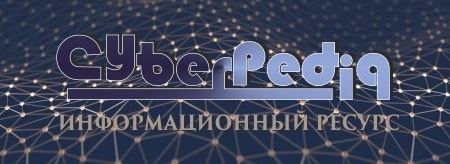
Индивидуальные и групповые автопоилки: для животных. Схемы и конструкции...
Кормораздатчик мобильный электрифицированный: схема и процесс работы устройства...
Топ:
Проблема типологии научных революций: Глобальные научные революции и типы научной рациональности...
Характеристика АТП и сварочно-жестяницкого участка: Транспорт в настоящее время является одной из важнейших отраслей народного...
Теоретическая значимость работы: Описание теоретической значимости (ценности) результатов исследования должно присутствовать во введении...
Интересное:
Отражение на счетах бухгалтерского учета процесса приобретения: Процесс заготовления представляет систему экономических событий, включающих приобретение организацией у поставщиков сырья...
Принципы управления денежными потоками: одним из методов контроля за состоянием денежной наличности является...
Наиболее распространенные виды рака: Раковая опухоль — это самостоятельное новообразование, которое может возникнуть и от повышенного давления...
Дисциплины:
![]() |
![]() |
5.00
из
|
Заказать работу |
|
|
Технико-экономические параметры вагона.
К основным параметрам грузовых вагонов оптимальная величина которых определяется в результате технико-экономического расчета относятся:
Т-тара вагона
Р-номенальная грузоподъемность
V-объем кузова вагона
Эти параметры выбираются в зависимости от следующих показателей:
2L сц- длинна вагона по осям сцепления автосцепки
2l- база вагона
M0-количество осей в вагоне
2В0-ширина заднего габарита подвижного состава
Н- высота габарита
2Sк- ширина рельсовой колеи
Q0- нормированная нагрузка на одну ось колесной пары(осевая нагрузка)
Qn- пагонная нагрузка (нагрузка на единицу длинны)
Аi- доля итого груза в общем объеме перевозок
Li-дальность перевозки i-го груза
Для сравнения различных вариантов конструкций удобно пользоваться относительными параметрами или характеристиками
Кт=T/R-технический коэффициент тары.
Кn=T/P*λ-погрузочный коэффициент тары,
Где λ- коэффициент использованного грузоподъема.
Vуд.=V/P-удельный объем.
Vn-V*γ-погрузочный объем,
Где γ- коэффициент заполненного объема.
qпб=T+P/2Lсу- погонная нагрузка брутто.
qпн=P/2Lсу- погонная нагрузка нетто.
Для сравнения универсальных вагонов испытывают следующие зависимости:
Pст=Σai/Σai/PстL-средняя статической нагрузки,
Где Pстi-статическая нагрузка итого груза.
Pстi=P/Vуд./Vу.г.- удельный объем перевозки груза(дано в таблице)
Pст.i=P*λi, где λi-коэффициент испытываемого грузоподъемности для итого груза (дано в таблице).
Pдин=Σai*li/Σ*ai*li/Pстi- средний динамический коэффициент.
Kпт=Т/Рдин.; погрузочный коэффициент тары.
qп.н.=Рдин/2Lсу-средняя пагонная нагрузка нетто.
В качестве критерия оценки оптимального варианта конструкции принимается обобщенный экономический, приведенные затраты (Спр),отраженные все стороны производства и эксплуатации вагонов.
|
Спр.=Э+Е*К, где Э- эксплуатация расходов.
К-капитальных вложений.
Е- нормативный коэффициент эффективности капитальных вложений.
Спр.=А1/Рст.+А2*2Lb/Рст+В1/Рдин.+В2*2Lb/Рдин.+F0/qпн.+D*Kпт., где A1;А2;В1;В2;F0;D-постоянный коэффициент (дано в таблице).
2Lb-внутренняя длина кузова.
По минимуму приведенных затрат выбирается оптимальный вариант конструкции.
Исходя из задач условий эксплуатации.
Р≤q0*m0-T
P≤qn*2hсу-Т,
тогда минимальная допустимая длина 2hсуmin*q0*m0/qn
Вывод: В данном пункте я рассмотрел технико-экономические параметры своего вагона.
Габариты ПС.
Габарит приближения строений — предельное поперечное перпендикулярное оси пути очертание, внутрь которого, помимо подвижного состава, не должны входить никакие части сооружений и устройств.
Габарит приближения строений
железнодорожный транспорт габарит погрузка
Габарит приближения строений - предельное поперечное перпендикулярное оси пути очертание, внутрь которого не должны заходить никакие части сооружений и устройств. Исключение представляют устройства, предназначенные для непосредственного взаимодействия с подвижным составом: провода контактной сети и детали их крепления, вагонные замедлители в рабочем состоянии, поворачивающаяся часть гидравлических колонн для набора воды и др.
Государственным стандартом ГОСТ 9238-83 установлены габариты подвижного состава: Т; 1-Т; 1-ВМ; 0-ВМ; 02-ВМ и 03-ВМ.
§ Габарит Т распространяется на подвижной состав, допущенный к обращению по путям, сооружения и устройства на которых отвечают требованиям габаритов приближения строений С и Сп.
§ Габарит 1-Т распространяется на подвижной состав, допущенный к обращению по всем путям общей сети дорог, подъездным путям, и путям промышленных предприятий.
§ Габариты 1-ВМ, 0-ВМ, 02-ВМ, 03-ВМ [1] распространяются на подвижной состав, допущенный к обращению по железным дорогам колеи 1520 (1524) мм и дорог колеи 1435 мм.
|
Горизонтальная габаритная рама определяет наибольшую допускаемую ширину строительного или проектного очертания вагона в любом его поперечном сечении по длине на расстоянии n1,n2,…на определенной высоте.
Вывод: В данном пункте я рассмотрел, и рассчитал габариты приближения строения для своего вагона.
Колесные пары.
Классификация и особенности устройства колесных пар
Колесные пары относятся к ходовым частям и являются одним из ответственных элементов вагона. Они предназначены для направления движения вагона по рельсовому пути и восприятия всех нагрузок, передающихся от вагона на рельсы при их вращении. Работая в сложных условиях загрузки, колесные пары должны обеспечивать высокую надежность, так как от них во многом зависит безопасность движения поездов. Поэтому к колесным парам предъявляются особые, повышенные требования Госстандартами, Правилами технической эксплуатации железных дорог, Инструкцией по осмотру, освидетельствованию, ремонту и формированию вагонных колесных пар, а также другими нормативными документами при проектировании, изготовлении и содержании в эксплуатации. Конструкция и техническое состояние колесных пар оказывают влияние на плавность хода, величину сил, возникающих при взаимодействии вагона и пути, и сопротивление движению.
Работая в современных режимах эксплуатации железных дорог и экстремальных условиях окружающей среды, колесная пара вагона должна удовлетворять следующим основным требованиям: обладать достаточной прочностью, имея при этом минимальную необрессоренную массу (с целью снижения тары подвижного состава и уменьшения непосредственного воздействия на рельсовый путь и элементы вагона при прохождении неровностей рельсовой колеи); обладать некоторой упругостью, обеспечивающей снижение уровня шума и смягчение толчков, возникающих при движении вагона по рельсовому пути; совместно с буксовыми узлами обеспечивать, возможно, меньшее сопротивление при движении вагона и возможно большее сопротивление износу элементов, подвергающихся изнашиванию в эксплуатации.
Колесная пара (рис. 3.1) состоит из оси 1 и двух укрепленных на ней колес 2. Тип колесной пары определяется типом оси и диаметром колес, а также конструкцией подшипника и способом крепления его на оси. Типы вагонных осей различают по размерам и форме шейки — для роликовых подшипников качения и подшипников скольжения. Размеры оси устанавливают в зависимости от величины расчетной нагрузки, воспринимаемой ею при эксплуатации.
|
Колесные пары Ш-950 предназначены для эксплуатации с подшипниками скольжения, а колесные пары РУ1-950, РУ1Ш-950, РУ-950 и РУ-1050 — с роликовыми подшипниками (РУ — роликовая унифицированная, Ш — торцевое крепление внутренних колец подшипников приставной шайбой). Исходя из расчетной нагрузки, определяются диаметры шеек 3, 4, 5 (см. рис. 3.1), подступичной 7 и средней 8 частей оси. Предподступичная часть 6 является ступенью перехода от шейки к подступичной части оси и служит для установки уплотняющих устройств буксы. На подступичных частях 6 прочно закрепляются колеса 2. В настоящее время в эксплуатации находятся еще небольшое количество колесных пар с осями III типа с подшипниками скольжения, которые заменяются на роликовые. На торцах их шеек 5 имеются буртики б, ограничивающие продольные перемещения подшипников скольжения, располагающихся в верхних частях.
Колесные пары с осями, предназначенными для эксплуатации с роликовыми подшипниками, различают между собой по конструкции торцевого крепления внутренних колец роликовых подшипников на шейке: 3 — с нарезной частью, а для навинчивания корончатой гайки; 4 — при помощи приставной шайбы, для чего на торцах делаются отверстия с нарезкой для болтов крепления. Такое крепление выполнено в двух вариантах: тремя или четырьмя болтами. Колесные пары с формой шейки 3 обозначаются РУ1-950, а с формой 4 — РУ1Ш-950.
Вагонные оси.
Вагонные оси (рис. 3.2) являются составной частью колесной пары и представляют собой стальной брус круглого переменного по длине поперечного сечения.
На подступичных частях 3 оси располагаются колеса, укрепленные жестко или подвижно, а на шейках 1 размещаются подшипники. Вагонные оси различают между собой: размерами, определяемыми в зависимости от заданной нагрузки; формой шейки оси в соответствии с применяемым типом подшипника — для подшипников качения и подшипников скольжения; формой круглого поперечного сечения — сплошные или полые; способом торцового крепления подшипников качения на шейке оси — корончатой гайкой или шайбой. Кроме того, оси классифицируются по материалу и технологии изготовления. Между шейками 1 и подступичными частями 3 находятся предподступичные части 2, служащие для размещения деталей задних уплотняющих устройств букс, а также снижения концентрации напряжений в переходных сечениях от подступичных частей к шейкам оси. В местах изменения диаметров для снижения концентрации напряжений имеются плавные сопряжения — галтели, выполненные определенными радиусами: от шейки 1 к предподступичной 2, от предподступичной к подступичной 3 и от средней 4 к подступичной частям. Снижение концентрации напряжений, вызванных посадкой внутреннего кольца роликового подшипника, обеспечивается разгружающей канавкой, расположенной у начала задней галтели шейки оси (рис. 3.2, г). Оси для подшипников качения на концах шеек имеют нарезную часть К (рис. 3.2, а) для навинчивания корончатой гайки, а на торце имеется паз с двумя нарезными отверстиями для постановки и крепления двумя болтами стопорной планки. В вагонных осях с креплением подшипников качения при помощи приставной шайбы в торцах шеек делаются нарезные отверстия для болтов (рис. 3.2, б) в двух вариантах: при помощи трех или четырех болтов. Оси для подшипников скольжения по торцам шеек имеют буртики М (рис. 3.2, в), служащие для ограничения смещения подшипников вдоль оси наружу при движении вагона. На торцах всех типов осей предусмотрены центровые отверстия (рис. 3.2, д, ё), служащие для установки и закрепления оси или колесной пары в центрах при обработке на токарном станке. Форма и размеры центровых отверстий стандартизированы. Оси колесных пар, оборудуемых дисковым тормозом, а также оси, на которых предусмотрена установка привода подвагонного генератора, имеют посадочные поверхности для установки тормозных дисков или деталей редуктора. Основные размеры и допускаемые нагрузки для стандартных типов осей вагонов широкой колеи, кроме вагонов электропоездов и дизель-поездов.
|
На шейке осей РУ-1 и РУ-1Ш устанавливаются роликовые подшипники с наружным диаметром 250 мм, а на шейке оси РУ — 280 мм, поэтому посадочные диаметры у них разные. Для грузовых вагонов с повышенными нагрузками на ось 245 кН предусмотрена усиленная ось, которая также применяется для специализированных грузовых вагонов с нагрузкой на ось 30 тс (сталь ОС ГОСТ 4728-96).
Колеса.
По конструкции вагонные колеса можно разделить на: безбандажные (цельные); бандажные (составные, состоящие из колесного центра, бандажа и предохранительного кольца); упругие, имеющие между бандажом и колесным центром упругий элемент; раздвижные на оси, вращающиеся на оси колеса. По способу изготовления колеса делятся на катаные и литые. В зависимости от размеров диаметра, измеренного в плоскости круга катания, — 950 и 1050 мм.
|
В эксплуатации колеса, перекатываясь по рельсовому пути и передавая ему значительные статические и динамические нагрузки через небольшую площадку, работают в сложных условиях окружающей среды. Одновременно с этим в процессе торможения между колесами и колодками, а также в контакте с рельсами возникают силы трения, вызывающие нагрев и износ обода, что способствует образованию в нем ряда дефектов. Удары на стыках могут вызывать появление трещин и отколов в ободе колес. В этой связи от их исправного состояния во многом зависит безопасность движения поездов.
Учитывая сложные условия работы и повышение надежности в эксплуатации, поверхность катания колеса должна обладать высокой прочностью, ударной вязкостью и износостойкостью, а металл диска и ступицы, удерживающихся на оси силами упругости, необходимой вязкостью. Этим требованиям удовлетворяют составные колеса, в которых бандаж можно изготовлять из стали повышенной прочности и твердости, а колесный центр — из более вязкой и дешевой стали. Кроме того, при достижении предельного износа или появлении другого повреждения в эксплуатации бандаж можно заменить без смены колесного центра.
Однако в современных условиях эксплуатации железных дорог из-за существенных недостатков по прочности и надежности, значительной трудоемкости формирования колесной пары и повышенной массы бандажные колеса в нашей стране были заменены безбандажными. Причем наиболее совершенными и надежными в эксплуатации признаны стальные цельнокатаные. Конструкция, размеры и технология изготовления колес определяются Гос. стандартами.
Стальное цельнокатаное колесо (рис. 3.10) состоит из обода 7, диска 2 и ступицы 3. Рабочая часть колеса представляет собой поверхность катания 4. Номинальный размер ширины обода составляет 130 мм. На расстоянии 70 мм от внутренней грани, а обода, являющейся базовой, расположен воображаемый круг катания, используемый для измерения специальными инструментами диаметра колеса, толщины обода и проката. Противоположная грань б называется наружной. Ступица 3 с ободом 1 объединены диском 2, расположенным под некоторым углом к плоскости круга катания, что придает колесу упругость и способствует снижению уровня динамических сил во время движения вагона. Ступица служит для посадки колеса на подступичной части оси. Поверхность катания 4 обрабатывается по стандартному профилю.
В соответствии с ГОСТ 10791-89 цельнокатаные колеса изготовляются из сталей двух марок: 1 — для пассажирских вагонов локомотивной тяги, немоторных вагонов электропоездов и дизель-поездов; 2 — для грузовых вагонов железных дорог колеи 1520 мм.
Химический состав сталей, в %, марки 1 — углерода 0,44—0,52, марганца 0,80—1,20, кремния 0,40—0,60, ванадия 0,08—0,15; марки 2 — углерода 0,55—0,65, марганца 0,50—0,90, кремния 0,20—0,42; для обеих марок сталей допускается не более: фосфора 0,035 и серы 0,040. Ободы колес подвергаются упрочняющей термической обработке путем прерывистой закалки и отпуска. Механические свойства стали ободов после упрочняющей термической обработки должны соответствовать нормам (табл. 3.4).
Ударная вязкость стали дисков колес при температуре 20 °С должна быть не менее: для стали марки 1 — 0,3 МДж/м² для стали марки 2 — 0,2 МДж/м².
На процессы взаимодействия колес с рельсами и безопасность движения поездов существенное влияние оказывает профиль поверхности катания. Стандартный профиль поверхности обода колеса (рис. 3.11) распространяется на колеса для колесных пар тележек грузовых и пассажирских вагонов локомотивной тяги. Он имеет гребень, служащий для направления движения и предохранения от схода колесной пары. Гребень имеет высоту 28 мм, измеряемую от его вершины до горизонтальной линии, проходящей через точку пересечения круга катания с профилем. Угол наклона наружной грани гребня оказывает влияние на безопасность движения: его увеличение повышает устойчивость колесной пары на рельсах и уменьшает износ.
Стандартный профиль (см. рис. 3.11) имеет конусность рабочей части 1:10, которая обеспечивает центрирование колесной пары при ее движении на прямом участке пути и предотвращает образование неравномерного износа по ширине обода колеса, а также улучшает прохождение кривых участков пути. Вместе с тем, конусность 1:10 создает условия для появления извилистого движения, что неблагоприятно влияет на плавность хода вагона.
Поверхность профиля катания колеса с конусностью 1:3,5 гораздо реже катится по рельсу, поэтому она меньше изнашивается. Благодаря наличию этой конусности и фаски 6 мм х45° наружная грань (см. рис. 3.11) приподнимается над головкой рельса даже при наличии допустимого проката, наплыва металла и других дефектов поверхности катания колес, обеспечивая безопасный проход стрелочных переводов. Профиль поверхности катания обода для колесных пар пассажирских вагонов, эксплуатируемых со скоростями движения свыше 160 км/ч, имеет горизонтальную площадку между размерами 60,7 до 70 мм, а далее конусности 1:50; 1:10; 1:3,5 и фаску 6 мм х45°. Наружная грань гребня составляет 65° к горизонтали вместо 60°, как это предусмотрено в стандартном профиле (см. рис. 3.11), переходные радиусы закруглений также изменены.
Расчет оси колесной пары на прочность.
Оценка прочности осуществляется по допускаемым напряжениям, при таком методе ось рассматривается при статическом состоянии, на нее действуют силы:
1) Вертикальные силы на обе шейки от массы брутто
Q=1,25 P0
2) Горизонтальные силы, как доля от вертикальных, приложенная в центре тяжести кузова
H=0,5 P0,
Где P0-максимальная статическая нагрузка от колесной пары на рельсы
1,25;0,5-коэфициенты учёта динамического воздействия сил в вертикальном и горизонтальном направлении.
Максимальная статическая нагрузка от колесной пары на рельсы при проектировании определенным заданием, при оценке прочности оси фактическая осевая нагрузка определяется по формуле:
P0=Pст+T/mo
Po=226,084кН,
Где Pст.- статическая нагрузка вагона, представляющая собой силу тяжести груза в вагоне
T-собственная сила тяжести от тары вагона
mo-число колесной пары вагона
Ось рассматривается как 2-х консольная шарнирная опертая балка. В расчетной схеме внесены силы приложенные на расстояние h_1,45 м от силы осевой линии колесной пары, вертикальной Q и горизонтальной H.Силы загружают вертикальные силы Р1 левую и Р2 правую шейки. В связи с учетом не благоприятных сочетаний несимметричных колебаний считаем, что нагрузка приложенная к середине левой шейки, а на другой она равна 0.
На левую шейку: Р1= +
Правую шейку: Р2= –
2b2-расстояние между серединой шеек 2,036м.
При этом вертикальные реакции рельсов:
N1= +
– левое
N2= +
– правое
2S- расстояние между катанием колес КП
2S- радиус колеса, =450 мм
Горизонтальная реакция рельса уравнивает горизонтальную силу и приложенную к гребню левого колеса. Из схемы видно, что Hp=H является левая половина оси, хотя и правая может оказаться в таком же положении при вписывании вагона в кривой участок пути с поворотом в другую сторону. Из условия равновесия оси, изгибающие моменты вызванные действием расчетных нагрузок в этом условном расчетном методе подсчитывается в трех наиболее опасных сечениях.
1-1-у внутренние галтели шейки
2-2-у подступичные части в плоскости круга катания колеса
3-3 в среднем сечении оси
М1=Р1 ,
L1-длина шейки оси (130, подступичной 194, средней 165)
М2=Р1 l2+H
L2-расстояние от середины шейки до плоскости круга катания колеса
М3=Р1 b2+H
-N1
Момент сопротивления изгибу для i-того расчета сечения для сплошной оси.
Wi-=
Исходя из уравнения прочности на изгиб
Mi=Wi[ i]
Gi- допускается направления в мПа.
В условном методе определении минимально допустимого диаметра оси обеспечивает необходимую прочность.
Шейка d1=
Подступичная часть d2=
Средняя часть d3=
Ро= = 226кН
Н=0.5 Р0=0.5
226=113
Р1= +
=565,215+322,03=887,245
Р2=565,215-322,03=243,185
N1=565,215+ =565,215+0,54=565,755
N2=565,215-0,54=564,675
М1=887,245 =84,288
L2=b2-S=1,018-0,79=0,228
М2=887,245 0,228+452,172
0,45=202,29+203,48=405,77
М3=887,245 1,018+203,48-565,755
0=903,21+203,48-446,95=659,7+4
Р1= +
=141,25+80,5=221,75
Р2=141,25+80,5=60,75
N1= +
=141,25+135,9=277,15
N2=141,25-135,9=5,35
М1=221,75 =221,75
0,095=21,06
М2=221,75 0,228+113
0,45=50,5+50,85=101,35
М3=221,75 0,228+113
0,45-227,15
0,79=225,7+50,85-219=57,55
d3= =
=
121
d2= =
=
186
d3= =
=
=157
Вывод: В данном пункте я рассмотрел колесные пары, вагонные оси и рассчитал ось колесной пары на прочность.
Посадки подшипников.
Необходимы посадки подшипников качения (СТ СЭВ 145—75) осуществляют подбором предельных отклонений сопряженных деталей вала и корпуса. Посадки внутренних колец подшипников на вал осуществляются по системе отверстия, наружных колец в корпус — по системе вала.
Выбор той или иной посадки зависит от условий работы подшипника: характера нагрузок, вращения внутреннего или наружного кольца, условий монтажа и т. д. Применяются посадки с зазором и натягом. Если вал вращается, то его соединение с внутренним кольцом осуществляется по посадке с натягом, а наружного кольца — по посадке с зазором или переходной посадке, которая допускает зазор. Если вращается корпус — то наоборот. Это необходимо для предотвращения заклинивания тел качения и обеспечения равномерного износа дорожек качения колец в неподвижных деталях.
Оценка работоспособности типовых подшипников качения производится по долговечности, которая выражается в миллионах километров пробега.
Для грузовых вагонов Ln>1,5 млн.км.
Pст=1/2*i(Qбр/Qкп)
Qбр- масса вагона брутто
Qкп- масса кп
m- число кп
i- число подшипников в одной буксе
Kq- коэффициент учитываемых динамических характеристик нагрузки буксового узла
Kq- 1.3
С=800000
акп=1200
i=2
m=4
Kq=1.3
z=15
lф=52
d=30
Pст=1/2i (Qбр/Qкп)=1/22(904344/4-1200)=1/4(226086-1200)=1/4*224886=56221,5
Pa=Pст*Кq
Pa=56221,5*1,3=73087,95
Lн=(С/Ра)m1*πD*10-3
Lн=(800000/73087,95)10/3*3,14*0,9*10-3=8,2млн.км.
Вывод: В данном пункте я рассмотрел назначение и типы буксовых узлов, подшипники качения и рассчитал подшипники качения на долговечность.
Рессорное подвешивание
Гасители колебаний
При движении вагона по периодическим неровностям пути (стыкам рельсов, например) со скоростью, когда частоты вынужденных и собственных колебаний близки по величине, могут возникать большие амплитуды колебаний кузова на рессорах (резонанс), если в системе рессорного подвешивания отсутствуют или малы силы сопротивления. Поэтому для гашения резонансных колебаний в систему рессорного подвешивания вводят специальные гасители, которые позволяют снизить амплитуды и ускорения колебательного движения, а следовательно, уменьшить воздействие динамических сил на элементы вагона и перевозимый груз. Многочисленные разновидности конструкций гасителей колебаний, применяемых в подвижном составе железных дорог, можно объединить в две большие группы: фрикционные и вязкого сопротивления. Рассмотрим некоторые из них.
Фрикционные гасители колебаний наиболее широко применяются в тележках грузовых вагонов.
В двухосных тележках типа ЦНИИ-ХЗ фрикционный гаситель колебаний состоит из двух фрикционных клиньев 2 (рис. 3.27, а), размещенных между наклонными поверхностями концов надрессорной балки 1 и фрикционными планками 5, укрепленными на колонках 4 боковой рамы тележки. Клинья опираются на двухрядные цилиндрические пружины 5.Работа таких гасителей заключается в следующем. При вертикальных колебаниях надрессорной балки 1 совместно с обрессоренными массами вагона фрикционные клинья 2 перемещаются вниз и вверх относительно фрикционных планок 3. В результате между клиньями и планками возникают силы трения, создающие сопротивление колебательному движению. При этом величина силы трения прямо пропорциональна прогибу пружин и возрастает с его увеличением, так как клинья прижимаются с большей силой. Работа сил трения преобразуется в тепловую энергию, которая рассеивается в окружающую среду. Такого типа гаситель называют фрикционным с переменной силой трения, зависящей от прогиба.
Фрикционный гаситель колебаний с постоянной силой трения, показанный на рис. 3.27, б, устроен так, что сила трения не зависит от прогиба рессорного подвешивания. В пазах 5 концов надрессорной балки установлены башмаки 2, в которых размещены стаканы 3 с пружинами 4. Стакан 3 прижат предварительно сжатой пружиной 4 к фрикционной планке 1 боковой рамы тележки. Сила трения, возникающая при колебании надрессорной балки совместно с опирающимися на нее частями, постоянна и зависит только от жесткости и величины предварительного сжатия пружины, а также коэффициента трения между взаимодействующих плоскостей стаканов и фрикционных планок.
Фрикционный гаситель колебаний, применяемый в трехосных тележках типа УВЗ-9М (рис. 3.27, в), создает силы трения, пропорциональные прогибу рессорного подвешивания. Нагрузка от надрессорной балки тележки через прокладку 1 и нажимной конус 2 передается на два раздвигающихся клина 3. При деформациях рессорного подвешивания под действием скошенных поверхностей нажимного конуса 2 раздвижные клинья 3 прижимаются к внутренней поверхности фрикционного стакана 6. Между трущимися поверхностями раздвижных клиньев 3 и стакана 6 при их взаимном перемещении возникают силы трения, пропорциональные прогибу пружины 5, размещенной между фланцем стакана 6 и опорным кольцом 4.
К гасителям колебаний с постоянной силой трения относится дисковый фрикционный гаситель (рис. 3.28, а), конструкция которого состоит из стального диска 6, зажатого между двумя фрикционными прокладками 2 с помощью пружины 7, болта 4, поводков 3 и резиновых прокладок 5. Рычаги 1 и 3 с помощью валиков крепят между опорами упругих элементов. При колебании вагона и относительном угловом перемещении рычагов 1 и 8, а следовательно диска 6 и прокладок 2, между ними возникают силы трения постоянной величины. Эти силы можно регулировать величиной сжатия пружины 7 с помощью гаек болта 4.
Телескопический фрикционный гаситель колебаний фирмы Крайслер (рис. 3.28, б) является гасителем с постоянной силой трения и применяется в тележках грузовых и пассажирских вагонов зарубежных стран. Он состоит из башмаков 2 с фрикционными накладками 5, выполненными из асбестовой массы, которые прижимаются к корпусу 6 с помощью усилия пружины 4, воздействующей на конусные (клиновые) головку 1 и шайбу 3. Сила трения такого гасителя регулируется гайками 7, сжимающими пружину 4.
Телескопический гаситель колебаний типа БИТМ (Брянский институт транспортного машиностроения) (рис. 3.28, в) отличается от гасителя фирмы Крайслер тем, что усилия на главные трущиеся поверхности передаются через эластичные прокладки 1 и 2 без вспомогательных клиновых поверхностей. Изменением толщины этих прокладок и усилием сжатия пружины можно регулировать соотношение сил трения при возвратно-поступательном движении частей гасителя относительно корпуса. Гаситель колебаний типа БИТМ обладает большей стабильностью по сравнению с гасителем фирмы Крайслер, поскольку усилия на главные трущиеся поверхности передаются через упругие элементы.
Телескопические гасители колебаний устанавливаются как вертикально, так и наклонно относительно оси упругих элементов подвешивания. При наклонном их расположении гасятся вертикальные и горизонтальные колебания вагона. Важным преимуществом телескопических гасителей является простота и быстрота замены неисправного гасителя исправным.
Гидравлические гасители колебаний.
Как отмечалось выше, существенным недостатком фрикционных гасителей колебаний является нестабильность их работы, т.е. ухудшение силовой характеристики. Эти и другие недостатки устранены в гасителях колебаний гидравлического типа и других гасителях вязкого сопротивления, которые, несмотря на усложнение изготовления, ремонта и технического обслуживания, широко применяются в тележках современных пассажирских вагонов.
В телескопических поршневых гидравлических гасителях колебаний сила сопротивления создается за счет перетекания жидкости из одной полости в другую через узкие калиброванные (дроссельные) отверстия. Сила сопротивления гасителя в этом случае зависит от вязкости жидкости, размеров дроссельных отверстий и пропорциональна скорости перемещения поршня.
Силовую характеристику в этих конструкциях создают на основе требований к ходовым качествам вагона путем подбора вязкости жидкости и размеров дроссельных отверстий.
Гидравлический гаситель колебаний (рис. 3.29) состоит из рабочего цилиндра 4, поршня 6 со штоком 1, неподвижного поршня 9 с отверстием 14, верхнего 7 и нижнего 8 клапанов, корпуса 3 и направляющей втулки 2. Между цилиндром 4 и корпусом 3 образуется резервуар 5. Гаситель заполнен вязкой жидкостью, которая подбирается с таким расчетом, чтобы в летнее и зимнее время ее вязкость изменялась незначительно.
Работа гидравлического гасителя колебаний заключается в следующем. При движении поршня 6 вниз (ход сжатия) верхний клапан 7 приподнимается и жидкость из подпоршневой полости цилиндра 4 перетекает в надпоршневую 12 через большие отверстия 11. Одновременно вследствие движения штока 1 вниз давление под поршнем 6 повышается и часть жидкости с сопротивлением перетекает из полости 10 через дроссельное отверстие клапана 8 в резервуар 5.
В это время давление жидкости в надпоршневой 12 и подпоршневой 10 полостях цилиндра 4 выравнивается, так как полости 10 и 12 соединены между собой через большие отверстия 11 поршня и приподнятого вверх клапана 6. При движении поршня 6 вверх (ход растяжения) верхний клапан 7 закрывается под действием повышенного давления в надпоршневой полости 12 и жидкость с сопротивлением перетекает через дроссельные каналы в подпоршневую полость 10. Одновременно в полости 10 наступает разрежение, вследствие чего нижний клапан 5 поднимается и пропускает жидкость из резервуара 5 в подпоршневую полость 10, восполняя недостающий объем жидкости, поступающий из меньшего надпоршневого пространства, включающего объем штока 1. Резервуар 5 гасителя служит для размещения объема жидкости, вытесняемой штоком 1 из цилиндра при движении поршня 6 вниз, а также является сборником жидкости, просачивающейся через кольцевой зазор между штоком и направляющей втулкой 2. Для предотвращения выдавливания жидкости наружу гаситель имеет уплотнение 13.
Расчет пружин на прочность от действия расчетной нагрузки «Рр»
Для определения наибольшего напряжения принимают расчетную силу
Рр =Pст*кзп,
где кзп-эксперементальное значение коэффициента контрольного запаса прогиба.
По нормам для грузовых вагонов кзп≥1,7÷1,8
В рессорном подвешивании грузовых 4-осных вагонах в качестве упругих элементов используется 28 2-х рядных цилиндрических пружин. Упругие свойства рессорного подвешивания оценивают коэффициент жесткости
C=p/f,
P-внешняя сила, действующая на упругие элементы в ньютонах.
Гибкость:
λ=1/С
Двойное рессорное подвешивание пассажирских тележек необходимо рассматривать как систему последующих соединений надбуксовых и центральных ступеней.
Дано | Наружная | Внутренняя |
Dср | 0,17 | 0,105 |
d | 0,03 | 0,019 |
np | 5,2 | 7,2 |
G | 80000 | 80000 |
kзп | 1,9 | 1,9 |
Pст=Pбрутто-Pи
Pбр=Т+Р
Pp=Pст*кзп
Сн=Q*d4/8*Dср*np
Ppn=Pp*Cn/Cn+Cb
Ppb=Pp*Cb/Cn+Cb
τn=8* Ppn* Dср/πd3*(4m-1/4m-4+0,615/m)≤750мПа
Pст=904344-78400/28=29498Н
Pp=29498*1,9=56046,2
Сн=80000*0,034,8*0,173*5,2=64800,0,204256=0,317мН,м2
Св=80000*106*0,0194/8*0,1053*7,2=0,155мН/м2
Ppn=53411Н
Ppb=56046*15597/332847=2578Н
τn=8*53411*0,17/3,14*0,033*(4*5,6-1/4*5,6-4+0,615/5,6)=72,2мПа
τb=8*2578*0?105/0,00008478*1?272=32,4МПа
Вывод: В данном пункте я рассмотрел рессорное подвешивание, назначение и классификацию, оценил напряжение состояния пружин рессорного подвешивания вагонов.
Тележки грузовых вагонов
Современные грузовые вагоны магистрального и промышленного транспорта имеют двух-, трех- и четырехосные тележки, а большегрузные транспортеры оснащены многоосными тележками, состоящими из набора перечисленных выше конструкций. Как правило, это модели с одноступенчатым рессорным подвешиванием. Исключение составляют лишь изотермические и некоторые специализированные вагоны, служащие для перевозки грузов, требующих транспортировки с повышенными скоростями.
Двухосные тележки. В связи с недостатками поясных тележек, включая сложность изготовления и ремонта, а также низкую надежность в
|
|
Адаптации растений и животных к жизни в горах: Большое значение для жизни организмов в горах имеют степень расчленения, крутизна и экспозиционные различия склонов...
Автоматическое растормаживание колес: Тормозные устройства колес предназначены для уменьшения длины пробега и улучшения маневрирования ВС при...
Археология об основании Рима: Новые раскопки проясняют и такой острый дискуссионный вопрос, как дата самого возникновения Рима...
Особенности сооружения опор в сложных условиях: Сооружение ВЛ в районах с суровыми климатическими и тяжелыми геологическими условиями...
© cyberpedia.su 2017-2024 - Не является автором материалов. Исключительное право сохранено за автором текста.
Если вы не хотите, чтобы данный материал был у нас на сайте, перейдите по ссылке: Нарушение авторских прав. Мы поможем в написании вашей работы!