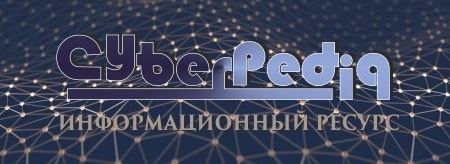
Организация стока поверхностных вод: Наибольшее количество влаги на земном шаре испаряется с поверхности морей и океанов (88‰)...
Поперечные профили набережных и береговой полосы: На городских территориях берегоукрепление проектируют с учетом технических и экономических требований, но особое значение придают эстетическим...
Топ:
Выпускная квалификационная работа: Основная часть ВКР, как правило, состоит из двух-трех глав, каждая из которых, в свою очередь...
Установка замедленного коксования: Чем выше температура и ниже давление, тем место разрыва углеродной цепи всё больше смещается к её концу и значительно возрастает...
Теоретическая значимость работы: Описание теоретической значимости (ценности) результатов исследования должно присутствовать во введении...
Интересное:
Финансовый рынок и его значение в управлении денежными потоками на современном этапе: любому предприятию для расширения производства и увеличения прибыли нужны...
Что нужно делать при лейкемии: Прежде всего, необходимо выяснить, не страдаете ли вы каким-либо душевным недугом...
Аура как энергетическое поле: многослойную ауру человека можно представить себе подобным...
Дисциплины:
![]() |
![]() |
5.00
из
|
Заказать работу |
|
|
ЗАДАНИЕ
Для курсового проектирования по дисциплине «Технология машиностроения» студентаГорбачева Ильи Юрьевича
Специальности 151001 "4"курса группы ТМ-406 Санкт-Петербургского Политехнического колледжа городского хозяйства.
Тема задания: Разработать технологический процесс обработки детали
«Втулка» в условиях среднесерийного производства.
Курсовой проект на указанную тему выполняется в следующем объёме:
Пояснительная записка:
Введение
РАСЧЕТНО - ТЕХНОЛОГИЧЕСКАЯ ЧАСТЬ
1.1. Описание конструкции и назначения детали.
1.2 Технологичность конструкции.
1.3 Характеристика материала.
1.4 Определение годовой программы выпуска.
1.5. Выбор и расчет заготовки.
1.6 Маршрут обработки.
1.6.1 Выбор оборудования.
1.6.2. Определение технологических базовых поверхностей и приспособлений.
1.6.3. Выбор режущего инструмента.
1.6.4. Выбор мерительного инструмента
1.7. Расчет режимов резания
1.8. Нормирование операций
1.9. Расчет управляющей программы для станка с ЧПУ в САПР ADEM-8,0.
КОНСТРУКТОРСКАЯ ЧАСТЬ
2.1. Проектирование и расчет специального приспособления
2.1.1. Описание конструкции и принципа работы приспособления
2.1.2. Расчет усилия зажима
2.1.3. Расчет погрешности базирования
2.2. Расчёт и конструирование режущего инструмента
2.3. Расчёт и конструирование мерительного инструмента
ТЕХНОЛОГИЧЕСКАЯ ДОКУМЕНТАЦИЯ
3.1. Комплект документации операционного технологического процесса обработки детали САПР ADEM-8,0.
Заключение
Литература
Приложение
Графическая часть
1. Чертёж детали.
2. Чертёж заготовки.
3. Чертёж режущего инструмента.
4. Чертеж мерительного инструмента с полями допусков.
|
5. Операционные эскизы с режущим инструментом.
6. Компоновка сборочного чертежа приспособления. Спецификация.
Представление проекта к защите в виде презентации и доклада
Дата выдачи «_06_» _сентября_ 2011 г.
Срок окончания «_10_» _декабря_ 2011 г.
Зав. отделением ____________ /В.А. Грешилова/
Стр. |
Оглавление
Введение. 3
1. ТЕХНОЛОГИЧЕСКАЯ ЧАСТЬ. 4
1.1. Описание конструкции и назначение детали. 4
Рис. 1 Втулка1.2. Технологичность конструкции. 4
1.3. Характеристика материала. 6
1.4. Определение годовой программы выпуска. 7
1.5. Выбор и расчет заготовки с экономическим обоснованием.. 8
1.6. Маршрут обработки. 24
1.6.1. Выбор оборудования с обоснованием.. 27
1.6.2. Определение технологических базовых поверхностей и выбор приспособлений. 31
1.6.3. Выбор мерительного инструмента. 32
1.7. Режимы резания и нормирования операций. 34
1.9. Расчет управляющей программы для станка с ЧПУв САПР ADEM-8,0. 39
2. КОНСТРУКТОРСКАЯ ЧАСТЬ. 42
2.2. Расчёт и конструирование режущего инструмента. 48
2.3. Расчёт и конструирование мерительного инструмента. 50
3. ТЕХНОЛОГИЧЕСКАЯ ДОКУМЕНТАЦИЯ. 51
3.1. Комплект документации маршрутно-операционного технологического процесса обработки детали в САПР ADEM-8,0. 51
Заключение. 52
Литература. 53
Приложение. 54
Введение
В данной пояснительной записке была изучена конструкция и служебное назначение детали «Втулка», проведён анализ технологичности детали.
Выбран материал для изготовления данной детали, а так жеспособ получения заготовки - литье, единственный возможный способ для данного сплава, проведен расчет себестоимости заготовки и выбран наиболее экономичный.
Разработан технологический маршрут механической обработки. Согласно маршруту выбрано оборудование и определены технологические базовые поверхности.
Был произведен расчет припусков на самые точные по требованиям поверхности, а также режимов резания и норм времени.
Спроектирован специальный режущий инструмент – мечик, а также мерительный инструмент – резьбовую пробку.
|
В данном курсовом проекте так же была выполнена управляющая программа на 030 Фрезерно-сверлильную операцию.
Выполнены чертежи (детали,заготовки), мерительного и режущего инструментов, а также полный комплект технологических документов – маршрутная карта, операционные карты и операционные эскизы.
1. ТЕХНОЛОГИЧЕСКАЯ ЧАСТЬ
Характеристика материала
Для изготовления детали “Втулка” применяется Сталь 20 ГОСТ 1050-88
Сталь конструкционная углеродистая качественная. Можно заменить сталью марки 15 и 25. Применение этой стали:
1. Трубы перегревателей.
2. Коллекторов и трубопроводов котлов давления.
3. Листы для штампованных деталей.
4. Цементуемые детали для длительной и весьма длительной службы при температурах до 350 град.
Свариваемость без ограничений
Таблица №1 Химический состав в %
C Углерод | Si Кремний | Mn Марганец | Ni Никель | S Сера | P Фосфор | Cr Хром | Cu Медь | N Азот |
0,17 – 0,24 | 0,17 – 0,37 | 0,35 – 0,65 | До 0,3 | До 0,04 | До 0,0035 | До 0,25 | До 0,3 | До 0,008 |
Таблица №2 Физические свойства
T | E 10-5 | a 106 | l | r | C | R 109 |
Град | МПа | 1/Град | Вт/(м·град) | кг/м3 | Дж/(кг·град) | Ом · м |
2.13 | — | — | — |
T – Температура, при которой получены данные свойства, [Град]
E – Модуль упругости первого рода, [МПа]
a – Коэффициент температурного (линейного) расширения (диапазон 20º - T), [1/Град]
l– Коэффициент теплопроводности (теплоемкость материала), [Вт/(м·град)]
r – Плотность материала, [кг/м3]
C – Удельная теплоемкость материала (диапазон 20º - T), [Дж/(кг·град)]
R – Удельное электросопротивление, [Ом·м]
Таблица №3 Механические свойства
Тип заготовки | Размер | Напр. | SB | ST | d5 | y | KCU | Термообр. | |
- | мм | - | МПа | МПа | % | % | кДж/м2 | - | |
Прокат нагартован. ГОСТ 1050 - 88 | |||||||||
Твердость 20 калиброванногонагартованного, ГОСТ 1050-88 | HB 10-1 = 207 МПа | ||||||||
SB– Предел кратковременной прочности, [МПа]
ST– Предел пропорциональности (предел текучести для остаточной деформации), [МПа]
d5 – Относительное удлинение при разрыве, [%]
y – Относительное сужение, [%]
KCU – Ударная вязкость, [кДж/м2]
HB – Твердость по Бринеллю, [МПа]
Таблица №4 Технологические свойства
Свариваемость: | Без ограничений. |
Флокеночувствительность: | Не чувствительна. |
Склонность к отпускной хрупкости: | Не склонна |
Таблица №5 Типы производств
|
Масса детали,кг | Тип производства | ||||
единичное | мелкосерийное | среднесерийное | крупносерийное | массовое | |
<1 | <20 | 20 – 2000 | 2000 – 20000 | 20000 – 100000 | >100000 |
1,0 – 4,0 | <15 | 15 – 1000 | 1000 – 10000 | 10000 – 75000 | >75000 |
4,0 – 10 | <10 | 10 – 500 | 500 – 5000 | 5000 – 50000 | >50000 |
10 – 20 | <7 | 7 – 250 | 250 – 2500 | 2500 – 25000 | >25000 |
>20 | <5 | 5 – 120 | 120 – 1200 | 1200 – 15000 | >15000 |
Среднесерийное производство характеризуется изготовлением деталей повторяющимися партиями (сериями).
В условиях среднесерийного производства представляется возможным расположить оборудование в последовательности технологического процесса для одной или нескольких деталей, требующих одинакового порядка обработки, со строгим соблюдением принципов взаимозаменяемости при обработке.
При небольшой трудоемкости обработки или недостаточно большой программе выпуска целесообразно обрабатывать заготовки партиями, с последовательным выполнением операций, т.е. после обработки всех заготовок партии на следующей операции. При этом время обработки на различных станках не согласовывается. Заготовки во время работы хранят у станков, а затем транспортируют целой партией.
Количество деталей в партии для одновременного запуска допускается определять упрощенным способом по формуле
([3] стр. 22)
где
N – годовая программа выпуска, шт;
а – периодичность запуска в днях.
рекомендуется периодичность запуска изделий: 3, 6, 12, 24
шт.
Метод – Прокат
Рис. 8Чертёж детали.
Химический состав и характеристики материалаСтали 20 ГОСТ 1050-88смотреть на странице 6
Рис.9 3-D модель детали.
Номинальные значения диаметральных размеров заготовки,соответствующие стандартизованным размерам по сортаменту,определяются по формуле (1) с последующим округлениемразмера до стандартизованного:
D1 = D + 2Z, где (1)
D1 – наружный расчетный диаметр заготовки;
D – наружный диаметр детали по чертежу;
Z – припуск на обработку по наружной поверхности;
Величины припусков в мм Z назначены исходя из следующих соображений:
на
черновую обработку 2,0
|
получистовую 1,0
чистовую 0,5
шлифование 0,2
На основании определенного наружного расчетного диаметра заготовки D1 проводится выбор стандартизованных диаметров заготовки посортаменту.условие: необходимо, чтобы наружный диаметрзаготовки был равен или больше диаметра детали.
1.Определение диаметра прутка:
Исходя из технологического маршрута, диаметр прутка равен:
D1=208+2(2+1+0,5)=208+7=215 мм, по сортаменту подходящий диаметр прутка - 220мм.
По ГОСТ 2590-88 – пруток горячекатаный обычной точности (В).
По ГОСТ 1050-88 - Из стали 20 обыкновенного качества с гарантированными механическими свойствами (М2)
2. Длина заготовки:
L3 = Lд + 2Zподр. (2)
где Lд — номинальная длина детали по рабочему чертежу, мм.
L3= 74+ 4=78 мм
Предельные отклонения на длину заготовки установлены по справочным таблицам. По 14 квалитету для данного изделия 141h14-1
С учетом верхнего предельного отклонения, длина заготовки - 78 мм.
Рис.10 Модель заготовки.
3. Выбор оптимальной длины проката для разделки на заготовки из расчета на некратность. Прокат поставляется длиной 4 и 7 метров.
Потери на зажим заготовки Lзаж приняты 80мм.
Заготовку отрезают на ленточно-пильных станках. Это самый производительный и дешевый способ. Характеристики этого способа резки:
Длину торцового обрезка проката определяем из соотношения
Lоб = (0,3 - 0,5) d, (3)
где d — диаметр сечения заготовки, мм; d = 220 мм:
Lоб = 0,5 • 220 = 66 мм.
Число заготовок, исходя из принятой длины проката определяется по формуле:
мм, где (4)
Lпр-длина проката
Lзаж-длина зажима
Lоб - длина обреза
Lз-длина заготовки
Lрез– ширина реза
Из проката длиною 4 м
шт
Получено47 заготовок из данной длины проката.
Из проката длиною 7 м
шт
Принято83 заготовок из данной длины проката.
Остаток длины (некратность) определяется в зависимости от принятой длины проката:
из проката длиною 4 м
Lнк4=Lпр – (Lз+Lрез)Х4, где (5)
Lнк4-остаток длины, мм
Lпр-длина проката, мм
Lоб-длина обреза, мм
Lз-длина заготовки, мм
Х4-число заготовок, шт
Lнк4= 4000-66-80-(82·47)= 0 мм
Пнк4=(Lнк100)/Lпр (6)
Lнк-остаток длины, мм
Lпр-длина проката, мм
Пнк4=(0·100)/4000=0%
некратность из проката длиною 7 мпо формулам (6;7)
Lнк7=7000-66-80-(82·83)=45 мм
Пнк7=(45·100)/7000= 0,6%
Из расчетов на некратность следует, что прокат длиною 4 м для изготовления заготовок более экономичен, чем прокат длиною7 м. Поэтому для заготовки принят прокат длиной 4 м.
Потери материала на зажим при отрезке по отношению к длине проката составят
Пзаж=(Lзаж·100)/Lпр(7)
Lзаж-длина зажима, мм
Lпр-длина проката, мм
|
Пзаж=(80·100)/4000=2%
Потери материала на длину торцевого обрезка проката в процентах по отношению к длине проката составят
Поб=(Lоб100)/Lпр (8)
Lпр-длина проката, мм
Поб =(66·100)/4000=1,65%
Общие потери (%) к длине выбранного проката
Пп.о=Пнк+Поб+Пзаж(9)
Пнк-остаток длины
Поб- потери материала на длину торцевого обрезка
Пзаж- потери материала на зажим
Пп.о = 0+1,65+2=3,65%
Расход материала на одну деталь с учетом всех технологических неизбежных потерь определяем по формуле:
Gз.п=Gз(100+Пп.о)/100 (10)
Gз-масса заготовки (22,14 кг)
Пп.о- общие потери к длине выбранного проката,
Gз.п =22,14 (100+3,65)/100=80,81 кг.
Коэффициент использования материала определянм по формуле
Ки.м =Gд/Gз.п(11)
Gд – масса детали (см. рис2)
Gз.п - расход материала
Ки.м = 8,9/80,81=0,11
Рис. 11Чертеж заготовки
Технические требования:
1.Число загатовок 47 штук
2.Минимальная значения некратности 9,6 мм
3.HB 1
Маршрут обработки
Рис. 10 Установочные технологические базы (У.Т.Б.)
Содержание операции | Оборудование | Приспособление | Режущий инструмент | Мерительный инструмент | У.Т.Б. |
005 Заготовительная. Заготовительная. Штамповать заготовку по тех. Процессу ОГМет. | - | - | - | - | - |
010 Контрольная. Контролировать размеры заготовки согласно чертежа. | Стол ОТК | - | - | 1.штангенциркуль ШЦ-2-250-0,1 ГОСТ 166-84. | - |
015 Токарная. А. Установить и закрепить заготовку 01. Подрезать торец; 02. Обработка тела вращения Ø208H14; 03. Точит 2 фаски по 1,6×45˚; 04. Расточить отверстия Ø80Н14 на расстоянии35 мм.; 05. Точить фаску 2,5х45º | 16К20 | Патрон 3х кулачковый ГОСТ 2675-80 | 1. Резец проходной отогнутый (BK6) ГОСТ 18879-73 2.Резец расточной (Т15К6) ГОСТ 18880-73 | 1.штангенциркуль ШЦ-2-250-0,1 ГОСТ 166-84; 2.образцы шероховатости ГОСТ 9378-93. | 4;3 |
020 Токарная ЧПУ А. Установить и закрепить деталь 01. Подрезать торец; 02. Обработка тела вращения Ø124H11 на расстояние44 мм.; 03. Прорезанные канавки 2×2 мм 04. Расточить отверстия Ø65H14 на расстояние 39 мм; 05. Расточить отверстия Ø62H14 на расстояние 39 мм.;(черн.) 06. Расточить отверстия Ø63H11 на расстояние 39 мм.; (получит.) 07. Расточить отверстия Ø64H9 на расстояние 39 мм.; (чист.) 08. Точить фаску 1,6х45º | SK40P | Патрон 3х кулачковый ГОСТ 2675-80 | 1.Резец контурный черновой ГОСТ 20872-80 (с пластиной из твёрдого сплава BK6) 3.Резец расточной черновой (Т15К6) СТП 344-74 4.Резец расточной чистовой (Т15К6) СТП 344-74 | 1.штангенциркуль ШЦ-2-250-0,1 ГОСТ 166-84; 2.образцы шероховатости ГОСТ 9378-93. 3.Штангенциркуль ШЦЦО 0-300-0,01 | 1;2 |
030 Фрезерно-сверлильная ЧПУ Установ А: Установить и закрепить деталь. 1.Сверлить последовательно 3сквозных отверстий под резьбу М12-7Н2.Зенковать последовательно 3 фасок 1,6х45º под резьбу М12-7Н; 3.Нарезать резьбу М12-7Н последовательно на 3;(черн.) 4.Нарезать резьбу М12-7Н последовательно на 3;(чист.) 5. Фрезеровать лыску 75±0,1 | 6Р11Ф3-1 | Спец. Приспособление | 1.сверло спиральное с к/хв Ø12 (Т5К10) ГОСТ 22735-77 2.Зенковка Ø 12 мм (Т5К10) ГОСТ 26258-87; 3.Метчик черновой М12 (Т15К6) ГОСТ 17927-72; 4.Метчик чистовой М12 (Т15К6) ГОСТ 17927-72; 5. Фреза концевая (Т15К6) ГОСТ 17026-71 | 1. резьбовой калибр-пробкасборочный М12-7H ГОСТ 14810-69; 2.штангенциркуль ШЦ-2-250-0,1 ГОСТ 166-84; | 1;5:6 |
045 Слесарная. Установ А: Установить и закрепить деталь 1.Зачистить заусенцы, притупить острые кромки. | Верстак | Тиски с призматическими губками и пневмозажимом ГОСТ 16518-96. | Напильник ГОСТ 1465-80 | - | - |
050 Контрольная. | Стол ОТК | - | - | 1.штангенциркуль ШЦ-2-250-0,1 ГОСТ 166-84; 2.образцы шероховатости ГОСТ 9378-93. 3. резьбовой калибр-пробкасборочный М12-7H ГОСТ 14810-69; | - |
Операция 015, 025. Токарная
[15] Выбран токарно-винторезный станок ГС526У-01. Выбор данного станка связан с его простотой и универсальностью, а также из-за его технических характеристик.
В САПР ADEM-8,0
Для создания управляющей программы обработки детали была использована система проектирования ADEMV8.0.модуль CAM,в которую был импортирован чертёж детали из системы Компас-3DV9.При внесении данных об обработке в модуль,CAM программа автоматически выполнила расчет траектории движения инструмента и управляющей программы для станка с ЧПУ.
Модуль подготовки управляющих программ
На станки с ЧПУ - ADEM CAM.
ADEM CAM позволяет задавать технологические переходы как для конструктивных элементовсостоящих из плоских 2D-контуров и 3D моделей, созданных в модуле ADEM CAD, так и дляимпортированных объемных 3D-моделей.
ADEM CAM включает инструменты для редактированиятехнологического маршрута и моделирования процесса обработки.Результатом работы модуля ADEM CAM является, отлаженная в процессе моделирования, управляющая программа для станка с ЧПУ.
Технологические объекты, составляющие технологический процесс обработки, являются ассоциативно связанными с геометрической моделью, созданной в ADEM CAD или импортированной из других систем проектирования. То есть все изменения внесенные конструктором в геометрическую модель проектируемого изделия, автоматически отражаются на технологическом процессе обработки.
Процесс создания технологического объекта на основе созданной или импортированнойгеометрической модели включает следующие стадии:
До начала генерации управляющей программы, был выбран тип оборудования и указан ряд дополнительных параметров.
Рис.14 Эскиз УП для операции 030 «Фрезерно-сверлильная с ЧПУ»
FANK0139.ANK
N000%*
N011M03*
N012G01Y+008000Z+000200F4712*
N013F0450*
N014Z-003200F0520*
N015Z+003200F4724*
N016F0450*
N017X+006928Y-012000F4712*
N018F0450*
N019Z-003200F0520*
N020Z+003200F4724*
N021F0450*
N022X-013856F4724*
N023F0450*
N024Z-003200F0520*
N025Z+003200F4724*
N026F0450*
N027F0000T01*
N028G01X+006928Y+012000F4712*
N029F0450*
N030Z-000360F0520*
N031Z+000360F4724*
N032F0450*
N033X-006928Y-012000F4712*
N034F0450*
N035Z-000360F0520*
N036Z+000360F4724*
N037F0450*
N038X+013856F4724*
N039F0450*
N040Z-000360F0520*
N041Z+000360F4724*
N042F0450*
N043F0000T01*
N044G01X-006928Y+012000F4712*
N045F0450*
N046Z-003200F0520*
N047Z+003200F4724*
N048F0450*
N049X+006928Y-012000F4712*
N050F0450*
N051Z-003200F0520*
N052Z+003200F4724*
N053F0450*
N054X-013856F4724*
N055F0450*
N056Z-003200F0520*
N057Z+003200F4724*
N058F0450*
N059F0000T01*
N060G01X+006928Y+012000F4712*
N061F0450*
N062Z-003200F0520*
N063Z+003200F4724*
N064F0450*
N065X+006928Y-012000F4712*
N066F0450*
N067Z-003200F0520*
N068Z+003200F4724*
N069F0450*
N070X-013856F4724*
N071F0450*
N072Z-003200F0520*
N073Z+003200F4724*
N074F0450*
N075F0000T01*
N076G01X+006928Y+004000F4712*
N077F0450*
N078X-007205Y-009100F4712*
N079F0450*
N080Z-003000F4724*
N081F0450*
N082Z-000200F0520*
N083Y+000100*
N084X+014410*
*
Программа выполняется - 25.08мин;
Длина управляющей программы 3,36м
N-номеркадра
G17-Переключение рабочих плоскостей (XY, XZ, YZ)
G01-линейная интерполяция
М03-Управление вращением шпинделя
X,Y,Z-координаты перемещения
F-скорость рабочей подачи
2. КОНСТРУКТОРСКАЯ ЧАСТЬ
2.1. Проектирование и расчет специального приспособления
При изготовлении детали «Фланец» на операции 030 Сверлильная используется специальное приспособление.
Использование специального приспособления позволит:
2.1.1. Описание конструкции и принципа работы приспособления
Согласно маршрута обработки на операции 030 Фрезерно-сверлильная,требуется сверлить группу из 3 отверстий Ø12 мм, выдерживая размер 30±0,1 мм.Операция будет выполняться на радиально-сверлильном станке 2М55.
В соответствии с принятой схемой базирования (см. п. 1.6.2) заготовка в приспособлении будет базироваться по плоскости и отверстию.
Принятая схема базирования реализована в станочном приспособлении следующим образом (рис. 2.3 Компоновка сборочного чертежа приспособления).
Рис. 15 Компоновка сборочного чертежа приспособления
В качестве зажимного устройства в станочном приспособлении используются быстросменная шайба (поз.18), и гайка (поз.15), которые будут приводиться в движение пневмокамерой двухстороннего действия.
При подаче сжатого воздуха в штоковую полость пневмокамеры, шток (поз.10) перемещается вниз, тянет за собой быстросменную шайбу (поз.18) и гайку (поз.15), зажимное устройство вместе со штоком (поз.10) будет перемещаться вниз и зажимать заготовку.
При подаче сжатого воздуха в бесштоковую полость пневмокамеры, шток (поз.10) и зажимное устройство перемещаются вверх, разжимая заготовку.
При выборе зажимного устройства приспособления следует руководствоваться следующим требованиям:
При зажиме не изменять первоначально заданное положение заготовки.
Сила зажима должна обеспечивать надежное закрепление детали и не допускать сдвига, поворота и вибрации заготовки при обработке на станке.
Зажим и открепление заготовки производится с минимальной затратой сил и времени рабочего.
Зажимной механизм должен быть простым по конструкции, компактным, максимально удобным и безопасным в работе (min габаритные размеры и число съемных деталей; устройство управления зажимным механизмом должно располагаться со стороны рабочего).
Зажимное устройство в приспособлении будет приводиться в движение при помощи диафрагменной пневмокамеры. Это устройство иногда называют пневмозажимным устройством.
Диафрагменная пневматическаякамерапредставляет собой замкнутыйобъем, разделенный эластичной диафрагмой на две изолированные друг от друга полости. Рабочий и возвратный ходыштока происходят от нажима диафрагмы, прогибающейся под действием сжатого воздуха.
Диафрагменная пневматическаякамерадвухстороннего действия- рабочие полости в сдвоенном исполнении. Их наиболее целесообразно применять встроенными в корпус оснастки, имеющей развитое основание. Как прикрепляемые или универсальные они громоздки и плохо компонуются с приспособлениями. Они значительно проще поршневых по конструкции и изготовлению. На них меньше сказывается плохое качество воздуха.
Диафрагменные пневмокамеры целесообразно применять в неответственных системах, где достаточно малого хода штока и где необходимо создать значительные зажимные усилия, не прибегая к помощи усилителей.
По условиям техники безопасности применение диафрагменных двигателей недопустимо, когда неожиданный прорыв диафрагмы вызывает мгновенное раскрепление зажимов приспособления, что может привести к несчастному случаю.
Преимуществапневмокамер:
простота конструкции и эксплуатации
ход поршня может быть любой величины, необходимой для работы механизма
быстрота действия – 0,6 – 1,5 с.
Недостаткипневмокамер:
диаметральные размеры больше осевых
падения усилия по длине хода штока
малый ход поршня
низкое давление рабочей среды (воздуха) ограничивает область использования
возможность мгновенного падения зажимного усилия до нуля при разрыве диафрагмы
непостоянство зажимного усилия, которое уменьшается по мере прогиба диафрагмы
2.1.2. Расчет усилия зажима
Рис.16 Схема зажима
Q – сила зажима, Н
Ро - осевая сила резания, Н
W – тянущее усилие на штоке, Н
Мкр – момент крутящий, Н мм
D; d– размеры опорной поверхности заготовки, мм
При данной схеме базирования сила зажима будет равна силе резания.
([4]стр.42)
Р = Рт/КРм, Н ([2.4],стр.136, карта 50, лист 1) (2.1)
где,
Рт - осевая сила резания табличная, Н ([2.4],стр.136, карта 50, лист 1)
Kрм-механические свойства обрабатываемого материала0,9 ([2.4],стр.143, карта 53, лист 1]
Табличная осевая сила
Рт = 645 Н
Принятая осевая сила
Р=645,0/0,9 =716 Н
Окончательно осевая сила
Р=716 Н
Р=Q=716 Н
Заключение
В результате разработки курсового проекта на деталь «Фланец» при годовой программе 2000 шт., был разработан технологический процесс обработки детали. При составлении технологического процесса оценены и выбраны наименее трудоёмкие и дешёвые способы изготовления «Фланца».
Путём анализа методов получения заготовки и способов получения готовой детали, выбрано оборудование; выбран и рассчитан режущий, мерительный инструмент и специальное приспособление.
В процессе проектирования произведены все необходимые расчеты, связанные назначением припусков, определением режимов резания и норм времени на обработку.
При выполнении курсового проекта использовались современные системы автоматизированного производства САПР ADEM 8/0 CAD/CAM/CAPP, САПР «КОМПАС -3D» используемые для разработки конструкторской, технологической документации и программирования станков ЧПУ.
Литература
1. Антонюк В.Е. «Справочник конструктора», М.: «Машиностроение», 2009 г.
5. Горбацевич А. Ф., Шкред В. А. Курсовое проектирование по технологии машиностроения: Учебное пособие для вузов. — 5-е издание, стереотипное. Перепечатка с четвертого издания 1983 г. - М.: ООО ИД «Альянс»,2007. -
6. Данилевский В.В. «Справочник молодого технолога-машиностроителя»,М.: «Высшая школа», 2008 г.
7. Дзюбандовский К.А. «Пневматические приспособления. Проектирование и эксплуатация»,М.: «Машиностроение», 2006г.
8. Добрыднев И.С. Курсовое проектирование по предмету «технология машиностроения».М.: «Машиностроение», 2009г.
12. «Общие машиностроительные нормативы времени», изд.2-е, М.: «Машиностроение», 2008г.
13. Нефедов Н.А. «Сборник задач и примеров по резанью металлов и режущему инструменту», М.: «Машиностроение», 2006 г.
14. Силантьева Н.А., Малиновский В.Р. «Техническое нормирование труда в машиностроении». - 2-е изд., перераб. и доп. – М.: Машиностроение, 2010 г.
15. Паспорт станка модели ГС526У-01
16. Паспорт станка модели L41 CNC
17. Паспорт станка модели 2М55Ф2
18. Шатилов А.А. «Станочные приспособления -справочник.» Т1,М.: «Машиностроение»,2008г.
19. http://ru.wikipedia.org –Интернет энциклопедия
Приложение
Графическая часть
1. Чертёж детали
обозначение чертежа ПКГХ.151001.ТМ-406. № по списку.01.КП.
2. Чертёж заготовки.
обозначение чертежа ПКГХ.151001.ТМ-406. № по списку.02.КП.
3. Операционные эскизы с режущим инструментом. – 3 листа
обозначение чертежа ПКГХ.151001.ТМ-406. № по списку.03.КП.
4. Чертёж режущего инструмента.
обозначение чертежа ПКГХ.151001.ТМ-406. № по списку.04.КП.
5. Чертеж мерительного инструмента с полями допусков.
ПКГХ.151001.ТМ-406. № по списку.05.КП.
6. Компоновка сборочного чертежа приспособления.
обозначение чертежа ПКГХ.151001.ТМ-406. № по списку.06.СБ.КП.
Спецификация
обозначение чертежа ПКГХ.151001.ТМ-406. № по списку. КП.
ЗАДАНИЕ
Для курсового проектирования по дисциплине «Технология машиностроения» студентаГорбачева Ильи Юрьевича
Специальности 151001 "4"курса группы ТМ-406 Санкт-Петербургского Политехнического колледжа городского хозяйства.
Тема задания: Разработать технологический процесс обработки детали
«Втулка» в условиях среднесерийного производства.
Курсовой проект на указанную тему выполняется в следующем объёме:
Пояснительная записка:
Введение
РАСЧЕТНО - ТЕХНОЛОГИЧЕСКАЯ ЧАСТЬ
1.1. Описание конструкции и назначения детали.
1.2 Технологичность конструкции.
1.3 Характеристика материала.
1.4 Определение годовой программы выпуска.
1.5. Выбор и расчет заготовки.
1.6 Маршрут обработки.
1.6.1 Выбор оборудования.
1.6.2. Определение технологических базовых поверхностей и приспособлений.
1.6.3. Выбор режущего инструмента.
1.6.4. Выбор мерительного инструмента
1.7. Расчет режимов резания
1.8. Нормирование операций
1.9. Расчет управляющей программы для станка с ЧПУ в САПР ADEM-8,0.
КОНСТРУКТОРСКАЯ ЧАСТЬ
2.1. Проектирование и расчет специального приспособления
2.1.1. Описание конструкции и принципа работы приспособления
2.1.2. Расчет усилия зажима
2.1.3. Расчет погрешности базирования
2.2. Расчёт и конструирование режущего инструмента
2.3. Расчёт и конструирование мерительного инструмента
|
|
Общие условия выбора системы дренажа: Система дренажа выбирается в зависимости от характера защищаемого...
Индивидуальные очистные сооружения: К классу индивидуальных очистных сооружений относят сооружения, пропускная способность которых...
Поперечные профили набережных и береговой полосы: На городских территориях берегоукрепление проектируют с учетом технических и экономических требований, но особое значение придают эстетическим...
Таксономические единицы (категории) растений: Каждая система классификации состоит из определённых соподчиненных друг другу...
© cyberpedia.su 2017-2024 - Не является автором материалов. Исключительное право сохранено за автором текста.
Если вы не хотите, чтобы данный материал был у нас на сайте, перейдите по ссылке: Нарушение авторских прав. Мы поможем в написании вашей работы!