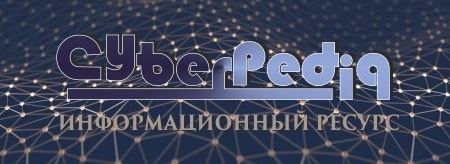
Организация стока поверхностных вод: Наибольшее количество влаги на земном шаре испаряется с поверхности морей и океанов (88‰)...
История развития пистолетов-пулеметов: Предпосылкой для возникновения пистолетов-пулеметов послужила давняя тенденция тяготения винтовок...
Топ:
Характеристика АТП и сварочно-жестяницкого участка: Транспорт в настоящее время является одной из важнейших отраслей народного...
Определение места расположения распределительного центра: Фирма реализует продукцию на рынках сбыта и имеет постоянных поставщиков в разных регионах. Увеличение объема продаж...
Основы обеспечения единства измерений: Обеспечение единства измерений - деятельность метрологических служб, направленная на достижение...
Интересное:
Распространение рака на другие отдаленные от желудка органы: Характерных симптомов рака желудка не существует. Выраженные симптомы появляются, когда опухоль...
Отражение на счетах бухгалтерского учета процесса приобретения: Процесс заготовления представляет систему экономических событий, включающих приобретение организацией у поставщиков сырья...
Подходы к решению темы фильма: Существует три основных типа исторического фильма, имеющих между собой много общего...
Дисциплины:
![]() |
![]() |
5.00
из
|
Заказать работу |
|
|
Монтаж электрооборудования. Размещение электроаппаратуры. Все органы электрического управления (кнопки, переключатели, лампочки) как станком, так и АЛ обычно сосредоточивают в пультах управления. Используют также кнопочные станции, включающие в себя две-три наладочные кнопки. Пульт управления станка представляет собой металлическую или пластмассовую коробку с крышкой, на которой монтируют органы управления. Коробка пульта рассчитана на встраивание в нее определенного числа элементов управления. Пульты обычно крепят (болтами) как к станине станка, так и к специальным стойкам. Лицевую сторону металлической крышки хромируют или покрывают специальными лаками и эмалями. Надписи гравируют или выполняют в виде табличек с помощью глубокого фотохимического гравирования. Пульт управления, применяемый в АЛ из АС, включает в себя тумбу и стол, на которых сосредоточены органы управления, сигнализации и устройства поиска неисправностей.
Шкафы управления. Электроаппаратуру размещают в специальном шкафу или в нише станины станка. Наиболее удобным для работы и обслуживания электроаппаратуры является её размещение в отдельном, специально предназначенном для этой цели шкафу, который устанавливают в непосредственной близости от станка (двери шкафа должны быть обращены к станку). Часто электрошкаф крепится непосредственно к станку и составляет общую с ним конструкцию.
Используются провода только с полихлорвиниловой или полиэтиленовой изоляцией, так как резиновая изоляция разрушается под действием масла и СОЖ. Провода чаще всего прокладывают в трубах и металлорукавах. Допускается прокладка в твердых пластмассовых гибких трубках, особенно по лоткам и каналам станин. Часто прокладку проводов ведут в специальных коробах, соединяющих шкафы управления отдельных станков. Верхняя прокладка проводов в коробах обеспечивает лучшую сохранность проводов и облегчает выполнение монтажных работ.
|
Для удобства и быстроты соединения отдельных станков применяют штепсельные разъёмы. Однако следует иметь ввиду, что попадание на эти разъёмы влаги и масла не допускается. Используют провода различной расцветки: чёрные (для силовых цепей), красные (для цепей управления переменного тока), синие (для цепей управления постоянного тока), жёлто-зелёные (для защитных цепей - заземления).
Различают два вида наладки электрооборудования:
- после изготовления станка или капитального ремонта
- в процессе эксплуатации станка.
Станки и АЛ, оснащенные специальными видами приводов, преобразователями, системами числового программного управления (ЧПУ), налаживаются техническими работниками лабораторий и наладчиками электрооборудования высокой квалификации.
Приступая к наладке, нужно иметь необходимые электроизмерительные приборы и приспособления, а также электросхему. Наладку электрооборудования вновь собранной АЛ после окончания электромонтажных работ ведут в таком порядке.
Проверяют качество электромонтажных работ, наличие предупредительных знаков напряжения и индексов у элементов электрооборудования, заземление станка. Проверяют исправность действия запоров электрошкафов и вводного автомата. Все крышки путевых выключателей, коробок зажимов и т. п. должны быть закрыты. Расцветка проводов должна соответствовать указанным в чертежах. Особенно важно убедиться, что защитные средства (нагревательные элементы тепловой защиты и др.) полностью соответствуют заданным по чертежу.
Мегомметром проверяют состояние изоляции проводов и обмоток двигателей электроаппаратуры. Сопротивление изоляции проводов должно быть не менее 1 мОм., а для обмоток электродвигателей 0.5 мОм. Далее проверят “заземление”, замеряя сопротивление проводов между основным заземляющим болтом и каждым устройством с напряжением выше 48 В. Это сопротивление не должно превышать 0.1 Ом.
|
Вводным автоматом включают напряжение и прежде всего проверяют отсутствие ложных “коротких” замыканий между проводами и замыканий проводов на “землю”.
Проверяют действие аварийной кнопки «Стоп».
Кратковременным нажатием наладочных кнопок проверяют направление вращения вала электродвигателя. В случае необходимости изменяют направление вращения, меняя местами два провода, присоединённые в зажимам электродвигателя. В случае, когда совершенно недопустимо обратное вращение вала, при первом пуске вал электродвигателя расцепляют с механизмом. I
Проверяют действие всех органов управления и сигнализации и исправляют ошибки монтажа и схем.
Проверяют действие основных блокировок, имитируя возможные отказы в путевом контроле. Особенно важно проконтролировать исходные положения узлов, неправильное перемещение которых может повлечь за собой поломку или аварию в АЛ.
На наладочном режиме многократно проверяют работу отдельных головок АЛ, транспорта, действие механизмов подналадки, контроля, смазки и всех других механизмов, имеющих электрическое управление.
Включают АЛ на полуавтоматический режим и проверяют последовательность работы линии. действие групповых наладочных кнопок и кнопки аварийного отвода.
Включают автоматический режим работы АЛ на несколько часов в целях отработки цикла и выявления причин задержек. После такой обкатки загружают обрабатываемые изделия и проверяют (приборами) нагрузку электродвигателей.
В процессе пуска и наладки выявляют и устраняют ошибки, допущенные при электромонтаже. В станках и АЛ индивидуального производства во время подобной обкатки выявляют и устраняют дефекты и недоработки принципиальной схемы и отбраковывают дефектные комплектующие изделия электрооборудования. Наладка цикла работы требует от наладчика хорошего знания кинематического устройства объекта наладки (станка и др.) и возможных аварийных ситуаций.
Наладчик-механик должен хорошо ознакомиться с назначением каждого органа управления на станке, кнопками, переключателями, сигнализацией. Наладчик должен знать основные блокировки, заложенные в схему управления станком, так как это поможет ему в поиске причины задержки автоматической работы, электрооборудование, основные показатели и условия нормальной работы.
|
Замеченные отклонения от нормальной работы электрооборудования устраняет только специалист-электрик. Одновременно с работой наладчика-электрика наладчик-механик выставляет упоры управления, действующие на путевые выключатели.
Проверка и испытание электрооборудования должны быть оформлены «Свидетельством о выходном контроле электрооборудования» (ГОСТ 5799—82).
Монтаж трубопроводов гидро- и пневмосистем. При монтаже трубопроводов подачи и отвода СОЖ необходимо выполнить следующие основные требования: обеспечить беспрепятственное поступление СОЖ ко всему режущему и абразивному инструменту в заданном количестве под заданным давлением; трубы и краны охлаждения не должны мешать доступу к обрабатываемой детали и инструменту; трубы (по диаметру, длине и расположению на станках) должны соответствовать чертежу; все горизонтальные участки напорного трубопровода должны иметь уклон 1:500 в сторону бака, чтобы обеспечить сток жидкости; в целях гарантированного заполнения напорной трубы ее следует устанавливать под магистральной трубой подачи СОЖ; для очистки трубопроводов в них необходимо предусматривать отверстия, закрытые пробками.
Монтаж трубопроводов гидросистемы производят после установки гидростанций с учетом соответствующих рекомендаций. Пневмопроводы монтируют в основном так же, как гидропроводы. Трубопроводы электрооборудования монтируют после установки электрошкафов.
Устройства для централизованной и местной смазки монтируют с учетом их удобного расположения для периодической заливки масла и свободного доступа к узлам станка в зоне обработки.
Устанавливают гидростанции, воздухоочистительные станции, электрошкафы, стенды и другое оборудование согласно установочному чертежу и общему виду.
Производят (согласно соответствующим монтажный чертежам) разводку коробов (предназначенных для размещения трубопроводов гидросистем, электропитания, сжатого воздуха и др.), расположенных над полом.
|
Закладывают в короба трубопроводы, электропроводы; соединяют их с оборудованием, электрошкафами и пультами управления, проверяют правильность электрических соединений путем прозванивания. Выполняют работы по заземлению оборудования; подсоединяют элёктропроводы к цеховым распределительным щитам и шинопроводам.
Верхнюю разводку трубопроводов выполняют так, чтобы обеспечить их размещение вне рабочих зон оборудования, проездов и проходов; при этом места соединений трубопроводов должны быть доступны для обслуживания.
Если разводка проходит под полом, то после установки оборудования все трубопроводы (подачи СОЖ, электроразводки, подачи сжатого воздуха, масла, воды и др.) укладывают на фундаментной плите, соединяют их согласно соответствующим схемам, опрессовывают (т. е. проверяют их работу под давлением, указанным в чертеже), заливают жидким бетоном и изготовляют чистый пол.
Наладка и эксплуатация гидроприводов. Система АС должка быть подготовлена к первоначальному пуску. Внутренние поверхности гидробаков должны быть очищены от пыли и грязи, промыты керосином и тщательно протерты. При этом обтирочный материал не должен оставлять на поверхности гидробаков волокон и очесов. Затем проверяют целостность и сохранность фильтров (заливных и воздушных) на магистрали всасывания насоса. Смятые и порванные сетки фильтров заменяют новыми. Затем заливают в гидробаки чистое, предварительно отфильтрованное минеральное масло.
Перед пробным пуском зону около станции гидропривода освобождают от посторонних предметов и проверяют затяжку болтов, гаек и пробок всех элементов гидропривода. Проверяют блокировки и положения всех механизмов, приводимых гидроприводом, во избежание их самопроизвольного перемещений при пробном пуске гидропривода.
Затем налаживают систему централизованной смазки и смазывают трущиеся поверхности всех гидрофицированных механизмов. Предупреждают обслуживающий персонал о пуске гидропривода и проверяют (в толчковом режиме) направление вращения валов электродвигателей и насосов на каждой станции гидропривода. Трубопроводы (путем кратковременного включения насосной установки) заполняют маслом. При этом направляющие распределителя и распределительные гидропанели переключают вручную (через отверстия в кожухах электромагнитов). Во избежание подсоса воздуха насосом по мере заполнения трубопровода периодически доливают масло в гидробак.
Воздух из гидросистемы выпускают не ранее чем через 4 ч после заполнения гидросистемы маслом. На время заполнения трубопроводов маслом и выпуска воздуха предохранительные клапаны насосов настраивают на минимально возможное давление, чтобы избежать растворения воздуха в масле.
|
Воздух из магистральных труб и присоединенных к ним гидроцилиндров выпускают в следующем порядке.
Открывают полностью вентили или краны, установленные в высших точках трубопровода; слегка ослабляют накидные гайки на концах магистральных труб для того, чтобы воздух, находящийся в трубках, имел возможность выйти наружу вместе с небольшим количеством масла.
Включают электродвигатель насоса и переключают электромагниты соответствующих распределителей (10—20 раз с интервалом 1—2 мин).
Закрывают вентили (или краны), заворачивают накидные гайки и настраивают предохранительные клапаны на минимально необходимое давление для перемещения поршней гидроцилиндров.
Перемещают поршни гидроцилиндров (от упора до упора) на быстром ходу путем ручного переключения электромагнитов распределителей. В случае управления насосами от разделительной панели с золотником разгрузки электромагнит разгрузки насоса низкого давления должен быть включен.
Выпускают воздух из магистральных труб до тех пор, пока из открытых вентилей и кранов не пойдет чистое масло (без пузырьков воздуха), после чего вновь закрывают вентили и краны, заворачивают гайки и доливают масло в гидробаки до отметок маслоуказателей. При пробном пуске неисправностями считают: стук и шум в насосных установках; вращение вала электродвигателя рывками; утечки масла. При появлении неисправностей гидропривод отключают и включают только после выявления и устранения неисправностей.
Выверка и наладка станков
Выверка станка
После того как фундамент изготовлен и принят, приступают к установке станины монтируемой машины.
Правильное положение машины в пространстве имеет большое значение для её нормальной работы. Точное расположение особенно важно для машин, связанных в технологическую линию различными транспортными устройствами: транспортёрами, рольгангами и направляющими. Наивысшая точность координирования машин в пространстве требуется в автоматических станочных линиях, где производственный процесс полностью автоматизирован.
Проверку положения машин в пространстве выполняют посредством контроля положения отдельных её деталей. Проверку ведут от так называемых контрольных баз. За контрольные базы обычно выбирают горизонтально, либо вертикально расположенные, точно и чисто обработанные плоские поверхности, а также наружные или внутренние цилиндрические поверхности. В технических условиях на монтаж любой машины обычно указаны величины предельных отклонений.
Наиболее часто встречающимися проверками при монтажных работах являются:
а) проверка горизонтальности;
б) проверка прямолинейности;
в) проверка параллельности и перпендикулярности;
г) проверка углов;
д) проверка соосности.
Все вышеперечисленные проверки выполняют монтажными контрольно-измерительными инструментами и приспособлениями
Проверку горизонтальности плоскостей, валов, осей, производят слесарными уровнями.
Станок устанавливают на фундамент только после затвердевания бетона. Преждевременная нагрузка на фундамент вызывает его разрушение (растрескивание).
Выверка станка происходит посредством регулирования уровня станины с помощью различных подкладок, клиньев, башмаков и домкратов.
Вследствие того что опорная часть фундамента практически не обладает достаточной точностью, станок устанавливают не непосредственно на фундамент, а на подкладки, представляющие собой металлические полосы толщиной 3... 10 мм или же стальные клинья с уклоном 4...5°, которые могут быть одинарными или двойными (рис. 4). Расположение клиньев указывается в чертеже на установку станка. Обычно клинья устанавливают по периметру станины через 500... 700 мм друг от друга. Крупные станки монтируют на башмаках (рис. 108, б), представляющих собой двойные клинья, регулируемые посредством винта. Монтаж станка начинается с установки его станины на стенде в ремонтном цехе или на фундаменте в цехе, где он будет работать.
Заливка станины производится лишь после сборки станка, окончательной выверки и сдачи ОТК. Это позволяет избежать деформации залитой станины после установки на нее тяжелых узлов.
(Для ускорения работы и повышения надежности установки при заливке следует применять быстросхватывающие цементы.) Станок устанавливают таким образом, чтобы фундамент со всех сторон выступал относительно подошвы станины примерно на одинаковое расстояние. Затем выверяют станок по уровню. Для проверки положения станины в продольном направлении уровни устанавливают в двух местах — на передней и задней направляющих станины (рис. 5).
Положение станины в поперечном направлении проверяют уровнями, также установленными в двух местах на мостиках. Подбивкой клиньев в соответствующих местах (см. рис. 108, а) добиваются горизонтальности установки станка во всех направлениях с точностью, предусмотренной техническими условиями на установку (0,04 мм на 1000 мм длины станины).
После выверки станка на клиньях под подошву станины подливают цементный раствор, имеющий состав 1:3 (цемент к песку).
Размерная наладка станков
Размерная наладка – установление требуемой точности относительно движения и положения исполнительных поверхностей инструмента, оборудования и приспособлений с целью получить требуемую точность обрабатываемых деталей.
Статическая наладка “на размер” станка, работающего регулируемым режущим инструментом (резцами, фрезами и т.д.), производится следующими типовыми методами: по пробным деталям, по эталону, шаблону или первой готовой детали.
При наладке по пробным деталям инструмент устанавливают на станке по лимбу на предварительно рассчитанный размер, затем обрабатывают партию из 3-5 деталей: обработанные детали измеряют и при необходимости корректируют положение режущего элемента на станке.
При наладке по эталону первой готовой детали или по шаблону инструмент устанавливают на неработающем станке до касания с поверхностью эталона, готовой детали или шаблона. По конструктивным формам эталон имитирует обрабатываемую деталь при её базировании в приспособлении в среднем положении. При конструировании массу эталона выбирают близкой к массе обрабатываемой детали.
4.3 Техническая документация для наладки
Техническая документация (конструкторская и технологическая), используемая при наладке и сдаче оборудования в эксплуатацию, регламентируется ГОСТами.
К конструкторской документации относятся сборочные чертежи, оборудования и его узлов, деталировочные чертежи, а также паспорт и руководство по эксплуатации. В паспорте содержатся: техническая характеристика; сборочный чертеж; кинематическая схема оборудования; увязочный чертеж узлов; документация на входящие узлы; ведомости покупных изделий, запасных частей, инструмента и приспособлений. В руководстве по эксплуатации содержатся: сведения по распаковке и транспортировании оборудования; чертеж фундамента с установочными размерами; сведения по подготовке оборудования к пуску; схема смазки; электрическая и гидравлическая схемы; сборочные чертежи узлов описанием их работы и методов регулирования; особенности ремонта узлов; характерные возможные неисправности; нормы точности оборудования.
Технологическая документация в зависимости от назначения подразделяется на основную и вспомогательную. К документации общего назначения относятся карта эскизов (представляющая собой графическое изображение технологического процесса обработки изделий) и технологическая инструкция (являющаяся описанием технологического процесса). К документам вспомогательного назначения относятся: маршрутная карта технологического процесса изготовления изделия; карта технологического процесса (с указанием переходов, режимов, обработки, данных о технологической оснастке, материальных и трудовых затратах); карта наладки (с дополнительной информацией к описаниям технологических процессов, касающейся наладки оборудования); ведомости оборудования и оснастки; ведомость расхода материалов; сведения о заготовках и др.
Основными документами, необходимым, для наладки технологического оборудования, являются следующие: чертежи заготовки и обработанной детали; карта технологического процесса и карта наладки.
|
|
Биохимия спиртового брожения: Основу технологии получения пива составляет спиртовое брожение, - при котором сахар превращается...
Механическое удерживание земляных масс: Механическое удерживание земляных масс на склоне обеспечивают контрфорсными сооружениями различных конструкций...
История создания датчика движения: Первый прибор для обнаружения движения был изобретен немецким физиком Генрихом Герцем...
Архитектура электронного правительства: Единая архитектура – это методологический подход при создании системы управления государства, который строится...
© cyberpedia.su 2017-2024 - Не является автором материалов. Исключительное право сохранено за автором текста.
Если вы не хотите, чтобы данный материал был у нас на сайте, перейдите по ссылке: Нарушение авторских прав. Мы поможем в написании вашей работы!