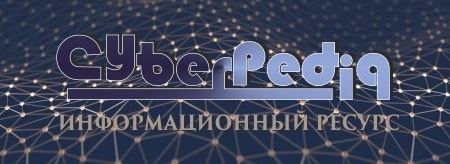
Археология об основании Рима: Новые раскопки проясняют и такой острый дискуссионный вопрос, как дата самого возникновения Рима...
Таксономические единицы (категории) растений: Каждая система классификации состоит из определённых соподчиненных друг другу...
Топ:
Характеристика АТП и сварочно-жестяницкого участка: Транспорт в настоящее время является одной из важнейших отраслей народного...
Установка замедленного коксования: Чем выше температура и ниже давление, тем место разрыва углеродной цепи всё больше смещается к её концу и значительно возрастает...
Оценка эффективности инструментов коммуникационной политики: Внешние коммуникации - обмен информацией между организацией и её внешней средой...
Интересное:
Средства для ингаляционного наркоза: Наркоз наступает в результате вдыхания (ингаляции) средств, которое осуществляют или с помощью маски...
Что нужно делать при лейкемии: Прежде всего, необходимо выяснить, не страдаете ли вы каким-либо душевным недугом...
Лечение прогрессирующих форм рака: Одним из наиболее важных достижений экспериментальной химиотерапии опухолей, начатой в 60-х и реализованной в 70-х годах, является...
Дисциплины:
![]() |
![]() |
5.00
из
|
Заказать работу |
|
|
Общая часть
2.1 Способы производства клинкера
![]() |
Производство портландцемента складывается, в основном, из следующих
операций: добычи сырья; приготовления сырьевой смеси, состоящего из дробления, помола и ее гомогенизации; обжига сырьевой смеси; помола обожженного продукта (клинкера) в тонкий порошок.
Существует три способа производства – мокрый, сухой и комбинированный.
При мокром способе сырьевую смесь измельчают совместно с водой. Получаемая сметанообразная жидкость – шлам – содержит 32-45% воды. По сухому способу сырьевые материалы предварительно высушивают, а затем совместно измельчают. Полученный тонкий порошок называют сырьевой мукой. При комбинированном способе производства сырьевая смесь готовится в виде шлама, полученного при обычном мокром способе производства, подвергается обезвоживанию в фильтр - прессах и вакуум-фильтрах до влажности 16-20%, грануляции, а затем обезвоживается в печах, работающих по сухому способу производства.
Способ производства выбирают в зависимости от технических и технико-
экономических факторов: свойств сырья, его однородности и влажности, наличия достаточной топливной базы и др.
На цементных заводах, работающих по мокрому способу, в качестве
сырьевых материалов для производства портландцементного клинкера часто используют мягкий глинистый и твердый карбонатный компоненты. Так как глинистый компонент мягкий, то его предварительное измельчение осуществляют в мельнице самоизмельчения «Гидрофол», а твердый карбонатный компонент дробят в 1-2 стадии в щековых дробилках. Глинистый шлам и измельченный известняк загружают в мельницу тонкого помола сырья в определенном соотношении, куда также направляют корректирующие добавки. Чтобы получить шлам заданного химического состава его корректируют в шлам - бассейнах или в потоке. Если и глинистый и карбонатный компоненты мягкие, то предварительное измельчение ведут в мельнице самоизмельчения «Гидрофол», а тонкий помол также в сырьевых трубных мельницах. Если оба компонента твердые, то предварительное их измельчают в дробилках, а тонкий помол также в сырьевой трубной мельнице. Откорректированный сырьевой шлам подают во вращающуюся печь на обжиг. При мокром способе производства для обжига клинкера используют длинные вращающиеся печи со встроенными теплообменными устройствами. Из печи клинкер поступает в холодильник, затем в силосы. Клинкер совместно с гипсом и при необходимости с добавками подаётся на помол, в результате которого получается готовый портландцемент.
|
При сухом способе производства портландцемента выбор схемы также
зависит от физических и химических свойств сырья. Если в качестве сырья используют твердый известняк и мягкую глину, то известняк после дробления и
глину направляют для предварительного измельчения в мельницу самоизмельчения «Аэрофол». Далее помол и сушку сырьевой смеси целесообразно вести одновременно в трубной сепараторной мельнице. Предварительное измельчение материалов и их сушка возможна совместно в дробилках-сушилках, аэросушилках и т.д., или сушку проводят в сушильном барабане, после чего материал измельчают. Сырьевую муку, выходящую из мельниц тонкого измельчения, доводят до заданного химического состава в
специальных смесительных силосах. Откорректированная сырьевая смесь поступает в систему циклонных теплообменников. Из циклонов материал подается в печь. Полученный клинкер охлаждается, отправляется на склад. Клинкер, гипс и при необходимости добавки подвергают помолу, получается портландцемент.
При комбинированном способе производства сырьевая смесь, как и при
|
мокром, готовится в виде шлама влажностью 35-40%. После корректирования шлам поступает в вакуум-фильтр или пресс-фильтр, где обезвоживается до влажности 16-20%. Образующийся при этом «сухарь» подсушивается и дробится
в сушилках-дробилках. Сырьевая смесь подаётся на обжиг, который осуществляется во вращающихся печах сухого способа. Все остальные операции производства портландцемента по этому способу не отличаются от соответствующих операций производства по мокрому и сухому способам.
2.2 Обоснование выбора вращающейся печи сухого способа
производства клинкера
В печах с циклонными теплообменниками можно обжигать при сухом способе производства как пластичные, так и не пластичные материалы без увлажнения и грануляции.
Достоинством печей с циклонными теплообменниками является применение порошкообразной сухой сырьевой смеси, низкий удельный расход тепла, высокая удельная производительность [45 -50 кг/м3], возможность достижения высокой единичной мощности установки, равной 5000 кг/сутки. Клинкера и болей, отсутствие движущихся частей, относительно простая конструкция.
Печи для обжига сухой сырьевой смеси при равной производительности примерно в двое короче печей для обжига шлама.
Это объясняется тем, что часть процессов из печи выносится в запечные теплообменные устройства.
Основными преимуществами печей с циклонными теплообменниками (по сравнению с печами других типов) являются:
- отсутствие в запечных теплообменниках движущихся частей;
- высокий коэффициент использования (до 95 %);
- возможность использования непластичного, трудногранулируемого сырья и снижения затрат сырья на испарение влаги;
- возможность использования шахты более грубого помола (остаток на сите с сеткой № 0085 до 20%);
- наиболее низкий расход тепла [до 3,05 мДж/ 730 ккал на 1кг клинкера] и самый высокий тепловой К.П.Д. (55- 60%);
- высокий съём клинкера вследствие хорошей (равномерной) предварительной тепловой обработки сырьевой смеси.
3 Технологическая часть
3.1 Характеристика топлива
Затраты на топливо в цементной промышленности очень высоки. Они
составляют до 40% себестоимости клинкера.
|
В цементной промышленности используют газообразное, жидкое и твёрдое
топливо. В качестве газообразного топлива применяют природный газ, смесь природного газа с подземной газификацией, а также коксовый газ – продукт коксования каменных углей. Наибольшее распространение получили природные топливные газы, требования к которым регламентированы ГОСТ 5542-78. В зависимости от месторождения содержание метана в природных газах составляет 80-99%, теплота сгорания 32-39 мДж/м3, плотность 0,72-0,85 кг/м3.
Газ поступает на цементное предприятие от газораспределительной станции
под давлением около 0,6 МПа, на газораспределительном пункте (ГРП), его давление снижается до 0,25%-0,3 МПа. От ГРП газ по специальным газопроводам транспортируют к местам его потребления.
Газовое пламя имеет меньшую светимость, что обуславливает повышение
расхода теплоты, тем не менее, это дешевый удобный вид транспорта. Газ не требует устройств для хранения, не дает отходов при сгорании, не загрязняет атмосферу. Применение газа упрощает автоматизацию процесса сжигания топлива и технологию производства клинкера. Постоянство химического состава и теплоты сгорания газа обеспечивает равномерность режима обжига и стабильность работы печи. При этом повышается стойкость футеровки, возрастает коэффициент использования печи, следовательно, увеличивается выпуск продукции. Газообразное топливо не требует специальных подготовок перед его сжиганием, что сокращает капитальные расходы.
3.2 Технологический и теплотехнический режим вращающейся печи
с циклонными теплообменниками
В основу работы печей с циклонными теплообменниками положен принцип теплообмена между отходящими газами и сырьевой мукой во взвешенном состоянии. Передача теплоты во взвешенном состоянии гарантирует быстроту, и равномерность нагревания смеси. Откорректированная сырьевая мука поступает в систему циклонных теплообменников. Отходящие из вращающейся печи газы с температурой 900-1000˚С через переходную шахту по газоходу движутся в циклонный теплообменник IV ступени, а затем последовательно проходят циклонные теплообменники ΙΙΙ, ΙΙ и Ι ступени, пылеулавливающее устройство и через дымовую трубу выходят в атмосферу. В газоходах циклонных теплообменников скорость газов значительно выше скорости движения частиц сырьевой муки. Поэтому подаваемая в газоход между Ι и ΙΙ ступенью циклонов сырьевая мука увлекается потоком газов в циклон Ι ступени, где материал подогревается, а газы соответственно охлаждаются. Поскольку диаметр циклона на много больше диаметра газохода, то скорость газового потока в циклоне резко снижается, и частицы сырьевой муки выпадают из газового потока. Осевший материал через затвор - мигалку поступает в газоход, соединяющий ΙΙ и ΙΙΙ ступени а из него выносится газами во ΙΙ ступень. В такой последовательности сырьевая мука опускается вниз, проходя поочерёдно циклоны и газоходы всех ступеней, начиная от относительно холодной (Ι) и кончая горячей (IV).
|
Из циклонного теплообменника выходит сырьевая смесь со скоростью декарбонизации не более 35%. Завершение процесса декарбонизации требует относительно долгого времени. Длительность обжига может быть сокращена при использовании трёхступенчатого обжига. Для этого между теплообменником и печью встраивают реактор - декарбонизатор, представляющий собой печь с форсункой, в вихревом потоке которого происходит сжигание части топлива и декарбонизация сырьевой смеси. Из циклонного теплообменника сырьевая мука с температурой 720- 750˚С поступает в декарбонизатор. Сюда же, тангенциально, через вихревую камеру подаётся смесь воздуха с топливом. Поток движется вдоль стенок вверх по спирали в камеру реакции. За время подъёма до выпускного
газохода смесь газов и твёрдых частиц совершает несколько оборотов вокруг оси декарбонизатора. Вследствие вихревого движения вдоль вертикальной оси реактора, возникает зона разряжения. В эту зону всасываются сырьевая мука и топливо, они смешиваются с газами и диспиргируются. Теплота, выделяющаяся при сгорании топлива, немедленно передаётся частицами сырьевой муки, которые нагреваются до 920 - 970˚С. При этом в декарбонизаторе не возникает светящегося факела горения, который виден во вращающей печи. Здесь около 90% теплоты передаётся конвекцией, и только около 10% - излучение. Далее сырьевая мука поступает во вращающуюся печь.
Время пребывания сырьевой муки в циклонных теплообменниках не превышает 25- 30 секунд. За короткое время сырьевая мука нагревается до 700- 800˚С, полностью дегидратируется и 25- 35% декарбонизируется. Поэтому в короткой печи с циклонными теплообменниками отсутствуют зоны испарения, подогрева и сокращена зона декарбонизации. В зоне декарбонизации происходит разложение СаСО3 и МgСО3:
|
МgСО3→МgО + СО2
СаСО3→ СаО + СО2
Эта зона наиболее напряжена в тепловом отношении, так как процесс разложения известняка требует больших количеств тепла. Температура материала в этой зоне 900 - 1200˚С.
При дальнейшем повышении температуры протекает реакция в твёрдой фазе с образованием силикатов, алюминатов, ферритов кальция. Эти реакции протекают с выделением тепла. Они идут в конце зоны кальцинирования и на небольшом протяжении за ней:
СаО + Fe2O3 → CaO· Fe2O3
CaO + Al2O3 → CaO · Al2O3
CаО · Al2O3 + 2СаО → 3CаО · Al2O3
3CаО · Al2O3 + CaO· Fe2O3→ 4CаО · Al2O3· Fe2O3
2СаО + SiO2 → 2CаО · SiO2
Часть печи, где происходят эти реакции, называют экзотермической зоной. Эта зона занимает 7 - 10% длины печи.
Далее материал поступает в зону спекания. Здесь он частично плавится и образуется жидкая фаза. Максимальная температура в зоне спекания 1420 - 1470˚С или в среднем приблизительно 1450˚С. Спекание начинается уже при температуре 1300˚С, продолжается при подъёме температуры материала до 1450˚С и при охлаждении его снова до 1300˚С. Тепло здесь передаётся излучением. Время пребывания материала в зоне спекания 15 - 30 минут при температуре 1450˚С и выходе гранул клинкера 10 – 50 мм. Повышение температуры обжига до 1600˚С позволяет завершить процесс клинкерообразования за 5 - 10 минут. Зона спекания занимает 10 - 15% длины печи.
Из зоны спекания материал поступает в зону охлаждения. Температура материала снижается до 1200 - 1000˚С. Часть жидкой фазы при этом кристаллизуется с выделением клинкерных минералов, а часть затвердевает в виде стекла. Зона охлаждения занимает 2- 4% длины печи.
Температуры выходящих из печи газов 1050 - 1150˚С, температура отходящих газов перед дымососом доходит до 300˚С. Разряжение в газоходах до 60 МПа и более.
3.3 Конструкция и принцип действия вращающейся печи с циклонными теплообменниками
Вращающиеся печи с циклонными теплообменниками предложены
Мюллером и впервые построены в ФРГ в 1950 году. Вращающиеся печи сухого способа производства различаются по размерам и виду запечных устройств.
Вращающаяся печь представляет собой наклонный стальной барабан, в загрузочную часть которого подаётся сырьевая мука. Со стороны выгрузочной части (головки) печи через форсунки вдувается топливо. Поступивший в печь материал вследствие вращения и наклонного положения обжигаемого барабана движется по направлению к головке печи. Материалы газа движутся по принципу противотока.
Обжигательный барабан вращающейся печи сваривается из отдельных обечаек, изготовленных из стального листа толщиной 24- 50мм. Внутри барабан выложен огнеупорной футеровкой, предохраняющей металл от действия высоких температур и уменьшающей тепловые потери. Печь опирается на опорные ролики, в точках опоры на печь надевают стальные бандажи. У одной из опор устанавливают два контрольных ролика, с левой и правой стороны бандажа, для наблюдения за перемещением печи.
На вращающуюся печь насаживают венцовую шестерню, при помощи которого печь вращается. Обжигательный барабан устанавливают под углом 3-4˚ к горизонту. Скорость вращения печи 0,5- 1,3 об/мин.
В основу работы печей с циклонными теплообменниками положен принцип теплообмена между отходящими газами и сырьевой мукой во взвешенном состоянии. Уменьшение размера частиц обжигаемого материала и резкое увеличение его поверхности, а также максимальное использование этой поверхности для контакта с теплоносителем интенсифицирует теплообмен между ними. Передача теплоты во взвешенном состоянии гарантирует быстроту и равномерность нагревания массы. Печи этого типа работают на порошкообразной смеси. Циклонные теплообменники состоят обычно из 4-х ступеней циклонов,
варенных из листовой стали толщиной 8-12мм. Циклоны, облицованные внутри огнеупорным кирпичом, расположенным по вертикали в металлических или железобетонных этажерках и соединены между собой газоходами, которые также облицованы огнеупорным кирпичом.
Откорректированная сырьевая мука пневмонасосом подаётся в бункер, откуда она питателем и элеватором транспортируется к дозирующему устройству. Из дозирующего устройства мука поступает в газоход, где подхватывается газами температурой до 400˚С и выносится в циклоны ΙV ступени. В газоходах циклонных теплообменников скорость газа составляет 15-20 м/с, что значительно выше скорости витания частиц сырьевой муки.
Из циклонов ΙV ступени мука, нагретая до 250- 350˚С, стекает через течку в газоход, соединяющий циклоны ΙΙ и ΙΙΙ ступени, где подхватывается подходящими газами и направляется в циклон ΙΙΙ ступени, из которого попадает таким же образом сначала в циклон ΙΙ ступени, а затем в циклон Ι ступени. Нагретая до 700- 800˚С сырьевая мука из теплообменника Ι ступени по охлаждаемой течке поступает во вращающуюся печь для завершения обжига, а затем в холодильник. Таким образом, сырьевая смесь последовательно проходит через все ступени циклонов сверху вниз, нагреваясь в каждой из них в среднем на 200˚С.
Газы и материалы движутся в одном направлении лишь на выходе в каждый циклон. В целом же, циклонные теплообменники работают по противоточной схеме. Отработанные газы поступают в пылеулавливающие устройства и через дымовую трубу выходят в атмосферу.
Общая часть
2.1 Способы производства клинкера
![]() |
Производство портландцемента складывается, в основном, из следующих
операций: добычи сырья; приготовления сырьевой смеси, состоящего из дробления, помола и ее гомогенизации; обжига сырьевой смеси; помола обожженного продукта (клинкера) в тонкий порошок.
Существует три способа производства – мокрый, сухой и комбинированный.
При мокром способе сырьевую смесь измельчают совместно с водой. Получаемая сметанообразная жидкость – шлам – содержит 32-45% воды. По сухому способу сырьевые материалы предварительно высушивают, а затем совместно измельчают. Полученный тонкий порошок называют сырьевой мукой. При комбинированном способе производства сырьевая смесь готовится в виде шлама, полученного при обычном мокром способе производства, подвергается обезвоживанию в фильтр - прессах и вакуум-фильтрах до влажности 16-20%, грануляции, а затем обезвоживается в печах, работающих по сухому способу производства.
Способ производства выбирают в зависимости от технических и технико-
экономических факторов: свойств сырья, его однородности и влажности, наличия достаточной топливной базы и др.
На цементных заводах, работающих по мокрому способу, в качестве
сырьевых материалов для производства портландцементного клинкера часто используют мягкий глинистый и твердый карбонатный компоненты. Так как глинистый компонент мягкий, то его предварительное измельчение осуществляют в мельнице самоизмельчения «Гидрофол», а твердый карбонатный компонент дробят в 1-2 стадии в щековых дробилках. Глинистый шлам и измельченный известняк загружают в мельницу тонкого помола сырья в определенном соотношении, куда также направляют корректирующие добавки. Чтобы получить шлам заданного химического состава его корректируют в шлам - бассейнах или в потоке. Если и глинистый и карбонатный компоненты мягкие, то предварительное измельчение ведут в мельнице самоизмельчения «Гидрофол», а тонкий помол также в сырьевых трубных мельницах. Если оба компонента твердые, то предварительное их измельчают в дробилках, а тонкий помол также в сырьевой трубной мельнице. Откорректированный сырьевой шлам подают во вращающуюся печь на обжиг. При мокром способе производства для обжига клинкера используют длинные вращающиеся печи со встроенными теплообменными устройствами. Из печи клинкер поступает в холодильник, затем в силосы. Клинкер совместно с гипсом и при необходимости с добавками подаётся на помол, в результате которого получается готовый портландцемент.
При сухом способе производства портландцемента выбор схемы также
зависит от физических и химических свойств сырья. Если в качестве сырья используют твердый известняк и мягкую глину, то известняк после дробления и
глину направляют для предварительного измельчения в мельницу самоизмельчения «Аэрофол». Далее помол и сушку сырьевой смеси целесообразно вести одновременно в трубной сепараторной мельнице. Предварительное измельчение материалов и их сушка возможна совместно в дробилках-сушилках, аэросушилках и т.д., или сушку проводят в сушильном барабане, после чего материал измельчают. Сырьевую муку, выходящую из мельниц тонкого измельчения, доводят до заданного химического состава в
специальных смесительных силосах. Откорректированная сырьевая смесь поступает в систему циклонных теплообменников. Из циклонов материал подается в печь. Полученный клинкер охлаждается, отправляется на склад. Клинкер, гипс и при необходимости добавки подвергают помолу, получается портландцемент.
При комбинированном способе производства сырьевая смесь, как и при
мокром, готовится в виде шлама влажностью 35-40%. После корректирования шлам поступает в вакуум-фильтр или пресс-фильтр, где обезвоживается до влажности 16-20%. Образующийся при этом «сухарь» подсушивается и дробится
в сушилках-дробилках. Сырьевая смесь подаётся на обжиг, который осуществляется во вращающихся печах сухого способа. Все остальные операции производства портландцемента по этому способу не отличаются от соответствующих операций производства по мокрому и сухому способам.
2.2 Обоснование выбора вращающейся печи сухого способа
производства клинкера
В печах с циклонными теплообменниками можно обжигать при сухом способе производства как пластичные, так и не пластичные материалы без увлажнения и грануляции.
Достоинством печей с циклонными теплообменниками является применение порошкообразной сухой сырьевой смеси, низкий удельный расход тепла, высокая удельная производительность [45 -50 кг/м3], возможность достижения высокой единичной мощности установки, равной 5000 кг/сутки. Клинкера и болей, отсутствие движущихся частей, относительно простая конструкция.
Печи для обжига сухой сырьевой смеси при равной производительности примерно в двое короче печей для обжига шлама.
Это объясняется тем, что часть процессов из печи выносится в запечные теплообменные устройства.
Основными преимуществами печей с циклонными теплообменниками (по сравнению с печами других типов) являются:
- отсутствие в запечных теплообменниках движущихся частей;
- высокий коэффициент использования (до 95 %);
- возможность использования непластичного, трудногранулируемого сырья и снижения затрат сырья на испарение влаги;
- возможность использования шахты более грубого помола (остаток на сите с сеткой № 0085 до 20%);
- наиболее низкий расход тепла [до 3,05 мДж/ 730 ккал на 1кг клинкера] и самый высокий тепловой К.П.Д. (55- 60%);
- высокий съём клинкера вследствие хорошей (равномерной) предварительной тепловой обработки сырьевой смеси.
3 Технологическая часть
3.1 Характеристика топлива
Затраты на топливо в цементной промышленности очень высоки. Они
составляют до 40% себестоимости клинкера.
В цементной промышленности используют газообразное, жидкое и твёрдое
топливо. В качестве газообразного топлива применяют природный газ, смесь природного газа с подземной газификацией, а также коксовый газ – продукт коксования каменных углей. Наибольшее распространение получили природные топливные газы, требования к которым регламентированы ГОСТ 5542-78. В зависимости от месторождения содержание метана в природных газах составляет 80-99%, теплота сгорания 32-39 мДж/м3, плотность 0,72-0,85 кг/м3.
Газ поступает на цементное предприятие от газораспределительной станции
под давлением около 0,6 МПа, на газораспределительном пункте (ГРП), его давление снижается до 0,25%-0,3 МПа. От ГРП газ по специальным газопроводам транспортируют к местам его потребления.
Газовое пламя имеет меньшую светимость, что обуславливает повышение
расхода теплоты, тем не менее, это дешевый удобный вид транспорта. Газ не требует устройств для хранения, не дает отходов при сгорании, не загрязняет атмосферу. Применение газа упрощает автоматизацию процесса сжигания топлива и технологию производства клинкера. Постоянство химического состава и теплоты сгорания газа обеспечивает равномерность режима обжига и стабильность работы печи. При этом повышается стойкость футеровки, возрастает коэффициент использования печи, следовательно, увеличивается выпуск продукции. Газообразное топливо не требует специальных подготовок перед его сжиганием, что сокращает капитальные расходы.
3.2 Технологический и теплотехнический режим вращающейся печи
с циклонными теплообменниками
В основу работы печей с циклонными теплообменниками положен принцип теплообмена между отходящими газами и сырьевой мукой во взвешенном состоянии. Передача теплоты во взвешенном состоянии гарантирует быстроту, и равномерность нагревания смеси. Откорректированная сырьевая мука поступает в систему циклонных теплообменников. Отходящие из вращающейся печи газы с температурой 900-1000˚С через переходную шахту по газоходу движутся в циклонный теплообменник IV ступени, а затем последовательно проходят циклонные теплообменники ΙΙΙ, ΙΙ и Ι ступени, пылеулавливающее устройство и через дымовую трубу выходят в атмосферу. В газоходах циклонных теплообменников скорость газов значительно выше скорости движения частиц сырьевой муки. Поэтому подаваемая в газоход между Ι и ΙΙ ступенью циклонов сырьевая мука увлекается потоком газов в циклон Ι ступени, где материал подогревается, а газы соответственно охлаждаются. Поскольку диаметр циклона на много больше диаметра газохода, то скорость газового потока в циклоне резко снижается, и частицы сырьевой муки выпадают из газового потока. Осевший материал через затвор - мигалку поступает в газоход, соединяющий ΙΙ и ΙΙΙ ступени а из него выносится газами во ΙΙ ступень. В такой последовательности сырьевая мука опускается вниз, проходя поочерёдно циклоны и газоходы всех ступеней, начиная от относительно холодной (Ι) и кончая горячей (IV).
Из циклонного теплообменника выходит сырьевая смесь со скоростью декарбонизации не более 35%. Завершение процесса декарбонизации требует относительно долгого времени. Длительность обжига может быть сокращена при использовании трёхступенчатого обжига. Для этого между теплообменником и печью встраивают реактор - декарбонизатор, представляющий собой печь с форсункой, в вихревом потоке которого происходит сжигание части топлива и декарбонизация сырьевой смеси. Из циклонного теплообменника сырьевая мука с температурой 720- 750˚С поступает в декарбонизатор. Сюда же, тангенциально, через вихревую камеру подаётся смесь воздуха с топливом. Поток движется вдоль стенок вверх по спирали в камеру реакции. За время подъёма до выпускного
газохода смесь газов и твёрдых частиц совершает несколько оборотов вокруг оси декарбонизатора. Вследствие вихревого движения вдоль вертикальной оси реактора, возникает зона разряжения. В эту зону всасываются сырьевая мука и топливо, они смешиваются с газами и диспиргируются. Теплота, выделяющаяся при сгорании топлива, немедленно передаётся частицами сырьевой муки, которые нагреваются до 920 - 970˚С. При этом в декарбонизаторе не возникает светящегося факела горения, который виден во вращающей печи. Здесь около 90% теплоты передаётся конвекцией, и только около 10% - излучение. Далее сырьевая мука поступает во вращающуюся печь.
Время пребывания сырьевой муки в циклонных теплообменниках не превышает 25- 30 секунд. За короткое время сырьевая мука нагревается до 700- 800˚С, полностью дегидратируется и 25- 35% декарбонизируется. Поэтому в короткой печи с циклонными теплообменниками отсутствуют зоны испарения, подогрева и сокращена зона декарбонизации. В зоне декарбонизации происходит разложение СаСО3 и МgСО3:
МgСО3→МgО + СО2
СаСО3→ СаО + СО2
Эта зона наиболее напряжена в тепловом отношении, так как процесс разложения известняка требует больших количеств тепла. Температура материала в этой зоне 900 - 1200˚С.
При дальнейшем повышении температуры протекает реакция в твёрдой фазе с образованием силикатов, алюминатов, ферритов кальция. Эти реакции протекают с выделением тепла. Они идут в конце зоны кальцинирования и на небольшом протяжении за ней:
СаО + Fe2O3 → CaO· Fe2O3
CaO + Al2O3 → CaO · Al2O3
CаО · Al2O3 + 2СаО → 3CаО · Al2O3
3CаО · Al2O3 + CaO· Fe2O3→ 4CаО · Al2O3· Fe2O3
2СаО + SiO2 → 2CаО · SiO2
Часть печи, где происходят эти реакции, называют экзотермической зоной. Эта зона занимает 7 - 10% длины печи.
Далее материал поступает в зону спекания. Здесь он частично плавится и образуется жидкая фаза. Максимальная температура в зоне спекания 1420 - 1470˚С или в среднем приблизительно 1450˚С. Спекание начинается уже при температуре 1300˚С, продолжается при подъёме температуры материала до 1450˚С и при охлаждении его снова до 1300˚С. Тепло здесь передаётся излучением. Время пребывания материала в зоне спекания 15 - 30 минут при температуре 1450˚С и выходе гранул клинкера 10 – 50 мм. Повышение температуры обжига до 1600˚С позволяет завершить процесс клинкерообразования за 5 - 10 минут. Зона спекания занимает 10 - 15% длины печи.
Из зоны спекания материал поступает в зону охлаждения. Температура материала снижается до 1200 - 1000˚С. Часть жидкой фазы при этом кристаллизуется с выделением клинкерных минералов, а часть затвердевает в виде стекла. Зона охлаждения занимает 2- 4% длины печи.
Температуры выходящих из печи газов 1050 - 1150˚С, температура отходящих газов перед дымососом доходит до 300˚С. Разряжение в газоходах до 60 МПа и более.
3.3 Конструкция и принцип действия вращающейся печи с циклонными теплообменниками
Вращающиеся печи с циклонными теплообменниками предложены
Мюллером и впервые построены в ФРГ в 1950 году. Вращающиеся печи сухого способа производства различаются по размерам и виду запечных устройств.
Вращающаяся печь представляет собой наклонный стальной барабан, в загрузочную часть которого подаётся сырьевая мука. Со стороны выгрузочной части (головки) печи через форсунки вдувается топливо. Поступивший в печь материал вследствие вращения и наклонного положения обжигаемого барабана движется по направлению к головке печи. Материалы газа движутся по принципу противотока.
Обжигательный барабан вращающейся печи сваривается из отдельных обечаек, изготовленных из стального листа толщиной 24- 50мм. Внутри барабан выложен огнеупорной футеровкой, предохраняющей металл от действия высоких температур и уменьшающей тепловые потери. Печь опирается на опорные ролики, в точках опоры на печь надевают стальные бандажи. У одной из опор устанавливают два контрольных ролика, с левой и правой стороны бандажа, для наблюдения за перемещением печи.
На вращающуюся печь насаживают венцовую шестерню, при помощи которого печь вращается. Обжигательный барабан устанавливают под углом 3-4˚ к горизонту. Скорость вращения печи 0,5- 1,3 об/мин.
В основу работы печей с циклонными теплообменниками положен принцип теплообмена между отходящими газами и сырьевой мукой во взвешенном состоянии. Уменьшение размера частиц обжигаемого материала и резкое увеличение его поверхности, а также максимальное использование этой поверхности для контакта с теплоносителем интенсифицирует теплообмен между ними. Передача теплоты во взвешенном состоянии гарантирует быстроту и равномерность нагревания массы. Печи этого типа работают на порошкообразной смеси. Циклонные теплообменники состоят обычно из 4-х ступеней циклонов,
варенных из листовой стали толщиной 8-12мм. Циклоны, облицованные внутри огнеупорным кирпичом, расположенным по вертикали в металлических или железобетонных этажерках и соединены между собой газоходами, которые также облицованы огнеупорным кирпичом.
Откорректированная сырьевая мука пневмонасосом подаётся в бункер, откуда она питателем и элеватором транспортируется к дозирующему устройству. Из дозирующего устройства мука поступает в газоход, где подхватывается газами температурой до 400˚С и выносится в циклоны ΙV ступени. В газоходах циклонных теплообменников скорость газа составляет 15-20 м/с, что значительно выше скорости витания частиц сырьевой муки.
Из циклонов ΙV ступени мука, нагретая до 250- 350˚С, стекает через течку в газоход, соединяющий циклоны ΙΙ и ΙΙΙ ступени, где подхватывается подходящими газами и направляется в циклон ΙΙΙ ступени, из которого попадает таким же образом сначала в циклон ΙΙ ступени, а затем в циклон Ι ступени. Нагретая до 700- 800˚С сырьевая мука из теплообменника Ι ступени по охлаждаемой течке поступает во вращающуюся печь для завершения обжига, а затем в холодильник. Таким образом, сырьевая смесь последовательно проходит через все ступени циклонов сверху вниз, нагреваясь в каждой из них в среднем на 200˚С.
Газы и материалы движутся в одном направлении лишь на выходе в каждый циклон. В целом же, циклонные теплообменники работают по противоточной схеме. Отработанные газы поступают в пылеулавливающие устройства и через дымовую трубу выходят в атмосферу.
Мероприятия по экономии теплоты и топлива
Расход тепла на обжиг портландцементного клинкера определяется условиями теплопередачи, которая зависит от конструкции печи, а также от состава и структуры сырья и за счёт более тонкого помола шихты и лучшей
гомогенизации. Все методы снижения расхода топлива при обжиге клинкера предусматривают более полное использование тепла отходящих газов. Для уменьшения потери тепла излучением в некоторых зонах устанавливают теплоизоляционные прокладки между корпусом печи и её футеровкой.
К мероприятиям, уменьшающим расход топлива, увеличивающим производительность печи и повышающим стойкость футеровки, относятся введение в сырьевую смесь различных интенсификаторов процесса обжига: плавикового шпата, гипса, фосфогипса и других. Процесс обжига можно также ускорить, устанавливая огнеупорные пороги в отдельных зонах вращающейся печи. Для интенсификации процесса обжига во вращающейся печи можно применять воздушно- кислородное дутьё, при этом повышается температура факела и газового потока за ним, возрастает температура футеровки, улучшается передача тепла от газового потока к материалу. В результате повышается производительность печи и снижается удельный расход топлива.
Интенсифицировать процесс обжига можно путём двухстороннего её питания. Например, в горячий конец печи через форсунку подавать высушенный, измельчённый, гранулированный доменный шлак. Многие вращающиеся печи устаревшей конструкции реконструировали: увеличили поверхность теплоотдачи в зонах сушки и подогрева путём расширения диаметра печи в холодной её части в 1,2 - 1,3 раза.
Поверхность теплопередачи увеличивают установкой внутрипечных и запечных теплообменников, изменением профилей печей, повышением скорости её вращения и устанавливают мощные дымососы, при этом производительность печей повышается на 15 - 20%.
Процесс обжиг
|
|
Состав сооружений: решетки и песколовки: Решетки – это первое устройство в схеме очистных сооружений. Они представляют...
Адаптации растений и животных к жизни в горах: Большое значение для жизни организмов в горах имеют степень расчленения, крутизна и экспозиционные различия склонов...
История развития хранилищ для нефти: Первые склады нефти появились в XVII веке. Они представляли собой землянные ямы-амбара глубиной 4…5 м...
Биохимия спиртового брожения: Основу технологии получения пива составляет спиртовое брожение, - при котором сахар превращается...
© cyberpedia.su 2017-2024 - Не является автором материалов. Исключительное право сохранено за автором текста.
Если вы не хотите, чтобы данный материал был у нас на сайте, перейдите по ссылке: Нарушение авторских прав. Мы поможем в написании вашей работы!