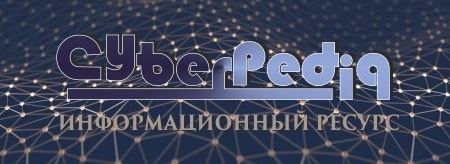
Двойное оплодотворение у цветковых растений: Оплодотворение - это процесс слияния мужской и женской половых клеток с образованием зиготы...
Особенности сооружения опор в сложных условиях: Сооружение ВЛ в районах с суровыми климатическими и тяжелыми геологическими условиями...
Топ:
Техника безопасности при работе на пароконвектомате: К обслуживанию пароконвектомата допускаются лица, прошедшие технический минимум по эксплуатации оборудования...
Оценка эффективности инструментов коммуникационной политики: Внешние коммуникации - обмен информацией между организацией и её внешней средой...
Интересное:
Берегоукрепление оползневых склонов: На прибрежных склонах основной причиной развития оползневых процессов является подмыв водами рек естественных склонов...
Мероприятия для защиты от морозного пучения грунтов: Инженерная защита от морозного (криогенного) пучения грунтов необходима для легких малоэтажных зданий и других сооружений...
Искусственное повышение поверхности территории: Варианты искусственного повышения поверхности территории необходимо выбирать на основе анализа следующих характеристик защищаемой территории...
Дисциплины:
![]() |
![]() |
5.00
из
|
Заказать работу |
|
|
Виды испарителей
Испаритель является одним из элементов холодильной машины, в котором рабочее вещество кипит за счет теплоты, подводимой от источника низкой температуры. Образовавшийся при кипении холодильного агента пар отсасывается из испарителя компрессором для совершения дальнейших процессов цикла холодильной машины. В зависимости от положенного в основу принципа испарители делятся на ряд групп по характеру охлаждаемого источника:
в зависимости от условий циркуляции охлаждаемой жидкости:
по характеру заполнения рабочим веществом:
Испарители могут подразделяться и на другие группы (в зависимости от того, на какой поверхности происходит кипение рабочего вещества; по характеру движения рабочего вещества и др.). В качестве промежуточного жидкого теплоносителя в испарителях применяются рассолы (водные растворы солей NaCl, СаС12), вода, спирт, водный раствор этиленгликоля и др.
С возрастанием концентрации рассола температура начала затвердевания (кристаллизации) сначала падает, затем становится равной температуре криогидратной точки и далее повышается. Заканчивается процесс кристаллизации вне зависимости от концентрации при криогидратной температуре. По мере выпадения кристаллов льда или соли, с понижением температуры рассола оставшаяся жидкая фаза будет либо увеличивать свою концентрацию (левая кривая), либо уменьшать (правая кривая) до состояния эвтектического раствора, соответствующего концентрации криогидратной точки. Для раствора NaCl криогидратная температура равна —21,2°С, а концентрация 28,9%; для раствора СаС12 — соответственно —55°С и 42,5%
|
Методика регулирования ТРВ
При выборе ТРВ необходимо также предусматривать соответствие его пропускной способности производительности прибора охлаждения (испарителя), так как только в этом случае можно обеспечить абсолютно устойчивую работу регулируемой холодильной установки. С этой целью следует предусматривать минимальный перегрев во всем диапазоне возможной производительности прибора охлаждения. Как можно видеть из рис. 1, регулирование может быть устойчивым, только если точка пересечения кривых рабочей характеристики прибора охлаждения и рабочей характеристики ТРВ соответствует рабочей точке холодопроизводительности установки.
Рис. 1. Кривые рабочих характеристик регулятора и испарителя для случая регулирования подачи хладагента в испаритель с помощью ТРВ.
Как только достигается статический перегрев Δt3, ТРВ начинает открываться и при полном открытии обеспечивает свою номинальную производительность. При этом перегрев повышается на величину перегрева открытого ТРВ Δtпо. Сумма статического перегрева Δt3, и перегрева открытого ТРВ Δtпо составляет рабочий перегрев Δtпн. Изготовители ТРВ устанавливают величину статического перегрева, как правило, в диапазоне от 3 до 5 К. Ее можно изменить в ту или иную сторону, вращая регулировочный винт и поджимая или отпуская при этом пружину. Данная операция приводит к эквидистантному сдвигу рабочей характеристики ТРВ влево или вправо, в результате чего появляется возможность обеспечить устойчивое регулирование установки, расположив рабочую характеристику ТРВ таким образом, чтобы она пересекла характеристику прибора охлаждения точно в рабочей точке номинальной холодопроизводительности. Дляприборов охлаждения, работающих при очень малых разностях температур, необходимо предусматривать теплообменник, который, переохлаждая жидкий хладагент, позволяет повысить перегрев.
|
Выполненная при отправке с завода изготовителя настройка ТРВ соответствует большинству установок. Если возникает необходимость дополнительной регулировки, то нужно использовать регулировочный винт (см. рис. 2). При вращении винта вправо (по часовой стрелке) перегрев повышается, при вращении влево (против часовой стрелки) перегрев понижается.
Для ТРВ марки Т2/ТУ2 полный оборот винта меняет температуру перегрева примерно на 4 ° при температуре кипения 0°С.
Начиная с ТРВ марки ТЕ5, полный оборот винта дает температуру перегрева около 0,5 К при температуре кипения 0°С.
Начиная с ТРВ марки ТКЕ3, полный оборот винта дает изменение перегрева примерно на 3 ° при температуре кипения 0°С.
Рис. 2. Настройка ТРВ с помощью регулировочного винта. Рекомендуется следующий метод регулировки. Дополнительно на выходе трубопровода из прибора охлаждения помимо манометра (5) устанавливается электронный термометр (3), датчик (6) которого крепится к термобаллону (4) ТРВ, как показано на рис. 3.
Рис. 3. Схема метода регулировки ТРВ:
1 — терморегулирующий вентиль с внутренним выравниванием; 2 — прибор охлаждения;
3 — электронный термометр; 4 — термобаллон; 5 — манометр;
6 — первичный датчик электронного термометра. Для обеспечения стабильности настройки ТРВ во времени необходимо производить ее при температуре в охлаждаемом объеме, близкой к температуре, при которой отключается компрессор. Не допускается производить настройку ТРВ (регулировку) при высокой температуре в охлаждаемом объеме.
Рекомендуемая регулировка заключается в том, чтобы настроить ТРВ на предельный режим, при котором начинаются пульсации. Для обеспечения этого при постоянной величине перегрева Δtпер = tв.п -t0, необходимо медленно открывать ТРВ до тех пор, пока не начнутся пульсации. При этом значение показаний манометра Рв.п и термометра tв.п не должны изменятся. При последующем открытии вентиля ТРВ могут начаться пульсации показаний манометра Рв.п и термометра tв.п. С этого момента нужно начать закрывать ТРВ до тех пор, пока пульсации не прекратятся (примерно на половину оборота регулирующего винта).
|
Рис. 4. Последовательность регулировки ТРВ
на номинальный режим. Чтобы избежать переполнения испарителя жидкостью, нужно действовать следующим образом. Вращая регулировочный винт вправо (по часовой стрелке), повышать перегрев до прекращения колебаний давления. Затем понемногу вращать винт влево до точки начала колебаний, после этого повернуть винт вправо примерно на 1 оборот (для Т2/ ТЕ2 и ТКЕ на ¼ оборота). При такой настройке колебания давления отсутствуют, и испаритель работает в номинальном режиме. Изменения перегрева в диапазоне ±0,5°С не рассматриваются как колебания.
Если в испарителе имеет место чрезмерный перегрев, это может быть следствием его недостаточной подпитки жидкостью. Снизить перегрев можно, вращая регулировочный винт влево (против часовой стрелки), постепенно выходя на точку колебаний давления. После этого повернуть винт вправо на один оборот (для ТРВ типа Т2/ТЕ и ТКЕ на ¼ оборота). При такой настройке колебания давления прекращаются, и испаритель работает в номинальном режиме. Изменения перегрева в диапазоне ±0,5°С не рассматриваются как колебания.
В случае если ТРВ будет отрегулирован на минимальный возможный перегрев, необходимый для нормальной работы данной холодильной установки, заполнение прибора охлаждения жидким хладагентом будет достигнуто номинальным, а пульсации величины перегрева паров хладагента прекратятся. В процессе регулировки ТРВ давление конденсации должно оставаться относительно стабильным и близким по значению (Рк ~ Рк.н) при номинальных условиях работы, так как от них зависит холодопроизводительность ТРВ.
При регулировке возможны следующие осложнения:
1. Не удается регулировкой добиться пульсаций.
Это означает, что при полностью открытом ТРВ, его производительность ниже, чем производительность прибора охлаждения. Это связано со следующими причинами: либо проходное сечение (f) ТРВ мало, либо в установке не хватает хладагента и на вход ТРВ поступает недостаточное количество жидкого хладагента из конденсатора.
|
2. Не удается устранить пульсации после их возникновения.
Это означает, что производительность ТРВ выше, чем пропускная способность прибора охлаждения. Это связано с тем, что либо проходное сечение (f) ТРВ слишком большое, либо прибору охлаждения не хватает жидкого хладагента.
Регулировка ТРВ невозможна, когда перегрев достигает большего значения (это наступает, когда ТРВ практически закрыт, давление испарения небольшое, и полный перепад температур между температурой воздуха на входе в прибор охлаждения tв1 и температурой кипения хладагента t0 большой). Это означает, что в приборе охлаждения образуется меньше паров, чем способен всасывать компрессор, т. е. холодопроизводительность прибора охлаждения недостаточна.
Следовательно, если не удается найти режим настройки, который устраняет пульсации давления, необходимо произвести замену ТРВ, либо осуществить замену седел с отверстиями (патронов), если конструкция ТРВ предусматривает наличие комплекта сменных патронов. В этом случае, чтобы снизить расход, нужно заменить ТРВ или сменить патрон с отверстием. Если перегрев в испарителе слишком большой, пропускная способность ТРВ мала. Тогда, чтобы повысить расход, нужно также поменять патрон. ТРВ компании Danfoss марки ТЕ поставляются с комплектом сменных патронов. ТРВ марки ТКЕ имеют фиксированное отверстие седла.
Дроссельное (или сопловое) отверстие многих ТРВ выполняется в виде сменного вкладыша, что позволяет обеспечить новое значение его производительности простой заменой этого элемента. Терморегулирующий (силовой, управляющий) тракт ТРВ, т. е. комплекс, состоящий из верхней части ТРВ (надмембранная полость, образующая терморегулирующий элемент), капиллярной трубки и термобаллона, также иногда бывает сменным, что позволяет подобрать наилучший вариант заправки термобаллона (паровая, жидкостная или адсорбционная заправка), наиболее подходящий для конкретных условий работы данной установки.
Рис. 5. Замена сменного вкладыша ТРВ и сменных патронов.
Перепад температур
Перепад температур на испарителе рассчитывается следующим образом:
ΔТ=Та1- Та2,
где ΔТа находится в пределах от 2 до 8 К (для трубчато-ребристых испарителей с принудительным обдувом).
Другими словами, при нормальной работе холодильной установки воздух проходящий через испаритель должен охлаждаться не ниже 2 К и не выше 8 К.
Рис. 2 – Схема и температурные параметры охлаждения воздуха на воздухоохладителе:
Та1 и Та2 – температура воздуха на входе и выходе из воздухоохладителя;
Ламелевые теплообменники
|
Посвящаем серию статей проектированию и применению ламелевых (оребренных) теплообменников, используемых в центральных кондиционерах (AHU) и приточных установках. Слишком часто некоторые производители теплообменников приводят некорректные данные, что дает основание проектантам ожидать нереальных результатов. В этой статье раскроем проблемы со стороны воздуха: влияние на производительность профиля ламелей (оребрения) и потери напора. Слегка затронем также и проблему влияния конденсата в случае батареи охлаждения.
Введение
Рассмотрим случай принудительного обдува теплообменной батареи. При этом величина скорости движения воздуха лежит в области от 1 до 5 м/сек. Течение воздуха между ламелями не является ламинарным, даже если в некоторых случаях может так показаться. Ламинарный поток не может быть здесь стабильным, так как за каждой трубкой создается интенсивный вихрь. Даже если ламинарному потоку воздуха удасться этот вихрь обойти, он „наткнется" на следующую трубку (см. рис. 2). Так что будем рассматривать обычный турбулентный поток, для которого чаще всего используют уравнения типа 1/а = C*v^n, где а — коэффициент теплоотдачи воздуха, v — скорость воздуха, C и n соответствующие коэффициенты. Подобное уравнение применяется к потери напора на стороне воздуха delta p = D*v^m. Коэффициент n колеблется согласно данных, приводимых в литературе, от 0,41 до 0,9, коэффициент m колеблется между 1,3 и 2, чаще 1,8 [1].
Наиболее точным методом определения всех коэффициентов считается американский норматив ARI 410 [2]. Он основан на измерении производительности нескольких теплообменников с различным количеством рядов, с разным шагом оребрения. В качестве рабочей жидкости использовалась горячая и холодная вода (как сухое так и мокрое охлаждение). Для одного типа геометрии и профиля теплообменника обычно проводится более 30 лабораторных тестов. Результаты измерений ложатся на прямую линию в логарифмической диаграмме (см. рис. 3). Точность метода ±5% от общей производительности для любой комбинации рядов, контуров, шагов оребрения.
Выводы
Очевидно чудес в технике не бывает. Более высокая производительность оплачивается большей поверхностью либо большими потерями напора.
Сопротивление по воздуху производители обычно указывают ниже, чем реальное. Советуем проявить здоровый пессимизм и при определении квалификации поставщика провести испытания как минимум одного теплообменника. То же самое относится и к проверке производительности теплообменника.
Солидность производителя теплообменников можно также предварительно проверить вопросом о методике расчета, используемом в его расчетной программе. Наибольшая разница между реальным и указанным расчетным значением может быть у охладителей, в случае, когда при расчете во внимание не принимались капли конденсата, образующиеся на поверхности ламели.
Для охладителей, работающих в условиях образования конденсата использование гидрофильного покрытия приводит к снижению потерей напора воздуха и повышает значение его скорости, при которой следует использовать каплеуловитель.
В установках охлаждения воды — чиллеры — производства Компании «Ксирон-Холод» используются только проверенные теплообменники/конденсаторы.
Терморегулирующие вентили
Терморегулирующие вентили (ТРВ) — это наиболее распространенные регуляторы питания испарителей хладагентом. Регулирование уставки перегрева ТРВ существенно влияет на холодопроизводительность оборудования.
Если ТРВ отрегулирован на большой перегрев или его термобаллон неправильно установлен, то это является причиной низкого давления всасывания. Если уставка перегрева ТРВ произведена неправильно, то выполняют следующие операции:
Если ТРВ имеет линию внешнего уравнивания, то манометр, установленный на ней, непосредственно и точно показывает определяемое давление. Для ТРВ с внутренним уравниванием определяют давление по манометру у всасывающего вентиля компрессора. Затем к этому значению прибавляют расчетное снижение давления во всасывающем трубопроводе между термобаллоном ТРВ и всасывающим вентилем компрессора. Сумма давления по манометру и расчетного снижения давления примерно равна давлению в трубопроводе в месте расположения термобаллона.
Агрегат работает с повышенной нагрузкой в том случае, когда его производительность недостаточна или увеличился расход холода. Единственным решением этой проблемы является замена агрегата на другой более производительный. Значительная тепловая нагрузка на испаритель возникает при высокой частоте вращения вентилятора, в результате чего повышается давление всасывания. Можно уменьшить частоту вращения вентилятора, и одновременно изменить разность между температурой потока воздуха, проходящего через испаритель, и температурой кипения хладагента. Рекомендуемая разность температур обычно составляет 11°С при кондиционировании воздуха и 6 — 9°С при охлаждении. Промышленная шоковая заморозка фруктов от компании «Ксирон-холод»
Рама, картер, блок-картер
Основные требования, которым должны удовлетворять конструкции рамы, картера и блок-картера, — прочность и жесткость. Последняя определяет точность и сохранение взаимного расположения осей механизма движения компрессора во время эксплуатации. Рамы, картеры и блок-картеры воспринимают силы, возникающие при работе компрессора, и передают на фундамент реакцию от крутящего момента, неуравновешенные силы и моменты сил инерции движущихся масс, а также вес компрессора.
Рамы крейцкопфных компрессоров находятся под атмосферным давлением. Проемы, люки и отверстия в рамах уплотнены легкими крышками и кожухами. В горизонтальных оппозитных компрессорах применяют преимущественно многоподшипниковые рамы коробчатого сечения, создающие облегченную, и жесткую конструкцию.
Картеры и блок-картеры бескрейцкопфных компрессоров находятся под давлением всасываемых паров холодильного агента. Это давление при работе компрессора не превышает 0,6 МПа для большинства холодильных агентов. Однако во время длительных стоянок машины давление в картере может повыситься до величины, определяемой температурой окружающего воздуха. Поэтому проверку на прочность и плотность блок-картеров и соответствующих корпусных деталей компрессоров, работающих в автоматическом режиме, проводят по тем же нормам, что и корпусных деталей на стороне нагнетания.
Рамы, картеры и блок-картеры обычно изготовляют литыми из чугуна, иногда сварными из стального листа. В малых компрессорах транспортных машин для уменьшения массы применяют алюминиевые сплавы. Литые детали в большинстве случаев для сохранения правильного положения осей и плоскостей приходится подвергать старению (искусственному или естественному), а сварные — отжигу. Эти же основные требования — точное взаимное положение осей и плоскостей — предъявляют и к механической обработке. Кроме того, уплотнительные плоскости (поверхности) картеров и блок-картеров должны обеспечивать возможность сборки с контрдеталями, обеспечивающей герметичность. Допустимые отклонения посадочных размеров рам, картеров и других деталей компрессоров, а также микрогеометрия основных посадочных поверхностей приведены в специальной литературе.
Холодильные агенты — основные определения, краткий исторический обзор, обозначения
Холодильный агент (хладагент) является рабочим телом холодильной машины, изменяющим в различных частях холодильного контура свое агрегатное состояние. При переходе из жидкого состояния в газообразное, который осуществляется в испарителе, хладагент отбирает тепло у окружающей среды в силу эндотермического характера процесса испарения, вырабатывая тем самым холод. Затем отобранное тепло удаляется из холодильной машины в результате последующей конденсации хладагента в конденсаторе и передается другой среде, причем процесс перехода хладагента из газообразного состояния в жидкое носит экзотермический характер.
Чтобы какое-то вещество могло выполнять функции хладагента, необходимо прежде всего, чтобы при атмосферном давлении его температура кипения была как можно ниже, объемы паров, образующихся при испарении, были незначительными, а давление конденсации — не слишком высоким и легко достижимым. Кроме того, хладагент должен быть неагрессивным по отношению к конструкционным материалам и маслам, как можно менее токсичным, невоспламеняемым и взрывобезопасным. Наконец, желательно, чтобы в тех условиях, в которых находятся наиболее распространенные холодильные сети, его удельная энтальпия была значительной. Иными словами, найти вещество, которое одновременно удовлетворяло бы всем этим требованиям, невозможно.
В качестве первого хладагента использовалась вода, поскольку с 1755 г. она служила «для получения фригорий (отрицательных калорий)» в лабораторной установке, которую создал WilliamGullen. Позднее, в 1834 г., американец JacobPerkins изготовил компрессионную машину, работавшую на диэтиловом эфире, а в 1844 г. тоже американец John Gorrie — машину со сжатием и расширением воздуха. Но французы не остались в долгу и в 1859 г. FerdinandCarre соорудил абсорбционную холодильную машину на аммиаке, а четыре года спустя Charles запустил компрессор, работающий на метиловом эфире. До конца XIX в. использовались еще два новых хладагента: углекислый газ (С02) и двуокись серы (S02), кроме того, один из уже названных хладагентов — аммиак — применяется не только в адсорбционных холодильных машинах, но и в компрессионных (Linde).
Эти три последних хладагента, а именно аммиак (R717), углекислый газ (R744) и двуокись серы (R764) оставались наиболее распространенными вплоть до 1930 г. Но после внедрения в 1930 г. в США новой категории хладагентов: хлорфторуглеродов, хорошо известных под аббревиатурой CFC, все ранее упоминавшиеся хладагенты, за исключением аммиака, почти полностью исчезли. Однако начиная с 1980 г. ученые стали подавать тревожные сигналы, привлекая внимание общественности к вредному воздействию CFC на окружающую среду. Поэтому производители начали разработку менее вредных для будущего планеты хладагентов, некоторые из которых уже появились на рынке. Эти хладагенты, заменяющие группу CFC, принадлежат главным образом к двум категориям химических соединений: фторхлорсодержащим углеводородам, или HCFC, и фторуглеводородам, или HFC.
Хотя число широкомасштабно используемых хладагентов было значительно сокращено, тем не менее их номенклатура остается еще достаточно многочисленной. Чтобы облегчить их обозначение, была введена система буквенно-цифровых индексов. Эта система установлена для всех химических соединений, состав которых не всегда в точности совпадает с описанными нами выше категориями CFC, HCFC или HFC. Они обозначаются буквой R с тремя цифрами после нее, т. е. Rcdu, где:
Для определения химической формулы соединения ее состав дополняют хлором таким образом, чтобы полное число одновалентных атомов, т. е. атомов водорода, фтора и хлора вместе взятых было равно 4 для производных метана, 6 для производных этана, 8 для производных пропана и т. д. По данным «Учебник по холодильной технике» Польманн 1998
Сжатие газов — основные понятия
В производственных процессах подвергаются переработке значительные количества газов и их смесей при давлении, отличном от атмосферного; кроме того, газы используются также для вспомогательных целей (для передавливания, перемешивания и распыления различных веществ). Все эти процессы проводят при сжатии или разрежении газов. Сжатие или разрежение газа (изменение объема) сопровождается изменением его давления и температуры.
Адиабатическое, изотермическое и политропическое сжатие и разрежение. Как известно из термодинамики, изменение состояния газа при изменяющихся объеме и давлении может протекать тремя путями: изотермически, адиабатически и политропически. Изменение давления газа при сжатии в значительной степени зависит от того, происходит ли во время сжатия теплообмен между сжимаемым газом и окружающей внешней средой. Практически такой теплообмен неизбежен, а во многих случаях даже и необходим, для чего используют искусственное охлаждение сжимаемого газа.
Теоретически можно представить себе два предельных случая сжатия газов, причем все реальные процессы сжатия газов будут являться промежуточными между ними.
В первом случае вся теплота, выделяющаяся при сжатии газа, полностью отводится наружу, и процесс изменения состояния газа, т. е. изменение его объема и давления, протекает при одной постоянной температуре; такой процесс называется изотермическим. Во втором случае, наоборот, вся теплота, выделяющаяся при сжатии газа, полностью остается внутри газа, повышая его температуру, при этом потери тепла в окружающую среду отсутствуют; такой процесс называется адиабатическим.
В действительности сжатие газов протекает не изотермически и не адиабатически, а в каждом частном случае лишь приближается к одному из этих процессов. Такой реальный процесс сжатия газа, при котором одновременно с изменением объема и давления происходит также изменение температуры и отвод тепла наружу, называется политропическим.
Теплота
Теплота — это энергия, полученная в результате изменения температуры. Теплота передается от более теплого тела к более холодному. Теплота — это температурная составляющая передачи энергии при работе машинных систем. Принимая во внимание, что работа — это передача энергии силой, которая перемещает массу на определенное расстояние, теплота передается от одного тела другому из-за разницы температур. Теплота передает внутреннюю кинетическую энергию от молекул более теплого тела более холодному. Такая передача энергии уменьшает уровень кинетической энергии молекул более теплого тела, что производит соответствующее уменьшение его температуры. Одновременно кинетическая энергия выравнивается и температура более холодного тела увеличивается.
Передачу энергии, которая затрагивает температуру тела, называют теплопередачей. Хотя передача теплоты происходит в основном в ответ на разницу температур, ее также вызывает сила трения — это взаимодействия, которые происходят на молекулярном уровне как движение тел относительно друг друга. Такие взаимодействия изменяют уровень кинетической энергии молекул между двумя поверхностями. В результате растягивания резинки молекулы движутся друг мимо друга, изменяют свою скорость и температуру всего тела. Данное изменение тепловой энергии — конверсионный процесс, где часть проделанной работы по перемещению тела сохраняется в виде энергии. В данном разделе описаны различные виды тепловой энергии и теплопередачи между телами.
Требования
По действующим в Западной Австралии правилам молоко должно быть охлаждено до температуры 4оС или ниже в течение 3,5 часов после начала доения. Однако для получения высококачественного продукта его следует охладить до температуры ниже 4оС как можно быстрее. Кроме того, очень важно хранить молоко при температуре ниже 4оС между операциями доения.
Системы охлаждения
Системы с непосредственным охлаждением (непосредственным испарением хладагента) и системы с теплоаккумуляцией являются основными системами, используемыми на молочных фермах для охлаждения молочных продуктов. Системы с непосредственным охлаждением включают в себя холодильный агрегат, обеспечивающий подачу охлаждающего хладагента, который отбирает тепло у молока, хранящегося в наливном танке.
Системы с теплоаккумуляцией используют холодильный агрегат, охлаждающий холодильную среду, которая хранится в теплоаккумулирующем танке. Холодильная среда используется затем для охлаждения молока с помощью теплообменника перед тем как молоко поступит в наливной танк. Обычно молоко поступает в наливной танк с температурой ниже 4оС.
Рис. 1. Типовое отделение для хранения молока. Показан охлаждаемый танк (молоко-охладитель), насос для перекачки, встроенный фильтр для очистки и пластинчатый охладитель.
Предварительное охлаждение
Предварительное охлаждение с помощью пластинчатого охладителя помогает снизить рост бактерий, и, кроме того, уменьшает нагрузку на холодильную установку. При этом существенно снижаются затраты на охлаждение. Для проверки эффективности предварительного охлаждения:
·измерить температуру на входе воды;
·измерить температуру на выходе молока. В идеальном случае разница между указанными температурами на входе и выходе должна быть 3оС или менее. На практике неэффективность часто обуславливается следующими причинами:
·неадекватность числа пластин для данного потока молока;
·неадекватность скорости потока воды (скорость потока воды должна быть в 2,5 — 3 раза больше максимальной скорости потока молока);
·неправильная установка — изготовители рекомендуют устанавливать однопроходные пластинчатые охладители таким образом, чтобы подача молока осуществлялась снизу. Для предотвращения отложения осадка между пластинами следует фильтровать перед тем, как направлять через пластинчатый охладитель. Пластинчатые охладители должны промываться с установленными фильтрами!
Температура между доениями
Регулирование температуры молока между доениями очень важно для поддержания качества в процессе хранения в танках. Охлаждение должно «включаться» до того, как температура достигнет 4оС.
Обучение
Все новые дояры (ки) или работники фермы должны пройти полный курс обучения правилам эксплуатации системы охлаждения и хранения молока перед тем, как на них будет возложена ответственность за эксплуатацию установки.
Департамент сельского хозяйства — Западная АвстралияFarmnoteNo 36/99 Авторы: J.R.M. (Ian) и Bell S. J. Gallagher
Кипение
Кипение — это процесс интенсивного испарения, который происходит при давлении пара жидкости, равном давлению окружающей среды. Для подъема давления пара до этого уровня необходимо передать жидкости большое количество энергии. Энергия увеличивает температуру жидкости до температуры насыщения. При повышении температуры жидкости увеличивается кинетическая энергия и количество молекул, отделяющихся от жидкости, давление пара у поверхности жидкости также повышается. Молекулы, обладающие высокой энергией у поверхности жидкости, нарушают связи и преодолевают силу притяжения. При подъеме над поверхностью жидкости их масса увеличивается, и давление, действующее на поверхность жидкости, повышает давление пара. Как,только давление пара сравняется с окружающим атмосферным давлением, атмосфера больше не может препятствовать отделению молекул от жидкости, и начинается кипение. Например, чтобы поднять давление пара воды комнатной температуры до атмосферного, температуру жидкости необходимо поднять до 100°С. Такое увеличение температуры поставляет кинетическую энергию, которая отделяет достаточное количество молекул от поверхности жидкости, и их общая масса вызывает давление пара 101,3 кПа. Кипение происходит, когда температура и давление пара жидкости пересекаются с температурой насыщения.
Для процесса кипения необходимо непрерывно поставлять дополнительную энергию для поддержания давления пара. Энергия производит необходимое преобразование потенциальной энергии молекул для изменения фазы скрытой теплоты.
Кипение характеризуется значительным движением и быстрым возникновением пузырей пара во всем объеме жидкости. Пузыри расширяются и поднимаются к поверхности жидкости в результате разницы плотности жидкости и пара. Пузыри разрушаются у поверхности и выпускают пар в окружающую среду. При разрушении пузырей пара у поверхности жидкости в атмосферу попадают крошечные капельки жидкости. Именно данные капли воды делают пар видимым над сосудом.
Конденсация
Конденсация — это процесс с участием скрытой теплоты, в результате которого пар переходит в жидкую фазу. Это происходит всякий раз, когда насыщенный пар подвергается температуре ниже температуры насыщения. Так как насыщенный пар существует в точке кипения жидкости, он находится в самой низкой температуре, которая возможна для сохранения свойств пара. Следовательно, минимальное понижение температуры заставляет пар конденсироваться. Когда насыщенный пар охлаждается, его молекулы попадают под действие сил жидкой молекулярной структуры и возвращаются в жидкое состояние.
Если конденсация происходит в закрытом сосуде, плотность (кг/м3) и давление пара уменьшаются. В результате происходит соответствующее уменьшение температуры насыщения жидкости. Для поддержания процесса конденсации при таких условиях температура жидкости должна непрерывно уменьшаться, чтобы соответствовать уменьшению давления насыщения. И наоборот, если пар непрерывно подается в сосуд для замещения массы пара, который конденсируется и отводится из сосуда, его плотность, давление и температура насыщения будут постоянными. Такой способ конденсации используется в системах машинного охлаждения и продолжается до полного извлечения теплоты из пара.
Испарение
Испарение — это тонкий термодинамический процесс, вызванный медленной передачей теплоты жидкости от окружающей среды. Процесс испарения производит быстрые изменения объема или массы жидкости. Испарение происходит в результате поглощения молекулами жидкости тепловой энергии из окружающей среды вследствие небольшой разницы температур. Данное увеличение энергии соответственно увеличивает кинетическую энергию жидкости. При передаче кинетической энергии в результате столкновений некоторые молекулы около поверхности достигают скоростей, которые намного выше, чем средняя скорость соседних молекул. При приближении некоторых молекул, обладающих высокой энергией, к поверхности жидкости они нарушают связи, преодолевают силу притяжения и переходят в атмосферу как молекулы пара.
Парообразование испарением происходит, если давление пара над жидкостью ниже, чем давление насыщения, которое соответствует температуре жидкости. Другими словами, испарение происходит, когда линии давления и температуры пара жидкости пересекаются на линии температуры насыщения в точке ниже атмосферного давления. Данные условия находятся на линии температуры насыщения ниже горизонтальной линии давления пара, которое соответствует температуре жидкости.
Объем испаряющейся жидкости непрерывно понижается при отделении молекул от поверхности и внедрении в окружающую атмосферу. После отделения некоторые молекулы пара сталкиваются с другими в атмосфере, передавая часть кинетической энергии. Когда сокращение энергии снижает скорость молекул пара ниже уровня отделения от жидкости, они попадают обратно и таким образом восстанавливают часть потерянного объема. Когда количество молекул, отделяющихся от жидкости, равняется количеству падающих обратно, возникает состояние равновесия. Как только возникает такое состояние, объем жидкости останется неизменным, пока изменения давления пара или температуры не произведут соответствующие изменения интенсивности испарен
|
|
Типы оградительных сооружений в морском порту: По расположению оградительных сооружений в плане различают волноломы, обе оконечности...
Историки об Елизавете Петровне: Елизавета попала между двумя встречными культурными течениями, воспитывалась среди новых европейских веяний и преданий...
Биохимия спиртового брожения: Основу технологии получения пива составляет спиртовое брожение, - при котором сахар превращается...
Археология об основании Рима: Новые раскопки проясняют и такой острый дискуссионный вопрос, как дата самого возникновения Рима...
© cyberpedia.su 2017-2024 - Не является автором материалов. Исключительное право сохранено за автором текста.
Если вы не хотите, чтобы данный материал был у нас на сайте, перейдите по ссылке: Нарушение авторских прав. Мы поможем в написании вашей работы!