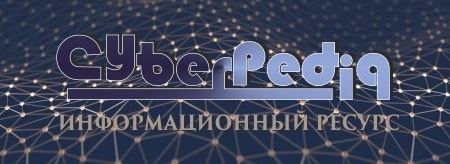
Организация стока поверхностных вод: Наибольшее количество влаги на земном шаре испаряется с поверхности морей и океанов (88‰)...
Историки об Елизавете Петровне: Елизавета попала между двумя встречными культурными течениями, воспитывалась среди новых европейских веяний и преданий...
Топ:
Марксистская теория происхождения государства: По мнению Маркса и Энгельса, в основе развития общества, происходящих в нем изменений лежит...
Установка замедленного коксования: Чем выше температура и ниже давление, тем место разрыва углеродной цепи всё больше смещается к её концу и значительно возрастает...
Когда производится ограждение поезда, остановившегося на перегоне: Во всех случаях немедленно должно быть ограждено место препятствия для движения поездов на смежном пути двухпутного...
Интересное:
Отражение на счетах бухгалтерского учета процесса приобретения: Процесс заготовления представляет систему экономических событий, включающих приобретение организацией у поставщиков сырья...
Национальное богатство страны и его составляющие: для оценки элементов национального богатства используются...
Принципы управления денежными потоками: одним из методов контроля за состоянием денежной наличности является...
Дисциплины:
![]() |
![]() |
5.00
из
|
Заказать работу |
|
|
Горячекатанный штрипс из малоуглеродистой стали непрерывное движение через печь, в которой при помощи газовых горелок его кромки нагревают t = 1450 º - t º сварки. При выходе из печи кромки штрипса обдуваются струей воздуха из сопла, чем обеспечивается удаление окалины с кромок штрипса и повышение температуры их нагрева на 50 – 60 º. Первая пара валков сворачивает штрипс в трубную заготовку без соединения кромок. Вторая приводная пара валков сводит кромки трубкой заготовки и, сжимая их, заставляет свариваться в трубу.
Сварка кромок сформированной трубкой заготовки представляет процесс кузнечной сварки, заключающийся в использовании способности к молекулярному сцеплению сдавливаемых поверхностей металлов, нагретых до высокой температуры.
5. Контактная сварка.
Классический способ сварки нагревом и давлением.
При контактной сварке место соединения металла нагревается прохождением электрического тока, который подается кратковременными импульсами (десятые доли секунд) большой силы (до 100000 А), напряжение 0,3 – 12 В. Одновременно или несколько позже проводится сжатие (осадка) стыка. Увеличение времени приводит к ухудшению качества сварного соединения. Обычно контактную сварку проводят в жестком режиме, получая интенсивный нагрев (с помощью больших сварочных токов) в наикратчайший промежуток времени.
Количество выделяющегося тепла определяется по закону Джоуля – Ленца:
![]() | (1) |
Где - величина сварочного тока
– величина электрического сопротивления зоны контакта, Ом.
t – время прохождения тока, сек.
Величина R зоны контакта обычно не превышает 0,1 Ом.
Источником тока при контактной сварке служат сварочные трансформаторы, их первичная обмотка включается в промышленную сеть, а вторичная присоединена к электродам, проводящим к свариваемым деталям ток большой силы при малом напряжении.
|
(U до 12 В является безопасным)
Установка для электроконтактной сварки включает в себя электрическую часть, состоящую из сварочного трансформатора, прерыватели (контактора) и механической части, обеспечивающей создание необходимого давления при сварке. К – контактор а) регулирует время прохождения сварочного тока б) плавное регулирование сварочного тока.
ПС – нужен для грубой настройки на сварочный режим.
Точечная сварка
Предназначена для соединения листовых заготовок.
Рис. 9(а)
Свариваемые детали 5 и 6 собирают внахлестку и располагают на неподвижном электроде 4. После опускания верхнего электрода 3 и сжатия деталей через них от вторичной обмотки трансформатора 1 пропускают ток. Металл в точке 2 интенсивно нагревается. Между электродами – до плавления (образуется ядро), а прилегающая к нему зона нагревается до пластического состояния. После кристаллизации ядра давление снимается.
Электроды – подвод тока – сжатие
Изготавливают из медных сплавов (сталь – большое сопротивление) – БрХ07. Суммарное сопротивление в цепи – сумма сопротивлений токоведущих частей.
![]() | (2) |
Где - сопротивление электрод – деталь
- собственное сопротивление детали
- контактное сопротивление детали
Сварка возможна тогда, когда >>
, чтобы все тепло выделилось в точке. Годной считается сварка, если металл вырывается с "мясом". Толщина 5мм + 5мм. Привод сжатия Р – пневматическая, гидравлическая, ручная.
Разновидностью точечной сварки является рельефная сварка, при которой одновременно сваривается несколько точек. Перед сваркой на одной из свариваемых деталей выштамповывают рельефы (выступы). При сварке выступы разогреваются и под действием давления специальных плит (электродов) расплющиваются.
Машины для точечной сварки могут быть стационарные передвижные, переносные. Наряду с одноточечными широко применяются многоточечные, у которых число электродов достигает несколько сотен, а производительность – десятков тысяч точек в час. Применяются в кораблестроении, автомобилестроении, корпус холодильника, стиральные машины.
|
Минусы: негерметичное соединение, высокая стоимость.
График изменения сварочного тока и усилия сжатия, совмещенные во времени, называются циклограммой. Цикл сварки состоит из следующих операций: сжатия свариваемых заготовок, включения и выключения сварочного тока и снятия усилия сжатия.
а) Сварка при постоянном давлении и применяется для сварки углеродистых и нержавеющих сталей толщиной до 3 мм.
б) Отличается тем, что после выключения сварочного тока усилие сжатия увеличивают. Это обеспечивает хорошее формирование металла и позволяет получить сварную точку повышенной прочности. Применяется для изделий из низкоуглеродистых сталей повышенной толщины.
в) Состоит из обжатия листов большим усилием перед сваркой, сварки при меньшем P U последующего обжатия повышенным усилием при выключенном токе. Применяется при сварке листов больших толщин, когда необходимо обеспечить формирование и отвердевание сварной точки.
4.2 Роликовая (шовная сварка)
Рис. 9 б)
Осуществляется на контактных машинах, у которых вместо стержневых электродов применяются ролики 2.
После сжатия свариваемых деталей 4 и 5 одновременно включается ток от трансформатора 1 и начинают вращаться ролики (или один ролик). Детали перемещаются между роликами или, наоборот, ролики перемещаются по детали, и металл сваривается.
Роликовую сварку можно рассматривать как разновидность точечной сварки, у которой каждая последующая точка перекрывает предыдущую, образуя сплошной прочный и сплошной шов.
Применят два способа сварки: с непрерывной подачей тока и с прерыванием тока.
Первый способ не получил распространение – могут быть непровары и пережоги. Еще существует шаговая сварка – детали перемещаются на определенный шаг, тогда включается ток.
Электроды – бронзы медь + магний, медь, бериллий, алюминий, цинк, магний или сплавы на основе вольфрама. Толщины 3+3.
Плюс: герметичность.
I = 2 – 5000 А; диаметром – 40 – 350 мм;
Усилие 6 кН; скорость сварки – 0,5 – 3,5 м/мин
|
Стыковая сварка
При стыковой сварке детали свариваются встык по всей поверхности соприкосновения. Сварка осуществляется на машинх ручного или автоматического действия. Рис. 7
Рис. 7 Схема сварочной машины для контактной стыковой сварки
Свариваемые детали 3 и 7 закрепляются в зажимах (губках) 4 и 6 сварочной машины. Зажим 4 укреплен на неподвижной относительно станины 1 плите 2, а затем 6 – на плите 5, которая может перемещаться по направляющим станины. Питание деталей электрическим током осуществляется через зажимы от вторичной обмотки сварочного трансформатора 8.
Существует два способа стыковой сварки: сопротивлением и оплавлением.
При сварке сопротивлением свариваемые детали вначале сближают до соприкосновения торцевыми поверхностями и сдавливают, а затем включают ток.
После нагрева деталей в зоне контакта до пластичного состояния производится осадка (сжатие) металла на величину припуска на сварку. В конце осадки ток выключается. Требует точной подгонки концов соединяемых деталей.
Минусы: ограничение по площади сечения свариваемых деталей F ≤ 300 мм2 , не хватает мощности машин, свариваются компактные сечения (кружки, трубы).
Сварка оплавлением возможна для изделий сечением 50000 – 60000 мм2 и более. При этом виде сварки заготовки собираются с зазором, на них подается напряжение (ток не идет). Эти детали начинают сближаться. На поверхности есть шероховатость. В месте контакта точек идет большой ток, происходит оплавление и выброс жидкого металла и так же в других точках. После образования на торцах деталей равномерного слоя расплавленного металла быстро производится осадка стыка. Начале осадки ток выключается.
Плюсы: не требуется точной подготовки торцов свариваемых деталей; улучшается качество шва, т. к. при осадке вместе с жидким металлом из стыка удаляются все загрязнения, в том числе и шлаки; сварка больших сечений деталей различной формы – круглой, квадратной, фасонной; свариваются не только однородные металлы, но и разнородные, например сталь и латунь, алюминий и медь и т. д.
Преимущества и недостатки контактной сварки.
|
Плюсы:
1. Низкая квалификация сварщика.
2. Отсутствуют расходуемые сварочные материалы.
3. Сварка во всех пространственных положениях.
4. Высокая производительность.
5. Достаточно легко механизировать и автоматизировать.
Минусы:
1. Ограничена толщина свариваемых деталей.
2. Сложное дорогое оборудование.
3. Отсутствуют неразрушающие методы контроля для конечной сварки.
Сварка трением
Рис. 20
Рис. 20 Принципиальная схема сварки трением: а – вращение одной детали; б – вращение обеих деталей; в – сварка неподвижных деталей с вращающейся сваркой; г – сварка при возвратно-поступательном движении одной из деталей
Производится за счет тепла, выделяемого при взаимном трении поверхности свариваемых деталей. Одна из деталей вращается вокруг своей оси со скоростью 700 – 1500 об/мин, или совершается возвратно-поступательное движение.
Благодаря трению свариваемые торцы обеих деталей нагреваются в тесение 4 – 5 сек. И подвергаются пластической деформации. После остановки – сжатие à сварка. Нагретый металл деформируется с образование "?" на токарных сверлильных, фрезерных станках: соединение встык режущих элементов (хвостовыми к резцам, сверлам, фрезам) свариваются тела вращения типа стержней, труб.
Плюсы: не нужен подвод электроэнергии; большая производительность.
Диффузионная сварка
Рис. 18
Рис. 18 Схема диффузионной сварки в вакууме: 1 – камера; 2 - гидравлический цилиндр; 3 – поршень со штоком; 4 – опора; 5 – нагреватель; 6 – свариваемые заготовки
Для трудносвариваемых металлов. Способ сварки давлением в вакууме. Основан на процессе взаимной диффузии металла в твердом состоянии.
Детали перед сваркой зачищают, обезжиривают и помеают в вакуум. Молекулы сидящие на поверхности, отсутствуют. Материал нагревается до t º = 0,4 – 0,6 Тпл. Процесс сваривания медленный (5 – 20 мин), но универсальный: разнородные металлы (титан-сталь, сталь-свинец, металл-керамика и др.) с существенно различающимися свойствами, иногда – иногда применяются прокладки, у которых нет растворимости друг в друге в твердом состоянии.
Применение: химическое машиностроение, полупроводниковая техника, космическая техника, резцы с твердыми пластинками.
Недостаток: длительность процесса.
Ультразвуковая сварка
Рис. 17 Схема ультразвуковой установки для сварки металлов: 1 - магнитострикционный вибратор; 2 – катушка; 3 – полиовод; 4 – наконечник полиовода; 5 – опорный электрод; 6 – свариваемое изделие
λ – длина волны звуковых колебаний; ξ – амплитуда колебаний наконечника; Р – усилие сжатия
Получение неразъемного соединение происходит за счет совместного воздействия на свариваемые детали ультразвуковых колебаний с частотой от 15 до 70 кГц и небольших сдавливающих усилий. Амплитуда колебаний 10 – 20 мкм. В месте контакта создаются сдвиговые деформации, обеспечивающие разрушение тонких пленок на соединяемых поверхностях и местный нагрев. При достижении определенной температуры и под воздействием сжимающих усилий материал пластически деформируется. При сближении поверхностей на расстояние действия межатомных сил между ними возникает прочная связь и образуется сварное соединение.
|
Ультразвуком хорошо сваривается медь, алюминий и многие другие пластичные материалы.
Плюсы: возможность соединять тонкие листы и фольгу с детали большой толщины. Продольные механические колебания очищают поверхность металла, благодаря чему нет необходимости в зачистке свариваемых поверхностей – обычно достаточно только обезжиривания.
Время сварки 0,5 – 3 с.
Соединение нахлестное: точечное и роликовое. Электроды из инструментальной стали (твердые).
Область применения:
- сварка пластмасс
- точное машиностроение
- электронная техника и т. д.
Способы сварки плавлением.
Наибольшее распространение получила дуговая сварка. В 1802 г профессор В. В. Петров открыл явление электрической дуги – один из видов электрического разряда в газовой среде. Петров рекомендовал применять электрическую дугу как источник тепла для мгновенного расплавления металла. Однако прошло свыше 80 лет, прежде чем явление электрической дуги было практически использовано. Наши соотечественники Бенардос и Славянов первыми в мире применили "дугу Петрова" для сварки металлов.
Сварка неплавящимся электродом С.Н.Э | Сварка плавящим электродом |
Аргонно-дуговая сварка | В зависимости от уровня механизации Ручная дуговая |
полуавтоматическая | |
автоматическая |
Дуговой электросваркой называется метод сварки, при котором местный нагрев и расплавление свариваемых частей осуществляющийся электрической дугой. Сварная дуга, представляющая собой мощный электрический разряд в газах, характеризуется ярким свечением и высокой температурой (около 6000 º С при атмосферном давлении). Зажигание дуги обычно производится мгновенным соприкосновением находящихся под электрическим напряжением электрода и основного металла и последующим их отводом на 2 – 4 мм.
В зависимости от способа воздействия дуги на основной металл различают сварку дугой прямого действия и дугой косвенного действия.
Рис. 3
Рис. 3 Схема электрической сварочной дуги прямого действия
Свариваемое изделие и электрод включены в электрическую цепь, и между ними зажимается дуга.
При сварке дугой косвенного действия свариваемое изделие не включается в электрическую цепь. В этом случае дуга горит между двумя электродами, расположенными под углом друг к другу.
По роду материал электрода:
1) С. Н. Э. – угольный или вольфрамовый (для поддержки горения дуги)
2) С. П. Э. – материал электрода служит еще дополнительным металлом для образования сварного соединения.
Сварка электрической дугой может выполнятся на постоянном или переменном токах. Сварка дугой постоянного тока осуществляется на прямой или обратной полярности. Прямая полярность – (Электрод "–"; деталь "+"), обратная полярность – (Электрод "+"; деталь "–"). При сварке на постоянном токе на положительном полюсе выделяется 43 % всего тепла, отрицательном – 36 % тепла. Поэтому при сварке большинства легированных сталей, чугуна, меди, алюминия, а также тонких деталей применяют обратную полярность. При сварке массивных деталей применяют прямую полярность, это обеспечивает хороший прогрев свариваемой детали. Температура в центре электрической дуги достигает 6000 º С. Средняя температура дуги зависит от свойств свариваемых металлов и составляет 3700 – 3800 º С.
Важным фактором, влияющим на качество сварки, является устойчивость, т. е. равномерность действия электрической дуги. Постоянный ток дает более устойчивую дугу, чем переменный ток. Это обеспечивается тем, что при переходе синусоиды напряжения через нулевое значение дуга гаснет.
В то же время экономически значительно выгоднее применение переменного тока, чем постоянного. Повышение устойчивости дуги достигается применение переменного тока повышенной частоты – 150 – 450 Гц, использованием ионизирующих покрытий электродов или наложением токов высокой частоты (ТВЧ) на основной ток дуги, при котором устойчивость дуги получается за счет непрерывной ионизации дугового столба ТВЧ. В этом случае на электрод подается, кроме тока от основного источника питания, одновременно и ток повышенной частоты от прибора осциллятора, достигающие до 106 Гц, и напряжения 2500 – 3000 В при небольшой мощности 0,2 – 0,3 кВт. Устойчивость дуги зависит также от расстояния между электродом и свариваемой детали в месте горения дуги, т. е. от так называемой длины дуги. Короткая дуга (до 5 мм) горит более устойчиво, чем длинная дуга (свыше 5 мм). Устойчивое горение дуги достигается при длине не более 0,6 – 0,8 диаметра электрода.
Зависимость напряжения дуги от тока и ее длины, отнесенная и к стационарным условиям, называется статической характеристикой дуги.
На рисунке изображены характеристики дуг, горячих в воздухе между стальными электродами. Для зажигания дуги при сварке в атмосфере воздуха при стальных электродах достаточно напряжения U = 45 – 50 В, а при угольных 55 – 65 В. После зажигания дуги напряжение резко падает и устанавливается практически постоянным.
Для питания сварочной дуги применяют специальные источники тока. Если при обычном питании током осветительных ламп, электродвигателей и др, следует иметь постоянное напряжение в питающей сети в виде почти прямой линии, параллельной оси абсцисс, то при питании сварной дуги необходим источник питания тока со специальной вольтамперной характеристикой.
Источник тока должен иметь падающую характеристику.
Для ограничения величины тока короткого замыкания и обеспечения постоянства режима сварки при колебаниях длины дуги необходимо, чтобы характеристика источника тока имела крутое падение в рабочей точке.
Напряжение холостого хода и источника тока должно быть в 2,5 – 3 раза больше напряжения дуги и составлять при ручной дуговой сварке 45 – 65 в, а переменного 55 – 100 в.
Источниками постоянного тока для служат сварочные генераторы постоянного тока, которые делятся на однопостовые (для питания одной сварочной дуги) и многопостовые (для питания нескольких дуг).
Питание сварочных постов переменным током производится от сварочных трансформаторов, понижающих напряжение, существующих в заводской сети (220, 380) до 60 – 65 В.
Электроды.
Угольные электроды выпускают в виде стержней диаметром 5 – 30 мм и длиной 200 – 300 мм. Плавящие электроды (металлические) – прутки из сварочной проволоки диаметром от 1 до 12 мм.
ГОСТом предусмотрены:
1. Углеродистая проволока марок Св 08, св08А, св08Г, и т. д. предназначенная для сварки углеродистой стали.
2. Легированная проволока – св08ГС, св18ХГСА, св12МХ и т.д. для сварки легированных сталей.
3. Высоколегированная проволока различных марок для сварки хромистых, хромолитиевых и др. высоколегированных сталей.
Электроды различают голые, тонко и толсто покрытые электроды. Цель покрытия:
1) защита металла шва от воздуха
2) устойчивость горения дуги
3) легирование шва
а) тонкое покрытие (ионизирующее) – 0,1 – 0,3 мм на сторону – для устойчивого горения дуги, но не защищает расплавленный металл от кислорода и азота воздуха (хрупкие соединения). Не применяется для ответственных сварочных работ. Наиболее распространенная обмазка состоит из 70 – 75 % мела и 25 – 30 % жидкого стекла.
б) толстые покрытия (0,5 – 3 мм) повышают устойчивость, защищают расплавленную ванну (газо-шлакообразующие – мука, шпат, мрамор и т. д.), раскисления расплавленного металла (ферромарганец, феррокремний, ферротитан и др.) и легирование наплавляемого металла. Получается качественный шов с определенными физико-механическими свойствами.
По назначению 4 типа:
1) Для сварки углеродистых и легированных конструкционных сталей. Типы Э34, Э50, Э80, Э42.
42 – σв = 42 кгс/мм2 – минимальное гарантируемое временное сопротивление разрыву металлического шва.
Для отв. конструкций нужна повышенная пластичность – в конце буква А (Э42А).
2) Для сварки теплоустойчивых сталей – типы ЭХМ, ЭМ, ЭХМФБ.
3) Для сварки высоколегированных сталей с особыми свойствами. Классифицируются по структуре и составу металла сварного шва. Электроды для сварки сталей аустенитного класса обозначают индексом ЭА.
ЭА – ЗМ6, ЭА – 2Б, ЭА – 1, ЭА – 2, ЭФ –Х13 и т. д.
Электроды ферритного класса обозначают ЭФ – Х11, ЭФ – Х30 – цифра – процент содержания меди.
4) Электроды для наплавочных работ для наплавки режущего инструмента, штампов и др. (тип ЭН – 80В, ЭНР - 62).
При делении этих электродов на типы за основу принимали химический состав качественного металла м его твердость. Например тип ЭН – 65Х11 НЗ – 33 означает наплавочный электрод, дающий металлические наплавки со средним содержанием 0,65 % углерода, 11 % хрома, 3 % никеля с твердостью 33 HRC.
Конструктор указывает тип электрода. Каждому типу может соответствовать несколько марок. Марка характеризуется составом покрытия, его технологическими свойствами (род и полярность тока, возможность сварки в различных положениях) и со свойствами металлического шва.
В зависимости от компонентов, входящих в покрытие электроды делятся по типу покрытия.
А – кислые
Б – основные
Р – рутиловые
Ц – целлюлозные
|
|
Биохимия спиртового брожения: Основу технологии получения пива составляет спиртовое брожение, - при котором сахар превращается...
Особенности сооружения опор в сложных условиях: Сооружение ВЛ в районах с суровыми климатическими и тяжелыми геологическими условиями...
Семя – орган полового размножения и расселения растений: наружи у семян имеется плотный покров – кожура...
Состав сооружений: решетки и песколовки: Решетки – это первое устройство в схеме очистных сооружений. Они представляют...
© cyberpedia.su 2017-2024 - Не является автором материалов. Исключительное право сохранено за автором текста.
Если вы не хотите, чтобы данный материал был у нас на сайте, перейдите по ссылке: Нарушение авторских прав. Мы поможем в написании вашей работы!