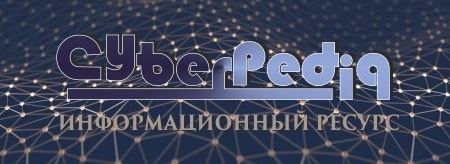
Типы оградительных сооружений в морском порту: По расположению оградительных сооружений в плане различают волноломы, обе оконечности...
Двойное оплодотворение у цветковых растений: Оплодотворение - это процесс слияния мужской и женской половых клеток с образованием зиготы...
Топ:
Характеристика АТП и сварочно-жестяницкого участка: Транспорт в настоящее время является одной из важнейших отраслей народного...
Эволюция кровеносной системы позвоночных животных: Биологическая эволюция – необратимый процесс исторического развития живой природы...
Интересное:
Аура как энергетическое поле: многослойную ауру человека можно представить себе подобным...
Финансовый рынок и его значение в управлении денежными потоками на современном этапе: любому предприятию для расширения производства и увеличения прибыли нужны...
Лечение прогрессирующих форм рака: Одним из наиболее важных достижений экспериментальной химиотерапии опухолей, начатой в 60-х и реализованной в 70-х годах, является...
Дисциплины:
![]() |
![]() |
5.00
из
|
Заказать работу |
|
|
Плоские сита. Многие зерноочистительные и сортирующие машины имеют в качестве рабочего органа движущиеся сита. При просеивании сквозь сита зерновая масса очищается от примесей, которые отличаются своими размерами от зерен основной культуры. Кроме того, зерно на ситах может быть разделено на сорта. Форма отверстий и их величина имеют большое значение и определяют назначение сита.
Сита с круглыми отверстиями разделяют зерновую массу по ширине частиц, сита с продолговатыми отверстиями – по толщине частиц (рисунок 2.2). Сита с квадратными отверстиями не обеспечивают четкого разделения зерновой массы, так как частицы могут располагаться как по стороне квадрата, так и по его диагонали. Поэтому сита с круглыми и квадратными отверстиями используются для очистки зерна от крупных и мелких примесей, сита с продолговатыми отверстиями – для сортирования зерна.
Каждое сито разделяет зерновую массу на две части: та часть, которая проходит сквозь отверстия, называется проходом; другая часть, которая остается на сите и ссыпается с него через край, называется сходом.
В зерноочистительных и сортирующих машинах обычно работают одновременно несколько сит с отверстиями разной величины
и формы для того, чтобы разделить зерновую массу сразу на несколько фракций. По форме сита различают плоские и цилиндрические (барабанные). Плоские сита применяются для очистки зерна и сухого солода от примесей; барабанные сита – для сортирования зерна и очистки сухого солода от ростков.
Размеры отверстий и частота расположения их на сите оказывают большое влияние на производительность сита. Чем большее количество отверстий приходится на единицу площади, тем больше вероятность попадания в них частиц зерна и, следовательно, тем выше производительность сита. Отношение суммы площадей отверстий к общей площади сита называется живым сечением сита, или коэффициентом использования площади сита. Чем больше живое сечение сита, тем выше его производительность, однако при слишком большой частоте расположения отверстий механическая прочность сита снижается.
|
Движение зерен по неподвижному ситу возможно только в том случае, когда оно будет наклонено к горизонту под углом большим угла трения зерен о сито. При начальной скорости, равной нулю, скорость движения тела по наклонной плоскости
, (2.1)
где – время движения тела по наклонной плоскости, с;
– коэффициент трения движущегося тела о плоскость.
Как видно из уравнения (2.1), зерна, скользящие вниз по наклонному ситу, будут двигаться равноускоренно (с увеличением времени скольжения увеличивается скорость). Скорость движения частиц может оказаться настолько большой, что многие частицы, находящиеся
в верхних слоях, не успеют войти в соприкосновение с ситом. Поэтому на неподвижном наклонном сите зерно должно двигаться очень тонким слоем и, следовательно, производительность такого сита всегда мала. Неподвижные сита в зерноочистительных машинах не применяют.
Чтобы повысить производительность плоских сит, их устанавливают под малым углом к горизонту, а движение зерна осуществляется посредством колебания сит. Ситовой корпус подвешивают при помощи плоских стальных пластин к станине машины и приводят его в колебательное движение посредством шатунно-кривошипного механизма. В зависимости от взаимного положения привода и ситового корпуса различают кинематические схемы:
1) наклонное сито с горизонтальными колебаниями;
2) горизонтальное сито с колебаниями в наклонной плоскости;
3) наклонное сито с колебаниями в наклонной плоскости.
Наклонные сита с горизонтальными колебаниями применяются наиболее часто в силу своей конструктивной простоты и легкости
в облуживании. Для таких сит получены следующие закономерности. Частица зерна, лежащая на наклонном сите, совершающем колебания
в горизонтальной плоскости, находится под действием сил тяжести, инерции и трения (рисунок 2.3).
|
На рисунке показано направление ускорения и сил инерции
при положении кривошипа в первом квадранте. В этом случае ускорение сита имеет направление слева направо.
Определим условия смещения частицы по поверхности сита.
В рассматриваемом случае ускорение сита
, (2.2)
где – угловая скорость кривошипа;
– радиус малого кривошипа;
– мгновенный угол поворота кривошипа.
Когда кривошип находится в первом или в четвертом квадранте, ускорение сита имеет направление слева направо. Сила инерции всегда противоположна направлению ускорения и, следовательно, в данном случае стремится сдвинуть частицу зерна вверх по наклонной плоскости сита (рисунок 2.3 а). При положении кривошипа во втором или
в третьем квадранте ускорение сита имеет направление справа налево, а сила инерции направлена слева направо и стремится сдвинуть частицу зерна вниз по наклонной плоскости сита (рисунок 2.3 б).
Сила инерции может быть рассчитана как произведение массы частицы на ее ускорение
:
. (2.3)
Сила тяжести может быть разложена на нормальную составляющую:
(2.4)
и продольную составляющую:
, (2.5)
где – угол наклона сита.
Аналогично можно разложить и силу инерции:
; (2.6)
. (2.7)
Величины и направления сил и
всегда постоянны и зависят только от веса частицы зерна и угла наклона сита. Составляющие силы инерции
и
имеют переменную величину и направление. Нормальная составляющая сила
прижимает частицу зерна к ситу при положении кривошипа в первом и четвертом квадрантах и, наоборот, отталкивает ее, когда кривошип находится во втором и в третьем квадрантах. Продольная составляющая сила
направлена вдоль сита
вверх, когда палец кривошипа находится в первом и четвертом квадрантах, и вниз, когда он находится во втором и в третьем квадрантах.
Движению зерна по ситу препятствует сила трения:
,
где – коэффициент трения зерна по ситу;
– угол трения.
Учитывая взаимодействие всех сил, движение частицы зерна вниз по наклонной плоскости сита будет наблюдаться при положении кривошипа во втором и в третьем квадрантах (см. рисунок 2.3 б) при следующем условии:
|
. (2.8)
При крайнем правом положении кривошипа сила, сдвигающая частицу зерна вниз по наклонной плоскости сита, имеет наибольшую величину. Для этого положения . С учетом этого, подставив
в неравенство (2.8) значения сил из уравнений (2.4 – 2.7), получается
. (2.9)
Заменив
,
неравенство (2.9) примет вид:
. (2.10)
Если число колебаний сита будет уменьшаться, то движущая сила будет также уменьшаться, и при некотором минимальном числе колебаний в минуту
она станет равной силе трения. При этом зерно прекратит движение по ситу. Тогда из уравнения (2.10) минимальное число колебаний сита
. (2.11)
При положении кривошипа в I и IV квадрантах сила направлена вверх по ситу (см. рисунок 2.3 а). При достаточно большом числе колебаний сила
может оказаться больше силы
и заставит частицу зерна подниматься вверх по наклонной плоскости сита, преодолевая силу трения. Чтобы не допускать встречного движения зерна (т.е. подъема вверх), число колебаний сита не должно превышать опреде-
ленного максимального значения. Этот максимум колебаний соответствует равенству движущей силы и силы трения:
. (2.12)
Решение уравнения относительно максимального числа колебаний сита приведет к следующему выражению:
. (2.13)
Для нормальной работы сит число колебаний должно иметь промежуточное значение между
и
.
Цилиндрические сита. Главным рабочим органом этих машин является перфорированный барабан. Цилиндрические сита устанавливают под небольшим углом к горизонту и приводят во вращательное движение. При медленном вращении сита на частицу зерна оказывает воздействие только сила тяжести, при быстром вращении сита возникает еще и центробежная сила.
Частица зерна во вращающемся сите прижимается к поверхности нормальной составляющей силы тяжести и центробежной силой
(рисунок 2.4).
Эти силы соответственно равны:
(2.14)
и
, (2.15)
где – радиус цилиндра;
– угловая скорость барабана;
– масса частицы;
– угол откоса частицы.
Под действием силы трения частица зерна будет перемещаться вместе с ситом до тех пор, пока сила
(составляющая силы тяжести
) не станет равной силе трения Т:
|
, (2.16)
или
. (2.17)
Заменив в уравнении
,
получим после преобразований:
. (2.18)
Отсюда число оборотов сита , соответствующее подъему частицы зерна на угол
:
. (2.19)
Если число оборотов барабанного сита увеличивать, то центробежная сила будет возрастать и частица зерна поднимется до горизонтального диаметра, затем выше на угол при определенном числе оборотов барабана
. Новое значение угла подъема зерна:
. (2.20)
С учетом угла подъема уравнение (2.18) относительно числа оборотов
:
. (2.21)
Дальнейшее увеличение скорости вращения барабана вызовет еще больший подъем зерна, и при предельном значении числа оборотов зерно достигнет зенита и, не оторвавшись от поверхности сита, будет продолжать движение вместе с ним. Следовательно, просеивание зерна сквозь сито прекратится.
Число оборотов определится из уравнения (2.21) при
:
. (2.22)
При нормальной работе число оборотов цилиндрического сита должно быть значительно меньше предельного; чем больше число оборотов сита, тем выше поднимается зерно и тем больше скорость обратного скольжения. При большой же скорости скольжения зерно не успевает проваливаться через отверстия.
Четкость деления зерна по сортам тем больше, чем продолжительнее зерно находится в соприкосновении с сортирующей поверхностью и чем интенсивнее оно при этом перемешивается. Оба эти фактора зависят от размеров, угла наклона и окружной скорости барабанного сита. Предельный наклон цилиндра составляет 0,1 м на 1 м длины, нормальная окружная скорость сита 0,7–1,2 м/сек.
Сепаратор с цилиндрическим ситом для сортирования зерна представлен на рисунке 2.5. Сортируемое зерно непрерывно подается через приемное устройство 1 в барабан, состоящий из двух сит 4 и 5. Барабан вращается внутри герметичного корпуса машины, внизу которого расположены два шнека 6, предназначенные для отвода кормового зерна (проход через сито 4) и зерна II сорта (проход через сито 5). Каждый шнек перекрыт частично клапаном 3 во избежание смешивания сортированного зерна. Крупное зерно I сорта сходит с сита 5.
В процессе работы сито очищается щетками 2.
Вследствие интенсивного перемешивания зерна в машине выделяется много пыли, для удаления которой необходима аспирация. На каждую тонну зерна необходимо отсасывать 150–200 м3 воздуха. Машина с барабанным ситом имеет большие габариты при относительно малой производительности, объясняется это тем, что лишь 1/5 общей
поверхности барабанного сита одновременно находится в работе. Достоинствами такой машины являются хорошее перемешивание зерна, плавность работы.
Производительность барабанного сита для зерна
, (2.23)
где – объемная масса зерна, кг/м3;
|
– угол наклона барабана к горизонту;
– наибольшая высота слоя зерна в поперечном сечении барабана, м.
Триеры. Примеси, отличающиеся от зерен основной длиной, отделить на ситах невозможно, так как сита разделяют зерно по ширине и толщине. Машины, которые выделяют из зерна примеси, отличающиеся от него длиной, называются триерами. Рабочим органом триера является цилиндр или диск с ячейками, выбирающими из зерновой массы короткие частицы (рисунок 2.6).
По назначению различают триеры двух видов: а) триеры для выделения из основной массы зерна половинчатых зерен и шаровидных примесей (куколя и других), количество которых редко достигает 5 %; б) триеры для отделения зерен основной культуры (пшеницы, ячменя
и т.п.), количество которой равно обычно 95 % ко всему объему зерновой массы, от длинных зерен овса и овсюга. Триеры первого вида называются куколеотборниками, триеры второго вида – овсюгоотборниками. Естественно, что при равных размерах куколеотборник имеет гораздо большую производительность, чем овсюгоотборник.
В зависимости от назначения триера его ячейки выполняют разных размеров. Диаметр ячеек триера для выделения половинчатых зерен ячменя, шаровидных зерен куколя и других семян составляет
6,25–6,5 мм; для выделения пшеницы – 8,5 мм; для выделения ячменя из овса – 9,5–10 мм.
Эффективность работы ячеистых поверхностей зависит от частоты ячеек на единице площади и порядка расположения ячеек [2, 8]. Наиболее рациональное расположение – шахматное, когда каждая ячейка размещена в центре правильного шестиугольника, а в вершинах находятся центры смежных ячеек. В этом случае число ячеек на 1 м2 поверхности определяют по следующей зависимости:
, (2.24)
где – шаг расположения ячеек, определяемый как
;
– диаметр триера.
Основные параметры цилиндрической поверхности с ячейками, определяющими ее производительность и эффективность: диаметр цилиндра, его длина, размеры и форма ячеек.
При медленном вращении цилиндра частицы зерна внутри цилиндра будут находиться под воздействием только одной силы – силы тяжести. При быстром вращении возникает еще центробежная сила. Частица зерна, находящаяся между ячейками, т.е. на гладкой поверхности вращающегося триерного цилиндра, будет прижиматься к поверхности силой (см. рисунок 2.4), которая слагается из нормальной составляющей веса частицы
и центробежной силы
:
, (2.25)
где – радиус цилиндра;
– угловая скорость триера;
– масса частицы;
– угол откоса частицы.
Сила будет стремиться скатить частицу зерна вниз:
. (2.26)
Под действием силы трения частица будет удерживаться на поверхности:
,
где – коэффициент трения зерна по ситу;
– угол трения.
Скольжение частицы будет возможно после того, как эти силы уравняются:
. (2.27)
После преобразований уравнение (2.27) примет вид:
, (2.27)
откуда угол, на который поднимаются частицы зерна, находящиеся на гладкой поверхности цилиндра:
. (2.28)
Соответствующее число оборотов триера можно найти из (2.27):
. (2.29)
При увеличении числа оборотов будет возрастать центробежная сила, вследствие чего частицы зерна будут подниматься до горизонтального диаметра или выше его на угол (см. рисунок 2.4). Угол
является составляющей угла
:
. С учетом угла подъема
уравнение (2.18) относительно числа оборотов
:
. (2.30)
Дальнейшее увеличение скорости вращения барабана вызовет еще больший подъем зерна, и при предельном значении числа оборотов зерно достигнет зенита и, не оторвавшись от поверхности сита, будет продолжать движение вместе с ним. Следовательно, просеивание зерна сквозь сито прекратится.
Число оборотов определится из уравнения (2.30) при
:
. (2.31)
Для тихоходных триеров
, (2.32)
что соответствует линейной скорости триера м/сек.
Для быстроходных триеров
, (2.33)
что соответствует м/сек.
Цилиндрические триеры. Цилиндрический тихоходный триер (рисунок 2.7) состоит из следующих основных частей: барабана 1, лотка 2 со шнеком 3 и приводного механизма, состоящего из конической зубчатой передачи 4. Рабочим органом цилиндрического триера является цилиндр 1, на внутренней поверхности которого имеются ячейки.
Во вращающемся триерном цилиндре короткие зерна (куколь и битые зерна) попадают в ячейки, а удлиненные зерна (пшеница и рожь) скользят по внутренней гладкой поверхности цилиндра и, поднявшись по ней до верхней границы зоны скольжения, отрываются от поверхности цилиндра и попадают в желоб шнека вывода очищенного зерна. Затем они удаляются из триера. Короткие зерна, поднявшись в ячейках триерного цилиндра в свободную от удлиненных зерен зону, выпадают в желоб вывода куколя и битого зерна и также выводятся из триера.
Зерно поступает через приемную коробку 5 на рабочую поверхность барабана, приводимого во вращение конической передачей 4. При вращении цилиндра короткие зерна заполняют ячейки и поднимаются на некоторую высоту; длинные частицы, не укладывающиеся
в ячейках полностью, выпадают из них при малом угле подъема и возвращаются в зерновую массу; короткие частицы, целиком укладывающиеся в ячейках, удерживаются в них дольше и выпадают из ячеек
в лоток 2, находящийся внутри цилиндра. Из лотка эти частицы
шнеком 3 выводятся наружу по стрелке А. Регулирование количества
выбрасываемых в лоток мелких зерен производится посредством поворота лотка вокруг неподвижного главного вала 9 при помощи рычага 10. Последний закрепляется в определенном положении болтом и гайкой на хорде. Более длинные зерна смеси продвигаются по внутренней поверхности цилиндра и выпадают из него через прямоугольные отверстия 7 в задней розетке 8.
Быстроходные триеры по сравнению с тихоходными имеют более высокую производительность за счет лучшего перемешивания зерна и увеличения числа проходящих мимо зерна ячеек благодаря большой окружной скорости цилиндра.
Вследствие больших скоростей, а следовательно, и большой центробежной силы, действующей на зерна, в быстроходном триере желоб со шнеком необходимо поднять выше, чем в тихоходном. Обычно вал быстроходного триера одновременно бывает и валом шнека (рису-
нок 2.8).
Стальной цилиндр 1 со штампованными ячейками состоит из отдельных обечаек, склепанных посредством стальных обручей 2. На концах цилиндра укреплены болтами 3 передняя 4 и задняя 5 розетки. Лоток 6 со шнеком свободно вращается на валу 7. Передняя розетка 4 посажена на вал 7 на шпонке, благодаря чему цилиндр и шнек жестко связаны между собой и вращаются одновременно. Положение лотка 6 со шнеком можно изменять червяком 8.
Наиболее совершенное действие ячеистой поверхности будет
в том случае, если большая часть ячеек при выходе из слоя зерна заполнена короткими частицами. Если же ячейки выходят пустыми или
с длинными частицами, то производительность триера снижается. Перемешивание зерна увеличивает возможность попадания коротких частиц в ячейки и повышает производительность.
К основным расчетным параметрам цилиндрического триера относят производительность, показатель кинематического режима, транспортирующую способность цилиндра, определяемую скоростью
осевого перемещения зерна, форму приемного желоба и геометрию его установки, а также потребляемую мощность.
Производительность цилиндрического триера (кг/ч) определяется по формуле
, (2.34)
где – удельная нагрузка на триерную поверхность, кг/(ч м2),(таблица 2.1);
– площадь ячеистой поверхности, м2.
Таблица 2.1 – Значения удельной нагрузки [ кг/(ч м2) ] для различных культур
Операция | ![]() |
Очистка пшеницы от примесей: коротких (куколя и др.) длинных (овсюга и др.) | 750–850 550–650 |
Очистка овса от коротких примесей | 650–700 |
Очистка гречихи от коротких и длинных примесей | 650–750 |
Разделение продуктов шелушения овса | 500–600 |
Отбор ломаных зерен из обработанного риса | 700–750 |
Контроль отходов машин: куколеотборочных овсюгоотборочных |
Для проверочных расчетов производительность цилиндрического триера можно определить, используя формулу
, (2.35)
где – коэффициент использования ячеистой поверхности;
– диаметр цилиндра, м;
– частота вращения цилиндра, об/мин;
– число ячеек на 1 м2 ячеистой поверхности;
– средняя масса зерна, выбираемого одной ячейкой, кг;
– длина цилиндра, м;
– подача мелкой фракции, кг/ч.
Для определения диаметра цилиндра в зависимости от производительности пользуются соотношениями:
Диаметр цилиндра, мм | ||||
Производительность, т/ч | до 1,2 | 1–2,5 | 2,5–3,5 | 3,5–5,0 |
Кинематический режим цилиндрического триера характеризуется показателем , откуда частота вращения
и окружная скорость цилиндра
:
,
, (2.36)
где – радиус цилиндра, м.
По кинетическому режиму цилиндрические триеры подразделяют на тихоходные и быстроходные: для тихоходных = 0,2¸0,3, для быстроходных
= 0,5¸0,6. Предельное значение
составляет 0,67. Отсюда предельная частота вращения цилиндра определяется в соответствии с уравнениями (2.32) и (2.33).
Потребляемую для работы триера мощность (кВт) определяют в зависимости от его производительности. Для ориентировочных расчетов можно пользоваться формулой
.
На практике используются также триерные блоки, предназначенные для выделения из зерновой смеси длинных (овсюг, соломка) и коротких (куколь, гречишка, дробленые зерна и т.п.) примесей.
Дисковый триер. На заводах в основном применяют дисковые триеры, обеспечивающие более высокую производительность и эффективность очистки зерна от примесей, чем цилиндрические триеры. Рабочими органами дисковых триеров являются диски с ячейками на боковых кольцевых поверхностях.
Наиболее распространены две формы ячеек (рисунок 2.9 а, б):
с плоским дном – для овальных зерен, полукруглым дном – для шаровидных зерен. Ячейки на дисках располагают по концентрическим
окружностям. Расположение ячеек разной формы и их размеры приведены в [2]. Триер ЗТК (см. рисунок 2.9 а) является куколеотборочной машиной, а триер ЗТО – овсюгоотборочной (см. рисунок 2.9 6). На одном и том же валу триера можно последовательно устанавливать диски для отделения как коротких, так и длинных частиц.
Во время работы дискового триера (рисунок 2.9 в) зерно непрерывным потоком подается в приемное устройство 1 и заполняет пространство между дисками – зона I; при вращении они захватывают зерно. Длинные частицы, выпадая из ячеек в зоне II, возвращаются
в общую массу в зоне I, а короткие частицы выпадают в зоне III и по щитку удаляются из триера. Изогнутые спицы 2 перебрасывают зерна от одного диска к другому вдоль всего корпуса машины к выходному каналу.
Ниже щитка 3 установлен шнек 4, который транспортирует примеси из рабочей зоны в контрольное отделение. При помощи щитков 3, расположенных между дисками, можно направить примеси в шнек или отводную самотечную трубу.
Установка дискового триера приведена на рисунке 2.10. Внутреннее пространство триера разделено накопительным отделением 6 на рабочее и контрольное отделения. Зерновую смесь из рабочего отделения в контрольное подают ковшовым колесом 7 и перепускным лотком 8. В верхней части кожуха расположены приемный патрубок 14 с за-слонкой для регулирования количества поступающего зерна в триер
и патрубок 13 для аспирации. В нижней части кожуха смонтировано
подвижное днище с отверстиями для удаления осевших на дно минеральных примесей и остатков зерна. Для сбора отходов предусмотрен патрубок 9. Основной рабочий орган триера – диски 5, которые на боковых поверхностях имеют карманообразные ячейки. На спицах дисков закреплены планки, предназначенные для перемешивания зерновой смеси и транспортирования ее вдоль триера. Диски 5 расположены так, что планка образует винтовую линию вдоль оси вала.
Зерно для очистки поступает в триер через приемный патрубок 14 и заполняет внутреннее пространство между дисками. При вращении дисков пшеница заполняет карманообразные ячейки и под действием центробежной силы и силы тяжести отбрасывается в выходной патрубок 10 и затем выводится из триера. Длинные примеси не захватываются ячейками. Гонками на дисках они транспортируются вдоль триера к стенке перегружателя, накапливаются в конце рабочего отделения и через отверстие в боковой стенке попадают в накопительное отделение 6, откуда ковшовым колесом 7 подаются в контрольное отделение. Здесь отделяются зерна пшеницы, попавшие вместе с длинными примесями. Примеси выпускают из триера через разгрузочный патрубок 11 в боковой стенке кожуха 12. Уровень зерна в контрольном отделении регулируют заслонкой, установленной на разгрузочном патрубке 11, которая позволяет регулировать попадание зерна в отходы, доводя его до нормируемой величины.
По сравнению с цилиндрическими триерами дисковый триер отличается более высокими удельными показателями и эффективностью очитки, что позволяет улучшить подготовку зерна к помолу и повысить качество готовой продукции.
К основным параметрам дискового триера относят производительность, диаметр дисков и их число, кинематический режим, конструктивное исполнение приемно-впускных и транспортирующих элементов и потребляемую мощность для привода триера.
Производительность дискового триера (кг/ч) определяют по формуле
, (2.37)
где – радиусы диска по внешним и внутренним ячейкам, м;
– удельная нагрузка, кг/(ч м2), (таблица 2.2);
– число дисков.
Таблица 2.2 – Значение удельной нагрузки, принимаемое при очистке различных культур
Операция | ![]() |
Очистка от примесей: коротких (куколя и др.) длинных (овсюга и др.) | 800–900 650–700 |
Разделение продуктов шелушения овса | 450–550 |
Для проверочных расчетов производительность дискового триера можно определить по формуле
, (2.38)
где – число дисков;
– частота вращения дисков, об/мин;
– средняя масса зерна, выбираемого одной ячейкой, кг;
– число ячеек на одной стороне диска;
– коэффициент использования ячеистой поверхности;
– подача мелкой фракции, кг/ч.
При очистке от коротких примесей = 0,03¸0,035, при очистке от длинных примесей
= 0,16¸0,18.
Число ячеек на одной стороне диска определяют по формуле
, (2.39)
где ,
– наружный и внутренний диаметры диска, мм;
– размер ячейки, мм;
– ширина перемычки между ячейками, мм.
Наружный диаметр дисков выбирают по конструктивным соображениям обычно
380, 460 и 630 мм. Внутренний диаметр
определяют из отношения
= 1,65. При заданной производительности число дисков определяется по формуле при известных значениях
и
. На одном валу обычно устанавливают от 12 до 30 дисков.
Кинематический режим дискового триера (таблица 2.3) определяется показателем:
, (2.40)
где – радиус диска по внешним ячейкам.
Таблица 2.3 – Оптимальные значения показателя кинематического
режима и частоты вращения дискового триера
Культура, вид очистки | ![]() | ![]() |
Пшеница, от коротких примесей Пшеница, от длинных примесей Ячмень, от коротких примесей Гречиха, от длинных примесей Просо, от длинных примесей Рис, от коротких примесей Разделение продуктов шелушения овса | 0,86–0,92 1,2–1,4 1,3–1,7 0,31–0,41 1,2–1,4 051–0,61 0,41–0,51 | 50–52 60–62 62–70 30–35 60–62 40–45 35–40 |
Обычно частоту вращения дискового ротора принимают не более 55 об/мин, таким образом,
. (2.41)
Для эффективной работы дискового триера необходимо согласование времени технологического воздействия на сепарируемую смесь
с временем транспортирования ее по длине ротора.
Скорость продольного перемещения зерна в триере определяется круговым и продольным шагом гонков, закрепленных на спицах,
и их углом атаки. В серийных дисковых триерах круговой шаг , продольный
, т.е. равен расстоянию между дисками. Гонки на дисках крепят к спицам через 120°.
Мощность привода (кВт) для дисковых триеров ориентировочно определяют по формуле
, (2.42)
для высоконагруженных триеров:
Историки об Елизавете Петровне: Елизавета попала между двумя встречными культурными течениями, воспитывалась среди новых европейских веяний и преданий...
Особенности сооружения опор в сложных условиях: Сооружение ВЛ в районах с суровыми климатическими и тяжелыми геологическими условиями...
Адаптации растений и животных к жизни в горах: Большое значение для жизни организмов в горах имеют степень расчленения, крутизна и экспозиционные различия склонов...
Биохимия спиртового брожения: Основу технологии получения пива составляет спиртовое брожение, - при котором сахар превращается...
© cyberpedia.su 2017-2024 - Не является автором материалов. Исключительное право сохранено за автором текста.
Если вы не хотите, чтобы данный материал был у нас на сайте, перейдите по ссылке: Нарушение авторских прав. Мы поможем в написании вашей работы!