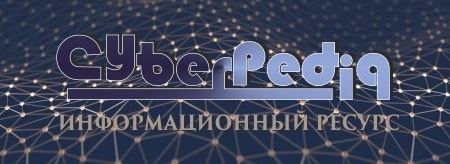
Кормораздатчик мобильный электрифицированный: схема и процесс работы устройства...
История создания датчика движения: Первый прибор для обнаружения движения был изобретен немецким физиком Генрихом Герцем...
Топ:
Определение места расположения распределительного центра: Фирма реализует продукцию на рынках сбыта и имеет постоянных поставщиков в разных регионах. Увеличение объема продаж...
Особенности труда и отдыха в условиях низких температур: К работам при низких температурах на открытом воздухе и в не отапливаемых помещениях допускаются лица не моложе 18 лет, прошедшие...
Отражение на счетах бухгалтерского учета процесса приобретения: Процесс заготовления представляет систему экономических событий, включающих приобретение организацией у поставщиков сырья...
Интересное:
Искусственное повышение поверхности территории: Варианты искусственного повышения поверхности территории необходимо выбирать на основе анализа следующих характеристик защищаемой территории...
Лечение прогрессирующих форм рака: Одним из наиболее важных достижений экспериментальной химиотерапии опухолей, начатой в 60-х и реализованной в 70-х годах, является...
Инженерная защита территорий, зданий и сооружений от опасных геологических процессов: Изучение оползневых явлений, оценка устойчивости склонов и проектирование противооползневых сооружений — актуальнейшие задачи, стоящие перед отечественными...
Дисциплины:
![]() |
![]() |
5.00
из
|
Заказать работу |
|
|
По технологическому принципу различают следующие основные разновидности зубчатых колес:
1) цилиндрические и конические колеса без ступицы и со ступицей, с гладким или шлицевым отверстием;
2) многовенцовые блочные колеса с гладким или шлицевым отверстием;
3) цилиндрические, конические, червячные колеса типа фланцев;
4) цилиндрические и конические колеса с хвостовиком;
5) валы-шестерни.
5.2. Общие принципы обработки зубчатых колес
При обработке зубчатых колес можно условно выделить два этапа: обработка до нарезания зубьев и обработка зубчатого венца.
Задачи первого этапа соответствуют аналогичным задачам, решаемым при обработке деталей классов:
- диски (плоские колеса без ступицы);
- втулки (со ступицей);
- валы (вал-шестерня).
Задачи второго этапа решаются в сочетании с отделочными операциями обработки корпуса колеса.
При построении технологического процесса обработки зубчатых колес учитывают:
- конструкцию и размеры колеса;
- форму и расположение зубчатого венца, количество венцов;
- точность и качество поверхностей;
- вид исходной заготовки;
- материал колеса и его термическую обработку;
- методы контроля зубчатого колеса;
- годовую программу выпуска.
Протяженность технологического маршрута обработки зубчатого колеса главным образом зависит от степени точности колеса. При изготовлении зубчатых колес высоких степеней точности (6, 5 и выше) механическая обработка должна чередоваться с операциями термической обработки для снятия остаточных напряжений («термическая стабилизация»). При этом существенно возрастает также число отделочных операций технологических баз и зубчатого венца.
|
5.3. Технологические задачи и типовые требования
к точности некоторых поверхностей зубчатых колес
5.3.1. Точность размеров
Самый точный элемент зубчатого колеса – это, как правило, отверстие D (рис. 5.1). Его изготовляют по Н6 для зубчатых колес 5-й степени точности, по Н7 для зубчатых колес 6, 7, 8-й степени точности, по Н8 для колес 9-й степени точности.
Точность окружности выступов d зубчатого венца зависит от метода контроля толщины зуба. Если d является измерительной базой, то допуск Td = 0,5Tн, где Tн - допуск на смещение исходного контура. Если d не является измерительной базой, то диаметр d можно изготавливать по IT12.
Рис. 5.1. Типовые требования к точности зубчатых колес
5.3.2. Точность формы
Как правило, особых требований нет.
5.3.3. Точность взаимного расположения
Если d используется для контроля толщины зуба, например, при контроле смещения исходного контура, то радиальное биение поверхности вершин зубьев относительно оси отверстия (измерительной базы) не более 0,25Tн.
Если d используется для выверки, т.е. в качестве технологической базы, то радиальное биение поверхности вершин зубьев относительно оси отверстия не более (0,6…0,65)Fr, где Fr - допуск радиального биения зубчатого венца.
При lст/D≥0,8 (lст - длина ступицы, D – диаметр базового отверстия) и сопряжении зубчатого колеса с валом по посадкам H7/g6, H7/f6 и H7/p6, H7/r6, H7/s6 торцевое биение базового торца зубчатого венца относительно оси отверстия не более 0,5Fβ, где Fβ - допуск направления зуба.
При lст/D<0,8 (lст - длина ступицы, D – диаметр базового отверстия) и сопряжении зубчатого колеса с валом по посадкам H7/k6, H7/n6, H7/m6, H7/js6 и H7/p6, H7/r6, H7/s6 торцевое биение базового торца зубчатого венца относительно оси отверстия не более 1/3*(d/lст)Fβ, где Fβ - допуск направления зуба.
Технологическое ограничение на торцевое биение при обработке зубчатых колес пакетом Fт≤0,25(d/B)Fβ, где Fβ – допуск на направление зуба;
Отклонение от параллельности оси шпоночного паза оси базового отверстия в пределах половины допуска на ширину паза.
|
Отклонение от симметричности оси шпоночного паза оси базового отверстия в пределах удвоенного допуска на ширину паза.
5.3.4. Твердость рабочих поверхностей
В результате термической обработки поверхностная твердость зубьев цементируемых зубчатых колес должна быть в пределах 45…60HRC при глубине цементированного слоя 1…2 мм. При цианировании твердость 42…53HRC, глубина упрочненного слоя 0,5…0,8 мм.
Твердость незакаливаемых поверхностей в пределах 180…270НВ.
5.3.5. Шероховатость базовых поверхностей
Отверстие, рабочие торцы, боковые поверхности зубьев – в пределах Ra = 1,6…0,4 мкм.
5.4. Материалы и заготовки
В зависимости от служебного назначения зубчатые колеса изготовляют из чугуна, углеродистых и легированных сталей, пластмасс, цветных металлов. Зубчатые колеса из легированных сталей лучше прокаливаются и меньше деформируются в сравнении с колесами из углеродистых сталей.
Материал зубчатого колеса должен иметь однородную структуру для стабильности размеров после термической обработки. Это особенно важно для размера отверстия и шага зубьев. Нестабильность структуры может возникнуть вследствие цементации и закалки при сохранении остаточного аустенита, а также в результате наклепа и при механической обработке.
Наибольшее коробление создает цементация, меньшее – закалка. Поэтому часто исправление коробления и повышение точности шевингованием выполняют после цементации, но до закалки.
Основные виды заготовок для зубчатых колес зависят от конструкции колеса и серийности выпуска. Это может быть:
- прокат;
- поковка, полученная свободной ковкой на ковочном молоте;
- штампованная заготовка в подкладных штампах (на молотах или прессах);
- штампованная заготовка в закрепленных штампах (на молотах, прессах или горизонтально-ковочных машинах);
- отливка;
- заготовка с зубьями, накатанными в холодном или горячем состоянии, образованными горячей или холодной штамповкой или при литье (для крупномодульных зубчатых колес).
Свободная ковка на молотах не обеспечивает получения конфигурации готовой детали, но улучшает структуру металла в сравнении с заготовкой, отрезанной от прутка.
При использовании штамповок, полученных в закрытых штампах, снижается расход металла из-за отсутствия облоя (до 10…30%), форма заготовки приближена к готовой детали, снижается себестоимость. Однако возрастает расход штампов.
|
Штамповка на прессах (в сравнении с молотами) обеспечивает заготовки, наиболее точные и близкие к форме готовой детали (припуски и напуски снижаются на 30%). На прессах можно штамповать заготовки с прошивкой отверстия.
Штамповка на ГКМ применяется для получения заготовок зубчатых колес с хвостовиком или с отверстием.
5.5. Технологические базы и основные схемы базирования
5.5.1. Требования к выбору технологических баз
Основными требованиями, учитываемыми при выборе чистовых технологических баз для обработки зубчатых колес, являются:
(1) обеспечить совмещение технологических баз с конструкторскими посадочными поверхностями;
(2) в качестве опорной технологической базы должен использоваться торец, обработанный совместно с основными посадочными поверхностями;
(3) при шевинговании базы должны совпадать с базами, используемыми при чистовом нарезании зубьев.
5.5.2. Основные схемы базирования
Выбор схем базирования зависит от конструктивных особенностей зубчатого колеса.
Для колес со ступицей (одно- и многовенцовых) при достаточной длине центрального базового отверстия (l/d>1) технологическая база – двойная направляющая поверхность отверстия и опорная база – поверхность торца.
Для одновенцовых колес типа дисков (l/d<1) после обработки отверстия и торца торец – установочная база, отверстие – двойная опорная база.
Для валов-шестерен технологические базы – как правило, поверхности центровых отверстий.
На первой операции для обеспечения наилучшей концентричности поверхностей вращения используют варианты базирования:
1) при обработке на токарных станках за одну установку штампованных и литых заготовок их закрепляют в кулачках патрона за «черную» поверхность ступицы или «черную» внутреннюю поверхность обода;
2) при обработке за две установки заготовку сначала крепят за «черную» поверхность обода и обрабатывают отверстие, а при второй установке заготовки на оправку обрабатывают поверхность обода и другие поверхности колеса.
|
После обработки отверстия и торца именно их принимают технологическими базами для большинства операций.
Колеса с нарезанными зубьями после упрочняющей термической обработки при шлифовании отверстия и торца в одном установе (восстановление технологических баз) базируют по эвольвентной боковой поверхности зубьев для обеспечения соосности начальной окружности и посадочного отверстия.
5.5.3. Основные рекомендации по выбору баз при обработке зубьев
Валы-шестерни
Базы – посадочные шейки, упор – торец вала или торец одной из шеек большего диаметра. Центровые отверстия на торцах вала допускается использовать в качестве технологических баз только при нарезании зубчатых колес с модулем m≤6 мм. Установочно-зажимные элементы – трехкулачковые самоцентрирующие и четырехкулачковые патроны с поддержкой центром в случае предварительной обработки посадочных шеек. При шевинговании – на центрах или в люнетах по рабочим шейкам с упором в торец.
У закаленных валов-шестерен отделку посадочных шеек после термообработки выполняют на восстановленных центровых отверстиях.
|
|
Индивидуальные очистные сооружения: К классу индивидуальных очистных сооружений относят сооружения, пропускная способность которых...
Общие условия выбора системы дренажа: Система дренажа выбирается в зависимости от характера защищаемого...
Организация стока поверхностных вод: Наибольшее количество влаги на земном шаре испаряется с поверхности морей и океанов (88‰)...
Двойное оплодотворение у цветковых растений: Оплодотворение - это процесс слияния мужской и женской половых клеток с образованием зиготы...
© cyberpedia.su 2017-2024 - Не является автором материалов. Исключительное право сохранено за автором текста.
Если вы не хотите, чтобы данный материал был у нас на сайте, перейдите по ссылке: Нарушение авторских прав. Мы поможем в написании вашей работы!