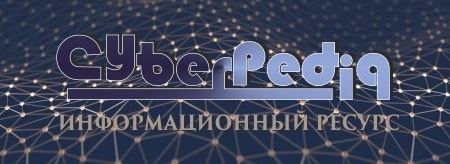
Таксономические единицы (категории) растений: Каждая система классификации состоит из определённых соподчиненных друг другу...
Своеобразие русской архитектуры: Основной материал – дерево – быстрота постройки, но недолговечность и необходимость деления...
Топ:
Характеристика АТП и сварочно-жестяницкого участка: Транспорт в настоящее время является одной из важнейших отраслей народного...
Основы обеспечения единства измерений: Обеспечение единства измерений - деятельность метрологических служб, направленная на достижение...
Особенности труда и отдыха в условиях низких температур: К работам при низких температурах на открытом воздухе и в не отапливаемых помещениях допускаются лица не моложе 18 лет, прошедшие...
Интересное:
Наиболее распространенные виды рака: Раковая опухоль — это самостоятельное новообразование, которое может возникнуть и от повышенного давления...
Что нужно делать при лейкемии: Прежде всего, необходимо выяснить, не страдаете ли вы каким-либо душевным недугом...
Аура как энергетическое поле: многослойную ауру человека можно представить себе подобным...
Дисциплины:
![]() |
![]() |
5.00
из
|
Заказать работу |
Содержание книги
Поиск на нашем сайте
|
|
В настоящее время чугун получают из железных руд в доменных печах. Эти печи имеют высоту порядка 30 м и могут выплавлять в сутки до 2000 т чугуна. Науглероживание железа происходит за счёт взаимодействия железа с печными газами, содержащими значительное количество СО. Образование сплава железа с углеродом, имеющего температуру плавления ниже, чем чистое железо, приводит к формированию капель жидкого чугуна, которые, стекая в нижнюю часть печи через слой раскалённого кокса, ещё больше насыщаются углеродом. Сырым продуктом, из которого вырабатывают все сорта чугуна и стали, является доменный чугун, или сырец, содержащий углерод (до 4,5%) и различные примеси (Si, Mn, S, Р), а иногда и легирующие элементы (Cr,Ni,V,AlnAp.).
Все сорта чугуна отличаются низким сопротивлением растяжению, а следовательно, повышенной хрупкостью. Разрушение происходит почти мгновенно, без видимых поперечных деформаций.
При сжатии чугун обладает явно выраженными упруго пластическими свойствами (Рис. 2.1). Даже при небольших напряжениях в чугуне образуются необратимые деформации, вследствие чего в чугуне отсутствует пропорциональность между напряжениями и деформациями. Кроме того, временные сопротивления раздроблению образцов чугуна даже одной плавки могут быть существенно различными. Из-за этих недостатков в настоящее время чугун используется только во второстепенных элементах (перильные ограждения и разнообразные элементы художественного дизайна). Но чугун коррозионностойкий материал. Поэтому его широко применяют в конструкциях, в которых это свойство является определяющим, например тюбингов для тоннельных отделок.
Если чугун-сырец подвергался переработке в пудлинговой (от англ. puddle - перемешивание) печи, то получали «сварочное железо» с содержанием углерода до 0,5%. В пудлинговой печи чугун нагревался раскалёнными газами, нагнетаемыми в печь вместе с кислородом воздуха. Часть углерода чугуна-сырца при этом выжигалась. На поде печи образовывалось малоуглеродистое тестообразное железо. Для придания железу однородности его перемешивали вручную или механическим способом. Иногда для этой цели использовали вращающиеся печи. В результате переработки чугуна пудлингованием получали крицы - железную губчатую массу с большим содержанием шлаков (Рис. 2.2). Крицы подвергали ковке с последующей прокаткой между валками. Шлаки, остававшиеся внутри железа, расплющиваясь в пластинки, придавали сварочному железу слоистое строение (Рис. 2.3).
В местах расположения шлаковых пластин отсутствует связь между волокнами железа, поэтому прочность сварочного железа вдоль и поперёк прокатки различная. Потребительские качества сварочного железа выше, чем у чугуна, поэтому из сварочного железа можно изготавливать элементы, работающие на растяжение, а следовательно, и на изгиб. Но сварочное железо в силу своей неоднородности обладало большим числом недостатков (неодинаковая прочность по толщине листа, недостаточная в ряде случаев ударная вязкость, чувствительность к концентраторам напряжений) и не допускало сварки и т. п.
Поэтому в отечественном мостостроении с начала XX в. сварочное железо не применяли. Оно постепенно заменялось литой сталью с содержанием углерода до 0,25%. Если сварочное железо имеет слоистую структуру, то литая сталь - мелкозернистую. В литой стали шлаки отсутствуют, так как в силу своей относительной лёгкости они всплывали на поверхность расплавленного металла и удалялись. Внедрению литого железа в практику отечественного мостостроения во многом способствовал проф. Н. А. Белелюбский.
Литая сталь, получаемая способами Бессемера, Томаса (крайне редко) или Мартена (наиболее широко), более однородна по своей структуре, чем сварочное железо. Сталь представляет собой сплав железа с углеродом (до 2%) и другими элементами. Атомы железа, находящиеся в жидком состоянии, располагаются беспорядочно. При остывании металла, после достижения температуры затвердевания, атомы железа во взаимодействии с неизбежными примесями размещаются в определённом порядке, образуют кристаллическую решётку. Кристаллы обычно имеют неправильную форму и носят название зёрен (кристаллитов).
Кристаллическое строение стали заметно на изломе образца. Блестящий излом с ярко выраженной кристалличностью является признаком хрупкости стали. Слоистый излом свидетельствует о низком качестве стали. Излом стали должен быть мелкозернистым, матовым. Высококачественная сталь имеет «шелковистый» излом. Отшлифованные и протравленные образцы стали под микроскопом выглядят в виде отдельных кристаллитов, имеющих разное строение (Рис. 2.4) в зависимости от содержания в стали углерода.
По химическому составу стали, используемые в мостостроении, можно разделить на две группы: малоуглеродистая (с содержанием угле-рода в долях %) и низколегированная (с содержанием полезных добавок не более 3...5% каждой).К малоуглеродистым по химическому составу сталям относятся СтЗ, Ст5, М16С, 16Д, а также Ст2 (для заклёпок). Раньше при изготовлении пролётных строений применяли специально предназначенную для мостостроения сталь СтЗ мост., содержащую 0,14...0,22% углерода. В стали М16С углерода несколько меньше, зато в Ст5 - больше.Углерод оказывает основное влияние на свойства стали. С увеличением содержания углерода прочность стали увеличивается, но уменьшается пластичность и вязкость. Так, например, Ст5 обладает высокой прочностью и твёрдостью, но плохо поддаётся механической обработке и сварке. Поэтому в настоящее время её используют для шарниров, катков, болтов-шарниров и прокладных листов под катки.
Кроме углерода, сталь практически всегда содержит полезные примеси - марганец (0,40...0,70%) и кремний (0,12...0.30%). Марганец и кремний способствуют раскислению стали. Кремний, правда, несколько снижает сопротивление стали коррозии, но этот недостаток устраняют добавкой меди (до 0,5%). Вместе с тем сталь содержит и вредные примеси, количество которых строго ограничивают. Сера с железом образует сульфид железа FeS с температурой плавления 985 °С. При нагреве стали до температуры 1000... 1200 °С (светло-красное каление) сульфид железа нарушает межкристаллитную связь, в результате чего сталь теряет свою прочность. При механической обработке (например, загиб) или при сварке в металле образуются трещины. Это явление называют красноломкостью. Красноломкость снижают введением в расплавленную сталь марганца. Образующийся пластичный сульфид марганца плавится при температуре 1620 °С.
Фосфор растворяется в железе, причём этот раствор остаётся в твёрдой фазе. Он резко снижает ударную вязкость (повышает хрупкость стали), т.е. вызывает так называемую хладноломкость.
Газы (кислород и азот) частично растворены в расплавленной стали и присутствуют в виде неметаллических включений (оксиды и нитриды). Оксиды хрупки и при горячей обработке не деформируются, а крошатся, разрыхляя металл, делая его красноломким. С течением времени нитриды способствуют развитию хрупкости металла (старение). С целью снижения влияния газов металл, выпущенный в ковш, выдерживают 5... 10 мин. для всплытия неметаллических включений и газов. Другой способ, обеспечивающий повышение качества стали - её вакуумирование в ковше перед разливкой. Для этого ковш помещают в камеру на 10...12 мин. при остаточном давлении примерно 2 мм рт. ст.
Степень раскисления стали маркируется индексами: кп - кипящая сталь, пс - полуспокойная, сп - спокойная, например, СтЗсп. Спокойная (раскисленная) сталь твердеет в изложницах до момента существенного снижения выделения газов. Такая сталь обладает высокой плотностью и однородностью. Раскисление осуществляют обычно в ковше добавлением в расплавленный металл раскислителей: кремния, марганца, алюминия. В последние годы расплавленную сталь обрабатывают синтетическими шлаками с целью её раскисления. Этот шлак, разогретый до температуры 1700 °С, заливают в объёме 3...5% от выпускаемой стали в разливочный ковш. Металл раскисляется, неметаллические включения в значительной степени переходят в шлак, количество серы в металле снижается на 50...70%. Следует иметь в виду, что усложнение технологи получения спокойной стали повышает её стоимость.
Сталь СтЗсп раньше широко использовали для изготовления стальных пролётных строений. Основной недостаток этой стали - значительное снижение ударной вязкости при низких температурах. В мостостроении сегодня эта сталь используется для изготовления болтов и гаек, несущих элементов тротуаров и смотровых приспособлений и элементов мостового полотна.
Если процесс раскисления не доведен до конца, то в стали при её остывании происходит процесс выгорания углерода с выделением газов (прежде всего СО). Газ, не имея свободы выхода из твердеющей при остывании стали, сохраняется в ней в виде мелких пузырьков с высоким содержанием в них серы и фосфора. Остывшая сталь при этом становится неоднородной. Полученная таким образом сталь называется кипящей. При прокатке такой стали пузырьки расплющиваются, создавая прослойки с вредными примесями. При термической обработке кипящей стали образуются трещины. Особенно этот недостаток проявляется при сварке. Поскольку прослойки с вредными примесями распределены в металле неравномерно, то процесс старения стали происходит неравномерно, и поведение конструкции во времени под нагрузкой непредсказуемо. Между тем стоимость получения кипящей стали относительно низкая. Мосты, построенные из такой стали, в России в настоящее время повсеместно заменяются. В современных мостах сталь СтЗ кп используется для изготовления нерабочих прокладок и элементов перильного ограждения.
Промежуточное положение по потребительским качествам и стоимости занимает полуспокойная сталь СтЗ пс. Она в настоящее время используется для настилов смотровых приспособлений и ходов.
Современный этап развития мостостроения характеризуется использованием для несущих конструкций мостов низколегированных сталей, содержащие добавки, улучшающие их потребительские свойства.
Легирующие добавки оказывают различные влияния на фазовые превращения в стали при её остывании. В основу обозначения марок легированных сталей положена буквенно-цифровая система. Легирующие элементы указывают русскими буквами: марганец - Г, кремний - С, хром - X, никель - Н, вольфрам - В, ванадий - Ф, титан - Т, молибден - М, кобальт - К, алюминий - Ю, медь - Д. Двухзначные цифры в начале марки - это среднее значение углерода в сотых долях процента, а цифры после букв - примерное содержание соответствующей добавки в целых процентах; отсутствие цифры указывает на то, что она составляет менее 1,5%. Для металлических конструкций мостов применяют низколегированные стали марок 15ХСНД, 10ХСНД, 14Г2АФД, 15Г2АФД. В настоящее время разработаны технические условия на толстолистовой прокат из сталей марок 12Г2СД и 12Г2СБД для мостостроения.
Прокат из сталей марок 15ХСНД и 10ХСНД в зависимости от вида термической обработки подразделяют на три категории: 1 -я - без термической обработки; 2-я - в нормализованном состоянии; 3-я - в термически улучшенном состоянии после закалки и высокого отпуска. Категория в заказе на сталь указывается после наименования марки стали - 15ХСНД-2. Первая категория в заказе не указывается. Нормализация заключается в нагревании до 940...960 °С и последующем охлаждении на воздухе, при котором сталь приобретает мелкозернистую структуру, позволяющую повысить потребительские качества стали.
Закалкой называют процесс термической обработки - нагрев до оптимальной температуры, выдержка и последующее быстрое охлаждение с целью получения повышенной прочности и твёрдости (пластичность стали при этом понижается). Отпуск проводят для снижения или полного устранения внутренних напряжений, уменьшения хрупкости закалённой стали и получения требуемой структуры и механических свойств. Высокий отпуск - нагрев стали от 450 до 650 °С и охлаждение (иногда в жидких средах, нагретых до 300°С).
Низколегированная сталь марки 15ХСНД имеет прочность на 40% выше, чем малоуглеродистая сталь 16Д. Для более прочных низколегированных сталей этот процент ещё выше. Это позволяет создавать облегченные пролётные строения, что особенно важно для большепролётных конструкций. Хотя низколегированные стали дорогие, снижение массы металла несущих конструкций позволяет в целом снизить стоимость конструкции.
Важной характеристикой листового проката является сплошность, устанавливаемая методами ультразвукового контроля в зависимости от величины контролируемых характеристик сплошности. Сплошность проката должна соответствовать 1 или 2 классу, указываемому в заказе на сталь после категории термической обработки - 15ХСНД-2-1.
Для опорных частей, шарниров, опорных подушек кабелей висячих мостов применяют литую углеродистую и легированную сталь марок 25Л, ЗОЛ, 35Л, 20ГЛ, 20ФЛ, 35ХН2МЛ и 35ГЛ, а также кованую углеродистую и легированную сталь марок КП275, КП245,..., КП1200.
Сталь выбирают с учётом расчётной температуры района, в котором предполагается строительство моста. При расчётной температуре до минус 40 °С принимают тип исполнения - обычное; при температуре от минус 40 °С до минус 50 °С - северное А; при температуре ниже минус 50 °С - северное Б.
Современные стали поставляют с гарантией свариваемости, обеспечиваемой технологией её приготовления и соблюдением требований по химическому составу.
Существенным недостатком стали является её относительно низкая сопротивляемость коррозии. Даже легирование не может в полной мере защитить металл от коррозии. Борьба с коррозией металла - важнейшая проблема, направленная на снижение металлоёмкости конструкций и продление срока их службы.
Металл от коррозии защищают различными методами. Если на поверхность металла наносится неметаллическое покрытие (например, свинцовый сурик), такой процесс называют покраской. При нанесении металлических покрытий (например, цинк) осуществляют так называемую металлизацию. Иногда осуществляют прокатку заготовки с наложенным на неё листами другого металла с высокими антикоррозионными свойствами (например, алюминия). Этот процесс называют плакированием.
|
|
Биохимия спиртового брожения: Основу технологии получения пива составляет спиртовое брожение, - при котором сахар превращается...
Общие условия выбора системы дренажа: Система дренажа выбирается в зависимости от характера защищаемого...
Автоматическое растормаживание колес: Тормозные устройства колес предназначены для уменьшения длины пробега и улучшения маневрирования ВС при...
История развития пистолетов-пулеметов: Предпосылкой для возникновения пистолетов-пулеметов послужила давняя тенденция тяготения винтовок...
© cyberpedia.su 2017-2025 - Не является автором материалов. Исключительное право сохранено за автором текста.
Если вы не хотите, чтобы данный материал был у нас на сайте, перейдите по ссылке: Нарушение авторских прав. Мы поможем в написании вашей работы!