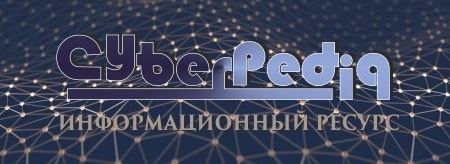
Двойное оплодотворение у цветковых растений: Оплодотворение - это процесс слияния мужской и женской половых клеток с образованием зиготы...
Археология об основании Рима: Новые раскопки проясняют и такой острый дискуссионный вопрос, как дата самого возникновения Рима...
Топ:
Оценка эффективности инструментов коммуникационной политики: Внешние коммуникации - обмен информацией между организацией и её внешней средой...
Процедура выполнения команд. Рабочий цикл процессора: Функционирование процессора в основном состоит из повторяющихся рабочих циклов, каждый из которых соответствует...
Определение места расположения распределительного центра: Фирма реализует продукцию на рынках сбыта и имеет постоянных поставщиков в разных регионах. Увеличение объема продаж...
Интересное:
Уполаживание и террасирование склонов: Если глубина оврага более 5 м необходимо устройство берм. Варианты использования оврагов для градостроительных целей...
Финансовый рынок и его значение в управлении денежными потоками на современном этапе: любому предприятию для расширения производства и увеличения прибыли нужны...
Распространение рака на другие отдаленные от желудка органы: Характерных симптомов рака желудка не существует. Выраженные симптомы появляются, когда опухоль...
Дисциплины:
![]() |
![]() |
5.00
из
|
Заказать работу |
|
|
Система ТРМ: хроника внедрения. Развертывание системы ТРМ на ОАО «Большевик» проводилось по специально разработанной программе, соответствующей программе, рекомендуемой Японской ассоциацией производственного обслуживания (JIPM).
Внедрение началось с подготовительного этапа.
На первом шаге этого этапа (в марте 2002 г.) директор по производству внес предложение о внедрении системы ТРМ.
На втором шаге были переведены с английского языка методические материалы по развертыванию системы ТРМ, после чего в апреле-мае 2002 г. 74 менеджера высшего и среднего звеньев прошли обучение методологии внедрения системы ТРМ.
25 июля 2002 г. состоялась информационная встреча, посвященная началу внедрения системы ТРМ, с участием менеджеров высшего и среднего звеньев Производственной дирекции и представителей других дирекций. На фабрике это мероприятие называют «Старт ТРМ», но основные действия по развертыванию системы начались гораздо позже — когда в работу включился основной производственный персонал.
На третьем шаге (13 сентября 2002 г.) были созданы головные органы организационной структуры ТРМ: Совет по внедрению ТРМ и его Секретариат.
В октябре 2002 г. были сформированы две проектные группы, в которые вошли 23 менеджера высшего звена. В течении трех месяцев участники этих групп осваивали технологию осуществления первых трех шагов самостоятельного обслуживания оборудования. На этом оборудовании коэффициент общей эффективности возрос с 58 до 85%.
С февраля 2003 г. в течении полугода на фабрике действовали пять модельных групп, состоящих из менеджеров среднего и низового звеньев, технических специалистов и производственного персонала. Ими также были обработаны технологии проведения первых трех шагов самостоятельного обслуживания оборудования и подано 51 предложение по отдельным улучшениям.
|
На четвертом шаге (с февраля по апрель 2003 г.) на заседании Совета по внедрению ТРМ была утверждена система показателей для оценки результативности и эффективности развертывания системы ТРМ и было принято решение о создании инструмента для анализа результатов мероприятий, проводимых в рамках развертывания системы.
На пятом шаге были разработаны Генеральный план и План мероприятий по внедрению системы ТРМ в Производственной дирекции ОАО «Большевик». 25 февраля 2003 г. генеральный директор фабрики утвердил эти документы.
В результате проведения мероприятий пяти указанных шагов руководство укрепилось во мнении, что внедрять ТРМ нужно и возможно. На следующем шаге 27-31 марта 2003 г. о начале внедрения системы ТРМ было объявлено персоналу фабрики, партнерам, представителям прессы. Собственно, это и стало шестым шагом — этапом «Начало внедрения системы ТРМ».
Как видно из выше описанного, первые результаты были получены еще до официального объявления о начале внедрения системы ТРМ на фабрике.
После этого начался этап «Внедрение системы ТРМ», на котором развертывание системы по десяти направлениям поддерживают специалисты, входящие в состав соответствующих тематических групп. В марте 2003 г. начали работу девять тематических групп. Десятая группа — «ТРМ в управленческих и обслуживающих структурах» — приступила к работе в январе 2005 г.
Основное направление развертывания системы ТРМ в Производственной дирекции ОАО «Большевик» — «Самостоятельное обслуживание оборудования операторами», мероприятия по которому реализуют операторы производственного процесса и ремонтники, объединенные соответственно в рабочие группы ТРМ цехов и рабочие группы ТРМ технических служб. Приведем основные этапы их деятельности по этому направлению.
В августе 2003 г. для поддержки финансирования рабочих групп были созданы Малые советы ТРМ цехов и Малый совет ТРМ технических служб.
|
В ноябре 2003 г. свою деятельность начали рабочие группы ТРМ цехов. Как видно, с момента начала внедрения ТРМ прошло более полу го да. Специалисты фабрики тщательно готовились к привлечению операторов.
С декабря 2003 г. по июнь 2004 г. участники рабочих групп ТРМ цехов в течение шести месяцев осуществляли мероприятия первого шага направления «Самостоятельное обслуживание оборудования операторами» — проводили чистку, совмещаемую с проверкой. Операторами было подано более 300 предложений по отдельным улучшениям.
С июля по декабрь 2004 г. участники рабочих групп ТРМ цехов принимали меры по источникам загрязнений, труднодоступным и сложным местам: выполняли мероприятия второго шага направления. В результате ими было подано еще 178 предложений по отдельным улучшениям.
С января по сентябрь 2005 г. участники рабочих групп ТРМ цехов и технических служб совместно разрабатывали «Временные нормы чистки, смазки, проверки» в рамках проведения мероприятий третьего шага.
Хотя информация о влиянии системы ТРМ на финансово-экономические показатели ОАО «Большевик» не разглашается, сам факт продолжения развертывания системы дает основание предположить, что эффект достаточно высокий. Вообще в результате внедрения этой системы, согласно определению ЛРМ, создается механизм, обеспечивающий «нуль несчастных случаев», «нуль брака», «нуль поломок». А, кроме того, коэффициент общей эффективности оборудования должен достичь 85%.
Источник. Пшенникова М.В. Система ТРМ: хроника внедрения // Методы менеджмента качества. 2005. № 10. С. 13-16.
Особенностью системы полного технического обслуживания оборудования являются: ориентация на максимизацию эффективности использования оборудования, охват всего жизненного цикла оборудования и всех подразделений предприятия, вовлечение в систему всего персонала — от руководителей до рядовых рабочих, охват системы рычагами управления через деятельность малых групп. Ключевым моментом в организации системы является самостоятельное обслуживание оборудования рабочими операторами, обеспечение заинтересованности рабочих в максимальной эффективности работы станков и другого технологического оборудования.
|
Создание системы полного технического обслуживания оборудования предполагает осуществление следующего комплекса мероприятий:
· формирование и поддержание оптимальной структуры парка оборудования с учетом особенностей выпускаемой продукции, технологии и объемов производства;
· обеспечение эффективной работы каждой единицы оборудования за счет конкретных усовершенствований как самого оборудования, так и системы его технического обслуживания;
· изменение обязанностей всех работающих таким образом, чтобы каждый рабочий-оператор не только выполнял производственные функции, но и самостоятельно обслуживал то оборудование, на котором работает;
· систематическое повышение квалификации и обучение рабочих-операторов и обслуживающих бригад;
· создание специальных организационных структур, ответственных за состояние оборудования и выполняющих функции календарного планирования ремонта, обеспечения запасными частями, осуществления модернизации оборудования и т.п.
|
|
Общие условия выбора системы дренажа: Система дренажа выбирается в зависимости от характера защищаемого...
История развития пистолетов-пулеметов: Предпосылкой для возникновения пистолетов-пулеметов послужила давняя тенденция тяготения винтовок...
История развития хранилищ для нефти: Первые склады нефти появились в XVII веке. Они представляли собой землянные ямы-амбара глубиной 4…5 м...
Папиллярные узоры пальцев рук - маркер спортивных способностей: дерматоглифические признаки формируются на 3-5 месяце беременности, не изменяются в течение жизни...
© cyberpedia.su 2017-2024 - Не является автором материалов. Исключительное право сохранено за автором текста.
Если вы не хотите, чтобы данный материал был у нас на сайте, перейдите по ссылке: Нарушение авторских прав. Мы поможем в написании вашей работы!