коррозионную стойкость в морской воде, в азотной, серной и соляной кислотах и несколько увеличивает устойчивость против износа. Силицирование проводят в порошкообразных смесях (например, 75% ферросилиция +20% шамота +5% Н4С1) или чаще в газовой среде, получаемый пропусканием хлора через реакционное пространство с обрабатываемыми деталями и ферросилицием или карбидом кремния. Процесс ведут при 950 – 1000 0С.
Силицированный слой (рис. 8.4 г ) является твердым раствором кремния в ά -железе. Под диффузионным слоем часто наблюдается слой перлита. Это объясняется оттеснением углерода из диффузионного слоя вследствие пониженной растворимости его в кремнистом феррите. Силицированный слой отличается повышенной пористостью, глубина его 0,3 – 1,0 мм. Несмотря на низкую твердость (НV 200 – 300), силицированный слой обладает высокой износостойкостью после предварительной пропитки маслом при 170 – 200 0С.
Силицированию подвергают детали, используемые в оборудовании химической, бумажной и нефтяной промышленности (валики насосов, трубопроводы, арматура, гайки, болты и т. д.).
Борирование, т. е. насыщение поверхностного слоя бором создает очень высокую твердость (Н V 1800 – 2000), износостойкость и устойчивость против коррозии в различных средах. Борирование стальных изделий чаще выполняют при электролизе расплавленных солей, содержащих бор. Хорошие результаты получены при газовом борировании. В этом случае насыщение бором проводят в среде диборана (В2Н6) или треххлористого бора в смеси с водородом при 850 – 900 0С. На поверхности образуется борид железа FеВ, а ниже – борид Fе2В и ά-твердый раствор (рис. 8.3д). Углерод и легирующие элементы уменьшают глубину бориро-ванного слоя, чаще она достигает 0,1 – 0,20 мм.
Борированию подвергают детали, применяемые в оборудовании нефтяной промышленности. Например, втулки грязевых нефтяных насосов для повышения их устойчивости против абразивного износа. Борирование поверхностей контакта штампов для горячей штамповки значительно повышает их стойкость. Борированию можно подвергать любые стали.
8. Контрольные вопросы
8.1. Преимущество поверхностной термической обработки от объемной.
8.2. Назовите основные виды ХТО.
8.3. Назначение и принцип цементации поверхности деталей.
8.4. Основные виды карбюризаторов используемых при цементации.
8.5. Основное условие необходимое для диффузии атомарного углерода в поверхностный слой детали.
8.6. Структура упрочненного слоя после цементации.
8.7. При каких условиях работы деталей целесообразно проводить азотирование.
8.8. Отличительные особенности азотирования по отношению к цементации.
8.9. Микроструктура и глубина азотированного слоя.
8.10. Обоснуйте предварительную объемную закалку детали с последующим высоким отпуском перед азотированием.
8.11. При каких условиях работы деталей целесообразно проводить цементацию.
8.12. Обоснуйте температуру цементации и азотирования.
8.13. В чем отличие высокотемпературного и низкотемпературного цианирования.
8.14. Как называются процессы одновременного насыщения поверхности изделия атомарным углеродом и азотом. Обоснуйте процессы.
8.15. Перечислите основные виды диффузионной металлизации.
Список рекомендуемой литературы
9.1. Практикум по технологии конструкционных материалов и материаловедению / Под.ред. С.С. Некрасова – М.:Агропромиздат, 1991г.
9.2. Дриц М.Е., Москалев М.А. Технология конструкционных материалов и материаловедение:-М.:Высшая шк., 1990г.
9.3. Арзамасов Б.Н. и др. Материаловедение: -М.:Машиностроение
Лабораторная работа № 9
|
|
Историки об Елизавете Петровне: Елизавета попала между двумя встречными культурными течениями, воспитывалась среди новых европейских веяний и преданий...
Опора деревянной одностоечной и способы укрепление угловых опор: Опоры ВЛ - конструкции, предназначенные для поддерживания проводов на необходимой высоте над землей, водой...
Таксономические единицы (категории) растений: Каждая система классификации состоит из определённых соподчиненных друг другу...
Биохимия спиртового брожения: Основу технологии получения пива составляет спиртовое брожение, - при котором сахар превращается...
© cyberpedia.su 2017-2024 - Не является автором материалов. Исключительное право сохранено за автором текста.
Если вы не хотите, чтобы данный материал был у нас на сайте, перейдите по ссылке: Нарушение авторских прав. Мы поможем в написании вашей работы!