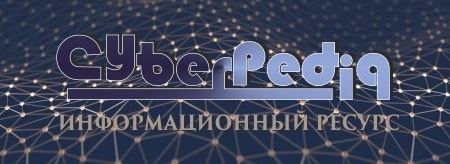
Индивидуальные и групповые автопоилки: для животных. Схемы и конструкции...
Таксономические единицы (категории) растений: Каждая система классификации состоит из определённых соподчиненных друг другу...
Топ:
Методика измерений сопротивления растеканию тока анодного заземления: Анодный заземлитель (анод) – проводник, погруженный в электролитическую среду (грунт, раствор электролита) и подключенный к положительному...
Оснащения врачебно-сестринской бригады.
Оценка эффективности инструментов коммуникационной политики: Внешние коммуникации - обмен информацией между организацией и её внешней средой...
Интересное:
Берегоукрепление оползневых склонов: На прибрежных склонах основной причиной развития оползневых процессов является подмыв водами рек естественных склонов...
Наиболее распространенные виды рака: Раковая опухоль — это самостоятельное новообразование, которое может возникнуть и от повышенного давления...
Отражение на счетах бухгалтерского учета процесса приобретения: Процесс заготовления представляет систему экономических событий, включающих приобретение организацией у поставщиков сырья...
Дисциплины:
![]() |
![]() |
5.00
из
|
Заказать работу |
|
|
Допустимые напряжения и коэффициенты запаса прочности при расчетах деталей машин
Механические характеристики материалов позволяют определить величину допускаемых напряжений [σ], входящих в выражения условий прочности.
Допускаемое напряжение - это наибольшее напряжение для материала конструкции, при котором в данных условиях нагружения гарантированы необходимая прочность и надежность работы. Его определяют по формуле
[σ]=σnp / n
где σпр - предельные напряжения, при достижении которых появляются признаки разрушения конструкции или возникают недопустимые пластические деформации материала. Для деталей из хрупких материалов предельными являются напряжения, близкие к пределу их прочности (σпр = σв), для
пластичных материалов - это предел текучести (σпр = σт);
n – коэффициент запаса прочности, который зависит от свойств материала, характера действующих нагрузок, условий эксплуатации конструкции и др. При расчетах деталей машин требуемый коэффициент запаса прочности принимают равным:
- для пластичных материалов n = 2...4,
- для хрупких n = 4...6.
Выбор материалов для изготовления деталей машин
Выбор материалов является ответственным этапом проектирования. Правильно выбранный материал в значительной мере определяет качество детали и машины в целом.
Выбирая материал, учитывают в основном следующие факторы:
1) соответствие свойств материала главному критерию работоспособности (прочность, жесткость. Износостойкость и др.);
2) весовые и габаритные требования к детали и машине в целом;
3) другие требования, связанные с назначением детали и условиями ее эксплуатации (противокоррозионная стойкость, фрикционные свойства, электроизоляционные свойства и т.д.);
|
4) соответствие технологических свойств материала конструктивной форме и намечаемому способу обработки детали (штампуемость, свариваемость, литейные свойства, обрабатываемость на станках и т.д.);
5) стоимость и дефицитность материала.
Для изготовления деталей машин применяют различные материалы.
Черные металлы, подразделяемые на чугуны и стали, имеют наибольшее распространение. Это объясняется, прежде всего, их высокой прочностью и жесткостью, а также сравнительно невысокой стоимостью.
Основными недостатками черных металлов являются большой удельный вес и слабая коррозионная стойкость.
Цветные металлы – медь, цинк, свинец, олово, алюминий и некоторые другие применяют главным образом в качестве составных частей сплавов (бронз, латуней, баббитов, дюралюминия и т.д.). Эти металлы значительно дороже черных и используются для выполнения особых требований: легкости, антифрикционности, антикоррозионности и др.
Неметаллические материалы – дерево, резина, кожа, асбест, металлокерамика и пластмассы – находят в машиностроении широкое применение.
Пластмассы являются материалами, широко применяющимися в современном машиностроении.
Общим для всех пластмасс является способность формоваться вследствие пластических деформаций при сравнительно невысоких температурах и давлениях. Это позволяет получать из пластмасс изделия почти любой сложной формы высокопроизводительными методами: литьем под давлением, штамповкой, вытяжкой, выдуванием и т.д.
sВторым преимуществом пластмасс, которое следует подчеркнуть, является сочетание легкости и высокой прочности, характеризуемое отношением В и называемое удельной прочностью. По этому показателю некоторые виды пластмасс могут успешно конкурировать с лучшими сортами стали и дюралюминия.g/
Высокая удельная прочность позволяет широко использовать пластмассы в конструкциях, вес, которых имеет особо важное значение (авиация, автомобилестроение и т.д.).
|
Отрицательным, пока еще не устраненным, свойством пластмасс является склонность их к так называемому старению. Старение сопровождается постепенным изменением механических характеристик и даже размеров деталей в процессе эксплуатации.
Рис. 19. Формирование заклепочного шва
Рис. 20. Однорядное заклепочное соединение
Отверстия под заклепки в деталях продавливают или сверлят. При продавливании образуются мелкие трещины по периферии отверстий. Трещины могут быть причиной разрушения заклепочного шва во время работы. Продавленные отверстия применяют в малоответственных конструкциях. Сверление – процесс малопроизводительный и дорогой. Сверленые отверстия применяют в конструкциях, где требуется высокая надежность. При больших диаметрах отверстий практикуют продавливание с последующим рассверливанием.
Каждая заклепка имеет свою зону действия D, на которую распространяется деформация сжатия в стыке деталей. Если зоны действия соседних заклепок пересекаются, то соединение будет плотным. Вследствие пластических деформаций в процессе клепки стержни заклепок заполняют отверстия и заклепки стягивают соединяемые детали. В результате относительному сдвигу склепанных деталей оказывают сопротивление как стержни заклепок, так и силы трения, возникающие на поверхности стыка.
Для обеспечения плотности шва иногда выполняют чеканку (пластическое деформирование листов, например, пневматическими молотками) вокруг заклепок и по кромкам листов.
Заклепки поставляются как готовые изделия.
Заклепочное соединение получают следующим способом.
В отверстия соединяемых деталей вставляют заклепки (см. рис. 19). Под закладную головку 1 устанавливают инструмент-поддержку. Специальной клепальной машиной или вручную (ударами молотка, кувалды) выступающий конец заклепки () осаживают обжимкой в замыкающую головку 2. Для стальных заклепок с
мм производят клепку вхолодную, то же относится к заклепкам из цветных металлов и сплавов; с
мм с нагревом заклепки до светло-красного каления (1000—1100 0С). Этот способ обеспечивает более высокое качество заклепочного шва, так как заклепки укорачиваются при остывании и стягивают детали, создавая на стыке их поверхностей большие силы трения, препятствующие относительному сдвигу деталей при действии нагрузки
|
Диаметры отверстий под заклепки dОТВ выбирают по стандарту в зависимости от диаметра заклепки. Для холодной клепки можно рекомендовать
dOTB = d3 + 0,05d3,
для горячей клепки
dOTB = d3 + 0,ld3,
где d3 — диаметр устанавливаемой заклепки.
Достоинства и недостатки заклепочных соединений по сравнению с другими видами неразъемных соединений.
Достоинства:
- высокая надежность соединения;
- удобство контроля качества клепки;
- повышенная сопротивляемость ударным и вибрационным нагрузкам;
- возможность соединения деталей из трудносвариваемых металлов, например из алюминия;
- не дают температурных деформаций;
- детали при разборке не разрушаются.
Недостатки:
- высокая стоимость, так как процесс получения заклепочного шва состоит из большого числа операций (разметка, продавливание или сверление отверстий, нагрев заклепок, их закладка, клепка) и требует применения дорогостоящего оборудования (станки, прессы, клепальные машины).
- повышенный расход материала для этого соединения (из-за ослабления соединяемых деталей отверстиями под заклепки требуется увеличение их толщины, применение накладок и т. п.);
- детали ослаблены отверстиями;
- высокий шум и ударные нагрузки при изготовлении;
- невозможность соединения деталей сложной конфигурации.
Область применения.
В настоящее время в связи с бурным развитием сварки заклепочные соединения имеют ограниченное применение (в конструкциях, для которых методы сварки и склеивания еще недостаточно разработаны или мало эффективны, а также в соединениях, работающих при больших вибрационных или ударных нагрузках при высоких требованиях к надежности соединения). Также в соединениях окончательно обработанных деталей, в которых применение сварки недопустимо из-за их коробления при нагреве. Большой объем клепально-сборочных работ производится при изготовлении летательных аппаратов. Некоторые самолеты имеют более миллиона заклепок. Заклепочные соединения находят применение в подъемно-транспортных машинах, в строительстве железнодорожных мостов, котлостроении и т. п.
|
Расчет заклепочного шва заключается в определении диаметра и числа заклепок, шага заклепочного шва, расстояния заклепок до края соединяемой детали и расстояния между рядами заклепок.
Диаметр d заклепки назначают из соотношения
(5.1)
где h - суммарная толщина соединяемых элементов
В прочных швах герметичность соединения не требуется, поэтому силы, действующие на соединенные детали, могут быть больше сил трения, развиваемых между ними (рис. 21). Поэтому заклепки прочных швов рассчитывают на срез и на смятие:
(5.2)
(5.3)
где τс и [τс] — соответственно расчетное и допускаемое напряжения на срез для заклепок;
σсм и [σсм] — соответственно расчетное и допускаемое напряжения на смятие между заклепками и соединяемыми листами;
F — сила, действующая на одну заклепку;
k — число плоскостей среза заклепок;
d0 — диаметр поставленной заклепки;
δmin — наименьшая толщина соединяемых элементов.
Необходимое число заклепок z в шве при симметрично действующей нагрузке F0 определяют расчетом заклепок на срез по формуле
Полученное по формуле (5.4) число заклепок z проверяют расчетом заклепок и соединяемых частей на смятие по формуле
Применение заклепок с длинами больше (3... 4)d может вызвать их изгиб в отверстии или незаполнение зазора между стержнем и отверстием.
Рис. 21.
Минимальный шаг p размещения заклепок определяют из удобства клепки, максимальный - из условия плотного соприкосновения соединяемых элементов.
Значения допускаемых напряжений принимают в зависимости от материала заклепки, способа обработки отверстия и условий работы. Так, для заклепок из стали марки Ст.З при обработке отверстия сверлением и нормальных условий эксплуатации: [т]ср = 140 МПа, [σ]см = 280 МПа.
При холодной клепке допускаемые напряжения снижают на 30 %.
Заклепочные соединения разделяют на;
а) силовые (иначе называемые прочными соединениями), используемые преимущественно в металлических конструкциях машин и строительных сооружениях;
б) силовые плотные (иначе называемые плотнопрочными соединениями), используемые в котлах и трубах, работающих под давлением.
Плотность также можно обеспечить с помощью клея.
Материал заклепок должен быть достаточно пластичным для обеспечения возможности формирования головок и однородным с материалом соединяемых деталей во избежание электрохимической коррозии. Стальные заклепки обычно изготовляют из сталей Ст.2, Ст.З, 09Г2 и др. Для соединения элементов из сталей повышенного качества целесообразно применять заклепки из тех же сталей, если возможно по условиям их пластического деформирования. Из легких сплавов для заклепок применяют В65, Д15 и др.
|
Для крепления лопаток некоторых паровых и газовых турбин применяют заклепки, устанавливаемые под развертку и работающие в основном на сдвиг.
Наиболее отработаны конструкции, типаж и технология заклепочных соединений в авиационной промышленности.
Кроме традиционных заклепок применяют:
заклепки из стержней с одновременным расклепыванием обеих головок и образованием гарантированного натяга по цилиндрической поверхности;
заклепки с потайной головкой и компенсатором — местной выпуклостью на головке, деформируемой при клепке и уплотняющей контакт головки;
заклепки для швов с односторонним подходом и с сердечником, который при осевом перемещении распирает заклепку, образуя замыкающую головку, а потом обрывается и фрезеруется для обеспечения гладкой поверхности;
В плотном и точном соединениях необходимо, чтобы вся внешняя нагрузка во избежание местных сдвигов воспринималась силами трения.
Рис. 22. Расчетные схемы односрезиого и двухсрезного заклепочного соединения
Расчет заклепок в соединении, находящемся под действием продольной нагрузки, сводится к расчету их на срез. В заклепочном соединении (рис. 22, а, б)допустимая нагрузка, отнесенная к одной заклепке,
(5.6)
где d — диаметр стержня заклепки; [т]ср— условное допускаемое напряжение заклепки на срез; i— число срезов.
При центрально действующей нагрузке F необходимое число заклепок
z = F/F1. (5.7)
Заклепки на смятие в односрезном или двухсрезном силовом соединении проверяют по формуле
(5.8)
где s— толщина стенки соединяемых деталей.
Проверка на смятие плотных соединений не нужна, так как в них вся продольная нагрузка воспринимается силами трения в стыке.
Соединяемые элементы проверяют на прочность в сечениях, ослабленных заклепками:
Допускаемое напряжение для соединений стальных деталей заклепками из сталей Ст2 и СтЗ при расчете по основным нагрузкам: на срез заклепок [τ]сρ = 140 МПа и на смятие [σ]см=280... 320 МПа, на растяжение соединяемых элементов из стали СтЗ [σ]р = 160 МПа.
При холодной клепке допускаемые напряжения в заклепках снижают на 30%.
Для элементов соединений с пробитыми н нерассверленными отверстиями допускаемые напряжения снижают на 30 %.
Если соединение работает при редких знакопеременных нагрузках, допускаемые напряжения понижают умножением на коэффициент
где Fmin и Fmax— наименьшая и наибольшая по абсолютной величине силы, взятые со своими знаками. Для соединения элементов из низкоуглеродистых сталей a = 1, b = 0,3, а для соединений из среднеуглеродистых сталей a = 1,2, b = 0,8.
Потребная площадь элементов, работающих на растяжение под действием силы F,
где - коэффициент прочности шва, величина которого обычно колеблется в пределах от 0,6 до 0,85;
p - шаг расположения заклепок.
При проектном расчете значением φ задаются, а потом производят проверочный расчет.
В групповых заклепочных соединениях, подверженных сложному напряженному состоянию, силы па одну заклепку определяются, как в резьбовых соединениях.
Расчет резьбы на прочность
Основные виды разрушения резьб: крепежных — срез витков, ходовых — износ витков. В соответствии с этим основными критериями работоспособности и расчета для крепежных резьб являются прочность, связанная с напряжениями среза t, а для ходовых резьб — износостойкость, связанная с напряжениями смятия s см, рис. 1.17.
Условия прочности резьбы по напряжениям среза:
для винта,
для гайки(1.12)
где H — высота гайки или глубина завинчивания винта в деталь; К = аb/р или К = се/р — коэффициент полноты резьбы; Кm — коэффициент неравномерности нагрузки по виткам резьбы.
Для треугольной резьбы К» 0,87, для прямоугольной К» 0,5 для трапецеидальной К» 0,65; Km» (0,6...0,7) —большие значения при sвв/sвг > 1,3, где sвв—предел прочности материала болта, а sвг —гайки. Это связано с тем. что увеличение относительной прочности материала винта позволяет в большей степени использовать пластические деформации в резьбе для выравнивания распределения нагрузки по виткам резьбы.
Если материалы винта и гайки одинаковы, то по напряжениям среза рассчитывают только резьбу винта, так как d1<d.
Условие износостойкости ходовой резьбы по напряжениям смятия: (1.13)
где z = H/p — число рабочих витков (например, число витков гайки). Формула (1.13)—общая для винта и гайки. Коэффициент Кm здесь принят равным единице, с учетом приработки ходовых резьб и при условии, что допускаемые напряжения принимают согласно с накопленным опытом эксплуатации.
Высота гайки и глубина завинчивания. Равнопрочность резьбы и стержня винта является одним из условий назначения высоты стандартных гаек.
Так, например, приняв в качестве предельных напряжений пределы текучести материала на растяжение и сдвиг и учитывая, что tT = 0,6 sT,
запишем условия равнопрочности резьбы на срез и стержня винта на растяжение в виде:
F/[(p/4)d12] — напряжение растяжения в стержне винта, рассчитанное приближенно по внутреннему диаметру резьбы d1. откуда при K = 0,87 и Km» 0,6 получаем:
H» 0,8d1. (1.14)
В соответствии с этим высоту нормальных стандартных гаек крепежных изделий принимают H» 0,8d. (1.15)
Кроме нормальных стандартом предусмотрены высокие H» 1,2 d низкие H» 0,5 d гайки.
Так как d > d1 (например, для основной крепежной резьбы d» 1,2 d1, то прочность резьбы при нормальных и высоких гайках превышает прочность стержня винта.
По тем же соображениям устанавливают глубину завинчивания винтов и шпилек в детали: в стальные детали H1 = d, в чугунные и силуминовые H1» 1,5d.
Стандартные высоты гаек (за исключением низких) и глубины завинчивания исключают необходимость расчета на прочность резьбы стандартных крепежных деталей
Расчет на прочность стержня винта (болта) при различных случаях нагружения
Стержень винта нагружен только внешней растягивающей силой. Примером служит нарезанный участок крюка для подвешивания груза (рис. 1.18). Опасным является сечение, ослабленное нарезкой. Площадь этого сечения оценивают приближенно по внутреннему диаметру d1 резьбы. Условие прочности по напряжениям растяжения в стержне:
Болт затянут, внешняя нагрузка отсутствует. Примером служат болты для крепления ненагруженных герметичных крышек и люков корпусов машин (рис. 1.19). В этом случае стержень болта растягивается осевой силой Fзат возникающей от затяжки болта, и закручивается моментом сил в резьбе Тр—см. формулу (1.5), где F равна Fзат. Напряжение растяжения от силы Fзат,
Напряжение кручения от момента ТР:
Требуемое значение силы затяжки
Fзат = А sсм, где А — площадь стыка деталей, приходящаяся на один болт, sсм — напряжение смятия в стыке деталей, значение которого выбирают по условиям герметичности.
Прочность болта определяют по эквивалентному напряжению: (1.18)
Вычисления показывают, что для стандартных метрических резьб, sэкв= 1,3 s.
Это позволяет рассчитывать прочность болтов по упрощенной формуле:
(1.19) Расчетами и практикой установлено, что болты с резьбой меньше M10....М12 можно разрушить при недостаточно квалифицированной затяжке. Например, болт с резьбой Мб разрушается при силе на ключе, равной 45Н; болт с резьбой М12 — при силе 180 H
Поэтому в среднем и тяжелом машиностроении не рекомендуют применять болты малых диаметров (меньше М8). На некоторых заводах для затяжки болтов используют специальные ключи предельного момента. Эти ключи не позволяют приложить при затяжке момент больше установленного. В таком случае отпадает необходимость ограничивать применение болтов малых диаметров (при условии, что ключи предельного момента применяют и в эксплуатации).
Болтовое соединение нагружено силами, сдвигающими детали в стыке
Условием надежности соединения является отсутствие сдвига деталей в стыке. Конструкция может быть выполнена в двух вариантах. Болт поставлен с зазором (рис. 1.20). При этом внешнюю нагрузку F уравновешивают силами трения в стыке, которые образуются от затяжки болта. Без затяжки болтов детали могут сдвигаться на значение зазора, что не допустимо. Рассматривая равновесие детали 2, получим условие отсутствия сдвига деталей
F £ iFTP = iFзат f, илиFзат = K F / (i f);
где i—число плоскостей стыка деталей (на рис. 1.20—i = 2; при соединении только двух деталей i = 1); f — коэффициент трения в стыке (f = 0,15...0,20 для сухих чугунных и стальных поверхностей);
К —коэффициент запаса (K =1,3...1.5 при статической нагрузке, K = 1,8...2 при переменной нагрузке).
Прочность болта оценивают по эквивалентному напряжению — формула (1.19).
Отметим, что в соединении, в котором болт поставлен с зазором. внешняя нагрузка не передается на болт. Поэтому болт рассчитывают только на статическую прочность по силе затяжки даже при переменной внешней нагрузке. Влияние переменной нагрузки учитывают путем выбора повышенных значений коэффициента запаса.
Болт поставлен без зазора (рис. 1.21).
В этом случае отверстие калибруют разверткой, а диаметр стержня болта выполняют с допуском, обеспечивающим беззазорную посадку. При расчете прочности соединения не учитывают силы трения в стыке, так как затяжка болта необязательна. В общем случае болт можно заменить штифтом. Стержень болта рассчитывают по напряжениям среза и смятия.
Условие прочности по напряжениям среза:
(1.21), где i — число плоскостей среза (на рис. 1.21a, i = 2; при соединении только двух деталей — рис. 1.21, б i = 1). Закон распределения напряжений смятия по цилиндрической поверхности контакта болта и детали (рис. 1.22) трудно установить точно.
В значительной степени это зависит от точности размеров и формы деталей соединения. Поэтому расчет на смятие производят по условным напряжениям. Эпюру действительного распределения напряжений (рис. 1.22, а) заменяют условной с равномерным распределением напряжений (рис. 1.22, б).
При этом для средней детали (и при соединении только двух деталей)
или для крайней детали
Формулы (1.22) справедливы для болта и деталей. Из двух значений scм в этих формулах расчет прочности выполняют по наибольшему, а допускаемое напряжение определяют по более слабому материалу болта или детали.
Сравнивая варианты установки болтов с зазором и без зазора (см. рис. 1.20 и 1.21), следует отметить, что первый вариант дешевле второго, так как не требует точных размеров болта и отверстия. Однако условия работы болта, поставленного с зазором, хуже, чем без зазора.
Так, например, приняв коэффициент трения в стыке деталей f» 0,2, K=1,5 и i = 1, из формулы (1.20) получим Fзат= 7,5F. Следовательно, расчетная нагрузка болта с зазором в 7,5 раз превышает внешнюю нагрузку. Кроме того, вследствие нестабильности коэффициента трения и трудности контроля затяжки работа таких соединений при сдвигающей нагрузке недостаточно надежна.
Болт затянут, внешняя нагрузка раскрывает стык деталей
Примером служат болты для крепления крышек резервуаров, нагруженных давлением p жидкости или газа (рис. 1.23). Затяжка болтов должна обеспечить герметичность соединения или нераскрытие стыка под нагрузкой. Задача о распределении нагрузки между элементами такого соединения статически неопределима и решается с учетом деформаций этих элементов. Обозначим: Fзат — сила затяжки болта; F=R/z — внешняя нагрузка соединения, приходящаяся на один болт (z — число болтов).
После приложения внешней нагрузки к затянутому соединении; болт дополнительно растянется на некоторую величину D, а деформация сжатия деталей уменьшится на ту же величину.
Для простоты можно сказать, что только часть внешней нагрузки дополнительно нагружает болт, а другая часть идет на разгрузку стыка.
Если обозначим c — коэффициент внешней нагрузки (учитывает; приращение нагрузки болта в долях от силы F, то дополнительна нагрузка болта равна c F, а уменьшение затяжки стыка — (1—c)F
Значение коэффициента c определяют по условию равенства дополнительных деформаций болта и деталей (условие совместности деформаций):
(1.23);
где lб — податливость болта, равная его деформации при единично нагрузке; lд — суммарная податливость соединяемых деталей.
Из равенства (1.23)
(1.24)
Далее получим приращение нагрузки на болт
(1.25)
расчетную (суммарную) нагрузку болта
(1.26)
и остаточную затяжку стыка от одного болта
(1.27)
12. Расчет стержня болта (винта) на прочность, при различных способах нагружения
Рассмотрим четыре случая работы соединения.
Стержень винта нагружен только внешней растягивающей силой F.
Болт затянут, внешняя нагрузка отсутствует.
Болтовое соединение нагружено силами, сдвигающими детали в стыке.
Болт затянут, внешняя нагрузка раскрывает стык деталей.
П ервый случай. Примером служит резьбовой участок грузового болта для подвешивания груза.
Опасным является сечение, ослабленное резьбой. Площадь этого сечения оценивают приближенно по внутреннему диаметру d1 резьбы. Условие прочности по напряжениям растяжения в стержне
,
г де допускаемое напряжение для растягивающей внешней нагрузки без затяжки болтов [σ] = 0,6 σT .
Второй случай. Примером служат болты для крепления ненагруженных герметичных крышек и люков корпусов машин. В этом случае стержень болта растягивается осевой силой Fзат, возникающей от затяжки болта, и закручивается моментом сил трения в резьбе Тр, т.е. работает на кручение. Прочность болта определяют по эквивалентному напряжению
Для стандартных метрических резьб расчеты показывают, что
σэкв 1,3 σ. Это позволяет производить расчет прочности болтов по упрощенной формуле
.
В среднем и тяжелом машиностроении не рекомендуют применять болты малых диаметров (меньше М8), т.к. их можно разрушить при недостаточно квалифицированной затяжке.
Т ретий случай. Условием надежности соединения является отсутствие сдвига деталей в стыке. Конструкция может быть выполнена в двух вариантах: первый, болт поставлен с зазором; второй – болт поставлен без зазора. Начнем рассмотрение с варианта, когда болт поставлен с зазором.
Внешняя нагрузка уравновешивается силами трения в стыке, которые образуются от затяжки болта. Без затяжки болтов детали могут сдвигаться на величину зазора, что недопустимо. Рассматривая равновесие детали 2, получаем условие отсутствия сдвига деталей
F i Fтр = i Fзат f, или Fзат=KF/(if),
где i – число плоскостей сдвига деталей (на рисунке i = 2); f – коэффициент трения в стыке; (f = 0,15…0,20); K – коэффициент запаса (K = 1,3…1,5 при статической нагрузке, K = 1,8…2 при переменной нагрузке).
Прочность болта оценивают по эквивалентному напряжению σэкв.
Замечание: В соединении, в котором болт поставлен с зазором, внешняя нагрузка не передается на болт. Поэтому болт рассчитывают только на статическую прочность по силе затяжки даже при переменной внешней нагрузке. Влияние переменной нагрузки учитывают путем выбора повышенных значений коэффициента запаса.
Болт поставлен без зазора.
В этом случае отверстие под болт калибруют разверткой, а диаметр стержня болта выполняют с допуском, обеспечивающим беззазорную посадку. При расчете прочности соединения не учитывают силы трения в стыке, так как затяжка болта не обязательна. В общем случае болт можно заменить штифтом. Стержень болта рассчитывают по напряжениям среза и смятия.
Условие прочности по напряжениям среза
Расчет на смятие производится по условным напряжениям из-за сложности установить точный закон распределения напряжений по цилиндрической поверхности деталей. При этом для средней детали (и при соединении только двух деталей)
Для крайних деталей
Из двух значений σсм расчет прочности выполняют по наибольшему, а допускаемое напряжение определяют по более слабому материалу болта или детали.
Ч етвертый случай. Болт затянут, внешняя нагрузкараскрывает стык деталей. Примером служат болты для крепления крышек цилиндров (резервуаров), нагруженных давлением р жидкости или газа.
Затяжка болтов должна обеспечить герметичность соединения или нераскрытие стыка под нагрузкой.
Обозначим: Fзат – сила затяжки болта; F1 = F/z – внешняя нагрузка соединения (от давления), приходящаяся на один болт; z – число болтов. Приложение внешней нагрузки вызывает дополнительную нагрузку на болт
,
где χ – коэффициент внешней нагрузки, который определяется по условию равенства деформаций болта и деталей:
где λδ – податливость болта, равная его удлинению при единичной нагрузке; λд – суммарная податливость соединяемых деталей.
Расчетная (суммарная) нагрузка болта:
Fp = Fзат + χ F1.
Для большинства практических случаев расчет податливостей деталей связан с большими трудностями. Между тем расчеты и испытания конструкций показывают, что χ можно принять равным или меньше (0,2….0,3) для соединений без мягких прокладок.
а) Прочность болта при статической нагрузке:
Здесь коэффициент 1,3 по-прежнему учитывает напряжения кручения, которые могут возникнуть при затяжке соединения под нагрузкой.
б) Прочность болта при переменных нагрузках.
При переменных нагрузках полное напряжение в болте можно разделить на постоянное (σm) и переменное с амплитудой (σа):
Запас прочности по переменным напряжениям подсчитывают по формуле:
,
где σ-1– предел выносливости материала болта; Kσ – эффективный коэффициент концентрации напряжений в резьбе; ψ σ – коэффициент чувствительности к асимметрии цикла напряжений.
Переменные напряжения вызывают явление усталости. Чем меньше χ, тем выше сопротивление болта усталости. При этом, упругие болты – хорошая защита от усталостного разрушения.
Рис. 34. Расчетные схемы клеммового соединения
Второй случай. Клемма достаточно гибкая, форма сопрягаемых деталей строго цилиндрическая, зазор в соединении равен нулю (рис.34,б). В этом случае можно полагать, что давление P распределено равномерно по поверхности контакта, а условие прочности соединения выражается в виде
Вспоминая теорему о равнодействующей равномерного давления на кривую стенку и рассматривая равновесие полуклеммы, запишем . После постановки и сокращения получим
Таким образом, нагрузочные способности для двух предельных случаев относятся как 2/π. Первый случай является самым неблагоприятным, а второй – наиболее рациональным с точки зрения потребной величины затяжки болтов. На практике условия работы клеммовых соединений рассматривают как среднее между двумя рассмотренными выше:
Для определения силы затяжки выразим Q:
где Z - число болтов, расположенных с одной стороны вала; k =1,3…1,8 - коэффициент надежности соединения.
При совместном действии M и S сдвигающей силой на поверхности контакта будет равнодействующая осевой силы S и окружной . Для такого случая
Планетарные передачи. Их преимущества и недостатки
Планетарными называют передачи, имеющие зубчатые колёса с перемещающимися осями. Эти подвижные колёса подобно планетам Солнечной системы вращаются вокруг своих осей и одновременно перемещаются вместе с осями, совершая плоское движение, называются они сателлитами (лат. satellitum – спутник). Подвижные колёса катятся по центральным колёсам (их иногда называют солнечными колёсами), имея с ними внешнее, а с корончатым колесом внутреннее зацепление. Оси сателлитов закреплены в водиле и вращаются вместе с ним вокруг центральной оси.
Планетарные передачи имеют ряд преимуществ перед обычными:
большие передаточные отношения при малых габаритах и массе;
возможность сложения или разложения механической мощности;
лёгкое управление и регулирование скорости;
малый шум вследствие замыкания сил в механизме.
Недостатки:
Повышенные требования к точности изготовления и монтажа передачи.
Резкое снижение КПД передачи с ростом передаточного отношения.
В планетарных передачах широко применяют внутреннее зубчатое зацепление с углом a w = 30о.
Для обеспечения сборки планетарных передач необходимо соблюдать условие соосности (совпадение геометрических центров колёс); условие сборки (сумма зубьев центральных колёс кратна числу сателлитов) и соседства (вершины зубьев сателлитов не соприкасаются друг с другом).
Зубчатые колёса планетарных передач рассчитываются по тем же законам, что и колёса обычных цилиндрических передач.
Критерии работоспособности деталей машин (прочность, жесткость, износостойкость, коррозионная стойкость, теплостойкость, вибростойкость)
Работоспособность деталей оценивается по критериям работоспособности. Основные критерии работоспособности и расчета деталей машин:
- прочность;
- жесткость;
- износостойкость;
- коррозионная стойкость;
- теплостойкость;
- виброустойчивость.
Значение того или иного критерия для данной детали зависит от ее функционального назначения и условий работы. Например, для крепежных винтов главным критерием является прочность, а для винтов резьбовых передач - износостойкость. При конструктировании деталей их работоспособность обеспечивают в основном выбором соответствующего материала, рациональной конструк
|
|
Наброски и зарисовки растений, плодов, цветов: Освоить конструктивное построение структуры дерева через зарисовки отдельных деревьев, группы деревьев...
Таксономические единицы (категории) растений: Каждая система классификации состоит из определённых соподчиненных друг другу...
Организация стока поверхностных вод: Наибольшее количество влаги на земном шаре испаряется с поверхности морей и океанов (88‰)...
Семя – орган полового размножения и расселения растений: наружи у семян имеется плотный покров – кожура...
© cyberpedia.su 2017-2024 - Не является автором материалов. Исключительное право сохранено за автором текста.
Если вы не хотите, чтобы данный материал был у нас на сайте, перейдите по ссылке: Нарушение авторских прав. Мы поможем в написании вашей работы!