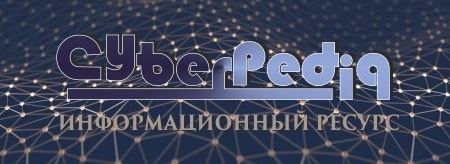
Археология об основании Рима: Новые раскопки проясняют и такой острый дискуссионный вопрос, как дата самого возникновения Рима...
Индивидуальные и групповые автопоилки: для животных. Схемы и конструкции...
Топ:
Эволюция кровеносной системы позвоночных животных: Биологическая эволюция – необратимый процесс исторического развития живой природы...
Особенности труда и отдыха в условиях низких температур: К работам при низких температурах на открытом воздухе и в не отапливаемых помещениях допускаются лица не моложе 18 лет, прошедшие...
Характеристика АТП и сварочно-жестяницкого участка: Транспорт в настоящее время является одной из важнейших отраслей народного...
Интересное:
Распространение рака на другие отдаленные от желудка органы: Характерных симптомов рака желудка не существует. Выраженные симптомы появляются, когда опухоль...
Искусственное повышение поверхности территории: Варианты искусственного повышения поверхности территории необходимо выбирать на основе анализа следующих характеристик защищаемой территории...
Аура как энергетическое поле: многослойную ауру человека можно представить себе подобным...
Дисциплины:
![]() |
![]() |
5.00
из
|
Заказать работу |
|
|
В качестве сырья для производства древесноволокнистых плит используют отходы лесопиления и деревообработки, дровяное долготье, мелкий круглый лес от рубок ухода и лесосечные отходы.
Подготовка сырья к производству заключается в приготовлении техноло-гической щепы (для внутреннего слоя) и стружки (для наружных слоев). Для наружных слоев трехслойных плит рекомендуется в первую очередь использовать древесину хвойных пород в виде кругляка, колотой древесины, карандашей и др.
Для наружных и внутренних слоев плит используем следующий породный состав древесного сырья: сосна, береза, осина (соотношение хвойных пород к лиственным – 60:40). На станки для переработки сырья поступает древесина со строго определенными размерами: длиной и толщиной (диаметром). Поэтому все сырье перед поступлением к стружечным станкам разделывают по длине и тол-щине (диаметру).
Толщина (диаметр) перерабатываемого сырья ограничивается размерами проходного окна питателя рубительной машины. Для разделки по длине длин-номерное сырье в пучках для наружных слоев поступает сначала в разобщитель 1, который раскатывает пучки в однорядный слой и поштучно выдает бревна или хлысты на многопильный станок для разделки сырья по длине 2, в ко-тором сырье разделывают на чураки длиной 1 м. На линии переработки сырья для наружного слоя плит устанавливаем один станок для разделки сырья по длине ДЦ-10.
После станка 2 раскроенное длинномерное сырье поступает по ленточному конвейеру через конвейер питатель в стружечный станок 5. На лини устанавливаем один стружечный станок ДС-6.
По скребковому конвейеру 6 стружка от стружечного станка 5 поступает в бункер 7. Используем три вертикальных бункера ДБО-60, один из которых – ре-зервный. Из бункера 7 стружка далее поступает в барабанную сушилку 8, где высушивается до влажности 5%. Устанавливаем три барабанных сушилки Н167-66, одна из которых – резервная. В качестве агента сушки выступают топочные газы с на-чальной температурой 3350С.
|
Высушенная стружка поступает через циклон в противопожарный бункер 10, где подвергается дополнительному охлаждению, откуда далее направляется в меха-ническую сортировку 11. На данной стадии устанавливаем качающуюся меха-ническую сортировку ДРС-2. Стружка допустимых размеров через циклон поступает вертикальный бункер 12, на котором дополнительно установлены весы 13. Исполь-зуем три бункера ДБО-60 (из них один – резервный). Стружку на данной стадии необ-ходимо дозировать по весу. Так как в бункере ДБО-60 весы не предусмотрены, устанавливаем дополнительно весы ОДКЧ-200А. Из бункера 12, дозированная масса стружки поступает в бункер питатель 14 откуда далее в смеситель 15. На данной линии используем малогабаритный скоростной смеситель с безвоз-душным распылением связующего ДСМ-5.
Из смесителя осмоленная стружка влажностью 15% поступает на конвейер распределения осмоленной стружки 17 по формирующим машинам 18 и 19. Фор-мирующие машины 18 предназначены для фракционирования стружки и форми-рования наружных слоев; 19 – для фракционирования стружки и формирования внутреннего слоя. До стадии формирования необходимо рассмотреть еще одну ли-нию поступления осмоленной стружки на конвейер 17.
Технологическая щепа и щепа из отходов по ленточному конвейеру 20 пос-тупает в механическую сортировку 11, где крупные частицы отсеиваются и поступают в рубительную машину 21. На данной линии используем рубительную машину 250×650Н-6WT немецкой фирмы «Клёкнер». После нее измельченная щепа через циклон вновь поступает на механическую сортировку 11. Из 11 мелкая щепа, не подходящая для производства (размеры которой меньше 0,5 мм), удаля-ется на сжигание. Щепа необходимых размеров поступает далее по скребковому конвейеру в бункер хранения щепы 7. На данной стадии необходимо установить три бункера ДБО-60, один из которых – резервный. Щепа и мелкие кусковые отходы из бункера 7 подаются в стружечные станки 22. На данной линии устанавливаем два центробежных стружечных станка ДС-7А. От станков 22 по скребковому конвейеру 24 стружка толщиной 0,4 мм от стружечных станков пос-тупает на промежуточное хранение в вертикальные бункера 7 а далее в барабанные сушильные установки 8, где высушивается до влажности 2,5%. Сюда же пос-тупают мелкие частицы и пыль от станка шлифования и сортировки плит. Устанав-ливаем три сушильные установки, одна из которых – резервная. В качестве су-шильного агента в сушилках выступают топочные газы с начальной температурой 450оС.
|
Из барабанных сушилок высушенная стружка пневмотранспортом, после очистки в циклонах, попадает на дополнительное охлаждение в противопожарный бункер 10 откуда далее поступает на стадию сортировки в сортировочную машину 25. В качестве сортировочной машины используем двухступенчатый пневматичес-кий сепаратор ДПС-1. Повторное сортирование позволит нам повысить качество изготовляемых древесностружечных плит (в частности – наружных слоев).
После первой ступени пневматической сепарации кондиционная стружка для наружных слоев толщиной 0,15 – 0,25 мм пневмотранспортом подается через циклон в бункер 7, откуда через весы 13 поступает последовательно в бункер-пита-тель 14, смеситель 15 для наружных слоев и далее на конвейер распределения осмоленной стружки 17. Кондиционная стружка толщиной 0,35 – 0,45 мм для внут-реннего слоя поступает на вторую ступень сепарации.
На второй стадии сепарации часть стружки пневмотранспортом подается через циклон в вертикальный бункер хранения стружки для внутреннего слоя 7. На данной стадии устанавливаем пять бункеров ДБО-60, один из которых – резерв-ный. В дополнение к ним для дозирования стружки по массе устанавливаем весы 13 и выравнивающий бункер-питатель 14 откуда далее в смеситель 15 для внутрен-него слоя и последовательно на конвейер распределения поступает осмоленная стружка. Вторая часть стружки попадает в дробилку 26, где повторно измельчается и подается через циклон пневмотранспортом в противопожарный бункер, где, сме-шиваясь со стружкой, поступающей из сушильных установок, поступает на пов-торную пневматическую сепарацию. На стадии повторного измельчения исполь-зуем дробилку ДМ-7.
|
Формирование непрерывного стружечного ковра (пакетов) из осмоленной стружки и горячее прессование древесностружечных плит происходит на автома-тической линии 26 – главном конвейере. Используем конвейер для прессования плит на поддонах, в котором все основные агрегаты и связывающая их система транспортных средств расположены по замкнутому контуру. Размеры поддонов, мм: длина (без зацепа) 3700, ширина 1895; размеры сформированного пакета, мм: длина 3550, ширина 1800, высота 200. Поддоны перемещаются цепными и ролико-выми конвейерами по замкнутому пути. Формирующие машины непрерывно дозируют и равномерно выдают (насыпают) стружку на движущиеся внизу поддоны. Для образования стружечного ковра, состоящего из трех слоев, отлича-ющихся размерами древесных частиц и содержанием связующего, в главном конвейере устанавливают последовательно друг за другом четыре формирующих машины. Формирующая ДФ-6 (подробное описание в приложении Б), приме-няемая в нашем случае, состоит из дозатора бункерного типа и питателя. Машина обеспечивает двухступенчатое дозирование: объемное с помощью вальца и весовое — ковшовыми весами. После объемного и весового дозирования осмоления стружка порциями одна за другой с небольшим смещением высыпается на конвейер, образуя на нем непрерывный слой значительной толщины (300…800 мм). Этот слой надвигается на вращающиеся зубчатые вальцы (n = 130…290 мин-1), которые захватывают стружку и сбрасывают ее вниз в рассеивающее устройство и далее на поддоны формирующего конвейера.
Формирующая машина ДФ-6 в сочетании с рассеивающим устройством ДРФ-1 или ДРФ-2 обеспечивает высокое качество формирования стружечного ковра.
Распределение стружки по ширине бункера-дозатора формирующей, машины достигается установкой над ней распределителя ДРМ-1 маятникового типа, течка для стружки которого получает качательное движение. Стружечный ковер фор-мируется на поддонах в виде бесконечной ленты с последующим разделением ее на заготовки (пакеты) определенной длины. Формирующий конвейер (участок под формирующими машинами) движется непрерывно и с равномерной скоростью 4,3 м/мин для получения равномерного стружечного ковра.
|
Стружечный ковер, разделенный на заготовки, поступает через метало-искатель 27 на предварительную подпрессовку в холодный гидравлический пресс для предварительной подпрессовки пакетов 28. При подпрессовке мы уменьшаем высоту прессуемых пакетов, устраняем просыпание мелких древесных частиц в нижнюю часть пакета при его транспортировке на поддонах, устраняем осыпание кромок пакетов, избегаем раздувание пакетов воздушным потоком во время смы-кания плит горячего многоэтажного пресса. Далее стружечный пакет на поддоне поступает на платформу контрольных весов 29. Масса пакета, находящегося на платформе, воспринимается рычажным механизмом и циферблатным указа-тельным прибором. На циферблате устанавливаем ограничительные контакты, ограничивающие допускаемое отклонение массы пакетов от заданной (расчетной), которое не должно превышать ± 3%. При отклонении дается световой сигнал и ко-манда специальному устройству для удаления таких пакетов с конвейера.
Нагрев стружечного пакета в период прессования осуществляем путем подачи под давлением перпендикулярно его плоскости пара, обладающего боль-шой теплоемкостью и способного передавать значительное количество теплоты. Для его осуществления необходимо иметь парогенератор и систему трубопро-водов. Обогреваемые плиты пресса имеют высверленные отверстия, через которые пар направляется в брикет. Для лучшего распределения пара по плоскости брикета с обеих его сторон предусматриваем проницаемые металлические поддоны. Про-должительность подачи пара – 53 с, так как толщина готовой плиты 19 мм.
Прессование осуществляется в многоэтажном гидравлическом прессе 30. Используем пресс А4743Б. Влажность осмоленной стружки наружных и внутрен-него слоев – 15% и 10% соответственно. Шаг конвейера tк = 4300 мм. Продол-жительность цикла прессования τц = 10 мин. Температура прессования 1800С. Пос-ле выдержки брикетов в прессе под давлением по их толщине отверждается связующее, склеивающее древесные частицы, в результате чего получается проч-ная древесностружечная плита. После этого пресс размыкается, к нему подходит разгрузчик, захватывает специальными захватами поддоны и при обратном движе-нии вытаскивает их с плитами из рабочих промежутков пресса на полки разгрузоч-ной этажерки. Этажерка начинает последовательно на один этаж опускаться и поддоны с плитами выгружаются из нее на конвейер, который направляется к мес-ту отделения готовых древесностружечных плит от поддонов.
|
После горячего прессования в плитах образуются внутренние напряжения, которые с течением времени (при охлаждении или кондиционировании) вырав-ниваются. Поэтому после выгрузки из пресса плиты сначала охлаждаются или кондиционируются в веерном охладителе 31 и только потом поступают на меха-ническую обработку. Одновременно в охладителе может находится не менее 15 – 16 плит (по числу промежутков пресса). Остальные ячейки пустые и расположены ниже осевой линии. За время поворота ячейки на 180оС плиты охлаждаются до 50 – 70оС в зависимости от температуры в цехе и затем передаются по роликовому конвейеру на штабелеукладчик 32, который укладывает их в пакеты. Плиты охла-ждаются только за счет омывания их воздухом. Сигнал на включение двигатель привода веера получает от разгрузочной этажерки пресса 30.
После горячего прессования древесностружечные плиты обрезаем на фор-матообрезном станке 33, в котором поперечные и продольные кромки обрезаются двумя парами неподвижных пил, расположенных под углом 90оС друг к другу. Мимо них с помощью цепных конвейеров перемещается плита. Обрезаемые рейки измельчаются в дробленку фрезами, установленными рядом с пилами на валу электродвигателей пильных головок, и удаляются эксгаустерной установкой в про-тивопожарный бункер 10 через циклон посредством пневмотранспорта.
Обрезанные плиты поступают на станок шлифования и сортировки плит 34. Шлифование древесностружечных плит осуществляем на широколенточном шли-фовальном станке шлифовальными лентами с постепенно уменьшающейся зернис-тостью. Шлифовальный станок выполняем в виде отдельных функциональных блоков: калибровального, калибровально-шлифовального (промежуточного), и шлифовального (чистового). Часть образующейся на этой стадии пыли на-правляется в барабанную сушилку 8, а другая часть – в бункер для пыли 35.
Подробное описание технологической схемы приведено в приложении А.
|
|
Двойное оплодотворение у цветковых растений: Оплодотворение - это процесс слияния мужской и женской половых клеток с образованием зиготы...
Эмиссия газов от очистных сооружений канализации: В последние годы внимание мирового сообщества сосредоточено на экологических проблемах...
Поперечные профили набережных и береговой полосы: На городских территориях берегоукрепление проектируют с учетом технических и экономических требований, но особое значение придают эстетическим...
Биохимия спиртового брожения: Основу технологии получения пива составляет спиртовое брожение, - при котором сахар превращается...
© cyberpedia.su 2017-2024 - Не является автором материалов. Исключительное право сохранено за автором текста.
Если вы не хотите, чтобы данный материал был у нас на сайте, перейдите по ссылке: Нарушение авторских прав. Мы поможем в написании вашей работы!