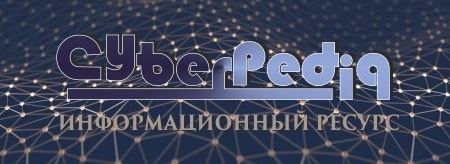
История развития пистолетов-пулеметов: Предпосылкой для возникновения пистолетов-пулеметов послужила давняя тенденция тяготения винтовок...
Своеобразие русской архитектуры: Основной материал – дерево – быстрота постройки, но недолговечность и необходимость деления...
Топ:
Техника безопасности при работе на пароконвектомате: К обслуживанию пароконвектомата допускаются лица, прошедшие технический минимум по эксплуатации оборудования...
Устройство и оснащение процедурного кабинета: Решающая роль в обеспечении правильного лечения пациентов отводится процедурной медсестре...
Отражение на счетах бухгалтерского учета процесса приобретения: Процесс заготовления представляет систему экономических событий, включающих приобретение организацией у поставщиков сырья...
Интересное:
Аура как энергетическое поле: многослойную ауру человека можно представить себе подобным...
Наиболее распространенные виды рака: Раковая опухоль — это самостоятельное новообразование, которое может возникнуть и от повышенного давления...
Искусственное повышение поверхности территории: Варианты искусственного повышения поверхности территории необходимо выбирать на основе анализа следующих характеристик защищаемой территории...
Дисциплины:
![]() |
![]() |
5.00
из
|
Заказать работу |
|
|
Чистые вещества и их классификация. В СССР принята классификация чистых материалов для полупроводниковой техники, согласно которой они подразделяются на З класса: А, В. С. К классу чистоты A1 и А2 относятся веществам с содержанием примесей выше 0,01%, которые можно определить методом классического химическоrо анализа. К классам чистоты В3-В6 и C7-C10 относятся вещества, для которых приводятся характеристики лишь по содержанию анализируемых примесей.
В последнее время высокочистые материалы принято подразделять на вещества эталонной чистоты (ВЭЧ) и особо чистые вещества (ОСЧ). В первых лимитируют присутствие небольшого количества особо нежелательных примесей. При этом указывают общее содержание примесей в виде цифр перед индексом. ВЭЧ, а также количество определяемых примесей и их суммарное содержание. Например, обозначение 003ВЭЧ4-7 соответствует материалу с общим содержанием примесей 0,003 масс.%, с четырьмя определяемыми примесями, количество которых равно 10-7масс. % По сравнению с материалами класса ВЭЧ вещества ОСЧ характеризуются большей чистотой. При этом количество определяемых примесей значительно больше, а потому общее содержание примеси практически соответствует сумме определяемых. Например, обозначение ОСЧ10-5 соответствует особо чистому веществу с десятью определяемыми примесями и с их общим содержанием 10-5 масс.% (пo старой классификации ВЭЧ).
В маркировке полупроводниковых материалов обозначают не только легирующей примеси, но и те свойства, которые наиболее важны для практического применения, а иногда и способ получения. Например, маркеровка БКЭФ-10/0,2 характеризует кремний (К), полученный бестиrельной зонной плавкой (Б), электронного типа проводимости (Э), леrированный фосфор (Ф) с удельным сопротивлением 10 Ом*см и временем жизни в основных носителей 0,2 мкс; арсенид галлия АГДЦЗ,5-17 - дырочного типа (Д), лeгированый цинком (Ц) с концентрацией дырок 3,5*1017. Фосфид галлия, применяемый для фотодиодов, маркируется, например, так: ФГЭТК-К/30 [Э – электронноrо типа, ТК - легирован теллуром, кислородом, К- - красное свечение p-n-nepеxод, 30 - яркость свечения. кд/м2].
|
Термодинамические условия зарождения фазовой границы. Процессы кристаллизации представляют собой фазовые переходы, сопровождающиеся увеличением степени упорядоченности. Эти процессы подразделяются на 2 типа: газ-кристалл, жидкость (стекло) кристалл. В термодинамическом отношении данные фазовые равновесия опнсываются однотипно. В предкристаллизационный период жидкости образуются ассоциаты в пределах ближнего порядка, которые, однако, не могут стать зародышем новой фазы из-за термодинамической нестабильности. Эта нестабильность - следствне их большой поверхностной энергии. Возникающие таким ооразом гoмoгенные флуктуации не способны к самостоятельному существованию в расплаве, и время их релаксации зависит от многих факторов: вязкости теплопроводности, теплоемкости и т. п. По мере снижения температуры стабильность и время релаксации (τ) гомогенных флуктуаций возрастают. Если τ→∞, эта величина исключается и для анализа системы достаточно знания термодинамических параметров.
Зародышем новой фазы следует считать ассоциат минимального размера, стабильность которого не зависит от времени: Образование зародыша сопровождается возникновением фазовой границы, что связано с затратой работы. Выделяющаяся при этом скрытая теплота
кристаллизации должна эффективно отводиться для обеспечения изотермических условий. В частности, образование гетерогенной флуктуации (зародыша новой фазы) в расплаве при температуре кристаллизации (температуре плавления) невозможно, поскольку выделяющаяся, скрытая теплота кристаллизации способствует разрушению новообразований. Для образования зародыша необходимо переохлаждение расплава, компенсирующее выделение тепла.
|
Для оценки размера критического зародыша необходимо учесть соотношение объемной и nоверхностноти свободной энергии при образовании новой фазы. Изменение свободной энергин при кристаллизации (для сферического зародыша) можно представить в виде
где γ - удельная поверхностная энергия; - изменение свободной энергии при кристаллизации для единицы объема; г - радиус зародыша; γ и
не зависят от г н имеют разные знаки.
С увеличением размера зародыша поверхностная энергия растет медленнее, чем уменьшается объемная энергия. При. некоторой величине r оба члена равны друг другу, что является термодинамическим критерием возникновения стабильного критическоrо зародыша радиусом rк. Величину rк можно определить, приравняв нулю производную :
Поскольку r = 0 ~не удовлетворяет условиям задачи, то справедливо единственное решение.
Тогда свободная энергия критического зародыша
Как следует из (?), размер.критического зародыша зависит от γ и которые определяются геометрией и энергетикой ближнеrо порядка.
В практическом отношении важно так называемое двумерное зарождение, которое реализуется при выращивании кристаллов на·затравках. При этом ориентирующее влияние подложки, обусловленное избыточной поверхностной энергией, снижает флуктуацию энергии , необходимую для образования двумерного зародыша, а та уменьшает размер критического зародыша. При этом свободную энергию зародыша можно представить в виде
Тогда из условия следует, что
Решающую роль в процессе зарождения (и дальнейшего роста кристаллов играет переохлаждение (пересыщение), которым определяется в конечном итоге разность химических потенциалов сосуществующих фаз. Существуют различные способы выражения пересыщений. Для выращивания из газовой фазы: ΔР = Р - Рs – абсолютное пересыщение; β = ΔР/Р s - относительное пересыщение; γ=Р/ Р s - коэффициент пересыщения; где Р - давление пара компонента в газовой фазе; P s - · равновесное. давление пара над твердой фаз Р > Рs
Для растворов используют концентрационное пересыщение ΔС=С- Cs - абсолютное, β=ΔС/Сs - относительное, γ=С/Сs - коэффициент пересыщения (С> Сs). Для кристаллизаци и из pacплава используют величину переохлаждения ΔТ=Тпл-Т, где Тпл - температура плавления вещества, Т - температура переохлажденного расплава, Т < Тпл.
|
Величина пересыщения (переохлаждения) определяет вероятность образования зародышей, их размер и число. При значительных пересыщениях образование зародышей облегчается, критический радиус зародыша уменьшается и вследствие этого возрастает число центров кристаллизации. Таким образом, при значительных пересыщениях создаются условия, способствующие росту поликристалла.
Для получения монокристалла необходимо каким-нибудь образом подавить образование множественных центров кристаллизации. Одним из путей является снижение пересыщения (переохлаждения), способствующее увеличению критического радиуса зародыша. Введение монокристаллической затравки приводит к аналогичным результатам. При этом спонтанный рост трехмерных зародышей подавляется, а осуществляется двумерный рост кристалла на затравке, более выгодный в термодинамическом отношении.
Однотемпературный синтез
(Получение соединений с малым давление диссоциации)
Особенности и границы применимости метода. Однотемпературный синтез из компонентов является одним из наиболее простых и распространенных. Преимущества этого метода: а) простота достижения стехиометрии в процессе синтеза и отсутствие потерь компонентов; б) несложное аппаратурное оформление; в) отсутствие посторонних веществ и избытка компонентов, которое обусловливает высокую чистоту получаемого продукта. Тем не менее этот метод обладает рядом недостатков, ограничивающих область его применения. Он применим лишь для получения веществ из малолетучих компонентов, поскольку при заметной их летучести возможны отклонения от стехиометрии за счет испарения. Данным методом трудно получать соединения, образующиеся по перитектической реакции. Поскольку необходимо нагревание компонентов выше температуры плавления соединения то получение тугоплавких фаз также затруднено. Это связано с необходимостью использовать специальные нагреватели, а также с ограничениями при выборе контейнерных материалов.
|
Прямой однотемпературный синтез может быть применен лишь к соединениям, образующимся в условиях нонвариантного равновесия, т. е. когда состав практически не зависит от давления. Для обоснованного выбора режима синтеза необходимо знать лишь Т – X-диаграмму состояния данной системы. Этот метод можно иногда использовать и для получения соединения из компонентов, обладающих заметной летучестью, при условии, что давление диссоциации соединения намного меньше, чем давление пара компонентов при той же температуре (и составляет не более 0,1 атм). При этом нагревание необходимо производить осторожно, постепенно поднимая температуру в соответствии со скоростью реакции во избежание разрушения ампулы.
Оборудование и материалы: Ампулы из кварцевого стекла*; печь с силитовым или нихромовым нагревателем и терморегулятором; установка для откачки и отпаивания ампул; ХА-термопары и потенциометр ПП-63; сырьё.
*Для синтеза InSb и Bi2Te3 используют ампулы с толщиной стенок 1,5-2 мм, для GeAs - с толщиной стенок 2,5-3 мм; диаметр ампул – 10-15 мм.
Порядок выполнения. Синтез предложенных соединений проводят в вакуумированных кварцевых ампулах. Кварцевое стекло при температурах синтеза не размягчается и не реагирует с расплавленными компонентами. Необходимый вакуум (10-2 мм рт. ст. во избежание окисления материалов) создают при помощи форвакуумного насоса без использования паромасляных диффузионных насосов. Дли получения достаточно чистых продуктов исходные компоненты и ампулы должны быть чистыми.
Взвешенные количества компонентов из расчета получения необходимой массы продута загружают в ампулу, которую откачивают, запаивают и помещают в печь, позволяющую производить равномерный нагрев. Температура поднимается по определенному режиму, зависящему от летучести компонентов и скорости реакции.
Двухтемпературный синтез
(Получение соединений с высоким давлением диссоциации)
Особенности и границы применимости метода. При получении соединений со значительным давлением пара необходимо контролировать температуру и давление, поскольку слитки заданного состава могут быть получены при этом только в условиях бивариантного равновесия. Возможность независимого регулирования и контроля температуры и давления в системе реализуется в условиях так называемого двухтемпературного метода синтеза. В этом методе нелетучий компонент должен находиться в более горячей зоне в двухтемпературной печи при температуре Т1, а летучий — в низкотемпературной при Т2 (Т1> Т2). Обычно температура Т1 должна быть на 10-20° выше температуры плавления синтезируемого сплава. В установившемся температурном режиме летучий компонент, испаряясь при температуре Т2, поглощается расплавленным (или твердым) нелетучим компонентом. Состав расплава определяется температурой Т1 и давлением пара в системе, которое, в свою очередь, регулируется температурой Т2. Для контролируемого регулирования давления в системе изменением температуры Т2 необходимо знать зависимость давления насыщенного пара летучего компонента от температуры.
|
Независимое регулирование температуры и давления в процессе синтеза позволяет варьировать условия опыта от мягких до жестких. К числу достоинств описываемого метода относится возможность синтеза соединений с высокими значениями температуры плавления и давления диссоциации, перитектических фаз и соединений, претерпевающих фазовый переход в твердом состоянии. В принципе этот метод можно считать достаточно универсальным, однако его практическое применение ограничено необходимостью знания Р–Т–х-диаграмм состояния, которые в настоящее время известны не для всех систем. Сведения о Р–Т–х-диаграммах являются необходимым, но недостаточным условием, обеспечивающим обоснованный выбор технологии, четкого режима проведения процесса двухтемпературного синтеза. Кроме термодинамических параметров следует иметь в виду и возможные кинетические ограничения, связанные с конечной скоростью насыщения конденсированной фазы летучим компонентом из пара.
Оборудование и материалы. Кварцевые трубки для ампул (внутренний диаметр 10—15, толщина стенок 3 – 4 мм); двухзонная печь с раздельной регулировкой температур; две термопары (ХА) и прибор для измерения температуры (потенциометр ПП-63); феррорезонансный стабилизатор напряжения на 0,75 кВт (С-0,75).
Порядок выполнения. Собирают установку по схеме, приведенной на рис. 2.
Двухтемпературную печь изготавливают путем намотки нихромовой проволоки (диаметр 0,6—0,8 мм) на кварцевую трубу длиной 0,5 м и внутренним диаметром 25 мм с последующей обмазкой смесью огнеупорной глины с асбестовой крошкой и небольшой добавкой шамота (10:20:1). Смесь замешивают на воде до тестообразного состояния. Для фиксации обмотки на гладкой поверхности кварцевой трубы вдоль трубы прокладываются 3—4 асбестовые нити. После обмазки печь просушивают пропусканием тока небольшой величины через обмотку. Затем необходимо проверить распределение температуры в печи (температурный профиль, рис. 3). Если это распределение отличается от приведенного на рис. 3 (наблюдаются местные «провалы» температуры или перегрев), то температурный профиль корректируется или дополнительной местной обмазкой, или снятием части теплоизоляции.
Рассчитанные количества компонентов располагают в противоположных концах толстостенных ампул так, чтобы при помещении в двухтемпературную печь фосфор находился в холодной зоне, а металл — в горячей. Ампулы вакуумируют до 10-2—10-3мм рт. ст. и отпаивают. Во всех работах необходимо соблюдать осторожность: точно выдерживать указанный температурный режим и скорость нагрева так как несоблюдение этих условий может привести к взрыву, а слишком быстрое охлаждение — к растрескиванию ампул. Вскрытие охлажденных ампул производят под тягой. Если в ампуле осталось некоторое количество непрореагировавшего фосфора, то возможно самовозгорание.
Пример синтеза GaAs
Кристаллы арсенида галлия получают на установке "Синтез".
В тигель из пиролитического нитрида бора высокой чистоты загружают 1,52 кг мышьяка марки ОСЧ17-4 (с учетом перегрева берут избыток мышьяка), 1,5 кг галлия чистотой 99.9999% и 0,8 кг оксида бора с остаточным содержанием влаги во флюсе 0,14% по массе. Тигель устанавливают в тепловое устройство камеры установки "Синтез”. После осуществления загрузки камеру установки закрывают, вакуумируют ее до остаточного давления 10-2 мм рт.ст, заполняют инертным газом - азотом до давления 21 атм и начинают нагревать флюс и загрузку в тигле до температуры синтеза 610° С.
В результате реакции между мышьяком и галлием в тигле образуется расплав арсенида галлия, покрытый слоем флюса. Затем нагревают расплав до температуры 1260°С и выдерживают в течение 12 мин. После этого проводят охлаждение расплава со скоростью 310 град/ч до температуры 1125°С. Вновь нагревают материал до температуры 1260°С со скоростью 310 град/ч, выдерживают 12 мин. и далее по заданной программе от ЭВМ охлаждают со скоростью 85 град/ч.
Таким образом получают кристаллический арсенид галлия с суммарным содержанием остаточных примесей на уровне 1,20∙1015 см3. Остальные примеры выполнения приведены в таблице, где примеры 2-11 выполнены в пределах, заявленных о формуле изобретения, с 12-21 показан выход за пределы, а пример 23 выполнен по способу-прототипу.
Проведенные дополнительные испытания полученного материала в процессах выращивания монокристаллов полуизолирующего арсенида галлия показали, что подвижность носителей заряда в выращенных монокристаллах была выше 4500см2 /В∙с, выращивание по способу-прототипу обеспечило подвижности носителей заряда в монокристаллах на уровне 3842 см2/B∙c
Использование предлагаемого способа обеспечивает по сравнению с прототипом получение более чистого арсенида галлия:
1) снижение суммарного содержания примесей;
2) увеличение подвижности носителей заряда с 3342 до 4598 см2/В∙с
Формула изобретения
Способ получения кристаллического арсенида галлия, включающий нагрев и взаимодействие исходного галлия с мышьяком под слоем влагосодержащего оксида бора при повышенном давлении инертного газа и охлаждение до комнатной температуры со скоростью 70-100 град/ч, отличающийся тем, что, с целью повышения чистоты конечного продукта, нагрев ведут до 1250-1270°С, проводят выдержку в течение 10-15 мин и охлаждение до 1100-1150°С со скоростью 300-320 град/ч, затем с этой же скоростью повторяют нагрев и выдержку, после чего проводят охлаждение до комнатной температуры.
№№ пп | Температура наrpeвa расплава до и после “термоудара” (Т), °С | Время выдержки,мин | Температура охлаждения расплава при “термоударе” (Т), °С | Скорость охлаждения расплава GaAs под флюсом (V1), град/ч | Скорость охлаждения расплава после “термоудара” (V2), град/ч | Суммарное содержание примесей, см-3 | Подвижность заряда. см2/В∙с |
1 | 1260 | 12 | 1125 | 310 | 85 | 1,20∙1015 | 4598 |
2 | 1250 | 12 | 1125 | 310 | 85 | 1,32∙1015 | 4592 |
3 | 1270 | 12 | 1125 | 310 | 85 | 1,41∙1015 | 4576 |
4 | 1245 | 12 | 1125 | 310 | 85 | 6,10∙1015 | 3961 |
5 | 1275 | 12 | 1125 | 310 | 85 г | 6,30∙1015 | 3932 |
6 | 1260 | 12 | 1160 | 310 | 110 | 1,34∙1016 | 3851 |
Таблица 2. Параметры эксперимента
Некоторые рекомендации по работе в лаборатории в процессе синтеза.
Лаборатория должна быть соответствующим образом оборудована. В ней необходимо организовать специализированные участки: вакуумный участок с газовой горелкой для стеклодувных и кварцедувных работ; термическии участок, в котором сосредоточены печи для одно- и двухтемпературного синтеза.
Для проведения необходимых процессов рекомендуется лаборатория, включающая два помещения по 36- 40 м2. При размещении оборудования целесообразно предусмотреть отделение участков синтеза и подготовки материалов от участков физико-химических и электрических исследований. Работа в физико-химической лаборатории требует соблюдения ряда мер предосторожности. Важным этапом является подбор и подготовка контейнерного материала пpи синтезе Универсальным контейнерным материалом считается плавленый кварц. По скольку некоторые практические работы связаны с высоким давлением пара в ампуле, последняя должна быть достаточно прочной. Прочность ампулы увеличивается прямо пропорционально толщине стенок и обратно. пропорционально квадрату диаметра (при прочих равных условиях). Однако эти зависимости часто не соблюдаются при наличии воздушных пузырьков, которые создают так называемую полосчатость кварцевого стекла. Поэтому для ответственных работ (связанных со значительными давлениями) необходимо использовать кварцевый контейнер с минимальным количеством воздушных включений, а еще лучше - кварцевое стекло двойной плавки, практически не содержащее включений.
Однако не все материалы инертны по отношению к кварцу. Так, галлий хорошо смачивая поверхность кварцевого стекла, начинает взаимодействовать с ним уже при 700°С. Многие арсениды после синтеза с трудом отделяются от стенок кварцевой ампулы, поскольку As203, присутствующая в небольших количествах, образует с кварцем легкоплавкие арсеносиликатные стекла. Поэтому в таких случаях рекомендуется проводить синтез или в ампулах с двойными стенками (одна вакуумированная ампула помещается в- другую, которая также вакуумируется). или в графитовых лодочках, введенных в кварцевую ампулу, или предварительно графитизировать внутренние стенки ампулы (например, путем пиролиза паров ацетона, продуваемых через трубку, нагретую до 1000°С). Однако при высоких температурах кварц способен пропускать кислород, поэтому в процессе длительного синтеза графитизированный слой может «выгорать.
При синтезе арсенидов необходимо иметь в виду, что металический мышьяк особой степени чистоты (ОСЧ) при контакте с воздухом легко окисляется, поэтому его измельчение, взвешивание и загрузку в ампулу следует производить в инертной атмосфере или по возможности быстро. При этом не следует измельчать компоненты до высокой степени дисперсности. Оптимальный размер зерна составляет 2-3 мм.
Хотя металлический мышьяк не ядовит, многие ero соединения (летучие или растворимые в воде) чрезвычайно токсичны. Образование таких соединении возможно в процессе синтеза арсенидов (при наличии кислорода образуется As203), при травлении и механической обработке сплавов (за счет гидролиза, например, возможно образование АsНз). и т. п. При взрыве ампулы в процессе синтеза арсенида необходимо экстренно проветрить помещение, а затем провести влажную уборку 10%-ным раствором Na2C03 и водой (в резиновых перчатках) для удаления следов As203, oceвшей на оборудовании.
Все установки для синтеза должны быть снабжены предохранительными металлическими сетками во избежание несчастного случая при возможном взрыве ампулы. При закалке образцов в воде необходимо использовать защитные очки или предохранительную маску из оргстекла. Вскрытие ампул для извлечения слитка следует производить, обернув их во влажное полотенце и одев защитные очки. Разбивают ампулу или в месте отпайки (однотемпературный синтез). или в средней части (двухтемпературный синтез).
Приборы и оборудования.
Настольная диффузионная печь. Модель SV x Fur-RD. Практичное решение для лабораторий и опытных производств.
Описание. Настольная диффузионная печь SVCS создана для применения в научно-исследовательских лабораториях и опытном производстве, сохраняя при этом характерный для полупроводниковой промышленности уровень качества. Система может использоваться для целого ряда различных процессов, благодаря широкой универсальности и количеству доступных опций. Основой системы является сочетание резистивного нагревателя из сплава Kanthal* с вакуумной керамической термоизоляцией и системы управления собственной разработки, обеспечивающей точный и стабильный контроль для высокой воспроизводимости процессов. Для простого взаимодействия с системой управления применяется сенсорный ЖК дисплей с графическим интерфейсом, а для сервиса, обновлений и диагностики используется ПК. Благодаря продуманной конструкции установки достигается легкость таких сервисных процедур, как замена кварцевых частей или ёмкостей с жидкими реагентами. Все газовые линии и компоненты сделаны из нержавеющей стали с электрополировкой внутренних поверхностей для достижения минимального уровня привносимых загрязнений. Применение орбитальной сварки и соединений с торцевым металлическим уплотнением позволяет безопасно использовать различные вещества, в том числе токсичные и горючие.
Технические параметры.
Размер пластин | 2“ - 6“ |
Размер загрузки | до 25 пластин |
Нагреватель | 1 или 3 зоны, проводник из сплава Kanthal* |
Рабочая зона | 300 мм (12“) |
Диапазон температур | от 200 °C до 1 230 °C, ±0,5 °C по рабочей зоне |
Энергопотребление | 20 kW |
Источник питания | 3 фазы, 400 или 480 VAC, 50 или 60 Hz |
Сжатый воздух | 4,8 - 7,6 бар |
Охлаждающая вода | 10 - 15 л/мин |
Вытяжная вентиляция | 210 м3/ч |
Опции | модуль CEM, система EBS, вспомогательное оборудование |
Особенности.
• Атмосферное или вакуумное исполнение
• Малые габариты (стандартная конфигурация: 1900 x 1100 x 680 мм, 95 кг)
• Низкое энергопотребление
• Легкость в эксплуатации и обслуживании
• Нагревательный элемент с 1 или 3 температурными зонами и макс. температурой до 1230 °С
• Современная модульная система управления собственного производства
• До 8 газовых линий и 2 источников пара
• Независимые от системы управления аппаратные блокировки для обеспечения безопасности
• Интеграция вакуумных откачных систем в сотрудничестве с ведущими производителями
|
|
Археология об основании Рима: Новые раскопки проясняют и такой острый дискуссионный вопрос, как дата самого возникновения Рима...
Биохимия спиртового брожения: Основу технологии получения пива составляет спиртовое брожение, - при котором сахар превращается...
Опора деревянной одностоечной и способы укрепление угловых опор: Опоры ВЛ - конструкции, предназначенные для поддерживания проводов на необходимой высоте над землей, водой...
Типы сооружений для обработки осадков: Септиками называются сооружения, в которых одновременно происходят осветление сточной жидкости...
© cyberpedia.su 2017-2024 - Не является автором материалов. Исключительное право сохранено за автором текста.
Если вы не хотите, чтобы данный материал был у нас на сайте, перейдите по ссылке: Нарушение авторских прав. Мы поможем в написании вашей работы!