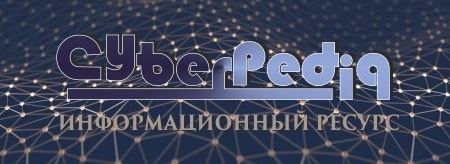
Кормораздатчик мобильный электрифицированный: схема и процесс работы устройства...
История создания датчика движения: Первый прибор для обнаружения движения был изобретен немецким физиком Генрихом Герцем...
Топ:
Техника безопасности при работе на пароконвектомате: К обслуживанию пароконвектомата допускаются лица, прошедшие технический минимум по эксплуатации оборудования...
Оснащения врачебно-сестринской бригады.
Устройство и оснащение процедурного кабинета: Решающая роль в обеспечении правильного лечения пациентов отводится процедурной медсестре...
Интересное:
Как мы говорим и как мы слушаем: общение можно сравнить с огромным зонтиком, под которым скрыто все...
Берегоукрепление оползневых склонов: На прибрежных склонах основной причиной развития оползневых процессов является подмыв водами рек естественных склонов...
Подходы к решению темы фильма: Существует три основных типа исторического фильма, имеющих между собой много общего...
Дисциплины:
![]() |
![]() |
5.00
из
|
Заказать работу |
|
|
Система контроля и испытаний оборудования подвижного состава в процессе ремонта имеет целью: а) недопущение к ремонту негодных деталей и узлов или неполноценных материалов для изготовления новых деталей — дефектовка, б) контроль соответствия ремонтируемых объектов техническим условиям и нормам на последовательных стадиях технологического процесса ремонта — операционный контроль и в) контроль допусков параметров функционирования отремонтированных объектов с целью убедиться в наличии достаточного запаса работоспособности па последующий межремонтный период — окончательный контроль.
Ответственность контроля и испытаний в процессе ремонта чрезвычайно велика на всех его стадиях. При дефектовке они определяют решение вопроса о необходимости ремонта или отбраковки деталей и о содержании ремонта. При некачественном контроле на этой стадии можно годные детали необоснованно отбраковать и, наоборот, негодные детали пропустить как годные или неправильно назначить ремонт. Во всех случаях это может повлечь за собой неожиданные отказы ремонтных объектов на линии задолго до конца межремонтных пробегов и резко повысить стоимость ремонтов. Операционный контроль деталей и узлов в процессе ремонта убеждает в том, что операции ремонта соответствуют требованиям технических условий, которые дают гарантию качественности ремонта. Своевременное обнаружение дефектов ремонта на этой стадии дает козможность или принять меры к их устранению или отбраковать детали как негодные и тем самым предупредить дальнейшие, уже бесполезные затраты на ремонт деталей и узлов. Контроль и испытания деталей и узлов на заключительной стадии ремонта подвижного состава дают возможность убедиться в соответствии допусковпараметры функционирования установленным ремонтным допускам,в наличии у ремонтных деталей определенного запаса работоспособности и дать определенную гарантию надежной и безотказной работы оборудования подвижного состава в эксплуатации.
|
Техника контроля неразрывно связана с общей технологией ремонта и является неотъемлемой частью технологического процесса. План операций технического контроля и их содержание выбирают из условия обеспечения максимума экономичности ремонта подвижногосостава с учетом технологических, экономическихи организационных соображений. Технологические предпосылки определяютнеобходимость проведения контроля в первую очередьна тех операциях, от точности которых зависит функционирование деталиили узла на подвижном составе. При ремонте групповых аппаратовтакой операциейявляется, например операция контроля развертки,при ре монте тяговых электрических машин операции контролясостоянияизоляции и др. Экономические предпосылки определяютнеобходимостьособо тщательного технического контроля деталейи узлов перед проведением трудоемких и дорогостоящих операцийремонта, так как неполноценные детали, попадая на дальнейшуюобработку, способствуют неоправданной затрате средстви загрузке оборудования. Такими операциями являются, например, операцииконтроля сварных швовперед термообработкой, операции контроляпараметров зубчатых колес перед окончательной отделкой зубьев.
Организационные предпосылки определяют необходимостьконтроля перед передачей деталей из одного цехав другойдля дальнейшей обработки.
Виды и методы контроля деталей и узлов подвижного состава при дефектовке и в процессе ремонта определяют их конструкцией, техническими условиями на ремонт. Содержание контроля механической обработки составляют измерения углов, длин ивзаимного положения составляютизмерения.
|
Контроль сборочных операций связан с определением погрешностей сборки: погрешностей посадок (установленных зазоров и натягов), погрешностей положения(перкосов, несосности, биения и пр.), погрешностей формы в результате деформации детали (при сварке, термообработке и пр.), погрешности балансировки (неуравновешенность, вибрация), механических повреждений сопрягающихся поверхностей (царапины, задиры, забоины), общего состояния объекта ремонта (комплектность, загрязнения, абразивными остатками, опилками, маслом и пр.). Наиболее распространенными погрешностями сборки являются погрешности посадок (ослабление и перенапряжение соединении), перекосы соединяемых деталей при неправильной или неравномерной затяжке гаек, неправильном подборе сопрягаемых деталей, прессовке без направляющих и т. д.
Основными методами контроляобработки и сборки являются наружный осмотр (визуальный контроль), проверка измерительными инструментами (инструментальный контроль) и субъективные! методы. При наружном осмотре (визуальном контроле) проверяют правильность комплектации изделия (наличие, в частности всех деталей крепежа и правильности разведения шплинтов), отсутствие внешних пороков (забоин, коррозии, царапин), правильность маркировки и пр. Инструментальный контроль имеет целью проверку качества обработки и сборки, зазоров в сопряжениях, проверку на биение и т. д. с использованием универсального пли специального контрольно-измерительного инструмента и приспособлений.
Технология и методы инструментального контроля в значительной степени зависят от конструктивных особенностей ремонтных узлов и программы ремонта. Принебольших программах ремонтов используют главным образом универсальный мерительный инструмент линейки, щупы, штанген-инструмент, микрометрический инструмент, угломеры и пр. При больших программах ремонта широко применяется специальный мерительный инструмент (предельные калибры, пробки, скобы, шаблоны) и контрольно-мерительные приспособления для комплексного контроля размеров и геометрических характеристик листовых рессор, пружин, балок управляемых мостов троллейбусов и пр.
Стенд представляет собой две вставленные одна в другую полые трубчатые балки 1 и 4,по концам которых на осях установлены монтажные шкворни 3 для проверяемой балки 2. Со шкворнями 3связаны стрелки 6, а с балками 1 и 4шкалы 5, указывающие наклон шкворней. Для проверки длины балки используют шкалу 9, нанесенную на балке 1, и стрелку 8, укрепленную на балке 4и входящую в прорезь балки 1. Скручивание балки проверяют по шкале и стрелке 7. Сама эта шкала приварена к балке 1, а ее стрелка – к балке 4.
|
В последнее время в связи с внедрением в ремонтную практику комплексной механизации и автоматизации получает распространение так называемый активный автоматическим контроль ремонтных операций в процессе самого ремонта. При этом по результатам измерений автоматически (по принципу автоматических систем замкнутого регулирования) осуществляется необходимая корректировка "технологического процесса, рассортировка деталей по размерам или другое программное управление.
Вместе с тем довольно широко еще применяется контроль качества ремонта субъективными методами. Сюда относятся: проверка «на качку» от руки, проверка отсутствия трещин и плотности посадки «на звук» при остукивании, проверка зацепления зубчатых колес «на свободное проворачивание» и «на шум» при работе на стенде во время прикатки, проверка качества сушки лакокрасочных покрытий «на отлип» и т. п. Точность субъективных методов контроля мала. По мере внедрения в ремонтное производство автоматики, рентгенотехники и других достижений техники эти методы контроля вытесняются. Заключительной контрольной операцией технологического процесса ремонта является испытание готового подвижного состава в стендовых условиях или на линии.
Дефектоскопия
Для деталей механического оборудования, работающих на ударные и знакопеременные нагрузки (осей колесных пар. ре* сор, сцепных приборов, деталей рессорного подвешивания, рулевых рычагов и поворотных цапф троллейбусов, деталей тяговой передачи, полуосей и др.), наиболее опасным видом разрушения являются изломы, связанные с появлением трещин усталости. Обычные методы дефектовки таких деталей — осмотр и инструментальный контроль недостаточны, так как не дают гарантии дальнейшей надежной работы в эксплуатации. Обнаружить развивающиеся трещин усталости, в особенности когда они залегают глубоко в детали практически трудно, а в ряде случаев и невозможно ни внешним осмотром, ни обычными методами измерений. Поэтому ответственные детали, состояние которых определяет безопасность движения при дефектовке проверяют методами дефектоскопии.
|
Основными методами дефектоскопии являются:магнитная, ультрозвуковая, люминесцентная, метод просвечивания иметод красок. Ни один из этих методов не является универсальным,поэтому в зависимости от конкретныхусловий проверки, материаладеталей, их размеров и конфигурацийприменяют те или другиеиз них. Внедрение дефектоскопии позволяет не только своевременно отбраковать негодные детали, но и анализировать причины брака с соответствующим изменением технологии ремонта деталей подвижного состава.
Магнитная дефектоскопия применяется для контроля деталей из Ферромагнитных материалов(сталей). Существуют два метода:
метод магнитных который применяют для выявления различныхдеталей (трещин, раковин), и методмагнитной структуроскопии,позволяющий судить о результатах термической обработки и оструктуре исследуемыхматериалов по их магнитным характеристикам.Метод магнитных порошковоснован на создании в испытуемой детали магнитного поля. Внутренние пороки вызывают искажение формы магнитных силовых линий в деталии на ее поверхности, которое может быть обнаружено при посыпании детали мелкими железными опилками (сухая магнитнаядефектоскопия) или обливании ее специальнойэмульсией, содержащей железные опилки (мокрая магнитная дефектоскопия). По форме узора, образуемого порошком на поверхности детали, судят о характере ее пороков.
Возможности выявления трещин и других пороков в деталях методом магнитных порошков связаны с взаимным расположением магнитных силовых линий и плоскости трещины. Резкое искажение формы магнитных силовых линий с выходом на поверхность создают только трещины неглубокого залегания, располагающиеся поперек линий поля
По этой причине применяют два методадефектоскопии: с циркулярным намагничиванием для выявления трещин, расположенных в направлении оси детали.
С импульсным намагничиванием для выявления трещин
расположенных поперек оси детали (рис. XIV.2, в). Дефектоскопия по методу полюсного намагничивания имеет большее применение, так как основное влияние на прочность деталей подвижного состава оказываются перечныетрещины. Магнитной проверке подвергаютоси колесных пар, валы тяговых двигателей, зубья шестерен, коренные листы рессор, подвески люльки, полуоси, трубу карданного вала и другие ответственные детали.
|
мокрый способ —при проверке деталей с шлифованными и полированными поверхностями. Магнитная эмульсия для мокрого способа дефектоскопии представляет собой смесь магнитного порошка трансформаторным маслом (200 г порошка на 1 л масла) Основными тинами дефектоскопов для магнитного контроля методом порошков являются неразъемный соленоидного типа, седлообразный и дефектоскоп для проверки зубчатых колес. Разъемными дефектоскопами проверяют, в частности, среднюю часть оси колесной пары. Дефектоскоп для этой проверки состоит из соленоида с разъемным магнитопроводом. Для удобства его располагают на тележке, которая перемещается вдоль оси колесной пары на специальным направляющим. Колесную пару укладывают шейками на роликах подъемников, которые позволяют правильно установить; ее относительно дефектоскопа и легко проворачивать. Для проверки нужных мест перемещают дефектоскоп вдоль оси колесной пары, одновременно посыпая ее магнитным порошком.
Большое влияние на возможность выявления пороков имеет глубина залегания трещины. Методом магнитной Дефектоскопии легко обнаруживают поверхностные трещины в деталях (см. рис. XIV.2, а). Внутренние пороки, даже при сравнительно неглубоком их залегании от поверхности детали, обнаружить трудно. Большое влияние на возможность выявления внутренних пороков оказывает род намагнчивающего тока (постоянный или переменный) и напряженность создаваемого им магнитного поля. Магнитный контроль можно производить постоянным и переменным током.
Недостатком магнитной дефектоскопии является то, что она применима для контроля деталей только из ферромагнитных материалов и позволяет обнаруживать в основном только поверхностные пороки: трещины, раковины, волосовины, и пр., расположенные на самой поверхности или в непосредственной близости от нее. Кроме того магнитная дефектоскопия мало пригодна для проверки деталей сложной формы.
Ультразвуковая дефектоскопия основана на свойстве ультразвука отражаться на границе раздела сред, в которых он распространяется. Ультразвуковой дефектоскоп позволяет осуществить передачу направленного ультразвукового излучения в проверяемую деталь и раздельно принять его отражение волны от стенок деталей и внутренних пороков. Существующие дефектоскопии дают возможность проверять деталь из любых металлов и сплавов и обнаруживать пороки площадью 3-4 м на глубине до 1 м. пороки расположены на сравнительно небольшой глубине (до 200-300мм), легко обнаружить этим методом, даже если их размеры не превышают 1-2 мм.
Принципиальная схема ультразвукового дефектоскопа показана на рисунке. В него входят: генератор 1 импульсов, возбуждающий ультразвуковые колебания пьезопластинки, встроенной в щуп-вибратор 2, который эти колебания передает в прозвучиваемый металл, щуп-резонатор 4 с пьезопластннкой, улавливающий отраженные колебания; приемно-усилительное устройство, усиливающее эти колебания; электроннолучевая трубка 7 с генератором развертки 6, обеспечивающая возможность визуального наблюдения на экране подаваемою и отраженных сигналов. На экране трубки, условно изображенной на рисунке, показаны три пика, первый из которых, а соответствует записи походного импульса, поданного в деталь, второй Ь — отраженному импульсу от дефекта (трещины 3) внутри изделия третий с — отраженному импульсу от противоположной поверхности изделия (так называемый донный сигнал). Конструкция шумов 2 и 4. используемых в качестве излучателей (вибраторов) и приемников (резонатора ультразвуковых колебаний, показана на рис. XIV.3, б. Шуп А предназначается для прозвучивания деталей с поверхностью не ниже 4-го класса чистоты (шлифованных или полированных), а щуп В —для прозвучивания детален с сильно шероховатой поверхностью. Основным элементом щупа является пьезоэлемепт 5, которым чаще всего является пластинка из титаната бария. Через накладку 7 он плотно соприкасается с контактным выводом 2, которые связан кабелем с генератором импульсов или усилителем дефекотоскопа (см. рис. XIV. 3, а). Контактный вывод прижат к пьезопластинке 5 натяжной гайкой 4 через изоляционную втулку 3. Пьезопластинка отделена от корпуса изоляционной втулкой 6. Щуп В дополнительно имеет резиновую контактную оболочку 8,в которой заключена жидкость 9. Резиновая оболочка обеспечивает плотный контакт с поверхностью изделия, ажидкость — передачу колебаний пьезопластинки 5поверхности изделия, или наоборот. При работе щупа вибратором к нему через :контактный вывод 2 подается от генератора импульсов переменное напряжение звуковой частоты, которое вызывает соответствующие механические колебания пьезопластинки. Эти колебания передаются в прозвучиваемый металл. При работе щупа резонатором механические колебания поверхности детали вызывают механические колебания пьезопластинки и появление на ее поверхностях электрических зарядов, которые снимаются контактным выводом 2 и создают электрический ток. Последний усиливается и поступает на пластины развертки электроннолучевой трубки дефектоскопа. Для облегчения перехода ультразвуковых волн с пьезопластинки вибратора в деталь и из детали на пьезопластинку резонатора поверхность детали в месте установки щупов смазывают маслом.
Применяют две основные схемы ультразвуковой дефектоскопии, на проход по методу звуковой тени —1 и по методу отражениями 2 (рис. XIV.3, в). Первая из них требует установки вибраторов В и
резонаторов Р с разных сторон изделия. Порок Д детали просвечивается «на проход». Применение этой схемы в ряде случаев ограничено. Дефектоскопия по методу отражения допускает установку вибраторов и резонаторов на одну и ту же поверхность изделия. Этот метод удобен и имеет более широкое распространение. Недостатком его является трудность выявления поверхностных пороков, связанная с образованием под поверхностью делали «мертвых зон» которые не могут быть прозвучены. Глубина мертвой зоны зависит от конструкции щупов. Применяют так называемые щупы для глубокого прозвучивания и наклонные щупы для неглубокого прозвучивания деталей. Механизм образования мертвых зон для этих щупов показан на рис. XIV. 3, г. Глубина h1, мертвой зоны при работе прямыми щупами в 5-6 раз больше глубины h2, мертвой зоны при работе наклонными щупами. С другой стороны применение щупов с наклонными головками приводит к уменьшению максимальной глубины Т прозвучивания деталей. Как видно из схемы, в этом случае при соответсвующей настройке дефектоскопа, можно работать без «донного» сигнала.
Основным недостатком ультразвуковой дефектоскопии являются трудности ее применения для контроля деталей сложной формы. Каждая деталь требует индивидуальной настройки дефектоскопа, при которой нужно разобраться во всех отраженных сигналах и определить наиболее удобные места установки щупов.
Метод просвечивания заключается в облучении деталей рентеновскими лучами или радиоактивных веществ: радия, урана, радиоактивного кобальта и др. О наличии внутренних пороков судя по изменению интенсивности излучения на выходе из металла.
В качестве источника излучения используют рентгеновскую лампу или камеру с радиоактивным веществом, а в качестве приемника кассету с фотопленкой. Просвечиваемое изделие помещают между лампой или камерой и кассетой. Структуру и пороки металла обнаруживают после проявления пленки. Методами просвечивания чаще всего контролируют качество сварки ответственных коротких швов. Для просвечивания изделий толщиной до 20 мм чаще пользуются рентгеновскими лучами толщиной более 50 мм – гамма-лучами радиоактивных веществ. Более проста установка для просвечивания лучами радиоактивных веществ, так как она не требует применение специальной аппаратуры. В основном же метод просвечивания применяют редко ввиду его трудоемкости.
Люминесцентный метод дефектоскопии применяют для выявления трещин в деталях из немагнитных материалов: алюминия, меди и их сплавов. Деталь покрывают раствором окиси магния способным флуоресцировать под действием ультрафиолетовых лучей кварцевой лампы, а затем промывают водой. При этой промывке раствор удаляется с поверхности изделия, но остается в полостях трещин и других поверхностных пороков. Подготовленную таким образом деталь сушат, покрывают порошком, впитывающим оставшийся в трещинах флуоресцирующий раствор, и осматривают в лучах кварцевой лампы через фильтр. На тех участках, где порошок впитал в себя раствор, возникает яркое зеленое свечение, позволяющее обнаружить места расположения трещин. Люминесцентный метод контроля позволяет выявить только поверхностные дефекты деталей.
Метод красок применяется как один из наиболее простых методов выявления поверхностных трещин деталей из любого металла. Деталь при этом методе дефектоскопии погружают в смесь масла и керосина с добавкой красителей, затем вынимают, насухо вытирают и покрывают меловой пудрой, растворенной в воде. Масло, выступившее из трещин на меловую пудру, дает после высыхания ярко окрашенный узор, характеризующий наличие и расположение волосовин, трещин и других пороков, выходящих наружу.
Метод красок по своей точности успешно может соперничать с методами магнитной дефектоскопии, исключая лишь случаи, когда трещины и волосовины имеют слишком малую глубину.
В настоящее время в практике ремонта подвижного состава городского электрического транспорта исключительное применение имеет магнитная дефектоскопия, которая не требует сложного оборудования и обеспечивает достаточную точность контроля.
|
|
Общие условия выбора системы дренажа: Система дренажа выбирается в зависимости от характера защищаемого...
Типы сооружений для обработки осадков: Септиками называются сооружения, в которых одновременно происходят осветление сточной жидкости...
Архитектура электронного правительства: Единая архитектура – это методологический подход при создании системы управления государства, который строится...
Особенности сооружения опор в сложных условиях: Сооружение ВЛ в районах с суровыми климатическими и тяжелыми геологическими условиями...
© cyberpedia.su 2017-2024 - Не является автором материалов. Исключительное право сохранено за автором текста.
Если вы не хотите, чтобы данный материал был у нас на сайте, перейдите по ссылке: Нарушение авторских прав. Мы поможем в написании вашей работы!