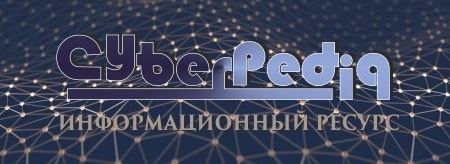
Наброски и зарисовки растений, плодов, цветов: Освоить конструктивное построение структуры дерева через зарисовки отдельных деревьев, группы деревьев...
Архитектура электронного правительства: Единая архитектура – это методологический подход при создании системы управления государства, который строится...
Топ:
Оснащения врачебно-сестринской бригады.
Методика измерений сопротивления растеканию тока анодного заземления: Анодный заземлитель (анод) – проводник, погруженный в электролитическую среду (грунт, раствор электролита) и подключенный к положительному...
Определение места расположения распределительного центра: Фирма реализует продукцию на рынках сбыта и имеет постоянных поставщиков в разных регионах. Увеличение объема продаж...
Интересное:
Подходы к решению темы фильма: Существует три основных типа исторического фильма, имеющих между собой много общего...
Средства для ингаляционного наркоза: Наркоз наступает в результате вдыхания (ингаляции) средств, которое осуществляют или с помощью маски...
Наиболее распространенные виды рака: Раковая опухоль — это самостоятельное новообразование, которое может возникнуть и от повышенного давления...
Дисциплины:
![]() |
![]() |
5.00
из
|
Заказать работу |
|
|
Режим ручной дуговой электросварки определяется диаметром электрода, величиной сварочного тока и длиной дуги.
Диаметр электрода устанавливают в зависимости от толщины свариваемых кромок, вида сварного соединения и размеров шва.
а) Для стыковых соединений приняты практические рекомендации по выбору диаметра электрода в зависимости от толщины свариваемого металла
При выборе диаметра электрода нужно учитывать также положение шва в пространстве. Вертикальные швы свариваются электродами диаметром не более 5 – 6 мм, а потолочные – не более 4 мм.
При выполнении угловых и тавровых соединений принимают во внимание размер катета шва. При катете шва 3…5 мм сварку производят электродом диаметром 3…4 мм; при катете 6…8 мм - диаметр электрода 4…5 мм.
За катет К принимают меньший катет вписанного в сечение шва сварного соединения неравнобедренного треугольника и равнобедренного треугольника.
Величина сварочного тока указывается га заводской этикетке, наклеиваемой на пачке электродов.
б) Величину тока при необходимости определяют по формуле:
![]() | (3) |
Где - коэффициент, принимаемый в зависимости от толщины обмазки в пределах от 35 до 60 (чем толще обмазка, тем больше значение
).
В среднем принимается 40 а на каждый 1 мм диаметра электрода.
в) На качество сварки значительно влияет также длина дуги: чем она короче, тем выше качество наплавленного металла.
![]() | (4) |
Зажигание дуги осуществляется прикасанием электрода к свариваемому изделию и отрывом его от изделия на величину 2 – 5 мм. В дальнейшем электроду необходимо сообщить 3 движения.
Рис. 13
Рис 13 Схема основных движений электрода
1 – подает электроду по мере его плавления вниз для поддержания постоянной дуги, 2 – перемещает его под углом 15 – 20 º к вертикали вдоль оси шва в сторону движения для заполнения разделки кромок. И 3 – дает электроду колебательные движения поперек шва для поучения уширенного валика.
|
В настоящее время разработаны скоростные методы ручной дуговой сварки.
- Сварка с глубоким проплавлением: Электрод опирается обмазкой на край изделия и перемещается вдоль шва без поперечных колебательных движений. Скорость и производительность сварки возрастает в 1,5 – 2 раза за счет увеличения доли основного металла в наплавленном металле шва, увеличение сварочного тока, более полного использования электродного металла.
- Сварка пучком электродов: два или несколько электродов связывают вместе в пучок, вставляемый в обычный электрододержатель. Дуга возбуждается у электрода, торец которого ближе к изделию, а затем по мере оплавления дуга автоматически переходит от одного электрода к другому. Сварка пучком электродов повышает производительность труда, уменьшает время на замену электродов и позволяет значительно повысить величину сварочного тока.
- При сварке трехфазной дугой две фазы источника переменного тока подключаются к двум качественным электродам, а третья – к свариваемому изделию (источники – специальные трехфазные трансформаторы). В процессе сварки возбуждаются 3 дуги: две – между каждым электродом и изделием и третья – между электродами. При этом выделяется большое количество тепла, что увеличивает производительность сварки в 2 – 3 раза, экономится электроэнергия, увеличивается устойчивость горения дуги.
Преимущества ручной сварки:
1) возможна в любых пространственных положениях (потолочном, горизонтальном, вертикальном) и в труднодоступных местах. Например корпуса судов – ручной дуговой.
2) хорошее качество швов.
Недостатки:
1)низкая производительность
2) сильное разбрызгивание металла
3) угар электрода.
Ручную сварку заменяют полуавтоматической.
|
Полуавтоматическая сварка
Сварка в струе углекислого газа осуществляется полуавтоматической установкой. Схема в лабораторной работе.
Сварщик выполняет только одно движение – перемещает горелку по траектории сварного шва. Электродная проволока и углекислый газ подаются в зону дуги через специальную газоэлектрическую горелку. Углекислый газ защищает место сварки от окружающего воздуха. Сварка выполняется постоянным током прямой полярности.
Для компенсации окислительного действия углекислого газа повышают содержание растительных примесей в электродной проволоке.
Плюсы:
1) возрастает в 1,5 – 2 раза производительность;
2) Допускает сварку металла малой толщины во всех пространственных положениях.
Автоматическая сварка
а) Под слоем флюса.
Рис 5
Рис 5 Схема автоматической дуговой сварки под флюсом
Электрическая дуга горит между концом голой электродной проволоки 3 и кромками свариваемого металла 2 под слоем гранулированного флюса. Подача проволоки из кассеты 6 в зону дуги осуществляется сварочной головкой 5. Флюс засыпается в разделку кромок1 впереди дуги из бункера 4. Сварной шов образуется либо в процессе перемещения сварочной головки относительно неподвижного изделия, либо при перемещении изделия относительно неподвижной сварочной головки со скоростью сварки.
В процессе сварки часть флюса расплавляется и при остывании образует легко удаляемую шлаковую корку. Нерасплавленный флюс поступает обратно в бункер через сопло и шланг 7.
Применение флюсов обеспечивает изоляцию сварочной ванны от кислорода и азота воздуха, исключает потери металла на угар и разбрызгивание.
Плюсы:
1) Производительность увеличивается в 5 – 20 раз.
2) Качество шва высокое.
3)Экономится электроэнергия и улучшаются условия труда сварщика (квалификация ниже).
Сваркой под флюсом получают неразъемные соединения деталей толщиной до 30 – 40 мм из углеродистых и легированных сталей, а также цветных сплавов (медь и сплавы, никель и сплавы) титан – нельзя из-за недостаточной защиты.
б) Электрошлаковая сварка.
Рис 6
Рис 6 Схема электрошлаковой сварки: вертикальная стрелка указывает направление сварки, а горизонтальные – направление перемещения электродов в зазоре
|
Свариваемые детали 1 располагают вертикально с зазором 20 – 40 мм. В зону сварки автоматически подается один или несколько электродов 4 и засыпается флюс. Процесс сварки начинается с возбуждения и поддержания дуги под флюсом между электродом и начальной планкой, перекрывающей нижние кромки свариваемых листов. Для предупреждения растекания жидкого металла и флюсов и для принудительного формирования шва применяются медные ползуны 2, охлаждаемые водой.
После расплавления флюса и образования шлаковой ванны 3 дуга гаснет, и ток от электрода к изделию идет только через жидкий шлак. Сварочный процесс из дугового переходит в электрошлаковый.
Выделяющееся при прохождении тока через расплавленный шлак тепло обеспечивает дальнейшее расплавление основного и электродного металлов. Перемешиваясь, они образуют общую сварочную ванну 5. Сварочная головка перемещается по изделию снизу вверх вместе с ползунами, формирующими сварной шов. Сварка заканчивается на конечной планке, куда выводится конечная ванна со скопившимися в ней газовыми пузырями и шлаковыми включениями. После окончания сварки планки отрезают.
Электрошлаковая сварка позволяет сваривать за один проход металл практически неограниченной толщины, обеспечивает высокую производительность, хорошее качество сварных соединений, не требует разделки кромок, по сравнению с автоматической сваркой под флюсом расходует меньше электроэнергии и флюсов.
Минус: крупнозернистый металл шва (σв меньше, δ меньше). Это можно устранить последующей т/о.
За счет принудительного формирования шва можно получить большой объем сварочной ванны. Это позволяет выполнить вертикальные швы, а также сваривать стыковые соединения металла большой толщины.
Применяется при изготовлении крупногабаритных конструкций. Освоении электрошлаковой сварки позволило заменить громоздкие и тяжелые цельнолитые и цельнокованые станины и корпуса более легкими и компактными сварно-литыми и сварно-коваными деталями.
в) Дуговая сварка в среде защищенных газов изоляции расплавленного металла от вредного воздействия кислорода и азота воздуха обеспечивается также путем создания газовой атмосферы вокруг дуги и зоны сварки.
|
Применяются инженерные газы (аргон и гелий) и активные (азот, углекислый газ) защитные газы.
Аргонно-дуговая сварка
-неплавящимся W электродом
- плавящим металлическим электродом.
Рис 8 а Сварка неплавящимся электродом
Рис 8 дуговая сварка в среде защитных газов
Электрическая дуга 5 горит между вольфрамовым электродом 4 и свариваемым металлом 1. Защитный газ 2 подается через кольцевой мундштук (держатель электрода) 3 и обволакивает всю зону дуги и сварочную ванну. Это обеспечивает получение наплавленного металла с высокими механическими свойствами. Сварку неплавящимся электродом ведут на постоянном токе прямой и обратной полярности и на переменном токе. Применяют присадочный материал.
Варить можно все, но метод малопроизводителен и дорогой из-за газ. Поэтому применяется для сварки титана, алюминия, легированных сталей небольшой толщины.
Рис 8 б. Сварка плавящим электродом 6.
Производится на постоянном токе обратной полярности. Целесообразна для соединения металлов толщиной не менее 3 мм.
г) При автоматической дуговой сварке углеродистых и низколегированных сталей плавящимся электродом в качестве защитного газа применяют углекислый газ, который в 10-15 раз дешевле аргона. Для предотвращения окислительного влияния его на сварочную ванну применяют электродную проволоку с повышенным содержанием раскислителей – кремния и марганца. Сварку ведут на постоянном токе обратной полярности. Принцип аналогичен аргоно-дуговой.
Газовая сварка
Это сварка плавлением. Нагрев идет за счет сгорания горючих веществ в струе кислорода. В качестве горючего используют ацетилен, углерод, природный газ, пары бензина, керосина и т. д.
Наибольшее применение получил ацетилен, который по сравнению с другим горючим дает более высокую температуру и наибольшее количество тепла в рабочей зоне сварочного пламени (в 10 – 15 раз дороже остальных горючих). Сгорая в кислороде дает самую высокую температуру пламени 3200 º С.
Технический ацетилен получают в генераторах, воздействую на карбид кальция водой
CaC2 + 2H2O = Ca(OH)2 + C2H2
Ацетилен – взрывоопасный газ
C2H2 может храниться и использоваться и в специальных стальных баллонах, окрашенных в белый цвет с надписью "ацетилен" красной краской. Баллон, с целью предохранения от взрыва, наполнен активированным углем, пропитанным ацетоном.
Кислород хранят и транспортируют в стальных баллонах голубого цвета с надписью "кислород" черными буквами. На баллоне имеется редуктор для понижения давления и для поддержания постоянного расхода газа.
Основной инструмент сварщика является газовая горелка, где происходит образование ацетиленокислородной смеси и ее сжигание с целью получения высокотемпературного концентрированного сварочного пламени. Сварочные горелки делятся на инжекторные (низкого давления) и безинжекторные (высокого или равного давления). Наиболее применяются – инжекторные.
|
Рис 12
Рис 12 принципиальная схема инжекторной горелки
В такую горелку кислород подается под давлением равным 0,3 – 0,4 Мн/м2. Вытекая с большой скоростью из сопла инжектора 4, струя создает разряжение, обеспечивающее подсос ацетилена в смесительную камеру 3. Из смесительной камеры C2H2 – О2 смесь подается через трубку 2 и мундштук 1 выталкивается в атмосферу, где, воспламеняясь, образует сварочное пламя.
Достоинства: простота оборудования и универсальность, позволяющая сваривать различные металлы разных толщин, что делает газовую сварку почти незаменимой в ремонтном деле.
При газовой сварке происходит более плавный нагрев свариваемого металла, чем при электродуговой. Это особенно важно при соединении сталей небольших толщин, сварке легкоплавких металлов, а также сварки чугуна с предварительным подогревом.
Газовую сварку в стационарных условиях не применяют (дорого и малопроизводительно). Применение – ремонто-монтаж, аварийные работы.
Пламя в зависимости от соотношения ацетилена и кислорода различают нормальное (восстановительное), окислительное и науглераживающее (ацетиленовое).
Состоит из трех зон:
1) ядро (5-20 мм) С2Н2 и О2 – ослепительно белый цвет
2) восстановительная зона СО + Н2 – синеватый цвет
3) окислительная зона СО2 + Н2О – максимальная температура, желто-красный цвет.
Нормальное пламя - = 1 – 1,2
Это вид не вызывает не окисления расплавленного металла, ни насыщение его углеродом.
Нормальным пламенем свариваемым большинство металлов. Окислительное пламя >1, 2 (избыток кислорода). Имеет голубоватый оттенок, горит с шумом. Отличается однородным ядром м факелом. Температура выше, чем у нормального. Используется для сварки низкоуглеродистой стали с присадочной проволокой, содержащей большое количество раскислителей (Марганец, кремний), латуни (для образования окисной пленки, предохраняющей цинк от испарения).
Науглераживающее пламя < 1 т. е. избыток ацетилена. Пламя имеет желтый цвет и коптит. Применяется при сварке высокоуглеродистых сталей и чугуна, что способствует пополнению углерода, выгорающего при сварке.
Техника газовой сварки.
Основной вид сварочного соединения – встык. Качество сварочного шва обеспечивается перевыбором сварочного режима и способа перемещения сварочной горелки и присадочного материала по шву.
Угол наклона мундштука горелки к поверхности свариваемой детали (Рис 10 а) выбирается в зависимости от толщины металла и его теплопроводности. Чем выше толщина свариваемого металла и его теплопроводность, тем больше должен быть угол наклона. Присадочный материал вводят под углом 30 – 40 º к поверхности детали.
Различают два способа газовой сварки: левый и правый.
При левой сварке рис 10 (б) горелку перемещают справа налево вслед за присадочной проволокой. Сварочное пламя направлено в сторону незаваренного шва.
При правой сварке – слева направо. Впереди перемещается пламя сварочной горелки, направленное на уже заваренный шов, а за ней следует пруток присадочного металла. При этом лучше использовать тепло пламени.
Режим газовой сварки.
1. Выбор мощности сварного пламени определяют по расходу ацетилена.
![]() | (5) |
Где – толщина свариваемого металла
К – коэффициент, экспериментально определяемый для различных материалов
К = 100 для чугуна и углеродистой стали
К = 75 для алюминия
К = 150 – 200 для меди (т. к. высокая теплопроводность)
2. Диаметр присадочной проволоки примерно берется на 1 – 2 мм больше половины свариваемых листов.
Резка металлов.
Применяется при невозможности использовать механическую резку или экономически целесообразна. Различают газовую и электродуговую.
Газовая резка.
Сущность: сжигание нагретого металла в струе кислорода и выдувание образовавшихся окислов из листа разреза.
Рис 11 резак инжекторного типа для кислородной резки
Резка осуществляется на том же оборудовании, что и сварка, лишь вместо горелки применяются специальные резаки. Резак (Рис 11) в отличие от горелки не только подает по каналу 2 газовую смесь для нагрева металла, но и имеет дополнительный канал 1 для подведения режущей струи кислорода. Газовую резку можно применять лишь для тех металлов, у которых температура плавления выше температуры воспламенения в кислороде и выше температуры плавления их окислов (железо, титан, углеродистые стали с содержанием углерода до 0,7 %, низколегированные стали). Чугун, большинство легированных сталей, алюминий, медь и их сплавы кислородной резке не поддаются, т. к. не отвечают этим требованиям – тугоплавкие окислы. Медь и ее сплавы – теплопроводность очень высокая – не режется кислородно-газовой резкой.
Схема ацетиленокислородной резки.
Металл в месте реза пламени подогревают до температуры воспламенения, а затем пускают струю кислорода, которая сжигает металл и выдувает полученные окислы из реза.
Для них – кислородно-флюсовая сварка (подача в режущую струю кислорода флюсы(порошки железа), при сгорании которого выделяется дополнительное тепло и отфлюсовываются образующиеся окислы).
Электродуговая резка.
Металл расплавляется в зоне реза электрической дугой. Этим способом можно резать любые металлы и сплавы. Резку ведут как на постоянном, так и на переменном токе, применяя тоже оборудование, что и для дуговой электросварки графитовым (или угольным) электродом или металлическим электродом с толстой обмазкой. Ввиду малой производительности и значительной неровности поверхности реза электродуговая резка не имеет большого распространения и применяется для разрезки лома, отрезки литников, прибылей, выпоров отливок высоколегированных сталей.
|
|
История развития хранилищ для нефти: Первые склады нефти появились в XVII веке. Они представляли собой землянные ямы-амбара глубиной 4…5 м...
История создания датчика движения: Первый прибор для обнаружения движения был изобретен немецким физиком Генрихом Герцем...
Таксономические единицы (категории) растений: Каждая система классификации состоит из определённых соподчиненных друг другу...
Кормораздатчик мобильный электрифицированный: схема и процесс работы устройства...
© cyberpedia.su 2017-2024 - Не является автором материалов. Исключительное право сохранено за автором текста.
Если вы не хотите, чтобы данный материал был у нас на сайте, перейдите по ссылке: Нарушение авторских прав. Мы поможем в написании вашей работы!