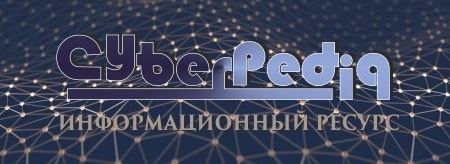
Опора деревянной одностоечной и способы укрепление угловых опор: Опоры ВЛ - конструкции, предназначенные для поддерживания проводов на необходимой высоте над землей, водой...
Индивидуальные и групповые автопоилки: для животных. Схемы и конструкции...
Топ:
Проблема типологии научных революций: Глобальные научные революции и типы научной рациональности...
Марксистская теория происхождения государства: По мнению Маркса и Энгельса, в основе развития общества, происходящих в нем изменений лежит...
Определение места расположения распределительного центра: Фирма реализует продукцию на рынках сбыта и имеет постоянных поставщиков в разных регионах. Увеличение объема продаж...
Интересное:
Лечение прогрессирующих форм рака: Одним из наиболее важных достижений экспериментальной химиотерапии опухолей, начатой в 60-х и реализованной в 70-х годах, является...
Наиболее распространенные виды рака: Раковая опухоль — это самостоятельное новообразование, которое может возникнуть и от повышенного давления...
Влияние предпринимательской среды на эффективное функционирование предприятия: Предпринимательская среда – это совокупность внешних и внутренних факторов, оказывающих влияние на функционирование фирмы...
Дисциплины:
![]() |
![]() |
5.00
из
|
Заказать работу |
|
|
Содержание
Введение
Подготовительно - расчётные работы
1.1 Основы монтажа технологического оборудования
1.2 Виды фундаментов
1.3 Разметка мест под фундаменты
1.4 Требования, предъявляемые к фундаментам
1.5 Расчёт фундаментов
Монтажные материалы и инструменты
2.1 Слесарно-сборочные инструменты, применяемы при монтаже
2.2 Монтажные контрольно-измерительные инструменты
2.3 Монтажные материалы
Монтаж
3.1 Установка оборудования на фундаменты
3.2 Подключение оборудования к сетям
Выверка и наладка станков
4.1 Выверка станка
4.2 Размерная наладка станков
4.3 Техническая документация для наладки
Обкатка и испытания смонтированного оборудования
Техника безопасности при проведении монтажных работ
6.1 Организация сборочных мест
6.2 Техника безопасности при проведении монтажных работ
Заключение
Список используемой литературы
Введение
Технологический процесс сборки должен осуществляться с наименьшими затратами при высокой производительности труда.
Рациональное построение технологического процесса сборки, степень оснащения его механизированными средствами, инструментом и приспособлениями, а также вопросы правильной организации труда являются основными в деле повышения производительности труда при сборочных работах. Особенность работ, выполняемых при сборке машин, заключается в строгой последовательности выполнения операций, что, в свою очередь, требует соответствующей организации работ отдельных сборочных бригад.
Процесс монтажа оборудования, включает в себя и сборочные операции, и подгоночно-наладочные работы. Правильная последовательность сборки всех элементов играет решающую роль.
|
Обычно даже самые крупные машины проходят контрольную сборку на заводе-изготовителе.
Технологический процесс сборки машины на месте эксплуатации должен разрабатываться в соответствии со сборочными чертежами и упаковочными ведомостями завода-изготовителя, прилагаемыми к поставляемой машине.
Подготовительно – расчётные работы по монтажу оборудования
Виды фундаментов
Для установки металлорежущего и другого технологического оборудования большей частью используются фундаменты трех видов:
1) общая бетонная плита первого этажа здания (рис. а);
2) утолщенная бетонная лента — ленточный фундамент (рис. б);
3) специально спроектированный массивный фундамент (индивидуальный иди групповой.
Фундаменты третьего вида подразделяются на обычные, т. е. опирающиеся на грунт (рис. в); свайные, т. е. опирающиеся на забитые бетонные сваи 1 (рис. г); виброизолированные — на пружинах 2 (рис. 1 д) или на резиновых ковриках 3 (рис. 1 е). Установка оборудования на обычный или свайный индивидуальный фундамент является жесткой, а на виброизоляционный фундамент — упругой.
Обычно на индивидуальные фундаменты устанавливают: тяжелое оборудование (массой более 10 т); оборудование, в котором отдельные узлы совершают резкие возвратно-поступательные перемещения (прессы, молоты и пр.); станки с нежесткими (т.е. с длинными и составными) станинами; прецизионное (особо точное) оборудование.
Требования, предъявляемые к фундаментам
При установке станков нормальной точности необходимо выполнять следующие основные требования: ограничить упругие перемещения станин под действием сил резания, массы перемещающихся узлов и осадок фундамента; ограничить уровень колебаний, вызываемых возмущениями, действующими в станке; обеспечить устойчивость при резании в заданном диапазоне обработки.
Фундамент, на который машина передает значительные статические и динамические нагрузки, должен удовлетворять следующим основным требованиям. Прежде всего фундамент должен быть прочным. При этом должны учитываться как статические, так и динамические нагрузки, воспринимаемые фундаментом. Во-вторых, фундамент должен быть устойчивым (также с учетом статических и динамических нагрузок). В-третьих, осадка фундамента должна быть равномерной и не выходить из допустимого предела. В-четвертых, сотрясения и вибрации фундамента при работе машины не должны превышать допускаемых величин. В противном случае нормальная работа машины будет нарушена. Кроме того, необходимо принять меры защиты от передачи вибраций как на соседние установки, так и на стены самого здания. И, наконец, конструкция и размеры фундамента должны удовлетворять условиям экономичности.
|
Прочность, устойчивость, равномерная осадка и допустимая величина вибраций обеспечиваются при расчете фундаментов.
Важное значение для обеспечения прочности имеет качество материалов, применяемых для устройства фундаментов, а также меры, предупреждающие разрушительное действие грунтовых вод.
К числу таких мер относятся изоляция фундаментов посредством промазки их поверхностей битумом и устройство прослойки из пластичной глины толщиной 15—20 см. Кладка из силикатного кирпича при устройстве временных фундаментов под машины изолируется от грунта независимо от наличия грунтовых вод.
Для равномерной осадки фундамента необходимо, чтобы центр тяжести машины, общий центр тяжести фундамента и центр тяжести его подошвы располагались по одной вертикали. Допустимый: эксцентриситет составляет 3—5% от размера соответствующей стороны подошвы фундамента. Для обеспечения допустимой величины осадки фундамента должно производиться исследование грунта на глубину не менее двойного размера ширины фундаментной подошвы. Когда габариты помещения и расположение оборудования не позволяют установить фундамент требуемого по расчету размера;, приходится прибегать к укреплению основания под фундамент применением песчаной постели или забивных свай.
Для того чтобы сотрясения и вибрации фундамента работающей машины не влияли на соседние прецизионные (точные) установки, принимают следующие меры защиты:
а) под подошву и с боковых сторон фундамента укладывают упругие вибропрокладки с высокой поглощательной способностью
|
б) между машиной и ее фундаментом помещают рессоры, пружины и другие упругие элементы.
Вибропрокладки должны обладать запасом прочности и упругости, полностью выдерживать статические и динамические на грузки и после снятия нагрузки — восстанавливать свои прежние размеры и форму.
Вибропрокладки делятся на три группы в зависимости от допускаемых напряжений:
а) мощные, выдерживающие давления более 3 кг/см2;
б) средние, выдерживающие давления от 1 до 3 кг/см2;
в) слабые, допускающие давления не свыше 1 кг/см2.
Следует учитывать, что глубина заложения фундамента не влияет на передачу вибраций стенам здания.
Фундаменты для станков, станина которых имеет сплошную опорную поверхность, следует проектировать в виде монолитного основания. Очертания фундамента в плане должны иметь наименьшее число углов. Глубина заложения фундамента в естественном грунте должна быть не менее глубины промерзания последнего.
Машина должна быть установлена на фундаменте без перекосов с обязательной выверкой по уровню.
Ввиду того, что верхнюю плоскость фундамента практически очень трудно выполнить совершенно плоской и горизонтальной машину устанавливают не прямо на фундамент, а на специальные подкладки.
Металлические подкладки выполняются либо в виде полос толщиной от 3 до 10 мм, либо в виде клиньев с уклоном 1: 20. Подкладки помещают между подошвой станины и фундаментом, достигая этим необходимой точности установки. С помощью стальных клиньев значительно удобнее и легче регулировать положение станка. Расстояние между соседними подкладкам или клиньями, установленными по периметру подошвы станка должно быть равно 500—600 мм. Обычно расположение клиньев по периметру подошвы станины указывается в монтажном чертеже.
При установке тяжелых станков применяют специальные башмаки, в которых клин перемещается с помощью винта. Расстояние между соседними башмаками, установленными по периметру подошвы станины, должно быть равно 1 м. Однако по всему периметру следует установить не менее трех башмаков.
Для машин, требующих особо точной установки, применяют специальные чугунные плиты, снабженные регулируемыми клиньями.
|
Установка машин с применением устройств, снабженных регулируемыми клиньями, позволяет периодически регулировать положение станины. Это особенно важно при неравномерной осадке фундамента в процессе его эксплуатации.
Установку на специальные подкладки и регулируемые клинья производят при монтаже станков, кузнечно-прессового оборудования, стационарных двигателей внутреннего сгорания, компрессоров. Выверка установки станины должна производиться в продольном и поперечном направлениях уровнем.
Что касается требований, предъявляемых к закреплению машин на фундаментах, то здесь необходимо отметить следующее. Машины, станины которых обладают достаточной жесткостью, например, легкие и средние станины общего назначения, могут быть установлены без крепления фундаментными болтами и вообще не нуждаются в отдельном фундаменте. После выверки таких станков на клиньях на бетонный пол цеха под подошву станины подливают цементный раствор, состоящий из одной части цемента и трех частей песка. Раствор должен быть подлит под всю поверхность подошвы станины. Предварительно на поверхности бетонного пола, которая будет соприкасаться с цементной подливкой, делают насечку. При. установке на фундамент высокоточных станков, станина которых не обладает достаточной жесткостью, подливку цементного раствора под подошву станины не производят, ибо приходится периодически выверять станок на точность с помощью регулируемых клиньев.
Фундаментные болты должны обладать достаточной прочностью, жестко соединять фундамент с машиной. Материалом для фундаментных и анкерных болтов служит углеродистая сталь. Диаметр фундаментных болтов определяется расчетом. Применять болты диаметром менее 14 мм не следует, так как они деформируются уже при затягивании.
Для закрепления машин, работающих без сильных сотрясений и толчков, применяют короткие фундаментные болты длиной 100—400 мм. Головки этих болтов делают разведенными или заершенными для того, чтобы они прочно держались в бетонной заливке.
Для закрепления тяжелых машин, работающих с сильными нитками и сотрясениями, например, ковочных молотов, применяют длинные анкерные болты до 3—4 м длиной. Головки анкерных болтов, имеющие прямоугольное сечение, вводят в прорезь анкерной плиты и устанавливают поперек прорези. В случаях крепления анкерными болтами удары и сотрясения машины воспринимаются всей массой фундамента.
Фундаментные и анкерные болты пропускаются сквозь отверстия в фундаментах, получаемые посредством деревянных конических пробок, закладываемых при изготовлении бетонных фундаментов. После изготовления фундамента, примерно через 2—3 часа пробки раскачивают и извлекают.
|
В теле фундамента образуются колодцы под фундаментные болты. Если деревянные пробки своевременно не удалить, то придется выжигать их раскаленным металлическим стержнем. Отверстия в фундаментах до начала установки болтов во избежание их засорений закрываются.
Заливку фундаментных болтов производят цементным раствором состава 1:3. Затягивание гаек фундаментных болтов при закреплении оборудования на фундаментах выполняют по правилам многоболтового крепления.
Установку машин на фундаменты следует начинать после полного затвердевания бетона. Преждевременное нагружение вызывает растрескивание и разрушение фундамента, причем это может проявиться в процессе его эксплуатации.
В табл. 1 приведены сроки затвердевания материала фундаментов в нормальных условиях.
Сроки готовности фундамента (табл. 1)
Материал фундаментов | Время выдержки фундамента от конца кладки до начала монтажа машины в сутках | Время от конца кладки до начала эксплуатации' машины в сутках. |
Железобетон и бетон | 2—3 | 4—7 |
Бутобетон и бутовая кладка | 4—6 | 8—12 |
Кирпичная кладка | 2—3 | 4-5 |
Расчёт фундаментов
Общие положения, которые нужно учитывать при расчете фундамента, следующие:
а) фундамент должен быть прочным и устойчивым;
б) площадь подошвы фундамента должна быть такой, чтобы удельное давление на грунт не превышало допустимого;
в) амплитуды вынужденных и частоты собственных колебаний фундамента не должны превышать определенной величины;
г) для того чтобы осадка фундамента происходила равномерно, необходимо центры тяжести машины, фундамента и его подошвы располагать по одной вертикали.
Сравнительно небольшая опорная площадь станины оборудования и значительная его масса обусловливают достаточно большую удельную нагрузку на фундамент. Площадь фундамента рассчитывается так, чтобы удельная нагрузка оборудования и самого фундамента, приходящаяся на 1 см2, не превышала допустимой нагрузки, выдерживаемой грунтом. Высота бетонного фундамента Н = К√L, где L — длина фундамента, м; K=0,3 для токарных, горизонтально-протяжных, продольно-фрезерных и продольно-строгальных ставков; К = 0,4 для шлифовальных станков; K = 0,6 для зуборезных, карусельных, консольных и бесконсольных фрезерных, горизонтально-расточных станков, вертикальных полуавтоматов; K=0,6…1 для вертикальных b радиально-сверлильных станков; K=0,8…1,4 для поперечно-строгальных и долбежных станков. Для АС, многооперационных станков и станков с ЧПУ величину Н увеличивают на 20%.
Монтажные материалы
Болты используются для крепления станка к фундаменту и принимают на себя значительные нагрузки.
Вследствие этого в машиностроении получили большое распространение различные виды специальных болтов, к числу которых относятся фундаментные, рым-болты, конусные и распорные.
На рис. 4 показаны основные виды фундаментных болтов для крепления машинных частей с фундаментом. По конструкции и назначению эти болты делятся на две группы: короткие - закладные и длинные - фундаментные болты.
Первые имеют обычно небольшую длину от 100 до 400 мм. Ими закрепляют на фундаментах машины, работающие со спокойной нагрузкой без толчков и сотрясений. В заранее приготовленные гнезда в кладке фундамента опускается один конец этих болтов. Второй конец должен быть связан с устанавливаемой машиной. После того как машина установлена и выверена на фундаменте, производится заливка нижней части болтов жидким раствором цемента.
Для закрепления на фундаментах тяжелых машин, работающих с толчками и ударами, применяются длинные фундаментные болты l =500 - 2500 мм.
Для прочности и надежности положения болтов в гнездах фундаментов их делают с заершенными концами (рис. 4,а.), завитыми в виде винта (рис. 4,6), с концами, загнутыми в виде крючка (рис. 4,в), и со вставленным поперечным стержнем. После общей подливки и затвердения фундамента производится затяжка гаек на болтах.
Анкетные болты (рис. 4, а) представляют собою обычный длинный болт, четырехгранная головка которого размещается либо в соответствующем гнезде, либо опирается на чугунную анкерную плиту. Анкерные плиты применяются главным образом для того, чтобы передать давление головки болта на большую площадь фундамента, тем самым достичь надежное и прочное крепление. Форма и размеры этих плит — самые различные. В.зависимости от размеров гнезд в фундаменте выбирается анкерная плита, которая с помощью болта и гайки стягивается с устанавливаемой машиной (без последующей заливки жидким раствором цемента).
Такое крепление машины дает надежное и прочное соединение и облегчает демонтаж оборудования.
Рым-болты имеют форму головки в виде кольца (рис. 4, а). Основное назначение этих болтов сводится к захвату и удержанию деталей и узлов во время транспортировки. Нарезанная часть стержня по соображениям надлежащей прочности делается более двух диаметров.
Фасонная головка формы кольца изготовляется за одно целое со стержнем в штампах. В зависимости от веса транспортируемых узлов меняются и размеры рым-болтов. По ГОСТ 4751-52 они изготовляются с диаметром резьбы от М8 и до М100.
Конусные (призонные) болты (рис. 4, б) делаются без головок. Конусная часть этого болта, чисто и точно обработанная, должна прилегать к внутреннему отверстию всей своей поверхностью. Такие болты обеспечивают точное и неподвижное соединение деталей при завинченной до предела гайке.
Распорные болты (рис. 4, в) применяются в случаях, когда требуется выдержать заданное расстояние между соединяемыми деталями. Болт вставляется в отверстия соединяемых деталей и пропускается через отверстие трубы (распорной втулки). Торцы распорной втулки не допускают сближения деталей. Навинчиванием и затягиванием гайки на выступающую резьбовую часть болта создается плотность соединения.
Монтаж
Выверка и наладка станков
Выверка станка
После того как фундамент изготовлен и принят, приступают к установке станины монтируемой машины.
Правильное положение машины в пространстве имеет большое значение для её нормальной работы. Точное расположение особенно важно для машин, связанных в технологическую линию различными транспортными устройствами: транспортёрами, рольгангами и направляющими. Наивысшая точность координирования машин в пространстве требуется в автоматических станочных линиях, где производственный процесс полностью автоматизирован.
Проверку положения машин в пространстве выполняют посредством контроля положения отдельных её деталей. Проверку ведут от так называемых контрольных баз. За контрольные базы обычно выбирают горизонтально, либо вертикально расположенные, точно и чисто обработанные плоские поверхности, а также наружные или внутренние цилиндрические поверхности. В технических условиях на монтаж любой машины обычно указаны величины предельных отклонений.
Наиболее часто встречающимися проверками при монтажных работах являются:
а) проверка горизонтальности;
б) проверка прямолинейности;
в) проверка параллельности и перпендикулярности;
г) проверка углов;
д) проверка соосности.
Все вышеперечисленные проверки выполняют монтажными контрольно-измерительными инструментами и приспособлениями
Проверку горизонтальности плоскостей, валов, осей, производят слесарными уровнями.
Станок устанавливают на фундамент только после затвердевания бетона. Преждевременная нагрузка на фундамент вызывает его разрушение (растрескивание).
Выверка станка происходит посредством регулирования уровня станины с помощью различных подкладок, клиньев, башмаков и домкратов.
Вследствие того что опорная часть фундамента практически не обладает достаточной точностью, станок устанавливают не непосредственно на фундамент, а на подкладки, представляющие собой металлические полосы толщиной 3... 10 мм или же стальные клинья с уклоном 4...5°, которые могут быть одинарными или двойными (рис. 4). Расположение клиньев указывается в чертеже на установку станка. Обычно клинья устанавливают по периметру станины через 500... 700 мм друг от друга. Крупные станки монтируют на башмаках (рис. 108, б), представляющих собой двойные клинья, регулируемые посредством винта. Монтаж станка начинается с установки его станины на стенде в ремонтном цехе или на фундаменте в цехе, где он будет работать.
Заливка станины производится лишь после сборки станка, окончательной выверки и сдачи ОТК. Это позволяет избежать деформации залитой станины после установки на нее тяжелых узлов.
(Для ускорения работы и повышения надежности установки при заливке следует применять быстросхватывающие цементы.) Станок устанавливают таким образом, чтобы фундамент со всех сторон выступал относительно подошвы станины примерно на одинаковое расстояние. Затем выверяют станок по уровню. Для проверки положения станины в продольном направлении уровни устанавливают в двух местах — на передней и задней направляющих станины (рис. 5).
Положение станины в поперечном направлении проверяют уровнями, также установленными в двух местах на мостиках. Подбивкой клиньев в соответствующих местах (см. рис. 108, а) добиваются горизонтальности установки станка во всех направлениях с точностью, предусмотренной техническими условиями на установку (0,04 мм на 1000 мм длины станины).
После выверки станка на клиньях под подошву станины подливают цементный раствор, имеющий состав 1:3 (цемент к песку).
Размерная наладка станков
Размерная наладка – установление требуемой точности относительно движения и положения исполнительных поверхностей инструмента, оборудования и приспособлений с целью получить требуемую точность обрабатываемых деталей.
Статическая наладка “на размер” станка, работающего регулируемым режущим инструментом (резцами, фрезами и т.д.), производится следующими типовыми методами: по пробным деталям, по эталону, шаблону или первой готовой детали.
При наладке по пробным деталям инструмент устанавливают на станке по лимбу на предварительно рассчитанный размер, затем обрабатывают партию из 3-5 деталей: обработанные детали измеряют и при необходимости корректируют положение режущего элемента на станке.
При наладке по эталону первой готовой детали или по шаблону инструмент устанавливают на неработающем станке до касания с поверхностью эталона, готовой детали или шаблона. По конструктивным формам эталон имитирует обрабатываемую деталь при её базировании в приспособлении в среднем положении. При конструировании массу эталона выбирают близкой к массе обрабатываемой детали.
4.3 Техническая документация для наладки
Техническая документация (конструкторская и технологическая), используемая при наладке и сдаче оборудования в эксплуатацию, регламентируется ГОСТами.
К конструкторской документации относятся сборочные чертежи, оборудования и его узлов, деталировочные чертежи, а также паспорт и руководство по эксплуатации. В паспорте содержатся: техническая характеристика; сборочный чертеж; кинематическая схема оборудования; увязочный чертеж узлов; документация на входящие узлы; ведомости покупных изделий, запасных частей, инструмента и приспособлений. В руководстве по эксплуатации содержатся: сведения по распаковке и транспортировании оборудования; чертеж фундамента с установочными размерами; сведения по подготовке оборудования к пуску; схема смазки; электрическая и гидравлическая схемы; сборочные чертежи узлов описанием их работы и методов регулирования; особенности ремонта узлов; характерные возможные неисправности; нормы точности оборудования.
Технологическая документация в зависимости от назначения подразделяется на основную и вспомогательную. К документации общего назначения относятся карта эскизов (представляющая собой графическое изображение технологического процесса обработки изделий) и технологическая инструкция (являющаяся описанием технологического процесса). К документам вспомогательного назначения относятся: маршрутная карта технологического процесса изготовления изделия; карта технологического процесса (с указанием переходов, режимов, обработки, данных о технологической оснастке, материальных и трудовых затратах); карта наладки (с дополнительной информацией к описаниям технологических процессов, касающейся наладки оборудования); ведомости оборудования и оснастки; ведомость расхода материалов; сведения о заготовках и др.
Основными документами, необходимым, для наладки технологического оборудования, являются следующие: чертежи заготовки и обработанной детали; карта технологического процесса и карта наладки.
Организация рабочих мест
Правильная организация рабочего места — необходимое условие высокопроизводительной работы как отдельного рабочего-сборщика так и целой бригады рабочих. Под организацией рабочего места следует понимать не только правильную расстановку оборудован; удобную конструкцию слесарных верстаков, наличие специальных стеллажей и ящиков для хранения деталей и инструментов, но и рациональное расположение инструментов непосредственно на верстаке, достаточное и правильное освещение, а также режим труда.
Большое значение имеет правильная расстановка оборудования (сверлильных станков, прессов, сборочных приспособлений) удобная конструкция слесарных верстаков. Последние бывают одноместные и многоместные. Удобнее пользоваться одноместными или двухместными верстаками. Верстак должен быть оснащен осветительной лампой на специальном поворотном кронштейне, слесарными тисками и инструментальным ящиком под крышкой верстака. Крышку верстака следует облицевать фиброй или линолеумом. Верстак подгоняют по росту рабочего подкладкой деревянных брусков.
Слесарю-сборщику переносный инструментальный ящик необходим в случаях частых переходов с одного объекта сборки на другой.
Для удобства транспортирования и сохранности деталей при сборке применяют стандартную или специальную тару.
Не менее важно обеспечить рабочие места сборщиков стеллажами надлежащей конструкции для размещения деталей. Для хранения устойчивых деталей небольших размеров можно использовать простые стеллажи. Для крупных деталей (особенно круглого сечения) удобнее применять стеллажи с наклонными полками, по которым детали подкатываются или скользят по мере того, как рабочий берёт их со стеллажа. При крупносерийном производстве машин сборочные участки должны быть оснащены специальными стеллажами для тяжёлых деталёй сложной конструкции, размещаемых в специальных гнёздах.
Располагать верстаки, стеллажи и иное оборудование нужно так, что бы сборщикам не приходилось много ходить, совершать лишние движения. Для стационарной сборки тяжелых машин должны быть оборудованы сборочные стенды.
Сборку крупных и тяжелых узлов производят в специальных приспособлениях, конструкция которых определяется размерами и формой собираемых узлов. Транспортирование тяжелых деталей (корпусов, станин и пр.) в сборочных цехах производят кран-балками, тельферами и кошками.
Производительность труда в значительной степени зависит и от правильного размещения слесарного инструмента на верстаке, общего порядка и чистоты на рабочем месте, рационализации рабочих движений, закрепления правильных приемов в работе и общей культуры труда.
6.2 Техника безопасности при монтаже промышленного оборудования
К числу особенностей монтажа промышленного оборудования относятся: большой объем такелажных работ, связанных с применением различных видов подъемно-транспортных механизмов, частая необходимость работать на значительной высоте, а также обилие силовых электропроводок с рабочим напряжением 220 или 380 В.
Невыполнение правил техники безопасности влечет за собой несчастные случаи.
Безопасность ведения работ в значительной степени зависят от правильной организации монтажной площадки и от согласованности в работе отдельных рабочих и целых бригад.
Все рабочие, связанные с работами по строповке, подъему и перемещению грузов с помощью грузоподъемных приспособлений, должны сдать экзамен специальной комиссии на знание правил техники безопасности. Лица моложе 18 лет не допускаются работать стропальщиками.
Проверке такелажного оборудования должно уделяться особое внимание. Не реже, чем через каждые 6 мес. стропы должны испытываться нагрузкой, величина которой вдвое превосходит рабочую. Выбор стропов для подъема груза определенного веса должен производиться по расчету. Обвязывание грузов и подвешивание их к крюкам грузоподъемных механизмов необходимо выполнять правильно с применением соответствующих узлов и петель.
Грузы, примерзшие к земле или засыпанные землей, поднимать с помощью подъемных механизмов запрещено. Все правила техники безопасности при работе с кранами должны безоговорочно выполняться.
Электропроводки и подключения должны быть выполнены весьма тщательно и заземлены. Двигатели электролебедок нужно также обязательно заземлить. Прикосновения к открытым токоведущим частям рубильников, панелей, к корпусам незаземленных электродвигателей и сварочных трансформаторов с неисправным защитным кожухом ведут к поражениям электрическим током.
При работе с воздушными компрессорами необходимо следить, за исправностью манометра и предохранительного клапана, та как аварии компрессоров чаще всего вызываются повышение температуры сжимаемого воздуха при неисправности указанной арматуры.
Для затяжки болтов нужно пользоваться исправным крепежным инструментом, не применять ключей, зев которых больше размеров болта или гайки.
При пользовании переносным электрическим или пневматическим механизированным инструментом нужно выполнять все правила его эксплуатации, гарантирующие безопасность работы.
Общий порядок и чистота на рабочем месте в значительно мере способствуют безопасной работе. При подготовке деталей к сборке последние часто приходите промывать в бензине, пары которого при отсутствии вытяжной вентиляции могут вызвать отравление работающих или взрыв и пожар в помещении.
Нельзя пренебрегать индивидуальными средствами защиты от поражения электрическим током (пользованием изолирующими резиновыми подкладками и перчатками).
При сборке тяжелых машин применяют разного рода подъемные приспособления, правила безопасной работы с которыми также обязательно должен знать слесарь-сборщик.
Перед пуском в ход машины, установленной на испытательном, стенде, нужно проверить наличие исправных защитных ограждении и дать предупредительный сигнал. Производить смазку и регулировку испытываемой машины на ходу запрещено.
Каждый вновь принимаемый рабочий должен быть проинструктирован по общим правилам техники безопасности на данном пред приятии. Перед допуском к выполнению определенной работы рабочий получает инструктаж от мастера. Кроме того, рабочему выдается под расписку письменная инструкция. Периодический инструктаж по технике безопасности должен проводиться не реже двух раз в год.
Заключение
Монтаж и выверка станка – очень трудоёмкий процесс. Он требует от монтажников высокой квалификации и большой точности в работе, так как станок устанавливается на длительное время при жёстком его использовании. Погрешности в установке недопустимы, так, это может повлечь несчастные случаи, травмы на производстве, повреждение оборудования или преждевременный выход его из строя, что может плачевно закончиться для станочника. Выход из строя оборудования – это так же и потери времени. Если неисправность возникла в станке или в АЛ, то это ещё и сбой в производстве. Предприятие не сможет уложиться в сроки и выполнить план.
Чтобы не возникало предвещающих поломку ситуаций, станочник должен внимательно относиться к данному ему станку, проверять работу всех механизмов, обращать внимание на стуки, дребезжания и вибрации, что бы вовремя доложить об этом ремонтной службе и принять меры по их устранению. Многие поломки могут напрямую зависеть от монтажа и быть следствие неправильной установки узлов, заливки фундамента, выверки узлов. В этом случае необходимо будет отрегулировать (выверить) станок заново или повторно произвести его разборку - сборку – монтаж - выверку.
Курсовая работа на тему: «Методы монтажа и выверки оборудования», выполнена на 32 листах формата А4, с 5 рисунками и пояснениями к ним в тексте. Курсовая работа состоит из 9 глав, делящихся на подпункты. Их краткое содержание приведено ниже.
Глава 1. Введение.
Отображает значение промышленного оборудования в народном хозяйстве, и важность работ связанных с монтажом и выверкой оборудования.
Глава 2. Подготовительно – расчётные работы.
Из неё мы узнаём опорные элементы, по которым происходит разметка места положения станка и методы разметки, последовательность завоза оборудования к месту монтажа, и, что не мало важно, документах необходимых для этого. Так же рассматриваются основные виды фундаментов, требования к ним и их расчёт.
Глава 3. Монтажные материалы и инструменты
В этой главе описываются необходимые для монтажа инструменты, монтажные материалы, слесарно-сборочные инструменты, их разновидности и применение. Монтажные контрольно-измерительные инструменты необходимые при установке станка и для проверки качества после монтажа.
Глава 4. Монтаж.
Монтаж – основной вопрос моей работы. Самое главное – последовательность монтажа. Сначала заливается фундамент, в него в свою очередь крепёжные болты, описанных мною типов, затем всё проверяется на точность и происходит монтаж узлом станка. Завершается всё установкой коммуникаций, т.е. прокладной и установкой трубопроводов (гидро- и пневмо-), электрошкафов и электропроводки.
Глава 5. Выверка и наладка станков.
Здесь я описал всё необходимое для наладки выверки станков, средств, за счёт чего это происходит и как происходит, измерительные инструменты и техническую документацию для наладки.
Глава 6. Обкатка и испытания смонтированного оборудования.
Станок можно считать пригодным к работе только после испытаний и обкатки. В этой главе приведён список некоторых существенных причин возникновения поломки. Также приведён пример акта приёмки станка из монтажа.
Глава 7. Техника безопасности при монтаже промышленного оборудования
Монтажник не допускается к работе если не выполнены требования техники безопасности. Основные требования приведены в этой главе.
Глава 8. Заключение.
Содержит краткое содержание глав курсовой работы.
Глава 9. Список используемой литературы.
Содержит список книг и их авторов, которые были применялись при написании данной курсовой работы.
Список используемой литературы
1. Л.С. Брон, С.Н. Власов, Г.М. Годович, К.Н. Константинов, А.П. Никольский, Б.И. Черпаков, учебник “Конструкции наладка и эксплуатация агрегатных станков и автоматических линий” Москва Высшая школа 2001г.
2. Ю.Н. Воронкин, Н.В. Поздняков, учебник “Методы профилактики и ремонта промышленного оборудования” Образовательно-издательский центр “Академия” 2002г.
3. А.Г. Схиртладзе, В.Ю. Новиков, учебник “Станочник широкого профиля” - Москва Высшая школа 2001г.
4. Б.И. Черпаков, Л.И. Вереина, учебник “Технологическое оборудование машиностроительного производства” Издательский центр “Академия” 2-е издание 2006г.
Содержание
Введение
Подготовительно - расчётные работы
1.1 Основы монтажа технологического оборудования
1.2 Виды фундаментов
1.3 Разметка мест под фундаменты
1.4 Требования, предъявляемые к фундаментам
1.5 Расчёт фундаментов
|
|
Состав сооружений: решетки и песколовки: Решетки – это первое устройство в схеме очистных сооружений. Они представляют...
Семя – орган полового размножения и расселения растений: наружи у семян имеется плотный покров – кожура...
Эмиссия газов от очистных сооружений канализации: В последние годы внимание мирового сообщества сосредоточено на экологических проблемах...
Механическое удерживание земляных масс: Механическое удерживание земляных масс на склоне обеспечивают контрфорсными сооружениями различных конструкций...
© cyberpedia.su 2017-2024 - Не является автором материалов. Исключительное право сохранено за автором текста.
Если вы не хотите, чтобы данный материал был у нас на сайте, перейдите по ссылке: Нарушение авторских прав. Мы поможем в написании вашей работы!