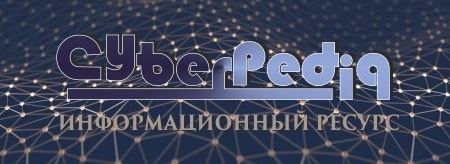
Поперечные профили набережных и береговой полосы: На городских территориях берегоукрепление проектируют с учетом технических и экономических требований, но особое значение придают эстетическим...
Архитектура электронного правительства: Единая архитектура – это методологический подход при создании системы управления государства, который строится...
Топ:
Отражение на счетах бухгалтерского учета процесса приобретения: Процесс заготовления представляет систему экономических событий, включающих приобретение организацией у поставщиков сырья...
История развития методов оптимизации: теорема Куна-Таккера, метод Лагранжа, роль выпуклости в оптимизации...
Организация стока поверхностных вод: Наибольшее количество влаги на земном шаре испаряется с поверхности морей и океанов...
Интересное:
Инженерная защита территорий, зданий и сооружений от опасных геологических процессов: Изучение оползневых явлений, оценка устойчивости склонов и проектирование противооползневых сооружений — актуальнейшие задачи, стоящие перед отечественными...
Лечение прогрессирующих форм рака: Одним из наиболее важных достижений экспериментальной химиотерапии опухолей, начатой в 60-х и реализованной в 70-х годах, является...
Уполаживание и террасирование склонов: Если глубина оврага более 5 м необходимо устройство берм. Варианты использования оврагов для градостроительных целей...
Дисциплины:
![]() |
![]() |
5.00
из
|
Заказать работу |
|
|
Расчет на прочность деталей и узлов двигателя.
Выбор размеров и расчет на прочность деталей поршневой группы.
Поршневая группа состоит из следующих основных деталей:
- поршня составного;
- поршневых колец, компрессионных и маслосъемных;
- поршневого пальца, плавающего.
Конструкция поршневой группы должна разрабатываться с учетом следующих требований:
- обеспечение надежного уплотнения полости цилиндра;
- эффективный отвод тепла от головки поршня;
- достаточно развиты опорные поверхности поршневого пальца для обеспечения умеренных удельных давлений;
- минимально возможная масса при сохранении необходимой прочности и жесткости.
Конструктивные соотношения:
Основные размеры поршня: | |
Общая длина поршня, м | 0,351 |
Средний радиус пластины, м | 0,119 |
Длина тронка, м | 0,2904 |
Толщина донышка, м | 0,0216 |
Толщина стенки, м | 0,06 |
Толщина (высота) кольца, м | 0,00675 |
Ширина кольца, м | 0,00945 |
Число компрессионных колец | |
Расстояние между бобышками, м | 0,1485 |
Длина поршневого пальца, м | 0,259 |
Диаметр поршневого пальца, м
Минимальное сечение поршня м2
Проверка на сжатие по минимальному сечению:
![]() ![]() ![]() ![]() ![]() ![]() ![]() ![]() | 0,108 1,61 |
Нагрузки на элементы поршня: | |
Проверка на сжатие по минимальному сечению, МПа | |
Напряжения по контуру в радиальном направлении, МПа | 115,4 |
Напряжения по контуру в тангенциальном направлении, МПа Напряжение в центре днища, МПа | 111,1 |
Напряжения изгиба посередине пальца, МПа |
Поршень стальной
|
Учитывая нагрузки, действующие на поршень, подбирается материал для его изготовления. В составных поршнях для изготовления головки применяют жаропрочные стали 20ХЗМВФ по ГОСТ 5632-72. Материал поршневых колец сталь 45 по ГОСТ 1050-88. Материал поршневого пальца - сталь 15 по ГОСТ 1050-88.
Разработка систем двигателя.
Система смазывания
Масляный насос забирает масло из поддона. Поскольку в узлах трения масло нагревается и загрязняется, его необходимо непрерывно охлаждать и очищать. В связи с этим от насоса масло направляется в фильтр грубой очистки, после чего в охладитель масла, а затем уже поступает на смазывание двигателя, после фильтра ФГО часть масла проходит через фильтр тонкой очистки и направляется обратно в поддон.
В состав системы смазывания входят также манометры, показывающие давление масла до фильтров и после них, термометры по которым можно судить о степени нагревания масла в двигателе и о работе холодильника. Давление в системе можно регулировать перепускным клапаном масляного насоса.
Для прокачивания системы двигателя перед пуском предназначен ручной насос с невозвратным клапаном.
Основные размеры и расчёт системы смазывания двигателя.
Составляющая теплового баланса в масло, %:
,
где - удельный эффективный расход топлива,
;
- ход поршня,
;
- среднее эффективное давление,
;
- температура наддувочного воздуха после охладителя, 0С;
- частота вращения двигателя,
.
Тепловой поток, отводимый от двигателя маслом:
Тепловой поток, отводимый маслом, :
,
где - расход топлива на номинальном режиме,
.
Массовый расход масла через систему, :
где
- теплоемкость масла
– температура масла на выходе из двигателя;
– температура масла на входе в двигатель.
|
Объёмный расход масла, м3/с:
,
где - плотность масла, принимается равной 910
.
По параметрам «подача – давление» производится выбор типа масляного насоса и определяются его конструктивные параметры.
Давление масла на выходе из насоса принимается равным 300 кПа. Тип масляного насоса – шестерённый.
Мощность масляного насоса:
где h - КПД насоса, h=0,7
Выбирается сетчатый фильтр.
Необходимая поверхность фильтра:
где – живое сечение фильтрующих элементов, где Vм=94,286 л/мин – расчётная маслопроизводительность масляного насоса;
wм=1,5 см/ ч – допускаемая средняя скорость масла.
кж=30,8% - коэффициент живого сечения
Размер ячейки – 0,125 мм; диметр проволоки – 0,10 мм; число ячеек на одну линию – 44,5
Средний температурный напор
где - эффективность нагревания, определяемая выражением
;
- отношение водяных эквивалентов, определяемое выражением
.
Qом – тепловой поток отводимый в ОМ забортной водой
к- коэффициент теплопередачи, к=300 Вт/(м2К)
Объем масла в циркуляционной системе:
Система смазывания
Масляный насос не подает масло при пуске
Неисправен невозвратный клапан НЕТ
на всасывающем трубопроводе.
ДА
Заполнить масляный насос и его
всасывающий трубопровод маслом
непосредственно перед пуском
с помощью резервного насоса.
НЕТ
Недостаточно масла в картере
ДА
Проверить уровень масла в картере
и при необходимости добавить масло
Увеличены зазоры у рабочих шестерен масляного НЕТ
насоса из-за плохой сборки или износа
ДА
1 2
ДА
Снять крышку масляного насоса и проверить торцевые и
радиальные зазоры между шестернями и корпусом
насоса. В случае износа шестерен заменить их. НЕТ
НЕТ
Подсасывание воздуха через неплотности
во всасывающем трубопроводе.
ДА
Опрессовать и уплотнить всасывающий трубопровод.
Перед повторным пуском залить масло в масляный
насос и всасывающую магистраль.
Ищите другую неисправность.
Капитальный ремонт
Выполняется, как правило, в специализированных заводах, где производится полная разборка дизеля с последующей дефектацией всех деталей. По результатам дефектации всех деталей. По результатам дефектации часть деталей подвергается восстановлению, а другую часть - отправляют в металлолом, с последующей заменой их новыми. После чего дизель собирают из новых и восстановленных деталей и узлов, регулируют и испытывают на стенде.
|
Расчет на прочность деталей и узлов двигателя.
|
|
Общие условия выбора системы дренажа: Система дренажа выбирается в зависимости от характера защищаемого...
Архитектура электронного правительства: Единая архитектура – это методологический подход при создании системы управления государства, который строится...
Эмиссия газов от очистных сооружений канализации: В последние годы внимание мирового сообщества сосредоточено на экологических проблемах...
Археология об основании Рима: Новые раскопки проясняют и такой острый дискуссионный вопрос, как дата самого возникновения Рима...
© cyberpedia.su 2017-2024 - Не является автором материалов. Исключительное право сохранено за автором текста.
Если вы не хотите, чтобы данный материал был у нас на сайте, перейдите по ссылке: Нарушение авторских прав. Мы поможем в написании вашей работы!