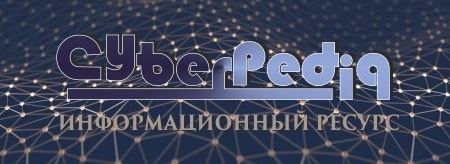
Эмиссия газов от очистных сооружений канализации: В последние годы внимание мирового сообщества сосредоточено на экологических проблемах...
Индивидуальные очистные сооружения: К классу индивидуальных очистных сооружений относят сооружения, пропускная способность которых...
Топ:
Устройство и оснащение процедурного кабинета: Решающая роль в обеспечении правильного лечения пациентов отводится процедурной медсестре...
Отражение на счетах бухгалтерского учета процесса приобретения: Процесс заготовления представляет систему экономических событий, включающих приобретение организацией у поставщиков сырья...
Теоретическая значимость работы: Описание теоретической значимости (ценности) результатов исследования должно присутствовать во введении...
Интересное:
Распространение рака на другие отдаленные от желудка органы: Характерных симптомов рака желудка не существует. Выраженные симптомы появляются, когда опухоль...
Как мы говорим и как мы слушаем: общение можно сравнить с огромным зонтиком, под которым скрыто все...
Наиболее распространенные виды рака: Раковая опухоль — это самостоятельное новообразование, которое может возникнуть и от повышенного давления...
Дисциплины:
![]() |
![]() |
5.00
из
|
Заказать работу |
|
|
Требования к источникам питания для дуговой сварки
Важными параметрами процесса сварки являются вольт-амперная характеристика сварочной дуги и внешняя характеристика источника питания. От их согласования во многом зависят устойчивость горения дуги и стабильность протекания процесса сварки.
На рис.1 показаны вольт-амперные характеристики дуги, представляющие собой зависимость между напряжением UД и током IДпри различной длине дуги l (l2 > l1). Вольт-амперная характеристика дуги нелинейна, поскольку в общем случае электрический ток в газах не подчиняется закону Ома (дуга является электрическим разрядом в газе, и ее сопротивление не равняется постоянной величине).
Рис.1 Вольт-амперные характеристики дуги
При малых токах (примерно до 100А) с его увеличением интенсивно возрастают степень ионизации и число заряженных частиц. Сопротивление столба дуги уменьшается, и для поддержания тока необходимо меньшее напряжение.
При возрастании тока увеличение степени ионизации происходит медленнее, рост количества носителей заряда уменьшается, и напряжение дуги становится мало зависящим от тока.
При больших плотностях тока степень ионизации высокая, дуга не расширяется, так как ограничена диаметром электрода, и ее сопротивление становится постоянным. На этом участке она подчиняется закону Ома - ток и напряжение прямо пропорциональны.
Для каждого способа сварки наиболее характерен свой участок характеристики дуги. Например, при ручной сварке покрытыми электродами и неплавящимся электродом в среде аргона сила тока относительно невелика, а диаметр электрода значителен. Эти условия соответствуют подающему участку характеристики дуги. При сварке под флюсом сила тока больше, чем при ручной сварке, поэтому характеристика переходит на пологий и частично на возрастающий участок. Сварка в углегислом газе характеризуется применением проволок малого диаметра, что пропорционально квадрату диаметра увеличивает плотность тока. Характеристика дуги становится возрастающей.
|
Рассмотрим особенности выбора внешней характеристики источника питания для различных способов сварки.
Ручная дуговая сварка
Одна из основных особенностей ручной сварки - частое изменение длины дуги. Оно связано с манипуляцией сварщиком электродом, его плавлением и необходимостью подачи электрода вниз, а также выполнением швов в неудобных и труднодоступных местах. Особенно частые колебания длины дуги возникают при недостаточной квалификации сварщика. Для обеспечения стабильности процесса сварки, требуемой глубины проплавления и хорошего качества шва необходимо, чтобы сила тока при колебаниях длины дуги изменялась минимально.
Если при ручной дуговой сварке использовать источник питания с пологопадающей характеристикой, то при удлинении дуги возможен ее обрыв из-за малого тока, а при укорочении дуги возможен прожог из-за чрезмерно большой силы тока. Поэтому при ручной сварке применяются источники питания с крутопадающей характеристикой, обеспечивающей максимальную стабильность процесса сварки.
Полуавтоматическая сварка
Особенностью полуавтоматической сварки является постоянная, независимая от сварщика скорость подачи сварочной проволоки. Для обеспечения устойчивого процесса сварки необходимо обеспечить постоянство длины дуги. В противном случае возможен обрыв дуги или короткое замыкание проволоки на изделие. Для обеспечения постоянства длины дуги необходимо, чтобы в процессе сварки соблюдалось соотношение:
Vпод = Vпл | |
где: | Vпод - скорость подачи сварочной проволоки; Vпл - скорость плавления сварочной проволоки. |
Характеристика источника питания должна быть такой, чтобы при случайном нарушении этого соотношения она позволяла вернуться к его соблюдению в максимально короткие сроки.
|
Рассмотрим, что происходит при механизированной сварке при неожиданном увеличении или уменьшении длины дуги. На рис.2 изображена возрастающая характеристика дуги при различной ее длине l, l1, l2, а также жесткая характеристика источника питания. При увеличении длины дуги рабочая точка О перемещается в O1 и сила тока уменьшается - I1. После уменьшения силы тока снижается количество теплоты, выделяемой в дуге, и скорость плавления проволоки уменьшается. В этот период времени скорость подачи проволоки становится больше скорости плавления: Vпод> Vпл. Конец проволоки приближается к изделию, и длина дуги самостоятельно восстанавливается. Этот процесс называется саморегулированием длины дуги.
Процесс сварки будет стабильным, если реакция по изменению скорости плавления проволоки после изменения длины дуги будет быстрой. В этом случае говорят, что процесс саморегулирования проходит активно.
Рассмотрим, как влияет на активность саморегулирования вид внешней характеристики источника питания. На рис.3 приведены три различные характеристики источников питания: пологопадающая (П), жесткая (Ж),возрастающая (В).
Наиболее резкие колебания силы тока, обеспечивающие активное саморегулирование, будут при возрастающей характеристике источника питания, при жесткой характеристике саморегулирование происходит менее активно, еще менее активно оно будет происходить при пологопадающей характеристике. Поэтому если проволока при сварке подается относительно медленно, возможно использование пологопадающих или жестких характеристик. Это обычно бывает при сварке под флюсом, когда диаметры проволок достаточно большие и скорости их подачи относительно невелики и колеблются в пределах 50-200 м/ч. При сварке в углекислом газе диаметры проволок ниже, поэтому для обеспечения высокой производительности их скорости подачи выше - до 400 м/ч. В этом случае обязательно применение жестких характеристик. При сварке на форсированных режимах при очень высоких скоростях подачи проволоки возможно применение источников питания с возрастающими характеристиками.
Источники питания с крутопадающими характеристиками, предназначенные для ручной полуавтоматической и автоматической сварки, применяться не могут, так как не обеспечивают саморегулирования длины дуги и стабильность процесса сварки.
|
Кроме принципа саморегулирования в некоторых сварочных аппаратах используется принцип автоматического регулирования длины дуги. Он заключается в том, что в процессе сварки скорость подачи проволоки не постоянна, а изменяется в зависимости от длины дуги, а следовательно, и напряжения на ней. Управление скоростью подачи проволоки осуществляется за счет обратной связи между дугой и двигателем подающего механизма.
Источники питания сварочной дуги классифицируются по следующим основнымпризнакам:
По роду сварочного тока источники питания сварочной дуги бывают переменного и постоянного тока. К источникам переменного тока относятся сварочные трансформаторы и генераторы повышенной частоты. Источниками постоянного тока являются сварочные преобразователи и сварочные выпрямители.
По виду внешних вольт-амперных характеристик источники питания сварочной дуги бывают с пологопадающей характеристикой, применяемой в основном при автоматической сварке под флюсом; с жесткой и возрастающей вольт-амперной характеристикой, применяемой при сварке в защитных газах и электрошлаковой сварке; с крутопадающей вольт-амперной характеристикой, используемой при ручной дуговой сварке. Бывают источники питания сварочной дуги и универсальные, т. е. обеспечивающие получение в нужный момент соответствующей вольт-амперной характеристики: крутопадающей, пологопадающей, жесткой или возрастающей.
По количеству используемых сварочных дуг источники питания могут быть однопостовыми или многопостовыми.
По способу установки источники питания сварочной дуги бывают стационарными или подвижными - переносными.
3.Ковка и штамповка. Сущность процессов, оборудование.
Штамповка (штампование) — процесс пластической деформации материала с изменением формы и размеров тела. Чаще всего штамповке подвергаются металлы или пластмассы. Существуют два основных вида штамповки — листовая и объёмная. Листовая штамповка подразумевает в исходном виде тело, одно из измерений которого пренебрежимо мало по сравнению с двумя другими (лист до 6 мм). Примером листовой штамповки является процесс пробивания листового металла, в результате которого получают перфорированный металл (перфолист). В противном случае штамповка называется объёмной. Для процесса штамповки используются прессы — устройства, позволяющие деформировать материалы с помощью механического воздействия.
|
По типу применяемой оснастки штамповку листовых материалов можно разделить на виды:
· штамповка в инструментальных штампах,
· штамповка эластичными средами,
· импульсная штамповка:
· магнитно-импульсная,
· гидро-импульсная,
· штамповка взрывом,
· валковая штамповка.
Холодная листовая штамповка
Сущность способа заключается в процессе, где в качестве заготовки используют полученные прокаткой лист, полосу или ленту, свёрнутую в рулон. Листовой штамповкой изготовляют самые разнообразные плоские и пространственные детали массой от долей грамма и размерами, исчисляемыми долями миллиметра (например, секундная стрелка ручных часов), и детали массой в десятки килограммов и размерами, составляющими несколько метров (облицовка автомобиля, самолёта, ракеты).
Для деталей, получаемых листовой штамповкой, характерно то, что толщина их стенок незначительно отличается от толщины исходной заготовки. При изготовлении листовой штамповкой пространственных деталей заготовка обычно испытывает значительные пластические деформации. Это обстоятельство вынуждает предъявлять к материалу заготовки достаточно высокие требования по пластичности.
При листовой штамповке чаще всего используют низкоуглеродистую сталь, пластичные легированные стали, медь, латунь, содержащую более 60 % Cu, алюминий и его сплавы, магниевые сплавы,титан и др. Листовой штамповкой получают плоские и пространственные детали из листовых неметаллических материалов, таких, как кожа, целлулоид, органическое стекло, фетр, текстолит, гетинакс и др.
Листовую штамповку широко применяют в различных отраслях промышленности, особенно в таких, как авто-, тракторо-, самолето-, ракето- и приборостроение, электротехническая промышленность и др.
К преимуществам листовой штамповки относятся:
· возможность получения деталей минимальной массы при заданной их прочности и жёсткости;
· достаточно высокие точность размеров и качество поверхности, позволяющие до минимума сократить отделочные операции обработки резанием;
· сравнительная простота механизации и автоматизации процессов штамповки, обеспечивающая высокую производительность (30—40 тыс. деталей в смену с одной машины);
|
· хорошая приспособляемость к масштабам производства, при которой листовая штамповка может быть экономически целесообразной и в массовом, и в мелкосерийном производстве.
Горячая объёмная штамповка
Горячая объёмная штамповка (ГОШ) — это вид обработки металлов давлением, при которой формообразование поковки из нагретой до ковочной температуры заготовки осуществляют с помощью специального инструмента — штампа. Течение металла ограничивается поверхностями полостей (а также выступов), изготовленных в отдельных частях штампа, так что в конечный момент штамповки они образуют единую замкнутую полость (ручей) по конфигурации поковки. В качестве заготовок для горячей штамповки применяют прокат круглого, квадратного, прямоугольного профилей, а также периодический. При этом прутки разрезают на отдельные (мерные) заготовки, хотя иногда штампуют из прутка с последующим отделением поковки непосредственно на штамповочной машине.
Применение объёмной штамповки оправдано при серийном и массовом производстве. При использовании этого способа значительно повышается производительность труда, снижаются отходы металла, обеспечиваются высокие точность формы изделия и качество поверхности. Штамповкой можно получать очень сложные по форме изделия, которые невозможно получить приёмами свободной ковки.
Штамповка в открытых штампах характеризуется переменным зазором между подвижной и неподвижной частями штампа. В этот зазор вытекает часть металла – облой, который закрывает выход из полости штампа и заставляет остальной металл заполнить всю полость. В конечный момент деформирования в облой выжимаются излишки металла, находящиеся в полости, что позволяет не предъявлять высокие требования к точности заготовок по массе. Недостаток такого способа штамповки - необходимость удаления облоя при последующей механической обработке. Штамповкой в открытых штампах можно получить поковки всех типов.
Штамповка в закрытых штампах характеризуется тем, что полость штампа в процессе деформирования остаётся закрытой. Зазор между подвижной и неподвижной частями штампа постоянный и небольшой, образование в нём облоя не предусмотрено. Устройство таких штампов зависит от типа машины, на которой штампуют. Например, нижняя половина штампа может иметь полость, а верхняя – выступ (на прессах), или верхняя – полость, а нижняя – выступ (на молотах). Закрытый штамп может иметь две взаимно перпендикулярные плоскости разъема. При штамповке в закрытых штампах необходимо строго соблюдать равенство объёмов заготовки и поковки, иначе при недостатке металла не заполняются углы полости штампа, а при избытке размер поковки по высоте будет больше требуемого. Отрезка заготовок должна обеспечивать высокую точность.
Холодная объёмная штамповка
При холодной объёмной штамповке (ХОШ) температура исходной заготовки ниже ковочной. Это обуславливает высокие значения сопротивления металла штамповочному давлению и существенно меньшую текучесть, что ограничивает возможность получения изделий сложной формы. Однако по сравнению с ГОШ металл не подвергается термическим модификациям, нет усадки при охлаждении и нет риска образования горячих трещин. Точность выполнения поверхностей при ХОШ сопоставима с таковой при обработке металлов резанием, однако после ХОШ на поверхности металла, отсутствуют концентраторы напряжений (риски и царапины). Поэтому методами ХОШ изготавливают высокоточные и (или) высоконагруженные детали, например: шаровые опоры подвески автомобилей, коленчатые валы ДВС, детали втулки несущих винтов вертолётов.
Валковая штамповка
Валковая штамповка — формоизменяющая операция обработки металлов давлением, получения осесимметричных деталей из цилиндрической заготовки путём одновременного действия на неё радиальных и осевых нагрузок. Осевая нагрузка заготовки создаётся за счёт перемещения пуансона, а радиальная — за счёт обкатки её боковой поверхности в роликах или валках. Таким образом, валковая штамповка является способом комплексного локального деформирования, в котором в одном технологическом процессе происходит совмещение одной из основных кузнечных операций — прошивки или осадки с поперечной прокаткой или обкаткой. Валковая штамповка позволяет изготавливать круглые в плане сплошные и полые детали, тонкостенные и толстостенные изделия малых размеров, применяемые в приборостроении, а также крупногабаритные детали с высокой точностью и качеством при технологических усилиях на порядок меньших, чем при традиционных методах объёмной штамповки. Комплексное нагружение очага пластической деформации локальным периодическим воздействием с одновременным воздействием через постоянно фиксируемую зону позволяет получить новый технологический эффект, недостижимый другими методами деформирования. Валковая штамповка способствует улучшению физико-механических свойств обрабатываемого металла, обеспечивает требуемое расположение его волокон, что повышает эксплуатационные свойства получаемых деталей. Относительно низкая стоимость оснастки, незначительное время подготовки производства, возможность быстрой переналадки на другой типоразмер детали, использование оборудования небольшой мощности позволяют применять валковую штамповку как в крупносерийном, так и в средне- и мелкосерийном производствах.
|
|
Типы оградительных сооружений в морском порту: По расположению оградительных сооружений в плане различают волноломы, обе оконечности...
Автоматическое растормаживание колес: Тормозные устройства колес предназначены для уменьшения длины пробега и улучшения маневрирования ВС при...
Наброски и зарисовки растений, плодов, цветов: Освоить конструктивное построение структуры дерева через зарисовки отдельных деревьев, группы деревьев...
Индивидуальные и групповые автопоилки: для животных. Схемы и конструкции...
© cyberpedia.su 2017-2024 - Не является автором материалов. Исключительное право сохранено за автором текста.
Если вы не хотите, чтобы данный материал был у нас на сайте, перейдите по ссылке: Нарушение авторских прав. Мы поможем в написании вашей работы!