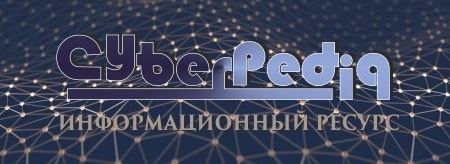
Историки об Елизавете Петровне: Елизавета попала между двумя встречными культурными течениями, воспитывалась среди новых европейских веяний и преданий...
Общие условия выбора системы дренажа: Система дренажа выбирается в зависимости от характера защищаемого...
Топ:
Теоретическая значимость работы: Описание теоретической значимости (ценности) результатов исследования должно присутствовать во введении...
Техника безопасности при работе на пароконвектомате: К обслуживанию пароконвектомата допускаются лица, прошедшие технический минимум по эксплуатации оборудования...
Установка замедленного коксования: Чем выше температура и ниже давление, тем место разрыва углеродной цепи всё больше смещается к её концу и значительно возрастает...
Интересное:
Берегоукрепление оползневых склонов: На прибрежных склонах основной причиной развития оползневых процессов является подмыв водами рек естественных склонов...
Что нужно делать при лейкемии: Прежде всего, необходимо выяснить, не страдаете ли вы каким-либо душевным недугом...
Лечение прогрессирующих форм рака: Одним из наиболее важных достижений экспериментальной химиотерапии опухолей, начатой в 60-х и реализованной в 70-х годах, является...
Дисциплины:
![]() |
![]() |
5.00
из
|
Заказать работу |
|
|
Для качества чугуна играет большую роль форма и размер графитных включений. С целью образования структуры мелкого графита в жидкий чугун перед разливкой его по формам вводят небольшое количество веществ, образующих нерастворимые в чугуне частицы, которые при затвердевании служат центрами кристаллизации графита.
Добавление в жидкий металл элементов, образующих дополнительные центры кристаллизации, называется модифицированием, а сами элементы - модификаторами. Модификаторами служат элементы: кальций (силикокальций), алюминий, кремний (ферро-силиций) и др., образующие при добавке в чугун соответствующие окислы: СаО; Al2 О3; Si2 О3 путем соединения с растворенным в чугуне кислородом, и находятся в жидком чугуне первое время во взвешенном состоянии.
В результате модифицирования чугун приобретает более высокие механические свойства. Кроме того чугун модифицируют алюминием (бором, висмутом и др. элементами) с целью ускорения отжига. В этом случае длительность отжига составляет 24-60 часов.
Модифицированию подвергают низкоуглеродистый чугун, сравнительно небольшое содержа-ние кремния и повышенное содержание марганца и имеющий без введения модификаторов структуру половинчатого чугуна, т.е. ледебурит, перлит и графит.
Марки модифицированного чугуна: СЧ 28-48, СЧ 32-52, СЧ 35-56 и СЧ 38-60.
Высокопрочный чугун получают присадкой в жидкий чугун небольших добавок некоторых щелочных и щелочноземельных металлов. Чаще для этой цели применяют магний. В количестве 0,03-0,07 %. По содержанию остальных элементов высокопрочный чугун не отличается от обычного серого чугуна.
Под действием магния графит в процессе кристаллизации принимает не пластинчатую, а шаровидную форму. Шаровидный графит значительно меньше ослабляет металлическую ос-нову чугуна, по сравнению с пластинчатым графитом. В отличие от пластинчатого шаровид-ный графит не является активным концентратором напряжений. Эти чугуны имеют более высокие механические свойства, не уступающие литой стали, сохраняя при этом положитель-ные свойства чугуна: хорошие литейные свойства и обрабатываемость резанием, способность гасить вибрацию, высокую износостойкость и т.д.
|
Обычный состав чугуна: С≤ 3,3 %; 2,2 -2,5 % Si; 0,5-0,8 %Мn; S ≤ 0,14 %; Р ≤ 0,2 %.
Маркировка высокопрочных чугунов осуществляется в соответствии с ГОСТ 7993-90. Например, ВЧ 40-10 означает - высокопрочный чугун со средним пределом прочности при растяжении - 40 кгс/мм²; с относительным удлинением – 10 %.
Чугуны ВЧ 50- 1,5 и ВЧ 60-2 имеют перлитную металлическую основу, чугуны ВЧ 45-5 перлитно - ферритную и ВЧ 40-10 – ферритную. Для снятия литейных напряжений, повышения механических свойств чугун нередко подвергают термической обработке.
Отливки из высокопрочного чугуна широко используются в различных отраслях народного хозяйства. Так, в автостроении и дизелестроении высокопрочный чугун применяется для коленчатых валов и др.; в тяжелом машиностроении для многих деталей прокатных станов и кузнечно-прессовом оборудовании (для шабот - молотов, траверс прессов, прокатных валков); в химической и нефтяной промышленности для корпусов насосов, вентилей и т.д.
В подшипниковых узлах используются антифрикционные чугуны с глобулярным графитом: АВЧ -1 с перлитной структурой и АВЧ -2 с повышенным содержанием кремния (2,2-2,7 %) и ферритно - перлитной структурой (50 % перлита) для работы с термически необработанными валами.
Разряд.
1.Сплавы железа с углеродом, в которых содержится более 2,14 % углерода называют чугунами (см. рисунок 14. Диаграмма железо – углерод (цементит).
При кристаллизации доэвтектических сплавов, содержащих от 2,14 до 4,3 % С, из жидкой фазы по достижении температур, соответствующих линии ликвидус ВС, сначала выделяются кристаллы аустенита. Состав жидкой фазы в интервале температур кристаллизации определяется линией ВС, а аустенита - линией JЕ.
|
При температуре 1147°С (или 1130 °С - температура эвтектики) в результате кристаллизации жидкого сплава состава С (4,3 % углерода) образуется эвтектика. Линия ЕСF (линия солидус) соответствует кристаллизации эвтектики - ледебурит (АЕ + Fe3C). Жс→АЕ + Fe3C.
Эвтектический сплав (4,3 %С) затвердевает при постоянной температуре с образованием только эвтектики - ледебурита (АЕ + Fe3C.)
На линии ликвидус CD в жидкой фазе при охлаждении начинают зарождаться кристаллы цементита. После окончательного затвердевания сплава линии СF (солидус) заэвтектические чугуны (4,3-6,67 %С) состоят из первичного цементита и ледебурита.
Характерные линии.
Линия SE (723 °С - 1130 °С). Окончание растворения цементита в аустените в заэвтектоидных сталях. Начало выделение цементита из аустенита в заэвтектоидных сталях. Критические точки - Асm (при нагреве) и Аr m (при охлаждении).
Линия РSК (727 °С). Превращения перлита в аустенит при нагреве. Превращения аустенита в перлит при охлаждении. Критические точки - Ас1(при нагреве) и Аr1(при охлаждении).
Линия ECF (1130 °С или 1147 °С)- начало плавления чугуна при нагреве; окончание затвердевания чугуна при охлаждении.
Линия АВСD - окончание расплавления стали и чугуна при нагреве начало затвердевания стали и чугуна при охлаждении.
2. В зависимости от содержания углерода, а, следовательно, и от структуры чугуны делятся на доэвтектические, эвтектические и заэвтектические. Их структура, а также вызываемые нагревом и охлаждением превращения отражаются диаграммой состояния Fe-С.
Структурными составляющими белых чугунов является перлит, ледебурит и первичный цементит. Перлит белых чугунов под микроскопом ничем не отличается ни по составу, ни по виду от перлита сталей.
Доэвтектическими -называют чугуны с содержанием углерода от 2,14 до 4,3 %. Доэвтетические чугуны после окончательного охлаждения имеют структуру, состоящую из темных участков перлита, ледебурита и вторичного цементита. С увеличением содержания углерода количества ледебурита в доэвтектических чугунах также увеличивается и при 4,3% С достигает 100 % занимаемой на микроструктуре площади (рисунок 26 а).
|
а (х300)
б (х450)
в (х150)
перлит ледебурит ледебурит цементит
Рисунок 26 – Микроструктура белых чугунов.
Ледебурит – цементитная эвтектика, представляющая собой смесь перлита с цементитом. Строение ледебурита более грубое, чем перлита в стали, поэтому оно различимо уже при увеличении порядка х200.
Эвтектическим называется чугун, структура которого состоит из одного ледебурита (перлит + цементит), с содержанием углерода 4,3 %С (рис. 26 б)
Заэвтектическими -называют чугуны с содержанием углерода свыше 4,3 %С (4,3-6,67 %С). Их структура состоит из первичного цементита в виде светлых игл и ледебурита (рис.26 в).
Серые чугуны, характеризуются наличием графита. Основа структуры серых чугунов ни чем не отличается от структуры сталей, т. е. может быть перлитной, перлито-ферритной и ферритной. Серые чугуны можно рассматривать как сталь с включениями графита. В зависимости от структуры основы различают перлитные, перлито-ферритные и ферритные чугуны.
Механические свойства серых чугунов в основном определяются формой и величиной графитовых включений. По форме графитовые включения бывают пластинчатыми (лепест-ковыми), хлопьевидными и шаровидными. Чугуны с хлопьевидной формой принято называть ковкими, а с шаровидной – высокопрочными.
Образование графитовых включений в той или иной форме зависит от многих факторов (ско-рости охлаждения, наличия некоторых примесей, применения модифицирования, термической обработки), которые в свою очередь оказывают влияние также на распад аустенита и образование определенной структуры основы.
По структуре основы эти чугуны делятся на: перлитные, перлито-ферритные, ферритные.
а (х340)
б (х340)
в (х450)
перлитные перлито-ферритные ферритные
Рисунок 27 – Микроструктура серых чугунов.
Ковкие чугуны получают из белых путем длительного отжига (томления). В результате такой термической обработки происходит распад цементита с образованием графита хлопьевидной формы. По структуре основы эти чугуны делятся на: перлитные, ферритные.
а (х200)
б (х200)
Перлитные ферритные
Рисунок 28 – Микроструктура ковких чугунов.
|
Высокопрочный чугун получают путем модификации расплавленного чугуна перед разливкой магнием (0,5-1,0 %), в результате чего выделяющийся графит принимает шаровидную форму (см. рисунок 18).
Тема № 5. Стали.
Разряды.
1. Железоуглеродистые сплавы содержащие до 2,14% углерода называют сталью.
Для выплавки стали применяют передельные и специальные чугуны. Их получают восстановлением из природных руд железа с последующим насыщением его углеродом. Чугун выплавляют в высоких шахтных печах - домнах.
Все применяемые в промышленности стали принято разделять на сорта по тем или иным признакам: по способу производства, химическому составу и назначению.
По способу производства сталь разделяют на мартеновскую (основную и кислую), выплавляемую в мартеновских печах, бессемеровскую, томасовскую, получаемую в конверторах, и электросталь, выплавляемую в дуговых или высокочастотных электропечах.
В мартеновских печах сталь получается в больших количествах, хорошей плотности и однородности, невысокой стоимости. Но экономичнее технологический процесс выплавки стали в кислородных конверторах. Сталь вполне качественная, пригодна для всех отраслей машиностроения. Примеси серы и фосфора в этой стали ниже, чем в мартеновской.
Наилучшими качествами обладает электросталь. Она чище мартеновской по фосфору, сере, газам, а также по неметаллическим примесям. Электростали применяются для изготовления ответственных деталей.
В зависимости от условий и степени раскисления различают следующие виды сталей.
Сталь спокойной плавки при разливке в изложницы выделяет мало газов и не кипит. Она полностью раскислена (очищена от закиси железа) марганцем, кремнием и алюминием, спокойно затвердевает, слиток получается плотным с образованием в верхней части усадочной раковины.
Кипящая сталь в процессе заливки кипит, выделяя большое количество газов, в связи с тем, что сталь заливается в изложницы не полностью раскисленной и при понижении температуры часть углерода вступает в реакцию с оставшейся закисью железа. Весь углерод не успевает выделиться из затвердевающего металла, оставаясь в нем в виде газовых пузырей.
Кипящая сталь не образует усадочной раковины. Полученные газовые микропоры завариваются в слитке при последующей прокатке. Кипящая сталь хорошо сваривается и штампуется при обработке листового проката, но по качеству уступает спокойной стали.
Полуспокойные стали – представляют стали промежуточного типа. Они получают все более широкое применение. Кипящие стали при маркировке дополнительно обозначают «кп», полуспокойную «пс» и спокойную «сп» или без обозначения.
По химическому составу стали делятся углеродистые и легированные.
|
По назначению стали разделяются на:
1.Конструкционные - применяются в основном для деталей машин и сооружений.
2. Инструментальная -применяются для изготовления инструмента.
3. Сталь с особыми физическими и химическими свойствами -применяется для изготовле-ния специальной аппаратуры и деталей машин (хромистые, никелевые, хромоникелевые).
По химическому составу конструкционная и инструментальная стали делятся на углеродистые и легированные. Сталь с особыми свойствами бывает только легированной.
2. Углеродистые стали. Сталь обыкновенного качества - наиболее дешевые. В процессе выплавки они меньше очищаются от вредных примесей содержат больше серы и фосфора. Кроме того они отливаются в крупные слитки, вследствие чего в них значительно развита ликвация (неоднородность) и они нередко содержат большое количество неметаллических включений. Они используются для менее ответственного назначения.
Углеродистая конструкционная сталь может быть обыкновенного качества (ГОСТ 380-2005) и качественной (ГОСТ1050-88).
Сталь обыкновенного качества разделяется на три группы: группы А, группы Б и В.
К группе А относится сталь, которая регламентируется только механическими свойствами, данные о химическом составе не приводятся. Обозначаются буквами Ст (сталь) и цифрами 1,2,3… 6. Чем больше это число, тем больше содержание углерода, а, следовательно, выше прочность и ниже пластичность. К ним относятся следующие марки стали: Ст0, Ст1, Ст2,Ст3, Ст3кп, Ст4, Ст4кп, Ст5.
Стали группы А применяют для деталей, используемых без термической обработки или обработки давлением, поскольку их химический состав может сильно колебаться: для лент, листов, проволоки др.
Сталь группы Б регламентируется только химическим составом, перед маркой такой стали при выплавке в мартеновской печи ставят букву М, например МСт1, а при бессемеровском производстве - букву Б, например БСт3.
К ним относятся марки: БСт0, БСт1кп, БСт2кп, БСт2сп, БСт3кп, БСт3сп, БСт4кп, БСт4сп, БСт5пс, БС5сп, БС5Гпс, БС6пс, БСт6сп. Сталь группы Б применяется для листового проката: швеллеров, балок, уголков, труб и др.
Сталь группы В представляет стали повышенного качества, которые поставляют с гарантированным химическим составом и механическими свойствами. В обозначении марки данной группы вводится буква В. Стали группы В выплавляют следующих марок: ВСт2, ВСт3, ВСт4, ВСт5. Состав данной стали соответствует аналогичной марке, из группы Б, а механические свойства – той же марке из группы А.
Стали группы Б и В применяют, когда сталь должна подвергаться горячей деформации или уп- рочняться термической обработкой, так как для определения режимов обработки необходимо знать химический состав стали. Стали группы В спокойные и полуспокойные применяют для изготовления сварных конструкций. Также они применяются для специализированного назначения: мосто- и судостроении, сельскохозяйственном машиностроении и т.д.
Качественную углеродистую конструкционную сталь выплавляют кислородно-конверторным способом в мартеновских и электропечах в зависимости от степени раскисления они могут быть спокойными или кипящими. Качественные стали выплавляют с соблюдением более строгих условий в отношении шихты и введения плавки и разливки. К сталям этой группы предъявляются более высокие требования относительно состава (ограничены пределы по содержанию углерода, меньшее содержание серы ≤ 0,04 % и фосфора ≤ 0,035- 0,04 %) количества неметаллических включений, макро – и микроструктуре.
Они разделяются на две группы: с нормальным содержанием марганца и с повышенным содержанием марганца. Сталь группы I применяют в виде прутков, поковок, листов и т.п. Такие стали маркируют цифрами 05, 08, 08кп (буквы «кп» означают кипящую сталь), 10, 20, 35 и т.д., показывающими среднее содержание углерода в сотых долях процента. В машиностроении из нее изготавливают валы, зубчатые колеса, шпиндели, вилки переключения, болты и т. п. Химический состав углеродистой конструкционной стали группы I приведен в ГОСТ 1050-88 (05кп, 08кп, 10, 20, 35, 45, 50, 65).
Качественные углеродистые конструкционные стали группы II с содержанием марганца от 0,7-1,0 % маркируют следующим образом: 15Г, 20Г, 40Г, 45Г, 50Г, 65Г. Буква Г указывает на повышенное содержание марганца. Марганец повышает прокаливаемость деталей, что позволяет получать после закалки и высокого отпуска повышенную прочность, вязкость и износостойкость. Однако сталь имеет склонность к перегреву и хрупкость после отпуска.
Автоматная сталь относится к конструкционным углеродистым сталям. Она содержит повышенный процент серы (0,08-0,3 %) и фосфора (0,08-0,15 %). Автоматная сталь маркируется буквой А и цифрами, которые указывают на содержание углерода в сотых долях процента, например сталь марки А12, А20 и т.д. Для повышения производительности применяют стали с добавкой свинца 0,15-0,3 %, обозначаемые АС (АС14, АС35Г2). Свинец в процессе резания снижает коэффициент трения и усилия резания. Сталь обладает хорошей обрабатываемостью резанием. Используется для изготовления болтов, гаек с мелкой резьбой и винтов на станках - автоматах. Детали из автоматной стали подвергают химико-термической обработке - нитро-цементации, цианированию.
Углеродистая инструментальная сталь - делится на качественную марок У7, У8 и т.д. и высококачественную с повышенным содержанием кремния и пониженным содержанием серы и фосфора (0,15- 0,30 % Si; не более 0,020 % S; не более 0,030 % P).
Буква У в марках стали означает углеродистую, а число, стоящее за буквой, указывает на содержание углерода в десятых долях процента. Буквой А, стоящей после цифры маркируются высококачественные стали. Например, У7А, У8А, У12А и т.д.
Особенностью углеродистых сталей является их небольшая прокаливаемость. Инструменты - зубила, клейма, молотки т.д., подвергаемые в работе ударам, изготавливают из стали У7А, У7, У8. У8А. Высокоуглеродистые стали У9, У9А, У10А, У12, У12А применяют для режущих ин-струментов - сверл, метчиков, фрез, разверток и т.д.
3. Легированные стали. Легированной сталью называют сталь, содержащую один или несколько легирующих элементов в различных комбинациях и количествах, изменяющих свойства этой стали и условия ее термической обработки. К легирующим элементам относятся хром, никель, титан, вольфрам, молибден, ванадий и др. Кроме того легирующими элементами могут быть кремний и марганец, если кремния в стали содержится не менее 0,8 %, а марганца - более 1 %.
Основной целью легирования стали является увеличение ее прокаливаемости. Высокие меха-нические свойства сталь получает после соответствующей термической обработки.
Маркировка легированных сталей. Легированные стали маркируют по буквенно –цифровой системе. Легирующие элементы обозначают русскими буквами, например хром - Х, никель – Н, марганец - Г, молибден - М, вольфрам - В, ванадий - Ф, алюминий - Ю, кремний - С, кобальт - К, титан - Т, бор - Р, и медь - Д.
Первые цифры в марках стали указывают на содержание углерода в сотых долях процента, а цифры, стоящие за буквой, на содержание легирующих элементов. Буква А в конце марки означает сталь с пониженным содержанием вредных примесей – серы и фосфора. Например, сталь 12ХН3А, расшифровывается так: 0,12 % углерода, около 1,0 % хрома, около 3,0 % никеля, буква А указывает на минимальное содержание серы и фосфора.
Если содержание легирующего компонента равно или меньше 1,0%, то цифра после буквы не ставиться.
Некоторые легированные стали обозначают буквами, стоящими впереди, Ш - шарикоподшипниковая, Р - быстрорежущая, Е - электротехническая.
Легированная конструкционная сталь. Из легированных конструкционных сталей изготавливают ответственные детали автомобилей, тракторов, металлорежущих станков и т.д.
По сравнению с углеродистыми конструкционными сталями легированные конструкционные стали обладают более высокими прочностными характеристиками и прокаливаемостью на большую глубину. Химический состав наиболее распространенных легированных сталей приведен в ГОСТ 4543-71 (15Х, 40Х, 20ХГ, 14959-79 (50С2,60С2, 60СГ, 50ХГ, 50ХГФА) ГОСТ 801-78 (18ХНВА, ШХ6, ШХ9 ШХ15, ШХ15СГ).
Легированная инструментальная сталь. По сравнению с углеродистой инструментальной сталью легированная инструментальная сталь высокими сопротивлением и твердостью, а также прокаливаемостью на большую глубину. Химический состав легированной инструментальной стали приведен в ГОСТ 5950-2000 (В1, Х, ХГ, ХВГ, 9ХС, ХВ5, Х12Ф1, 5ХНМ, 5ХНТ, 3Х2В8). Инструмент, изготавливаемый из легированной инструментальной стали охлаждают в масле, что препятствует образованию трещин. Из стали В1 изготавливают сверла и метчики, из стали Х, ХГ и 9ХС - фрезы, сверла, плашки, калибры и штампы, деформирующие металл в холодном состоянии. Сталь ХВГ мало деформируется, поэтому из нее изготавливают шпоночные протяжки, развертки и калибры. Из стали Х6ВФ и Х12Ф1 изготавливают инструменты, которые должны иметь высокую твердость и повышенную износостойкость - накатные плашки, статоры гидронасосов, гибочные и обрезные штампы и т.д. Стали 5ХНВ, 5ХНМ, 5ХНТ обладают большой вязкостью и прокаливаемостью, поэтому их применяют для кузнечных молотовых штампов, на которых деформируется металл в горячем состоянии. Сталь 3Х2В8 весьма прочная и устойчивая против воздействия высоких температур, поэтому из нее изготавливают матрицы, пуансоны и пресс-формы для литья под давлением медных и алюминиевых сплавов.
Быстрорежущие стали по своему химическому составу являются высоколегированными. Они содержат вольфрам, хром, ванадий, молибден, кобальт. Быстрорежущие стали обладают высокими прочностью, твердостью и красностойкостью. Наиболее распространенной маркой быстрорежущей стали является сталь Р18, содержащая 0,7-0,8 % углерода, 17,5-19,0 % вольфрама, 3,8- 4,4 % хрома и 1,0-1,4 % ванадия. Из такой стали изготавливают червячные развертки, сверла, долбяки, протяжки и другой инструмент. В качестве заменителя стали Р18 применяют быстрорежущую сталь Р9.
К сталям с особыми физическими свойствами относятся: нержавеющие, кислото-, окалино- и износостойкие, жаропрочные, магнитные, немагнитные электротехнические и сплавы с высоким сопротивлением.
Разряд.
1.Влияние углерода. С увеличением содержания углерода изменяется структура стали. Сталь, содержащая 0,8 %С, состоит из одного перлита, а в стали, содержащей больше 0,8 % С, кроме перлита, имеется вторичный цементит, а если меньше 0,8 %С, то структура стали состоит из феррита и перлита (см. рисунок 14. Диаграмма Fe – C). Увеличение углерода в стали ведет к повышению прочности и понижению пластичности. Влияние углерода на механические свойства и структуру представлено на рисунке 29
|
При малом содержании углерода сталь обладает низкой прочностью, высокими пластичностью, свариваемостью и деформацией в холодном состоянии (штампуется). При содержании углерода более 0,3 % сталь хорошо закаливается. С увеличением углерода в стали снижается плотность, растет электро-сопротивление и коэрцитивная сила и понижается теплопроводность, остаточная индукция магнитная проницаемость.
Влияние примесей. Сталь является многокомпонентным сплавом, содержащим углерод и ряд постоянных, а иногда неизбежных примесей Мn, Si, S, P,O, N, H и др., которые оказывают влияние на ее свойства.
Влияние кремния и марганца. Содержание кремния в углеродистой стали в качестве примеси обычно не превышает 0,35-0,4 % и марганца 0,5- 0,8 %. Кремний и марганец пере-ходят в сталь в процессе ее раскисления при выплавке. Кремний и марганец раскисляют, т.е., соединяясь с кислородом закиси железа FeO, в виде окислов переходят в шлак. Эти процессы раскисления улучшают свойства стали.
Кремний (Si), остающийся после раскисления в твердом растворе (в феррите), сильно повышает предел текучести σт. Это снижает способность стали к вытяжке особенно к холодной высадке. Поэтому в сталях, предназначенных для холодной штамповки и высадки, содержание кремния должно быть сниженным.
Марганец ( Мn) заметно повышает прочность, практически не снижая пластичности и резко уменьшая красноломкость стали, т.е. хрупкость при высоких температурах, вызванную влиянием серы.
Влияние серы ( S). Сера является вредной примесью в стали. С железом она образует химическое соединение FeS, которое практически не растворимо в железе в твердом состоянии, но растворимо в жидком металле. Соединение FeS с железом образуют легкоплавкую эвтектику, с температурой плавления 988 ° С. Кристаллизуясь из жидкости по окончании затвердевания, эвтектика преимущественно располагается по границам зерна. При нагревании стали до температуры прокатки или ковки (1000 – 1200 ° С) эвтектика расплавляется, нарушается связь между зернами металла и вследствие этого при деформации стали возникают надрывы и трещины. Это явление называется красноломкостью.
Марганец образует с серой тугоплавкое соединение MnS, практически исключает явление красноломкости.
Сернистые включения резко снижают механические свойства, особенно вязкость и пластичность (в поперечном направлении вытяжки при прокатке и ковке), а также предел выносливости. Эти включения ухудшают свариваемость и коррозионную стойкость.
Поэтому содержание серы в стали строго ограничивают. В зависимости от качества стали оно не должно превышать 0,035-0,06 %. Для высококачественной стали сера не превышает 0,02-0,03 %, для стали обыкновенного качества допускается 0,03-0,04 %S.
Влияние фосфора (Р). Фосфор растворяется в феррите и аустените, а при высоком содержании образуется фосфид Fe3P, содержащий 15,62 % Р.Растворяясь в феррите, фосфор сильно искажает кристаллическую решетку и увеличивает пределы прочности и текучести, но сильно уменьшает пластичность и вязкость. Снижение вязкости тем значительнее, чем больше в стали углерода. Фосфор значительно повышает порог хладноломкости стали и уменьшает работу развития трещины. Каждые 0,01 %Р повышает порог хладноломкости стали на 20-25 ° С.
Кроме того, фосфор склонен к ликвации. Вследствие этого в серединных слоях слитка отдельные участки сильно обогащаются фосфором и имеют резко пониженную вязкость. В большинстве сталей фосфор является вредной примесью и в зависимости от качества стали его содержание допускается не более 0,025- 0,08 %.
Влияние азота, кислорода и водорода. Азот и кислород присутствуют в стали в виде хрупких неметаллических включений (например, окислы FeO, SiO2, Al2O3, Fe4N и др.), в виде твердого раствора или, находясь в свободном виде, располагаются в дефектных участках металла (раковины, трещины и т.д.). Примеси внедрения (азот, кислород), концентрируясь в зернограничных объемах и, образуя выделения нитридов и оксидов по границам зерен, повышают порог хладноломкости и понижают сопротивление хрупкому разрушению. Неметаллические включения (окислы, нитриды, частицы шлаков и т.п.), являются концент-раторами напряжений, могут в значительной мере понизить, если они присутствуют в повы-шенных количествах или располагаются в виде скоплений, предел выносливости и вязкость разрушения.
Очень вредным является растворенный в стали водород, который сильно охрупчивает сталь. Поглащенный при выплавке стали водород не только охрупчивает сталь, но приводит к образованию в катаных заготовках и крупных поковках флокенов. Флокены представляют собой очень тонкие трещины овальной или округлой формы, имеющие в изломе вид пятен - хлопьев серебристого цвета. Флокены резко ухудшают свойства стали. Металл, имеющий флокены, нельзя использовать в промышленности. Водородное охрупчивание стали часто наблюдается при сварке. Оно проявляется в образовании холодных в наплавленном и основ-ном металле.
Нанесение на поверхность стальных изделий гальванических покрытий или травление в кислотах для очистки поверхности от окалины и загрязнений связано с опасностью насыщения поверхности водородом, что также вызывает охрупчивание. Если водород находится в поверхностном слое, то он может быть удален в результате нагрева при 150-180 °С, лучше всего в вакууме. Наводороживание и охрупчивание возможно и при работе стали в контакте с водородом, особенно при высоком давлении.
Наиболее вероятно хрупкость вызывается давлением молекулярного водорода, выделившегося в порах, трещинах и других несплошностях металла, а также в зоне концентрации дефектов строения, особенно в процессе пластического деформирования. Именно с влиянием водорода связано появление склонности к так называемому замедленному разрушению.
Применяемые в последние годы выплавка или разливка в вакууме значительно уменьшает содержание водорода в стали.
Высококачественные стали отличаются от качественных с тем же содержанием углерода, ограничением вредных примесей S и P. В высококачественных сталях допускается содержание фосфора не более 0,03 % иногда не более 0,025 %, содержание серы до 0,03 %.
Для сталей качественной и обычного качества допускается более высокое содержание серы -0,04-0,05 %.
Углеродистая инструментальная сталь делится на качественную марок У7, У8 и т.д. и высококачественную с повышенным содержанием кремния и пониженным содержанием серы и фосфора (0,15- 0,30% Si; не более 0,020 % S; не более 0,030 % P).
Высококачественные стали маркируются дополнительной буквой А после цифр, например У8А или для легированных конструкционных - 38ХА, 35Х2МА.
2. Классификация углеродистой стали приведена в 1-2 разряде.
Качественную углеродистую конструкционную сталь в зависимости от содержания углерода классифицируют на низкоуглеродистые с содержанием углерода до 0,3 %, среднеуглеродистые с содержанием углерода 0,3- 0,5 %, высокоуглеродистые 0,5- 0,85%С. Низкоуглеродистые стали: 05, 08, 08кп, 10, 10кп.
Они обладают невысокой прочностью и высокой пластичностью, поэтому используются в основном для холодной штамповки, особенно для вытяжки. Штампуемость стали тем хуже, чем больше в ней углерода. Кремний, повышая предел текучести, снижает штампуемость, особенно способность принимать вытяжку.
Стали 15, 20, 25 применяют без термической обработки или в нормализованном виде. Стали поступают в виде проката, труб, листов, ленты и проволоки. Эти стали хорошо сваривается, часто используются для цементуемых деталей, работающих на износ и не испытывающих больших нагрузок. Предназначаются для менее ответственных деталей.
Среднеуглеродистые стали: 30, 35, 40,45, 50. Эти стали применяют после нормализации, улучшения и поверхностной закалкидля самых разнообразных деталей во всех отраслях машиностроения. Недостаток - прокаливаемость сталей невелика. Критический диаметр при закалке воде не превышает 10-12мм. Поэтому следует применять для небольших деталей или для более крупных, но не требующих сквозной прокаливаемости.
Высокоуглеродистые стали: 60, 65, 70, 75, 80, 85 – обладают более высокой прочностью, износостойкостью и упругими свойствами; применяются после закалки и отпуска, нормализации и отпуска, поверхностной закалки для деталей, работающих в условиях трения. Из сталей изготавливают пружины, рессоры, шпиндели, прокатные валки и т.д.
Качественные углеродистые стали с повышенным содержанием марганца 0,7-1,0 % (15Г, 25Г, 35Г, 40Г, 45Г, 50Г и др.) применяют для тех же целей, что и аналогичные с нормальным содержанием марганца (0,25-0,7 %). Марганец повышает прокаливаемость, пределы прочности и текучести, но несколько снижает пластичность и вязкость.
По способу производства, (как указывалось выше) сталь разделяют на мартеновскую (основную и кислую), выплавляемую в мартеновских печах, бессемеровскую, томасовскую, получаемую в конверторах, и электросталь, выплавляемую в дуговых или высокочастотных электропечах.
При бессемеровском процессе выплавки в стали остается до 0,07-0,12 % Р (фосфора), то есть то количество, которое имел чугун, и до 0,06 % S.
В мартеновских печах удаляется большая часть фосфора, сталь получается в больших количествах, хорошей плотности и однородности, невысокой стоимости. Сталь, изготовленная в основной мартеновской печи, содержит немного фосфора (0,02-0,04 %) и серы 0,03- 0,05 %.
Но экономичнее технологический процесс выплавки стали в кислородных конверторах. Сталь вполне качественная, пригодна для всех отраслей машиностроения. Примеси серы и фосфора в этой стали ниже, чем в мартеновской.
Наилучшими качествами обладает электросталь. Она чище мартеновской по фосфору, сере (не более 0,02 %), газам, а также по неметаллическим примесям. Электростали применяются для изготовления ответственных деталей.
Разряд.
1. Легированной сталью называют сталь, содержащую помимо углерода и другие легирующие элементы. Сталь может содержать один или несколько легирующих элементов в различных комбинациях и количествах, изменяющих свойства этой стали и условия ее терми-ческой обработки.
К легирующим элементам относятся хром, никель, титан, вольфрам, молибден, ванадий и др. Кроме того легирующими элементами могут быть кремний и марганец, если кремния в стали содержится не менее 0,8 %, а марганца - более 1 %.
В зависимости от вводимых в сталь легирующих элементов они получают названия: содержащие хром называются хромистыми; хром и никель – хромоникелевыми; хром, марга-нец, кремний – хромомарганцевокремнистыми и т.д.
Основной целью легирования стали является увеличение ее прокаливаемости.
Влияние легирующих элементов на свойства стали. Легирующие элементы по- разному влияют на свойства стали. Их вводят в количествах, при которых наиболее полно проявляется положительное действие каждого элемента.
Углерод -наиболее сильно действующий элемент, содержащийся во всех марках стали. С увеличением содержания углерода значительно повышается твердость и понижается плас-тичность. При малом содержании углерода сталь обладает низкой прочностью, высокой пластичностью, свариваемостью и деформацией в холодном состоянии (штампуемостью), при содержании углерода более 0,3% сталь хорошо закаливается.
Хром -сильный карбидообразующий элемент, способствующий уменьшению зерна в стали при нагреве и повышающий твердость, прочность и прокаливаемость. Добавка хрома в количестве 5 % и выше значительно увеличивают коррозионную и кислотную стойкость. При содержании хрома более 12 % сталь становится нержавеющей и жаростойкой.
Никель - находится твердом состоянии с ферритом. Он повышает не только прочность стали, но и ее вязкость и пластичность даже при пониженных температурах. При нагреве противодействует росту зерен и увеличивает прокаливаемость. При содержании 24-26 % никеля сталь становится немагнитной и коррозионостойкой.
Молибден добавляют в количестве 02,-0,5 %. Он повышает прочность, твердость, прокаливаемость и противодействует росту зерен при нагреве стали под ковку и термическую обработку. Молибден способствует увеличению жаростойкости и уменьшению склонности стали к хрупкости после отпуска.
Ванадий препятствует росту зерен аустенита, повышает твердость, пластичность и вязкость и является хорошим раскислителем стали. Ванадиевая сталь мало склонна к перегреву и при термической и химико-термической обработке ее можно нагревать в широком интервале температур.
Вольфрам образует стойкие карбиды, растворяющиеся в аустените лишь при высоких температурах. Инструментальные быстрорежущие стали, содержащие до 18 % вольфрама, после термической обработки обладают высокой твердостью, износ<
|
|
История развития хранилищ для нефти: Первые склады нефти появились в XVII веке. Они представляли собой землянные ямы-амбара глубиной 4…5 м...
Эмиссия газов от очистных сооружений канализации: В последние годы внимание мирового сообщества сосредоточено на экологических проблемах...
Адаптации растений и животных к жизни в горах: Большое значение для жизни организмов в горах имеют степень расчленения, крутизна и экспозиционные различия склонов...
Индивидуальные и групповые автопоилки: для животных. Схемы и конструкции...
© cyberpedia.su 2017-2024 - Не является автором материалов. Исключительное право сохранено за автором текста.
Если вы не хотите, чтобы данный материал был у нас на сайте, перейдите по ссылке: Нарушение авторских прав. Мы поможем в написании вашей работы!