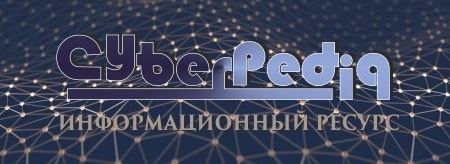
Организация стока поверхностных вод: Наибольшее количество влаги на земном шаре испаряется с поверхности морей и океанов (88‰)...
Таксономические единицы (категории) растений: Каждая система классификации состоит из определённых соподчиненных друг другу...
Топ:
История развития методов оптимизации: теорема Куна-Таккера, метод Лагранжа, роль выпуклости в оптимизации...
Устройство и оснащение процедурного кабинета: Решающая роль в обеспечении правильного лечения пациентов отводится процедурной медсестре...
Методика измерений сопротивления растеканию тока анодного заземления: Анодный заземлитель (анод) – проводник, погруженный в электролитическую среду (грунт, раствор электролита) и подключенный к положительному...
Интересное:
Средства для ингаляционного наркоза: Наркоз наступает в результате вдыхания (ингаляции) средств, которое осуществляют или с помощью маски...
Наиболее распространенные виды рака: Раковая опухоль — это самостоятельное новообразование, которое может возникнуть и от повышенного давления...
Принципы управления денежными потоками: одним из методов контроля за состоянием денежной наличности является...
Дисциплины:
![]() |
![]() |
5.00
из
|
Заказать работу |
|
|
Сварка.
Сварка – технологический процесс получения неразъемного соединения деталей, осуществляемый за счет использования межатомных сил сцеплений. Для соединения двух или более частей металла в одно целое необходимо осуществить тесное сближение их атомов на расстояние порядка 4·10−8 см, чтобы между ними начали действовать силы взаимного притяжения.
Ядра атомов имеют положительный заряд. Силы притяжения действуют на расстоянии 2 – 5 А.
Поверхность любого гладкого тела не является ровной, имеются микронеровности. Даже после полировки шероховатость?
Причины, препятствующие образованию сварных соединений:
1) Шероховатость поверхности
2) Наличие на поверхности прилипших (адсорбированных) молекул газов, окислов и т. д.
Для сближения атомов необходимо провести следующие:
а) нагрев кромки свариваемых поверхностей Тнагр > Тпл до образования общей ванны жидкого металла. После затвердевания образуется сварной шов.
б) Создание в месте контакта напряжений, превышающих предел текучести.
σ > σТ.
Гребни сжимаются, молекулы газа отскакивают. В процессе происходит снятие неровностей и течение металла вдоль соединяемых поверхностей, сто приводит к разрушению и удалению окисных пленок и обеспечивается условие возникновения межатомных связей.
в) нагрев (ниже Тпл) для снижения σв, НВ и приложения усилия.
В результате такого нагрева повышается способность к перемещению и диффузии.
Сварка
Классификация способов сварки.
Сварка давлением | Сварка плавлением | Давление и нагрев |
-холодная | -дуговая | -трение |
-сварка взрывом | -газовая | -ультразвук |
-электрошлаковая | -диффузионная | |
-"новые" способы сварки (сварка концентрированными источниками энергии) | -печная (кузнечно-горновая) | |
-контактная |
|
Способы сварки
1. Холодная сварка.
Заготовки соединяют путем совместной пластической деформации соединяемых поверхностей. Можно сваривать стыковые и нахлестные швы.
Детали сжимают при σ ≥ σт. Рекомендуется для пластических материалов: медь, алюминий в электромеханической промышленности.
2. Сварка взрывом.
Соединение нахлесточное. Детали могут быть больших размеров. Взрыв характеризуется большой скоростью и большим усилием. За счет энергии взрываемого вещества верхняя пластина вдавливается в нижнюю. Продолжительность сварки взрывом не превышает несколько микросекунд. Может быть использована для изготовления биметалла, для планирования поверхностей деталей конструкционных сталей металла с особыми свойствами: лист углеродистой стали + лист титана, нержавеющей стали.
3. Сварка трением.
Соединение стыковое. Две детали, одна зажимается неподвижно, вторая прижимается к первой и приводится во вращение. Происходит нагрев, металл становится мягким и пластичным и затем прижимается. Нагретый металл деформируется с образованием "воротничка". Свариваются тела вращении: кружки, трубы. Этим способом можно приваривать хвостовики к сверлам, разверткам, метчикам (экономия материала).
4. Печная (кузнечно-горновая) сварка.
При кузнечной сварке металл нагревается до состояния пластичности, а затем проковывается в местах соединения. Этим достигается плотное прилегание соединяемых кусков, образуется сварное соединение. Применяется в ремонтных мастерских.
Точечная сварка
Предназначена для соединения листовых заготовок.
Рис. 9(а)
Свариваемые детали 5 и 6 собирают внахлестку и располагают на неподвижном электроде 4. После опускания верхнего электрода 3 и сжатия деталей через них от вторичной обмотки трансформатора 1 пропускают ток. Металл в точке 2 интенсивно нагревается. Между электродами – до плавления (образуется ядро), а прилегающая к нему зона нагревается до пластического состояния. После кристаллизации ядра давление снимается.
|
Электроды – подвод тока – сжатие
Изготавливают из медных сплавов (сталь – большое сопротивление) – БрХ07. Суммарное сопротивление в цепи – сумма сопротивлений токоведущих частей.
![]() | (2) |
Где - сопротивление электрод – деталь
- собственное сопротивление детали
- контактное сопротивление детали
Сварка возможна тогда, когда >>
, чтобы все тепло выделилось в точке. Годной считается сварка, если металл вырывается с "мясом". Толщина 5мм + 5мм. Привод сжатия Р – пневматическая, гидравлическая, ручная.
Разновидностью точечной сварки является рельефная сварка, при которой одновременно сваривается несколько точек. Перед сваркой на одной из свариваемых деталей выштамповывают рельефы (выступы). При сварке выступы разогреваются и под действием давления специальных плит (электродов) расплющиваются.
Машины для точечной сварки могут быть стационарные передвижные, переносные. Наряду с одноточечными широко применяются многоточечные, у которых число электродов достигает несколько сотен, а производительность – десятков тысяч точек в час. Применяются в кораблестроении, автомобилестроении, корпус холодильника, стиральные машины.
Минусы: негерметичное соединение, высокая стоимость.
График изменения сварочного тока и усилия сжатия, совмещенные во времени, называются циклограммой. Цикл сварки состоит из следующих операций: сжатия свариваемых заготовок, включения и выключения сварочного тока и снятия усилия сжатия.
а) Сварка при постоянном давлении и применяется для сварки углеродистых и нержавеющих сталей толщиной до 3 мм.
б) Отличается тем, что после выключения сварочного тока усилие сжатия увеличивают. Это обеспечивает хорошее формирование металла и позволяет получить сварную точку повышенной прочности. Применяется для изделий из низкоуглеродистых сталей повышенной толщины.
в) Состоит из обжатия листов большим усилием перед сваркой, сварки при меньшем P U последующего обжатия повышенным усилием при выключенном токе. Применяется при сварке листов больших толщин, когда необходимо обеспечить формирование и отвердевание сварной точки.
|
4.2 Роликовая (шовная сварка)
Рис. 9 б)
Осуществляется на контактных машинах, у которых вместо стержневых электродов применяются ролики 2.
После сжатия свариваемых деталей 4 и 5 одновременно включается ток от трансформатора 1 и начинают вращаться ролики (или один ролик). Детали перемещаются между роликами или, наоборот, ролики перемещаются по детали, и металл сваривается.
Роликовую сварку можно рассматривать как разновидность точечной сварки, у которой каждая последующая точка перекрывает предыдущую, образуя сплошной прочный и сплошной шов.
Применят два способа сварки: с непрерывной подачей тока и с прерыванием тока.
Первый способ не получил распространение – могут быть непровары и пережоги. Еще существует шаговая сварка – детали перемещаются на определенный шаг, тогда включается ток.
Электроды – бронзы медь + магний, медь, бериллий, алюминий, цинк, магний или сплавы на основе вольфрама. Толщины 3+3.
Плюс: герметичность.
I = 2 – 5000 А; диаметром – 40 – 350 мм;
Усилие 6 кН; скорость сварки – 0,5 – 3,5 м/мин
Стыковая сварка
При стыковой сварке детали свариваются встык по всей поверхности соприкосновения. Сварка осуществляется на машинх ручного или автоматического действия. Рис. 7
Рис. 7 Схема сварочной машины для контактной стыковой сварки
Свариваемые детали 3 и 7 закрепляются в зажимах (губках) 4 и 6 сварочной машины. Зажим 4 укреплен на неподвижной относительно станины 1 плите 2, а затем 6 – на плите 5, которая может перемещаться по направляющим станины. Питание деталей электрическим током осуществляется через зажимы от вторичной обмотки сварочного трансформатора 8.
Существует два способа стыковой сварки: сопротивлением и оплавлением.
При сварке сопротивлением свариваемые детали вначале сближают до соприкосновения торцевыми поверхностями и сдавливают, а затем включают ток.
После нагрева деталей в зоне контакта до пластичного состояния производится осадка (сжатие) металла на величину припуска на сварку. В конце осадки ток выключается. Требует точной подгонки концов соединяемых деталей.
Минусы: ограничение по площади сечения свариваемых деталей F ≤ 300 мм2 , не хватает мощности машин, свариваются компактные сечения (кружки, трубы).
|
Сварка оплавлением возможна для изделий сечением 50000 – 60000 мм2 и более. При этом виде сварки заготовки собираются с зазором, на них подается напряжение (ток не идет). Эти детали начинают сближаться. На поверхности есть шероховатость. В месте контакта точек идет большой ток, происходит оплавление и выброс жидкого металла и так же в других точках. После образования на торцах деталей равномерного слоя расплавленного металла быстро производится осадка стыка. Начале осадки ток выключается.
Плюсы: не требуется точной подготовки торцов свариваемых деталей; улучшается качество шва, т. к. при осадке вместе с жидким металлом из стыка удаляются все загрязнения, в том числе и шлаки; сварка больших сечений деталей различной формы – круглой, квадратной, фасонной; свариваются не только однородные металлы, но и разнородные, например сталь и латунь, алюминий и медь и т. д.
Преимущества и недостатки контактной сварки.
Плюсы:
1. Низкая квалификация сварщика.
2. Отсутствуют расходуемые сварочные материалы.
3. Сварка во всех пространственных положениях.
4. Высокая производительность.
5. Достаточно легко механизировать и автоматизировать.
Минусы:
1. Ограничена толщина свариваемых деталей.
2. Сложное дорогое оборудование.
3. Отсутствуют неразрушающие методы контроля для конечной сварки.
Сварка трением
Рис. 20
Рис. 20 Принципиальная схема сварки трением: а – вращение одной детали; б – вращение обеих деталей; в – сварка неподвижных деталей с вращающейся сваркой; г – сварка при возвратно-поступательном движении одной из деталей
Производится за счет тепла, выделяемого при взаимном трении поверхности свариваемых деталей. Одна из деталей вращается вокруг своей оси со скоростью 700 – 1500 об/мин, или совершается возвратно-поступательное движение.
Благодаря трению свариваемые торцы обеих деталей нагреваются в тесение 4 – 5 сек. И подвергаются пластической деформации. После остановки – сжатие à сварка. Нагретый металл деформируется с образование "?" на токарных сверлильных, фрезерных станках: соединение встык режущих элементов (хвостовыми к резцам, сверлам, фрезам) свариваются тела вращения типа стержней, труб.
Плюсы: не нужен подвод электроэнергии; большая производительность.
Диффузионная сварка
Рис. 18
Рис. 18 Схема диффузионной сварки в вакууме: 1 – камера; 2 - гидравлический цилиндр; 3 – поршень со штоком; 4 – опора; 5 – нагреватель; 6 – свариваемые заготовки
Для трудносвариваемых металлов. Способ сварки давлением в вакууме. Основан на процессе взаимной диффузии металла в твердом состоянии.
|
Детали перед сваркой зачищают, обезжиривают и помеают в вакуум. Молекулы сидящие на поверхности, отсутствуют. Материал нагревается до t º = 0,4 – 0,6 Тпл. Процесс сваривания медленный (5 – 20 мин), но универсальный: разнородные металлы (титан-сталь, сталь-свинец, металл-керамика и др.) с существенно различающимися свойствами, иногда – иногда применяются прокладки, у которых нет растворимости друг в друге в твердом состоянии.
Применение: химическое машиностроение, полупроводниковая техника, космическая техника, резцы с твердыми пластинками.
Недостаток: длительность процесса.
Ультразвуковая сварка
Рис. 17 Схема ультразвуковой установки для сварки металлов: 1 - магнитострикционный вибратор; 2 – катушка; 3 – полиовод; 4 – наконечник полиовода; 5 – опорный электрод; 6 – свариваемое изделие
λ – длина волны звуковых колебаний; ξ – амплитуда колебаний наконечника; Р – усилие сжатия
Получение неразъемного соединение происходит за счет совместного воздействия на свариваемые детали ультразвуковых колебаний с частотой от 15 до 70 кГц и небольших сдавливающих усилий. Амплитуда колебаний 10 – 20 мкм. В месте контакта создаются сдвиговые деформации, обеспечивающие разрушение тонких пленок на соединяемых поверхностях и местный нагрев. При достижении определенной температуры и под воздействием сжимающих усилий материал пластически деформируется. При сближении поверхностей на расстояние действия межатомных сил между ними возникает прочная связь и образуется сварное соединение.
Ультразвуком хорошо сваривается медь, алюминий и многие другие пластичные материалы.
Плюсы: возможность соединять тонкие листы и фольгу с детали большой толщины. Продольные механические колебания очищают поверхность металла, благодаря чему нет необходимости в зачистке свариваемых поверхностей – обычно достаточно только обезжиривания.
Время сварки 0,5 – 3 с.
Соединение нахлестное: точечное и роликовое. Электроды из инструментальной стали (твердые).
Область применения:
- сварка пластмасс
- точное машиностроение
- электронная техника и т. д.
Способы сварки плавлением.
Наибольшее распространение получила дуговая сварка. В 1802 г профессор В. В. Петров открыл явление электрической дуги – один из видов электрического разряда в газовой среде. Петров рекомендовал применять электрическую дугу как источник тепла для мгновенного расплавления металла. Однако прошло свыше 80 лет, прежде чем явление электрической дуги было практически использовано. Наши соотечественники Бенардос и Славянов первыми в мире применили "дугу Петрова" для сварки металлов.
Сварка неплавящимся электродом С.Н.Э | Сварка плавящим электродом |
Аргонно-дуговая сварка | В зависимости от уровня механизации Ручная дуговая |
полуавтоматическая | |
автоматическая |
Дуговой электросваркой называется метод сварки, при котором местный нагрев и расплавление свариваемых частей осуществляющийся электрической дугой. Сварная дуга, представляющая собой мощный электрический разряд в газах, характеризуется ярким свечением и высокой температурой (около 6000 º С при атмосферном давлении). Зажигание дуги обычно производится мгновенным соприкосновением находящихся под электрическим напряжением электрода и основного металла и последующим их отводом на 2 – 4 мм.
В зависимости от способа воздействия дуги на основной металл различают сварку дугой прямого действия и дугой косвенного действия.
Рис. 3
Рис. 3 Схема электрической сварочной дуги прямого действия
Свариваемое изделие и электрод включены в электрическую цепь, и между ними зажимается дуга.
При сварке дугой косвенного действия свариваемое изделие не включается в электрическую цепь. В этом случае дуга горит между двумя электродами, расположенными под углом друг к другу.
По роду материал электрода:
1) С. Н. Э. – угольный или вольфрамовый (для поддержки горения дуги)
2) С. П. Э. – материал электрода служит еще дополнительным металлом для образования сварного соединения.
Сварка электрической дугой может выполнятся на постоянном или переменном токах. Сварка дугой постоянного тока осуществляется на прямой или обратной полярности. Прямая полярность – (Электрод "–"; деталь "+"), обратная полярность – (Электрод "+"; деталь "–"). При сварке на постоянном токе на положительном полюсе выделяется 43 % всего тепла, отрицательном – 36 % тепла. Поэтому при сварке большинства легированных сталей, чугуна, меди, алюминия, а также тонких деталей применяют обратную полярность. При сварке массивных деталей применяют прямую полярность, это обеспечивает хороший прогрев свариваемой детали. Температура в центре электрической дуги достигает 6000 º С. Средняя температура дуги зависит от свойств свариваемых металлов и составляет 3700 – 3800 º С.
Важным фактором, влияющим на качество сварки, является устойчивость, т. е. равномерность действия электрической дуги. Постоянный ток дает более устойчивую дугу, чем переменный ток. Это обеспечивается тем, что при переходе синусоиды напряжения через нулевое значение дуга гаснет.
В то же время экономически значительно выгоднее применение переменного тока, чем постоянного. Повышение устойчивости дуги достигается применение переменного тока повышенной частоты – 150 – 450 Гц, использованием ионизирующих покрытий электродов или наложением токов высокой частоты (ТВЧ) на основной ток дуги, при котором устойчивость дуги получается за счет непрерывной ионизации дугового столба ТВЧ. В этом случае на электрод подается, кроме тока от основного источника питания, одновременно и ток повышенной частоты от прибора осциллятора, достигающие до 106 Гц, и напряжения 2500 – 3000 В при небольшой мощности 0,2 – 0,3 кВт. Устойчивость дуги зависит также от расстояния между электродом и свариваемой детали в месте горения дуги, т. е. от так называемой длины дуги. Короткая дуга (до 5 мм) горит более устойчиво, чем длинная дуга (свыше 5 мм). Устойчивое горение дуги достигается при длине не более 0,6 – 0,8 диаметра электрода.
Зависимость напряжения дуги от тока и ее длины, отнесенная и к стационарным условиям, называется статической характеристикой дуги.
На рисунке изображены характеристики дуг, горячих в воздухе между стальными электродами. Для зажигания дуги при сварке в атмосфере воздуха при стальных электродах достаточно напряжения U = 45 – 50 В, а при угольных 55 – 65 В. После зажигания дуги напряжение резко падает и устанавливается практически постоянным.
Для питания сварочной дуги применяют специальные источники тока. Если при обычном питании током осветительных ламп, электродвигателей и др, следует иметь постоянное напряжение в питающей сети в виде почти прямой линии, параллельной оси абсцисс, то при питании сварной дуги необходим источник питания тока со специальной вольтамперной характеристикой.
Источник тока должен иметь падающую характеристику.
Для ограничения величины тока короткого замыкания и обеспечения постоянства режима сварки при колебаниях длины дуги необходимо, чтобы характеристика источника тока имела крутое падение в рабочей точке.
Напряжение холостого хода и источника тока должно быть в 2,5 – 3 раза больше напряжения дуги и составлять при ручной дуговой сварке 45 – 65 в, а переменного 55 – 100 в.
Источниками постоянного тока для служат сварочные генераторы постоянного тока, которые делятся на однопостовые (для питания одной сварочной дуги) и многопостовые (для питания нескольких дуг).
Питание сварочных постов переменным током производится от сварочных трансформаторов, понижающих напряжение, существующих в заводской сети (220, 380) до 60 – 65 В.
Электроды.
Угольные электроды выпускают в виде стержней диаметром 5 – 30 мм и длиной 200 – 300 мм. Плавящие электроды (металлические) – прутки из сварочной проволоки диаметром от 1 до 12 мм.
ГОСТом предусмотрены:
1. Углеродистая проволока марок Св 08, св08А, св08Г, и т. д. предназначенная для сварки углеродистой стали.
2. Легированная проволока – св08ГС, св18ХГСА, св12МХ и т.д. для сварки легированных сталей.
3. Высоколегированная проволока различных марок для сварки хромистых, хромолитиевых и др. высоколегированных сталей.
Электроды различают голые, тонко и толсто покрытые электроды. Цель покрытия:
1) защита металла шва от воздуха
2) устойчивость горения дуги
3) легирование шва
а) тонкое покрытие (ионизирующее) – 0,1 – 0,3 мм на сторону – для устойчивого горения дуги, но не защищает расплавленный металл от кислорода и азота воздуха (хрупкие соединения). Не применяется для ответственных сварочных работ. Наиболее распространенная обмазка состоит из 70 – 75 % мела и 25 – 30 % жидкого стекла.
б) толстые покрытия (0,5 – 3 мм) повышают устойчивость, защищают расплавленную ванну (газо-шлакообразующие – мука, шпат, мрамор и т. д.), раскисления расплавленного металла (ферромарганец, феррокремний, ферротитан и др.) и легирование наплавляемого металла. Получается качественный шов с определенными физико-механическими свойствами.
По назначению 4 типа:
1) Для сварки углеродистых и легированных конструкционных сталей. Типы Э34, Э50, Э80, Э42.
42 – σв = 42 кгс/мм2 – минимальное гарантируемое временное сопротивление разрыву металлического шва.
Для отв. конструкций нужна повышенная пластичность – в конце буква А (Э42А).
2) Для сварки теплоустойчивых сталей – типы ЭХМ, ЭМ, ЭХМФБ.
3) Для сварки высоколегированных сталей с особыми свойствами. Классифицируются по структуре и составу металла сварного шва. Электроды для сварки сталей аустенитного класса обозначают индексом ЭА.
ЭА – ЗМ6, ЭА – 2Б, ЭА – 1, ЭА – 2, ЭФ –Х13 и т. д.
Электроды ферритного класса обозначают ЭФ – Х11, ЭФ – Х30 – цифра – процент содержания меди.
4) Электроды для наплавочных работ для наплавки режущего инструмента, штампов и др. (тип ЭН – 80В, ЭНР - 62).
При делении этих электродов на типы за основу принимали химический состав качественного металла м его твердость. Например тип ЭН – 65Х11 НЗ – 33 означает наплавочный электрод, дающий металлические наплавки со средним содержанием 0,65 % углерода, 11 % хрома, 3 % никеля с твердостью 33 HRC.
Конструктор указывает тип электрода. Каждому типу может соответствовать несколько марок. Марка характеризуется составом покрытия, его технологическими свойствами (род и полярность тока, возможность сварки в различных положениях) и со свойствами металлического шва.
В зависимости от компонентов, входящих в покрытие электроды делятся по типу покрытия.
А – кислые
Б – основные
Р – рутиловые
Ц – целлюлозные
Рис. 13
Рис 13 Схема основных движений электрода
1 – подает электроду по мере его плавления вниз для поддержания постоянной дуги, 2 – перемещает его под углом 15 – 20 º к вертикали вдоль оси шва в сторону движения для заполнения разделки кромок. И 3 – дает электроду колебательные движения поперек шва для поучения уширенного валика.
В настоящее время разработаны скоростные методы ручной дуговой сварки.
- Сварка с глубоким проплавлением: Электрод опирается обмазкой на край изделия и перемещается вдоль шва без поперечных колебательных движений. Скорость и производительность сварки возрастает в 1,5 – 2 раза за счет увеличения доли основного металла в наплавленном металле шва, увеличение сварочного тока, более полного использования электродного металла.
- Сварка пучком электродов: два или несколько электродов связывают вместе в пучок, вставляемый в обычный электрододержатель. Дуга возбуждается у электрода, торец которого ближе к изделию, а затем по мере оплавления дуга автоматически переходит от одного электрода к другому. Сварка пучком электродов повышает производительность труда, уменьшает время на замену электродов и позволяет значительно повысить величину сварочного тока.
- При сварке трехфазной дугой две фазы источника переменного тока подключаются к двум качественным электродам, а третья – к свариваемому изделию (источники – специальные трехфазные трансформаторы). В процессе сварки возбуждаются 3 дуги: две – между каждым электродом и изделием и третья – между электродами. При этом выделяется большое количество тепла, что увеличивает производительность сварки в 2 – 3 раза, экономится электроэнергия, увеличивается устойчивость горения дуги.
Преимущества ручной сварки:
1) возможна в любых пространственных положениях (потолочном, горизонтальном, вертикальном) и в труднодоступных местах. Например корпуса судов – ручной дуговой.
2) хорошее качество швов.
Недостатки:
1)низкая производительность
2) сильное разбрызгивание металла
3) угар электрода.
Ручную сварку заменяют полуавтоматической.
Полуавтоматическая сварка
Сварка в струе углекислого газа осуществляется полуавтоматической установкой. Схема в лабораторной работе.
Сварщик выполняет только одно движение – перемещает горелку по траектории сварного шва. Электродная проволока и углекислый газ подаются в зону дуги через специальную газоэлектрическую горелку. Углекислый газ защищает место сварки от окружающего воздуха. Сварка выполняется постоянным током прямой полярности.
Для компенсации окислительного действия углекислого газа повышают содержание растительных примесей в электродной проволоке.
Плюсы:
1) возрастает в 1,5 – 2 раза производительность;
2) Допускает сварку металла малой толщины во всех пространственных положениях.
Автоматическая сварка
а) Под слоем флюса.
Рис 5
Рис 5 Схема автоматической дуговой сварки под флюсом
Электрическая дуга горит между концом голой электродной проволоки 3 и кромками свариваемого металла 2 под слоем гранулированного флюса. Подача проволоки из кассеты 6 в зону дуги осуществляется сварочной головкой 5. Флюс засыпается в разделку кромок1 впереди дуги из бункера 4. Сварной шов образуется либо в процессе перемещения сварочной головки относительно неподвижного изделия, либо при перемещении изделия относительно неподвижной сварочной головки со скоростью сварки.
В процессе сварки часть флюса расплавляется и при остывании образует легко удаляемую шлаковую корку. Нерасплавленный флюс поступает обратно в бункер через сопло и шланг 7.
Применение флюсов обеспечивает изоляцию сварочной ванны от кислорода и азота воздуха, исключает потери металла на угар и разбрызгивание.
Плюсы:
1) Производительность увеличивается в 5 – 20 раз.
2) Качество шва высокое.
3)Экономится электроэнергия и улучшаются условия труда сварщика (квалификация ниже).
Сваркой под флюсом получают неразъемные соединения деталей толщиной до 30 – 40 мм из углеродистых и легированных сталей, а также цветных сплавов (медь и сплавы, никель и сплавы) титан – нельзя из-за недостаточной защиты.
б) Электрошлаковая сварка.
Рис 6
Рис 6 Схема электрошлаковой сварки: вертикальная стрелка указывает направление сварки, а горизонтальные – направление перемещения электродов в зазоре
Свариваемые детали 1 располагают вертикально с зазором 20 – 40 мм. В зону сварки автоматически подается один или несколько электродов 4 и засыпается флюс. Процесс сварки начинается с возбуждения и поддержания дуги под флюсом между электродом и начальной планкой, перекрывающей нижние кромки свариваемых листов. Для предупреждения растекания жидкого металла и флюсов и для принудительного формирования шва применяются медные ползуны 2, охлаждаемые водой.
После расплавления флюса и образования шлаковой ванны 3 дуга гаснет, и ток от электрода к изделию идет только через жидкий шлак. Сварочный процесс из дугового переходит в электрошлаковый.
Выделяющееся при прохождении тока через расплавленный шлак тепло обеспечивает дальнейшее расплавление основного и электродного металлов. Перемешиваясь, они образуют общую сварочную ванну 5. Сварочная головка перемещается по изделию снизу вверх вместе с ползунами, формирующими сварной шов. Сварка заканчивается на конечной планке, куда выводится конечная ванна со скопившимися в ней газовыми пузырями и шлаковыми включениями. После окончания сварки планки отрезают.
Электрошлаковая сварка позволяет сваривать за один проход металл практически неограниченной толщины, обеспечивает высокую производительность, хорошее качество сварных соединений, не требует разделки кромок, по сравнению с автоматической сваркой под флюсом расходует меньше электроэнергии и флюсов.
Минус: крупнозернистый металл шва (σв меньше, δ меньше). Это можно устранить последующей т/о.
За счет принудительного формирования шва можно получить большой объем сварочной ванны. Это позволяет выполнить вертикальные швы, а также сваривать стыковые соединения металла большой толщины.
Применяется при изготовлении крупногабаритных конструкций. Освоении электрошлаковой сварки позволило заменить громоздкие и тяжелые цельнолитые и цельнокованые станины и корпуса более легкими и компактными сварно-литыми и сварно-коваными деталями.
в) Дуговая сварка в среде защищенных газов изоляции расплавленного металла от вредного воздействия кислорода и азота воздуха обеспечивается также путем создания газовой атмосферы вокруг дуги и зоны сварки.
Применяются инженерные газы (аргон и гелий) и активные (азот, углекислый газ) защитные газы.
Аргонно-дуговая сварка
-неплавящимся W электродом
- плавящим металлическим электродом.
Рис 8 а Сварка неплавящимся электродом
Рис 8 дуговая сварка в среде защитных газов
Электрическая дуга 5 горит между вольфрамовым электродом 4 и свариваемым металлом 1. Защитный газ 2 подается через кольцевой мундштук (держатель электрода) 3 и обволакивает всю зону дуги и сварочную ванну. Это обеспечивает получение наплавленного металла с высокими механическими свойствами. Сварку неплавящимся электродом ведут на постоянном токе прямой и обратной полярности и на переменном токе. Применяют присадочный материал.
Варить можно все, но метод малопроизводителен и дорогой из-за газ. Поэтому применяется для сварки титана, алюминия, легированных сталей небольшой толщины.
Рис 8 б. Сварка плавящим электродом 6.
Производится на постоянном токе обратной полярности. Целесообразна для соединения металлов толщиной не менее 3 мм.
г) При автоматической дуговой сварке углеродистых и низколегированных сталей плавящимся электродом в качестве защитного газа применяют углекислый газ, который в 10-15 раз дешевле аргона. Для предотвращения окислительного влияния его на сварочную ванну применяют электродную проволоку с повышенным содержанием раскислителей – кремния и марганца. Сварку ведут на постоянном токе обратной полярности. Принцип аналогичен аргоно-дуговой.
Газовая сварка
Это сварка плавлением. Нагрев идет за счет сгорания горючих веществ в струе кислорода. В качестве горючего используют ацетилен, углерод, природный газ, пары бензина, керосина и т. д.
Наибольшее применение получил ацетилен, который по сравнению с другим горючим дает более высокую температуру и наибольшее количество тепла в рабочей зоне сварочного пламени (в 10 – 15 раз дороже остальных горючих). Сгорая в кислороде дает самую высокую температуру пламени 3200 º С.
Технический ацетилен получают в генераторах, воздействую на карбид кальция водой
CaC2 + 2H2O = Ca(OH)2 + C2H2
Ацетилен – взрывоопасный газ
C2H2 может храниться и использоваться и в специальных стальных баллонах, окрашенных в белый цвет с надписью "ацетилен" красной краской. Баллон, с целью предохранения от взрыва, наполнен активированным углем, пропитанным ацетоном.
Кислород хранят и транспортируют в стальных баллонах голубого цвета с надписью "кислород" черными буквами. На баллоне имеется редуктор для понижения давления и для поддержания постоянного расхода газа.
Основной инструмент сварщика является газовая горелка, где происходит образование ацетиленокислородной смеси и ее сжигание с целью получения высокотемпературного концентрированного сварочного пламени. Сварочные горелки делятся на инжекторные (низкого давления) и безинжекторные (высокого или равного давления). Наиболее применяются – инжекторные.
Рис 12
Рис 12 принципиальная схема инжекторной горелки
В такую горелку кислород подается под давлением равным 0,3 – 0,4 Мн/м2. Вытекая с большой скоростью из сопла инжектора 4, струя создает разряжение, обеспечивающее подсос ацетилена в смесительную камеру 3. Из смесительной камеры C2H2 – О2 смесь подается через трубку 2 и мундштук 1 выталкивается в атмосферу, где, воспламеняясь, образует сварочное пламя.
Достоинства: простота оборудования и универсальность, позволяющая сваривать различные металлы разных толщин, что делает газовую сварку почти незаменимой в ремонтном деле.
При газовой сварке происходит более плавный нагрев свариваемого металла, чем при электродуговой. Это особенно важно при соединении сталей небольших толщин, сварке легкоплавких металлов, а также сварки чугуна с предварительным подогревом.
Газовую сварку в стационарных условиях не применяют (дорого и малопроизводительно). Применение – ремонто-монтаж, аварийные работы.
Пламя в зависимости от соотношения ацетилена и кислорода различают нормальное (восстановительное), окислительное и науглераживающее (ацетиленовое).
Состоит из трех зон:
1) ядро (5-20 мм) С2Н2 и О2 – ослепительно белый цвет
2) восстановительная зона СО + Н2 – синеватый цвет
3) окислительная зона СО2 + Н2О – максимальная температура, желто-красный цвет.
Нормальное пламя - = 1 – 1,2
Это вид не вызывает не окисления расплавленного металла, ни насыщение его углеродом.
Нормальным пламенем свариваемым большинство металлов. Окислительное пламя >1, 2 (избыток кислорода). Имеет голубоватый оттенок, горит с шумом. Отличается однородным ядром м факелом. Температура выше, чем у нормального. Используется для сварки низкоуглеродистой стали с присадочной проволокой, содержащей большое количество раскислителей (Марганец, кремний), латуни (для образования окисной пленки, предохраняющей цинк от испарения).
Науглераживающее пламя < 1 т. е. избыток ацетилена. Пламя имеет желтый цвет и коптит. Применяется при сварке высокоуглеродистых сталей и чугуна, что способствует пополнению углерода, выгорающего при сварке.
Техника газовой сварки.
Основной вид сварочного соединения – встык. Качество сварочного шва обеспечивается перевыбором сварочного режима и способа перемещения сварочной горелки и присадочного материала по шву.
Угол наклона мундштука горелки к поверхности свариваемой детали (Рис 10 а) выбирается в зависимости от толщины металла и его теплопроводности. Чем выше толщина свариваемого металла и его теплопроводность, тем больше должен быть угол наклона. Присадочный материал вводят под углом 30 – 40 º к поверхности детали.
Различают два спосо
|
|
Семя – орган полового размножения и расселения растений: наружи у семян имеется плотный покров – кожура...
Автоматическое растормаживание колес: Тормозные устройства колес предназначены для уменьшения длины пробега и улучшения маневрирования ВС при...
Двойное оплодотворение у цветковых растений: Оплодотворение - это процесс слияния мужской и женской половых клеток с образованием зиготы...
Наброски и зарисовки растений, плодов, цветов: Освоить конструктивное построение структуры дерева через зарисовки отдельных деревьев, группы деревьев...
© cyberpedia.su 2017-2024 - Не является автором материалов. Исключительное право сохранено за автором текста.
Если вы не хотите, чтобы данный материал был у нас на сайте, перейдите по ссылке: Нарушение авторских прав. Мы поможем в написании вашей работы!