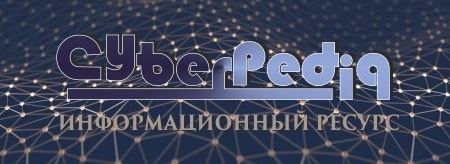
Историки об Елизавете Петровне: Елизавета попала между двумя встречными культурными течениями, воспитывалась среди новых европейских веяний и преданий...
Своеобразие русской архитектуры: Основной материал – дерево – быстрота постройки, но недолговечность и необходимость деления...
Топ:
Установка замедленного коксования: Чем выше температура и ниже давление, тем место разрыва углеродной цепи всё больше смещается к её концу и значительно возрастает...
Методика измерений сопротивления растеканию тока анодного заземления: Анодный заземлитель (анод) – проводник, погруженный в электролитическую среду (грунт, раствор электролита) и подключенный к положительному...
Характеристика АТП и сварочно-жестяницкого участка: Транспорт в настоящее время является одной из важнейших отраслей народного хозяйства...
Интересное:
Как мы говорим и как мы слушаем: общение можно сравнить с огромным зонтиком, под которым скрыто все...
Что нужно делать при лейкемии: Прежде всего, необходимо выяснить, не страдаете ли вы каким-либо душевным недугом...
Аура как энергетическое поле: многослойную ауру человека можно представить себе подобным...
Дисциплины:
![]() |
![]() |
5.00
из
|
Заказать работу |
|
|
Размер Номинал ES EI Допуск Квалитет
А1 19 0,2 -0,2 0,4 -
А2 48 0,1 -0,1 0,2 -
А3 10 0,18 -0,18 0,36 -
А4 2,5 0,2 -0,2 0,4 -
А5 58 0,37 -0,37 0,74 -
Z1 2 3,23 -0,4 3,63 -
Z2 0 0,762 0,5 0,262 -
Z3 0 0,762 0,5 0,262 -
Z4 2 1,284 -0,4 1,684 -
S1 29 0,104 -0,026 0,13 11
S2 26 0,474 0,422 0,052 9
S3 29 0,11 0,026 0,084 10
S4 18 0,474 0,264 0,21 12
S5 19 0,736 0,526 0,21 12
S6 19 0,026 -0,026 0,052 9
S7 19 0,026 -0,026 0,052 9
B1 64 0,914 -0,986 1,9 16
B2 31 1,31 -0,29 1,6 16
Найдена 1-я цепь: А1[4,6] S6[4,6]
Исходное уравнение: А1=S6
Замыкающее звено: А1min = 18,8 А1max = 19,2
Неизвестное звено: S6
Расчетное уравнение: S6 = А1
т.к. искомое звено имеет 9 квалитет, то допуск TS6 = 0,052
Окончательное уточнение с учетом вида расположения поля допуска (js):
S6min = 18,974 S6max = 19,026
Допуск замыкающего звена: TА1 = + 0,052 = 0,052 <= 0,4 (Точность зам. звена обеспечена!)
Найдена 2-я цепь: А2[4,9] S3[6,9] S6[4,6]
Исходное уравнение: + А2min = + S3min + S6min
Замыкающее звено: А2min = 47,9
Неизвестное звено: S3min
Увеличивающее звено: S6min = 18,974
Расчетное уравнение: + S3min = + А2min - S6min
Результат расчета неизвестного: S3min = 29,026
т.к. искомое звено имеет 10 квалитет, то допуск TS3 = 0,084
Окончательный результат с учетом допуска: S3min = 29,026 S3max = 29,11
Допуск замыкающего звена: TА2 = + 0,084 + 0,052 = 0,136 <= 0,2 (Точность зам. звена обеспечена!)
Найдена 3-я цепь: А3[7,9] S3[6,9] S7[6,7]
Исходное уравнение: + А3min = + S3min - S7max
Замыкающее звено: А3min = 9,82
Увеличивающее звено: S3min = 29,026
Неизвестное звено: S7max
Расчетное уравнение: - S7max = - S3min + А3min
Результат расчета неизвестного: S7max = 19,026
т.к. искомое звено имеет 9 квалитет, то допуск TS7 = 0,052
Окончательный результат с учетом допуска: S7min = 18,974 S7max = 19,026
Допуск замыкающего звена: TА3 = + 0,052 + 0,084 = 0,136 <= 0,36 (Точность зам. звена обеспечена!)
Найдена 4-я цепь: А5[2,9] S3[6,9] S1[2,6]
|
Исходное уравнение: + А5min = + S3min + S1min
Замыкающее звено: А5min = 57,63
Увеличивающее звено: S3min = 29,026
Неизвестное звено: S1min
Расчетное уравнение: + S1min = - S3min + А5min
Результат расчета неизвестного: S1min = 28,974
т.к. искомое звено имеет 11 квалитет, то допуск TS1 = 0,13
Окончательный результат с учетом допуска: S1min = 28,974 S1max = 29,104
Допуск замыкающего звена: TА5 = + 0,13 + 0,084 = 0,214 <= 0,74 (Точность зам. звена обеспечена!)
Найдена 5-я цепь: Z2min[4,5] S4[5,6] S6[4,6]
Исходное уравнение: + Z2min = - S4max + S6min
Замыкающее звено: Z2min = 0,5
Неизвестное звено: S4max
Увеличивающее звено: S6min = 18,974
Расчетное уравнение: - S4max = + Z2min - S6min
Результат расчета неизвестного: S4max = 18,474
т.к. искомое звено имеет 12 квалитет, то допуск TS4 = 0,21
Окончательный результат с учетом допуска: S4min = 18,264 S4max = 18,474
Перерасчет припуска: Z2 = - S4 + S6
Найденный припуск: Z2min = 0,5 Z2max = 0,762
Допуск замыкающего звена: TZ2 = + 0,21 + 0,052 = 0,262 <= 0,262 (Точность зам. звена обеспечена!)
Найдена 6-я цепь: Z3min[7,8] S5[6,8] S7[6,7]
Исходное уравнение: + Z3min = + S5min - S7max
Замыкающее звено: Z3min = 0,5
Неизвестное звено: S5min
Уменьшающее звено: S7max = 19,026
Расчетное уравнение: + S5min = + Z3min + S7max
Результат расчета неизвестного: S5min = 19,526
т.к. искомое звено имеет 12 квалитет, то допуск TS5 = 0,21
Окончательный результат с учетом допуска: S5min = 19,526 S5max = 19,736
Перерасчет припуска: Z3 = + S5 - S7
Найденный припуск: Z3min = 0,5 Z3max = 0,762
Допуск замыкающего звена: TZ3 = + 0,21 + 0,052 = 0,262 <= 0,262 (Точность зам. звена обеспечена!)
Найдена 7-я цепь: Z4min[9,10] B2[6,10] S3[6,9]
Исходное уравнение: + Z4min = + B2min - S3max
Замыкающее звено: Z4min = 1,6
Неизвестное звено: B2min
Уменьшающее звено: S3max = 29,11
Расчетное уравнение: + B2min = + Z4min + S3max
Результат расчета неизвестного: B2min = 30,71
т.к. искомое звено имеет 16 квалитет, то допуск TB2 = 1,6
Окончательный результат с учетом допуска: B2min = 30,71 B2max = 32,31
Перерасчет припуска: Z4 = + B2 - S3
Найденный припуск: Z4min = 1,6 Z4max = 3,284
Допуск замыкающего звена: TZ4 = + 1,6 + 0,084 = 1,684 <= 1,684 (Точность зам. звена обеспечена!)
Найдена 8-я цепь: А4[2,3] S2[3,6] S1[2,6]
Исходное уравнение: + А4min = - S2max + S1min
|
Замыкающее звено: А4min = 2,3
Неизвестное звено: S2max
Увеличивающее звено: S1min = 28,974
Расчетное уравнение: - S2max = + А4min - S1min
Результат расчета неизвестного: S2max = 26,474
т.к. искомое звено имеет 9 квалитет, то допуск TS2 = 0,052
Окончательный результат с учетом допуска: S2min = 26,422 S2max = 26,474
Допуск замыкающего звена: TА4 = + 0,052 + 0,13 = 0,182 <= 0,4 (Точность зам. звена обеспечена!)
Найдена 9-я цепь: Z1min[1,2] S1[2,6] B2[6,10] B1[1,10]
Исходное уравнение: + Z1min = - S1max - B2max + B1min
Замыкающее звено: Z1min = 1,6
Уменьшающее звено: S1max = 29,104
Уменьшающее звено: B2max = 32,31
Неизвестное звено: B1min
Расчетное уравнение: + B1min = + S1max + B2max + Z1min
Результат расчета неизвестного: B1min = 63,014
т.к. искомое звено имеет 16 квалитет, то допуск TB1 = 1,9
Окончательный результат с учетом допуска: B1min = 63,014 B1max = 64,914
Перерасчет припуска: Z1 = - S1 - B2 + B1
Найденный припуск: Z1min = 1,6 Z1max = 5,23
Допуск замыкающего звена: TZ1 = + 0,13 + 1,6 + 1,9 = 3,63 <= 3,63 (Точность зам. звена обеспечена!)
В поперечном направлении
Найдено 12 цепей. Точность обеспечена во всех цепях.
Таблица результатов
Размер Номинал ES EI Допуск Квалитет
А1 17,5 0,22 -0,22 0,44 -
А2 2 0,2 -0,2 0,4 -
А3 65 0,37 -0,37 0,74 -
А4 5 0,22 -0,22 0,44 -
А5 25 0,26 -0,26 0,52 -
А6 20 0,26 -0,26 0,52 -
А7 15 0,22 -0,22 0,44 -
А8 1,5 0,2 -0,2 0,4 -
А9 125 0,5 -0,5 1 -
Z1 3 2,94 -1 3,94 -
Z2 0 0,78 0,5 0,28 -
Z3 3 0,384 -1 1,384 -
S1 20 0,042 -0,042 0,084 10
S2 5 0,117 0,042 0,075 11
S3 18 0,458 0,328 0,13 11
S4 4 0,958 0,883 0,075 11
S5 105 0,182 0,042 0,14 10
S6 88 0,182 0,042 0,14 10
S7 87 0,542 0,402 0,14 10
S8 85 0,402 0,262 0,14 10
S9 82 0,402 0,262 0,14 10
S10 40 0,042 -0,058 0,1 10
B1 131 2,024 -0,476 2,5 16
B2 23 0,342 -0,958 1,3 16
Технологические размерные цепи рассчитывают чаще всего методом полной взаимозаменяемости. Замыкающим звеном в технологической размерной цепи является то, которое получается последним как результат выполнения всех остальных.
Некоторые особенности имеет методика расчета размерных цепей, у которых замыкающим звеном является припуск на обработку. Вначале табличным способом или расчетом находят его минимальную величину Z min. Затем определяют значение наименьшего предельного размера увеличивающего звена Sg min или наибольшего предельного размера уменьшающего звена Sl max:
;
где ng, n l - соответственно число увеличивающих и уменьшающих звеньев.
После чего для данного звена устанавливают допуск, назначают предельные отклонения (верхнее EsS и нижнее EiS) и определяют его номинальный размер
|
или
Далее рассчитывают номинальный размер припуска Z и его наибольшее значение Z max:
Находят верхнее EsZ и нижнее EiZ предельные отклонения припуска:
;
.
Правильность расчетов проверяют по уравнениям
;
.
Полученные размеры указываем на операционных эскизах.
11. Определение режимов резания
Сверлить осевое отверстие, выдерживая размер диам. 5+0,3
t, мм | S, мм/об | V, м/мин | n, об/мин | Tо, мин |
2,5 | 0,14 | 0,09 |
Расточить основное отверстие тонко, выдерживая размеры диам. 25+0,033; 18+0,474+0,264
Исходные данные для расчетов:
- материал обрабатываемой заготовки -сталь
- предел прочности обрабатываемого материала - sв =750, МПа.
- материал режущей части инструмента - твердый сплав
- обрабатываемый диаметр, D =25 мм
- длина обработки, L = 38 мм
Выбираем глубину резания в зависимости от стадии обработки поверхности (черновая, предварительная, чистовая), t =0,3 мм [13, стр. 266]
Выбираем рабочую подачу в зависимости от глубины резания и достигаемой шероховатости поверхности, S =0,1 мм/об [13, стр. 267]
Рассчитываем скорость резания по зависимости [13, стр. 265]:
где Сv, m, x, y – коэффициенты, учитывающие вид обработки [13, стр. 269]:
Сv = 420
m = 0.2
x = 0.15
y = 0.2
Т - значение стойкости инструмента, для одноинструментальной обработки Т = 30 … 60 мин, принимаем
Т =45 мин.
kv – коэффициент, учитывающий конкретные условия обработки [13];
kv=0,3681792
Коэффициент kv определяется по зависимости:
kv = kmv*kpv*kiv*kfv*kf1v*kr, где
kmv - коэффициент, учитывающий влияние материала заготовки определяется по зависимости [13, стр. 261]:
kmv = kg*(750/sв)nv, здесь
kpv - коэффициент, учитывающий состояние обрабатываемой поверхности [13, стр. 263]
kpv =0.8
kiv - коэффициент, учитывающий материал инструмента [13, стр. 263]:
kiv =0.85
kfv - коэффициент, учитывающий влияние главного угла в плане [13, стр. 271],
kfv = 0.8
kf1v - коэффициент, учитывающий влияние вспомогательного угла в плане [13, стр. 271],
kf1v = 0.8
kr - коэффициент, учитывающий влияние радиуса при вершине инструмента [13, стр. 271],
kr = 0.94
Частота вращения шпинделя рассчитывается по формуле
|
n = (1000*V)/(3,14*D)
расчетное значение n корректируем в соответствии с рядом частот вращения шпинделя станка, n =1760 об/мин
Фактическая скорость резания V =138 м/мин
Определяем основное время обработки То по зависимости:
То = L/(n*S)
To=0,25 мин
Таблица с режимами для обработки
t, мм | S, мм/об | V, м/мин | n, об/мин | Tо, мин |
0,3 | 0,1 | 0,25 |
Режимы резания на остальные технологические переходы определяем аналогично или выбираем по рекомендациям производителей инструментов и указываем в технологической документации.
12. Расчет суммарной погрешности обработки
Суммарную погрешность будем определять на размер диам. 25+0,033
Расточить основное отверстие тонко, выдерживая размеры диам. 25+0,033; 18+0,474+0,264
t, мм | S, мм/об | V, м/мин | n, об/мин | Tо, мин |
0,3 | 0,1 | 0,25 |
Все погрешности, определяющие точность обработки деталей машин на металлорежущих станках, могут быть разделены на три категории:
1) погрешности установки заготовок – ey;
2) погрешности настройки станка – Dн;
3) погрешности на стадии процесса обработки, которые вызываются:
а) размерным износом режущих инструментов – Dи;
б) упругими деформациями технологической системы под влиянием силы резания – Dу;
в) геометрическими неточностями станка SDст;
г) температурными деформациями технологической системы SDт.
При обработке на станках с ЧПУ дополнительно возникают погрешности позиционирования элементов системы и отработки программ управления.
Расчет точности необходим в основном для операций чистовой обработки, выполняемых с допуском по 6-му – 11-му квалитетам.
Суммарные погрешности обработки деталей на настроенных станках определяют по уравнениям:
– для диаметральных размеров
;
Расчет погрешности диаметральных размеров при однорезцовом точении может быть выполнен по методике, изложенной в [12].
После определения суммарной погрешности DS проверяется возможность обработки без брака:
где – допуск на операционный размер.
В случае несоблюдения этого условия необходимо предложить конкретные мероприятия по снижению DS.
1. Определим величину погрешности Dи (на радиус), вызванную размерным износом резца:
где: L - длина пути резания при обработке партии N деталей, определяемая как:
L = p*D*l/So = (3,14*25*38/0,1)*21 = 626430 мм (627 м)
Дополнительный путь резания L0=500 м соответствует начальному износу вершины резца в период приработки.
Для сплава Т30К4 относительный износ и 0=5 мкм/км.
(627+500)/1000*5 = 5,64 мкм;
2. Определим колебание отжатий системы Dу вследствие изменения силы Py из-за непостоянных глубины резания и податливости системы при обработке.
Dy=Wmax×(Py max – Py min)
где Wmax - наибольшая податливость системы, мкм/кН;
|
Pymax, Pymin наибольшее и наименьшее значения составляющей силы резания, совпадающей с направлением выдерживаемого размера, кН.
Для станка DMC 55 H duoBLOCK повышенной точности наибольшее допустимое перемещение продольного суппорта под нагрузкой 22 кН составляет соответственно 350 мкм. При установке расточной оправки консольно в шпинделе минимальную податливость системы не определяют из-за малого свеса заготовки, поэтому максимальная податливость будет возможна при положении резца в конце обработки, т.е. у передней бабки станка. Исходя из этого, можно принять Wmax=350/22=15,91 мкм/кН.
Имея в виду, что W=y/Py, после соответствующих преобразований получим. При установке оправки консольно величина наибольшей податливости инструмента:
= (32/20)*((120/20)*(120/20)*(120/20)) = 345,6 мкм.
Тогда максимальная податливость технологической системы:
Wmax =345,6+15,91=361,51 мкм/кН.
Наибольшее Pymax и наименьшее Pymin нормальные составляющие усилия резания определяются согласно формуле:
Py =10×Cp×tx×sy×vn×Kp,
где: постоянная Cp =243, показатели степеней x=0,9 y=0,6 n= -0,3; поправочный коэффициент Kp =Kмp×Kjp×Kgp×Klp×Krp =1.
На предшествующей операции (чистовом растачивании) заготовка обработана с допуском по IT10, т.е. возможно колебание припуска на величину 1/2×(IT9+IT7), что для диаметра 25 мм составит (0,08+0,033)/2 = 0,059 мм, а колебание глубины резания составит:
tmin= Zmin=0,3 мм;
tmax=Zmin+0,059=0,3+0,059=0,359 мм;
Py max= 2,43×0,3590,9×0,10,6×138-0,3×1= 0,069 кН;
Py min= 2,43×0,30,9×0,10,6×138-0,3×1= 0,062 кН.
Колебание обрабатываемого размера вследствие упругих деформаций:
Dy=Wmax×(Py max-Py min)= 361,51*(0,069-0,062) = 2,531 мкм
3. Определим погрешность, вызванную геометрическими неточностями станка SDст.
где С - допустимое отклонение от параллельности оси шпинделя направляющим станины в плоскости выдерживаемого размера на длине L;
l - длина обрабатываемой поверхности.
Для многоцелевых станков повышенной точности при наибольшем диаметре обрабатываемой поверхности до 100 мм С = 6 мкм на длине L = 150 мм.
При длине обработки l =38 мм:
= (6/150)*38 = 1,52 мкм.
4. В предположении, что настройка резца на выполняемый размер производится с учетом дискретного перемещения инструмента шаговым двигателем, то примем метод регулирования положения вершины резца с контролем положения резца с помощью стрелочного индикатора с ценой деления 0,01 мм, определим погрешность настройки в соответствии с формулой:
,
где Dр - погрешность регулирования положения резца;
Dизм - погрешность измерения размера детали;
кр=1,73 и ки=1,0 - коэффициенты, учитывающие отклонения величин Dр и Dизм от нормального закона распределения.
Для заданных условий обработки:
Dр=5 мкм и Dизм=9 мкм при измерении IT8 мм. Тогда погрешность настройки
Dн = 8,4 мкм.
5. Определим температурные деформации технологической системы, приняв их равными 15 % от суммы остальных погрешностей:
= 0,15*(5,64+2,531+1,52+8,4) = 3,075 мкм
6. Определим суммарную погрешность обработки:
= 28,39 мкм.
DS не превышает заданную величину допуска (Td=33 мкм), поэтому возможна обработка без брака.
13. Расчет технических норм времени и трудоемкости обработки детали
Определим нормы времени на Многоцелевую операцию 005.
В серийном производстве определяется норма штучно-калькуляционного времени:
Где
· Тп.з.- подготовительно-заключительное время, мин;
· n- количество деталей в партии запуска (в нашем случае 21, см расчет выше), шт;
· Тшт.- норма штучного времени, мин.
Тшт.=То+Тус+Тзо+Туп+ Тизм+Тоб.ст
где:
То- основное время, мин;
Т ус - время на установку/снятие детали, мин;
Туп- время на приемы управления, мин;
Т зо –время на закрепление и открепление детали;
Т об.ст – общее время на обслуживание рабочего места и отдыха
Тоб.ст.=Топ*(nоб.ст./100%),где Топ – оперативное время.
Топ. = То +Тв
nоб.ст. –затраты времени на обслуживание рабочего места, %;
Время работы станка по программе управления (время цикла обработки) tп.у. равно неполному оперативному времени работы станка: tп.у.=tо+tм.в.=tоп.н.
Элементы штучного времени определяются так же, как и для случаев обработки на станке с ручным управлением.
Определяем основное время по переходам:
Основное время на всю операцию:
åТо = 0,48+0,18+0,65+0,62+0,66+0,48+0,14+1,38+0,05+0,14+0,19+0,25+0,62+0,88+0,14+0,3+0,09+0,1+0,07+0,37+0,09+0,07+0,27+0,09+0,1+0,08+0,03+2,19+1,54+0,57+0,45+0,12+0,09+0,1+0,08+0,1+0,55+0,31+0,44+0,78+0,42+0,22 = 16,48 мин
Определяем вспомогательное время:
Так как способы установки и закрепления заготовок при обработке на станках с ЧПУ принципиально не отличаются от способов, применяемых на станках с ручным управлением, то tв.у. определяют по имеющимся нормативам для станков с ручным управлением (для приспособления открытого типа с винтовыми зажимными механизмами):
tв.у.=1,45 мин [13, с.54]
Машинное вспомогательное время tм.в. включает комплекс приемов, связанных с позиционированием (для операции 005 обработка ведется за 5 позиций - время поворота стола станка 0,2 мин), ускоренным перемещением рабочих органов станка, подводом инструмента вдоль оси в зону обработки и последующим отводом, автоматической сменой режущего инструмента из инструментального магазина (в операции 005 используется 42 инструмента - время смены инструмента 0,4 мин):
Тв = 1,45+(5*0,2)+(42*0,4) = 19,25 мин
Определяем время обслуживания рабочего места и время на личные надобности:
В состав по организационному обслуживанию рабочего места включены: осмотр, нагрев системы ЧПУ и гидросистемы, опробование оборудования, получение инструмента от мастера в течение смены, смазывание и очистка станка в течение смены, предъявление контролеру ОТК пробной детали, уборка станка и рабочего места по окончанию работы.
К техническому обслуживанию рабочего места относятся: смена затупившегося инструмента, коррекция инструмента на заданные размеры, регулирование и подналадка станка в течение смены, удаление стружки из зоны резания в процессе работы.
На обслуживание рабочего места и личные надобности отводится 12% от оперативного времени tоп.
tоп=tо+tв.у.+tм.в.
Штучно-калькуляционное время определяется:
Тшт.к.=Тшт+Тп.з./n мин
Тп.з.- подготовительно-заключительное время на партию, мин;
n- размер партии деталей, запускаемых в производство, шт;
Подготовительно-заключительное время Тп.з. при обработке на станках с ЧПУ состоит из затрат времени (приемов) Тп.з.1, из затрат Тп.з.2, учитывающих дополнительные работы, и времени Тп.з.3 на пробную обработку детали.
Тп.з.=Тп.з.1+Тп.з.2+Тп.з.3 [13, с.604]
В соответствии с руководящим материалом Оргстанкинпрома принята единая норма Тп.з1=15 мин для всех станков с ЧПУ.
Тп.з.2=22 мин [13, табл.12 с.607]
Тп.з.3=8 мин [13, табл.15 с.617]
Тп.з.=15+22+8=45 мин
Тшт.к = (16,48+19,25)*1,12+45/21 = 42,16 мин
Нормы времени на другие операции определяем аналогично и заносим в соответствующие графы операционных карт технологической документации.
Определение типа производства и размера партии деталей
Определение типа производства несет в себе знаковую информацию для последующего выбора оптимальных параметров и характеристик проектируемого технологического процесса. Тип производства определяем по методике изложенной в источниках [4, 6, 12, 13],Первоначально тип производства определяем для базового технологического процесса (ТП), а затем, после проведения нормирования проектируемого ТП определим для него тип производства с целью расчета экономических параметров- технологической себестоимости, приведенных затрат, экономического эффекта.
Тип производства по ГОСТ 3.1108-74 характеризуется коэффициентом закрепления операции Кз.о., который показывает отношение суммы числа деталей операции, условно закрепленных за оборудованием, к числу принятых единиц оборудования.
Кз.о.=
где Оi-число деталей операций, условно закрепленных за оборудованием на i-й операции рассматриваемого ТП; Цi-принятое число единиц оборудования на i-й операции; m-число операций в рассматриваемом ТП.
Оi=
где -нормативный коэффициент загрузки оборудования;
- фактический коэффициент загрузки оборудования на i-й операции.
=
где Срi-расчетное число единиц оборудования на i-й операции; Сi-принятое число единиц оборудования на i-й операции (получается из соответствующего значения Срi путем округления последнего до ближайшего большего целого; в меньшую сторону допускается округлять, если 1,08).
Срi=Тшт.к.N 60·Fд·Kв.н.·
з.н.,
где Тшт.к.-норма штучно-калькуляционного времени на выполнение i-й операции,мин.; N-годовая программа выпуска данного изделия, шт.; Fд- годовой действительный фонд времени работы оборудования, ч.
При Кз.о. 1- производство массовое; если 1< Кз.о.
10- крупносерийное; 10< Кз.о.
20- среднесерийное; 20< Кз.о.
40- мелкосерийное. В единичном производстве Кз.о. не регламентируется.
Результаты всех промежуточных расчетов запишем в таблице.
Исходные данные:
Годовая программа: программа выпуска изделий 350 шт в год
N= 350 шт.;
Количество деталей на изделие m = 1;
По справочным данным [6, стр.22] при двухсменном режиме работы годовой действительный фонд времени работы оборудования Fд=4015 ч. В предположении, что тип производства массовый, примем нормативный коэффициент загрузки оборудования з.н.=0,75 [6, стр.20], коэффициент выполнения норм Кв.н.=1,3 [13].
№ п/п | Наименование операции | Т шт.к, | С р, | С пр, | К з.ф. | О, | |||
ч | шт | шт | шт | ||||||
1. | Фрезерно-отрезной (8Г662) | 0,1 | 0,01 | 0,0752 | 10,6382222 | ||||
2. | Разметочная (Плита) | 0,083 | 0,0083 | 0,17447 | 4,58544061 | ||||
3. | Горизонтально- расточная (Селере) | 0,128 | 0,0128 | 0,06016 | 13,2977778 | ||||
4. | Токарно-винторезная (1М63) | 0,1 | 0,01 | 0,09024 | 8,86518519 | ||||
5. | Токарно-винторезная (1М63) | 2,0 | 0,20153743 | 0,20154 | 3,9694859 | ||||
6. | Токарно-винторезная (1М63) | 0,3 | 0,17446524 | 0,17447 | 4,58544061 | ||||
7. | Разметочная (Плита) | 0,12 | 0,07520053 | 0,0752 | 10,6382222 | ||||
8. | Вертикально-фрезерная (6Р13) | 0,36 | 0,1263369 | 0,12634 | 6,33227513 | ||||
9. | Слесарная | 0,053 | 0,1263369 | 0,12634 | 6,33227513 | ||||
10. | Радиально-сверлильная (2М55) | 0,17 | |||||||
11. | Круглошлифовальная (3М174) | 0,283 | |||||||
12. | Круглошлифовальная (3М174) | 0,17 | |||||||
13. | Круглошлифовальная (3М174) | 0,2 | |||||||
14. | Токарно-винторезная (1М63) | 0,2 | |||||||
15. | Слесарная | 0,053 | |||||||
Сумма | 4,32 | 69,2443248 | |||||||
Кзо= | 17,31 | ||||||||
№ п/п | Наименование операции | Т шт.к, | С р, | С пр, | К з.ф. | О, | |||
ч | шт | шт | шт | ||||||
16. | Разметочная (Плита) | 0,25 | 0,07520053 | 0,0752 | 10,6382222 | ||||
17. | Токарно-винторезная (1К62) | 0,58 | 0,17446524 | 0,17447 | 4,58544061 | ||||
18. | Токарно-винторезная (1К62) | 0,2 | 0,06016043 | 0,06016 | 13,2977778 | ||||
19. | Токарно-винторезная (1К62) | 0,3 | 0,09024064 | 0,09024 | 8,86518519 | ||||
20. | Токарно-винторезная (1К62) | 0,67 | 0,20153743 | 0,20154 | 3,9694859 | ||||
21. | Токарно-винторезная (1К62) | 0,58 | 0,17446524 | 0,17447 | 4,58544061 | ||||
22. | Вертикально-фрезерная (6М13П) | 0,25 | 0,07520053 | 0,0752 | 10,6382222 | ||||
23. | Вертикально-фрезерная (6М13П) | 0,42 | 0,1263369 | 0,12634 | 6,33227513 | ||||
24. | Слесарная | 0,42 | 0,1263369 | 0,12634 | 6,33227513 | ||||
Сумма | 3,67 | 69,2443248 | |||||||
Кзо= | 17,31 | ||||||||
hЗ.Ф = mр/Р – фактический коэффициент загрузки оборудования;
где mр – расчётное количество станков;
Р – принятое количество станков.
Вывод: Так как равенство 10£ КЗ.О £ 20 выполняется для обоих деталей, то производство является среднесерийным.
Определяем размер партии деталей:
=(420*12)/253=20,87
Принимаем n = 21 шт.
5. Выбор и обоснование метода получения заготовки
Главным при выборе заготовки является обеспечение заданного качества готовой детали при ее минимальной себестоимости. Себестоимость детали определяется суммированием себестоимости заготовки по калькуляции заготовительного цеха и себестоимости ее последующей обработки до достижения заданных требований качества по чертежу. Выбор заготовки связан с конкретным технико-экономическим расчетом себестоимости готовой детали, выполняемым для заданного объема годового выпуска с учетом других условий производства.
Сравним себестоимость изготовления способом поковки, штамповки и проката [6].
Поковка:
Сз = хGзаг.хК1хК2хК3хК4хК5 –(Gз – Gзаг.)х
Сi –базовая стоимость 1т. заготовки., руб.
Gдет. – масса детали.
Gзаг.- масса заготовки.
Sотх.- цена 1т. отходов (стружки), руб.
К1…К5- коэффициенты, зависящие от класса точности заготовки, группы сложности детали и массы заготовки, марки материала детали, объёма выпуска деталей и способа производства [13].
Группа сложности поковки:2
Группа серийности поковок:2
Сзаг.=(((52100/1000)*2,2*0,8*1,13*1,0*1,15*0,73)-((2,2-0,53)*(510/1000))) =
86,13 = руб.
Штамповка на ГКШП:
Группа сложности штамповки:2
Группа серийности штамповок:5
Сзаг. = ((58700/1000)*0,95*0,95*1,15*1,1*1,2*0,8)-((0,95-0,53)*(510/1000)) =
= 64,12 руб.
Вывод: себестоимость заготовки, получаемой штамповкой на кривошипных прессах меньше, чем методом поковки свободной ковкой. Учитывая повышение затрат на введение дорогостоящей термической обработки для снятия внутренних напряжений после удаления большого припуска, следует изменить способ получения заготовки по сравнению с принятый в базовом технологическом процессе.
Конструктивные характеристики детали
Масса детали: 0,53 кг.
Группа детали: Удлиненной формы (с прямой осью)
Группа стали: Сталь с массовой долей углерода до 0,55% включительно и суммарной массовой долей легирующих элементов до 2,0% включительно
Вид обработки: Кривошипные горячештамповочные прессы (открытая штамповка)
Тип разъёма: Плоский
Чертежи деталей с нанесенными технологическими указаниями называются технологическим чертежом и представляют собой руководящий технический материал для работников модельного, инструментального и заготовительного цехов, участвующих в изготовлении отливки, а также для приемщиков ОТК.
Выбор технологических баз для первой операции производится с учетом обеспечения надежного базирования и закрепления заготовки при обработке ее поверхностей. При этом желательно, чтобы базовые и обрабатываемые поверхности на первой операции находились в одной половине опоки или штамповочной формы.
Определение припусков на обработку (на сторону) производится дифференциально на каждую обрабатываемую поверхность заготовки в зависимости от норм точности, установленных на поковку в целом, ее отдельные поверхности и размеры.
6. Технико-экономический анализ и обоснование выбора технологического процесса
Одним из главных недостатков заводского варианта технологического процесса является нерациональное использование технологического оборудования и несовершенство применяемых методов получения поверхностей. Ярким примером того является использование разметочных операций, а соответственно перехода выверки заготовки на столе станка, что в современном технологическом процессе не допустимо в условиях среднесерийного производства.
Основным направлением сокращения затрат вспомогательного времени является автоматизация производственных процессов. Одним из главных направлений автоматизации является применение станков с ЧПУ. Эффективность применения этих станков выражается в повышенной точности и однородности размеров и формы обрабатываемых заготовок, в повышении производительности обработки, связанной с уменьшением доли вспомогательного времени, в снижении себестоимости обработки, связанной с повышением производительности, в снижении требований к квалификации станочника. Сложные, дорогостоящие в изготовлении и требующие трудоемкой наладки кулачки, упоры, кондукторы в системах ЧПУ не требуются, что значительно удешевляет и ускоряет наладку.
Поэтому станки с ЧПУ являются принципиально новыми средствами автоматизации для мелкосерийного и серийного машиностроения, сочетающими в себе производительность и точность станков-автоматов с гибкостью универсального оборудования.
Для современного этапа развития станков с ЧПУ характерно резкое расширение их функциональных возможностей, повышение уровня автоматизации и все более широкое применение в системах управления мощных вычислительных средств (микро-ЭВМ и микропроцессорной техники). Появилась новая разновидность металлорежущего оборудования – многоцелевые станки.
В многоцелевых станках выражен новый подход к построению технологического процесса. Они обеспечивают различными видами инструмента комплексную обработку деталей без переустановок или при минимальном их числе.
Чтобы перейти от одной технологической операции к другой, приходится каждый раз освобождать деталь, снимать ее со станка и транспортировать на другой станок, где вновь производить установку (базирование), настройку на исходные размеры и закрепление. Каждая переустановка обрабатываемой детали непременно вносит свои погрешности в ее окончательные размеры.
Таким образом, большой выбор выполняемых на одном станке разнородных операций изменяет представление о традиционных технологических группах станков.
Учитывая приведенные выше доводы, можно улучшить существующий технологический процесс следующим образом:
Для детали «Корпус»
С учетом особенности конструкции детали - пространственная сложнопрофильная, требующая обработки с пяти сторон и, принимая во внимание, наличие большой площади необрабатываемых поверхностей, а также с учетом изменения способа получения заготовки (точная штамповка на прессах) принимаем решение сформировать технологический процесс из двух этапов - многоцелевая обработка на станке с горизонтальным расположением шпинделя, оснащенным опциональным поворотным столом, обеспечивающим возможность обработки с пяти сторон и слесарная обработка, включающая получение радиального отверстия малого диаметра (0,5 мм) на настольном сверлильном станке.
На многоцелевой операции получим торцы с пяти сторон фрезерованием и за пять позиций, реализуемых за счет поворота стола станка относительно вертикальной и горизонтальной осей, получим все основные поверхности детали - внутренние цилиндрические, внутренние канавки, внутренние резьбы, внутренний конус и др., а также наружные цилиндрические поверхности, наружные резьбы, шестигранник. В качестве оборудования предлагается использовать многоцелевой горизонтальный станок повышенной точности модели DMC 55 H duoBLOCK, который может оснащаться в качестве опции специализированным поворотным столом с программируемым поворотом вокруг двух осей.
Заготовку устанавливаем в специальное приспособление с базированием по необрабатываемым наружным цилиндрическим поверхностям диам. 23 мм в призмы, две из которых расположены горизонтально на одной оси, а третья располагается под углом 90 град. относительно оси призм и плоскости плиты. Закрепляем заготовку прихватами по необрабатываемым поверхностям с расположением элементов закрепления с учетом возможности обработки различных поверхностей.
Наружные цилиндри<
|
|
Наброски и зарисовки растений, плодов, цветов: Освоить конструктивное построение структуры дерева через зарисовки отдельных деревьев, группы деревьев...
История создания датчика движения: Первый прибор для обнаружения движения был изобретен немецким физиком Генрихом Герцем...
Эмиссия газов от очистных сооружений канализации: В последние годы внимание мирового сообщества сосредоточено на экологических проблемах...
Индивидуальные и групповые автопоилки: для животных. Схемы и конструкции...
© cyberpedia.su 2017-2024 - Не является автором материалов. Исключительное право сохранено за автором текста.
Если вы не хотите, чтобы данный материал был у нас на сайте, перейдите по ссылке: Нарушение авторских прав. Мы поможем в написании вашей работы!