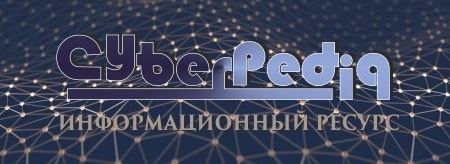
Историки об Елизавете Петровне: Елизавета попала между двумя встречными культурными течениями, воспитывалась среди новых европейских веяний и преданий...
Состав сооружений: решетки и песколовки: Решетки – это первое устройство в схеме очистных сооружений. Они представляют...
Топ:
Теоретическая значимость работы: Описание теоретической значимости (ценности) результатов исследования должно присутствовать во введении...
Эволюция кровеносной системы позвоночных животных: Биологическая эволюция – необратимый процесс исторического развития живой природы...
Устройство и оснащение процедурного кабинета: Решающая роль в обеспечении правильного лечения пациентов отводится процедурной медсестре...
Интересное:
Подходы к решению темы фильма: Существует три основных типа исторического фильма, имеющих между собой много общего...
Наиболее распространенные виды рака: Раковая опухоль — это самостоятельное новообразование, которое может возникнуть и от повышенного давления...
Уполаживание и террасирование склонов: Если глубина оврага более 5 м необходимо устройство берм. Варианты использования оврагов для градостроительных целей...
Дисциплины:
![]() |
![]() |
5.00
из
|
Заказать работу |
|
|
Целью проращивания солода является синтез и активизация неактивных ферментов, под влиянием которых в процессе затирания достигается растворение всех резервных веществ зерна. Под действием ферментов при солодоращении часть сложных веществ зерна превращается в мальтозу, глюкозу, мальтодекстрины и высшие декстрины, пептоны, пептиды, аминокислоты и др.
Переход зародыша от состояния покоя к активной жизнедеятельности возможен только при достаточной влажности, наличии кислорода и оптимальной температуры.
Технологические требования к проращиванию зерна характеризуются следующими показателями: температурой, при которой происходит проращивание зерна на отдельных стадиях; содержанием влаги в зерне; соотношением кислорода и диоксида углерода в слое зерна на отдельных стадиях проращивания; продолжительностью проращивания.
На морфологические изменения зерна и на глубину его растворения влияет интенсивность аэрации зерна при проращивании. Слабая аэрация замедляет рост корешков, и растворение эндосперма протекает быстрее. Интенсивная аэрация способствует росту корешков и листовой части зародыша, но при этом усиливается дыхание и расходуется больше питательных веществ.
Активация и образование ферментов. В спелом зерне меньшая часть ферментов находится в активном состоянии, а большая часть связана с белками и поэтому не активна. При прорастании зерна белки под действием протеолитических ферментов расщепляются и связанные с ними ферменты переходят в свободное, активное состояние. Действие гемицеллюлаз делает доступным содержимое крахмальных зерен для воздействия а -амилазы. Накопление ферментов происходит и в результате новообразования в алейроновом слое и зародыше [3, 9]. Значительную роль в этом играет гибберелловая кислота (ГК) – ростовое вещество, образующееся в прорастающем зерне.
|
Ферменты могут действовать при высоких температурах и в отсутствие кислорода, когда зародыш погибает. Эту их способность используют при солодоращении: сначала прорастающему зерну подают достаточно кислорода для образования ферментов, а затем подачу воздуха прекращают. При этом ферменты продолжают действовать, растворяя эндосперм, а зародыш почти не развивается. Это дает возможность уменьшать потери ценных веществ зерна.
Дыхание зерна. Проращивание зерна сопровождается интенсивным дыханием – потреблением кислорода и образованием диоксида углерода. Основным материалом для дыхания служат углеводы.
При аэробном дыхании мальтоза, образовавшаяся из крах-
мала под действием ферментов, превращается в глюкозу, ко-
торая окисляется до диоксида углерода и воды с выделением теплоты 2822 кДж/г-моль.
При недостаточном притоке воздуха во время замачивания
и проращивания нарушается естественное дыхание зерна, что наблюдается, например, при проращивании зерна в высоком слое, когда
в массе зерна накапливается диоксид углерода и повышается температура. Это вызывает анаэробное дыхание, протекающее
в соответствии с суммарным уравнением спиртового брожения:
кДж/г-моль.
В последней реакции на каждую молекулу глюкозы, израсходованную на дыхание, выделяется в 12 раз меньше теплоты и в 3 раза меньше диоксида углерода, чем при аэробном дыхании. Поэтому, чтобы обеспечить себя необходимой энергией, зерно должно расходовать намного больше сахара, чем при аэробном дыхании. При хорошей аэрации обеспечивается более эффективное в энергетическом
отношении аэробное дыхание и снижается расход углеводов, затрачиваемых на анаэробное дыхание.
Практически установлено, что для получения солода с хорошей растворимостью, высокой ферментативной активностью и минимальными потерями сухих веществ процесс солодоращения должен протекать медленно, при возможно низких температурах.
|
Превращение углеводов. Расщеплению крахмала предшествует расщепление гемицеллюлоз и белков соответствующими ферментами. Крахмал на 80 % состоит из амилопектина и на 20 % из амилозы. Часть его расщепляется под действием амилолитических ферментов
(a -амилаз), разрывающих связь a-(1–4) связи. Образующиеся декстрины становятся доступными для действия b -амилазы. Мальтоза расщепляется b -глюкозидазой до глюкозы.
Таким образом, в результате гидролиза крахмала образуется смесь олигосахаридов, декстринов и моносахаридов.
Изменение азотсодержащих веществ. Считается, что в процессе солодоращения до 40 % азотистых веществ становятся водорастворимыми. Глубина растворения высокомолекулярной фракции белковых веществ влияет на качество солода и получаемого из него пива. При слабом растворении белков пиво плохо фильтруется и осветляется,
а при понижении температуры в пиве появляется муть. Пиво, полученное
из солода с сильным белковым растворением, имеет низкую пеностойкость, не обладает полнотой вкуса.
Температура, продолжительность солодоращения и аэрация. Солодоращение при температуре 13–16 °С обеспечивает умеренный рост зародыша и максимальное накопление амилолитических ферментов, при этом достигается глубокий распад белковых веществ.
Температура проращивания светлого солода не должна превышать 18 °С, для темного солода допускается 21–23 °С. В темном солоде должно быть большое количество аминокислот и моносахаридов, которые, взаимодействуя при высокой температуре, образуют красящие вещества, называемые меланоидинами, и ароматические вещества.
Биологические и ферментативные процессы при солодоращении регулируются интенсивностью аэрации. Поэтому процесс солодоращения делится на две стадии: первая (1–4 сут), когда подается достаточное количество воздуха, характеризуется ростом зерна и накоплением ферментов, вторая (5–7 сут), когда подача кислорода воздуха ограничена, жизнедеятельность зародыша притормаживается и происходят основные ферментативные процессы.
Способы проращивания зерна
Замоченное зерно проращивают в солодорастильных аппаратах
с соблюдением температурного и влажностного режимов, подвода необходимого количества кондиционированного воздуха для дыхания зерна и удаления диоксида углерода. Также необходимо периодически перемешивать зерновую массу. Подобные условия могут быть созданы в помещениях или аппаратах, изолированных от окружающей среды.
|
Различают токовые и пневматические солодовни. Если проращивание зерна проводят на полу в тонком слое, солодовню называют токовой. Проращивание зерна в специальных механизированных ящиках или барабанах с искусственной аэрацией называется пневматическим.
Токовая солодовня размещается в одноэтажном или многоэтажном здании с гладким полом (током). Температуру в рабочем помещении поддерживают 10–12 °С, относительную влажность воздуха
85–90 %. Длительность проращивания (7–8 сут) зависит от качества
и сорта приготовляемого солода. При солодоращении выделяется большое количество диоксида углерода, поэтому солодовни оборудованы приточной и вытяжной вентиляцией.
Однако тяжелый ручной труд при перелопачивании зерна на току, трудность механизации работ, зависимость процесса солодоращения от внешних метеорологических условий, потребность в большой производственной площади заставляют отказаться от этого вида солодовен.
В настоящее время для проращивания зерна применяют в основном пневматические солодорастильные аппараты, представляющие собой барабаны или ящики, в которых проращиваемое зерно не соприкасается с атмосферным воздухом. В них нагнетают кондиционированный воздух, который продувается сквозь слой прорастающего зерна, аэрируя и охлаждая его при этом, а перемешивание осуществляют механическим способом.
Используются солодорастильные аппараты других типов: шахтные, туннельные, башенные, ленточные. Распространены статические солодорастильные аппараты, в которых происходит совмещение процессов замачивания и проращивания зерна.
Солодорастильные аппараты ящичного типа. Солодорастильные аппараты ящичного типа наиболее распространены в производстве солода. Ящичная солодовня состоит из солодорастильных аппаратов ящичного типа прямоугольной формы с ситчатыми днищами камер кондиционирования воздуха, вентиляторов и воздуховодов. Воздух увлажняют и охлаждают в специальных кондиционерах, которые могут быть индивидуальными для каждого аппарата или групповыми для нескольких аппаратов. Замоченный солод поступает в солодорастильные аппараты самотеком вместе с водой, которая затем удаляется через подситовое пространство.
|
Количество аппаратов соответствует числу суток проращивания зерна, обычно их бывает восемь. Заполнение аппаратов по высоте зависит от объема прорастающего зерна и изменяется ежедневно, так как по мере прорастания объем 1 т зерна увеличивается от 2 до 3,2 м3,
а высота слоя солода – от 0,8 до 1,1 м.
Во всех солодорастильных аппаратах ящичного типа солод перемешивают периодически шнековыми ворошителями, а в аппаратах
с передвижной грядкой – ковшовыми.
В механизированных пневматических солодорастильных аппаратах ящичного типа в зависимости от конструкции проводится несколько технологических операций без применения ручного труда: увлажнение и ворошение проращиваемого зерна, выгрузка свежепроросшего солода, мойка ящиков.
Замоченное зерно проращивают в пневматических солодовнях, соблюдая определенный температурный режим (10–14 0С), проводя при этом аэрацию (при относительной влажности воздуха 100 %)
и отвод теплоты, которая выделяется при дыхательных окислительно-энергетических процессах, протекающих в солоде. Согревание солода происходит за счет интенсивного дыхания зерна, которое проявля-
ется в окислении соответственно крахмала и жиров. Удельные
тепловыделения при окислении этих веществ составляют соответственно 17390 и 39480 кДж/кг. Знание количества окисленного вещества позволяет определить количество теплоты, выделившейся при солодоращении, и, следовательно, рассчитать расход и параметры кондиционированного воздуха.
Солодорастильный аппарат ящичного типа с индивидуальными камерами кондиционирования воздуха. Состоит из нескольких длинных открытых солодорастильных ящиков, разделенных между собой стенкой (рису-
нок 3.4). Вентилятор 1 нагнетает в канал 10 воздух, который направляется в увлажнители 2, а далее поступает в подситовое пространство ящиков 3, откуда попадает в солодорастильные ящики. Со стороны увлажнителя ящики изолированы стенкой, а с противоположной стороны открыты. В конце ящиков имеется проход, через него солодоворошитель 4 можно перемещать с одного ящика на другой. Под проходом установлен конвейер 6 для удаления свежепроросшего солода. В аппарате при работе повторно используется часть отработанного воздуха, который из помещения солодовни попадает через отверстия в решетках проходов между ящиками в канал 7 и всасывается вентилятором 8. Отработанный воздух может выбрасываться наружу через канал 5 или вентилятором 1 через клапан 9 снова нагнетаться
в ящики. Частоту вращения вентилятора 1 можно регулировать, чтобы подавать необходимое количество воздуха.
|
Конструкция солодорастильного аппарата такого типа обеспечивает хорошее проветривание проращиваемого зерна в каждом
ящике [2].
Солодорастильный ящик (рисунок3.5) имеет прямоугольную форму. Основное дно 1 сделано с небольшим уклоном для стока воды. Второе (ситчатое) дно 2, на которое укладывают замоченное зерно, сделано из углеродистой оцинкованной стали. Щелевидные отверстия в ситах имеют размер примерно (1,5–2,0)´25 мм. Живое сечение сит составляет не менее 15 % от общей площади поверхности. Через подситовое пространство в слой зерна подают кондиционированный воздух. На стенках ящика установлен передвижной солодоворошитель 4 с вертикальными шнеками. Перед загрузкой сита стенки и пол очищают от примесей, подситовое пространство обрабатывают 2%-ным раствором хлорной извести. Замоченное зерно вместе с водой подают из замочного аппарата в ящик и с помощью шнекового ворошителя распределяют на сите ровным слоем высотой 0,60–0,85 м.
Вначале продуванием кондиционированного воздуха зерно подсушивают, а затем в нем поддерживают аэробные условия дыхания и необходимую температуру. Для обеспечения нормального процесса проращивания зерна продуваемый воздух должен иметь 100%-ную влажность и температуру на 2 °С ниже температуры солода. Пневматический аппарат оснащается отдельным напорным вентилятором, системой охлаждения и увлажнения воздуха. Отношение ширины аппарата к длине выбирается с учетом обеспечения равномерного распре-деления воздуха и может составлять 1:4 и 1:8. Стенка аппарата высотой 1,2–3 м над ситом изготавливается из железобетона или кирпича толщиной 0,15–0,20 м. На верхней части боковых стенок устанавливаются рельсы и зубчатые штанги для передвижения шнекового ворошителя. Высота подситового пространства аппарата составляет 1,6–2,0 м.
Живое сечение плетенных из нержавеющей проволоки сит, на которых находится зерно, должно быть больше 20 %. Днище аппарата должно иметь уклон для стока воды в сборник. Выгрузка свежепроросшего солода из аппарата проводится в течение 2–3 ч.
Шнековый солодоворошитель (рисунок 3.6) представляет собой подвижную каретку с вертикальными шнеками. Во время работы он движется по рельсам вдоль ящика, а вертикальные шнеки при этом вращаются и перемешивают солод. Поступательная скорость всех ворошителей 0,5 м/мин, частота вращения шнеков – 8,5 об/мин.
Каретка ворошителя 1 четырьмя колесами 2 опирается на рельсы, уложенные на продольных стенках ящика. В движение ворошитель приводится электродвигателем 3, установленным на плите 4 каретки. двигатель получает энергию при помощи контакта, скользящего по троллейным проводам, или при помощи изолированного кабеля, подвешенного на скользящих кольцах вдоль ящика. Движение от электродвигателя передается через пару зубчатых колес валу 5, который через
червячные передачи 6 приводит во вращение вертикальные шнеки 7. Соседние шнеки вращаются во встречных направлениях для лучшего перемешивания солода.
Передвижение ворошителя вдоль ящика производится тем же электродвигателем 3. Для этой цели на валу одного вертикального шнека имеется червячная пара 8, передающая движение большой конической шестерне 9; малые конические шестерни 10 находятся в постоянном зацеплении с большой шестерней 9 и свободно вращаются на валу 11. Между малыми шестернями на том же валу сидит на скользящей шпонке кулачковая муфта 12. При помощи механизма управления 13 эта муфта может быть сцеплена с той или другой шестерней 10. Переключение кулачковой муфты обеспечивает реверсирование хода каретки.
Солодовни с передвижной грядкой. Солодовня с передвижной грядкой (рисунок3.7) представляет собой длинный ящик 6, в котором подситовое пространство разделено в поперечном направлении перегородками на секции 10, число которых равно или кратно числу суток ращения солода.
На продольных стенках ящика 6 уложены рельсы, по которым вдоль ящика периодически передвигается ковшовый солодоворошитель 5
с помощью тележки 4. При рабочем ходе ворошитель 5 перебрасывает проращиваемое зерно, чем достигается не только его перемешивание, но и перемещение вдоль ящика.
Рабочий ход ворошителя имеет направление от места выгрузки готового солода к месту загрузки замоченного зерна. Замоченное зерно из замочных аппаратов 7 и 8 загружается всегда в одно и то же место солодорастильного ящика 6. Ворошитель приводится в движение через каждые 12 или 24 ч и каждый раз перебрасывает зерно на один шаг,
а на освободившуюся площадь сита вновь загружается замоченное зерно. Солод, проходя к месту выгрузки, при очередном рабочем ходе ворошителя выбрасывается в бункер 3, откуда транспортерами 1 и 2 (шнеком, лентой и т.п.) передается в сушилку.
Кондиционированный воздух для продувания зерна нагнетается вентилятором в канал 10, проходящий вдоль ящика, а затем – в каждое отделение подситового пространства. Подача кондиционированного воздуха из этого канала в каждое отделение подситового пространства 9 регулируется шибером в зависимости от интенсивности роста, необходимости отвода выделяющегося диоксида углерода и поддержания оптимальной температуры.
Ковшовый ворошитель (рисунок 3.8) состоит из каретки 1, конвейера 2 с ковшами, механизма 5 подъема его, приводов конвейера
и каретки 1. Ковши с резиновыми скребками 3 размещены по всей ширине ящика.
Работа ворошителя начинается с того, что один конец конвейера опускают в крайнее нижнее положение, при котором ковши не доходят до сита ящика примерно на 10–15 мм. Затем приводят в движение конвейер и каретку. Ковши зачерпывают солод и перебрасывают его назад
относительно движения каретки, которая медленно перемещается вперед вдоль ящика. При этом солод не только перемешивается, но и перемещается вдоль ящика на один шаг в направлении, противоположном движению каретки.
Сита очищаются от солода резиновыми скребками, укрепленными на ковшах. В конце ящика, где установлены концевые выключатели, каретка останавливается, а ковшовый конвейер механизмом подъема перемещается в верхнее положение. При поднятом конвейере каретка быстро совершает обратный путь. Скорость движения цепи
с ковшами 9,8 м/мин.
Ворошение зерна и перемещение грядки по ситу на площадь, равную площади одной подситовой секции, осуществляется в направлении, обратном движению ворошителя. На освобожденную площадь сита вновь загружается замоченное зерно.
При параллельной установке нескольких солодорастильных ящиков с передвижными грядками кондиционеры размещают с таким расчетом, чтобы в каждом из них воздух готовился для определенной стадии солодоращения: в первом – неувлажненный воздух для подсушивания влажного, только что выгруженного в ящик замоченного зерна
и подвяливания свежепроросшего солода перед выгрузкой его из солодовни в сушилку; во втором кондиционере – охлажденный и увлажненный воздух для проветривания грядки на третий-четвертый день солодоращения и т.д.
В аппаратах с передвижной грядкой обеспечивается полная механизация процессов перемешивания зерновой массы, перевалки и выгрузки свежепроросшего солода. Производственная площадь используется максимально. К недостаткам аппаратов этого типа относятся цикличность процесса и сложность регулирования параметров воздуха
в отдельных зонах, так как кондиционер общий, а грядки неразделенные, кроме того, процесс нельзя вести с накоплением диоксида угле-рода.
Статический солодорастильный аппарат. В таких аппаратах замачивают и проращивают зерно, а также сушат солод в одном ящике, что позволяет уменьшить расход воды на 1 т сухого солода в 10 раз. Аппараты компактны, высокомеханированы. Высота слоя свежепроросшего ячменного солода в ящике до 1,2 м. Каждый ящик имеет индивидуальную установку кондиционирования воздуха, испольуемого при солодоращении, а также установку нагрева его для сушки солода.
В статическом солодорастильном аппарате (рисунок 3.9) очищенное отсортированное зерно из бункера 3 самотеком поступает в аппарат 4 для мойки и дезинфекции.
Неполноценное легкое зерно отделяется и через приемное устройство направляется в сборник 1. Заполненный водой и зерном моечный аппарат оставляют в покое на 20–30 мин, затем смесь зерна с водой интенсивно перемешивают сжатым воздухом.
Через 5–6 ч тщательно промытое зерно в виде водно-зерновой смеси гидротранспортером или шнеком направляется в солодорастильный ящик 5, где оно разравнивается, замачивается и проращивается,
и полученный солод сушится. Аппарат 5 периодического действия представляет собой индивидуальную камеру с ситчатым днищем, шнековым солодоворошителем 6 для ворошения и выгрузки солода.
Для обеспечения равномерного распределения давления сушильного агента в подситовом пространстве его высота должна составлять не менее 2 м. Для увлажнения и охлаждения воздуха, поступающего
в аппарат 5 в период замачивания и проращивания зерна, под ситом дополнительно устанавливаются форсунки, распыливающие воду
в тонкую и однородную пыль.
Выгруженное на сита аппарата 5 зерно оставляют в покое на 5 ч, обеспечивая при этом удаление избыточной воды. Во время замачивания зерно перемешивается и орошается водой из форсунок, установленных стационарно вдоль солодорастильного аппарата или на ворошителе. Замачивание осуществляется воздушно-оросительным способом с периодической или непрерывной продувкой слоя кондиционированным способом и орошением распыленной водой. Оптимальный расход кондиционированного воздуха составляет 250–300 м3/(ч.т),
а оптимальный расход воды – 1 м3 на 1 т зерна.
Продолжительность замачивания зерна до достижения влажности 45 % составляет в среднем 30–40 ч. После чего зерно приобретает нужную
влажность и начинается процесс солодоращения, во время которого зерно ворошат по установленному режиму 2–3 раза в сутки и продувают при помощи вентилятора 7 кондиционированным воздухом с использованием рециркуляции.
Готовый свежепроросший солод в аппарате 5 высушивается горячим воздухом, подаваемым через специальный теплогенератор 9 вентилятором 8. Сушку и термическую обработку солода проводят без ворошения в течение 20 ч. Расход сушильного агента на сушку солода составляет 4–4,5 тыс. м3 при давлении 1000 Па. В конце сушки расход агента уменьшается до 2 тыс. м3 /(ч.т) при давлении 400 Па. В процессе сушки солода необходимо не только удалить из него избыточную влагу, но и обеспечить благоприятные условия для протекания физиологических, биохимических и химических процессов, в результате которых продукт приобретает определенные технологические свойства.
Высушенный солод транспортером 10 направляется на росткоотбойную машину 11 и далее на склад для хранения.
Корпус ворошителя (риунок 3.10) представляет собой конструкцию, снабженную тремя крышками для обслуживания механизмов.
К нему крепится шнековый механизм 6. Разгрузочный конвейер шнекового ворошителя 6 статической солодовни состоит из вертикально установленных шнеков, смонтированных на конических роликоподшипниках в корпусах, которые крепятся фланцами к верхней стенке корпуса ворошителя. Шнеки имеют левое и правое вращение. Ворошитель передвигается по рельсам на четырех колесах с помощью цепочного механизма 5.
Система орошения 1 состоит из насоса с электродвигателем, трубопроводов со всасывающими патрубками и форсунками, установленными под корпусом 2, ворошителя между шнеками. Для удаления сухого солода солодорастильный ящик оборудуют скребковым транспортером, на который наклонным шнеком разгрузочной передвижной
стенки подается солод. Разгрузочная передвижная стенка 9 состоит из сварной рамы 3, откидной стенки, горизонтального шнека 7 и наклонного шнекового механизма 8 с индивидуальным приводом 4.
При загрузке вымытого зерна ворошитель находится под загрузочной стенкой, которая одновременно является торцовой стенкой ящика. Разгрузочная стенка подвешена на опорных площадках, прикрепленных к боковым стенкам ящика. По окончании загрузки ящика зерном включают последовательно механизмы ворошения его и движения ворошителя, который начинает перемещаться вдоль ящика, разравнивая зерно специальными планками, закрепленными на валах выше шнеков. При выгрузке солода из ящика ворошитель устанавливают в крайнее положение вплотную к разгрузочной стенке. С помощью рычагов соединяют ворошитель со стенкой и откидывают ее крышку,
в результате чего солод ссыпается в короб горизонтального шнека, затем включают последовательно шнек стенки, механизмы ворошения
и передвижения. Вертикальные шнеки поднимают солод до уровня короба горизонтального шнека, солод ссыпается в него и перемещается горизонтальным шнеком к приемному устройству наклонного шнека. Последний выводит солод на скребковый транспортер, расположенный вдоль ящика.
|
|
Опора деревянной одностоечной и способы укрепление угловых опор: Опоры ВЛ - конструкции, предназначенные для поддерживания проводов на необходимой высоте над землей, водой...
Папиллярные узоры пальцев рук - маркер спортивных способностей: дерматоглифические признаки формируются на 3-5 месяце беременности, не изменяются в течение жизни...
Организация стока поверхностных вод: Наибольшее количество влаги на земном шаре испаряется с поверхности морей и океанов (88‰)...
Общие условия выбора системы дренажа: Система дренажа выбирается в зависимости от характера защищаемого...
© cyberpedia.su 2017-2024 - Не является автором материалов. Исключительное право сохранено за автором текста.
Если вы не хотите, чтобы данный материал был у нас на сайте, перейдите по ссылке: Нарушение авторских прав. Мы поможем в написании вашей работы!