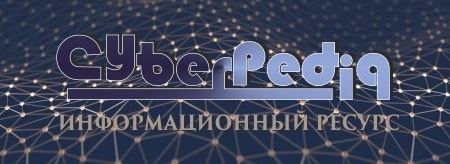
Двойное оплодотворение у цветковых растений: Оплодотворение - это процесс слияния мужской и женской половых клеток с образованием зиготы...
Семя – орган полового размножения и расселения растений: наружи у семян имеется плотный покров – кожура...
Топ:
Техника безопасности при работе на пароконвектомате: К обслуживанию пароконвектомата допускаются лица, прошедшие технический минимум по эксплуатации оборудования...
Установка замедленного коксования: Чем выше температура и ниже давление, тем место разрыва углеродной цепи всё больше смещается к её концу и значительно возрастает...
Отражение на счетах бухгалтерского учета процесса приобретения: Процесс заготовления представляет систему экономических событий, включающих приобретение организацией у поставщиков сырья...
Интересное:
Распространение рака на другие отдаленные от желудка органы: Характерных симптомов рака желудка не существует. Выраженные симптомы появляются, когда опухоль...
Мероприятия для защиты от морозного пучения грунтов: Инженерная защита от морозного (криогенного) пучения грунтов необходима для легких малоэтажных зданий и других сооружений...
Что нужно делать при лейкемии: Прежде всего, необходимо выяснить, не страдаете ли вы каким-либо душевным недугом...
Дисциплины:
![]() |
![]() |
5.00
из
|
Заказать работу |
|
|
Основными операциями в технологии приготовления резиновых смесей являются подготовка ингредиентов, их смешивание и получение полуфабрикатов определенной формы
Производство резиновых смесей с порошкообразным наполнителем. Каучук нарезают на куски и пластифицируют с помощью многократного пропуска через специальные вальцы, подогреваемые до 40—50° С. В результате получают однородную пластическую массу, обладающую способностью хорошо смешиваться с остальными ингредиентами.
Пластифицированный каучук смешивают на вальцах или в смесителях с порошкообразным наполнителем и другими ингредиентами. Первым в каучук вводят про- тивостаритель, последним серу или ускоритель вулканизации. Полученную в результате смешивания массу подвергают каландрированию.
Каландрирование резиновых смесей проводят на специальных машинах (каландрах) для получения сырой резины в виде листов или лент определенной толщины. По конструкции каландры похожи на рабочую трехвал- ковую клеть листопрокатных станов. Верхний и средний валки каландра подогреваются до 60—95° С, а нижний охлаждается до 15° С. Резиновая масса направляется в зазор между верхней парой валков; нагреваясь на них, она обволакивает средний валок и втягивается в зазор между средним и нижним валком. Выходящую с каландра листовую резину накладывают на прокладочную ткань, предупреждающую от слипания, и наматывают на деревянные барабаны. В таком виде сырая каланд- рованная резина может сохраняться при температуре 5—20° С до трех месяцев. Каландрованная резина в дальнейшем подвергается формованию.
Производство резиновых материалов с тканевым наполнителем. Для получения прорезиненных тканей в зависимости от назначения применяют легкие или утяжеленные хлопчатобумажные или льняные ткани и шелк.
|
Прорезинивание проводят методами пропитывания и промазывания тканей резиновыми смесями без наполнителя или с порошкообразным наполнителем. Пропитку осуществляют на клеепропиточных машинах резиновым клеем или раствором резиновой смеси в органическом растворителе (бензине, дихлорэтане и др.). Пропитанная ткань проходит сушку в камерах, а затем подвергается вулканизации.
Ткань промазывают на промазочных каландрах. При этом пластифицированная резиновая масса провальцо- вывается на каландре и втирается в непрерывно движущуюся ткань. Толщина резиновой пленки на ткани регулируется зазором между валками каландра. Полученную ткань отправляют на вулканизацию.
Производство эбонитовых смесей. Эбонит получают смешением каучука со значительным количеством серы (до 40—-50% от массы каучука) с последующим нагревом. Смешение проводят на вальцах или в смесителях. В качестве наполнителя применяют эбонитовую пыль — размельченные отходы производства. Полученную эбонитовую смесь перерабатывают в листовой или профильный материал, формуют и подвергают вулканизации.
Эбонит обладает высокой химической стойкостью, хорошими диэлектрическими свойствами, легко обрабатывается, но имеет низкую температуростойкость. Его применяют для производства корпусов и пластин аккумуляторов, деталей слаботочной аппаратуры, в химическом машиностроении и т. д.
ТЕХНОЛОГИЧЕСКИЕ МЕТОДЫ ФОРМООБРАЗОВАНИЯ ДЕТАЛЕЙ ИЗ РЕЗИНЫ
Формообразование резиновых технических изделий проводят различными методами: шприцеванием, горячим и холодным прессованием, литьем под давлением и т. д. Каждый метод имеет свои технологические возможности и его применяют для получения определенного типа изделий.
Производство изделий из листовой резины. Сырая листовая резина, получаемая с каландров после смешения ингредиентов, и прорезиненная ткань, обработанная на клеепропиточных машинах, становятся конструкционным материалом только после процесса вулканизации.
|
Вулканизация — это процесс обработки отформованной сырой резиновой смеси серой, металлическим натрием или диамииобензолом. Различают горячую и холодную вулканизацию. При горячей вулканизации рези
новую смесь выдерживают при температуре 130—160° С под давлением 1—4 атм. Вулканизаторы, находящиеся в резиновой смеси, взаимодействуют с макромолекулами каучука и образуют межмолекулярные связи. При этом теряется пластичность каучука, изделия приобретают повышенную механическую прочность, упругость и износостойкость. Для вулканизации применяют специальные вулканизационные котлы, автоклавы, прессы. При холодной вулканизации каучук обрабатывают раствором полухлористой серы. В результате изделия становятся прочными и эластичными.
Готовая листовая резина и прорезиненная ткань поступают на раскрой или штамповку. Для раскроя применяют дисковые, клинковые и циркульные ножи, а в массовом производстве — резательные машины роторного типа.
Сложные фасонные заготовки вырубают штанцевы- ми ножами или вырезают по закройным шаблонам. Штанцевый нож представляет собой рамку соответствующей конфигурации, изготовленную из стальной полосы. Высота штанца составляет 40—80 мм, толщина 4—■ 5 мм, нижний край с наружной стороны остро отточен. Вырубку проводят на специальных прессах, подкладывая под резину деревянные или гуттаперчевые прокладки. Вырубку можно проводить и в металлических штампах,
Производство резиновых профилей. Резиновые шнуры, полосы, трубки и другие профили получают шприцеванием —выдавливанием сырой резиновой массы на червячном прессе через специальную матрицу. Червячный винт и рабочий цилиндр пресса обогревают паром, а изделие, выходящее из матрицы, во избежание деформации охлаждают В воде. Профили имеют Рис" иы3'под едавленнем РеЗЯ* сечение, несколько большее, чем t- нижняя "крышкаГ 2- отверстие в матрице, из-за упру- нк~;
ГИХ СВОЙСТВ И дают усадку ПО камеры; 5-напорная каме- пгшнр ра: <>-~ шток; 7-траверса
![]() |
длине, пресса; в —сердечник формы
Отформованные профили подвергают вулканизации.
Прессование. При прессовании сырую резиновую смесь или прорезиненную ткань совместно (если необходимо) с армирующими материалами укладывают в нагретую прессформу, устанавливают на гидравлический пресс и подают давление 20—100 кгс/см2. Процесс горячего прессования сопровождается вулканизацией. При холодном прессовании отформованное изделие подогревают и направляют в вулканизационные котлы.
|
Методом прессования изготавливают клиновидные ремни, уплотнительные кольца, муфты и т. д.
Литье под давлением. Схема литья под давлением резиновых изделий представлена на рис. 443. Разогретая сырая резиновая смесь из напорной камеры 5 выдавливается штоком 6 через литниковые каналы в форму 2.
Количество отливок зависит от количества гнезд и емкости формы.
Так как резиновая смесь подается под давлением при температуре 80—100° С, то одновременно происходит вулканизация.
При литье под давлением сокращается число подготовительных операций (отсутствует каландрирование, резка и т. д.). Этим способом производят изделия сложной формы и крупногабаритные изделия.
Глава 4 ПРОИЗВОДСТВО ДЕТАЛЕЙ ИЗ МЕТАЛЛИЧЕСКИХ ПОРОШКОВ
Производство деталей из металлических порошков относится к отрасли техники, называемой металлокерамикой или порошковой металлургией. Методы порошковой металлургии позволяют получать материалы и детали, обладающие высокой жаропрочностью, износостойкостью, твердостью, заданными стабильными магнитными свойствами. При этом порошковая металлургия позволяет получать большую экономию металла и значительно снижать себестоимость изделий. Например, при изготовлении ряда деталей методами литья с последующей механической обработкой отходы металла составляют до 60—80%, а при получении деталей методами порошковой металлургии отходы металла могут составить 2—5%.
Порошковая металлургия позволяет получать метал- локерамические материалы с особыми физико-химическими, механическими и технологическими свойствами, которые невозможно получить методами литья, обработки давлением.
Технология получения металлокерамических материалов и деталей состоит из ряда последовательных операций: получение металлических порошков, формование, спекание, отделочные операции.
|
МЕТОДЫ ПОЛУЧЕНИЯ МЕТАЛЛИЧЕСКИХ ПОРОШКОВ
Исходные материалы и метод получения порошков оказывают влияние на химический состав, размеры и форму получаемых металлических порошков. Порошки из одного материала, но полученные разными методами, будут иметь резкое различие в технологических, физико-химических и механических свойствах. Поэтому при выборе метода получения металлического порошка следует учитывать не только стоимость производства, но и соответствие порошка условиям его дальнейшей переработки и свойствам получаемого изделия.
Существуют механические и физико-химические методы получения металлических порошков (табл. 25).
При получении порошков механическими методами исходный материал измельчают без изменения химического состава. Получение металлических порошков механическими методами сопряжено с их загрязнением.
При физико-химических методах получения металлических порошков изменяется химический состав сырья или его агрегатное состояние. Получение металлических порошков восстановлением из окислов является наиболее распространенным, высокопроизводительным и экономичным методом.
К основным технологическим свойствам металлических порошков относятся насыпная масса, текучесть и прессуемость.
Насыпная масса является объемной характеристикой и определяется массой единицы объема свободно насыпанного порошка в граммах на сантиметр кубический. Постоянство насыпной массы обеспечивает постоянную усадку при спекании. Насыпная масса одного и того же
МЕТОДЫ ПОЛУЧЕНИЯ МЕТАЛЛИЧЕСКИХ ПОРОШКОВ
Метод |
Характеристика метода |
Материалы |
Примечание |
Форма и размеры частиц, мкм
Размол в шаровых мельницах
Размол в вихревых мельницах
Виброизмельчеиие Грануляция
Восстановление нз окислов
Электролиз
Карбонильный
|
|
Эмиссия газов от очистных сооружений канализации: В последние годы внимание мирового сообщества сосредоточено на экологических проблемах...
Особенности сооружения опор в сложных условиях: Сооружение ВЛ в районах с суровыми климатическими и тяжелыми геологическими условиями...
Наброски и зарисовки растений, плодов, цветов: Освоить конструктивное построение структуры дерева через зарисовки отдельных деревьев, группы деревьев...
Таксономические единицы (категории) растений: Каждая система классификации состоит из определённых соподчиненных друг другу...
© cyberpedia.su 2017-2024 - Не является автором материалов. Исключительное право сохранено за автором текста.
Если вы не хотите, чтобы данный материал был у нас на сайте, перейдите по ссылке: Нарушение авторских прав. Мы поможем в написании вашей работы!