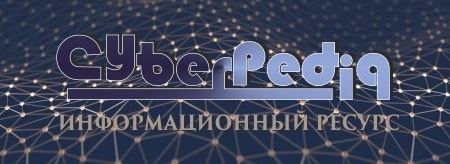
Адаптации растений и животных к жизни в горах: Большое значение для жизни организмов в горах имеют степень расчленения, крутизна и экспозиционные различия склонов...
История развития пистолетов-пулеметов: Предпосылкой для возникновения пистолетов-пулеметов послужила давняя тенденция тяготения винтовок...
Топ:
Проблема типологии научных революций: Глобальные научные революции и типы научной рациональности...
Основы обеспечения единства измерений: Обеспечение единства измерений - деятельность метрологических служб, направленная на достижение...
Определение места расположения распределительного центра: Фирма реализует продукцию на рынках сбыта и имеет постоянных поставщиков в разных регионах. Увеличение объема продаж...
Интересное:
Лечение прогрессирующих форм рака: Одним из наиболее важных достижений экспериментальной химиотерапии опухолей, начатой в 60-х и реализованной в 70-х годах, является...
Средства для ингаляционного наркоза: Наркоз наступает в результате вдыхания (ингаляции) средств, которое осуществляют или с помощью маски...
Что нужно делать при лейкемии: Прежде всего, необходимо выяснить, не страдаете ли вы каким-либо душевным недугом...
Дисциплины:
![]() |
![]() |
5.00
из
|
Заказать работу |
МИНИСТЕРСТВО СЕЛЬСКОГО ХОЗЯЙСТВА РОССИЙСКОЙ ФЕДЕРАЦИИ
ФЕДЕРАЛЬНОЕ ГОСУДАРСТВЕННОЕ БЮДЖЕТНОЕ
ОБРАЗОВАТЕЛЬНОЕ УЧРЕЖДЕНИЕ
ВЫСШЕГО ПРОФЕССИОНАЛЬНОГО ОБРАЗОВАНИЯ
«ИЖЕВСКАЯ ГОСУДАРСТВЕННАЯ СЕЛЬСКОХОЗЯЙСТВЕННАЯ АКАДЕМИЯ»
УТВЕРЖДАЮ: Проректор по учебной работе профессор _____________П.Б. Акмаров «____» __________________2013г. |
МАТЕРИАЛОВЕДЕНИЕ
Практикум по выполнению лабораторных работ для студентов бакалавров
направления «Агроинженерия» по профилям:
110800 – «Технические системы в агробизнесе»
110800.62 – «Технический сервис в АПК»
110800 – «Электрооборудование и электротехнологии»
ФГБОУ ВПО Ижевская ГСХА
2013
УДК
ББК М
Лабораторный практикум составлен на основе Государственного образовательного стандарта высшего профессионального образования, утвержденного приказом Министерства образования Российской Федерации по направлению подготовки бакалавров по направлению «Агроинженерия»
«_»___________
Лабораторный практикум рассмотрен и рекомендован к изданию редакционно – издательским советом ФГБОУ ВПО Ижевская ГСХА,
протокол №_ __ от _________ 20г.
Рецензент:
Е.В. Харанжевский– к.т.н., доцент кафедры общей физики ФГБОУ ВПО «УдГУ»
Составители:
С.М. Стрелков– к.т.н, доцент кафедры ремонта машин и технологии конструкционных материалов
А.Г. Ипатов– к.т.н, доцент кафедры ремонта машин и технологии конструкционных материалов
Ответственный за выпуск - зав. кафедрой ремонта машин и технологии конструкционных материалов, к.т.н. доцент В.И. Широбоков
Материаловедение: лабораторный практикум / Состав, С.М. Стрелков, А.Г. Ипатов; отв. за вып. В.И. Широбоков. – Ижевск: ФГБОУ ВПО ИжГСХА, 2013. – 124с.
В лабораторном практикуме приводятся теоретические и методические сведения, ориентирующие студентов при выполнении лабораторных работ. Практикум предназначен для студентов 1 курса очной и заочной формы обучения инженерных факультетов по направлению бакалавриата «Агроинженерия»
ББКМ
УДК.
© ФГБОУ ВПО Ижевская ГСХА, 2013
© Стрелков СМ., Ипатов А.Г. сост., 2013.
Содержание
Лабораторная работа № 1 Кристаллизация. Ее влияние на структуру и свойства металла. 4
Лабораторная работа № 2 Твердость. Методы определения твердости. 13
Лабораторная работа № 3 Макроструктурный и микроструктурный анализ металлов и сплавов. 21
Лабораторная работа № 4 Изучение микроструктуры сталей в равновесном состоянии 36
Лабораторная работа № 5 Изучение микроструктуры и свойства чугунов. Структура, свойства и применение чугунов. 45
Лабораторная работа № 6 Практика термической обработки сталей. 53
Лабораторная работа № 7 Изучение микроструктуры термообработанных сталей..63
Лабораторная работа № 8 Изучение структуры и свойства сталей после химико-термической обработки. 76
Лабораторная работа № 9 Изучение структуры и свойства легированных сталей. 90
Лабораторная работа № 10 Изучение структуры и свойства цветных сплавов. 103
Приложение…………………………………………………………………………....120
Лабораторная работа №1
КРИСТАЛЛИЗАЦИЯ. ЕЕ ВЛИЯНИЕ НА СТРУКТУРУ
И СВОЙСТВА МЕТАЛЛА
Цель работы
1.1. Изучить механизм и кинетику процесса кристаллизации.
1.2. Изучить макроструктуру металлических слитков.
1.3. Изучить влияние условий кристаллизации на структуру и механические свойства металла.
Задание
2.1. Получить задание у преподавателя по изучению процесса кристаллизации.
2.2. Провести настройку микроскопа.
2.4. Проследить за процессом кристаллизации.
2.3. Зарисовать схему роста кристаллов.
Техника безопасности
3.1. Подготовку микроскопа и водного солевого раствора произвести только в присутствии преподавателя или учебного мастера.
3.2. Микроскопы с электрическим освещением включать только в присутствии преподавателя.
3.3. При обнаружении возникших неисправностей обратится к преподавателю или учебному мастеру.
3.5. Запрещается самостоятельно устранять неисправности оборудования.
Оснащение рабочего стола
Водные растворы солей (хромпика К2Сr2О7, марганцовокислого калия КМnО4, свинца PbNO3), биологические микроскопы, металлические слитки.
Отчет о работе
Отчет о выполнении лабораторной работы должен содержать следующее:
6.1. Название работы;
6.2. Цель работы;
6.3. Список литературы.
6.4.Сведения из теории:
а) Основные механизмы и закономерности кристаллизации. Зарисовать характерный рисунок макроструктуры слитка,
б) Зарисовать кинетику процесса кристаллизации на примере водного раствора соли свинца.
6.5. Выводы
Работу выполнил:
ст.-т___________гр._____________
Работу принял:
______________________________
Основные положения
Кристаллизация – это процесс перехода вещества из жидкого состояния в твердое - кристаллическое. В расплавленном металле нет дальнего порядка: расстояния между атомами не являются постоянными, объемы с упорядоченным расположением атомов то возникают, то снова исчезают (рис. 1, а). В процессе кристаллизации устанавливается дальний порядок: атомы располагаются на определенных расстояниях по каждому пространственному направлению, образуя кристаллическую решетку (рис.1.1,б). Такое упорядоченное расположение возникает за счет равновесия сил притяжения и отталкивания между атомами и соответствует минимуму энергии взаимодействия атомов в металле.
Рис унок 1.1 – Расположение атомов в жидком (а) и твердом (б) металле
Процесс кристаллизации может идти самопроизвольно, а может вызываться какими-то искусственными причинами.
Самопроизвольно идут только те термодинамические процессы, которые приводят к уменьшению свободной энергии системы. (Свободная энергияF – это изменяемая часть полной энергии системы). С повышением температуры металла его свободная энергия, как в жидком, так и в твердом состоянии снижается, но с разной скоростью: свободная энергия жидкого металла снижается быстрее (рис. 1.2). Поэтому кривые зависимости свободной энергии от температуры пересекаются при какой-то температуре TS. При любой температуре ниже TS меньшим уровнем свободной энергии обладает твердый металл, поэтому, если охладить расплав до температуры T 1 < TS, начнется кристаллизация. И, наоборот, при температурах выше TS устойчиво жидкое состояние, поскольку жидкий металл имеет меньший уровень свободной энергии. Значит, нагрев до T 2 > TS приведет к плавлению.
Рисунок 1.2 – Зависимости свободной энергии металла от температуры
Температура TS, при которойсвободная энергия металла в твердом и жидком состоянии одинакова, называется теоретической температурой кристаллизации. При этой температуре жидкость и кристаллы находятся в равновесии, поэтому металл одновременно находится и в жидком и в твёрдом агрегатном состоянии.
Чтобы кристаллизация осуществилась, необходимо некоторое переохлаждение относительно теоретической температурой кристаллизации. В таком случае образование кристаллов дает выигрыш в свободной энергии, что и является стимулом процесса. Поэтому на самом деле кристаллизация всегда происходит при температуре ниже TS. Реальная температура кристаллизацииT Р всегда меньше теоретической. Разность между теоретической и реальной температурой кристаллизации называется степенью переохлаждения Δ T:
Δ T = TS – T Р.
Измеряя температуру металла в процессе кристаллизации, можно получить кривую охлаждения (рис. 1.3). Это график в координатах «температура – время». На этой кривой имеется горизонтальный участок, соответствующий переходу металла из жидкого состояния в твердое. Постоянная температура на этом участке поддерживается за счет выделения скрытой теплоты кристаллизации.
Рисунок 1.3 – Кривая охлаждения расплавленного металла
Степень переохлаждения при кристаллизации не является постоянной величиной. Она увеличивается с увеличением скорости охлаждения металла. В реальных заводских условиях изготовления отливок степень переохлаждения обычно не превышает 20–30°, но для очень чистых металлов может достигать нескольких сотен градусов.
Механизм процесса кристаллизации можно представить в виде двух элементарных процессов:
1) Образование в жидкости центров кристаллизации (зародышей, мельчайших твердых частиц).
2) Рост кристаллов из образовавшихся зародышей.
Скорости этих элементарных процессов зависят от степени переохлаждения Δ T или скорости охлаждения металла V. В большинстве случаев процессы кристаллизации металла на металлургических заводах, в литейных цехах происходят при сравнительно небольших степенях переохлаждения. Следовательно, в кристаллизующейся жидкости образуется небольшое число центров кристаллизации и из них вырастает небольшое число кристаллов, что приводит к появлению крупнозернистой структуры после затвердевания металла.
а б
а – начало процесса; б – окончание процесса
Рисунок 1.4 – Кристаллизация при медленном охлаждении:
Если же кристаллизация происходит при больших скоростях охлаждения и больших степенях переохлаждения (Δ T 2 , V 2), то в жидкости образуется большое количество центров кристаллизации и из них, соответственно, вырастает большое число кристаллов. Металл при этом получается мелкозернистый (рис.1.6).
а б
а – начало процесса; б – окончание процесса
Рисунок 1.5 – Кристаллизация при быстром охлаждении:
Столкновение растущих кристаллов приводит к потере ими правильной огранки. Такие потерявшие правильную форму кристаллы называются зернами.
При очень маленькой скорости охлаждения может возникнуть один-единственный центр кристаллизации, из которого вырастет один кристалл (монокристалл). Необходимые в электронике монокристаллы полупроводников выращивают путем очень медленного вытягивания затравки из расплава.
При огромных скоростях охлаждения достигаются такие большие степени переохлаждения, что тепловое движение атомов в металле замедляется, атомы не успевают образовать дальний порядок, выстроиться в кристаллическую решетку. Жидкое, неупорядоченное состояние металла оказывается как бы «замороженным». Металл становится твердым, но не имеет кристаллического строения. Это аморфный металл или металлическое стекло. Аморфные металлы широко применяются в современной аудиотехнике благодаря уникальным магнитным свойствам.
Поскольку структура металла определяет его свойства, рассмотренные закономерности кристаллизации могут быть использованы для формирования необходимых свойств металла при отливке деталей.
Мелкозернистый металл обладает более высоким сопротивлением деформации и большей вязкостью. Дело в том, что границы зерен являются барьером для развития деформации и для роста трещины. В мелкозернистом металле суммарная поверхность зерен в единице объема больше, чем в крупнозернистом. Поэтому и сопротивление мелкозернистого металла деформированию и разрушению больше. Чтобы разрушить металл с мелким зерном требуется затратить больше энергии.
Поэтому при отливке деталей, испытывающих значительные нагрузки при эксплуатации, целесообразно проводить процесс кристаллизации при высокой скорости охлаждения, чтобы получить мелкозернистую структуру. Если необходимую скорость кристаллизации обеспечить не удается (в отливках большой массы), то для измельчения зерна в жидкий металл вводят небольшие добавки примесей в виде мелких нерастворимых в расплаве частиц, увеличивая тем самым число центров кристаллизации. Такой процесс называется модифицированием, а вводимые добавки – модификаторами.
В качестве модификаторов обычно применяются мелкие частицы карбидов, оксидов (Сr7С3, VC, ТiC, Al2О3 и др.) и некоторые вещества, облегчающие образование зародышей в жидкости (В, Mg и др.). Измельчению зерна способствует также вибрация кристаллизующегося металла.
Следует иметь в виду, что при получении отливок затвердевание металла в форме происходит с разными скоростями охлаждения в различных ее частях.
Скорость охлаждения уменьшается от стенки формы к центральной ее части, при этом меняется и направление теплоотвода в местах роста кристаллов. В результате полученный слиток имеет неодинаковое строение по сечению, а значит, и разные свойства (рис. 1.6). Поверхностный слой будет мелкозернистый (т.е., с высокими механическими свойствами), центральная часть слитка крупнозернистая. | |
![]() | 1 – корка (зона мелких по-разному ориентиро- ванных кристаллов); 2 – зона столбчатых кристаллов, растущих в направлении, обратном направлению теплоотвода; 3 – зона крупных, произвольно ориентированных кристаллов; 4 – усадочная раковина в верхней части слитка. |
Рис унок 1.6 – Характерные зоны слитка | Размер этих зон существенно меняется в зависимости от состава металла и условий крис- |
таллизации. Рост кристаллов во второй зоне имеет направленный характер. Они растут перпендикулярно стенкам изложницы, образуются древовидные кристаллы – дендриты (рис. 1.7). Растут дендриты с направлением, близким к направлению теплоотвода.
![]() | Так как теплоотвод от незакристаллизовавшегося металла в середине слитка в разные стороны выравнивается, то в центральной зоне образуются крупные дендриты со случайной ориентацией. Зоны столбчатых кристаллов в процессе кристаллизации стыкуются, это явление называется транскристаллизацией. Для малопластичных металлов и для сталей это явление нежелательное, так как при после дующей прокатке, ковке могут образовы- |
Рисунок 1.7 – Схема дендрита по Чернову Д.К. |
ваться трещины в зоне стыка. В верхней части слитка образуется усадочная раковина, которая подлежит отрезке и переплавке, так как металл более рыхлый (около 15…20 % от длины слитка).
8. Контрольные вопросы
8.1. Что является движущей силой процесса кристаллизации?
8.2. Каков механизм кристаллизации металла?
8.3. Что такое степень переохлаждения?
8.4. Почему структура слитка неодинакова по сечению?
8.5. Как влияет скорость охлаждения при кристаллизации на структуру металла?
8.6. Как можно получить мелкозернистый металл?
8.7. Как влияет структура металла на механические свойства?
8.8. Почему свойства крупнозернистого и мелкозернистого металла различны?
8.9. По какой причине на микроструктуре слитка формируются столбчатые дендриты?
8.10. Что такое модификаторы?
8.11. Какие химические элементы и соединения являются модификаторами?
8.12. Что характеризует состояние термодинамического равновесия?
8.13. Приведите пример вещества в термодинамическом равновесии?
8.14. Что такое свободная энергия вещества?
8.15. Как изменение свободной энергии влияет на агрегатное состояние?
Лабораторная работа №2
ТВЕРДОСТЬ. МЕТОДЫ ОПРЕДЕЛЕНИЯ ТВЕРДОСТИ
1.Ц ель работы
1.1. Ознакомиться с условиями испытаний и характеристиками твердости, конструкциями приборов и с методиками ее определения на приборах Бринелля и Роквелла. Сравнить их достоинства и недостатки.
З адание
2.1. Определить твердость хотя бы одного отожженного стального образца соответственно по приборам Бринелля и Роквелла.
2.2. По показателям твердости незакаленных образцов (сталь марок 10, 30, 45, У8А, У10А, У12А), в том числе испытуемых другими студентами, построить график зависимости твердости стали от содержания в ней углерода.
2.3. Уметь правильно обозначать и сравнивать характеристики твердости.
О борудование и материалы
3.1. Твердомер ТШ (Бринелля).
3.2. Лупа Бринелля для измерения диаметра отпечатка.
3.3.Твердомер ТК (Роквелла) с конусным и шариковым наконечником.
3.4.Отожженные образцы сталей 10, 20, 30, 45, У8А, У10А, У12А.
Техника безопасности
4.1. Процесс измерения твердости следует проводить только с разрешения преподавателя или учебного мастера.
4.2. Не следует прикасаться к движущимся частям твердомера при работе.
4.3. Процесс установки и изъятия образцов следует выполнять только после полной остановки твердомера.
4.4. Не следует устанавливать и испытывать материалы и образцы несоответствующие лабораторным.
4.5. Запрещается самостоятельно устранять неисправности оборудования.
С одержание отчета
Дать характеристику твердости как свойства металла. Отметить существующие способы ее измерения. Начертить схемы измерения наконечниками на приборах Бринелля и Роквелла и описать методику измерения твердости на них. Заполнить табл. 1. Построить график зависимости твердости стали от содержания в ней углерода. Объяснить полученную закономерность. Произвести анализ наблюдений и установить область применения твердомеров Бринелля и Роквелла (указать преимущества и недостатки каждого из них), а также форму наконечника, обеспечивающую повышенную точность измерения твердости.
Работу выполнил:
ст.-т___________гр._____________
Работу принял: ______________________________
Таблица 1 – Журнал наблюдений
Характеристика образцов |
О сновные положения 7.1. Имерение твердости по Бринеллю (ГОСТ 9012-59)
Число твердости по Бринеллю НВ характеризуется отношением нагрузки, действующей на шарик, к площади поверхности сферического отпечатка:
Рисунок 2.1 – Схема нагружения где P – нагрузка на шарик, кгс; F – площадь отпечатка, мм2; D – диаметр шарика, мм; d – диаметр отпечатка, мм. Получаемое число твердости при прочих равных условиях определяется диаметром отпечатка - d. Отпечаток тем меньше, чем выше твердость испытуемого металла. Отпечаток измеряется специальным измерительным микроскопом или лупой Бринелля. Твердость НВ вычисляют как среднее не менее чем, по двум отпечаткам, а диаметр каждого отпечатка как среднее из двух его измерений по двум взаимно перпендикулярным диаметрам. Удобно твердость определять по диаметру отпечатка d шарика в металле, пользуясь специальной таблицей. Таблица позволяет сравнивать между собой значения твердости, полученные разными методами испытаний. Испытание на твердость проводят на специальном приборе – твердомере Бринелля ТШ. Твердомер обеспечивает установленные ГОСТ 9012-59 условия испытаний (табл.2), применяемые в различных сочетаниях. Таблица 2.2 – У словия испытаний по Бринеллю *
Примечание: *выделенное жирным шрифтом – стандартные условия испытаний.
Для того чтобы совпадали числа твердости металла, определенные при разных диаметрах шарика, необходимо создать подобные (одинаковые) условия деформации металла под шариком: Р=кD2, где к=30, 10 или 2,5, так же, как и время выдержки под нагрузкой, в зависимости от диаметра шарика, интервала твердости, материала и его толщины. Для получения правильного отпечатка необходимы следующие условия: толщина образцов не менее 10-кратной глубины отпечатка, расстояние центра отпечатка от края образца не менее 4 d. Твердость по Бринеллю в стандартных условиях испытаний записывается: НВ 232, НВ 420 и т.п. Твердость, определенная в нестандартных условиях (например, шарик 5 мм, нагрузка 750 кг.с., время выдержки 30 сек.): НВ 5-750-30 230. Размерность указывается только при выражении числа твердости в Н/мм2. Существует достаточно хорошая корреляция между величиной твердости по Бринеллю и пределом прочности σв многих металлов и сплавов, которая представляется в специальных таблицах. Так, для сталей, алюминия и алюминиевых сплавов с НВ (20 – 45), дюралюмина эта связь описывается формулой σв=(0,33 – 0,36)НВ кгс/мм2; для серого чугуна σв=(НВ – 40)/6; для стального литья σв=(0,3 – 0,4)НВ. Эта и другие подобные зависимости широко используются в инженерной деятельности, так как позволяют быстро, просто и достаточно надежно определить прочность металлов.
7.2 Измерение твердости по Роквеллу (ГОСТ 9013 – 59) При этом методе испытания на твердость в металл статически вдавливается алмазный (или твердосплавный) конус с углом при вершине в 1200 или стальной твердый шарик диаметром D = 1,588 мм = Число твердости определяется глубиной проникновения наконечника в металл. Чем она меньше, тем выше твердость (см. рис 2.2). Глубину проникновения наконечника в металл легко измерить и связать с показывающим прибором, поэтому на твердомерах Роквелла установлен прибор, сразу показывающий число твердости.
Рисунок 2.2 – Схема измерения твердости по Роквеллу
Твердомеры для измерения твердости по Роквеллу типа ТК могут создавать нагрузку на наконечник Р = 60, 100, 150 кГс. Каждая нагрузка имеет свою шкалу, свои пределы измерения и свое обозначение твердости, см. табл. 3. Таблица 3. – Условия испытаний, обозначение и пределы измерения твердости по Роквеллу
Методом Роквелла по шкале С измеряют твердость закаленных сталей твердостью НВ (230-700), по шкале В – твердость мягких сталей, цветных металлов и сплавов с НВ (60-240), по шкале А – твердость закаленных сталей с НВ (380-780). Место измерения твердости должно быть тщательно отшлифовано, или отполировано. Глубина слоя металла, твердость которого измеряется, должна быть не менее 10 глубин вдавливания наконечника в металл.
Лабораторная работа №3 МЕТАЛЛОВ И СПЛАВОВ Ц ель работы
1.1. Изучить методику макроструктурного анализа металлов и сплавов невооруженным глазом или при увеличении до 30…50 раз через лупу. 1.2. Освоить технологию приготовления микрошлифов, ознакомиться с устройством металлографического микроскопа, изучить микроструктуры шлифа до и после травления; уяснить принцип выявления структур и практическое значение данного метода. Приборы и материалы 2.1. Оборудование: Шлифовальная машина (цеховая), полировальная машина, металлографический микроскоп МИМ – 2. 2.2. Материалы: образцы макрошлифов и изломов, заготовки для микрошлифов из стали 40 (в равновесном состоянии), шлифовальная бумага отечественного производства (под номерами 12, 10, 8, 6, 4), войлочный круг для полировки, 5-% раствор азотной кислоты в этиловом спирте, дисцилированная вода, паста ГОИ или окись хрома, полировочная алмазная паста. Техника безопасности 3.1. Процесс подготовки микрошлифов следует проводить в спецодежде или в халатах. 3.2. Процесс травления микрошлифов производить только под вытяжным шкафом с использованием средств индивидуальной защиты. 3.3. Процесс шлифования и полирования микрошлифов следует производить только с использованием специального приспособления. 3.4. Включение шлифовальной и полировальной машины следует производить только в присутствии преподавателя или учебного мастера. 3.5. Запрещается самостоятельно устранять неисправности оборудования. Порядок выполнения работы 4.1. Зарисовать по образцам изломы с выявлением размеров зерен, волокнистости, кристалличности, дендритности и др. 4.2. Механически обработать образец для приготовления микрошлифа (шлифование, полирование). 4.3. Изучить микроструктуру шлифа под микроскопом до травления. 4.4. Определить общее увеличение микроскопа. 4.5. Зарисовать схему увеличенной микроструктуры, указав строение сплава (неметаллические включения, металлическую основу). Пользуясь шкалой баллов, определить балл оксидов и сульфидов (ГОСТ 1778—70). 4.6. Протравить шлиф реактивом. 4.7. Изучить микроструктур шлифа под микроскопом после травления. 4.8. Зарисовать схему микроструктуры после травления, указав строение сплава (границы зерен, зерна однородного и неоднородного строения, размер зерна), пользуясь для этого шкалой величины зерна (ГОСТ 5639—65).
Содержание отчета Вотчет необходимо включить: название работы, цель работы, технологию приготовления микрошлифа; реактив, применяемый для травления стали и чугуна; оптическую схему металлографического микроскопа и ее краткое описание; схемы микроструктур иих описание. В выводах указать особенности строения исследуемого металла, выявленные микроанализом до травления и после травления, наличие неметаллических включений, дефектов, размер, форму зерен и их влияние на свойства (красноломкость), прочность, твердость, пластичность.
Работу выполнил: ст.-т___________гр._____________ Работу принял: ______________________________
Общие сведения Современные металлы и сплавы, различаясь по составу и строению, обладают разнообразными свойствами. Независимо от этого, в процессе эксплуатации машин в результате изнашивания, коррозии, усталости материала и других процессов, а так же из-за нарушений режимов эксплуатации, правил обслуживания степень годности бывших в эксплуатации деталей и сборочных единиц к дальнейшему использованию может быть различной. В конкретных условиях трения и изнашивания деталей изменяются геометрические параметры, шероховатость рабочих поверхностей и физико-механические свойства поверхностных слоев материала, а так же возникают и накапливаются усталостные повреждения. В связи с этим для получения достаточной информации о пригодности деталей к дальнейшему использованию результаты, какого либо одного метода испытания, даже очень совершенного, не могут дать полной информации о ресурсах дальнейшей работоспособности деталей. Для решения данных проблем обычно используются несколько методов анализа, которые дополняют друг друга. Однако о работоспособности большинства деталей, бывших в эксплуатации, можно судить и по результатам определенных, даже несложных методов анализа. В данных методических указаниях приведены основные из них. Структурные методы исследования включают методы макроструктурного и микроструктурного анализа. Метод макроструктурного анализа (макроанализ) заключается в изучении строения металлов и сплавов невооруженным глазом или при небольших увеличениях с помощью лупы. Макроанализ позволяет наблюдать одновременно большую поверхность образца или детали, поэтому при помощи микроструктурного анализа можно установить вид излома (вязкий, хрупкий), величину, форму и расположение зерен и дендритов литого металла, характер предшествующей обработки металла и т. д. Кроме того, макроанализ дает возможность обнаружить газовые пузыри, усадочные пустоты, трещины, ликвацию серы, фосфора и т. д. Ликвацией называется неоднородность химического состава в сплавах. Различают три вида ликвации: зональную, по удельному весу и дендритную (внутрикристаллическую). Зональная ликвация наблюдается в объеме слитка. По мере кристаллизации металл слитка будет все более разделяться по температуре кристаллизации компонентов: вначале кристаллизуются более тугоплавкие составляющие, затем – менее тугоплавкие, поэтому химический состав зон будет различным.Однако в процессе многократной обработки давлением(более 90 – % металлических сплавов в настоящее время подвергаются обработке давлением) начальная зональная ликвация нивелируется и становится малосущественной. Ликвация по плотности (удельному весу) наблюдается при сплавлении металлов, сильно различающихся по плотности. Так, в сплавах системы свинец – сурьма верхняя часть слитка будет обогащена сурьмой, тем самым, отличаясь от среднего состава сплава. Дендритная ликвация наблюдается в объеме одного зерна. Чем больше температурный интервал между началом и концом кристаллизации сплава, тем больше будут отличаться по составу отдельные участки внутри зерен. В этих случаях в дендритах оси первого порядка бывают обогащены более тугоплавким компонентом и в них содержание различных примесей бывает наиболее низким. Кристаллизующиеся в конце междендритные пространства содержат наибольшее количество более легкоплавких компонентов и различных примесей. Изучение макроструктуры нередко дополняется так же исследованием излома металла, что позволяет судить о причинах разрушения (усталостный излом, закалочные трещины и т. п.). Усталостные повреждения нарушают сплошность материала, способствуют возникновению микро- и макротрещин, выкрашиванию металла рабочих поверхностей и излому деталей. Постепенное накопление повреждений в металлах и сплавах под действием циклических нагрузок, приводящих к образованию трещин и разрушению, называют усталостью, а свойство металлов сопротивляться усталости – выносливостью. Усталостный излом состоит из места зарождения разрушения, из очага разрушения, зоны стабильного развития трещины и зоны долома – участка развития трещины, связанного с окончательным разрушением. Очаг разрушения обычно расположен вблизи поверхности. Поверхность как наиболее нагруженная часть сечения (при изгибе, кручении) претерпевает микродеформации, а затем в наклепанной зоне образуются подповерхностные трещины. Растет, однако, только та трещина, которая имеет достаточную длину и острую вершину – магистральная трещина. Продвигаясь в глубь металла, усталостная трещина образует глубокий и острый надрез. Скорость роста трещины невелика. Рост трещины продолжается до тех пор, пока сечение не окажется столь малым, что действующие напряжения превысят разрушающие. Тогда происходит быстрое разрушение, что и приводит к образованию зоны долома. Зона долома имеет структуру, характерную для разрушения при однократных разрушениях (хрупкого или вязкого в зависимости от природы материала). Для определения предела выносливости (наибольшее значение напряжения цикла, при действии которого не происходит усталостное разрушение образца после заданного числа циклов нагружения) проводят испытания на усталость по ГОСТ 25502 – 84. Цикл нагружения – это совокупность переменных значений напряжений за один период их изменения. Дефекты шлифования вызываются значительными контактными напряжениями (до 10000 кгс/мм2) и температурами (до 1000 град.), возникающими из-за неблагоприятной формы абразивных зерен (большие углы резания). Одной из главных причин такого напряженного состояния является то обстоятельство, что значительная часть зерен не режет, а проскальзывает из – за того, что радиусы закругления режущего лезвия зерен большие – они быстро притупляются и в при дальнейшей работе зерна не режут, а проскальзывают. В поверхностных слоях обрабатываемых деталей происходят структурные превращения, появляются значительные напряжения. Это приводит к «пережогу» и возникновению трещин, которые являются началом разрушения. Для макроструктурного анализа не требуется специального, сложного оборудования, достаточно знаний влияния видов выявленных дефектов на работоспособное состояние деталей. Методом микроструктурного анализа изучают поверхностное строение металлов и сплавов при помощи оптических микроскопов при относительно больших увеличениях - обычно от 50 до 2000 раз. ПРИ таких увеличениях можно обнаружить элементы структуры размером до 0,2 мкм. Изучение микроструктуры проводят на специально приготовленных образцах – микрошлифах. Микрошлифы должны иметь зеркально-блестящую поверхность, потому что структуру металлов и сплавов как тел непрозрачных, рассматривают в отраженном свете (устройство микроскопа приведено ниже). Под микроскопом на микрошлифе после полирования можно увидеть микротрещины и неметаллические включения (графит в чугунах, оксиды, сульфиды и т. д.). Для выявления самой микроструктуры металла поверхность шлифа травят, т.е. обрабатывают специальными реактивами, состав которых зависит от состава металла. Выявление микроструктуры при травлении основано на том, что различные фазы протравливаются неодинаково и таким образом, окрашиваются по-разному. В результате травления микрошлифов чистых металлов, возможно, выявить
![]() Семя – орган полового размножения и расселения растений: наружи у семян имеется плотный покров – кожура... ![]() Автоматическое растормаживание колес: Тормозные устройства колес предназначены для уменьшения длины пробега и улучшения маневрирования ВС при... ![]() Эмиссия газов от очистных сооружений канализации: В последние годы внимание мирового сообщества сосредоточено на экологических проблемах... ![]() Опора деревянной одностоечной и способы укрепление угловых опор: Опоры ВЛ - конструкции, предназначенные для поддерживания проводов на необходимой высоте над землей, водой... © cyberpedia.su 2017-2024 - Не является автором материалов. Исключительное право сохранено за автором текста. |