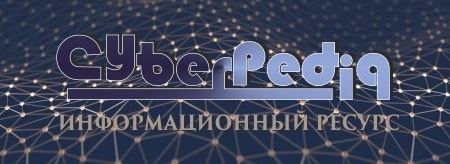
Общие условия выбора системы дренажа: Система дренажа выбирается в зависимости от характера защищаемого...
Биохимия спиртового брожения: Основу технологии получения пива составляет спиртовое брожение, - при котором сахар превращается...
Топ:
Марксистская теория происхождения государства: По мнению Маркса и Энгельса, в основе развития общества, происходящих в нем изменений лежит...
Интересное:
Финансовый рынок и его значение в управлении денежными потоками на современном этапе: любому предприятию для расширения производства и увеличения прибыли нужны...
Берегоукрепление оползневых склонов: На прибрежных склонах основной причиной развития оползневых процессов является подмыв водами рек естественных склонов...
Средства для ингаляционного наркоза: Наркоз наступает в результате вдыхания (ингаляции) средств, которое осуществляют или с помощью маски...
Дисциплины:
![]() |
![]() |
5.00
из
|
Заказать работу |
|
|
Проектирование состава смесей по методу Хвима имеет много общего с методом Маршалла. Для уплотнения образцов в методе Хвима применяется месильный уплотнитель (ASTM D1560). Оценка таких свойств как: количество пустот в общей смеси (VTM), количество пустот в минеральном заполнителе (VMA) и количество пустот, заполненных битума (VFA) проводится одинаково, независимо от какой метод проектирования состава смесей применяется.
Поскольку применялись одни и те же заполнители, то можно предположитьт что были получены те же показатели VTM, VMA и VFA, что и при испытаниях по методу Маршалла. Эти показатели, однако, отличались, поскольку применялись разные способы уплотнения.
Показатели, которые могут быть оценены при подборе оптимального содержания битума для метода проектирования смесей по Хвиму - это стабильность по Хвиму и количество пустот в общей смеси. Для этого метода проектирования смесей количество пустот в общей смеси должно составлять 3-5%, а стабильность по Хвиму – 40-55%. Содержание асфальта 6,9% может так же быть выбрано в качестве оптимального; однако, стабильность по Хвиму, при 6,9%, составляет 40, что является пограничным значением (смотрите рисунок 4-25). Было бы целесообразнее понизить оптимальное содержание битума до 6,3%, что повысило бы величину стабильности по Хвиму до 43, а количество пустот в общей смеси составило 4,9. Прошлый опыт всегда полезен при выборе оптимального содержания битума, поскольку свойства изменяются с начала изготовления на месте, поэтому знание направления, в котором происходят изменения, является положительным.
Рисунок 4-25. Результаты испытания на стабильность по Хвиму
Требования при проектировании состава смесей по методу Суперпейв
|
Верхний слой дорожной одежды из горячей асфальтобетонной смеси (38 мм толщиной) проектируется с таким расчетом, чтобы выдерживать эквивалентную одноосную нагрузку (ESALs) 15000000 в период эксплуатации дорожного покрытия. Требуется заполнитель с номинальным размером зерен 9,5. Заполнители, представленные в таблице 4-14 – приемлемы для использования. Контрольные пределы и предел зоны ограничения представлены в таблице 4-10. На основании информации о внешних условиях в качестве вяжущего используется PG 64-22.
Анализ вяжущего вещества
Убедитесь в том, что вяжущее вещество, которое предполагается использовать, отвечает требованиям для PG 64-22. Предполагается, что для этого метода, результаты испытаний соответствуют требованиям, рассмотренным в главе 2.
Анализ заполнителя
Для выявления требуемых по спецификации свойств заполнителя проводятся специальные испытания. К этим свойствам относятся: удельный вес, абсорбция, истирание L.A. и сульфатоустойчивость. Стандартных требований по удельному весу и абсорбции нет, но эти данные бывают нужны в процессе проектирования смесей. Результаты испытаний показывают, что величины истирания L.A. и сульфатоустойчивости находятся в пределах установленных требований.
Общие типичные свойства заполнителя на поверхности толщиной 100 мм представлены в таблице 4-17.
После того, как определится процентная доля каждого заполнителя, используемого в смеси, смесь заполнителей проверяют на соответствие требованиям спецификации. Для определения характеристик заполнителей проводят четыре согласованных испытания, на каждом заполнителе. Для определения суммарного показателя трех из четырех свойств отдельные компоненты могут быть смешаны математически. Однако, угловатость зерен мелкого заполнителя устанавливается с помощью испытаний на смеси мелких заполнителей.
Таблица 4-17. Общие типичные свойства для эквивалентной одноосной нагрузки 15000000 при использовании на поверхности толщиной 100мм
|
Свойство | Спецификация |
Кубовидность зерен крупного заполнителя | Минимум 95/90 |
Кубовидность зерен мелкого заполнителя | Минимум 45 |
Пластинчатые или игольчатые зерна крупного заполнителя | Максимум 10 |
Эквивалент песка мелкого заполнителя | Минимум 45 |
Результаты испытаний четырех отдельных заполнителей представлены в таблице 4-18
Таблица 4-18. Результаты испытаний для отдельных заполнителей
Свойство | Результаты испытаний | |||
Заполнитель 1 | Заполнитель 2 | Заполнитель 3 | Заполнитель 4 | |
Кубовидность зерен крупного заполнителя | 100/100 | 100/100 | - | - |
Кубовидность зерен мелкого заполнителя | - | 48 | 47 | 42 |
Пластинчатые или игольчатые зерна крупного заполнителя | 3 | 5 | - | - |
Эквивалент песка мелкого заполнителя | - | - | 52 | 58 |
Из результатов испытаний каждого заполнителя, приведенных в таблице 4-18, и требований, приведенных в таблице 4-17, видно, что все заполнители соответствуют требованиям теста по угловатости зерен крупного заполнителя, количеству пластинчатых и игольчатых зерен и эквиваленту песка. Остается единственный вопрос – соответствует ли мелкий заполнитель установленному требованию по кубовидности зерен мелкого заполнителя. Заполнитель 3 соответствует минимальному требованию 45 единиц, в то время как заполнитель 4 не соответствует этому требованию. Если при проектировании смесей используется заполнитель 4, то смесь из заполнителей 3 и 4 следует проанализировать на кубовидность зерен мелкого заполнителя.
Для выявления лучшей структуры заполнителя необходимо проанализировать три гранулометрических состава. В этом случае, один гранулометрический состав находится выше зоны ограничения и два гранулометрических состава - ниже зоны ограничения. Если заполнитель 3 не соответствует требованию по угловатости зерен, то его количество в смеси должно быть доведено до минимума. Подобранные смеси представлены в таблице 4-19.
Экспериментальная смесь №1 находится выше зоны ограничения, а смесь №2 и №3 – ниже этой зоны. Между гранулометрическим составом заполнителя смесей 2 и 3 большой разницы нет. По отношению к имеющимся заполнителям это вопрос диапазона отклонений, которые могут произойти, но все же остаются в контрольных пределах и ниже зоны ограничения. Даже такое маленькое отклонение может привести к формированию совершенно иной структуры заполнителя. График трех экспериментальных гранулометрических составов показан на рисунке 4-26.
|
Чтобы определить кубовидность зерен мелкого заполнителя мелкие заполнители смешиваются для каждого из трех гранулометрических составов. Для гранулометрического состава 1 значение составляет 46 единиц, а для гранулометрического состава 2 и 3 – 47 единиц.
Таблица 4-19. Экспериментальные смеси для анализа структуры заполнителя
Смесь | 9,5 мм | 4,75 мм | 2,36 мм | 1,18 мм | 0,6 мм | 0,3 мм | 0,075 мм |
100% №1 | 89 | 03 | 1 | 1 | 1 | 1 | 0,1 |
100% №2 | 100 | 58 | 10 | 8 | 5 | 4 | 2,2 |
100% №3 | 100 | 99 | 81 | 71 | 46 | 26 | 10,0 |
100% №4 | 100 | 100 | 99 | 94 | 86 | 68 | 2,5 |
Экспериментальная смесь №1 | 99 | 80 | 58 | 51 | 37 | 24 | 5,9 |
Кол-во заполнителя 1-10% | |||||||
Кол-во заполнителя 2-25% | |||||||
Кол-во заполнителя 3-50% | |||||||
Кол-во заполнителя 4-15% | |||||||
Экспериментальная смесь №2 | 96 | 53 | 33 | 29 | 23 | 14 | 3,3 |
Кол-во заполнителя 1-35% | |||||||
Кол-во заполнителя 2-30% | |||||||
Кол-во заполнителя 3-25% | |||||||
Кол-во заполнителя 4-10% | |||||||
Экспериментальная смесь №3 | 97 | 59 | 34 | 30 | 23 | 15 | 3,6 |
Кол-во заполнителя 1-25% | |||||||
Кол-во заполнителя 2-40% | |||||||
Кол-во заполнителя 3-25% | |||||||
Кол-во заполнителя 4-10% |
Экспериментальные смеси
После определения оптимального содержания битума для этих смесей, образцы готовят для анализа структуры заполнителя. В этом случае оптимальное содержание битума оценивается исходя из прошлого опыта с такими же материалами. Оптимальное содержание битума для всех трех смесей заполнителей составило 5,0%.
Число оборотов, необходимое для этого состава смеси, составляет 128, что отражено в таблице 4-11 (исходя из эквивалентной одноосной нагрузки 15 млн. и средней высокой расчетной температуры воздуха 41-42С). Параметры Ni и Nm составляют 9 и 208 соответственно. Таким образом, все смеси уплотнятся при 208 оборотах. Величины плотности при Nd и Ni определяются, вычислением объема на основании замеров высоты в период уплотнения, и внесением поправок на основании сравнения измеренной и фактической плотности при Nm.
|
Рисунок 4-26. График гранулометрического состава трех экспериментальных смесей
Таблица 4-20. Волюметрические данные по экспериментальным смесям
Номер образца | Число об. | Вес образца, (граммы) | Высота (мм) | Объем (см3) | Неуточн. плотн. | Теор. макс. плотн. | Неуточнен. плотность | Уточнен. плотн. |
Эксперимент. смесь №1
Эксперимент. Смесь №2
Эксперимент. Смесь №3
Волюметрические результаты по уплотнению образцов экспериментальных смесей представлены в таблице 4-20. Результаты испытаний собирали по интервалам от 10 оборотов до 100, и затем по интервалу 25 через Nd и Nm. Здесь представлены результаты для 9, 128 и 208 оборотов, при которых проводился анализ качества НМА. Высота этих образцов определяется как высота уплотняемого образца. Затем рассчитывают объем, исходя из диаметра (150 мм) и измеренной высоты. Величина неуточненной плотности рассчитывается на основании веса образца и измеренного объема. Фактическая плотность определяется для каждого образца, уплотняемого до Nm. Поправочный коэффициент определяется исходя из фактической плотности при Nm и измеренной плотности Nm. Этот коэффициент применяется к неуточненной плотности при других уровнях вращения для определения уточненной плотности.
Данные по уплотнению экспериментальных смесей представлены в сводной таблице 4-21. Эти данные следует преобразовать для предполагаемого оптимального содержания битума (содержание битума, при котором количество пустот составляет 4%), чтобы полностью проанализировать ожидаемое качество смеси при оптимальном содержании асфальта. Чтобы вычислить оптимальное содержание нужно сначала скорректировать используемое содержание битума (0,5%). Расчеты производятся по следующей формуле:
|
Pbe = Pbi – (0,4 x (4 – Va))
где:
Pbe = вычисленное оптимальное содержание битума
Pbi = содержание битума, использованные в экспериментальных смесях
Va = процент пустот
Таблица 4-21. Данные по уплотнению экспериментальных смесей
Определение | Объемная плотность заполнителя | % битума | Кол-во пустот в общей смеси | Кол-во пустот в минеральном заполнителе | Заполненные пустоты | % Gmm при Ni | % Gmm при Ni |
Смесь №1 | 2,631 | 5,0 | 4,5 | 15,4 | 70,8 | 88,4 | 97,4 |
Смесь №2 | 2,625 | 5,0 | 3,8 | 14,8 | 74,3 | 86,7 | 97,6 |
Смесь №3 | 2,622 | 5,0 | 4,2 | 15,0 | 72,0 | 86,6 | 97,2 |
Таким образом, вычисленное оптимальное содержание битума для экспериментальных смесей 1,2 и 3 составляет 5,2; 4,9 и 5,1 соответственно. Теперь можно вычислить количество пустот в минеральном заполнителе при установленном значении оптимального содержания асфальта по следующей формуле:
VMAe = VMAi + C x (4-Va)
где:
VMAe = рассчитанное количество пустот в минеральном заполнителе
VMAi = исходное количество пустот для экспериментальной смеси
С = постоянная величина: 0,1 если количество пустот менее 4,0%
0,2, если количество пустот выше 0,4%
Va = количество пустот
Расчетное количество пустот при оптимальном содержании битума составляет 15,3; 14,8 и 15,0 для смесей 1,2 и 3 соответственно. Процент пустот, заполненных битумом, при оптимальном его содержании оценивают при помощи уравнения:
VFAрасчетное = 100 ((VMAe – 4,0) / VMAe)
Следовательно, для экспериментальных смесей 1, 2 и 3 процент пустот, заполненных битумом, составляет 73,8%; 73,0% и 73,3% соответственно. Теперь рассчитывают процент Gmm при Ni для оптимального содержания битума. Для этого используется уравнение:
Расчетный процент Gmm при Ni = % Gmm для испытательной смеси при Ni – (4,0 - Va)
Таким образом, расчетный процент Gmm при Ni для оптимального содержания асфальта у смесей 1, 2 и 3 составляет 88,9 86,5 и 86,8 соответственно. Теперь рассчитывают процент Gmm при Nm для оптимального содержания асфальта. Для этого используется уравнение:
Расчетный процент Gmm при Nm = % Gmm для испытательной смеси при Nm – (4,0 - Va)
Замена одного компонента уравнения дает значения 97,9; 97,4 и 97,4 для смесей 1,2 и 3 соответственно.
Теперь волюметрические данные и данные по уплотнению сводят в одну таблицу. Смотрите таблицу 4-22.
Таблица 4-22. Сводная таблица расчетных параметров для экспериментальных смесей с оптимальным содержанием асфальта
Смесь | Расчетный % Gmm при Ni | Расчетный % Gmm при Nm | Расчетное оптимальное содержание битума | Расчетное кол-во пустот в минеральном заполнителе | Расчетное кол-во заполненных пустот |
1 | 88,9 | 97,9 | 5,2 | 15,3 | 73,8 |
2 | 86,5 | 97,4 | 4,9 | 14,8 | 73,0 |
3 | 86,8 | 97,4 | 5,1 | 15,0 | 73,3 |
Проанализировав данные, приходим к выводу, что смесь №3 является самой подходящей. Смесь №1 не соответствует требованиям по Ni и Nm для процентного содержания Gmm. Смесь №2 не соответствует требованиям по количеству пустот в минеральном заполнителе с номинальным размером зерен 9,5 мм.
|
|
Адаптации растений и животных к жизни в горах: Большое значение для жизни организмов в горах имеют степень расчленения, крутизна и экспозиционные различия склонов...
Архитектура электронного правительства: Единая архитектура – это методологический подход при создании системы управления государства, который строится...
Типы оградительных сооружений в морском порту: По расположению оградительных сооружений в плане различают волноломы, обе оконечности...
Особенности сооружения опор в сложных условиях: Сооружение ВЛ в районах с суровыми климатическими и тяжелыми геологическими условиями...
© cyberpedia.su 2017-2024 - Не является автором материалов. Исключительное право сохранено за автором текста.
Если вы не хотите, чтобы данный материал был у нас на сайте, перейдите по ссылке: Нарушение авторских прав. Мы поможем в написании вашей работы!