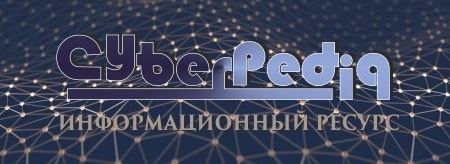
Механическое удерживание земляных масс: Механическое удерживание земляных масс на склоне обеспечивают контрфорсными сооружениями различных конструкций...
Археология об основании Рима: Новые раскопки проясняют и такой острый дискуссионный вопрос, как дата самого возникновения Рима...
Топ:
Методика измерений сопротивления растеканию тока анодного заземления: Анодный заземлитель (анод) – проводник, погруженный в электролитическую среду (грунт, раствор электролита) и подключенный к положительному...
Определение места расположения распределительного центра: Фирма реализует продукцию на рынках сбыта и имеет постоянных поставщиков в разных регионах. Увеличение объема продаж...
Характеристика АТП и сварочно-жестяницкого участка: Транспорт в настоящее время является одной из важнейших отраслей народного хозяйства...
Интересное:
Лечение прогрессирующих форм рака: Одним из наиболее важных достижений экспериментальной химиотерапии опухолей, начатой в 60-х и реализованной в 70-х годах, является...
Мероприятия для защиты от морозного пучения грунтов: Инженерная защита от морозного (криогенного) пучения грунтов необходима для легких малоэтажных зданий и других сооружений...
Искусственное повышение поверхности территории: Варианты искусственного повышения поверхности территории необходимо выбирать на основе анализа следующих характеристик защищаемой территории...
Дисциплины:
![]() |
![]() |
5.00
из
|
Заказать работу |
|
|
План.
· Измерительные инструменты 2
· Токарная обработка 5
· Фрезерные работы 7
· Особенности работы на станках сверлильно-расточной
группы 10
· Обработка металла абразивным инструментом 14
· Резка и рубка металла 17
· Правка и гибка металла 20
· Резка металла 22
· Опиливание металла 24
· Сверление, зенкирование и развертывание 27
· Нарезные резьбы 31
· Заклепочное соединение 33
· Паяние, лужение, склеивание 35
· Механизированный ручной инструмент 38
· Притирка и доводка 40
· Особые виды сборочно-разборочных работ 42
· Комплексные работы 44
|
· Практическая контрольная работа 46
Измерительные инструменты.
Точность измерения определяется главным образом ценой деления шкалы измерительного инструмента, т.е. размером, соответствующим одному делению шкалы.
Штангенциркуль состоит из штанги, губок, рамки, губок рамки, нониуса, зажима рамки, глубиномера. Точность измерения штангенциркулем определяется шкалой нониуса.
Нониусы имеют величину отсчета 0,1; 0,05;0,02 мм. Деление на штанги наносят через 1 мм. Штангенциркуль изготовляют с верхнем пределом измерения от 125 до 2000 мм. Штангенциркули проверяют концевыми мерами 3 класса при величине отсчета 0,05 и 0,02 мм и 4 класса при величине отсчета 0,1 мм.
Штангенрейсмас применяется для измерения размеров и разметки высот. Основными его узлами являются: штанга, нониус, рамка, основание с плоской опорной поверхностью, ножки и узел микрометрической подачи. Остро заточенная ножка служит для разметки, ножка – для измерения высот. Штангенрейсмасы изготовляют с верхними пределами измерения 200 –1000 мм.
Отсчет измеряемого размера по шкале нониуса производится следующим образом. Целое число миллиметров отсчитывается по нулевой риски нониуса и шкале штанги, а число десятых и сотых долей миллиметра – по риске нониуса, наиболее точно совпавшей с риской шкалы.
Штангенглубиномер совмещается со штангенциркулем или выполняется как самостоятельный инструмент. Он состоит из штанги и траверсы с плоской измерительной поверхностью. Измеряемый размер детали соответствует расстоянию от торца штанги до нижней плоскости траверсы. Верхний предел измерения штангенглубиномерами составляют 100-500 мм. Измерение аналогично штангенциркулю.
Микрометр служит для измерения линейных размеров с гарантированной точностью отсчета 0,01 мм. Принцип измерения основан на преобразовании угловых перемещений в линейные при помощи винтовой пары. Основными узлами микрометра являются: скобы с пяткой и стеблем, микрометрический винт с барабаном, фрикционная передача и стопорное приспособление. Предельное перемещение микрометра составляет 25 мм. Верхний предел измерения 25 – 1600 мм. Особенно высокие требования предъявляются к жесткости микрометра. Пятка и стебель запрессовываются в корпус скобы. Передвижная пятка применяется только для больших размеров микрометров с 300 мм и выше. Стебель является гайкой для микровинта и одновременно обеспечивает его центрирования и направление по наружному диаметру для соблюдения параллельности измерительных поверхностей. На наружном диаметре стебля нанесены продольный штрих и поперечные деления через 0,5 мм. На конусной поверхности барабана сделано 50 делений, и, таким образом, поворот микровинта на одно деление барабана соответствует продольному перемещению микровинта на 0,01 мм, т.к. его шаг равен 0,5 мм. Измеряемый размер с точностью до 0,5 мм отсчитывается по делению стебля, а с точностью до 0,01 мм – по делениям барабана.
|
Микрометрический нутромер устанавливается на номинальный диаметр измеряемого отверстия и проверяется обычно в измерительной лаборатории.
Микрометрический глубиномер состоит из основания с измерительной плоскостью, с крепленной с основанием стебля. В этом стебле вертикально перемещается микровинт с измерительным стержнем. Стопор закрепляет микровинт в требуемом положении. Предел измерения глубиномера равен 100 мм.
Уровень служит для определения отклонений обрабатываемых поверхностей от горизонтального или вертикального положения.
Контрольные плиты применяются для контроля плоскости и прямолинейности поверхностей.
Линейки применяются для проверки прямолинейности плоскостей по методу просвета или по количеству пятен на краску. Типы линеек следующие: лекальные, прямоугольные, двутавровые, мостиковые и угловые.
Транспортиры обычно применяются для измерения и разметки углов на плоскости.
Рулетка представляет собой стальную ленту на поверхность, которой нанесена шкала деления. Рулетка применяется для измерения линейных размеров: длины, ширины, высоты деталей и расстояний между их отдельными частями, а также длин дуг, окружностей и кривых.
|
Щупы применяют для контроля зазоров между поверхностями в пределах от 0,03 до 1 мм.
Жесткие калибры – скобы применяются для контроля валов разделяются на регулируемые и нерегулируемые, односторонние и двусторонние, однопредельные и двухпредельные, цельные и сборные.
Регулируемые скобы при износе проходной стороны могут быть восстановлены за счет повторной регулировки и доводки измерительных поверхностей.
Двусторонняя скоба имеет измерительные поверхности с двух сторон, соответствующие предельным размерам вала. Рабочие поверхности не проходной стороны не подвергаются износу и поэтому делаются более короткими.
Двухпредельная скоба обеспечивает контроль детали по верхнему и нижнему предельным размерам, но конструктивно она может быть выполнена как односторонняя или двусторонняя. В первом случае оба предельных размера выполняются последовательно.
Цельные скобы для контроля малых диаметров валов выполняются из листового материала.
Сборные скобы чаще всего применяются для контроля больших размеров и имеют сварную или регулируемую конструкцию.
Калибры – пробки для контроля отверстий могут быть выполнены с точечным контактом – для диаметров свыше 250 мм, с линейным контактом – для диаметров от 100 до 250 мм и с поверхностным контактом - для диаметров до 100 мм.
Конусные калибры – втулки и пробки для контроля конических валов и отверстий имеют две предельные риски на пробки и соответствующие ступени на торце втулки для контроля наибольшего и наименьшего диаметров отверстия и вала. Угол конуса контролируется по краске, нанесенной тонким слоем на образующую пробки или втулки.
Резьбовые калибры – пробки и кольца служат для контроля предельных размеров среднего приведенного диаметра резьбы, который рассчитывается с учетом допускаемых отклонений по шагу резьбы, углу профиля и собственно среднему диаметру резьбы.
Индикаторы применяются для измерения отклонений от заданного размера, при проверке биения, эксцентричности. Индикатор можно применять как для абсолютных, так и для относительных измерений.
|
Токарная обработка.
Режущая часть любого инструмента имеет форму клина, с помощью которого производится отделение стружки.
Резец состоит из двух частей: головки и стержня, который служит для закрепления резца. Основными элементами головки резца являются: передняя поверхность, по которой сходит стружка, задняя поверхность, обращенная к поверхности резания, главная режущая кромка, образованная пересечением передней и главной задней поверхностей, вспомогательная режущая кромка.
Углы заточки резца образуют:
· главный передний угол – угол между передней поверхностью резца и плоскостью.
· главный задний угол – угол между главной задней поверхностью резца и плоскостью резания.
· угол заострения – угол между передней и главной задней поверхностями резца.
· главный угол в плане – угол между проекцией главной режущей кромки на основную плоскость и направлением подачи.
· угол наклона – угол между режущей кромкой и плоскостью.
· угол резания - угол между передней поверхностью резца и плоскостью резания.
· угол при вершине в плане – угол между проекциями режущих кромок на основную плоскость.
Чем больше твердость обрабатываемого материала, тем
меньше должен быть передний угол и больше угол резания.
При обработке деталей на металлорежущих станках различают следующие элементы режима резания: глубину резания, подача, скорость резания.
Глубина резания измеряется как расстояние между обработанной и обрабатываемой поверхностью.
Подача режущего инструмента относительно обрабатываемой поверхности измеряется за один оборот шпинделя.
Скорость резания – скорость перемещения режущей кромки инструмента относительно обрабатываемой поверхности детали.
При обработке металлов резанием необходимо обеспечить наиболее полное использование режущих свойств твердого сплава, его высокую теплостойкость и сопротивление сжатию, а так же и значительную хрупкость. В зависимости от обрабатываемого материала выбирается необходимая марка твердого сплава и геометрия инструмента. Обработка производится при наибольших допустимых значениях глубины резания и подачи. Скорость резания, благодаря высокой теплостойкости твердого сплава, выбирается такой, чтобы обеспечить нагрев стружки до 850 – 900 градусов. При этих температурах прочность обрабатываемого материала и сила резания резко уменьшается, прочность твердого сплава почти не изменяется, а вязкость его увеличивается.
Наибольшая производительность при черновой обработке, соответствующая наибольшему объему стружки, снимаемой в минуту при нормативной стойкости инструмента, обеспечивается при выборе наибольшей глубины резания, за тем подачи механизма подачи станка и прочности резца и в последнюю очередь скорости резания.
|
Наибольшая производительность при чистовой обработке, соответствующая наибольшей поверхности обработки в минуту при нормативной стойкости инструмента, обеспечивается при выборе в первую очередь подачи, а затем уже скорости резания.
В процессе резания инструменты изнашиваются как по передней, так и по задней поверхности. Стойкость инструмента зависит от многих факторов, но основными из них являются: геометрия и материал инструмента, материал и термообработка деталей, охлаждение и режим резания. От правильного выбора стойкости инструмента зависит в свою очередь производительность и себестоимость обработки детали.
Техника безопасности.
1. Берегите зрения, применяй защитные очки.
2. Для защиты от порезов и ожогов металлической стружкой применяй специальные стружкоотводчики.
3. Полностью удаляй стружку со станка.
4. Обязательно останови станок и выключи электродвигатель, если необходимо: произвести чистку, смазку, уборку, наладку станка.
5. Выключай станок и отводи инструмент от детали при перерывах в подаче электроэнергии.
6. Применяй ограждение опасных мест станка.
7. заправляй одежду, чтобы была застегнута.
8. Не применяй опасных приемов работы.
9. Проверяй исправность остановочно-пусковых приспособлений.
10.Надежно крепи приспособления детали и инструмент.
11.Работай только с исправным инструментом.
12.Устойчиво укладывай детали на рабочем месте.
13.Содержи рабочее место в чистоте.
14.Проверяй исправность местных грузоподъемных устройств и не перегружай их.
15.Строго соблюдай правила безопасного обращения с электрооборудованием, проверяй исправность заземления.
16.Предупреждай кожные заболевания – мой руки с мылом после работы, изучай правила первый помощи пострадавшему.
Фрезерные работы.
Фрезы классифицируются по следующим признакам:
по технологическому признаку различают фрезы для обработки следующих поверхностей:
1. плоскостей;
2. пазов и шлиц;
3. фасонных поверхностей;
4. зубчатых колес и резьб;
5. тел вращения;
6. для разрезки материала.
По конструктивному признаку различают следующие типы:
по направлению зуба:
1. с прямыми,
2. с наклонными,
3. с винтовыми,
4. с разнонаправленными.
По конструкции зуба: с остроконечными, с затылованными зубьями.
По внутреннему устройству: цельные, со вставными зубьями, сборные головки.
По способу крепления: фрезы с отверстием; концевые.
Техника безопасности.
· На рабочем месте не должно быть ничего лишнего, должно содержаться в чистоте.
· Спецодежда должна быть застегнута на все пуговицы.
· Каждый предмет надо класть на одно и тоже отведенное место.
· Проходы между станками должны быть свободными.
· Следует очищать станок от стружки.
· На полу не должно быть подтеков и капель масла.
· Перед началом работы фрезеровщик обязан проверить исправность станка, подготовить рабочее место, убедиться в правильности наладки станка.
· Фрезы должны храниться и транспортироваться в таре.
· При установке фрез необходимо одевать рукавицы.
Разметка и рубка металла.
Разметка применяется для того, чтобы не сделать ошибки при обработке заготовок и не испортить их. Для этого на поверхность заготовки наносят точно по чертежу контурные линии, обозначающие границы, на которых разрешается снимать излишний слой металла. Припуск в металлообработке – это толщина слоя материала, удаляемого с поверхности обработки резанием.
При плоскостной разметке обычно бывает достаточно двух баз: первая для откладывания размеров по ширине, вторая по высоте. При плоскостной разметке за базы принимаются: обработанные наружные кромки заготовки, осевые или центровые линии. Разновидность чертилок: чертилка круглая, чертилка с отогнутым концом, чертилка вставными стальными стержнями.
Приемы заточки кернера: опустить экранчик заточного станка или одеть предохранительные очки и включить двигатель заточного станка, проверить биение круга, кернер взять в левую руку за середину, а правой рукой за противоположный конец затачиваемому, расположить на периферии заточного круга, выдерживая угол наклона 30 градусов, с легким нажимом поворачивать керненр вокруг оси кернера пальцами правой руки, во избежании отпуска рабочий части керненра в связи с нагревом острие кернера периодически охлаждать в жидкости, проверить угол заточки кернера по шаблону.
Прием заточки чертилки: подготовить заточный станок, взять чертилку за середину, расположить чертилку на периферии заточного круга под небольшим углом наклона и выдерживая угол наклона, легким нажимом равномерно вращать чертилку, затачивают чертилку под углом 15 – 20 градусов.
Прием заточки ножек циркуля: подготовить заточный станок, свести ножки циркуля так, чтобы они находились в плотном соприкосновении, расположить ножки циркуля под необходимым углом по отношению к абразивному кругу, заточить в начале конец одной ножки и затем вторую ножку, довести на оселке острые концы ножек циркуля и снять заусенцы на боковых гранях и внутренних плоскостях ножек.
Прежде чем приступить к разметке, необходимо: очистить заготовку от пыли, грязи и следов коррозии. Изучить чертеж размеченной детали: особенности конструкции, размеры и ее назначение. Проверить заготовку наружным осмотром: наличие на поверхности наплывов, неровностей, окалины, коррозии.
Точно измерить заготовку и проверить припуски на обработку. Определить поверхность заготовки, окрасить размечаемые поверхности, приступить к разметке детали.
Детали обычно изготавливаются по чертежам и техническим условиям. В слесарном деле встречаются различные виды брака, возникающие главным образом в результате не правильного выполнения основных слесарных операций.
Причины брака: не зависящие от разметчика, зависящие от разметчика.
Чем острее клин, тем меньше угол, тем меньше усилия потребуется для его углубления в материал и наоборот. Угол заточки зависит от обрабатываемого материала. Чем тверже материал, тем он прочнее и тем больше усилия необходимо для резания. Это потребует увеличение прочности инструмента, то есть увеличения сечения его рабочей части. Поэтому для обработки твердых материалов необходимы большие углы заострения инструмента. Для обработки мягких материалов требуются меньшие усилия. Следовательно, прочность инструмента может быть ниже, то есть угол заточки меньше.
Процесс резания обеспечивается благодаря наличию у режущих инструментов углов. Слесарные зубила изготовляются из стали марок У7А, У8А, 8ХФ. На режущей и ударной части зубила не должно быть отколов и заусенцев. Сработанные зубила надо заправлять так:
Захватить клещами конец зубила со стороны ударной части и медленно нагреть другой конец до красного цвета, нагретый конец отковать до необходимого размера, перехватить клещами откованную часть зубила, нагреть и отковать другой конец – ударная часть зубила, после ковки отжечь зубило, опилить режущую и ударную часть зубила, закалить режущую часть на длине 30 мм, а ударную часть на длине 15 мм, заточить зубило под угол.
В зависимости от назначения обрабатываемой детали рубка может быть: чистовой и черновой. При чистовой рубки за один проход снимают слой металла толщиной 0,5 – 1 мм, при черновой рубки – 1,5 – 2 мм. Достигаемая точность при рубке 0,4 – 1 мм. Виды слесарных молотков:
С круглым бойком, с круглым бойком, со вставными бойками из мягкого металла, деревянный, боек, клин, носок, ручка. Основной характеристикой молотка является его масса. Молоток массой 200 г. рекомендуется применять для инструментальных работ, а также для разметки и правки; молотки массой 400 - 600 для слесарных работ; молотки массой 800 – 100 г применяется редко. Конец слесарного молотка, на который насаживается молоток, расклинивается деревянными клиньями. У правильно насаженного молотка ручка образует угол 90 градусов с осью молотка. Ручка молотков делают из наиболее твердых и упругих пород дерева. Ручки должны иметь овальное сечение.
Тиски не должны подвергаться ударом молотка. Параллельные тиски должны иметь накладные губки. Подвижная губка не должна иметь боковое колебания, сходясь, губки должны прикасаться по всей длине верхнего ребра и не должны быть выше одна другой, подвижные части тисков следует смазывать.
Возможный брак при рубке:
1. Из – за невнимательной работы не выдержаны требуемые размеры.
2. При работе тупым инструментом или неправильной установке его неровная поверхность.
3. При рубке хрупких металлов у края могут откалываться частички металла.
4. Глубокие выхваты зубилом или крейцмейселем.
Техника безопасности при разметочных работах.
· Осторожно обращаться с острыми концами чертилок и циркулей.
· Надежно устанавливать разметочную плиту на столе.
· Осторожно обращаться с раствором медного купороса.
· Не работать на неисправном заточном станке, при отсутствии кожуха, экранчика и биении круга.
Техника безопасности при рубке металла.
· Заточку инструмента вести при опущенном экранчике или в защитных очках.
· При работе пользоваться только исправным инструментом.
· Для предохранения рук от повреждений должны быть одеты на зубила предохранительные резиновые шайбы, а на руке защитный щиток.
· При рубке пользоваться предохранительными щитками.
· Особенное внимание обращать на установку зазора между подручником и заточным кругом, который должен быть не менее 3 мм.
· При заточке зубила, крейцмеселя строго соблюдать выполнение приемов держания их при заточке.
· Подавать сжатый воздух в инструмент необходимо после установке его в рабочее положение.
· Во время работы нельзя соединять или разъединять шланки.
Правка и гибка металла.
Сгибая в окружность полосу по толщине, получим цилиндрическое кольцо; причем, внешняя часть металла несколько вытянется, а внутренняя сожмется. Следовательно, длине заготовки будет соответствовать окружность, приходящая посредине между внешней и внутренней окружностями кольца.
В холодном состоянии гнут трубы небольшого диаметра до 20 мм. Гибка труб с наполнителем в горячем состоянии производится при диаметре труб более 100 мм. Гибку труб в горячем состоянии с наполнителем производят в следующем порядке:
1. Один конец трубы закрывают пробкой.
2. Для предотвращения смятия, выпучивания и появление трещины при гибки труб их наполняют мелким, сухим, речным песком, который просеивают через сито с ячейками размером 2 мм, а слишком мелкий песок не пригоден.
3. Второй конец трубы закрывают деревянной пробкой, у которой должно быть отверстия или канавки для выхода газа, образующегося при нагреве трубы.
4. Рассчитать длину нагреваемого участка изгиба на трубе и разметить мелом.
5. Надеть рукавицы.
6. Установить трубу.
7. Нагревать трубу паяльной лампой или пламенем газовой горелки до вишнево – красного цвета на небольшой длине, равной 6 диаметрам.
8. Изогнуть трубу по копиру.
9. Изгиб трубы проверить шаблоном.
10.По окончанию гибки пробки выколотить или выжечь и высыпать песок.
Трубу рекомендуется гнуть с одного нагрева, так как повторный нагрев ухудшает качества металла. При нагреве обращать внимание на прогрев песка. Нельзя допускать излишнего перегрева отдельных участков. От сильно нагретой части трубы отскакивает окалина. В случаи перегрева трубу до гибки охлаждают до вишнево – красного цвета. Если трубу изгибают под углом 90 градусов, то нагревают участок, равный 6 диаметрам трубы, если гнут трубу под углом 60 градусов, то нагревают участок, равный 4 диаметрам трубы, если под углом 45 градусов, то 3 диаметром трубы.
Сварные трубы нужно располагать при гибке так, чтобы ее сварной шов располагался в нейтральном слое, иначе он может разойтись. При гибке возможны следующие дефекты: косые загибы и механические повреждения обработанной поверхности, как результат не правильной разметки ил и зажима детали в тисках, а также нанесения сильных ударов.
Круглые прутки диаметром свыше 30 мм, валы и трубы правят винтовыми прессами, путем нажима витом с призматическим наконечником. Проверка производится индикатором. Отклонение стрелки индикатора покажет величину не прямолинейности.
Техника безопасности при правке металла:
· Рукоятки молотков должны быть без трещин с надежно закрепленными на них бойками.
· Боек молотка должен иметь гладкую, полированную с легка выпуклую поверхность.
· При правке работать обязательно в рукавицах.
· Содержать свое рабочее место в чистоте и порядке.
· Следует надежно крепить обрабатываемые детали.
· При правке полосы или прутка они должны касаться плиты не менее в двух точках.
Техника безопасности при гибке металла.
· Надежно закреплять детали в слесарных тисках или в приспособлениях.
· Работать только на исправном оборудовании и приспособлении.
· Слесарные молотки должны иметь хорошие ручки и быть плотно насажаны.
· При работе на гибочных станках точно соблюдать правило безопасности, изложены в специальных памятках.
· При гибке труб в горячем состоянии работать в руковицах.
Резка металла.
Основные размеры наиболее ходовых ножовочных ручных полотен, изготавливаемых из стали марок У10, У10А, У12, У12А, а также У8, У8А, У9, У9А. Производительность резания ножовочного полотна с нулевым передним углом ниже, чем полотна с передним углом больше нуля. При резки ножовкой надо следить за тем, чтобы в работе участвовало не менее 2,5 зубьев, чтобы ширина разреза, была немного больше толщены полотна и чтобы избежать заеданий ножовочного полотна в металл, зубья разводят, каждые два зуба отгибают в противоположные стороны на 0,25 – 0,6 мм. Для резки мягких металлов применяют ножовочное полотно с крупным шагом, а для резки тонкого полосового металла – ножовочное полотно с мелкими зубьями. Чаще пользуются ножовочными полотнами с шагом 1,3 –1,6 мм при котором на длине 25 мм насчитывается от 17 до 20 зубьев. Нажимать на ножовку надо при движении в перед, а при обратном ходе нажимать не следует. Твердый металл требует более сильного нажима на ножовку, чем мягкие. Ручной ножовкой работают чаще всего без охлаждения. Для уменьшения трения полотна о стенки пропила применяют густую смазку – сало или графитную мазь. Во время резки ножовочное полотно уводит в сторону, в результате этого выкрашиваются зубья или полотно ломается. При поломке зубьев полотна не следует продолжать работу этой ножовкой иначе произойдет поломка смежных зубьев и быстрое затупление всех остальных.
Для восстановление режущей поверхности ножовки, у которой выкрошился зуб, необходимо на точиле или шлифовальном круге сточить 2 – 3 соседних с ним зуба. Если во время резки сломалось старое ножовочное полотно, нельзя работать новой ножовкой, она не войдет в прорезь. Надо повернуть изделие, начать резать в другом месте.
Резка металла ручными ножницами.
Выбор ножниц в зависимости от конфигурации разрезаемого металла:
Прямые ножницы с прямыми режущими лезвиями для разрезания металла по прямым линиям и по окружностям большого радиуса. Кривые ножницы с криволинейными режущими лезвиями применяются для вырезания в листовом материале отверстий и криволинейных участков.
Приемы резания электрическими ножницами:
Проверить исправность электроножниц, установить зазор между ножами в зависимости от толщены разрезаемого металла, проверить точность зазора щупом, подключить токопроводящий провод в электросеть, взять ножницы, обхватив рукоятку и поместить палец на рычаг выключателя с курком, подводить лист между верхним ножом и нижним, передвигать электроножницы вперед, направлять по линии реза так, чтобы риска была видна., режущие кромки необходимо периодически смазывать машинным маслом.
Резка труб ножовкой.
1. Отметить линию разрезания.
2. Зажать трубу в тисках в деревянной колодке.
3. Резку осуществлять ножовочным полотном с мелким зубом.
4. В начале резки ножовку держать горизонтально. После того как зубья полотна войдут в металл, ножовку следует наклонить на себя.
5. Число двойных ходов должно составлять 35 – 45 в минуту.
Резка труб труборезом.
1. Отметить мелом место резания по всему периметру.
2. Вращающая рукоятка с винтом зажать трубу в прижиме между угловой выемкой основания и сухарем с уступом.
3. На конец зажатой в прижиме трубы надеть труборез.
4. Вращая рукоятку трубореза вокруг оси по часовой стрелке, подвести подвижный ролик до соприкосновения со стенками трубы
5. Сделать один оборот труборезом трубы и проверить линию среза.
6. Место реза смазывать маслом для охлаждения режущих кромок роликов.
Техника безопасности при резке металла.
· При работе оберегать руки от ранения об заусенцы.
· Надежно закреплять заготовки в тисках.
· При работе электроинструментами: работу производить в резиновых перчатках и на резиновом коврике, корпус электроинструмента, работающего под напряжением свыше 36 вольт, должен быть заземлен, электропровод к электроинструменту должен иметь защиту от механических повреждений.
· При работе на приводных ножовочных станках: не касаться руками ножовочного полотна при работе на станке, не оставлять станок подключенным при перерывах.
Опиливание металла.
Напильник слесарный состоит из носок, заплечик, хвостовик, узкая сторона, широкая сторона, ребро, ненасеченный участок, задний угол, передний угол, угол основной насечки, угол вспомогательной насечки.
Характеристики насечек: у напильника с одинарной насечкой зубья расположены наклонно к его оси. Благодаря сравнительно большой длине зубьев, они снимают широкую стружку, это требует большого усилья.
Двойная перекрестная насечка состоит из основной, которая образует профиль зуба, и вспомогательной, которая формирует стружкоделительные канавки. Это обеспечивает дробление стружки.
Рашпильная точечная насечка в виде зубьев пирамидальной формы, получаемой вдавливанием в металл специального трехгранного зубила. Обрабатывают им очень мягкие металлы и не металлические материалы.
Напильники с дуговой насечкой в виде острых однородных по шагу и глубине зубьев криволинейной формы. Применяются при обработке кузовов автомобилей.
Машинные напильники – стержневые для опиловочных станков.
Борнапильники – это фасонные головки с насеченными или фрезерованными зубьями. Ими обрабатывают фасонные поверхности.
Дисковые напильники применяются для зачистки отливок, поковок, снятие заготовок.
Припуск на обработку – слой металла, снимаемый за один рабочий ход, и точность обработки, должны быть следующими:
Обработка | Напильники | Номера насечек | Припуск на обработку, мм | Слой, снимаемый за один ход, мм | Точность обработки, мм |
Черновое опиливание | Драчевый | 0 и 1 | 0,5-1,0 | 0,05-0,10 | 0,1-0,2 |
Чистовое опиливание | Личной | 2 и 3 | 0,15-0,30 | 0,02-0,06- | 0,02-0,05 |
Отделочная обработка | Бархатный | 4 и 5 | 0,05-0,10 | 0,01-0,03 | 0,01-0,005 |
Для обеспечения долговечности и эффективности работы напильника надо соблюдать следующие правила:
1. Предохранять напильник даже от незначительных ударов, исключать соприкосновение напильников.
2. Не допускать попадания на напильник влаги.
3. Оберегать напильник от попадания масла и наждачной пыли.
4. Во избежание преждевременного износа напильники перед опиливанием заготовок, поверхности которых покрыты ржавчиной, необходимо удалить ржавчину механическим способом.
5. Нельзя обрабатывать напильником материалы, твердость которых равна или превышает его твердость.
6. Периодически очищать напильник от стружки.
7. Напильники применяют только по их назначению.
Наиболее частыми видами брака при опиливании являются:
1. Неровности поверхности и завалы краев заготовки, как результат не умелого пользования напильником
2. Вмятины или повреждения заготовки в результате не правильного зажима в тисках.
3. Не точность размеров опилиной заготовки вследствие не правильной разметки, снятие очень большого или малого слоя металла, а также не правильного измерения измерительным инструментом.
4. Задиры, царапины поверхности детали, возникающие в результате небрежной работы, не правильно выбранного напильника.
Техника безопасности при опиливании.
· Нельзя работать напильниками без рукояток или с расколотыми, негодными рукоятками. Рукоятки должны быть годными и иметь полированную наружную поверхность и кольцо.
· Запрещаются приемы наседки рукояток на напильник, во избежание соскакивания рукоятки или напильника и получение травм.
· При опиливании не следует охватывать нос напильника снизу, при холостом ходе можно задеть за деталь и поранить пальцы.
· Стружку образующуюся при опиливании, нельзя сбрасывать голыми руками и сдувать, иначе возможно ранение рук. Стружка удаляется волосяными щетками.
· Во избежании попадания стружки в волосы, работать следует в головных уборах.
· Большое значение при опиливание имеет правильная организация рабочего места, верстаки должны быть прочными и устойчивыми. Тиски нужно прочно крепить на верстаках.
· Во время работы на верстаке не должно быть ничего лишнего, напильники должны укладываться на специальные подставки с право от тисков, после окончания работы, тиски и верстак очищаются и протераются.
· Категорически запрещается работать с электрифицированными и пневматическими инструментами без предварительного изучения специальных инструкций.
Нарезные резьбы.
При ручном нарезании следует работать полным набором метчиком. Нарезание резьбы одним метчиком приводит к получению недоброкачественной резьбы и поломке метчика. В начале ручного нарезания метчик вращают при небольшом нажиме, как только инструмент в отверстие на длину своей заборной части, нажим на метчик прекращают. Нарезать резьбу в ручную рекомендуется с применением смазки: машинного масла и олифы для стали; керосина для алюминия и чугуна.
Нарезание резьбы плашкой. Перед нарезанием резьбы рекомендуется выполнить на стержне заходную фаску. Наличие у плашки заборного конуса с обоих торцов позволяет начинать резание с любой стороны плашки. Условия установки изделия и инструмента, правила вращения плашки, смазочно – охлаждающие жидкости – такие же, что у метчиков.
Качество нарезанной резьбы следует проверять резьбовыми калибрами: пробками и кольцами. Для определения шага и профиля резьбы пользуются резьбомерами, представляющими собой зубчатые пластинки, выполненные по профилю резьбы. При измерении пластинку резьбомера зубцами прикладывают к резьбе детали. На каждой пластинке указана величина шага резьбы в мм или число ниток на один дюйм. Выпускают два набора резьбомеров: для метрической резьбы, для резьб трубной и дюймовой.
В машиностроение применяются: метрическая, дюймовая, трубная резьба.
Метрическая резьба имеет треугольный профиль с углом 60 градусов с плоскосрезанной вершиной.
Дюймовая резьба имеет треугольный плоскосрезанный профиль с углом 55 или 60 градусов, шаг выражается числом ниток на длине одного дюйма.
Трубная резьба – это дюймовая с мелким шагом. Вершина витков у нее закругленные и резьбовые детали соединяются без зазора, это обеспечивает герметичность.
В комплект метчиков, состоящий из трех штук входят: черновой метчик, средний, чистовой. Все они имеют разные диаметры.
Причинами неудовлетворительного качества нарезаемой резьбы, часто приводящему к браку, являются:
Рваная резьба, тупая резьба, неточный профиль резьбы, ослабленная резьба, тугая резьба, срыв резьбы.
Техника безопасности при нарезании резьбы.
· При нарезании резьбы в ручную в деталях с сильно выступающими острыми частями необходимо следить за тем, чтобы при повороте метчика с воротком не поранить руку.
· Во избежание поломки метчика при нарезании резьбы: нельзя работать затупившимся метчиком, а при нарезании резьбы в глухих отверстиях следует чаще удалять стружку.
· При работе на станках и электрифицированными резьбонарезателями необходимо проверять заземление и исправность пусковых устройств.
· При нарезании резьбы нельзя смазку станка производить на ходу.
· Нельзя работать на станке электрическими, пневматическими резьбонарезат<
|
|
История создания датчика движения: Первый прибор для обнаружения движения был изобретен немецким физиком Генрихом Герцем...
Историки об Елизавете Петровне: Елизавета попала между двумя встречными культурными течениями, воспитывалась среди новых европейских веяний и преданий...
Адаптации растений и животных к жизни в горах: Большое значение для жизни организмов в горах имеют степень расчленения, крутизна и экспозиционные различия склонов...
История развития хранилищ для нефти: Первые склады нефти появились в XVII веке. Они представляли собой землянные ямы-амбара глубиной 4…5 м...
© cyberpedia.su 2017-2024 - Не является автором материалов. Исключительное право сохранено за автором текста.
Если вы не хотите, чтобы данный материал был у нас на сайте, перейдите по ссылке: Нарушение авторских прав. Мы поможем в написании вашей работы!