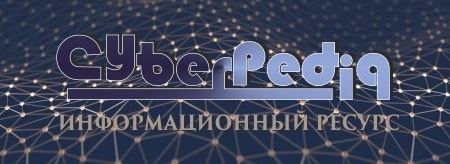
Эмиссия газов от очистных сооружений канализации: В последние годы внимание мирового сообщества сосредоточено на экологических проблемах...
Индивидуальные и групповые автопоилки: для животных. Схемы и конструкции...
Топ:
Оснащения врачебно-сестринской бригады.
Марксистская теория происхождения государства: По мнению Маркса и Энгельса, в основе развития общества, происходящих в нем изменений лежит...
Интересное:
Распространение рака на другие отдаленные от желудка органы: Характерных симптомов рака желудка не существует. Выраженные симптомы появляются, когда опухоль...
Наиболее распространенные виды рака: Раковая опухоль — это самостоятельное новообразование, которое может возникнуть и от повышенного давления...
Средства для ингаляционного наркоза: Наркоз наступает в результате вдыхания (ингаляции) средств, которое осуществляют или с помощью маски...
Дисциплины:
![]() |
![]() |
5.00
из
|
Заказать работу |
|
|
Шпоночным называется соединение соосных деталей с помощью шпонки
Шпонка — специальная деталь, размещаемая в пазах вала и ступицы. В машиностроении применяют стандартизованные призматические, сегментные, клиновые, цилиндрические шпонки. Достоинства: простота конструкции, невысокая стоимости изготовления, удобство сборки и разборки.
Призматические шпонки используются в конструкциях наиболее часто. Они имеют прямоугольное сечение с отношением высоты к ширине h / b для валов диаметром до 22 мм - h / b = 1 а для валов больших диаметров - до h / b = 0,5. Материал шпонок — чистотянутая сталь с пределом точности σВ≥600 МПа. Сегментные шпонки используют в основном на малонагруженных участках вала.
137 Критерии работоспособности и расчет соединений.(шпонка)
Шпоночные соединения выходят из строя из-за смятия рабочих граней. Возможен также и срез шпонок. Прочностную надежность соединений оценивают по напряжениям смятия σсм на рабочих гранях. где Т - вращающий момент; lP - рабочая длина шпонки; t 2 = 0,4 h - глубина врезания шпонки в ступицу; σсм - допускаемое напряжение на смятие. Рабочую длину шпонки ℓр можно определить из соотношения lp=2T/(dt2[σсм]). Проверку прочности шпонок на срез обычно не производят. Если условие прочности не выполняется, то используют две шпонки, установленные под углом 120 или 180°.
ШПОНОЧНЫЕ И ЗУБЧАТЫЕ (ШЛИЦЕВЫЕ) СОЕДИНЕНИЯ
Шпоночные и зубчатые соединения служат для закрепления деталей на осях и валах. Такими деталями являются шкивы, зубчатые колеса, муфты, маховики, кулачки и т. д. Соединения нагружаются в основном вращающим моментом.
§ 6.1. Шпоночные соединения
Все основные виды шпонок можно разделить на клиновые и призматические. Первая группа шпонок образует напряженные, а вторая — ненапряженные соединения. Размеры шпонок и допуски на них стандартизованы.
|
Соединение клиновыми шпонками (например, врезной клиновой шпонкой; рис. 6.1) характеризуется свободной посадкой ступицы на вал (с зазором); расположением шпонки в пазе с зазорами по боковым граням (рабочими являются широкие грани шпонки); передачей вращающего момента от вала к ступице в основном силами трения, которые образуются в соединении от запрессовки шпонки. Запрессовка шпонки смещает центры вала и ступицы на некоторое значение Δ, равное половине зазора посадки и деформации деталей. Это смещение вызывает дисбаланс и неблагоприятно сказывается на работе механизма при больших частотах вращения.
Клиновая форма шпонки может вызвать перекос детали, при котором ее торцовая плоскость не будет перпендикулярна оси вала. Обработка паза в ступице с уклоном, равным уклону шпонки, создает дополнительные технологические трудности и часто требует индивидуальной пригонки шпонки по пазу. Такая пригонка совершенно недопустима в условиях массового производства. Эти недостатки послужили причиной того, что применение клиновых шпонок резко сократилось в условиях современного производства. Значительное сокращение применения клиновых щпонок позволяет не рассматривать в настоящей курсе их конструктивные разновидности и расчет на прочность
71. Штифтовые и клеммовые соединения.
Штифтовые соединения
Образуются совместным сверлением соединяемых деталей и установкой в отверстие с натягом специальных цилиндрических или конических штифтов.
Соединения предназначены для точного взаимного фиксирования деталей, а также для передачи небольших нагрузок.
Конструкции штифтов многообразны. Известны цилиндрические (а,б), конические (в,г,д), цилиндрические пружинные разрезные (е), просечённые цилиндрические, конические и др. (ж,з,и,к), простые, забиваемые в отверстия (б,в), выбиваемые из сквозных отверстий с другой стороны (гладкие, с насечками и канавками, пружинные, вальцованные из ленты, снабжённые резьбой для закрепления или извлечения (д) и т.д. Применяются специальные срезаемые штифты, служащие предохранителями.
|
Гладкие штифты выполняют из стали 45 и А12, штифты с канавками и пружинные – из пружинной стали.
При закреплении колёс на валу штифты передают как вращающий момент, так и осевое усилие.
Достоинства штифтовых соединений:
простота конструкции;
простота монтажа-демонтажа;
точное центрирование деталей благодаря посадке с натягом;
работа в роли предохранителя, особенно при креплении колёс к валу.
Недостатком штифтовых соединений является ослабление соединяемых деталей отверстием.
Клеммовые соединения применяют в том случае, когда место закрепления рычага на валу непостоянно.
Вследствие действия силы Р, сжимающей клеммы и растягивающей болт, между поверхностями ступицы рычага и вала возникает сила трения, создаваемое затяжкой болта. Затяжка болта должна быть такой, чтобы момент трения равнялся внешнему моменту, или для надежности был бы больше, обычно на 20%.
Приближенно усилие Р кгс, сжимающее клеммы и растягивающее болт, определяют по формулам:
;
где Q - усилие на рычаге, кгс; L - длина рычага, см; d - диаметр вала, см; l - расстояние от оси болта до центра вала, см; f - коэффициент трения; F - площадь его сечения болт. - рабочее напряжение растяжения
72. Корпусные детали механизмов. Назначение.
159 Общие сведения о деталях корпусов. Детали корпусов. Являются наиболее металлоемкими и трудоемкими. Их рациональное проектирование дает значительные эффекты (экономические, эксплуатационные и др.).
Конструкции и материалы.
Корпус редуктора (вместе с крышкой) имеет сложную форму и подвержен действию пространственных нагрузок. Расчет деталей корпуса на прочность и жесткость возможен лишь методами теории упругости.Конструкции деталей корпусов сложны и разнообразны. На практике их конструируют по прототипам. Невысокая нагруженность корпуса редуктора позволяет изготавливать его тонкостенным, а жесткость обеспечивать с помощью ребер и соответствующих утолщений. Для облегчения изготовления корпуса выполняют с разъемом по плоскости, проходящей через оси валов. Экономически целесообразный способ изготовления - литье, а материал - серый чугун. Корпуса могут отливаться из сталей, алюминиевых и магниевых сплавов. Стыковые поверхности корпуса и отверстия под подшипники обрабатывают на станках.
|
Для защиты от коррозии и в декоративных целях детали корпусов покрывают красками и др. покрытиями.
Конструкция и материалы.
Конструкции и материалы.
Корпус редуктора (вместе с крышкой) имеет сложную форму и подвержен действию пространственных нагрузок. Расчет деталей корпуса на прочность и жесткость возможен лишь методами теории упругости.Конструкции деталей корпусов сложны и разнообразны. На практике их конструируют по прототипам. Невысокая нагруженность корпуса редуктора позволяет изготавливать его тонкостенным, а жесткость обеспечивать с помощью ребер и соответствующих утолщений. Для облегчения изготовления корпуса выполняют с разъемом по плоскости, проходящей через оси валов. Экономически целесообразный способ изготовления - литье, а материал - серый чугун. Корпуса могут отливаться из сталей, алюминиевых и магниевых сплавов. Стыковые поверхности корпуса и отверстия под подшипники обрабатывают на станках.
Для защиты от коррозии и в декоративных целях детали корпусов покрывают красками и др. покрытиями.
73. Требования, предъявляемые к корпусным деталям. Классификация. Конструкции.
От конструкции корпусных деталей во многом зависит точность, жесткость и виброустойчивость всей машины. Поэтому к ним предъявляются соответствующие требования достаточно большой жесткости и виброустойчивости, сохранения точности, технологичности конструкции, минимального веса, удобства расположения компонуемых сборочных единиц и механизмов и эстетики.
Отконструкции корпусных деталей во многом зависит точность, жесткость и виброустойчивость всего станка.
Отконструкции корпусных деталей и узлов во многом зависит точность, жесткость и виброустойчивость всего станка. К корпусным деталям станка, предъявляются следующие требования: высокая жесткость и виброустойчивость, длительное сохранение точности, технологичность конструкции, минимально возможный вес, удобное взаимное расположение отдельных узлов, наличие резервуаров для смазки и охлаждения и нИ ш для электроаппаратуры. [ 8 ]
|
Есликонструкция корпусной детали такова, что базовая плоскость имеет недостаточную протяженность, или на ней отсутствуют базовые отверстия, следует создать дополнительные технологические площадки с отверстиями на них для обеспечения обработки детали от этих баз. В качестве черновой технологической базы при подготовке основной базы рекомендуется использовать поверхности, которые должны быть наиболее точными по ТУ. [ 9 ]
Технологичностьконструкции корпусных деталей имеет особенное значение, так как от этого в значительной степени зависит трудоемкость их изготовления. Чтобы снизить трудоемкость изготовления корпусных деталей и повысить их качество, необходимо при проектировании обеспечить следующие технологические требования.
Классификация корпусных деталей:
1.
-По степени конструктивной сложности
1.
простые, не имеющие внутренних перегородок, рёбер и приливов;
2.
сложные.
2.
-По сообщённости внутреннего пространства с внешней средой
1.
закрытые, внутренняя полость которых, как во время работы, так и в неработающем состоянии, полностью изолирована от внешней среды;
2.
полузакрытые, внутренняя полость которых может сообщаться с внешней средой в отдельные моменты (часть времени) работы машины (механизма) или в неработающем состоянии;
3.
открытые, внутренняя полость которых постоянно сообщена с внешней средой.
3.
По пригодности для хранения эксплуатационного запаса смазочных материалов -
3.1) сухие корпуса, не предназначенные для хранения эксплуатационного запаса смазочных материалов;
3.2) маслонаполненные, ёмкость которых достаточна для хранения эксплуатационного запаса смазочных материалов.
4) По основному материалу, из которого изготовлены детали корпуса -
4.1) металлические (чугун, сталь литая, сталь сварная, лёгкие сплавы - алюминиево-кремниевые, алюминиево-магниевые);
4.2) неметаллические (пластики, дерево, фанера).
Серый чугун (СЧ15, СЧ20) является одним из самых дешёвых и распространённых материалов для изготовления корпусных деталей. Вместе с тем чугунные корпусные детали имеют наибольшую массу по сравнению с аналогичными деталями, выполненными из других материалов. Поэтому из чугуна изготавливают корпуса стационарных машин и механизмов, устанавливаемых на фундаменте.
74. Упругие элементы. Назначение. Конструкци и.
Упругими элементами называют детали машин, работа которых основана на способности изменять свою форму под воздействием внешней нагрузки и восстанавливать ее в первоначальном виде после снятия этой нагрузки.
В технических устройствах используется большое число различных упругих элементов, но наиболее распространены следующие три типа элементов, выполненных как правило из металла:
Пружины (рис. 16.1, а…м) – упругие элементы, предназначенные для создания (восприятия) сосредоточенной силовой нагрузки.
Торсионы (рис. 16.1, н) - упругие элементы, выполненные обычно в форме вала и предназначенные для создания (восприятия) сосредоточенной моментной нагрузки.
Мембраны - упругие элементы, предназначенные для создания (восприятия) распределенной по их поверхности силовой нагрузки (давления).
|
Пружины и упругие элементы используют в конструкциях в качестве виброизолирующих, амортизирующих, аккумулирующих, натяжных, динамометрических и других устройств.
Классификация пружин: По виду воспринимаемой нагрузки различают:пружины растяжения, сжатия, кручения и изгиба.
По геометрической форме их называют: винтовыми, спиральными, прямыми и др.
В зависимости от назначения пружины бывают: силовыми (аккумуляторы энергии или движители), измерительными (упругие чувствительные элементы), амортизирующими и т. д.
В машиностроении наиболее распространены
винтовые цилиндрические пружины растяжения, сжатия и кручения.
Реже применяют специальные пружины:
тарельчатые и кольцевые – сжатия,
спиральные и стержневые- кручения; листовые (рессоры). пружины а - растяжения; б - сжатия; в - кручения; г - фасонные
а - тарельчатая; б- кольцевая; в - спиральная; г - стержневая; д - рессора
|
|
Общие условия выбора системы дренажа: Система дренажа выбирается в зависимости от характера защищаемого...
Семя – орган полового размножения и расселения растений: наружи у семян имеется плотный покров – кожура...
Археология об основании Рима: Новые раскопки проясняют и такой острый дискуссионный вопрос, как дата самого возникновения Рима...
Историки об Елизавете Петровне: Елизавета попала между двумя встречными культурными течениями, воспитывалась среди новых европейских веяний и преданий...
© cyberpedia.su 2017-2024 - Не является автором материалов. Исключительное право сохранено за автором текста.
Если вы не хотите, чтобы данный материал был у нас на сайте, перейдите по ссылке: Нарушение авторских прав. Мы поможем в написании вашей работы!