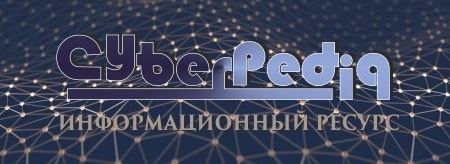
Типы оградительных сооружений в морском порту: По расположению оградительных сооружений в плане различают волноломы, обе оконечности...
Особенности сооружения опор в сложных условиях: Сооружение ВЛ в районах с суровыми климатическими и тяжелыми геологическими условиями...
Топ:
Методика измерений сопротивления растеканию тока анодного заземления: Анодный заземлитель (анод) – проводник, погруженный в электролитическую среду (грунт, раствор электролита) и подключенный к положительному...
Установка замедленного коксования: Чем выше температура и ниже давление, тем место разрыва углеродной цепи всё больше смещается к её концу и значительно возрастает...
Организация стока поверхностных вод: Наибольшее количество влаги на земном шаре испаряется с поверхности морей и океанов...
Интересное:
Влияние предпринимательской среды на эффективное функционирование предприятия: Предпринимательская среда – это совокупность внешних и внутренних факторов, оказывающих влияние на функционирование фирмы...
Уполаживание и террасирование склонов: Если глубина оврага более 5 м необходимо устройство берм. Варианты использования оврагов для градостроительных целей...
Искусственное повышение поверхности территории: Варианты искусственного повышения поверхности территории необходимо выбирать на основе анализа следующих характеристик защищаемой территории...
Дисциплины:
![]() |
![]() |
5.00
из
|
Заказать работу |
Цель работы
1.1. Изучить оборудование для термической обработки сталей.
1.2. Изучить технологию отжига, закалки и нормализации углеродистых сталей.
1.3. Определить влияние скорости охлаждения на твердость углеродистых сталей после термической обработки.
Задание
2.1. Изучить принцип определения температуры термической обработки углеродистых сталей на основе диаграммы состояния «железо – углерод».
2.2. Изучить методику определения времени нагрева и выдержки закаливаемого образца в печке.
2.3. Провести отжиг образцов (Сталь 45).
2.4. Провести закалку отожженных образцов в следующих средах: вода, индустриальное масло И 20.
2.5. Провести нормализацию (сталь 45).
2.6. Провести отпуск закаленных образцов.
2.7. Определить твердость термообработанных образцов на приборах ТК – 2, ТШ - 2.
Техника безопасности
3.1. Процесс закалки следует проводить только в присутствии преподавателя или учебного мастера.
3.2. Не следует прикасаться к нагретым частям нагревательной печи.
3.3. Процесс загрузки и выемки образцов следует выполнять только с использованием специальных клещей и спецодежды.
3.4. Включение печки и твердомера разрешается только по указанию преподавателя (учебного мастера), ведущего занятия.
3.5. Запрещается самостоятельно устранять неисправности оборудования.
Оснащение рабочего места
4.1. Оборудование: нагревательная печь СНОЛ, твердомер ТК-2 и ТШ- 4.
4.2. Инструмент: набор клещей, емкости с охлаждающими жидкостями (вода, масло).
4.3. 3 образца для термообработки из стали 45.
Последовательность выполнения работы
5.1. Измерить твердость образцов до термической обработки на приборе Бринелля.
5.2. Определить по справочным данным режимы термической обработки стали 40 (отжига, нормализации и закалки).
5.3. Загрузить образцы в печь и после заданной выдержки последовательно, по одному, охладить в воде, масле и на воздухе.
Образцы подвергаются отжигу до лабораторного занятия.
5.4. Измерить, твердость образцов после термической обработки на приборе Роквелла.
5.5.Загрузить образцы в печь и подвергнуть их высокому отпуску с охлаждением на воздухе.
5.6. Выключить нагревательную печь и убрать рабочее место.
Отчет о работе
Отчет о выполнении лабораторной работы должно отражать следующее:
6.1. Название работы.
6.2. Цель работы.
6.3. Список литературы.
6.4. Сведения из теории: основные виды термических обработок.
6.5. Таблица 1. Результаты испытаний
Марка стали |
Твердость Исходная |
Толщина образца |
Общее время нагрева |
Твердость | ||
В воде | В масле | На воздухе | ||||
Сталь 45 |
6.6. Результаты испытаний твердости образцов представить в виде зависимости твердости от среды охлаждения.
6.7. Выводы.
Работу выполнил:
ст.-т___________гр._____________
Работу принял:
______________________________
Общие сведения о термической обработке
Теоретические сведения. Термической обработкой стали называется технологический процесс, состоящий из нагрева стали до определенной температуры, выдержки при данной температуре и последующего охлаждения с заданной скоростью. При термической обработке стали получают необходимые свойства, изменяя ее структуру без изменения химического состава.
Любой режим термической обработки может быть представлен графически в координатах «температура - время». Термическую обработку характеризуют основные параметры: нагрев до определенной температуры, выдержка при этой температуре, скорость нагрева и скорость охлаждения (рис. 6.1).
Рисунок 6.1 – График термической обработки стали
В зависимости от температурных режимов и скоростей охлаждения термическая обработка подразделяется на следующие виды: отжиг, нормализация, закалка, отпуск
В зависимости от содержания углерода температуру нагрева углеродистой стали выбирают по диаграмме железо - цементит (рис.6.2), уточняют по справочным данным и экспериментальным путем. Время определяется расчетом, по справочным данным и опытом. В настоящей работе рассматриваются отжиг, нормализация и закалка, которые осуществляются за счет превращений аустенита.
Отжиг заключается в нагреве стали выше критических температур (точек АС1 или АСз), выдержке при данной температуре и медленном охлаждении (обычно вместе с печью). В зависимости от требований, предъявляемых к свойствам стали, различают следующие виды отжига: диффузионный (гомогенизация), полный, неполный (для заэвтектоидных сталей называется сфероидизацией), изотермический, низкий (рис. 6.2).
Цель отжига — устранить внутренние напряжения, измельчить зерно, придать стали пластичность перед последующей обработкой и привести структуру в равновесное состояние.
Рисунок 6.2 – Схема различных видов отжигов
Диффузионный отжиг(гомогенизация) производится при температурах 1100...1200° С в течение 30...50 ч для устранения дендритной ликвации.
Конструкционные стали подвергаются полному отжигу — нагреву до температуры на 30...50 0С выше точки А С3, с последующим медленным охлаждением, обеспечивающим превращение аустенита в ферритоцементитную смесь в области температур, близких к АС1. Инструментальные (заэвтектоидные) стали нагревают на 30...50 0С выше точки АС1 — неполный отжиг. Этот отжиг на зернистый перлит производится с целью снижения твердости для лучшей обрабатываемости резанием и подготовки структуры к закалке.
При изотермическом отжиге конструкционную сталь нагревают до температуры на 30...50 0С выше точки Ас3, а инструментальную – выше АС1 на 50...100 0С, затем следует выдержка и медленное охлаждение в расплавленной соли до температуры несколько ниже точки Ас1, (680..700 0С). При этой температуре сталь подвергают изотермической выдержке, при которой происходит полное превращение аустенита в перлит, с последующим охлаждением на воздухе.
Нормализацией стали называют нагрев доэвтектоидных сталей выше критической точки Ас3, эвтектоидных и заэвтектоидных сталей – выше критической точки Аст на 30...50 0С с непродолжительной выдержкой и последующим охлаждением на воздухе. После нормализации углеродистые стали имеют ту же структуру, что и при отжиге, но перлитные смеси получаются более мелкодисперсными, так как распад аустенита происходит при больших степенях переохлаждения. Цель нормализации – перекристаллизация зерна стали, снятие внутренних напряжений, подготовка стали к дальнейшей пластической деформации, механической или термической обработке. Нормализация – дешевый и простой вид термической обработки углеродистых сталей, содержащих менее 0,5...0,6 % С, при подготовке их к обработке резанием и может заменять отжиг. В заэвтектоидных сталях нормализация с температуры выше Астпредназначена для устранения цементитной сетки.
Наиболее распространенным видом упрочняющей термической обработки углеродистых сталей, содержащих углерода более 0,3%, является закалка.
3акалкой называется термообработка, состоящая из нагрева доэвтектоидных сталей выше критической точки Ас3, эвтектоидных и заэвтектоидных сталей выше Ас1на 30...50 0С (рис. 6.3), выдержки при данной температуре с целью полного превращения ά –Fe в γ-Fe и последующего охлаждения со скоростью больше критической (минимальная скорость охлаждения, обеспечивающая превращение переохлажденного аустенита в мартенсит).
Рисунок 6.3 - Диаграмма интервалов закалочных температур
При скорости охлаждения больше критической углерод не успевает выделиться из кристаллической решетки (в соответствии с ее перестройкой из γ-железа в ά-железо), в результате чего образуется однофазный перенасыщенный твердый раствор углерода в ά-железе, который получил название мартенсита. Пресыщение углеродом приводит к значительным искажениям пространственной решетки железа, создается высокая плотность порогов дислокации, нарушается равенство межатомных сил и в стали накапливается значительная внутренняя потенциальная энергия. Сталь приобретает высокую твердость, но ее пластичность при этом падает.
При закалке в качестве охлаждающей среды чаще всего используют воду, иногда с добавками солей, щелочей. Для закалки существенное значение имеет скорость охлаждения в интервале температур, где аустенит менее устойчив(650…5500 0С). Этот интервал температур при закалке нужно пройти быстро. Важное значение имеет скорость охлаждения в интервале температур 300…200 ОС, когда во многих сталях происходит образование мартенсита. В этом районе температур требуется медленное охлаждение (на воздухе), во избежание возникновения напряжений и закалочных трещин. В зависимости от способа охлаждения стали различают следующие виды закалок: закалка в одном охладителе, закалка в двух средах, ступенчатая закалка, изотермическая закалка и закалка с обработкой холодом.
Закалка в одном охладителе заключается в том, что нагретую под закалку деталь погружают в закалочную среду, в которой она находится до полного охлаждения. Применяют для несложных деталей из углеродистых и легированных сталей.
При закалке в двух средах (прерывистая закалка) деталь сначала погружают в быстроохлаждающую среду (вода), а затем быстро переносят в другую среду (масло или на воздух), где она охлаждается до комнатной температуры. Такую закалку применяют обычно для обработки инструмента из высоколегированной стали.
При ступенчатой закалке нагретая деталь охлаждается в среде температурой 200...250 0С (например, в горячем масле), а затем после небольшой выдержки охлаждается на воздухе.
Изотермическая закалка производится так же, как и ступенчатая, но выдержка в закалочной среде более продолжительная, до полных фазовых превращений.
Закалка с обработкой холодом заключается в охлаждении закаленной стали, содержащей остаточный аустенит, до температур ниже нуля. Обработка холодом производится после закалки, после чего весь остаточный аустенит может переходить в мартенсит. Применяется для высокоуглеродистых сталей (выше 0,6 % С) и инструментальных сталей.
Дефекты закалки: недогрев, перегрев, пережог, обезуглероживание, коробление, трещины и т.д.
Если нагрев стали был ниже критической точки, то говорят о закалке с недогревом. Этот дефект исправимый, для чего сталь подвергают отжигу, а затем проводят закалку в соответствии с технологическими рекомендациями.
Перегрев имеет место тогда, когда сталь нагревают до температуры значительно превышающей критическую. Перегрев стали перед закалкой ведет к крупнозернистому, резко – игольчатому хрупкому мартенситу. Перегрев также можно исправить отжигом с последующей закалкой.
При пережоге стали, кислородпроникаетна границы зерен, хрупкость становится еще большей. Сожженная сталь окончательно испорчена, и вторичной термической обработкой ее исправить нельзя.
Обезуглероживание и окисление поверхности происходит при нагреве в пламенных или электрических печах без контролируемых атмосфер. Чтобы избежать этих дефектов, надо нагрев вести в специальных печах с защитной (инертной и контролируемой) атмосферой.
Закалка стали сопровождается увеличением внутренних напряжений (вследствие искажения кристаллической решетки), которые являются причиной образования трещин и коробления. Трещины являются неисправимым дефектом, а коробления можно устранить последующей рихтовкой или правкой. По указанным выше причинам, закаленные изделия и инструмент подвергают отпуску.
Отпуском называют нагрев закаленной стали до температуры ниже точки Ас1 с выдержкой при данной температуре и последующим охлаждением на воздухе). Цель отпуска — уменьшение закалочных напряжений, снижение твердости и увеличения пластичности и ударной вязкости. Основное превращение при отпуске – распад мартенсита, т. е. выделение углерода из пересыщенного твердого раствора в виде мельчайших кристалликов карбида железа – вторичного цементита.
В зависимости от температуры нагрева различают три вида отпуска.
Низкий отпуск производится при 120...150 °С (отпуск на отпущенный мартенсит). Его применяют после закалки инструментов, цементованных и цианированных изделий, а также после поверхностной закалки. При низком отпуске выделяются карбиды железа из участков мартенсита, которые снижают концентрацию углерода и тем самым закалочные напряжения, при этом твердость стали не уменьшается.
Средний отпуск (отпуск на троостит) происходит при нагреве до температур 350...450° С после закалки. При этом снижается твердость. Средний отпуск рекомендуется для пружин и рессор.
Высокий отпуск ' (отпуск на сорбит) производится при температуре 500... 650° С. Применяют в машиностроении для изделий из конструкционной стали с целью обеспечения достаточной прочности, одновременно вязкости и пластичности. Сочетание закалки с высоким отпуском на сорбит называется улучшением. Эту операцию применяют для среднеуглеродистых сталей (0,35...0,6 %С).
8. Контрольные вопросы
8.1 Что называется термической обработкой.
8.2. Пользуясь диаграммой железо – углерод, укажите, до какой температуры необходимо нагревать при закалке сталь, содержащую 0,4% С.
8.3. Как влияет критическая скорость закалки на выбор охладителя.
8.4. Чем отличается нормализация от других видов термических обработок.
8.5. Для каких изделий целесообразно проводить закалку с обработкой холодом и почему.
8.6. Что называют «улучшением» стали.
8.7. С какой целью после закалки проводят отпуск.
8.8. Перечислите основные виды отпуска и характеристики свойств отпущенных сталей;
8.9. Как влияет скорость охлаждения на продукты распада аустенита;
8.10. Основные виды термических обработок, применяемых в машиностроении;
8.11. С какой целью производят отжиг стали;
8.12. Основные виды отжига;
8.13. Принцип упрочнения стали при закалке;
8.14. Назовите основные дефекты при закалке стали;
8.15. Какая скорость охлаждения называется критической скоростью закалки;
8.16. Можно ли провести закалку стали марок Сталь 15 и Сталь 20;
Список рекомендуемой литературы
9.1. Практикум по технологии конструкционных материалов и материаловедению / Под.ред. С.С. Некрасова – М.: Агропромиздат, 1991.
9.2. Дриц М.Е., Москалев М.А. Технология конструкционных материалов и материаловедение. - М.: Высшая шк., 1990.
9.3. Арзамасов Б.Н. и др. Материаловедение. – М.: Машиностроение, 1986.
Лабораторная работа № 7
Особенности сооружения опор в сложных условиях: Сооружение ВЛ в районах с суровыми климатическими и тяжелыми геологическими условиями...
Своеобразие русской архитектуры: Основной материал – дерево – быстрота постройки, но недолговечность и необходимость деления...
Механическое удерживание земляных масс: Механическое удерживание земляных масс на склоне обеспечивают контрфорсными сооружениями различных конструкций...
Биохимия спиртового брожения: Основу технологии получения пива составляет спиртовое брожение, - при котором сахар превращается...
© cyberpedia.su 2017-2024 - Не является автором материалов. Исключительное право сохранено за автором текста.
Если вы не хотите, чтобы данный материал был у нас на сайте, перейдите по ссылке: Нарушение авторских прав. Мы поможем в написании вашей работы!