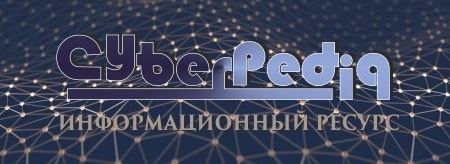
Архитектура электронного правительства: Единая архитектура – это методологический подход при создании системы управления государства, который строится...
Историки об Елизавете Петровне: Елизавета попала между двумя встречными культурными течениями, воспитывалась среди новых европейских веяний и преданий...
Топ:
Оценка эффективности инструментов коммуникационной политики: Внешние коммуникации - обмен информацией между организацией и её внешней средой...
Определение места расположения распределительного центра: Фирма реализует продукцию на рынках сбыта и имеет постоянных поставщиков в разных регионах. Увеличение объема продаж...
Методика измерений сопротивления растеканию тока анодного заземления: Анодный заземлитель (анод) – проводник, погруженный в электролитическую среду (грунт, раствор электролита) и подключенный к положительному...
Интересное:
Принципы управления денежными потоками: одним из методов контроля за состоянием денежной наличности является...
Как мы говорим и как мы слушаем: общение можно сравнить с огромным зонтиком, под которым скрыто все...
Инженерная защита территорий, зданий и сооружений от опасных геологических процессов: Изучение оползневых явлений, оценка устойчивости склонов и проектирование противооползневых сооружений — актуальнейшие задачи, стоящие перед отечественными...
Дисциплины:
![]() |
![]() |
5.00
из
|
Заказать работу |
|
|
В системе железо — углерод существуют следующие фазы: жидкая фаза, феррит, аустенит, цементит, графит.
1. Жидкая фаза. В жидком состоянии железо хорошо растворяет углерод в любых пропорциях с образованием однородной жидкой фазы.
2. Феррит — Твёрдый раствор внедрения углерода в α-железе с ОЦК (объёмно-центрированной кубической) решёткой.
Феррит имеет переменную предельную растворимость углерода: минимальную — 0,006 % при комнатной температуре (точка Q), максимальную — 0,02 % при температуре 700 °C (точка P). Атомы углерода располагаются в центре грани или (что кристаллогеометрически эквивалентно) на середине рёбер куба, а также в дефектах решетки.
При температуре выше 1392 °C существует высокотемпературный феррит, с предельной растворимостью углерода около 0,1 % при температуре около 1500 °C (точка I)
Свойства феррита близки к свойствам чистого железа. Он мягок (твердость — 130 НВ) и пластичен, магнитен (при отсутствии углерода) до 770 °C.
3. Аустенит (γ) — твёрдый раствор внедрения углерода в γ-железе с ГЦК (гране-центрированной кубической) решёткой.
Атомы углерода занимают место в центре гранецентрированной кубической ячейки.
Предельная растворимость углерода в аустените — 2,14 % при температуре 1147 °C (точка Е).
Аустенит имеет твёрдость 200—250 НВ, пластичен, парамагнитен.
При растворении других элементов в аустените или в феррите изменяются свойства и температурные границы их существования.
4. Цементит (Fe3C) — химическое соединение железа с углеродом (карбид железа), со сложной ромбической решёткой, содержит 6,67 % углерода. Он твёрдый (свыше 1000 HВ), и очень хрупкий. Цементит фаза метастабильная и при длительным нагреве самопроизвольно разлагается с выделениемграфита.
|
В железоуглеродистых сплавах цементит как фаза может выделяться при различных условиях:
· — цементит первичный (выделяется из жидкости),
· — цементит вторичный (выделяется из аустенита),
· — цементит третичный (из феррита),
· — цементит эвтектический и
· — эвтектоидный цементит.
Цементит первичный выделяется из жидкой фазы в виде крупных пластинчатых кристаллов. Цементит вторичный выделяется из аустенита и располагается в виде сетки вокруг зёрен аустенита (после эвтектоидного превращения они станут зёрнамиперлита). Цементит третичный выделяется из феррита и в виде мелких включений располагается у границ ферритных зёрен.
Эвтектический цементит наблюдается лишь в белых чугунах. Эвтектоидный цементит имеет пластинчатую форму и является составной частью перлита.
Цементит может при специальном сфероидизируюшем отжиге или закалке с высоким отпуском выделяться в виде мелких сфероидов.
Влияние на механические свойства сплавов оказывает форма, размер, количество и расположение включений цементита, что позволяет на практике для каждого конкретного применения сплава добиваться оптимального сочетания твёрдости, прочности, стойкости к хрупкому разрушению и т. п.
5. Графит — фаза состоящая только из углерода со слоистой гексагональной решёткой. Плотность графита (2,3) много меньше плотности всех остальных фаз (около 7,5 — 7,8) и это затрудняет и замедляет его образование, что и приводит к выделению цементита при более быстром охлаждении. Образование графита уменьшает усадку при кристаллизации, графит выполняет роль смазки при трении, уменьшая износ, способствует рассеянию энергии вибраций.
Графит имеет форму крупных крабовидных (изогнутых пластинчатых) включений (обычный серый чугун) или сфероидов (высокопрочный чугун).
Графит обязательно присутствует в серых чугунах и их разновидности — высокопрочных чугунах. Графит присутствует также и в некоторых марках стали — в графитизированных сталях.
|
3.Сварные соединения и швы,их классификация.
Сварные швы и соединения
Сварной шов – это закристаллизовавшийся металл, который в процессе сварки находился в расплавленном состоянии.
Сварное соединение – ограниченный участок конструкции, содержащий один или несколько сварных швов.
Виды сварных швов
В зависимости от формы сечения сварные швы могут быть
Виды сварных швов приведены на рисунке ниже.
Рисунок. Сварные швы: стыковой, угловой и прорезной.
Виды сварных соединений
В зависимости от характера сопряжения свариваемых деталей различают следующие виды сварных соединений:
Стыковым соединением называется сварное соединение двух элементов, примыкающих друг к другу торцевыми поверхностями и размещенных на одной поверхности или в одной плоскости. Основные виды стыковых сварных соединений представлены на рисунке ниже.
Рисунок. Стыковые сварные соединения: без скоса кромок, с криволинейным скосом кромок, с V-образным скосом кромок, с X-образным скосом кромок.
Угловым соединением называется сварное соединение двух элементов, размещенных под углом и сваренных в месте примыкания их краев.
Тавровым соединением называется такое сварное соединение, в котором торец одного элемента примыкает под углом и присоединен к боковой поверхности другого элемента.
Основные виды угловых и тавровых сварных соединений продемонстрированы на рисунке ниже.
Рисунок. Угловые и тавровые сварные соединения: без скоса кромок, со скосом одной кромки, с двумя скосами одной кромки.
Нахлесточным соединением называется сварное соединение параллельно размещенных и частично перекрывающихся элементов.
Торцовым соединением называется такое сварное соединение, в котором боковые поверхности элементов примыкают друг к другу.
Рисунок. Нахлесточные сварные соединения без скоса кромок и торцовые сварные соединения.
Билет№16
1.Сущность и назначение термообработки.Виды термообработки.Термическая обработка заключается в нагревании деталей по определенному режиму до заданной температуры, выдержке при этой температуре, а затем охлаждении с определенной скоростью. В случае обработки холодом, т. е. при отрицательных температурах, процесс состоит в охлаждении деталей в камере холода с некоторой скоростью, выдержке при заданной отрицательной температуре и нагревании до комнатной температуры. Таким образом, режим термической обработки определяется совокупностью ряда факторов — температурой и скоростью нагрева или охлаждения, продолжительностью выдержки при заданной температуре.
|
2. Подготовка деталей под сварку, виды и операции.
Подготовка поверхности металла под сварку. При подготовке деталей под сварку поступающий металл подвергается правке, разметке, наметке, резке, подготовке кромок под сварку, холодной или горячей гибке.
Металл правят либо вручную, либо на различных листоправильных вальцах. Ручную правку выполняют на чугунных или стальных правильных плитах ударами кувалды или с помощью ручного винтового пресса. Угловая сталь правится на правильных вальцах (прессах), двутавры и швеллеры - на приводных или ручных правильных прессах.
Разметка и наметка - это такие операции, которые определяют конфигурацию будущей детали. Механическая резка применяется для прямолинейного реза листов, а иногда для криволинейного реза листов с использованием для этой цели роликовых ножниц с дисковыми ножами. Углеродистые стали разрезают газокислородной и плазменно-дуговой резкой. Эти способы могут быть ручными и механизированными. Для резки легированных сталей, цветных металлов может применяться газофлюсовая или плазменно-дуговая резка.
Основной металл и присадочный материал перед сваркой должны быть тщательно очищены от ржавчины, масла, влаги, окалины и различного рода неметаллических загрязнений. Наличие указанных загрязнений приводит к образованию в сварных швах пор, трещин, шлаковых включений, что приводит к снижению прочности и плотности сварного соединения.
Подготовка кромок под сварку. К элементам геометрической формы подготовки кромок под сварку (рис. 25) относятся угол разделки кромок α, притупление кромок S, длина скоса листа L при наличии разности толщин металла, смещение кромок относительно друг друга б, зазор между стыкуемыми кромками а.
|
Рис. 25. Элементы геометрической формы подготовки кромок под сварку (а) и шва (б):
в - ширина шва, h - высота шва, К - катет шва
Угол разделки кромок выполняется при толщине металла более 3 мм, поскольку се отсутствие (разделки кромок) может привести к непровару по сечению сварного соединения, а также к перегреву и пережогу металла; при отсутствии разделки кромок для обеспечения провара электросварщик должен увеличивать величину сварочного тока.
Разделка кромок позволяет вести сварку отдельными слоями небольшого сечения, что улучшает структуру сварного соединения и уменьшает возникновение сварочных напряжений и деформаций.
Зазор, правильно установленный перед сваркой, позволяет обеспечить полный провар по сечению соединения при наложении первого (корневого) слоя шва, если подобран соответствующий режим сварки.
Длиной скоса листа регулируется плавный переход от толстой свариваемой детали к более тонкой, устраняются концентраторы напряжений в сварных конструкциях.
Притупление кромок выполняется для обеспечения устойчивого ведения процесса сварки при выполнении корневого слоя шва. Отсутствие притупления способствует образованию прожогов при сварке.
Смещение кромок создает дополнительные сварочные деформации и напряжения, тем самым ухудшая прочностные свойства сварного соединения. Смещение кромок регламентируется либо ГОСТами, либо техническими условиями. Кроме того, смещение кромок не позволяет получать монолитного сварного шва по сечению свариваемых кромок.
ГОСТ 5264-80 предусматривает для стыковых соединений формы подготовленных кромок, представленные на рис. 26; для угловых соединений - на рис. 27; тавровых – на рис. 28 и нахлесточных - на рис. 29.
Рис. 26. Форма подготовленных кромок под сварку для стыковых соединений
Рис. 27. Форма подготовленных кромок под сварку для угловых соединений
Рис. 28. Форма подготовленных кромок под сварку для тавровых соединений
Рис. 29. Форма подготовленных кромок под сварку для нахлесточных соединений
Подготовку кромок под сварку выполняют на механических станках - токарных (обработка торцов труб), фрезерных, строгальных - обработка листов и т. д., а также применением термической резки. Листы, трубы, изготовленные из углеродистых сталей, обрабатываются газокислородной резкой. В качестве горючих газов могут служить ацетилен, пропан, коксовый газ и т. д. Цветные металлы, а также нержавеющие стали обрабатываются плазменной резкой.
Перед сваркой особо ответственных конструкций торцы труб или листов после газокислородной резки обрабатывают дополнительно механическим путем; это делается для того, чтобы избежать каких-либо включений в металле.
Требования к сборке металлических деталей перед сваркой. Применяемые сборочно-сварочные приспособления должны обеспечивать доступность к местам установки деталей и прихваток, к рукояткам фиксирующих и зажимных устройств, а также к местам сварки. Эти приспособления должны быть также достаточно прочными и жесткими, обеспечивать точное закрепление деталей в нужном положении и препятствовать их деформированию в процессе сварки. Кроме того, сборочно-сварочные приспособления должны обеспечивать наивыгоднейший порядок сборки и сварки: наименьшее число поворотов при наложении прихваток и сварных швов; свободный доступ для проверки размеров изделий и их легкий съем после изготовления; безопасность сборочно-сварочных работ.
Любая сборочная операция не должна затруднять выполнение следующей операции. Поступающие на сборку детали должны быть тщательно проверены; проверке подлежат все геометрические размеры детали и подготовленная форма кромок под сварку.
Сборка сварных конструкций, как правило, осуществляется либо по разметке, либо с помощью шаблонов, упоров, фиксаторов или специальных приспособлений - кондукторов, облегчающих сборочные операции. Подготовку и сборку изделий под сварку выполняют с соблюдением следующих основных обязательных правил:
притупление кромок и зазоры между ними должны быть равномерными по всей длине;
кромки элементов, подлежащих сварке, и прилегающие к ним места шириной 25-30 мм от торца кромки должны быть высушены, очищены от грата после резки, масла, ржавчины и прочих загрязнений;
во избежание деформаций прихватку следует выполнять качественными электродами через интервал не более 500 мм при длине одной прихватки 50-80 мм;
для обеспечения нормального и качественного формирования шва нужно в начале и в конце изделия прихватывать планки.
|
3.Классификация сверлильных и расточных станков..
Сверлильные (вертикально сверлильные, одношпиндельные, многошпиндельные, горизонтально сверлильные, радиально сверлильные)Основные типы сверлильно-расточных станков следующие: вертикально-сверлильные одно- и многошпиндельные; радиально-сверлильные; горизонтально-сверлильные для глубокого сверления и горизонтально-центровальные. Сверлильные и расточные станки. Характерным признаком станков этой группы является главное вращательное движение инструмента. Поступательное движение подачи могут осуществлять как заготовка, так и инструмент. Станки предназначены в основном для обработки отверстий.Сверлильно-расточные станки по классификатору отнесены к группе, внутри которой их делят на следующие типы:1 — вертикально-сверлильные; 2 — одношпиндельные полуавтоматы; 3 — многошпиндельные полуавтоматы; 4 — координатно-расточные; 5 — радиально-сверлильные; 6 — горизонтально-расточные; 7 — алмазно-расточные; 8 — горизонтально-сверлильные; 9 — разные сверлильные.
Билет№17
1.Краткие характеристики видов химико-термической обработки..
Химико-термическая обработка (ХТО) стали — совокупность операций термической обработки с насыщением поверхности изделия различными элементами (углерод, азот, алюминий, кремний, хром и др.) при высоких температурах. Химико-термическая обработка повышает твердость, износостойкость, кавитационную, коррозионную стойкость. Химико-термическая обработка, создавая на поверхности изделий благоприятные остаточные напряжения сжатия, увеличивает надежность, долговечность. Цементация стали — химико-термическая обработка поверхностным насыщением малоуглеродистой (С<0,2%) или легированных сталей при температурах 900…950°С — твердым (цементация твердым карбюризатором), а при 850…900°С — газообразным (газовая цементация) углеродом с последующей закалкой и отпуском. Цель цементации и последующей термической обработки — повышение твердости, износостойкости, также повышением пределов контактной выносливости поверхности изделия при вязкой сердцевине.Азотирование стали — химико-термическая обработка поверхностным насыщением стали азотом путем длительной выдержки ее при нагреве до б00…650°С в атмосфере аммиака NН3. Азотированные стали обладают очень высокой твердостью (азот образует различные соединения с железом, алюминием, хромом и другими элементами, обладающие большей твердостью, чем карбиды). Азотированные стали обладают повышенной сопротивляемостью коррозии в таких средах, как атмосфера, вода, пар.
2.Источники питания сварочной дуги.Их классификация.
|
|
Особенности сооружения опор в сложных условиях: Сооружение ВЛ в районах с суровыми климатическими и тяжелыми геологическими условиями...
История развития пистолетов-пулеметов: Предпосылкой для возникновения пистолетов-пулеметов послужила давняя тенденция тяготения винтовок...
Эмиссия газов от очистных сооружений канализации: В последние годы внимание мирового сообщества сосредоточено на экологических проблемах...
Организация стока поверхностных вод: Наибольшее количество влаги на земном шаре испаряется с поверхности морей и океанов (88‰)...
© cyberpedia.su 2017-2024 - Не является автором материалов. Исключительное право сохранено за автором текста.
Если вы не хотите, чтобы данный материал был у нас на сайте, перейдите по ссылке: Нарушение авторских прав. Мы поможем в написании вашей работы!