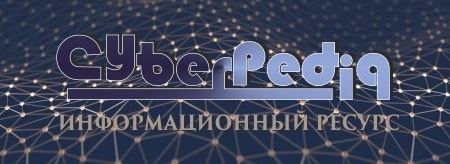
Адаптации растений и животных к жизни в горах: Большое значение для жизни организмов в горах имеют степень расчленения, крутизна и экспозиционные различия склонов...
Биохимия спиртового брожения: Основу технологии получения пива составляет спиртовое брожение, - при котором сахар превращается...
Топ:
Методика измерений сопротивления растеканию тока анодного заземления: Анодный заземлитель (анод) – проводник, погруженный в электролитическую среду (грунт, раствор электролита) и подключенный к положительному...
Оценка эффективности инструментов коммуникационной политики: Внешние коммуникации - обмен информацией между организацией и её внешней средой...
История развития методов оптимизации: теорема Куна-Таккера, метод Лагранжа, роль выпуклости в оптимизации...
Интересное:
Как мы говорим и как мы слушаем: общение можно сравнить с огромным зонтиком, под которым скрыто все...
Наиболее распространенные виды рака: Раковая опухоль — это самостоятельное новообразование, которое может возникнуть и от повышенного давления...
Средства для ингаляционного наркоза: Наркоз наступает в результате вдыхания (ингаляции) средств, которое осуществляют или с помощью маски...
Дисциплины:
![]() |
![]() |
5.00
из
|
Заказать работу |
11.6.1 Расчет по определению коэффициента дымообразования для комбинации материалов на основании данных, полученных при последовательных испытаниях одиночных материалов, входящих в состав комбинации, проводится по формуле
,
(11.2)
где - расчетное значение коэффициента дымообразования для комбинации материалов;
i - номер материала в комбинации;
- массовый процент i-го материала в комбинации;
- экспериментально установленные значения коэффициента дымообразования i-го материала;
n - количество материалов в комбинации.
11.6.2 Для установления расчетных значений коэффициента дымообразования в соответствии с формулой (11.2) изначально принимаются следующие допущения:
- вклад каждого одиночного материала в формирование среды с измененными оптическими свойствами пропорционален его содержанию в комбинации и его дымообразующей способности;
- количественная оценка дымообразующей способности комбинированных изделий подчиняется правилу аддитивности.
11.6.3 Параметры дымообразования, установленные при испытаниях одиночных материалов, принимались за исходные данные для расчета ожидаемых значений коэффициента дымообразования комбинаций материалов. В соответствии с принципом аддитивности выполнялся расчет коэффициента дымообразования комбинации материалов по формуле (11.2).
11.6.4 Для расчетного определения коэффициента дымообразования комбинированных материалов проводится сравнительный анализ полученных данных - ожидаемые (расчетные) параметры, - экспериментально установленных, и применяется формула (11.3) для определения величины относительной погрешности
,
(11.3)
где - относительная погрешность, %;
- значение коэффициента дымообразования, полученное при испытаниях комбинированных материалов;
- расчетное значение коэффициента дымообразования.
11.6.5 Взаимное расположение слоев в комбинированных материалах (изделиях) по отношению к источнику зажигания испытательной установки на значения параметров дымообразования не влияет.
11.6.6 Относительная погрешность, рассчитанная по формуле (11.3), не должна превышать 10 % для оценки исследуемых параметров, как в режиме термоокислительного разложения, так и в режиме пламенного горения.
Оформление протокола испытаний
Условия и результаты испытаний регистрируют в протоколе, форма которого приведена в приложении Е.
Требования безопасности
Установку для определения коэффициента дымообразования необходимо располагать под вытяжным зонтом. Рабочее место оператора должно удовлетворять действующим требованиям по электробезопасности и санитарно-гигиеническим требованиям в соответствии с ГОСТ 12.1.005.
12 Метод экспериментального определения линейной скорости распространения пламени твердых веществ и материалов
Основные положения
12.1.1 Метод определения линейной скорости распространения пламени (ЛСРП) по поверхности горизонтально расположенных образцов твердых веществ и материалов распространяется на горючие твердые вещества и материалы, в том числе строительные, а также на лакокрасочные покрытия.
12.1.2 Методика не распространяется на вещества в газообразном и жидком виде, сыпучие материалы и пыли.
12.1.3 Результаты испытаний применимы только для оценки свойств материалов в контролируемых лабораторных условиях и не всегда отражают поведение материалов в реальных условиях пожара.
Испытательное оборудование
12.2.1 Схема испытательного оборудования для определения ЛСРП представлена на рисунке 12.1.
12.2.2 Электрическая радиационная панель 4 состоит из керамической плиты, в пазах которой равномерно закреплен нагревательный элемент (спираль) из проволоки марки Х20Н80-Н (ГОСТ 12766.1). Параметры спирали (диаметр, шаг намотки, электрическое сопротивление) должны быть такими, чтобы суммарная потребляемая мощность не превышала 8 кВт. Керамическая плита помещена в теплоэлектроизолированный корпус, закрепленный на вертикальной стойке 6, и подключена к электрической сети с помощью блока питания. Для увеличения мощности инфракрасного излучения и уменьшения влияния потоков воздуха перед керамической плитой установлена сетка из жаростойкой стали. Радиационная панель устанавливается под углом 60° к поверхности горизонтально расположенного образца.
12.2.3 Держатель образца 1 (см. рисунок 12.1) состоит из подставки и рамки.
Рамку закрепляют на подставке горизонтально так, чтобы нижняя кромка электрической радиационной панели находилась от верхней плоскости рамки с образцом на расстоянии 30 мм по вертикали и 60 мм по горизонтали (см. рисунок 12.2).
На боковой поверхности рамки нанесены контрольные деления через каждые (30 1) мм.
12.2.4 Вытяжной зонт 2 (см. рисунок 12.1) размерами 360 х 360 х 700 мм, установленный над держателем образца, служит для сбора и удаления продуктов горения.
12.2.5 Газовая горелка 5 (см. рисунок 12.1) представляет собой трубку диаметром 3,5 мм из жаростойкой стали с запаянным концом и пятью отверстиями, расположенными на расстоянии 20 мм друг от друга. Горелка в рабочем положении установлена перед радиационной панелью параллельно поверхности образца по длине середины нулевого участка. Расстояние от горелки до поверхности испытываемого образца составляет (8 1) мм, а оси пяти отверстий ориентированы под углом 45° к поверхности образца. Для стабилизации запального пламени горелка помещена в однослойный чехол из металлической сетки. Газовая горелка подсоединяется гибким шлангом через вентиль, регулирующий расход газа, к баллону с пропан-бутановой фракцией. Давление газа должно находиться в диапазоне от 10 до 50 кПа. В положении "контроль" горелку выводят за край рамки.
12.2.6 Блок питания состоит из регулятора напряжения с максимальным током нагрузки не менее 20 А и регулируемым выходным напряжением от 0 до 240 В.
12.2.7 При испытаниях используют следующие средства измерения и приборы контроля за условиями окружающей среды:
- устройство для измерения времени (секундомер) с диапазоном измерения от 0 до 60 мин, с ценой деления 0,2 с;
- термоанемометр предназначен для измерения скорости воздушного потока с диапазоном измерения от 0,2 до 5,0 м/с и точностью 0,1 м/с;
- для измерения температуры (справочный показатель) при испытании материалов используют термоэлектрический преобразователь 3 (см. рисунок 12.1) типа ТХА с диаметром термоэлектрода не более 0,5 мм, спай изолированный, с диапазоном измерения от 0 до 500 °С, не более 2 класса точности. Термоэлектрический преобразователь должен иметь защитный кожух из нержавеющей стали диаметром (1,6 0,1) мм и закрепляться таким образом, чтобы изолированный спай находился в центре сечения суженной части вытяжного зонта;
- прибор для регистрации температуры с диапазоном измерения от 0 до 500 °С, не более 0,5 класса точности;
- для измерения линейных размеров используют линейку металлическую или рулетку, имеющую диапазон измерения от 0 до 1000 мм, с ценой деления 1 мм;
- для измерения атмосферного давления используют барометр с диапазоном измерения от 600 до 800 мм рт. ст. и ценой деления 1 мм рт. ст.;
- для измерения влажности воздуха используют гигрометр, имеющий диапазон измерения от 20 до 93 % (от 15 до 40 °С), с ценой деления 0,2.
1 - держатель образца; 2 - вытяжной зонт; 3 - термоэлектрический преобразователь; 4 - электрическая радиационная панель; 5 - газовая горелка; 6 - вертикальная стойка на опоре
Рисунок 12.1 - Общий вид установки для определения линейной скорости распространения пламени
Примечание - В качестве устройства, регулирующего расход газа, может использоваться расходомер типа ротаметр или аналогичный прибор с диапазоном, обеспечивающим требования 12.4.3.
1 - держатель с образцом; 2 - образец; 3 - электрическая радиационная панель
Рисунок 12.2 - Взаимное расположение радиационной панели и держателя с образцом
Образцы для испытаний
12.3.1 Для испытания одного вида материала изготавливают пять образцов длиной (320 2) мм, шириной (140
2) мм, фактической толщиной, но не более 20 мм. Если толщина материала составляет более 20 мм, необходимо срезать часть материала с нелицевой стороны, чтобы толщина составляла 20 мм. При изготовлении образцов экспонируемая поверхность не должна подвергаться обработке.
12.3.2 Для анизотропных материалов изготавливают два комплекта образцов (например, по утку и по основе). При классификации материала принимается худший результат испытания.
12.3.3 Для слоистых материалов с различными поверхностными слоями изготавливают два комплекта образцов с целью экспонирования обеих поверхностей. При классификации материала принимается худший результат испытания.
12.3.4 Кровельные мастики, мастичные покрытия и лакокрасочные покрытия испытывают нанесенными на ту же основу, которая использована в реальной конструкции. При этом лакокрасочные покрытия следует наносить не менее чем в четыре слоя, с расходом каждого в соответствии с технической документацией на материал.
12.3.5 Материалы толщиной менее 10 мм испытывают в сочетании с негорючей основой. Способ крепления должен обеспечивать плотный контакт поверхностей материала и основы.
В качестве негорючей основы следует использовать хризотилцементные листы размерами 320 х 140 мм, толщиной 10 или 12 мм, изготовленные по ГОСТ 18124.
Примечание - Допускается использование листов из асбестоцемента и других негорючих материалов.
12.3.6 Образцы для испытаний кондиционируют в лабораторных условиях до достижения постоянной массы, но не менее 48 ч.
Калибровка установки
12.4.1 Калибровка установки должна проводиться в помещении при температуре (23 5) °С и относительной влажности воздуха (50
20) %.
12.4.2 Измеряют скорость воздушного потока в центре сечения суженной части вытяжного зонта. Она должна находиться в диапазоне от 0,25 до 0,35 м/с.
12.4.3 Необходимо отрегулировать расход газа через запальную газовую горелку таким образом, чтобы высота язычков пламени составляла (11 2) мм. После этого запальную горелку выключают и переводят в положение "контроль".
12.4.4 Нужно включить электрическую радиационную панель и установить держатель образца с тарированной асбестоцементной плитой, в которой расположены отверстия с датчиками теплового потока в трех контрольных точках. Центры отверстий (контрольные точки) расположены по центральной продольной оси от края рамки держателя образца на расстоянии соответственно 15, 150 и 280 мм.
12.4.5 Следует нагреть радиационную панель, обеспечивая плотность теплового потока в стационарном режиме для первой контрольной точки (13,5 1,5) кВт/м2, для второй и третьей точки соответственно (9
1) кВт/м2 и (4,6
1) кВт/м2. Плотность теплового потока контролируют датчиком типа Гордона с погрешностью не более
8 %.
12.4.6 Считается, что радиационная панель вышла на стационарный режим, если показания датчиков теплового потока достигают значений заданных диапазонов и остаются неизменными в течение 15 мин.
12.4.7 Калибровку установки проводят при периодической или повторной метрологической аттестации, а также при вводе в эксплуатацию, замене узлов после ремонта установки.
Проведение испытания
12.5.1 Испытания должны проводиться в помещении при температуре (23 5) °С и относительной влажности воздуха (50
20) %.
12.5.2 Необходимо настроить скорость воздушного потока в вытяжном зонте согласно 12.4.2.
12.5.3 Следует нагреть радиационную панель и проконтролировать плотность теплового потока в трех контрольных точках согласно 12.4.5.
12.5.4 Нужно закрепить испытываемый образец в держателе, нанести на лицевой поверхности риски с шагом (30 1) мм, зажечь запальную горелку, перевести ее в рабочее положение и отрегулировать расход газа согласно 12.4.3.
12.5.5 Необходимо поместить держатель с исследуемым образцом в установку в соответствии с рисунком 12.2 и включить секундомер в момент контакта пламени запальной горелки с поверхностью образца. Временем воспламенения образца считается момент, когда фронт (или пробежка) пламени достигает отметки нулевого участка.
12.5.6 Испытание длится до момента прекращения распространения фронта пламени по поверхности образца.
В процессе испытания фиксируют:
- время воспламенения образца, с;
- время прохождения фронтом пламени каждого i-го участка поверхности образца (i = 1, 2,... 9), с;
- общее время прохождения фронтом пламени всех участков, с;
- расстояние L, на которое распространился фронт пламени, м;
- максимальную температуру Тmax дымовых газов, °С;
- время достижения максимальной температуры дымовых газов, с.
История развития пистолетов-пулеметов: Предпосылкой для возникновения пистолетов-пулеметов послужила давняя тенденция тяготения винтовок...
Поперечные профили набережных и береговой полосы: На городских территориях берегоукрепление проектируют с учетом технических и экономических требований, но особое значение придают эстетическим...
Индивидуальные и групповые автопоилки: для животных. Схемы и конструкции...
Особенности сооружения опор в сложных условиях: Сооружение ВЛ в районах с суровыми климатическими и тяжелыми геологическими условиями...
© cyberpedia.su 2017-2024 - Не является автором материалов. Исключительное право сохранено за автором текста.
Если вы не хотите, чтобы данный материал был у нас на сайте, перейдите по ссылке: Нарушение авторских прав. Мы поможем в написании вашей работы!