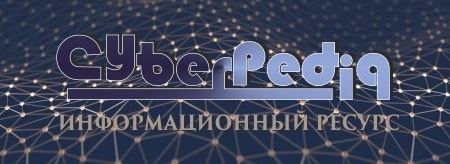
Типы оградительных сооружений в морском порту: По расположению оградительных сооружений в плане различают волноломы, обе оконечности...
История создания датчика движения: Первый прибор для обнаружения движения был изобретен немецким физиком Генрихом Герцем...
Топ:
Устройство и оснащение процедурного кабинета: Решающая роль в обеспечении правильного лечения пациентов отводится процедурной медсестре...
История развития методов оптимизации: теорема Куна-Таккера, метод Лагранжа, роль выпуклости в оптимизации...
Марксистская теория происхождения государства: По мнению Маркса и Энгельса, в основе развития общества, происходящих в нем изменений лежит...
Интересное:
Лечение прогрессирующих форм рака: Одним из наиболее важных достижений экспериментальной химиотерапии опухолей, начатой в 60-х и реализованной в 70-х годах, является...
Распространение рака на другие отдаленные от желудка органы: Характерных симптомов рака желудка не существует. Выраженные симптомы появляются, когда опухоль...
Влияние предпринимательской среды на эффективное функционирование предприятия: Предпринимательская среда – это совокупность внешних и внутренних факторов, оказывающих влияние на функционирование фирмы...
Дисциплины:
![]() |
![]() |
5.00
из
|
Заказать работу |
|
|
Лекция № 38
Глава 8. АВТОМАТИЗАЦИЯ ПРОЦЕССОВ ВАРКИ СТЕКЛА
Основные задачи автоматизации. Функциональная схема автоматизации стекловаренной печи
План
1 Стадии стекловарения
2 Ванная стекловаренная печь
3 Основные задачи автоматизации
4 Функциональная схема системы автоматического регулирования расхода газа с коррекцией по его температуре
5 Функциональная схема системы автоматического регулирования разрежения с коррекцией по давлению в печи
6 Функциональная схема системы автоматического регулирования уровня стекломассы
7 Функциональная схема системы регулирования соотношения газ — воздух
Стадии процесса стекловарения в ванных печах
Процесс стекловарения является основным технологическим процессом производства листового стекла и стеклоизделий. Прежде чем сформулировать задачи автоматизации, кратко рассмотрим основные стадии процесса стекловарения в ванных печах и особенности технологического агрегата — ванной стекловаренной печи.
Обычно рассматривают следующие стадии процесса стекловарения.
Стадия силикатообразования характеризуется тем, что к концу ее основные химические реакции в твердом состоянии между компонентами шихты закончены. В шихте не остается отдельных составляющих ее компонентов, большинство газообразных включений улетучивается. Для обычных натрий-кальциевых стекол эта стадия завершается при температуре 800 — 900 °С и характеризуется плавлением, кипением шихты и постепенным уменьшением объема куч шихты от загрузки в глубину варочной части.
Стадия стеклообразования характеризуется тем, что к концу ее стекломасса становится прозрачной, в ней отсутствуют непроваренные частицы шихты, однако она пронизана большим количеством пузырей и свилей. Эта стадия завершается при температуре 1150 — 1200 °С.
|
Стадия дегазации (осветления) характеризуется тем, что в конце ее стекломасса освобождается от видимых газовых включений, устанавливается равновесное состояние между стекломассой (жидкой фазой) и газами, остающимися в самой стекломассе (газовая среда). Внешним характерным признаком является наличие варочной пены. Отсутствие пены свидетельствует о завершении процесса осветления.
Стадия гомогенизации характеризуется однородностью и освобождением стекломассы от свилей. Визуально для процесса характерно чистое зеркало стекломассы при более низких температурах.
Стадия студки характеризуется снижением температуры на 200 — 300 °С, необходимым для достижения рабочей вязкости стекломассы. После прохождения стадии студки стекломасса при определенной температуре и вязкости поступает на формование, где из нее вырабатывается лента стекла или стеклоизделия.
В настоящее время процесс стекловарения на промышленных предприятиях осуществляют в ванных стекловаренных печах, где догрузка шихты, варка стекла и выработка ленты стекла (или стеклоизделий) происходят в течение всей кампании печи непрерывно и одновременно.
Ванная стекловаренная печь
Ванная стекловаренная печь состоит из бассейна, пламенного пространства, регенераторов, переводных клапанов и загрузчиков шихты. Бассейн представляет собой ванну, выложенную из огнеупорных брусьев и расположенную на самостоятельном основании. Стены бассейна, испытывающие гидростатическое давление стекломассы, обвязывают металлическими креплениями, а варочную часть снабжают дополнительно искусственным охлаждением. Пламенное пространство ограничено стенами и сводом, подвешенными на металлических опорах. Между стенами и бассейном печи оставляют закладываемый огнеупорным кирпичом промежуток (заклинок) высотой до 120 мм для наблюдения за печью и ее обслуживания. Стены и свод выкладывают из динаса и изолируют материалами, стойкими при высоких температурах. Бассейн печи выкладывают из огнеупорных брусьев, например, «Бакор-33», «Бакор-41».
|
Регенераторы представляют собой камеру прямоугольного сечения, внутри которой расположена насадка, выложенная из шамотного кирпича. Регенераторы служат для использования тепла отходящих газов и нагрева воздуха, подаваемого в горелки ванных печей с поперечным направлением пламени. Они могут быть вертикальными и горизонтальными. Чаще применяют вертикальные регенераторы.
Подачу горючего газа и воздуха, а также отвод отходящих газов в регенеративных печах производят с помощью переводных клапанов.
Топливо (газ, мазут) подают в печь обычно через водоохлаждаемые фурмы или форсунки, которые вставлены в щечки горелок. Снизу в горелки подается предварительно подогретый в регенераторах воздух. Топливо поступает по раздельным трубопроводам для каждой стороны печи и разводится по горелкам. Подача воздуха на современных стекольных заводах осуществляется принудительно с помощью вентиляторов под насадки регенераторов.
В настоящее время применяют следующие схемы подачи воздуха: от одного вентилятора в боров; индивидуально в каждую секцию регенератора от общего ветилятора; индивидуально в каждую секцию регенератора от отдельных вентиляторов; отдельно в каждую секцию регенераторов при количестве индивидуальных вентиляторов, уменьшенном вдвое.
Для охлаждения огнеупоров стены стекловаренной печи охлаждают сжатым воздухом.
Автоматизация технологического процесса стекловарения является сложной проблемой. Основной технологический агрегат стекольного производства — ванная стекловаренная регенеративная печь с поперечным направлением пламени представляет собой многозвенный объект с распределенными параметрами, значительной инерционностью и свойством самовыравнивания, подверженный случайным и детерминированным возмущениям, воздействующим как на входные, так и выходные параметры.
В качестве входных параметров объекта регулирования могут быть приняты: расход газа по горелкам, расход воздуха на горение, химический состав шихты, давление в печи, а также ряд дополнительных факторов (температура окружающей среды, атмосферное давление, теплотворная способность газа и пр.).
|
В качестве выходных параметров могут быть приняты: объем отбираемой из печи стекломассы, ее выработочная характеристика — вязкость, зависящая от химического состава и температуры расплава стекломассы.
Схематически стекловаренная печь представляет собой ванну с расплавом стекла, поверхность которого частично покрыта шихтой и варочной пеной. Сверху к поверхности стекломассы примыкает газовое пространство, в котором расположены газовые горелки, направляющие поток тепла в стекломассу.
Для полного математического описания стекловаренной печи необходимо одновременно моделировать процессы, происходящие в газовом пространстве, факелах горелок, шихте и стекломассе. Это сложная и трудоемкая задача. При моделировании процессов, происходящих в стекломассе, последнюю считают однородной несжимаемой ньютоновской жидкостью. Каждый элемент объема характеризуют следующими параметрами: плотностью ρ, давлением Р, температурой Т и скоростью υ.
Литература
1 Кочетов В.С. Автоматизация производственных процессов и АСУП промышленности строительных материалов.- Л.; Стройиздат, 1981. [стр. 300 - 313]
Лекция № 39
Литература
1 Кочетов В.С. Автоматизация производственных процессов и АСУП промышленности строительных материалов.- Л.; Стройиздат, 1981. [стр. 313 - 319]
Лекция № 40
Литература
1 Кочетов В.С. Автоматизация производственных процессов и АСУП промышленности строительных материалов.- Л.; Стройиздат, 1981. [стр. 319 - 328]
Лекция № 41
Основные сведения
Для обеспечения более оптимального режима работы регенераторов, использующих тепло отходящих газов, применяют системы автоматического управления переводом пламени, которые позволяют:
— автоматически выполнять необходимые операции по реверсированию пламени в ванной печи по заданной программе без вмешательства обслуживающего персонала или по его команде;
— сократить до минимума время перевода пламени, что способствует уменьшению потерь тепла;
|
— упростить обслуживание и исключить ошибки по времени между переводами направления пламени.
В результате работы автоматической системы перевода направления пламени происходит повышение производительности стекловаренных печей и снижение удельного расхода топлива.
Наиболее рационально переводить пламя по разности температур верха насадочных решеток регенераторов. Практически же перевод направления пламени на отечественных заводах производят по времени с корректировкой продолжительности. Последовательность работы схемы перевода следующая: системой предусматривается подача предупредительного сигнала о начале перевода направления пламени. После подачи звукового сигнала автоматически отключаются локальные системы автоматического регулирования. Далее прекращается подача топлива на рабочей стороне (2 с), переключаются воздушные и дымовоздушные переводные клапаны (7 с). За время выдержки (3—8 с) происходит удаление газов, открываются клапаны и подается топливо на противоположной стороне стекловаренной печи (2 с). После незначительной паузы включаются локальные регуляторы.
Схема автоматического управления переводом направления пламени предусматривает обычно три режима работы:
— автоматический — команда на перевод дается с помощью моторного реле времени типа МРВ-26м через каждые 30 мин; при технологической необходимости промежутки между переводами могут быть неодинаковыми, но в сумме должны составлять 60 мин;
— полуавтоматический — команда на перевод дается обслуживающим персоналом путем нажатия соответствующей кнопки;
— наладочный — перевод пламени осуществляется путем закрывания и открывания кранов ручного управления, установленных на байпасных линиях, а перевод воздуха — нажатием кнопок, воздействующих непосредственно на магнитные пускатели, управляющие двигателем воздушного шибера.
Литература
1 Кочетов В.С. Автоматизация производственных процессов и АСУП промышленности строительных материалов.- Л.; Стройиздат, 1981. [стр. 329 - 332]
Лекция № 42
Основные сведения
Изменение давления в рабочем пространстве стекловаренной печи существенно влияет на процесс осветления стекломассы и ее температурный режим. При изменении количества тепла, поступающего в печь, необходимо изменять положение дымового шибера так, чтобы поддержать, постоянное давление (нулевое) у зеркала стекломассы. Повышенное давление возникает при увеличении количества газа и воздуха, поступающих на горение. В этом случае продукты горения выбиваются из всех неплотностей кладки печи, устремляются в зоны студки, выработки, нарушая нормальное протекание процесса. Если тяга избыточна, то в газовом пространстве создается разрежение; в рабочее пространство печи через неплотности кладки подсасывается наружный воздух, охлаждающий стекломассу, нарушающий технологический процесс.
|
Давление в ванной стекловаренной печи регулируется системой, работающей по пропорционально-интегральному (ПИ) закону регулирования. В качестве регулирующего органа используется подъемный или поворотный шибер, устанавливаемый на общем дымоходе перед дымовой трубой. Предпочтительным является применение двухкаскадной системы автоматического регулирования давления, принципиальная электрическая схема которой изображена на рис. 122.
Литература
1 Кочетов В.С. Автоматизация производственных процессов и АСУП промышленности строительных материалов.- Л.; Стройиздат, 1981. [стр. 332 - 334]
Лекция № 43
Основные сведения
Поддержание постоянного уровня стекломассы в бассейне стекловаренной печи в значительной мере влияет на процесс стекловарения и выработки стекла. От стабильности уровня стекломассы зависит качество вырабатываемой продукции и износ огнеупорной кладки, которая наиболее интенсивно разрушается на границе раздела стекломассы и газового пространства печи. При поддержании уровня стекломассы постоянным скорость разрушения огнеупорных брусьев существенно снижается за счет теплового равновесия в брусе между теплом, получаемым от бассейна печи, и охлаждением сжатым воздухом наружной стороны бассейна.
Для улучшения технологического режима процесса стекловарения считают целесообразным осуществлять непрерывную загрузку шихты, причем чем длительнее работа загрузчиков, тем равномернее покрытие зеркала стекломассы шихтой. При позиционном регулировании уровня стекломассы в бассейне печи возникает колебательный режим, изменяющий как уровень стекломассы, так и границу шихты и плотной пены. При применении непрерывных регуляторов уменьшается амплитуда колебаний, а потому использование П- и ПИ-регуляторов повышает эффективность системы автоматического регулирования уровня стекломассы и улучшает качество стекломассы, идущей на выработку.
Для контроля уровня стекломассы применяют поплавковые, электроконтактные, пневматические, оптические и радиационные уровнемеры. Наибольшей точностью контроля обладают оптические уровнемеры (например, разработки Киевского филиала ВИАСМ).
В настоящее время предпочтение отдается системам автоматического регулирования уровня с пропорционально-интегральными (ПИ) законами регулирования. Применение более сложных систем для стабилизации уровня стекломассы является целесообразным, так как в этом случае повышается точность поддержания заданного уровня стекломассы и уменьшаются возмущения, вносимые цикличной подачей шихты.
Литература
1 Кочетов В.С. Автоматизация производственных процессов и АСУП промышленности строительных материалов.- Л.; Стройиздат, 1981. [стр. 334 - 339]
Лекция № 44
Основные сведения
В ходе управления технологическими процессами стекловарения и выработки стекла выявляется необходимость в использовании дополнительной визуальной информации, характеризующей состояние того или иного технологического процесса производства.
На стекольных заводах обычно обслуживающий персонал осуществляет визуальный контроль путем непосредственного наблюдения за технологической ситуацией через смотровые отверстия, например, ванной стекловаренной печи. Естественно, такой контроль является кратковременным, так как производится в условиях сильного теплового излучения от стенок технологического агрегата. На современных же стекловаренных агрегатах непосредственный визуальный контроль в значительной мере еще затруднен из-за герметизации бассейна стекловаренной печи.
Применение технологического телевидения открывает перед производственниками и исследователями широкие возможности для качественного и непрерывного контроля за ходом процесса стекловарения в ванных печах с поста управления.
Использование телевизионных методов дает возможность наблюдать кинетику плавления стекольной шихты, изменение формы и границы варочной пены, состояние огнеупорной кладки, форму и ориентацию факела, состояние регенеративных насадок и других характерных визуальных признаков.
В то же время применение телевизионного контроля дает возможность герметизировать технологические агрегаты, что способствует стабилизации технологического и теплового режимов процесса стекловарения и выработки стекла, а также удлинению кампании стекловаренных агрегатов.
Для ведения процесса стекловарения необходим контроль следующих характерных визуальных признаков состояния процесса: положения куч шихты; положения границы раздела пены и чистой стекломассы; формы факелов; направления потока шихты; переключения и включения горелок во время цикла регенерации; состояния футеровки.
Одновременный контроль перечисленных факторов, каждый из которых обладает своими отличительными особенностями, до недавнего времени производился стекловаром только визуально.
В настоящее время наиболее широко технологическое телевидение в нашей стране и за рубежом используется при производстве стекла способом плавающей ленты.
Для контроля технологической ситуации во флоат-ванне применяют четыре телевизионные камеры, соединенные с отдельным видеоконтрольным устройством. С помощью этих камер оператор следит за прохождением формуемой ленты стекла через ванну с расплавом металла, вздутием ленты в средней части, положением бортоформующих валков, отклонением плавающей ленты в сторону, вследствие чего может произойти деформация, разрыв ленты и, как следствие, останов технологического агрегата. Телевизионные камеры устанавливаются с двух сторон ванны с расплавом металла. Для контроля процесса растекания стекломассы и ширины ленты стекла камеры устанавливают со стороны слива стекломассы в ванну с расплавом.
Применение системы технологического телевидения и видеозаписи дает возможность оператору более успешно определить оптимальное положение квельпункта в бассейне печи и выяснить необходимость изменения температурного режима для коррекции этого положения.
Следует отметить, что применение устройства видеозаписи, кроме уже перечисленных преимуществ, целесообразно для записи на магнитную ленту тех или иных технологических ситуаций, которые могут длительно храниться и быть использованы для технологической наладки агрегатов и обучения обслуживающего персонала.
Литература
1 Кочетов В.С. Автоматизация производственных процессов и АСУП промышленности строительных материалов.- Л.; Стройиздат, 1981. [стр. 339 - 347]
Лекция № 38
Глава 8. АВТОМАТИЗАЦИЯ ПРОЦЕССОВ ВАРКИ СТЕКЛА
|
|
Опора деревянной одностоечной и способы укрепление угловых опор: Опоры ВЛ - конструкции, предназначенные для поддерживания проводов на необходимой высоте над землей, водой...
Типы сооружений для обработки осадков: Септиками называются сооружения, в которых одновременно происходят осветление сточной жидкости...
Наброски и зарисовки растений, плодов, цветов: Освоить конструктивное построение структуры дерева через зарисовки отдельных деревьев, группы деревьев...
Общие условия выбора системы дренажа: Система дренажа выбирается в зависимости от характера защищаемого...
© cyberpedia.su 2017-2024 - Не является автором материалов. Исключительное право сохранено за автором текста.
Если вы не хотите, чтобы данный материал был у нас на сайте, перейдите по ссылке: Нарушение авторских прав. Мы поможем в написании вашей работы!