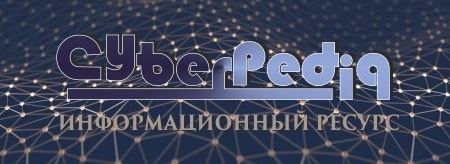
Эмиссия газов от очистных сооружений канализации: В последние годы внимание мирового сообщества сосредоточено на экологических проблемах...
Таксономические единицы (категории) растений: Каждая система классификации состоит из определённых соподчиненных друг другу...
Топ:
Характеристика АТП и сварочно-жестяницкого участка: Транспорт в настоящее время является одной из важнейших отраслей народного хозяйства...
История развития методов оптимизации: теорема Куна-Таккера, метод Лагранжа, роль выпуклости в оптимизации...
Характеристика АТП и сварочно-жестяницкого участка: Транспорт в настоящее время является одной из важнейших отраслей народного...
Интересное:
Наиболее распространенные виды рака: Раковая опухоль — это самостоятельное новообразование, которое может возникнуть и от повышенного давления...
Средства для ингаляционного наркоза: Наркоз наступает в результате вдыхания (ингаляции) средств, которое осуществляют или с помощью маски...
Берегоукрепление оползневых склонов: На прибрежных склонах основной причиной развития оползневых процессов является подмыв водами рек естественных склонов...
Дисциплины:
![]() |
![]() |
5.00
из
|
Заказать работу |
|
|
Завод непрерывного действия со смесителем барабанного типа. Схематическое изображение компонентов типичного асфальтобетонного завода непрерывного действия показано в иллюстрации 6-1. Движение материалов на данной схеме идет слева направо. Инертные материалы со склада фронтальным погрузчиком подаются в бункер-дозатор холодного инертного материала. Минимальное необходимое количество бункеров зависит от количества различных заполнителей которые будут использоваться в изготовлении асфальтобетонной смеси. Большинство установок имеют 4–5 бункера-дозатора холодного материала. Для поддержания постоянной подачи материала, через разгрузочное окно, металлические стенки бункера-дозатора имеют крутой угол наклона, на бункера-дозаторы мелких фракций устанавливаются вибраторы (используются если гравитационная подача недостаточна). Разгрузочное окно каждого бункера оборудовано регулируемыми заслонками и дозатором с регулируемой скоростью, для пропорциональной подачи материала из каждого бункера, чтобы смесь инертных материалов соответствовала подобранному составу асфальтобетонной смеси. Сборочный конвейер подает материал на конвейер загрузки холодных инертных материалов, который переносит материал в сушильно-смесительный агрегат барабанного типа. Автоматическая система весов в этом конвейере постоянно взвешивает количество заполнителя и содержание в нем влаги, поступающих в смеситель барабанного типа. В диспетчерской делается коррекция общего веса влажного содержимого заполнителя, чтобы система дозировки асфальта могла закачать правильное количество битумного вяжущего в смеситель. Корректирование влажности выполняется посредством физического определения содержания влаги в куче заполнителя или в заполнителе из сборочного конвейера и введением этой информации в компьютер.
|
Рис. 6-1. Схематическое изображение главных компоненты типичного асфальтобетонного завода непрерывного действия
Типичный барабанный смеситель имеет прямоточный дизайн, в котором заполнитель двигается в том же направлении (параллельно) как и выхлопные газы (хотя было построено некоторое количество устройств этого типа с противоточным дизайном). Поэтому, заполнитель подается в барабан со стороны горелки, где во время его движения в разгрузочной сторону, он высушивается и нагревается. Битумное вяжущее закачивается из резервуара-хранилища битумного вяжущего и подается в смеситель в точке около 1/3 длины смесителя от разгрузочной стороны. Некоторые установки используют дополнительный непрерывный лопастной смеситель, который подобен порционному смесителю. Битумное вяжущее добавляется к заполнителю в непрерывный лопастной смеситель после выхода горячего заполнителя из барабана. Когда асфальтовое вяжущее подается в барабан, оно закачивается на в зону смешивания барабана, в его нижней части, примерно в том же месте, что и минеральный заполнитель или собственный минеральный наполнитель (пыль) из рукавного фильтра. Добавление битумного вяжущего и пыли близко друг к другу позволяет битумному вяжущему захватить мелкий заполнитель и покрыть его перед тем, как его подхватит высокоскоростной поток выхлопных газов. Выхлопные газы проходят через систему пылеулавливания, где большее количество пыли улавливается и удаляется, что соответствует требованиям по регулированию промышленных газообразных выбросов.
Битумное вяжущее покрывает заполнитель в процессе продвижения материала ниженей 1/3 барабана. Через разгрузочный желоб горячая АБС выходит из барабана в конвейерную систему, которая транспортирует асфальтобетонную смесь в бункер промежуточного хранения (или бункер другого типа) из которого она разгружается в грузовики через автоматическую систему весов. Затем смесь транспортируется к месту выгрузки.
|
Все движения материала от холодной загрузки до бункера промежуточного хранения отслеживаются из диспетчерской асфальтобетонного завода. Датчики в различных местах завода отслеживают скорость конвейера, вес заполнителя, температуру и другие критические функции, которые влияют на эффективность процесса.
Асфальтобетонный завод цикличного действия. Схематическое изображение компонентов на асфальтобетонном заводе цикличного действия показано на иллюстрации 6-2. Каждый значительный компонент асфальтобетонного завода пронумерован и описывается в пояснении. Сравнение первых двух или трех компонентов на асфальтобетонных заводах непрерывного действия и циклического действия показывает, что система холодной загрузки для обоих типов завода одинакова. До операции просушивания, главная разница в автоматической системе весов на конвейере холодной загрузки на заводе непрерывного действия. Пропорционально загруженный материал подается конвейером в сушильный агрегат барабанного типа.
Рис. 6-2 Схема расположения основных компонентов асфальтобетонного завода цикличного действия.
Сушильный барабан на заводе циклического действия имеет типичный противоточный дизайн, в котором заполнитель передвигается в направлении противоположном потоку выхлопных газов. Сушилка оборудована горелкой, которая обеспечивает нагрев для выпаривания влаги из заполнителя и его последующего нагрева до заданной температуры. Нагретый заполнитель выгружается из сушильного барабана и через закрытый элеватор поднимается на вершину смесительной башни. Горячие, наполненные пылью выхлопные газы из сушилки проходят через систему пылесборника для удаления частичек пыли, чтобы соответствия стандартам выброса газообразных отходов. Собранная пыль возвращается в элеватор горячего материала или в накопительный бункер и по необходимости снова добавляется в горячую асфальтовую смесь.
Порционный смеситель башенного типа содержит серии группу узлов, которые отслеживают, хранят, пропорционально распределяют по весу, смешивают и разгружают горячую смесь в грузовик или в бункер промежуточного хранения. После того как в верхней части смесительной башни заполнитель покидает элеватор горячего материала. Он попадает на виброцонный грохот, который предназначен для сортировки материала по размеру. После сортировки заполнителя он хранится в бункерах горячего материала. Затем хранящийся заполнитель пропорционально загружается для изготовления горячей асфальтобетонной смеси. Сначала вибрирующим сито в бункер отделяется самый мелкий материал; негабаритный материал с верхней деки грохота подается в специальный бункер и удаляется из башни. Весь материал разделенный на грохоте на определенные фракции хранится в горячих бункерах. Затем система контроля подает горячий заполнитель из бункеров на весы горячих инертных материалов. Затем заполнитель поступает в мешалку, Горячее битумное вяжущее, которое взвешивается в весовом битумном котле, распыляется в мешалке через несколько секунд после сухого перемешивания. Смеситель, это обычно двухвальный, смеситель с двух-направленным вращением, разработанным для покрытия заполнителя битумным вяжущим. После смешивания, горячая асфальтобетонная смесь выгружается непосредственно в грузовик или перемещается в бункер промежуточного хранения, где грузовики могут загружаться для перевоза смеси к месту выгрузки.
|
В дополнение к уже упомянутых компонентам, как для завода непрерывного действия так и для завода циклического действия. существуют также устройства для хранения и дозирования минерального наполнителя или других добавок, включая известь и знаменитое асфальтовое дорожное покрытие (RAP). Также нагреваемый резервуар-хранилище битумного вяжущего для обоих типов асфальтобетонного завода.
Барабанные смесители
Задача барабанного смесителя экономично высушивать и нагревать заполнитель и смешивать его с битумным вяжущим таким образом, чтобы производимая горячая асфальтобетонная смесь при конечной выгрузке была равномерно покрыта битумным вяжущим и имела желаемую температуру. Чтобы достичь этой цели, барабанный смеситель включает в себя множество элементов, которые описываются ниже.
|
Загрузка заполнителя. Холодный заполнитель из бункеров-дозаторов материала подается в смеситель через серию конвейеров через наклонный желоб или через конвейер. Наклонный желоб загружает заполнитель самотеком под углом, направляющим материал в сторону разгрузочного конца и на дно барабана, дальше от пламени. Подающий конвейер, находящийся под горелкой, имеет достаточную скорость, чтобы «бросать» заполнитель дальше от горелки в раздаточную сторону, так чтобы он не пересекался с пламенем.
Барабан. Заполнитель входит в барабан самотеком через наклонный желоб. Время, которое заполнитель проводит в барабане (время выдержки) зависит от длины барабана, скорости вращения барабана, угла установки барабана, конструкции демпферных колец и размера заполнителя. Обычно время выдержки варьируется от 3 до 4 минут.
Ранние барабанные смесители использовали такую же пропорцию длины к диаметру барабана равную 4:1, как используется в сушилках завода циклического действия, несмотря на то, что сушка и нагрев материала происходит в прямотоке, тогда как конструкция завода циклического действия использует противоток. В некоторых системах материалы RAP добавляются где-то в середине, что приводит к необходимости дополнительной длины для высушивания и правильного нагрева этого материала. Поэтому для барабанов более современного дизайна пропорция длины барабана к диаметру увеличилась до 5:1 или 6:1.
Диаметр барабана это главный элемент конструкции, от которого зависит его производительность. Таблица 6-1 показывает диапазон максимальной производительности барабанной установки. С увеличением диаметра барабана, увеличивается ее производительность, которая оценивается как квадрат диаметра барабана для заполнителя с низкой влажностью. С увеличением содержания влаги, производительность начинает страдать все более сильно, так как необходимо выпарить большее количество добавленной воды. Поэтому хотя диаметр барабана это важный фактор при проектировании оборудования, который в наибольшей степени влияет на потенциальную производительность, влажная составляющая заполнителя это фактор, который влияет на производительность завода.
Пластины это металлические элементы, приваренные или прикрученные внутри и по окружности барабана. Они предназначены для контроля движения заполнителя, когда он проходит через барабан. Хотя каждый производитель использует в своих барабанных установках пластины различных моделей, форм, количества и места их расположения внутри барабана, но все они были разработаны для нагрева и выслушивания заполнителя, использования минимального количество топлива и для достаточного покрытия заполнителя асфальтовым вяжущим. Первый комплект пластин (пластины зоны загрузки) расположен под большим углом в отношении длины барабана, чтобы толкать заполнитель вдоль барабана и дальше от пламени. Если заполнитель попадает в зону факела рядом с точкой входа, это приведет к недостаточному горению и поглощению поверхностью заполнителя капель несгоревшего топлива. Тонкая пленка несгоревшего топлива может значительно уменьшить адгезию тонкой пленки битумного вяжущего с заполнителем, уменьшая долговечность и прочность асфальтобетонной смеси. Удаление заполнителя из зоны горения, позволяет ему увеличить эффективность сжигания топлива и как следствие большую теплоотдачу инертным материалам.
|
Таблица 6-1. Типичная продуктивность барабанных смесителей прямоточного и противоточного типа различных диаметров (1)
Конструкция
Барабана
Диаметр барабана
(футы)
Максимальный выходной объем
(куб. футов в мин.)
Производительность для различных процентов влажности*, тонн в час
Прямоток
Противоток
· 154 °С температура хранения / 149 °С температура при выгрузке (1 тонна = 1364 кг; 1 фут = 0,305 м)
Следующие комплект пластин (зона интенсивной сушки)(от изогнутых пластин с с зазубренными вырезами по свободному краю до просто изогнутых пластин) в процессе вращения барабана поднимают часть заполнителя со дна и в процессе вращения ссыпают в струю горячих выхлопных газов. В процессе продвижения заполнителя вниз вдоль барабана, все большее его количество поднимается и каскадом падает через поток выхлопных газов. В процессе продвижения материала вниз вдоль барабана, в нем установлены пластины все большего размера, чтобы поднимать большее количество высыхающего заполнителя. Дизайн пластин меняется вдоль барабана от пластинчатого типа к зазубренным, и от зазубренных пластин к чашеобразным, каждые из которых поднимает больший объем заполнителя, чем предыдущий. Как только заполнитель проходит чашеобразные пластины, его подающий поток создает завесу поперек барабана. Таким образом увеличивая эффективность теплопередачи и предотвращается проникновение огня и очень горячих газов из места загрузки в точку подачи RAP или битумного вяжущего.
Где-то в середине длинны барабана, сразу после точки подачи материала RAP, некоторые производители устанавливают демпферное кольцо, которое замедляет поток целинного заполнителя. Эти замедляющие движение заполнителя кольца, которые также называют кольцами(donut) или дамбой (dam), прикреплены по окружности внутри барабана и исполняют роль препятствия для потока заполнителя, заставляя заполнитель скапливаться перед кольцом. Когда такое большое количества заполнителя поднимается и ссыпается через диаметральное сечение барабана, плотная завеса заполнителя сразу создается перед местом подачи RAP, что помогает улучшить высушивание и предотвращает проникновение пламени к материалам RAP. Доступ раскаленных газов в зону ввода RAP может вызвать «голубое горение» и привести к проблемам с защитой окружающей среды. Другие производители используют в этом месте барабана толкающие пластины, чтобы бросать заполнитель в обратном направлении, в переднюю сторону барабана. Любая из этих конфигураций производит концентрацию заполнителя перед местом ввода материала RAP.
Смешивающие пластина расположены сразу после середины барабана. Эти пластины часто называют пластинами типа J (J-flights), из-за их изогнутой формы. Они предназначены для поднятия заполнителя и битумного вяжущего и их дальнейшего смешивания посредством вращения и затем кидание смешанного материала через выхлопные газы. Когда битумное вяжущее соприкасается с наполненными влагой выхлопными газами, он начинает пузыриться, увеличиваясь в объеме. Таким образом очень быстро происходит покрытие заполнителя битумным вяжущим и каскад смеси подающий через поток выхлопных газов завершает фазу смешивания, в процессе барабаного смешивания.
В конце барабана установлены разгрузочные пластины, они занимают очень короткий сегмент барабана и предназначены для выталкивания материала из барабана с одной из его сторон или разгрузки под силами гравитации, через специальные окна, в разгрузочный желоб.
Горелки. Важно понять как происходит процесс сгорания, так как это ключ к себестоимости и эффективности. Топливо сжигается для обеспечения тепловой энергии, для выпаривания влаги из заполнителя, его дальнейшего нагрева, а также для нагрева асфальтобетонной смеси до желаемой отгрузочной температуры. Горелки это простые устройства, используемые для эффективного сжигания топлива и таким образом для производства тепла необходимого для высушивания. Эти горелки специально разработаны для нагрева и высушивания заполнителя и используют комбинацию технологий из других областей применения процесса сгорания.
В горелках закрытого типа (с принудительной подачей воздуха), 100 процентов воздуха для горения подается нагнетательным вентилятором. Воздух проталкивается через сужение в точку подачи топлива. Топливо подается под давлением через форсунку с небольшим расширением. Затем оно распыляется маленькими каплями в воздухе, проталкивается через нагнетатели и затем воспламеняется запальником. Для полного сгорания необходима подача достаточного количества воздуха, а также капельки топлива должны быть достаточно маленькими, приблизительно 80 микрон в диаметре.
Второй тип широко используемой горелки, это горелка открытого типа, в которой часть воздуха в зону горения подается засчет разряжения, создаваемого вытяжным вентилятором. Вытяжной вентилятор системы газовой очистки завода обеспечивает до 70 процентов вторичного воздуха для ее горения. Горелка оснащена форсункой для распыления топлива и запальником для его воспламенения. Для поддержания постоянной интенсивности горения, установлено автоматическое регулирование количества топлива поступающего в форсунку.
На асфальтобетонных заводах используются оба вида горелок, чтобы сформировать гибридный тип горелки. На многих заводах 70 процентов необходимого воздуха втягивается вытяжным вентилятором (вторичный воздух) и 30 процентов нагнетается воздуходувкой воздуха горения (главный воздух). В иллюстрации 6-3 дается схематическое изображение горелки гибридного типа. На асфальтобетонных заводах нагнетательная воздуходувка используется также для распыления топлива. Баланс воздуха, необходимого для полного сгорания обеспечивается созданием необходимого разряжения в зоне горения вытяжным вентилятором с системы газовой очистки завода.
Рис. 6-3. Типичная гибридная горелка асфальтового завода, использующая нагнетаемый и всасываемый воздух для горения (2).
Вне зависимости от типа используемой горелки, чтобы убедится в полном сгорании топлива, необходимо обеспечить подачу минимально-необходимого количества воздуха. Это минимальное количество воздуха, необходимое для полного сгорания топлива, определяется как стехиометрическое условие. Обычно добавляется 25 процентов дополнительного воздуха, чтобы убедиться, что в момент возгорания топлива, в горелке дополнительный воздух. Однако в основном горелки это просто распылитель топлива и инжектор, которые подают топливо и часть воздуха, необходимого для горения. Баланс воздуха должен восполняться вытяжным вентилятором. Поэтому, необходимо обеспечить достаточный приток воздуха для вытяжного вентилятора, чтобы он смог справиться с компонентами выхлопных газов сформированных из испарений, водяного пара, продуктов сгорания, избыточного воздуха и подсос воздуха из атмосферы. Ссылка 3 предоставляет указание на взаимоотношения между компонентами выхлопных газов в установке барабанного типа, работающей с производительностью в 250 тонн в час (таблица 6-2). При увеличении содержания влаги в материале, объем испарений и водяного пара увеличивается более значительно, чем другие компоненты потока выхлопного газа.
Чтобы оценить воздействие испарений и водяного пара на производительность обратитесь к Таблице 6-2. Таблицы 6-1 и 6-2 показывают, что для поддержания производительности в 250 тонн в час, необходимый размер барабана увеличивается значительно с увеличением содержания влаги: при 5% содержания влаги необходим барабан в 7 футов, при 10% влаги требуется 9 футовый (2.74 метров) барабан, а при 15% содержании влаги 10 футовый (3.05 метра) барабан не обладает достаточной мощностью системы вывода выхлопных газов, чтобы поддерживать производительность на уровне 250 тонн в час. Поэтому, для поддержания одинаковой производительности в различных частях США, где содержание влаги в запасах материалов сильно отличается, необходимо оборудование различного размера и различные капиталовложения. Во Флориде для поддержания производительности на уровне 250 тонн в час потребуется 10 футовый (3.05 метра) барабан, тогда как в Нью-Мексико или в Аризоне 5 или 6 футового (1.52 или 1.83 м) барабана будет достаточно из-за разницы в содержании влаги в запасах заполнителя.
Совершенно очевидно, что единственный значительный фактор влияющий на производительность барабанной установки определенного размера это содержание влаги в запасе заполнителя. Поэтому подрядчик должен обратить особое внимание не те факторы, которые уменьшают содержание влаги на участке хранения и загрузки заполнителя и должен обучить оператора фронтального погрузчика при наполнении бункеров холодной загрузки всегда работать в наиболее сухой части запасов заполнителя. В регионах с высоким уровнем осадков во время строительного сезона может быть оправдана необходимость в применении защитных мер, например размещение запасов заполнителя на мощеных поверхностях, устройство навеса или другого покрытия или использование постоянных крытых хранилищ.
Таблица 6-2.
|
|
Эмиссия газов от очистных сооружений канализации: В последние годы внимание мирового сообщества сосредоточено на экологических проблемах...
История создания датчика движения: Первый прибор для обнаружения движения был изобретен немецким физиком Генрихом Герцем...
Биохимия спиртового брожения: Основу технологии получения пива составляет спиртовое брожение, - при котором сахар превращается...
Типы сооружений для обработки осадков: Септиками называются сооружения, в которых одновременно происходят осветление сточной жидкости...
© cyberpedia.su 2017-2024 - Не является автором материалов. Исключительное право сохранено за автором текста.
Если вы не хотите, чтобы данный материал был у нас на сайте, перейдите по ссылке: Нарушение авторских прав. Мы поможем в написании вашей работы!