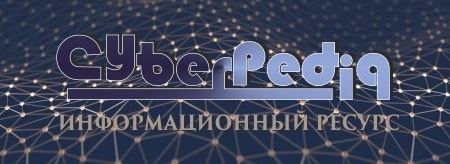
Археология об основании Рима: Новые раскопки проясняют и такой острый дискуссионный вопрос, как дата самого возникновения Рима...
Индивидуальные и групповые автопоилки: для животных. Схемы и конструкции...
Топ:
Выпускная квалификационная работа: Основная часть ВКР, как правило, состоит из двух-трех глав, каждая из которых, в свою очередь...
Определение места расположения распределительного центра: Фирма реализует продукцию на рынках сбыта и имеет постоянных поставщиков в разных регионах. Увеличение объема продаж...
Когда производится ограждение поезда, остановившегося на перегоне: Во всех случаях немедленно должно быть ограждено место препятствия для движения поездов на смежном пути двухпутного...
Интересное:
Распространение рака на другие отдаленные от желудка органы: Характерных симптомов рака желудка не существует. Выраженные симптомы появляются, когда опухоль...
Уполаживание и террасирование склонов: Если глубина оврага более 5 м необходимо устройство берм. Варианты использования оврагов для градостроительных целей...
Финансовый рынок и его значение в управлении денежными потоками на современном этапе: любому предприятию для расширения производства и увеличения прибыли нужны...
Дисциплины:
![]() |
![]() |
5.00
из
|
Заказать работу |
|
|
ПРОЕКТИРОВАНИЕ СТРОИТЕЛЬСТВА, РЕКОНСТРУКЦИЯ ИЛИ МОДЕРНИЗАЦИЯ ПРЕДПРИЯТИЯ
Обоснование реконструкции бетоносмесительного цеха
Предприятие ОАО “Гомельжелезобетон” планирует произвести реконструкцию бетоносмесительного цеха. Принимая во внимание этот аспект потребуется реконструкция существующего отделения приготовления химических добавок, замена существующих дозаторов и бетоносмесителей, модернизирование системы транспортирования бетонной смеси. Модернизация существующей системы позволит обеспечить: стабильное водоцементное отношение на уровне требуемом для работы формовочного оборудования, более точное дозирование и перемешивание компонентов бетонной смеси, учет расхода компонентов и выхода готовой смеси и многое другое. А также для получения бетона с определенными свойствами понадобится организация отделения по приготовлению эффективных химических добавок.
Реконструкцию следует производить путем внедрения на предприятии систем автоматического управления дозированием сырья и приготовления бетонной смеси, что позволяет увеличить точность подготовки компонентов смеси, за счет чего повышается качество выпускаемой продукции, уменьшается влияние "человеческого фактора" и повышается производительность оборудования.
Характеристика проектируемого предприятия
Характеристика местных условий
Абсолютная минимальная температура -35°С;
Абсолютная максимальная температура +35°С;
Средняя максимальная температура наиболее жаркого месяца +24°С;
Период со среднесуточной температурой воздуха 8°С - 137 суток (средняя температура - 1,3°С);
Период со среднесуточной температурой воздуха 10°С - 212 суток (средняя температура - 0,8°С).
|
Средняя температура наружного воздуха:
месяц | Температура, ºС | месяц | Температура, ºС |
январь | -6,9 | июль | 18,6 |
февраль | -6,3 | август | 17,4 |
март | -1,8 | сентябрь | 12,5 |
апрель | 6,3 | октябрь | 6,4 |
май | 13,7 | ноябрь | 0,6 |
июнь | 16,9 | декабрь | -4,3 |
годовая | 6,1 |
Среднемесячная относительная влажность воздуха в %:
наиболее холодного месяца - 82%;
наиболее жаркого месяца - 55%;
Количество осадков - 661 мм в год;
суточный максимум - 69 мм.
Повторяемость направления ветра приведена на листе №1
Сырьевая база и транспорт
Все основные материалы необходимые для производства продукции поставляются с заводов изготовителей Республики Беларусь.
Таблица 1.2 - Сырьевая база и транспорт
Наименование материала | Поставщик | Транспортировка |
1 | 2 | 3 |
Щебень гранитный фр.5-10, фр. 5-20 | РУПП «Гранит», Брестская обл., г.п. Микашевичи | Железнодорожный транспорт |
Песок строительный кварцевый Мк 1,5-2,0 | КУП УПТК Гомельского исполнительного комитета | Автомобильный транспорт |
Портландцемент ПЦ-500 Д0, ПЦ-500 Д20 | ПРУП «Белорусский цементный завод», ПРУП «Гродненский цементно-шиферный завод», ПРУП «Кричевский цементно-шиферный завод» | Железнодорожный транспорт |
Керамзитовый гравий фр.5-20 | ОАО «Керамин», г. Новолукомль | Железнодорожный транспорт |
Арматура Ø3 - Ø40, классов S500, S240, S400, S800 | РУП БМЗ г. Жлобин | Автомобильный транспорт |
Состав завода
В состав завода входят:
склады - цемента, заполнителей, готовой продукции, арматуры;
основные цеха - бетоносмесительный, арматурный, формовочный;
вспомогательные узлы - компрессорная, мастерские;
административно-бытовой корпус.
Режим работы предприятия
Принимаем следующий режим работы предприятия: 5-ти дневная рабочая неделя и 6-ти дневная рабочая неделя каждую восьмую неделю.
Согласно принятому режиму работы: номинальная количество рабочих суток в год - 260; количество рабочих смен в сутки 2; длительность рабочего дня 16 часов.
|
Расчет временной загрузки
Исходные данные. Таблица 1.3 - Потребность в бетонной смеси | ||||||||
Суточная загрузка | ||||||||
Участок | Смена | Часовая потребность | План на месяц | |||||
| 1 | 2 | 3 | 1 | 2 | 3 | ||
I пролет | 26,6 | 26,6 | 26,6 | 3,3 | 3,3 | 3,3 | 1596,0 | |
II пролет | 49,4 | 49,4 | 19,8 | 6,2 | 6,2 | 2,5 | 2370,0 | |
III пролет | Ж/б | 15,0 | 15,0 | 15,0 | 1,9 | 1,9 | 1,9 | 900,0 |
Вибропресс | 5,0 | 5,0 | 0,0 | 0,6 | 0,6 | 200,0 | ||
IV пролет | Кольца | 10,0 | 1,3 | 200,0 | ||||
Ж/б | 8,7 | 8,7 | 8,7 | 1,1 | 1,1 | 1,1 | 520,0 | |
К/б | 1,3 | 1,3 | 1,3 | 0,2 | 0,2 | 0,2 | 80,0 | |
Товарные смеси | 150,0 | 18,8 | 3000,0 | |||||
Сумма | 266,0 | 106,0 | 71,4 | 33,2 | 13,2 | 8,9 |
Таблица 1.4 - Пооперационная продолжительность подачи бетонной смеси (замеры операций производились по факту)
Операция | Продолжительность, сек |
Выгрузка б/с из смесителя | 42 |
Перемещение поперечной тележки | 15 |
Выгрузка б/с в продольную тележку | 33 |
Возврат поперечной тележки | 15 |
Пауза | 54 |
Выгрузка б/с из смесителя | 59 |
Перемещение поперечной тележки | 15 |
Выгрузка б/с в продольную тележку | 31 |
Перемещение телеги до поста | Скорость 0,5м/сек |
Выгрузка б/с: 1,2 пролет, пост колец, вибропресс 3,4 пролет | 30 200 |
Возврат тележки на БСЦ | Скорость 0,5м/сек |
Расчет I смены (самая загруженная).
Цикл производства товарных смесей составляет 180 сек (3 мин), следовательно часовая производительность второй секции, работающей на улицу составляет (60/3)х1=20 м3 при замесе 1 м3, но т.к. бетоносмеситель второй секции позволяет производить замесы V=1,25 м3, производительность второй секции составит (60/3)х1,25=25 м3, что в полной мере обеспечит часовую потребность в товарных смесях.
Работа 2-ой секции
Цикл подачи бетонной смеси на I пролет составляет, примерно 370 сек.
Для обеспечения часовой потребности I пролета понадобится (3,3/1,6)х370=764 сек (13 мин).
Цикл подачи бетонной смеси на II пролет составляет, примерно 440 сек.
Для обеспечения часовой потребности II пролета понадобится (6,2/1,6)х440=1705 сек (28,5 мин).
Цикл подачи бетонной смеси на III пролет составляет, примерно 660 сек для самоходных бункеров с бетоном V= 1,5 м3 (1,5 м3 - средний объем заказа бетонной смеси при замесе за два раза), и 510 сек для самоходных бункеров с бетоном V=0,7 м3 (0,7 м3 - средний объем заказа при замесе за один раз). (потребность: 70% V=1,5 м3, 30% V=0,7 м3).
Для обеспечения часовой потребности III пролета (кроме вибропресса) понадобится (1,9х0,7/1,5)х660=585 сек (10 мин)
|
(1,9х0,3/0,7)х510=415 сек (7 мин)
Итого10+7=17 мин.
Цикл подачи бетонной смеси на пост формования колец составляет, примерно 582 сек. Для обеспечения часовой потребности поста формования колец понадобится (1,3/1,6)х582=473 сек (8 мин). Цикл подачи бетонной смеси на IV пост колец составляет, примерно 793 сек для самоходных бункеров с бетоном V=1,5 м3, и 620 сек для самоходных бункеров с бетоном V=0,7 м3. (потребность: 40% V=1,5 м3, 60% V=0,7 м3)..
Для обеспечения часовой потребности IV пролета понадобится:
ж/б (1,1х0,4/1,5)х793=233 сек (4 мин);
ж/б (1,1х0,6/0,7)х620=585 сек (10 мин);
Итого ж/б4+10=14 мин;
к/б (0,2х0,4/1,5)х793=43 сек (0,7 мин);
к/б (0,2х0,6/0,7)х620=106 сек (1,7 мин);
Итого к/б 2,5 мин
Следовательно, общее время составляет 13+28,5+17+8+14+2,5=83 мин, с учетом поправочного коэффициента 83х1,1=92 мин (при работе одной продольной тележкой).
БСЦ может отправлять тележку загруженную 1,6 м3 б/с примерно каждые 320 сек. Средний срок оборачиваемости одной тележки составляет 580 сек, следовательно БСЦ способно загрузить две бетоновозные телеги на 90% во времени.
Таким образом, при равномерной загрузке бетоновозных тележек общее время требуемое для обеспечения формовочного цеха бетонной смесью для стабильной работы в течении часа составит:
/2=46 мин. (коэффициент запаса более 20%).
Работа 1-го смесителя:
Цикл подачи бетонной смеси на участок вибропрессования составляет, примерно 320 сек.
Для обеспечения часовой потребности поста вибропресса понадобится (0,6/0,8)х320=240 сек (4 мин), с учетом поправочного коэффициента время увеличивается до 5 мин.
Кроме того, 1-й смеситель может отдавать цементный раствор на все посты существенно не увеличивая свою загрузку и уменьшая загрузку 2-й секции.
Расчет II смены
Цикл подачи бетонной смеси на I пролет составляет, примерно 370 сек.
Для обеспечения часовой потребности I пролета понадобится (3,3/1,6)х370=764 сек (13 мин).
Цикл подачи бетонной смеси на II пролет составляет, примерно 440 сек.
Для обеспечения часовой потребности II пролета понадобится (6,2/1,6)х440=1705 сек (28,5 мин).
Цикл подачи бетонной смеси на III пролет составляет, примерно 660 сек для тележек с бетоном V=1,5 м3, и 510 сек для тележек с бетоном V=0,7 м3. (потребность в телегах: 70% V=1,5 м3, 30% V=0,7 м3).
|
Для обеспечения часовой потребности III пролета (кроме вибропресса) понадобится (1,9х0,7/1,5)х660=585 сек (10 мин)
(1,9х0,3/0,7)х510=415 сек (7 мин)
Итого10+7=17 мин.
Цикл подачи бетонной смеси на IV пост формования колец составляет, примерно 793 сек для тележек с бетоном V=1,5 м3, и 620 сек для тележек с бетоном V=0,7 м3. (потребность в тележках: 40% V=1,5 м3, 60% V=0,7 м3)..
Для обеспечения часовой потребности IV пролета понадобится:
ж/б (1,1х0,4/1,5)х793=233 сек (4 мин);
ж/б (1,1х0,6/0,7)х620=585 сек (10 мин);
Итого ж/б4+10=14 мин;
к/б (0,2х0,4/1,5)х793=43 сек (0,7 мин);
к/б (0,2х0,6/0,7)х620=106 сек (1,7 мин);
Итого к/б 2,5 мин
Следовательно, общее время составляет 13+28,5+17+14+2,5=75 мин, с учетом поправочного коэффициента 75х1,1=83 мин (работа одной продольной тележки).
/2=42 мин (работа двумя продольными тележками)
Цикл подачи бетонной смеси на участок вибропрессования составляет, примерно 320 сек.
Для обеспечения часовой потребности поста вибропресса понадобится (0,6/0,8)х320=240 сек (4 мин), с учетом поправочного коэффициента время увеличивается до 5 мин.
Расчет III смены
Цикл подачи бетонной смеси на I пролет составляет, примерно 370 сек.
Для обеспечения часовой потребности I пролета понадобится (3,3/1,6)х370=764 сек (13 мин).
Цикл подачи бетонной смеси на II пролет составляет, примерно 440 сек. Для обеспечения часовой потребности II пролета понадобится (2,5/1,6)х440=688 сек (12 мин). Цикл подачи бетонной смеси на III пролет составляет, примерно 660 сек для тележек с бетоном V=1,5 м3, и 510 сек для тележек с бетоном V=0,7 м3. (потребность в тележках: 70% V=1,5 м3, 30% V=0,7 м3). Для обеспечения часовой потребности III пролета (кроме вибропресса) понадобится (1,9х0,7/1,5)х660=585 сек (10 мин)
(1,9х0,3/0,7)х510=415 сек (7 мин)
Итого10+7=17 мин.
Цикл подачи бетонной смеси на IV пост формования колец составляет, примерно 793 сек для телег с бетоном V=1,5 м3, и 620 сек для телег с бетоном V=0,7 м3. (потребность в телегах: 40% V=1,5 м3, 60% V=0,7 м3)..
Для обеспечения часовой потребности IV пролета понадобится:
ж/б (1,1х0,4/1,5)х793=233 сек (4 мин);
ж/б (1,1х0,6/0,7)х620=585 сек (10 мин);
Итого ж/б4+10=14 мин;
к/б (0,2х0,4/1,5)х793=43 сек (0,7 мин);
к/б (0,2х0,6/0,7)х620=106 сек (1,7 мин);
Итого к/б 2,5 мин
Следовательно, общее время составляет 13+12+17+14+2,5=58,5 мин, с учетом поправочного коэффициента 58,5х1,1=65 мин (работа одной продольной тележкой).
/2=33 мин (работа двумя продольными тележками).
Выводы.
Как видно из представленного расчета, мощности оборудования бетоносмесительного цеха должно быть достаточно для полного обеспечения предприятия бетонной смесью с учетом увеличения мощностей. В случае, если фактическая ситуация не будет соответствовать полученным данным, необходимо пересмотреть загрузку смесителей бетоносмесительного цеха. Так, для бесперебойной подачи бетонной смеси на II пролет формовочного цеха можно использовать смеситель №1, загрузка которого составит примерно 50%, при этом 2-я секция БСЦ полностью сможет обеспечивать потребность в бетонной смеси остальных постов. Бетонную смесь на участок вибропрессования возможно также подавать смесителем №1, несущественно увеличивая его загрузку, либо одним из смесителей 2-й секции.
|
Основные положения технологии арматурного цеха
Для армирования железобетонных конструкций применяется горячекатаная круглая сталь гладкая и периодического профиля классов S240, S400, соответствующая требованиям ГОСТ 5781-82. В качестве напрягаемой арматуры применяется стержневая горячекатаная сталь периодического профиля S800 по ГОСТ 10884-94.
Стержни класса S240 диаметром до 12 мм, класса S400 диаметром до 10 мм включительно изготавливаются в мотках или стержнях, а больших диаметров - в стержнях. Стержни изготавливаются длиной от 6 до 12 м (при согласовании с производителем возможно изготовление стержней большей длины). Для правки арматуры, поступающей в мотках, принимаем правильно-отрезные установки, которые одновременно производят очистку стали. Принимаем правильно-отрезной станок СМЖ-357, имеющий следующие характеристики:
диаметр арматуры гладкой 4-10 мм, периодического профиля 6-8 мм;
длина прутков 1000-9000 мм;
точность +3; -2;
скорость подачи и правки арматуры 31 м/мин;
мощность электродвигателя 12,6 кВт.
А также правильно-отрезной станок И-6118:
диаметр гладкой арматуры 2,5 - 6,3 мм;
точность ±2;
скорость подачи и правки арматуры 25 м/мин; *
мощность электродвигателя 6,9 кВт,
Для резки арматурной стали, поставляемой в прутках, принимаем станок СМЖ-1725, имеющий следующие характеристики:
наибольший диаметр арматуры класса S240 - 40 мм; S400-25мм;
число ходов ножа в мин. 33;
ход ножа 45 мм;
мощность электродвигателя 3 кВт,
Для гибки стержневой арматуры принимаем станок СМЖ-173А;
максимальный диаметр изгибаемого прутка из стали класса S240 - 40 мм, S400 - 32мм;
мощность электродвигателя 3 кВт;
габаритные размеры 760x780x780 мм.
Для резки коротких стержней принимаем станок АРС-М:
диаметр отрезаемых стержней 3-55 мм;
класс арматуры S500:
длина отрезаемых стержней, наименьшая - 50 мм, наибольшая - 1000 мм;
число резов в мин - 42,
мощность электродвигателя 4 кВт;
габаритные размеры 1160x1040x665 мм.
Для сварки сеток и каркасов прижимаем крестообразный тип сварных соединений, выполняемых контактной точечной сваркой. Этот способ позволяет механизировать и автоматизировать процесс изготовления плоских сварных изделий. Для сварки сеток принимаем одноточечную сварочную машину МТ-2102:
наибольший диаметр свариваемой арматуры 22x22 мм;
потребляемая мощность 10 кВт.
Для монтажных сварочных операций при сборке элементов каркасов для дуговой электрической сварки принимаем сварочный аппарат переменного тока:
марка трансформатора ТСП-1;
марка регулятора номинальная;
мощность 12 кВт.
Для изготовления объемных арматурных каркасов принимаем установку СМЖ-56:
положение сборки каркасов - вертикальное;
число одновременно собираемых каркасов -1;
максимальные размеры каркасов 7200x3600x300 мм, диаметры свариваемой арматуры от 5×5 до 12×16 мм;
габаритные размеры установки 8400x3180x4600 мм.
Для изготовления закладных деталей тавровыми соединениями под флюсом принимаем сварочный автомат АДФ-2001 [10, с.62];
диаметр привариваемых анкерных стержней 8-40 мм;
производительность 200 сварок/ч.
Для высадки головок стержней напрягаемой арматуры принимаем установку СМЖ-128Ам:
наибольший диаметр арматуры класса S800 - 25 мм;
число стержней на которых одновременно производится высадка - 1;
максимальная длина стержней - 14000 мм;
производительность - 80 стержней/ч.
Число установок для высадки арматурных стержней определим по формуле:
, (1.5)
где Q - годовая производительность завода, шт.;ст - приведенное количество стержней в изделии, шт;у - производительность установки по высадке, шт/ч.
Для плит перекрытия предварительно напряженных Nст=8 шт;
.
Для плит покрытия предварительно напряженных Nст=2 шт;
.
Принимаем 2 установки.
Основные положения технологии формовочного цеха
Бетонные и железобетонные изделия на предприятии ОАО «Гомельжелезобетон» выпускаются по конвейерной, полуконвейерной, агрегатно-поточной и стендовой технологиям. Основным технологическим оборудованием являются бетоноукладчики, виброплощадки, конвейера, тележки для вывоза готовых изделий, самоходные бетоновозные бункера. На каждом пролёте работают по два мостовых крана, а полигон обслуживается козловым. Для ускорения твердения принимаем ямные и щелевые пропарочные камеры в зависимости от технологии.
В качестве формы для плит покрытия принимаем разборную стальную форму на 1 изделие, для наружных стеновых панелей - форму-вагонетку. Формы должны быть изготовлены в соответствии с ГОСТ 25781 и ГОСТ 18104; точность размеров форм должна быть на класс выше точности размеров изготавливаемых в них изделий, внутренние размеры собранной формы должны находиться в пределах минусовых допусков размеров изделий.
Для чистки рабочих поверхностей форм и отсеков кассет и стендов применяют пневмоскребок и металлическую щетку. Для смазки используют смазку на основе пасты ОПЛ-СМ и эмульсол. Смазку наносят щеткой.
В начале производят армирование форм и отсеков кассет и стендов, затем подаётся бетонная смесь.
Бетонная смесь от бетоносмесителя в формовочный цех транспортируется по бетоновозной эстакаде и выгружается в промежуточный или непосредственно в бункер бетоноукладчика или. Бетонирование изделий производят при помощи бетоноукладчика или бадьи (в зависимости от технологии). Для уплотнения бетонной смеси принимаются виброустановки и глубинные вибраторы.
Для бетона с маркой М250 на портландцементе с отпускной прочностью 85% (плиты покрытия) принимаем следующий режим твердения в ямной пропарочной камере:
2 ч - предварительная выдержка;
3 ч - подъем температуры;
6 ч - изометрическая выдержка;
2 ч - остывание.
Для керамзитобетона наружных стеновых панелей твердеющих в щелевой камере:
3,5 ч - подъем температуры;
7,5 ч - изометрическая выдержка;
2 ч - остывание
Температура изотермической выдержки 80 ºС. После ТВО изделия подвергаются распалубке. После освобождения изделия от действия формообразующего приспособления, оно стропится и при помощи крана устанавливается на пост отделки и мелкого ремонта, а форма или кассета снова снова готова к началу цикла.
На посту доводки изделие осматривается, производится очистка закладных деталей и доводка поверхности изделия до требуемой категории. Затем изделие стропится и перемещается на тележку вывоза готовой продукции, где производится контроль качества изготовления. Там же производится приёмка изделий ОТК.
Для вывоза изделий используется телега СМЖ-151. Продолжительность выдерживания готовых изделий в цехе при температуре наружного воздуха ниже 0°С составляет 12 ч.
Определение количества основного и вспомогательного оборудования
Число камер ТВО определяется по формуле:
, (1.6)
где Nи - число одновременно твердеющих изделий в камере;
Коб - оборачиваемость камер Коб=Тк/tпр,
Тк - продолжительность работы камер за сутки, ч;пр - длительность полного цикла тепловлажностной обработки, включая затраты времени на загрузку и выгрузку изделий, ч.
Для плит покрытия:
Выбираем камеру с одним изделием в плане и семью по высоте.
Габариты формы 6,39×1,896×0,426 м.
Продолжительность работы камер за сутки 24 ч.
Продолжительность ТВО 13 ч.
Время на загрузку одной камеры 7∙0,204=1,43 ч.
Разгрузка камеры осуществляется за 1,43 ч
tпр=13+1,43+1,43=15,86 ч
Коб=24/15,86=1,51и=7 шт.к=4582/(7∙1,51∙255)=1,7 шт.
Принимаем 2 камеры.
Необходимое число форм:
ц=15,86+0,204=16,064 ч
Коб.ф=2∙8/16,064=0,996ф=1,05∙4582/(0,996∙255)=18,9.
Принимаем 19 форм.
Для фундаментов под трёхшарнирные рамы:
Выбираем камеру с одной формой в плане и двумя формами по высоте.
Габаритные размеры формы 5,3×1,68×1,82.
В форме размещаются два изделия.
Продолжительность ТВО 13 ч.
Время на загрузку одной камеры 2·0,5/2+0,15=0,65 ч.
Время на выгрузку 0,3 ч.
пр=13+0,65+0,3=13,95 ч.
Коб=24/13,95=1,72и=4 изделияк=2400/(4·1,72·255)=1,4
Принимаем 2 камеры.
Необходимое число форм:
tц=13,95+0,25=14,2 ч
Коб.ф=2∙8/14,2=1,13ф=1,05∙2400/(1,13∙255)=8,8.
Т.к. в форме 2 изделия: Nф=5 форм.
Число ведущих агрегатов определяется по формуле:
, (1.7)
где Q - годовая производительность, шт.;- максимальная продолжительность ритма работы линии, мин;
τр - расчетное число рабочих суток в году;и - число одновременно формуемых изделий;см - длительность рабочей смены, ч;см - число рабочих смен в сутки.
Для производства железобетонных ребристых плит покрытия принят полуконвейерный способ производства.
Согласно табл.14 [2] максимальный ритм работы составляет 15 мин.
Принимаем 1 линию.
Для производства железобетонных фундаментов под трёхшарнирные рамы принят агрегатно-поточный способ производства.
Согласно табл.14 [2] максимальный ритм работы составляет 20 мин.
Принимаем 1 линию.
Для производства двухслойных наружных стеновых панелей для сельхоз зданий принят конвейерный способ производства.
Согласно табл.15 [2] максимальный ритм работы составляет 12 мин.
Принимаем 1 линию.
Для производства трёхшарнирных рам принят кассетный способ производства.
Число кассетных установок определяется по формуле:
(1.8)
где nотс - число отсеков в кассетной установке (принимаем равным 10);цк - продолжительность технологического цикла изготовления изделия, ч;
;
Принимаем 1 кассетную установку.
Определение необходимой производственной площади
Площадь существующего БСЦ составляет 144 м2.
Производственная площадь арматурного цеха ориентировочно определяется по формуле:
Sa=ma/Ca, (1.9)
где ma - производство арматурных изделий в год, т;
Са - съем арматурных изделий с 1 м2 площади цеха в год, равный 3 т.=5640 т. С учетом 3% отходов ma=5809,2 т.
=5809,2/3=1936,4 м2.
Вспомогательная площадь между отделениями арматурного цеха для хранения запаса полуфабрикатов арматурных элементов и размещения в цехе готовых арматурных изделий определяется по формуле:
.з= maза.э/(tрNсмtсм mу.а), (1.10)
где ma - потребность в арматурных изделиях в год, т;
за.э - норма запаса арматурных элементов, ч;у.а - усредненная масса арматурных изделий, размещенных на 1 м2 площади цеха, т.
за.э=8 ч; mу.а=0,35 т [2].а.э.=5809,2×8/(253×2×8×0,35) = 32,8 м2.
Площадь для хранения арматурной стали:
а.скл= mа за.с/(tрmу.с), (1.11)
где за.с - норма запаса арматурной стали на складе, сут;у.с - усредненная масса металла, размещенных на 1 м2 площади склада, т.
за.с=25 суток; mу.с=2,375 т [2].а.скл=5809,2×25/(253×2,375)=242 м2.
Вспомогательная площадь в формовочном цехе для хранения форм и оснастки, находящейся в эксплуатации, или для текущего их ремонта определяется:
пр.ф(р)=Sх(р)nc, (1.12)
где Sх(р) - норма требуемой площади на каждые 100 т форм, м2, Sх(р)=50 м2[2];с - число сотен тонн форм в цехе.
Металлоемкость формы для плит покрытия равна 5,0 т.
с1=19∙5/100=0,95
Металлоемкость формы для плит покрытия равна 3,0 т.
с2=5∙3/100=0,15
Металлоемкость формы-вагонетки равна 8,5 т.
с3=18∙8,5/100=1,53пр.ф(р)=50×(0,95+0,15+1,53)=131,5 м2.
Вспомогательная площадь для хранения в формовочном цехе запаса арматурных изделий определяется по формуле:
пр.а= maзач/(tрNсмtсм mу.а), (1.13)
где зач - норма запаса арматурных элементов в формовочном цехе, зач=4 ч [2].
пр.а=5809,2×4/(253×2×8×0,03)=191,3 м2.
Определение потребной численности рабочих и цехового персонала
Штатная ведомость цехов приведена в таблице 1.5.
Таблица 1.5 - Штатная ведомость
№ п/п | Наименование | Число работающих | Длительность смены | ||
1 смена | 2 смена | Всего | |||
1 | 2 | 3 | 4 | 5 | 6 |
Формовочный цех | |||||
1 | Производственные рабочие | 52 | 44 | 96 | 8 |
Вспомогательные рабочие | 2 | 2 | 4 | 8 | |
ИТР | 4 | 3 | 7 | 8 | |
Арматурный цех | |||||
2 | Производственные рабочие | 14 | 14 | 28 | 8 |
Вспомогательные рабочие | 1 | 1 | 2 | 8 | |
ИТР | 2 | 1 | 3 | 8 | |
Бетоносмесительный цех | |||||
3 | Производственные рабочие | 4 | 3 | 7 | 8 |
Вспомогательные рабочие | 7 | 6 | 13 | 8 | |
ИТР | 2 | 1 | 3 | 8 | |
РЭМС, РЭЭС | |||||
4 | Вспомогательные рабочие | 60 | 15 | 75 | 8 |
ИТР | 6 | 2 | 8 | 8 | |
РСУ | |||||
5 | Вспомогательные рабочие | 13 | - | 13 | 8 |
ИТР | 2 | - | 2 | 8 | |
Участок сбыта | |||||
6 | Вспомогательные рабочие | 10 | 6 | 16 | 8 |
ИТР | 3 | - | 3 | 8 | |
ЖДУ | |||||
7 | Вспомогательные рабочие | 4 | 3 | 7 | 8 |
ИТР | 3 | 2 | 5 | 8 | |
Лаборатория | |||||
8 | Вспомогательные рабочие | 3 | 2 | 5 | 8 |
ИТР | 11 | 2 | 13 | 8 | |
АХО, АТУ, охрана | |||||
9 | Вспомогательные рабочие | 33 | 6 | 39 | 8 |
ИТР | 3 | - | 3 | 8 | |
Заводоуправление | |||||
10 | ИТР | 43 | - | 43 | 8 |
Итого: производственных рабочих - 131 чел.
Вспомогательных рабочих - 174 чел.
ИТР - 90 чел.
ИТОГО ПО ЗАВОДУ: 395 чел.
1.9 Организация, планирование и управление предприятием
Планирование на предприятии - это совокупность действий по разработке программ деятельности промышленного предприятия и его подразделений, определению направлений, темпов и пропорций развития с целью достижения максимального эффекта при минимальных затратах.
Планирование строится на определенных принципах и выступает в различных видах. Они характеризуются: научностью, органическим единством видов планирования, непрерывностью, оптимальностью и стабильностью.
Принцип научности планирования базируется на системном подходе при изучении, познании и сознательном использовании экономических законов, особенностей техники и технологии производства при разработке показателей плана на всех уровнях - народнохозяйственном, отраслевом, предприятий и его подразделений. Научное планирование требует технических и экономических обоснований плана при использовании прогрессивных норм затрат живого и овеществленного труда (использования оборудования, сырья, материалов, энергии, фондов времени и др.) и должно основываться на технико-экономических прогнозах.
Принцип органического единства народнохозяйственного, отраслевого и технико-экономического планирования на предприятии требует учета целей всех предприятий, входящих в систему народного хозяйства при общности интересов коллективов трудящихся. Это положение достигается дифференцированием форм и показателей планирования в зависимости от его уровня (предприятие, отрасль) и балансированием его основных показателей по уровням управления.
Принцип непрерывности планирования обусловливается непрерывностью процессов воспроизводства и преемственностью плановых заданий во времени (год, квартал, месяц, декада, сутки), органической связью перспективного и текущего планирования.
Принцип оптимальности планирования реализуется применением экономико-математических методов и составлением балансовых плановых моделей при наиболее рациональном использовании ресурсов для достижения поставленной цели с минимальными затратами общественного труда.
Принцип стабильности планирования базируется на минимальном числе изменений в плане, а следовательно, на его высокой надежности, которая обеспечивается всеми изложенными выше принципами.
Внутризаводское планирование, осуществляемое в соответствии с задачами развития всего народного хозяйства, является органической составной частью единой системы, народнохозяйственного планирования.
Одним из основных вопросов эффективной деятельности предприятий в новых условиях хозяйствования является выбор трудовым коллективом напряженных плановых заданий, отвечающих общественным потребностям и росту дохода предприятия. Чтобы это условие выполнялось, необходима личная заинтересованность работников. Поэтому устанавливается прямая зависимость заработной платы от результатов труда всего коллектива и лично каждого его члена. Создаются условия для широкого распространения подряда на цех, участок, бригаду, инженерно-технических работников и служащих, т. е. перехода на коллективный подряд всего предприятия.
Планирование на государственном предприятии подразделяется на несколько видов. По глубине разработки планы могут быть перспективными и текущими, а по содержанию - технико-экономическими или оперативно-производственными. прогресса, рубежи социального развития. Основные направления экономического и социального развития в конкретных цифрах и заданиях реализуют экономическую стратегию на пятилетний период.
Пятилетние планы экономического и социального развития предприятия состоят из следующих разделов:
) Производство и реализация продукции.
Основными показателями являются объем продукции, подлежащей реализации по договорным обязательствам, объем производства основных видов продукции в натуральном выражении по обеспечению госзаказов и потребностей других организаций.
) Техническое развитие и организация производства.
В этом разделе обязательными являются установление и расчет основного задания по выполнению научно-технических программ, по разработке, освоению и внедрению новых высокоэффективных технологических процессов и видов продукции; основных показателей технического уровня производства и важнейших видов выпускаемой продукции; экономический эффект от проведения научно-технических мероприятий.
) Повышение экономической эффективности производства.
) Нормы и нормативы.
В современных условиях все этапы планирования осуществляются на основе системы научно обоснованных технико-экономических норм и нормативов по видам работ и нормативам чистой продукции; затратам труда, сырья, материалов и топливно-энергетических ресурсов; по использованию производственных мощностей; образованию единого фонда развития науки и техники; образованию фонда развития производства; материального поощрения, социально-культурных мероприятий и жилищного строительства; удельным капитальным вложениям.
) Капитальное строительство.
В планах в обязательном порядке устанавливаются показатели ввода в действие основных фондов, производственных мощностей и объектов за счет централизованных лимитов государственных капитальных вложений и собственных средств предприятия.
) Потребность в основных материальных ресурсах.
В разработке плана материально-технического обеспечения предприятия указывается объем поставок основных видов материально-технических ресурсов, необходимых для выполнения плана, а также задания по среднему снижению норм расхода материальных ресурсов.
) Труд и кадры.
Основными показателями, характеризующими эффективность труда, являются рост производительности труда, исчисляемый по чистой продукции (нормативной); нормативы прироста заработной платы и прироста чистой продукции (нормативной).
) Себестоимость, прибыль и рентабельность производства. В этом разделе плана обосновывается общая сумма прибыли, а в отдельных отраслях - снижение себестоимости продукции.
) Фонды экономического стимулирования.
) Финансовый план.
) Социальное развитие коллектива.
Все мероприятия социального развития согласовываются с нормативами образования фондов социально-культурных мероприятий и жилищного строительства и нормативами их роста в зависимости от роста производительности труда.
) Охрана природы и рациональное использование природных ресурсов.
Текущее планирование на предприятиях строительных материалов и изделий охватывает период до одного года. Годовые планы составляются на основе пятилетних с разбивкой по месяцам и кварталам, а для оперативного руководства по декадам, неделям и дням, и сменам.
ПРОЕКТИРОВАНИЕ СТРОИТЕЛЬСТВА, РЕКОНСТРУКЦИЯ ИЛИ МОДЕРНИЗАЦИЯ ПРЕДПРИЯТИЯ
|
|
Наброски и зарисовки растений, плодов, цветов: Освоить конструктивное построение структуры дерева через зарисовки отдельных деревьев, группы деревьев...
Особенности сооружения опор в сложных условиях: Сооружение ВЛ в районах с суровыми климатическими и тяжелыми геологическими условиями...
Механическое удерживание земляных масс: Механическое удерживание земляных масс на склоне обеспечивают контрфорсными сооружениями различных конструкций...
История создания датчика движения: Первый прибор для обнаружения движения был изобретен немецким физиком Генрихом Герцем...
© cyberpedia.su 2017-2024 - Не является автором материалов. Исключительное право сохранено за автором текста.
Если вы не хотите, чтобы данный материал был у нас на сайте, перейдите по ссылке: Нарушение авторских прав. Мы поможем в написании вашей работы!