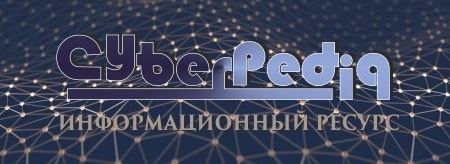
Историки об Елизавете Петровне: Елизавета попала между двумя встречными культурными течениями, воспитывалась среди новых европейских веяний и преданий...
Папиллярные узоры пальцев рук - маркер спортивных способностей: дерматоглифические признаки формируются на 3-5 месяце беременности, не изменяются в течение жизни...
Топ:
Теоретическая значимость работы: Описание теоретической значимости (ценности) результатов исследования должно присутствовать во введении...
Комплексной системы оценки состояния охраны труда на производственном объекте (КСОТ-П): Цели и задачи Комплексной системы оценки состояния охраны труда и определению факторов рисков по охране труда...
Марксистская теория происхождения государства: По мнению Маркса и Энгельса, в основе развития общества, происходящих в нем изменений лежит...
Интересное:
Инженерная защита территорий, зданий и сооружений от опасных геологических процессов: Изучение оползневых явлений, оценка устойчивости склонов и проектирование противооползневых сооружений — актуальнейшие задачи, стоящие перед отечественными...
Подходы к решению темы фильма: Существует три основных типа исторического фильма, имеющих между собой много общего...
Принципы управления денежными потоками: одним из методов контроля за состоянием денежной наличности является...
Дисциплины:
![]() |
![]() |
5.00
из
|
Заказать работу |
|
|
В подъемно-транспортных машинах находит применение большое количество разнообразных конструкций колодочных тормозов, различающихся в основном по схемам рычажных систем. Обычно они состоят из рычагов и двух колодок, расположенных диаметрально относительно тормозного шкива. Торможение механизма колодочным тормозом происходит в результате создания силы трения между тормозным шкивом, связанным с одним из валов механизма, и тормозной колодкой, соединенной посредством рычажной системы с неподвижными элементами конструкции.
В простейшем случае одноколодочного тормоза (рисунок 4.1,а) замыкающая сила Р, приложенная к тормозному рычагу, создает нажатие колодки на тормозной шкив, вследствие чего на вращающемся шкиве возникает сила трения F = f ∙ N, противодействующая вращению механизма. Если момент силы F больше момента движущей силы, действующей на том же валу, то скорость движения замедляется и движение прекращается.
Рисунок 4.1 – Расчетные схемы тормозов:
а – одноколодочного, б – двухколодочного
Тормозной момент, создаваемый одноколодочным тормозом:
, (4.1)
где f – коэффициент трения;
N – сила нажатия колодки на шкив;
D – диаметр тормозного шкива.
Отсюда необходимое усилие нажатия колодки на шкив:
(4.2)
Необходимую величину усилия Р, замыкающего тормоз, находят из условия равновесия рычага относительно его оси вращения:
, (4.3)
где l1 – расстояние от основания до оси тормозного шкива;
b – плечо;
l – длина плеча.
Знаки «плюс» или «минус» в уравнении определяются направлением вращения тормозного шкива. На рисунке 4.1 зазор между колодкой и шкивом при наличии сил трения между ними показан условно – для упрощения выявления на схеме действующих сил. При одноколодочном тормозе сила N нажатия колодки на шкив воспринимается валом тормозного шкива и подшипниками вала, вследствие чего увеличиваются размеры вала и подшипников. Поэтому одноколодочные тормоза применяют весьма редко и только в ручных механизмах.
|
Наиболее широко применяют двухколодочные тормоза с тормозными колодками, шарнирно связанными с тормозным рычагом (рисунок 4.1, б). Тормозной момент, создаваемый двухколодочным тормозом, составляется из суммы тормозных моментов, развиваемых каждой тормозной колодкой. Усилия нажатия колодок на, шкив определяются из уравнений равновесия тормозных рычагов. Момент от силы трения N∙f на плече, равном расстоянию от поверхности трения до оси колодки, стремится повернуть колодку, что приводит к неравномерному распределению давления между накладкой и шкивом по дуге обхвата. При конструировании тормозов стремятся разместить ось вращения колодки как можно ближе к поверхности трения, вследствие чего этот момент обычно относительно невелик и при составлении уравнений равновесия рычагов влиянием этого момента можно пренебречь.
В современных конструкциях тормозов для уничтожения усилия, изгибающего тормозной вал, применяют тормоза с прямыми рычагами. При этом тормозные моменты, создаваемые каждой колодкой, одинаковы и не зависят от направления вращения тормозного шкива. Общий тормозной момент двухколодочного тормоза при прямых рычагах:
, (4.4)
где η – к. п. д. рычажной системы тормоза, учитывающий потери на трение в шарнирах рычажной системы, η = 0,9÷0,95 (большие значения принимают для шарниров, имеющих смазку).
Условное среднее давление между шкивом и колодкой тормоза определяют из соотношения:
, (4.5)
где Fк – площадь одной тормозной колодки;
D – диаметр шкива;
В – ширина колодки, принимаемая обычно для обеспечения полного контакта между колодкой и шкивом, на 5-10 мм меньше ширины шкива;
|
β – угол обхвата шкива одной колодкой (обычно принимают β = 60÷100°).
Для получения малогабаритного тормоза, уменьшения мощности его размыкающего устройства (привода) и в то же время получения большого тормозного момента в тормозах подъемно-транспортных машин используют специальные материалы, обладающие повышенными фрикционными качествами. Из фрикционных материалов, выпускаемых отечественной промышленностью, наилучшими свойствами применительно к использованию в тормозах подъемно-транспортных машин обладает вальцованная лента 6КВ-10, «накладки тормозные вальцованные» ТУ 3027-51 Главшинпрома, а также вальцованная лента 8-229-63, обладающая повышенной износоустойчивостью. Вальцованную ленту выпускают толщиной 4-8 и шириной 20-100 мм. Длина ленты не ограничивается.
Вальцованная лента имеет высокую износоустойчивость, стабильный коэффициент трения, мало изменяющийся в процессе работы при нагреве тормоза. Она хорошо работает в паре с чугунным или стальным тормозным шкивом, имеющим твердость поверхности трения не ниже НВ250; при более низкой твердости происходит повышенный износ стального тормозного шкива и фрикционного материала. Фрикционный материал обычно крепят к тормозной колодке или ленте латунными или медными заклепками.
Исходя из необходимости предохранения поверхности шкива от чрезмерного износа, головку заклепки располагают от поверхности трения фрикционного материала не менее чем на половину толщины накладки (рисунок 4.2). Центр заклепки располагают от края накладки не менее чем на 15 мм во избежание выкрашивания. Расстояние между заклепками рекомендуется принимать не менее 80-100 мм.
В данном проекте предлагаю использовать способ соединения накладок с металлическим элементом путем приклеивания термостойкими клеями. Этот способ обеспечивает более полное использование фрикционного материала и повышает износоустойчивость фрикционной пары.
а – до модернизации, б – после модернизации,
1 – колодка, 2 – накладка, 3 – клей
Рисунок 4.2 – Крепление фрикционной накладки к тормозной колодке.
Предлагаю теплостойкий клей ВС-10Т. Данный клей предназначается для склеивания деталей из различных материалов (стали, дюралюминия, теплостойких пенопластов, стеклотекстолита и сотоматериалов, изготовленных на основе стеклоткани, пропитанной фенолоформальдегидной смолой) между собой и в сочетании друг с другом в конструкциях, работающих без снижения прочности клеевого шва при 200оС в течении 200 часов и при 300оС – 5 часов с учетом термостойкости склеиваемых материалов. Клей ВС-10Т применяется так же вместо заклепок при склеивании фрикционных накладок с металлическими колодками ведомых дисков сцепления.
|
Клей ВС-10Т выглядит как коричневая жидкость, он ограниченно стоек к воде, стоек к маслу, бензину и органическим растворителям. Рабочая температура клея: от -60 до 300оС. Клей ограниченно стоек в различных климатических условиях, не вызывает коррозии металлов, имеет высокую длительную прочность. Гарантийный срок хранения клея ВС-10Т с момента изготовления – 8 месяцев.
Технические характеристики клея ВС-10Т указаны в таблице 4.1.
Таблица 4.1 – Технические характеристики клея ВС-10Т
Массовая доля сухого остатка, % | 20-26 |
Условная вязкость по вязкозометру типа ВЗ-246 с диаметром сопла 6 мм, с | 35-70 |
Предмет прочности при сдвиге по клеевому соединению стали 30ХГСА, кгс/см2: - при температуре 20оС, не менее - при температуре 200оС, не менее - при температуре 300оС, не менее | |
Кислотное число, мг∙КОН/г, не более | 0,06 |
При отсутствии смазки рекомендуются следующие значения коэффициентов трения различных материалов:
Чугун и сталь по чугуну……………………………………0,15
Тканая тормозная асбестовая лента по чугуну и стали….0,35
Вальцованная лента по чугуну и стали…………………….0,42
Пластмасса типа КФЗ, КФЗМ по чугуну…………………..0,22
То же по стали………………………………………………..0,29
Горячеформованный фрикционный материал (на каучуке)
по чугуну и стали………………………………………….0,32
Дерево по чугуну…………………………………………….0,30
Дерево по стали………………………………………………0,25
Кожа по чугуну и стали……………………………………...0,20
Бронза по чугуну и стали……………………………………0,17
Бронза по бронзе……………………………………………..0,18
Сталь по текстолиту…………………………………………0,15
Сталь по фибре………………………………………………0,17
|
Эти значения коэффициента трения являются гарантированными расчетными, ниже которых при нормальных условиях работы действительное значение коэффициента трения не опускается.
Допускаемые значения давлений при использовании фрикционных материалов в колодочных тормозах механизмов среднего режима работы рекомендуется принимать по таблице 4.2. Для легкого режима работы рекомендуемые значения давлений можно повышать на 30%. Для тяжелого и весьма тяжелого режимов работы они должны быть снижены на 30%.
Таблица 4.2 – Допускаемые давления в колодочных тормозах
Материал трущихся поверхностей | Давление [p] в тормозах, кг/см2 | |
в стопорном | в спускном | |
Чугун и сталь по чугуну | ||
Сталь по стали | ||
Тормозная асбестовая лента по металлу | ||
Вальцованная лента по металлу |
Основные фрикционные материалы по результатам их испытаний в различных условиях работы имеют следующие значения допускаемой температуры нагрева, при превышении которой они теряют свои фрикционные качества: вальцованная лента tдоп = 220° С; тормозная асбестовая лента типа А (пропитка битумом) tдоп = 200° С; тормозная асбестовая лента типа Б (пропитка масляная) tдоп = 175° С. Превышение допускаемой температуры приводит к нарушению надежности тормозного устройства.
Замыкающая сила Р в современных конструкциях колодочных тормозов создается в большинстве случаев усилием сжатой пружины. Применение специального замыкающего груза, вследствие его значительной инерции, приводящей к увеличению времени замыкания и размыкания тормоза, ограничено некоторыми мало нагруженными тормозными устройствами.
В качестве размыкающего устройства (привода рычажной системы тормоза) используются специальные тормозные электромагниты, электрогидравлические и электромеханические толкатели, включаемые параллельно двигателю механизма. Поэтому размыкание тормоза и освобождение механизма происходит одновременно с включением двигателя. При выключении тока привод тормоза и двигатель механизма выключаются, тормоз под действием замыкающей силы замыкается и производит остановку механизма.
В отечественном подъемно-транспортном машиностроении применяются длинноходовые электромагниты постоянного тока типа КМП и ВМ (водозащищенного исполнения) и переменного тока типа КМТ, короткоходовые электромагниты постоянного тока типа МП и ТКЛ, а также переменного тока типа МО-Б (однофазный магнит).
К недостаткам тормозных электромагнитов следует отнести резкое включение магнита, сопровождающееся ударом якоря о сердечник, и практическую невозможность регулирования скорости движения якоря, вследствие чего не представляется возможным осуществить плавное изменение величины тормозного момента в процессе торможения. В связи с этим в подъемно-транспортном машиностроении получают все большее применение электрогидравлический и электромеханический приводы тормозов, осуществляемые при помощи электрогидравлических и электромеханических толкателей.
|
Электрогидравлический толкатель – это независимый механизм, состоящий из центробежного насоса, приводимого от электродвигателя малой мощности и поршневой группы, соединяемой с рычажной системой тормоза рисунок 4.3.
На рисунке показана одна из конструкций электрогидравлических толкателей при выключенном двигателе и крайнем нижнем положении поршня 1. При включении тока лопастное колесо 6 центробежного насоса, укрепленного в нижней части цилиндра 5, начинает вращаться и создает избыточное давление в золотниковой коробке 3, под влиянием которого золотник 4 поднимается, сжимает пружину 2 и открывает доступ жидкости через золотниковые отверстия в цилиндр под поршнем. При этом происходит перекачивание жидкости из пространства над поршнем в пространство под поршнем, и поршень 1 под влиянием избыточного давления начинает подниматься, преодолевая сопротивление внешней нагрузки. При выключении тока лопастное колесо останавливается, и поршень под действием внешней нагрузки и собственного веса опускается вниз, заставляя жидкость перетекать в пространство над ним. Лопасти рабочего колеса насоса выполнены радиальными, что делает насос, а следовательно, и толкатель независимыми от направления вращения двигателя толкателя.
Рисунок 4.3 – Электрогидравлический двухштоковый толкатель
Двухштоковые толкатели данного типа требуют повышенной точности изготовления и склонны к заклиниванию. Поэтому более современной моделью являются одноштоковые толкатели типа ТГ (рисунок 4.4), выпускаемые отечественной промышленностью.
Рисунок 4.4 – Электрогидравлический одноштоковый толкатель
В этом толкателе электродвигатель 1 размещен в нижней части корпуса 2 и погружен в рабочую жидкость – масло АМГ-10, трансформаторное масло или специальную жидкость ПМС-20 и ПГ-271, что обеспечивает лучшие условия охлаждения двигателя и возможность его более интенсивного использования. Регулирование времени подъема спуска поршня толкателя осуществляется винтами 4 и 5, воздействующими на втулку 3, изменяющую сечения отверстий истечения жидкости.
Электрогидравлические толкатели являются устройством, не чувствительным к механическим перегрузкам: если внешняя нагрузка превышает его подъемную силу, то поршень толкателя остается на месте, а насос продолжает работать, создавая нормальное рабочее давление жидкости под поршнем. При этом ток в обмотке двигателя, а также напряжения в элементах толкателя не увеличиваются. Ход штока толкателя можно произвольно ограничить как в сторону подъема, так и в сторону спуска, причем это не вызывает изменение подъемного усилия и дополнительный расход энергии или нагрев обмотки двигателя. Большими достоинствами электрогидравлических толкателей по сравнению с электромагнитами являются плавная работа устройства с большим числом (до 1000) включений в час, высокая износоустойчивость элементов толкателя, простота эксплуатации, резкое уменьшение пусковых токов. Применение регулировочных клапанов позволяет в весьма широких пределах изменять время срабатывания тормоза и время торможения. На время хода поршня толкателя, кроме величины отверстий истечения рабочей жидкости, влияет также и нагрузка на шток толкателя – чем больше внешняя нагрузка, тем больше время подъема и меньше время опускания.
Однако электрогидравлические толкатели имеют также и недостатки. Так, наличие рабочей жидкости в корпусе требует обеспечения хорошего уплотнения и создает неудобства в эксплуатации, особенно при низких температурах. Конструкция толкателя весьма сложная и требует для обеспечения надежной работы высокой точности изготовления, что предопределяет их высокую стоимость. Выпускаемые нашей промышленностью толкатели могут работать только в вертикальном положении – отклонение от вертикали не должно превышать 15°. Конструкция тормоза с приводом от электрогидравлического толкателя приведена на рисунке 4.5.
Рисунок 4.5 – Колодочный тормоз с электрогидравлическим приводом
В обычных конструкциях электрогидравлических толкателей избыточное давление рабочей жидкости не превышает 1 кг/см2 во избежание вспенивания при обратном ходе поршня. Однако имеются конструкции, в которых давление жидкости имеет значительно большую величину (от 7 до 15 атм.), что позволяет создать малогабаритные устройства, развивающие большие усилия.
Электромеханические толкатели, так же как и электрогидравлические, нечувствительны к механическим перегрузкам. Так, если внешняя нагрузка превышает подъемную силу толкателя, то шток его остается в крайнем нижнем положении, а двигатель продолжает работать, создавая нормальное рабочее усилие на штоке. При этом не образуются ни повышенные токи в двигателе, ни повышенные напряжения в элементах толкателя. Ход его можно ограничить произвольно как в сторону подъема, так и в сторону спуска без изменения величины подъемного усилия.
|
|
Типы сооружений для обработки осадков: Септиками называются сооружения, в которых одновременно происходят осветление сточной жидкости...
Индивидуальные очистные сооружения: К классу индивидуальных очистных сооружений относят сооружения, пропускная способность которых...
Адаптации растений и животных к жизни в горах: Большое значение для жизни организмов в горах имеют степень расчленения, крутизна и экспозиционные различия склонов...
Поперечные профили набережных и береговой полосы: На городских территориях берегоукрепление проектируют с учетом технических и экономических требований, но особое значение придают эстетическим...
© cyberpedia.su 2017-2024 - Не является автором материалов. Исключительное право сохранено за автором текста.
Если вы не хотите, чтобы данный материал был у нас на сайте, перейдите по ссылке: Нарушение авторских прав. Мы поможем в написании вашей работы!