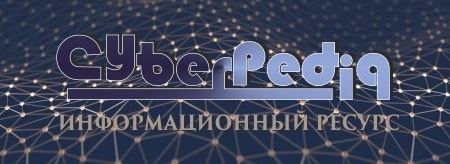
Папиллярные узоры пальцев рук - маркер спортивных способностей: дерматоглифические признаки формируются на 3-5 месяце беременности, не изменяются в течение жизни...
Археология об основании Рима: Новые раскопки проясняют и такой острый дискуссионный вопрос, как дата самого возникновения Рима...
Топ:
Оценка эффективности инструментов коммуникационной политики: Внешние коммуникации - обмен информацией между организацией и её внешней средой...
История развития методов оптимизации: теорема Куна-Таккера, метод Лагранжа, роль выпуклости в оптимизации...
Марксистская теория происхождения государства: По мнению Маркса и Энгельса, в основе развития общества, происходящих в нем изменений лежит...
Интересное:
Искусственное повышение поверхности территории: Варианты искусственного повышения поверхности территории необходимо выбирать на основе анализа следующих характеристик защищаемой территории...
Распространение рака на другие отдаленные от желудка органы: Характерных симптомов рака желудка не существует. Выраженные симптомы появляются, когда опухоль...
Как мы говорим и как мы слушаем: общение можно сравнить с огромным зонтиком, под которым скрыто все...
Дисциплины:
![]() |
![]() |
5.00
из
|
Заказать работу |
|
|
Shipbuilding The finest hours for U.S. shipbuilding were during World War II when 2710 Liberty ships, 531 Victory ships and 525 T-2 tankers were built for the war effort. Through 1945, some 5171 vessels of all types were constructed
to American Bureau of Shipping (ABS) class during the Maritime Commission wartime shipbuilding program. At this time in shipbuilding history, welding was replacing riveting as the main method of assembly.
The importance of welding was emphasized early in the war when President Roosevelt sent a letter to Prime Minister Winston Churchill, who is said to have read it aloud to the members of Britain's House of Commons. The letter read in part, "Here there had been developed a welding technique which enables us to construct standard merchant ships with a speed unequaled in the history of merchant shipping."
The technique the President was referring to was undoubtedly submerged arc welding, which was capable of joining steel plate as much as 20 times faster than any other welding process at that time.
During this period of assimilation, eight Liberty ships were lost due to a problem called brittle fracture. At first, many blamed welding, but history would soon prove that the real cause of brittle fracture was steels that were notch sensitive at operating temperatures. The steel was found to have high sulfur and phosphorus contents. On more than 1400 ships, crack arrestors were used to prevent crack propagation. No crack was known to grow past an arrestor. This safeguard helped reduce casualties from 140 to 20 per month.
The ASME Code
In the late 1920s and early 1930s, the welding of pressure vessels came on the scene. Welding made possible a quantum jump in pressure attainable because the process eliminated the low structural efficiency of the riveted joint. Welding was widely utilized by industry as it strove to increase operating efficiencies by the use of higher pressures and temperatures, all of which meant thick-walled vessels. But before this occurred, a code for fabrication was born from the aftermath of catastrophe.
On April 27, 1865, the steamboat Sultana blew up while transporting 2200 passengers on the Mississippi River. The cause of the catastrophe was the sudden explosion of three of the steamboat's four boilers, and up to 1500 people were killed as a result. Most of the passengers were Union soldiers homeward bound after surviving Confederate prison camps. In another disaster on March 10, 1905, a fire tube boiler in a shoe factory in Brockton, Mass., exploded, killing 58, injuring 117 and causing damages valued at $250,000. These two incidents, and the many others between them, proved there was a need to bring safety to boiler operation. So, a voluntary code of construction went into effect in 1915 - the ASME Boiler Code.
As welding began to be used, a need for nondestructively examining those welds emerged. In the 1920s, inspectors tested welds by tapping them with hammers, then listening to the sound through stethoscopes. A dead sound indicated a defective weld. By 1931, the revised Boiler Code accepted welded vessels judged safe by radiographic testing. By this time, magnetic particle testing was used to detect surface cracks that had been missed radiographic testing. By this time, magnetic particle testing was used to detect surface cracks that had been missed by radiographic inspection. In his history of the ASME Code, A. M. Greene, Jr., referred to the late 1920s and early 1930s as "the great years." It was during this period that fusion welding received widespread acceptance. Nowadays, thousands of individuals who make their living in welding live and breathe the ASME Code every minute of the working day.
|
In 1977, Leonard Zick, chairman of the main committee of the ASME Code, said, "It's more than a code; the related groups make up a safety system. Our main objective is to provide requirements for new construction of pressure-related items that, when followed, will provide safety to those who use them and those who might be affected by their use. "
LNG Tankers
A triumph of the code was the huge aluminum spheres built by General Dynamics in Charleston, S.C. They were built to criteria established by the U.S. Coast Guard and were based on Section VIII, Division 1, of the ASME Code.
At about 2 a.m. on October 2, 1976, the first welded aluminum sphere for a liquefied natural gas tanker was rolled out of a building in Charleston, then moved over to a special
stand for final hydropneumatic testing. It soon passed the test with flying colors. The sphere itself weighed 850 tons and measured 120 ft (36 m) in diameter. Each sphere consisted of more than 100 precisely machined plates, "orange peel" in shape. The plates were gas metal arc welded together using 7036 lb (3166 kg) of filler metal. Total length of the welds on each sphere was 48.6 miles. Completed spheres were barged along the coast and delivered onto steel tankers under construction at General Dynamics' shipyard in Quincy, Mass. This type of LNG tanker was based on the MossRosenberg design from Norway.
At General Dynamics' facility in Charleston, 80% of the metalworking manhours were spent welding. Much of the filler metal deposited in Charleston was 5183 aluminum. The vertical joints were welded using special equipment from Switzerland in which the operator rode in a customdesigned chair alongside the welding arc. At this distance, he was able to monitor the weld and observe the oscillation of the 1Z.5 -mm diameter filler metal. Actual welding was controlled remotely. About 30 weld passes were required for each joint.
The massive equatorial ring was welded outdoors. In this setup, nine heavily machined, curved aluminum extrusions had to be welded together. To do it, 88 GMA weld passes were made from the outside and 60 more from the
inside.
The Alaska Pipeline
Perhaps no single welding event in history ever received so much attention as did the Alaska Pipeline. Crews of seasoned welders braved Alaska's frigid terrain to weld this large-diameter pipeline, from start to finish. At one point, 17,000 people were working on the pipeline - 6% of the total population of Alaska. The entire pipeline only disturbed about 12 square miles of the 586,000 square miles of the state of Alaska.
Welders were called upon to handle and weld a new steel pipe thicker and larger than most of them had ever encountered before, using electrodes also new to most. And, the requirements were the stiffest they had ever seen.
|
The U.S. Department of the Interior and a new pipeline coordinating group representing the state of Alaska instituted some changes. So, the original specifications for field welding were tossed, replaced by much stiffer requirements for weld toughness. Instead of the conventional pipeline welding electrode planned originally for the bulk of field welding, the new requirements required higher quality. The only electrode the engineers could find that met the new requirements was an E8010-G filler metal from Germany, so it was soon flown over by the planeload. Some of the Pipeline Welders Union out of Tulsa, Okla., then welding in Alaska, had used this electrode while working on lines in the North Sea, but most welders were seeing it for the first time.
One of the requirements was 100% X-ray inspection of all welds. The films were processed automatically in vans that traveled alongside the welding crews.
Welders worked inside protective aluminum enclosures intended to protect the weld joint from the wind. Lighting inside the enclosures enabled welders to see what they were doing during Alaska's dark winter.
On the main pipeline, preheat and the heat between weld passes was applied at first by spider-ring burners. Induction heating was used later during construction.
High-Rise Construction
About 30 years ago, steel construction went into orbit. The 100-story John Hancock Center in Chicago and the 110-story twin towers of New York's World Trade Center were under construction. Above ground, the World Trade Center required some 176,000 tons of fabricated structural steel. The Sears Tower came later. Bethlehem Steel Corp. had received orders for 200,000 tons of rolled steel products for the South Mall complex in Albany, N.Y. Allied Structural Steel Co. was reported to have used multiple-electrode gas metal arc welding in the fabrication of the First National Bank of Chicago Building.
In a progress report on the erection of the critical corner pieces for the first 22 floors of the 1107-ft (332-m) high John Hancock Center, an Allied Structural Steel spokesman said various welding processes were being used in that portion of the high-rise building. More than 12,000 tons of structural steel were used in that section. Webs and flanges for each interior H column were made up of A36 steel plate with thicknesses up to 6172 in. (16.5 cm). The long fillet weld s at the web-to-flange contact face s were made using the submerged arc process, while the box consumed in shop fabrication for this building, while 165,000 lb (74,250 kg) of weld metal was consumed during field erection. Weld metal consumption in shop fabrication for the U.S. Steel Building in Pittsburgh, Pa., reached 609,000 lb (274,050 kg).
During this same period, Kaiser Steel Corp. had used the consumable guide version of electroslag welding to deposit 24,000 welds in the Bank of America world headquarters building in San Francisco. At the time, this building was regarded as the tallest earthquake-proof structure ever erected on the West Coast. In terms of welding, one of the most intensive structures built during this period was NASA's Vertical Assembly Building on Merritt Island, Fla. Shop-welded sections for this giant structure consumed 830,000 lb (373,500 kg) of weld metal.
For the World Trade Center, Leslie E. Robertson, a partner in charge of the New York office of Skilling, Helle, Christiansen, Robertson, said a computer was used to produce the drawing lists, beam schedules, column details and all schedules for exterior wall panels. Millions of IBM cards were then sent to every fabricator. These cards gave fabricators the width, length, thickness and grade of steel of every plate and section in all of the columns and panels. "In addition," he said, "the fabricators are given all of the requirements of every weld needed to make up the columns and panels. Many of these cards are used as equable to the production of drawings. They are sent directly from the designer to the fabricators. Draftsmen never become involved."
|
Elsewhere in New York City, Leo Plofker, a partner in one of the city's leading design engineering firms, extensively used welding in design. Among Plofker's achievements are the Pan-Am Building and the all-welded, 52-story office building known as 140 Broadway. "Our decision to make extensive use of welding is strictly based on economics," he said. "Welded design results in savings in steel. Field welding can cause some problems, but they are not too serious as long as you maintain control over the welders and you insist that qualified personnel be employed to perform nondestructive testing of the welds."
After-reading activity
Find the following sentences in the text and express in your own words what they mean:
1. Nowadays, thousands of individuals who make their living in welding live and breathe the ASME Code every minute of the working day.
2. A. M. Greene, Jr. referred to the late 1920s and early 1930s as "the great years."
3. About 30 years ago, steel construction went into orbit.
4. Welded design results in savings in steel.
5. In the late 1920s and early 1930s, the welding of pressure vessels came on the scene.
6. In 1977, Leonard Zick, chairman of the main committee of the ASME Code, said, “ It's more than a code …;”
Fill in the blanks:
1. Before welding, … was the main assembly method in constructing standard merchant ships.
2. … was the fastest welding process for joining steel plate in 1940s.
3. The first quality inspectors used … to tap the metal and hear the noise.
4. The use of higher pressures and temperatures made it necessary to construct … vessels.
5. Magnetic particle testing was more efficient than radiographic testing in detecting ….
6. The use of IBM cards during the construction of the World Trade Center made it possible not to involve ….
7. In case of X- ray inspection one has to process ….
Speaking
True or false?
1. In 1940s all the welding techniques known were fast enough to produce ships.
2. Americans lost a lot of ships because of problems associated with welding. 3. Introduction of welding into the high pressure and temperature structures construction made it possible to make a great advance in industry. 4. The ASME Code was introduced to ensure safety in boiler production.
5. Draftsmen played an important part in the construction of the World Trade Center.
PART 3. WELDING PROCESSES & EQUIPMENT
Lead-in
You already know what kind of training you should go through to become welder. Among other things, a welder should know about processes which are similar to welding. Look through the vocabulary and the text below and say what the main difference between welding and related metal joining processes is.
Vocabulary
soldering | пайка; пайка мягким (легкоплавким) припоем |
tinning | лужение; облуживание |
leading | свинцевание |
brazing | 1) пайка твердым припоем (из меди и цинка) 2) покрытие медью |
sweat | паять, запаивать, припаивать (in, on) |
gimmick | 1) сложное приспособление Syn: gadget 2) а) прием, трюк, уловка, ухищрение, хитрость |
filler metal | присадочный металл, присадка |
filler rod | присадочный пруток; присадочная проволока |
heat buildup | теплообразование, тепловведение |
heat distortion | деформация (материала) из-за теплового нагрева |
stitch welding | прерывистая шовная сварка; точечная сварка перекрывающимися точками; автоматическая точечная сварка |
|
Reading
Text 1. Introduction to Welding Processes & Equipment
Among the first things a new welder needs to understand, is what the different kinds of welding processes and equipment are, and their application.
A quick rundown:
Terms:
Soldering: Bonding by melting a soft metal to the surface of pieces to be joined. Low temperature. Good for joining dissimilar materials. Most common solders are lead-tin alloys.
Tinning: A soldering process, where the surface of a metal is coated with solder.
Leading: A form of soldering, solder is used to fill in the surface of metal. Brazing: Similar to soldering, but uses a higher temperature to fuse the filler metal to the work pieces. Stronger bond. (Includes "Silver Soldering") Work heated to pre-melt temperatures.
Welding: Joining 2 similar work pieces by melting them together, usually with an additional filler rod of some sort to take up space. Materials must be similar.
Cutting: Work is heated to melting point and beyond, and "cut" by oxidizing metal. (Literally burning it away).
Shield: A barrier to keep oxygen away from heated work to prevent oxidation. Includes chemical coatings called flux (liquids, pastes, solids, which may be vaporized into a barrier gas when heated), and inert gasses.
Oxidation of the surfaces will prevent proper bonding of the metals.
Gas Welding
Uses Flame from burning gas to create welding heat.
Propane torch: (Soldering, heating) Good for sweating pipes, starting fires, and spending hours trying to heat frozen bolts, while the surrounding metal gets just as hot.
Oxyacetylene torch: (Cutting, welding, brazing, soldering, leading) Most universal and useful welding tool. (Uses Acetylene gas and Oxygen for hot flame) With the right bits, rod, and technique, you can weld almost anything. Good for cutting anything from sheet metal to the turret off a tank, lead filling, brazing (a sort of hard soldering process) welding plate, welding sheet metal, welding aluminium, heating frozen bolts, or alternately cutting them off, drilling holes in plate, welding cast iron, shrinking and forming steel, and can double as a flame thrower in a pinch. Drawbacks are: Overheating of some types of work, harder to control quality of some processes.
Oxy-propane: (Soldering, brazing, heating) A cheap compromise between low cost and portable propane, and Oxy-Acetylene. Better than the former, not as good as the latter.
Arc welding
Uses an electric arc to create welding heat.
Basic AC & DC arc welders (AC is cheaper) Uses flux coated steel (or other) rods of various types for different jobs. Makes some of the best welds on heavy gauge steels and cast iron. Cutting rods can make clean holes through thick stock, and are about the only thing which can cut Kryptonite bike locks. Very difficult to weld thin metals. You can also get a carbon arc torch to use on an arc welder to braze. Eastwood's "stitch" welder is a gimmick used on an arc welder to buzz the rod in and out, which may help on thinner stock. (learning how to weld better, or going to a different process is usually a better idea.)
MIG (Metal Inert Gas): A DC arc welding process which uses filler metal fed in the form of a spool of thin wire, shielded by flow of inert gas (He, Argon) instead of flux used in Arc. Very fast, much easier than Arc Welding, with less heat buildup. Very good for sheet metal, due to minimal heat distortion. Harder to weld thick stock, as welds are weaker due to poorer penetration. The modern choice for steel body work, it can also be used for Aluminium with Argon as the shield gas.
TIG (Tungsten Inert Gas): A high frequency AC arc process which uses a tungsten electrode shielded by an inert gas to create a fine, controllable torch. Uses a separate filler rod, as in Oxy-Acetylene welding. Capable of welding very thin metals. About the best process for Aluminium, Stainless steel, and other exotic stuff.
Resistance welding: includes spot welding: Uses the heat generated by electricity flowing through work to melt and fuse. i.e.- put an electrode on either side of 2 overlapped sheets of steel, turn on power. Metal in between heats up, and melts together. An old favorite for assembling car bodies.
Plasma Cutters: Not a welder, but related. A high voltage arc is used to superheat and ionize a stream of air to the "plasma" state. The stream of plasma makes a rapid, clean, narrow cut with minimal heating of the work piece.
|
After-reading activity
Answer the following questions:
1. What is the main difference between soldering and brazing?
2. What is used by welders to prevent oxidation?
3. What makes soldering advantageous before welding?
4. What welding processes are suitable for welding thin/thick metal plates?
5. What makes plasma cutting better than gas cutting?
Vocabulary
coalescence | соединение, слипание; сращение |
filler material | присадочный материал |
molten pool | ванна расплавленного металла, сварочная ванна |
gas flame | газовое пламя |
solid-phase | твёрдая фаза |
ultrasonic | ультразвуковой |
friction | трение |
furnace печь
diffusion 1) рассеивание
2) диффузия
high-current сильноточный
low-voltage низковольтный, низкого напряжения discharge разряд
arc column столб дуги
direct current (dc) постоянный ток
alternating current переменный ток
(ac)
layer слой; пласт; ряд
molten-metal капля жидкого металла droplet
flux флюс
inert atmosphere инертная среда annulus тех. узкое кольцо (зазор и т. п.)
torch сварочная горелка (для автоматической сварки –
головка)
base metal основной металл grain зерно
precipitation осаждение
residual stress остаточное напряжение
Find the English equivalents for the following words and word combinations: источник тепла, расплавленный металл, необходимый размер, сварной шов, не нагретый металл, механические свойства, максимум температуры, защищать поверхности, быстрое охлаждение, осуществлять контроль, препятствовать окислению, вступать в химическую реакцию, термообработка, бомбардировка электронами, зона термического [теплового] воздействия, общая потребляемая энергия
Reading
|
|
Биохимия спиртового брожения: Основу технологии получения пива составляет спиртовое брожение, - при котором сахар превращается...
Двойное оплодотворение у цветковых растений: Оплодотворение - это процесс слияния мужской и женской половых клеток с образованием зиготы...
Таксономические единицы (категории) растений: Каждая система классификации состоит из определённых соподчиненных друг другу...
Типы сооружений для обработки осадков: Септиками называются сооружения, в которых одновременно происходят осветление сточной жидкости...
© cyberpedia.su 2017-2024 - Не является автором материалов. Исключительное право сохранено за автором текста.
Если вы не хотите, чтобы данный материал был у нас на сайте, перейдите по ссылке: Нарушение авторских прав. Мы поможем в написании вашей работы!