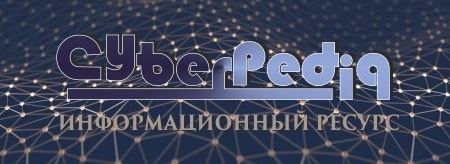
Таксономические единицы (категории) растений: Каждая система классификации состоит из определённых соподчиненных друг другу...
Археология об основании Рима: Новые раскопки проясняют и такой острый дискуссионный вопрос, как дата самого возникновения Рима...
Топ:
Характеристика АТП и сварочно-жестяницкого участка: Транспорт в настоящее время является одной из важнейших отраслей народного...
Оценка эффективности инструментов коммуникационной политики: Внешние коммуникации - обмен информацией между организацией и её внешней средой...
Основы обеспечения единства измерений: Обеспечение единства измерений - деятельность метрологических служб, направленная на достижение...
Интересное:
Уполаживание и террасирование склонов: Если глубина оврага более 5 м необходимо устройство берм. Варианты использования оврагов для градостроительных целей...
Как мы говорим и как мы слушаем: общение можно сравнить с огромным зонтиком, под которым скрыто все...
Что нужно делать при лейкемии: Прежде всего, необходимо выяснить, не страдаете ли вы каким-либо душевным недугом...
Дисциплины:
![]() |
![]() |
5.00
из
|
Заказать работу |
Устройство и эксплуатация центробежных нагнетателей
Назначение и устройство ЦБН
Центробежные нагнетатели служат для компримирования (сжатия) природного газа, транспортируемого по магистральным газопроводам.
По числу ступеней нагнетатели делятся на одноступенчатые и многоступенчатые. Основное различие этих машин в конструкции ротора. В одноступенчатых нагнетателях используется ротор консольного типа с одним рабочим колесом, насаженным на консольный участок вала. В двухступенчатых нагнетателях применяются двух опорный (межопорный) ротор с двумя рабочими колесами.
По конструкции корпуса нагнетатели делятся на однокорпусные и двухкорпусные. Все одноступенчатые нагнетатели имеют один прочный корпус с торцевой крышкой. Преимуществом одноступенчатых нагнетателей является то, что торцевая крышка выполняется глухой. При консольном расположении ротора используется одностороннее расположение подшипников и сальников вала в корпусе нагнетателя, поэтому торцевая крышка не является несущей и не имеет отверстия. Такая конструкция крышки облегчает вскрытие полости нагнетателя и не требует снятия подшипников и сальника при разборке нагнетателя.
Большинство двухступенчатых нагнетателей двухкорпусные. Наружный прочный корпус рассчитан на максимальное давление газа в нагнетателе. Он имеет стальную литейно-кованную и литейно-сварную конструкцию и уплотняется массивными торцевыми крышками, в которых расположены подшипники и сальники вала. Газовые коммуникации подсоединяются к прочному корпусу. Прочный корпус выполняется массивным, что обеспечивает не только прочность, но и жесткость конструкции, необходимую для центровки нагнетателя.
Внутренний корпус собирается отдельно и включает в себя проточную часть нагнетателя.
По конструкции проточной части нагнетатели различаются устройством диффузоров и нагнетательных полостей.
В нагнетателях используются лопаточные диффузоры (ЛД) и безлопаточные диффузоры (БЛД).
Лопаточный диффузор имеет преимущество перед БЛД в организации потока на выходе из рабочего колеса, поэтому обладает повышенным газодинамическим КПД. Расчетные значения давления на выходе из диффузора достигаются на меньшем диаметре, поэтому он обеспечивает меньшие габариты нагнетателей. Недостатком лопаточного диффузора является более крутая напорная характеристика, что ухудшает точность регулирования рабочей точки.
Безлопаточный диффузор оказывает меньшее динамическое воздействие на рабочее колесо, имеет более пологую напорную характеристику прост в изготовлении.
В качестве нагнетательных устройств используются боковые спиральные улитки с изменяющимся проходным сечением и боковые сборные кольцевые камеры. Нагнетательная улитка является диффузорным элементом, поэтому в ней вырабатывается дополнительное статическое давление за счет снижения скорости газа. Недостаток спиральной улитки – усложненная конструкция проточной части нагнетателя.
Сборная кольцевая камера имеет преимущество в организации равномерного потока на выходе из нагнетателя, за счет чего снижается динамическое воздействие потока на ротор нагнетателя. Она имеет простую конструкцию и более технологична.
По перепаду давления нагнетатели делятся на полнонапорные и неполнонапорные.
Все двухступенчатые нагнетатели - полнонапорные, со степенью сжатия ε=1,55, способны в одном агрегате выработать необходимый для ГКС перепад давления.
Большинство одноступенчатых нагнетателей – неполнонапорные, со степенью сжатия ε=1,25. Для обеспечения необходимого для ГКС перепада давления они должны включаться в технологическую схему последовательно, по две или три в одной линии.
Нагнетатель состоит из следующих основных узлов: корпуса, ротора, подшипников и элементов системы уплотнения.
Неполнонапорный нагнетатель представляет собой одноступенчатый компрессор. Проточная часть нагнетателя состоит из конфузора, канала рабочего колеса, лопаточного диффузора и сборной кольцевой камеры, образованной улиткой. Ротор состоит из вала, рабочего колеса и обтекателя. Ходовая часть нагнетателя (ротор, подшипники, торцевое масляное уплотнение и другие элементы) заключена в специальную гильзу, устанавливаемую в корпус нагнетателя. Ротор вращается на двух подшипниках скольжения. Один, ближний к рабочему колесу. является опорным подшипником. Второй опорно-упорный (ОУП). Для предотвращения проникновения газа из нагнетателя в галерею нагнетателей, а также масла в проточную часть нагнетателя применено торцевое масляное уплотнение вала. Подробное описание устройства нагнетателя смотри в приложении.
Полнонапорный нагнетатель представляет собой двухступенчатый компрессор. Вся ходовая часть и внутренняя статорная часть комбинированные торцевые и лабиринтные уплотнения, диффузоры, обратный направляющий аппарат и другие элементы выполнены в виде пакета, устанавливаемого в корпус.
Ротор имеет два рабочих колеса, расположенных между опорными шейками вала. Рабочие колеса одинаковой конструкции отличаются только шириной лопаток. Лопатки отфрезерованы из тела основного диска. Покрывающий диск соединяется с основными заклепками, пропущенными через тело лопаток. Рабочие колеса насажены на вал с гарантированным натягом.
Для уменьшения осевого усилия непосредственно за вторым рабочим колесом также с натягом на вал насажен разгрузочный поршень-думмис
На валу также установлен диск упорного подшипника. Ротор вращается в двух одинаковых по конструкции опорных вкладышах. Вкладыш является одновременно втулочным уплотнением, служащим для поддержания давления масла в полости торцового уплотнения.
Для восприятия осевых усилий, действующих на ротор нагнетателя, и для установки ротора в заданном осевом положении относительно неподвижных элементов служит упорный подшипник.
В основу системы уплотнения вала полнонапорных нагнетателей также положен принцип гидравлического затвора.
В современных конструкциях нагнетателей природного газа используются различные конструкции сальников вала. Наибольшее распространение получили сальники двух типов: с торцовым уплотнением и с плавающими кольцами (втулками).
Для поддержания требуемых давления и расхода компримируемого газа центробежные нагнетатели включают по следующей схеме: один нагнетатель (полнонапорный или неполнонапорный); два последовательно работающих неполнонапорных нагнетателя; две (или более) группы неполнонапорных нагнетателей, включенных в газопровод параллельно; один, два или более неполнонапорных нагнетателей, работающих на промежуточный коллектор (первая ступень сжатия), в который включено соответствующее число неполнонапорных нагнетателей второй ступени.
Последовательная работа двух центробежных нагнетателей необходима для поддержания тре6уемого давления газа на участке газопровода между КС. Параллельное включение в работу или трех групп последовательно работающих: неполнонапорных нагнетателей или полнонапорных нагнетателей обеспечивает повышенную производительность КС при сохранении требуемого давления газа в МГ.
Основными параметрами работы нагнетателей являются: давление газа, степень сжатия, температура газа, объемная производительность и частота вращения силового вала, см. таблицу.
Подготовка нагнетателя к пуску
Газоперекачивающий агрегат КЦ готовят к пуску по распоряжению сменного инженера после согласования с центральной диспетчерской службой объединения. Машинист, получивший задание на подготовку нагнетателя к пуску, выполняет следующее:
– проверяет положение кранов технологической обвязки нагнетателя:
– краны № 1; 2; 4; 6 – должны быть закрыты;
– краны № 3; 3-бис; 5 – должны быть открыты;
– подает импульсный газ на узлы управления кранами;
– подсоединяет шланги импульсных линий к штуцерам пневмоцилиндров кранов;
– проверяет положение кранов топливного и пускового газа:
– краны № 11; 12; 13; СК; РК – должны быть закрыты;
– краны № 9; 10; 11-бис; 12-бис – должны быть открыты.
– проверяет наличие топливного и пускового газа;
– производит осмотр воздухозаборной камеры, чтобы убедиться в отсутствии посторонних предметов, делает соответствующую запись в журнал осмотра ВЗК;
– проверяет уровень масла в МБ агрегата: и температуру масла она должна быть не менее 25°С);
– проверяет наличие напряжения»220 В,»380 В и =220 В, =27 В (табло «Есть напряжение на агрегате»).
После выполнения вышеперечисленных операций на агрегатной панели загорается табло «Агрегат готов к пуску».
Остановка агрегата
Нормальная остановка происходит по команде сменного персонала нажатием кнопки «н/о» при этом происходит открытие крана № 6, снижается частота вращения силового вала; разгружается нагнетатель: краны № 3, 3¢ – открываются; краны № 1, 2 – закрываются кран № 5 открывается для выпуска газа из полости нагнетателя в атмосферу. При давлении газа в полости нагнетателя менее 2 кгс/см2 отключается маслонасос уплотнения. Закрывается регулирующий клапан на подаче топлива в камеру сгорания. Температура газа перед турбиной снижается. Затем закроется стопорный клапан и кран № 12 топливного газа, откроются выпускные воздушные клапана и кран № 9. После выбега роторов снижения температуры: за ТНД < 100 °С, подшипников < 70°С, останавливается пусковой насос смазки. В суточной ведомости агрегата машинист проставляет дату и время остановки агрегата. Подробное описание нормальной остановки смотри в главе 3.12 настоящего пособия.
Вывод агрегата в резерв
Вывод ГПА в резерв осуществляется сменным персоналом под руководством сменного инженера по распоряжению начальника цеха или инженера по эксплуатации.
При выводе агрегата в резерв машинист обязан:
– закрыть кран на коллекторе подвода импульсного газа к узлам управления кранами технологической обвязки нагнетателя, топливного и пускового газа ГПА №1, 2, 3, 3-бис, 4, 5, 6, 9, 10, 11, 12;
– стравить газ с линий импульсного газа кранами № 1, 2, 3, 4, 5, 6, 9, 10, 11, 12;
– снять шланги, соединяющие коллектор подвода импульсного газа к узлам управления кранами;
– проверить снятие шлангов со штуцеров пневмоцилиндров кранов № 1, 2, 4, 6, 11, 12 на открытие; кранов № З, З-бис, 5, 9, 10 на закрытие;
– отключить питание цепей управления кранами.
О проделанной работе машинист докладывает сменному инженеру, который фиксирует в оперативном журнале дату и время вывода агрегата в резерв.
Вывод агрегата в ремонт
Агрегат к ремонту готовит сменный персонал по распоряжению начальника цеха. Перед началом ремонтных работ сменный персонал должен произвести следующие мероприятия:
– перекрыть и стравить импульсный газ на узлы управления кранами технологической обвяэки нагнетателя, топливного и пускового газа ГПА № 1, 2, 3, З-бис, 4, 5, 6, 9, 10, 11, 12;
– снять шланги с пневмоцилиндров кранов № 1, 2, 3, 3-бис, 4, 5, 6, 9, 10, 11, 12;
– снять шланги соединяющего коллектора подвода импульсного газа и узлы управления кранами (обеспечен видимый разрыв); Все снятые шланги с пневмоцилиндров кранов и линий импульсного газа, сдать на хранение в специальный ящик на ГЩУ;
– на кран № 4 установить «блок-замок»;
– снять штурвалы с кранов № З, 3¢;
– на краны № 1, 2, 4, 6, 11, 12 вывести плакаты «Не открывать»;
– на краны № 3, З-бис, 5, 9, 10 вывесить плакаты «Не закрывать»;
– установить заглушки на штуцерах пневмоцилиндров кранов;
– набить смазкой краны № 1, 2, 4, 6, 11, 12;
– установить силовые заглушки на кранах 11-бис и 12-бис во фланцевых соединениях после кранов 11-бис и 12-бис по ходу газа;
– отключить питание цепей управления кранами;
– на ГЩУ и местном щите управления вывесить плакаты «Не включать, работают люди»;
– в оперативном журнале сменного инженера зафиксировать дату и время вывода агрегата в ремонт.
Машинист обязан при приеме смены, 1 раз в смену и при сдаче смены проводить проверку состояния запорной арматуры и органов управления на ГПА, находящихся в резерве и ремонте.
Устройство и эксплуатация центробежных нагнетателей
Назначение и устройство ЦБН
Центробежные нагнетатели служат для компримирования (сжатия) природного газа, транспортируемого по магистральным газопроводам.
По числу ступеней нагнетатели делятся на одноступенчатые и многоступенчатые. Основное различие этих машин в конструкции ротора. В одноступенчатых нагнетателях используется ротор консольного типа с одним рабочим колесом, насаженным на консольный участок вала. В двухступенчатых нагнетателях применяются двух опорный (межопорный) ротор с двумя рабочими колесами.
По конструкции корпуса нагнетатели делятся на однокорпусные и двухкорпусные. Все одноступенчатые нагнетатели имеют один прочный корпус с торцевой крышкой. Преимуществом одноступенчатых нагнетателей является то, что торцевая крышка выполняется глухой. При консольном расположении ротора используется одностороннее расположение подшипников и сальников вала в корпусе нагнетателя, поэтому торцевая крышка не является несущей и не имеет отверстия. Такая конструкция крышки облегчает вскрытие полости нагнетателя и не требует снятия подшипников и сальника при разборке нагнетателя.
Большинство двухступенчатых нагнетателей двухкорпусные. Наружный прочный корпус рассчитан на максимальное давление газа в нагнетателе. Он имеет стальную литейно-кованную и литейно-сварную конструкцию и уплотняется массивными торцевыми крышками, в которых расположены подшипники и сальники вала. Газовые коммуникации подсоединяются к прочному корпусу. Прочный корпус выполняется массивным, что обеспечивает не только прочность, но и жесткость конструкции, необходимую для центровки нагнетателя.
Внутренний корпус собирается отдельно и включает в себя проточную часть нагнетателя.
По конструкции проточной части нагнетатели различаются устройством диффузоров и нагнетательных полостей.
В нагнетателях используются лопаточные диффузоры (ЛД) и безлопаточные диффузоры (БЛД).
Лопаточный диффузор имеет преимущество перед БЛД в организации потока на выходе из рабочего колеса, поэтому обладает повышенным газодинамическим КПД. Расчетные значения давления на выходе из диффузора достигаются на меньшем диаметре, поэтому он обеспечивает меньшие габариты нагнетателей. Недостатком лопаточного диффузора является более крутая напорная характеристика, что ухудшает точность регулирования рабочей точки.
Безлопаточный диффузор оказывает меньшее динамическое воздействие на рабочее колесо, имеет более пологую напорную характеристику прост в изготовлении.
В качестве нагнетательных устройств используются боковые спиральные улитки с изменяющимся проходным сечением и боковые сборные кольцевые камеры. Нагнетательная улитка является диффузорным элементом, поэтому в ней вырабатывается дополнительное статическое давление за счет снижения скорости газа. Недостаток спиральной улитки – усложненная конструкция проточной части нагнетателя.
Сборная кольцевая камера имеет преимущество в организации равномерного потока на выходе из нагнетателя, за счет чего снижается динамическое воздействие потока на ротор нагнетателя. Она имеет простую конструкцию и более технологична.
По перепаду давления нагнетатели делятся на полнонапорные и неполнонапорные.
Все двухступенчатые нагнетатели - полнонапорные, со степенью сжатия ε=1,55, способны в одном агрегате выработать необходимый для ГКС перепад давления.
Большинство одноступенчатых нагнетателей – неполнонапорные, со степенью сжатия ε=1,25. Для обеспечения необходимого для ГКС перепада давления они должны включаться в технологическую схему последовательно, по две или три в одной линии.
Нагнетатель состоит из следующих основных узлов: корпуса, ротора, подшипников и элементов системы уплотнения.
Неполнонапорный нагнетатель представляет собой одноступенчатый компрессор. Проточная часть нагнетателя состоит из конфузора, канала рабочего колеса, лопаточного диффузора и сборной кольцевой камеры, образованной улиткой. Ротор состоит из вала, рабочего колеса и обтекателя. Ходовая часть нагнетателя (ротор, подшипники, торцевое масляное уплотнение и другие элементы) заключена в специальную гильзу, устанавливаемую в корпус нагнетателя. Ротор вращается на двух подшипниках скольжения. Один, ближний к рабочему колесу. является опорным подшипником. Второй опорно-упорный (ОУП). Для предотвращения проникновения газа из нагнетателя в галерею нагнетателей, а также масла в проточную часть нагнетателя применено торцевое масляное уплотнение вала. Подробное описание устройства нагнетателя смотри в приложении.
Полнонапорный нагнетатель представляет собой двухступенчатый компрессор. Вся ходовая часть и внутренняя статорная часть комбинированные торцевые и лабиринтные уплотнения, диффузоры, обратный направляющий аппарат и другие элементы выполнены в виде пакета, устанавливаемого в корпус.
Ротор имеет два рабочих колеса, расположенных между опорными шейками вала. Рабочие колеса одинаковой конструкции отличаются только шириной лопаток. Лопатки отфрезерованы из тела основного диска. Покрывающий диск соединяется с основными заклепками, пропущенными через тело лопаток. Рабочие колеса насажены на вал с гарантированным натягом.
Для уменьшения осевого усилия непосредственно за вторым рабочим колесом также с натягом на вал насажен разгрузочный поршень-думмис
На валу также установлен диск упорного подшипника. Ротор вращается в двух одинаковых по конструкции опорных вкладышах. Вкладыш является одновременно втулочным уплотнением, служащим для поддержания давления масла в полости торцового уплотнения.
Для восприятия осевых усилий, действующих на ротор нагнетателя, и для установки ротора в заданном осевом положении относительно неподвижных элементов служит упорный подшипник.
В основу системы уплотнения вала полнонапорных нагнетателей также положен принцип гидравлического затвора.
В современных конструкциях нагнетателей природного газа используются различные конструкции сальников вала. Наибольшее распространение получили сальники двух типов: с торцовым уплотнением и с плавающими кольцами (втулками).
Для поддержания требуемых давления и расхода компримируемого газа центробежные нагнетатели включают по следующей схеме: один нагнетатель (полнонапорный или неполнонапорный); два последовательно работающих неполнонапорных нагнетателя; две (или более) группы неполнонапорных нагнетателей, включенных в газопровод параллельно; один, два или более неполнонапорных нагнетателей, работающих на промежуточный коллектор (первая ступень сжатия), в который включено соответствующее число неполнонапорных нагнетателей второй ступени.
Последовательная работа двух центробежных нагнетателей необходима для поддержания тре6уемого давления газа на участке газопровода между КС. Параллельное включение в работу или трех групп последовательно работающих: неполнонапорных нагнетателей или полнонапорных нагнетателей обеспечивает повышенную производительность КС при сохранении требуемого давления газа в МГ.
Основными параметрами работы нагнетателей являются: давление газа, степень сжатия, температура газа, объемная производительность и частота вращения силового вала, см. таблицу.
Биохимия спиртового брожения: Основу технологии получения пива составляет спиртовое брожение, - при котором сахар превращается...
История создания датчика движения: Первый прибор для обнаружения движения был изобретен немецким физиком Генрихом Герцем...
Особенности сооружения опор в сложных условиях: Сооружение ВЛ в районах с суровыми климатическими и тяжелыми геологическими условиями...
История развития пистолетов-пулеметов: Предпосылкой для возникновения пистолетов-пулеметов послужила давняя тенденция тяготения винтовок...
© cyberpedia.su 2017-2024 - Не является автором материалов. Исключительное право сохранено за автором текста.
Если вы не хотите, чтобы данный материал был у нас на сайте, перейдите по ссылке: Нарушение авторских прав. Мы поможем в написании вашей работы!