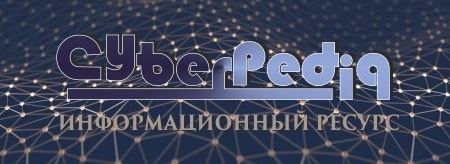
Общие условия выбора системы дренажа: Система дренажа выбирается в зависимости от характера защищаемого...
Поперечные профили набережных и береговой полосы: На городских территориях берегоукрепление проектируют с учетом технических и экономических требований, но особое значение придают эстетическим...
Топ:
Теоретическая значимость работы: Описание теоретической значимости (ценности) результатов исследования должно присутствовать во введении...
Выпускная квалификационная работа: Основная часть ВКР, как правило, состоит из двух-трех глав, каждая из которых, в свою очередь...
Техника безопасности при работе на пароконвектомате: К обслуживанию пароконвектомата допускаются лица, прошедшие технический минимум по эксплуатации оборудования...
Интересное:
Влияние предпринимательской среды на эффективное функционирование предприятия: Предпринимательская среда – это совокупность внешних и внутренних факторов, оказывающих влияние на функционирование фирмы...
Берегоукрепление оползневых склонов: На прибрежных склонах основной причиной развития оползневых процессов является подмыв водами рек естественных склонов...
Что нужно делать при лейкемии: Прежде всего, необходимо выяснить, не страдаете ли вы каким-либо душевным недугом...
Дисциплины:
![]() |
![]() |
5.00
из
|
Заказать работу |
|
|
РЕФЕРАТ
Расчетно-пояснительная записка включает: 46 страниц, 10 таблиц, 2 рисунков, 6 литературных источников.
поликонденсация, полиэфир П6-БА, этиленгликоль, адипиновая кислота, 1,4-бутандиол, тетрабутоксититан.
Цель: спроектировать производство полиэфира П6-БА мощностью 1150т/год.
В расчетно-пояснительной записке приведены: технологическая схема производства, характеристика сырья, вспомогательных материалов и готового продукта, расчёт материального баланса и необходимого количества оборудования, механический расчет основного аппарата, тепловой расчёт.
![]() |
Содержание
Титульный лист 1
Лист нормоконтролера 2 Задание выполнение квалификационной работы 3
Реферат 4
Содержание 5
Обозначения и сокращения 7
Введение 8
1. Технико-экономическое обоснование метода производства и объема производства 12
2. Технологическая часть
2.1 Теоретические основы производства 13
2.1.1 Химические и физико-химические основы производства 14
2.1.2 Технологические основы 17
2.2 Характеристика исходного сырья, полуфабрикатов и вспомогательных материалов и энергетических средств 18
2.3 Характеристика готовой продукции и отходов производства 20
2.4 Разработка блок схемы производства 21
2.5 Материальный расчет производства 22
2.6 Описание аппаратурно- технологической схемы производства 26
2.7 Технологическая документация процесса 29
2.8 Выбор и расчет количества основного- и вспомогательного оборудования 31
2.9 Механический расчет
2.9.1 Расчет цилиндрической обечайки 33
2.9.2 Расчет днища и крышки аппарата 33
2.9.3 Расчет элементов рубашки 34
2.9.4 Фланцевые соединения и штуцера 35
2.9.5 Опоры аппарата 37
|
2.9.6 Расчет мешалки 37
2.10 Тепловой расчет 39
3. Стандартизация 46
4. Заключение по проекту 47
5. Список использованной литературы 48
ИСПОЛЬЗУЕМЫЕ УСЛОВНЫЕ СОКРАЩЕНИЯ
АДК - Адипиновая кислота
ЭГ – Этиленгликоль
ТБТ – Тетрабутоксититан
ПЭ - Полиэфир
ВВЕДЕНИЕ
Успешно развивающееся промышленное производство сложных полиэфиров всегда было значимым для страны. Всему миру был хорошо известен натуральный полиэфир – янтарь, но путь получения искусственного полиэфира был трудным, но достижимым. Технология получения полиэфиров была разработана в 1959-1962 гг. Первое на «Казанском заводе синтетического каучука» производство полиэфиров было организовано в 1966 году, а в 1979 году введено в действие производство полиэфира ПБА, марки полиэфиров ПБА I и ПБА III – в 1986 году [1].
Едва ли найдутся отрасли народного хозяйства, где бы ни применялись полиэфиры. При этом выделяются отрасли, в которых объем их потребления особенно велик. К ним относятся: судостроение, автомобилестроение и транспортное машиностроение, строительство, химическая промышленность, электротехническая промышленность, мебельная промышленность, товары народного потребления [1].
Полиэфиры служат основой для производства уретановых каучуков, монолитных и пористых изделий методом литья, для получения оптически чувствительных уретановых полимеров, а также в качестве компонента в клеевых композициях. Полиэфиры нашли широкое применение в резинотехнической промышленности, машиностроении, при изготовлении магнитных лент, а также для изготовления заливочных и лакокрасочных материалов.
Полиэтиленадипинаты устойчивы к старению, обладают низкой летучестью и хорошими миграционными свойствами, их окраска более светлая, к экстракции углеводородами они более устойчивы, чем например полиэтиленсебацинаты.
В промышленности полиэфиры применяют в качестве пластификаторов. Введение пластификаторов в каучуки облегчает их переработку, повышает пластичность резиновой смеси, способствует уменьшению разогрева при смешивании и снижает опасность под вулканизации.
|
Таким образом, достаточно многообразное применение полиэфиров во многих отраслях промышленности свидетельствует о их важности и значимости как в качестве целого, так и полупродукта в составе различных композиционных материалов.
1 Технико-экономическое обоснование
Метода производства
Производства
Технология получения полиэфиров и на их основе – нового класса высокомолекулярных соединений – полиуретанов, превосходящих по износостойкости все известные полимерные материалы, разработана в 1959- 1962 гг. Опытное производство полиуретанов освоено на производственной базе ВНИИСК. Промышленное производство полиэфиров по непрерывной технологии организовано на «Казанском заводе синтетического каучука» в 1966 г., а в 1979г. введено в действие производство полиэфира ПБА.
Сложные полиэфиры адипиновой кислоты и различных гликолей (П-6, ПС, П6-БА, ПБА, ЭДА-50, П-9А) используются для получения полиуретанов методом литья, для вальцуемых полиуретановых каучуков, отличающихся высокими прочностными показателями, сочетанием высокой твердости с эластичностью, уникальной стойкостью к истиранию, растворителям, маслам, топливам, агрессивным средам, для получения компонент в клеевых композициях в обувной промышленности, машиностроении, при изготовлении магнитных лент, а также для изготовления заливочных и лакокрасочных материалов.
Механический расчет
Аппарат с мешалкой предназначен для проведения синтеза полиэфира П6-БА:
Основные размеры аппарата [5]:
Объем аппарата, Vап =10 м2
Диаметр аппарата, D=2600 мм,
Высота цилиндрической части аппарата, L=2390 мм
Рабочее давление в аппарате 0,4 МПа
Рабочее давление в рубашке 0,6 МПа
Мешалка рамная
Расчет элементов рубашки.
В качестве расчетного давления принимают давление в рубашке. Для корпусов с внутренним D=2600 мм, диаметр рубашки принимают больше диаметра D на 200 мм [5].
Толщина стенки цилиндрической части рубашки [5]:
SR= р×D / 2×φ × [σ] - p
Где φ = 1 - коэффициент прочности сварного шва;
р - рабочее давление в рубашке.
SR= 0,6×2600 / 2×1 × 126 – 0,6
S= Sr + с
S = 5,59 мм + 2 мм = 7,59 мм
Округляем значение в большую сторону до ближайшей стандартной толщины S = 8 мм [5].
|
Проверка [13]:
(S - с) / D 1
(8 мм - 2 мм) / 2600 мм = 0,0023 - Условие выполняется.
Проверка на допускаемое наружное давление [5]:
[p]= 2×φ × [σ] ×(S - с)/ (D+(s-c) = 2×126×1×6 / 2606=0,62 МПа
0,6 ≤ 0,62 МПа - Условие надежной эксплуатации выполняется.
Эллиптическое днище [5]:
SR= p×D / 2×φ × [σ] – 0,5 × р = 0,6 ×2600 / 2×1×126 – 0,5 ×0,6= 5,89
S = SR +с = 5,89 + 2 = 7,89 мм
Округляем значение в большую сторону до ближайшей стандартной толщины S = 8 мм. [5].
Проверка [5]:
S - c / D
8 мм - 2 мм / 2600 = 0,0023 - Условие выполняется.
Проверка на допускаемое наружное давление [5]:
[р] = 0,62 МПа
0,62 МПа - Условие надежной эксплуатации выполняется.
Тепловой расчет
Цель теплового расчета - определение требуемой поверхности теплообмена проектируемого аппарата. Расчет поверхности теплообмена основан на совместном решении уравнений теплового баланса и теплопередачи [6].
Уравнение теплового баланса: Qnp = Qpacx - приход теплоты в аппарат должен быть равен расходу теплоты в том же аппарате.
Тепловой баланс рассчитываем по данным материального баланса, то есть на цикл работы для одного аппарата.
Исходные данные для теплового расчета:
Аппарат:
Масса аппарата – 10000 кг
Теплоемкость конструкционного материала (сталь двухслойная 16ГС+12Х18Н10Т ГОСТ 108, рубашка ВСТ 3 сп ГОСТ 380-7) - 0,503 кДж × кг /град
Температурный режим:
Тн = 20 °С - начальная температура
Тк = 205 °С - конечная температура
Загрузка сырья в один аппарат с рабочим объемом 10 м3:
mAK = 3629,42 кг
mБд = 2734,50 кг
mП6-БА = 5309,73 кг
mотгоны = 894,93 кг
mпотери = 159,29 кг
Средние удельные теплоемкости сырья и готового продукта:
СAK = 1,426 кДж × кг / град
Сбд = 3,078 кДж × кг / град
Сп6-ба = 2,467 кДж × кг / град
Для теплового расчета используем следующее уравнение:
Qисх + Qмеш + Qтепл + Qкат = Qпрод + Qнагрев + Qпотери
Qисх - тепло, вносимое потоками исходного сырья;
Qмеш - тепло, выделяющееся при перемешивании механическим устройством;
Qтепл - тепло, вносимое теплоносителем;
Qкат - тепло, вносимое катализатором;
Qпрод - тепло, уносимое продуктами реакции;
Qнагрев - теплота, затраченная на нагрев реактора;
Qпотери - тепловые потери, уносимые в окружающую среду.
Qмеш и Qкат можно пренебречь, так как частота вращения мешалки и количество загружаемого катализатора небольшие.
|
Qисх = QAK + QБД
Qпрод = QП6-БА + QП6-БА(потери) + Qотгоны
Q = m × cp × t
Где m – масса вещества, кг;
cp – теплоемкость вещества, кДж × кг / град;
t - температура вещества.
QAK = 3629,42 × 1,426 × 20 = 103511,0584 кДж
QБД = 2734,50 ×3,078 × 20 = 168335,82 кДж
QП6-БА = 5309,73 × 2,467 × 205 = 2685316,30155 кДж
QП6-БА(потери) = 159,29 × 2,467 × 205 = 80558,52815 кДж
Qотгоны = (626,451 × 2262,6) + (268,479 × 649,45) = 1417408,0326 + 174363,68655 = 1591771,71915 кДж
Где 2262,6 кДж / кг × град - теплота парообразования воды;
649,45 кДж / кг × град - теплота испарения отгонов.
Qисх = QAK + QБД = 103511,0584+168335,82=271846,88 кДж
Qпрод = QП6-БА + QП6-БА(потери) + Qотгоны = 2685316,30155 + 80558,52815 + 1591771,71915 = 4357646,54875 кДж
Теплота, затраченная на нагрев реактора:
Qнагрев = Ga × с × (Тк – Тн)
Где Ga - масса аппарата, кг;
с - теплоемкость конструкционного материала, кДж × кг / град;
Тк и Тн - конечная и начальная температуры аппарата.
Qнагрев = 10000 × 0,503 × (205 - 20) = 930550,0 кДж
Тепловые потери, уносимые в окружающую среду:
Qпотери = α × F × t
Где F - поверхность теплообмена, м2 ;
t - разность температур стенки аппарата и окружающей среды;
α = αк + αл - суммарный коэффициент массоотдачи, равный сумме коэффициента теплоотдачи конвекцией αк, Вт / м2 × К и коэффициента теплоотдачи лучеиспусканием αл, Вт / м2 × К.
αк = 1,82
αк = 10,37 Вт/м2 × К
αл = с1 × ((Тn / 100)4 - (Т0 / 100)4) / tn – t0
Где c1 = 4,2 - степень темноты поверхности аппарата [9]
αл = 4,2 × (500,55 К - 73,7 К) / 180 = 9,96 Вт / м2 × К
α = 10,37 + 9,96 = 20,33 Вт / м2 × К
Qпотери = 20,33 × 23,5 × 185 = 88384,675 кДж = 24,55 кВт
Тепло, подводимое теплоносителем:
Qтепл = Qпрод + Qнагрев + Qпотери - Qисх = 1210,3 + 258,49 + 24,55 - 75,51 = 1417,83 кВт
Положительный знак указывает на то, что тепло необходимо подводить с помощью теплоносителя.
Результат теплового баланса отражается в таблице 2.10
Таблица 2.10 - Тепловой баланс производства П6-БА.
Приход | Расход | ||||
Тепловой поток | КВт | % | Тепловой поток | КВт | % |
Адипиновая кислота кислота | 28,75 | 1,97 | Полиэфир П6-БА | 745,92 | 51,13 |
1,4-бутандиол | 46,76 | 3,20 | П6-БА (потери) | 22,38 | 1,53 |
Теплоноситель ПЭС-5 | 1417,83 | 94,83 | Отгоны | 30,28 | |
Тепло на нагрев | 258,49 | 15,46 | |||
Потери в окружающую среду | 24,55 | 1,60 | |||
Итого | 1493,34 | 1493,34 |
Необходимая поверхность теплообмена может быть рассчитана из уравнения теплопередачи:
QT = k × F × tcp
Отсюда расчетная поверхность теплообмена равна:
Fрас = QT / k × tcp
Где k - коэффициент теплопередачи, Вт / м2 × град;
tcp - средняя температура среды,
к = 1 / (1/α1 + 1/α2 + 1 /гз1 + 1/гз2 + δ/λ)
Где α1 и α2 - коэффициенты теплоотдачи реакционной среды и теплоносителя, Вт / м2 × град;
гз1 и гз2 - тепловая проводимость загрязненных стенок, Вт / м2 × град:
|
гз1 = 2900 Вт / м2 × град - вода среднего качества,
гз2 - 5700 Вт / м2 × град - для органической жидкости;
δ - толщина стенки, м;
λ = 46,5 Вт / м × град - коэффициент теплопроводности стали
Коэффициент теплоотдачи реакционной среды α1:
α1 =Nu × λ/D
Где λ -теплопроводность реакционной среды, Вт / м × град;
D - диаметр аппарата, м
Nu - коэффициент Нуссельта
Коэффициент Нуссельта:
Nu = 0,36 × Re0,67 × Pr0,33 × (μ / μст) 0,14
Где μ и μст - вязкость реакционной среды, Па × с [6];
Re - коэффициент Рейнольдса;
Рг - коэффициент Прандтля.
Re = n × dM2 × p / μ
Где n - частота вращения мешалки, с-1;
dM - диаметр мешалки, м;
р - плотность реакционной среды, г/см
Re= 0,84 × 1,6252 × 1153,5/0,04 = 63965,18
Рг = ср × μ / λ
Где ср - 1180 кДж / кг × град - теплоемкость реакционной среды;
λ = 0,06 Вт / м × град - теплопроводность реакционной смеси [6];
Рг = 1180 × 0,04 / 0,06 = 786,6
Nu = 0,36 × 63965,180,67 × 786,60,33 × (0,04 / 0,035)0,14 = 5495,44
α1 = 5495,44× 0,06 / 2,2 = 149,87 Вт / м2 × град
Коэффициент теплоотдачи теплоносителя α2:
α2 = Nu × λ / d
Где λ = 0,645 Вт / м × град - теплопроводность теплоносителя, Вт / м × град [6];
Nu - коэффициент Нуссельта;
d - диаметр канала (трубы), м [6];
Nu = 0,66 × Re0,5 × Pr0,33 × (Рг / Рг ст)
Где Pr и Рг ст - коэффициенты Прандтля для теплоносителя в центре и у стенки аппарата;
Re - коэффициент Рейнольдса
Re = w×d×p/μ
Где w = 0,8 м/с - скорость подачи теплоносителя;
d - диаметр трубы (канала), м;
р = 1075 г/см3 для 200 - плотность теплоносителя;
μ = 0,038 Па × с для 200 - вязкость теплоносителя [6],
Re = 0,8 × 0,5 × 1075/0,038 = 1131
Рг = ср × μ / λ
Где ср - теплоемкость теплоносителя (ср = 4190 кДж / кг × град в центре аппарата при 200; ср = 4450 кДж / кг × град у стенки аппарата при 230);
λ - теплопроводность реакционной среды (λ = 0,845 Вт / м × град в центре аппарата при 200; λ = 0,873 Вт/м × град у стенки аппарата при 230);
μ - вязкость теплоносителя (μ = 0,007 Па × с в центре аппарата при 200; μ = 0,0064 Па × с у стенки аппарата при 230) [6];
Рг = 4190 × 0,007 / 0,845 = 34,71
Ргст = 4450 × 0,0064 / 0,873 = 32,62
Nu = 0,66 × 11310,5 × 34,710,33 × (34,71 /32,62) = 72,51
α2 = 72,51 × 0,645 / 0,05 = 935,38 Вт / м2 × град
Обогрев осуществляется теплоносителем ПЭС-5 с начальной температурой:
t = 250= 523 К
t1н = 523 К, t1к = 503 К
t2н = 293 K, t2к = 473 К
А = (t1н - t2н) / (t1к - t2к) = (523 - 473) / (503 - 293) = 1,67
Средняя температура среды:
tср = (t2к - t2н) / 2,3 lg ((t1н - t2н) / (t1к - t2к)) × (A - 1) / 2,3 lg A
tср = (473 - 293) / 2,3 lg((523 - 293) / (523 - 473)) × (1,67 - 1) / 2,3 lgl,67 = 92,12
Коэффициент теплопередачи:
k = 1 / (1/122,74 + 1/2900 + 0,006/46,5 + 1/5700 + 1/935,38) =
109,59 Вт/ м2 × град
Тогда расчетная поверхность теплопередачи:
Fрас = 1417,83 / (109,59 × 92,12) = 14,0 м2
Реальная поверхность теплопередачи:
Fреал = π × D × Нж = 3,14 × 2,6 × 2,784 = 22,7 м2
Fрас = 14,0 м2< Fpeaл = 22,7 м2. Следовательно, эффективный теплоперенос обеспечен.
Запас площади поверхности:
(22,7/ 14,0 ×100) - 100 = 38,3%
3 СТАНДАРТИЗАЦИЯ
При выполнении курсового проекта использованы следующие нормативные документы:
ГОСТ 10558-80 Адипиновая кислота
ГОСТ 10136-77 Этиленгликоль. Технические условия
ГОСТ 9293-74 Азот
ГОСТ 6824-76 1,4-Бутандиол. Технические условия
ГОСТ 13004-77 Жидкости полиэтиленсилоксановые. Технические условия.
ГОСТ 6613-86 Сетки проволочные тканые с квадратными ячейками
ТУ 6-09-2738-89 Тетрабутоксититан технический (тетрабутиловый эфир титановой кислоты орто; тетрабутилортотитанат)
ТУ 38.103582-85 Полиэфир П6-БА
ЗАКЛЮЧЕНИЕ ПО ПРОЕКТУ
Спроектировано производство сложного полиэфира П6-БА. Проектная мощность - 1150 т/год. Проведены необходимые материальные, технологические расчеты, а также тепловой и механический расчет реактора.
5 СПИСОК ИСПОЛЬЗОВАННОЙ ЛИТЕРАТУРЫ
1. Казанский завод синтетического каучука [Электронный ресурс].- Режим доступа: http/Avww.kzsk.ru, свободный. - Проверено 24.12.08.
2. Соболев В.М., Промышленные синтетические каучуки /А.М.Соболев, И.В.Бородина. -М.: Химия, 1977.- 392с.
3. Коршак В.В., Равновесная поликонденсация / В.В.Коршак, С.В.Виноградов. - М.: Наука, 1986. -414с.
4. Аверко-Антонович, Л.А. Химия и технология синтетического каучука / Л.А.Аверко-Антонович, Ю.О. Аверко-Антонович, П.А.Кирпичников [и др.]. - М.: Химия 2008. – 357 с.
5. Лащинский, А.А. Основы конструирования и расчета химической аппаратуры: справочник / А.А.Лащинский, А.Р.Толщинский. - 2-е изд., перераб. и доп. - Л.: Машиностроение, 1970. - 752с.
6. Павлов, К.Ф. Примеры задачи по курсу процессов и аппаратов химической технологии: учеб.пособие для ВУЗов / 'К.Ф.Павлов, П.Г.Романков, В.А.Носков. - 9-е изд., перераб. и доп. - Л.: Химия, 1981. - 560с.
7. Заикин А.Е. Основы проектирования производств полимеров/А.Е. Заикин. Казан. гос. технол. ун-т, 2000.-32 с.
РЕФЕРАТ
Расчетно-пояснительная записка включает: 46 страниц, 10 таблиц, 2 рисунков, 6 литературных источников.
поликонденсация, полиэфир П6-БА, этиленгликоль, адипиновая кислота, 1,4-бутандиол, тетрабутоксититан.
Цель: спроектировать производство полиэфира П6-БА мощностью 1150т/год.
В расчетно-пояснительной записке приведены: технологическая схема производства, характеристика сырья, вспомогательных материалов и готового продукта, расчёт материального баланса и необходимого количества оборудования, механический расчет основного аппарата, тепловой расчёт.
![]() |
Содержание
Титульный лист 1
Лист нормоконтролера 2 Задание выполнение квалификационной работы 3
Реферат 4
Содержание 5
Обозначения и сокращения 7
Введение 8
1. Технико-экономическое обоснование метода производства и объема производства 12
2. Технологическая часть
2.1 Теоретические основы производства 13
2.1.1 Химические и физико-химические основы производства 14
2.1.2 Технологические основы 17
2.2 Характеристика исходного сырья, полуфабрикатов и вспомогательных материалов и энергетических средств 18
2.3 Характеристика готовой продукции и отходов производства 20
2.4 Разработка блок схемы производства 21
2.5 Материальный расчет производства 22
2.6 Описание аппаратурно- технологической схемы производства 26
2.7 Технологическая документация процесса 29
2.8 Выбор и расчет количества основного- и вспомогательного оборудования 31
2.9 Механический расчет
2.9.1 Расчет цилиндрической обечайки 33
2.9.2 Расчет днища и крышки аппарата 33
2.9.3 Расчет элементов рубашки 34
2.9.4 Фланцевые соединения и штуцера 35
2.9.5 Опоры аппарата 37
2.9.6 Расчет мешалки 37
2.10 Тепловой расчет 39
3. Стандартизация 46
4. Заключение по проекту 47
5. Список использованной литературы 48
ИСПОЛЬЗУЕМЫЕ УСЛОВНЫЕ СОКРАЩЕНИЯ
АДК - Адипиновая кислота
ЭГ – Этиленгликоль
ТБТ – Тетрабутоксититан
ПЭ - Полиэфир
ВВЕДЕНИЕ
Успешно развивающееся промышленное производство сложных полиэфиров всегда было значимым для страны. Всему миру был хорошо известен натуральный полиэфир – янтарь, но путь получения искусственного полиэфира был трудным, но достижимым. Технология получения полиэфиров была разработана в 1959-1962 гг. Первое на «Казанском заводе синтетического каучука» производство полиэфиров было организовано в 1966 году, а в 1979 году введено в действие производство полиэфира ПБА, марки полиэфиров ПБА I и ПБА III – в 1986 году [1].
Едва ли найдутся отрасли народного хозяйства, где бы ни применялись полиэфиры. При этом выделяются отрасли, в которых объем их потребления особенно велик. К ним относятся: судостроение, автомобилестроение и транспортное машиностроение, строительство, химическая промышленность, электротехническая промышленность, мебельная промышленность, товары народного потребления [1].
Полиэфиры служат основой для производства уретановых каучуков, монолитных и пористых изделий методом литья, для получения оптически чувствительных уретановых полимеров, а также в качестве компонента в клеевых композициях. Полиэфиры нашли широкое применение в резинотехнической промышленности, машиностроении, при изготовлении магнитных лент, а также для изготовления заливочных и лакокрасочных материалов.
Полиэтиленадипинаты устойчивы к старению, обладают низкой летучестью и хорошими миграционными свойствами, их окраска более светлая, к экстракции углеводородами они более устойчивы, чем например полиэтиленсебацинаты.
В промышленности полиэфиры применяют в качестве пластификаторов. Введение пластификаторов в каучуки облегчает их переработку, повышает пластичность резиновой смеси, способствует уменьшению разогрева при смешивании и снижает опасность под вулканизации.
Таким образом, достаточно многообразное применение полиэфиров во многих отраслях промышленности свидетельствует о их важности и значимости как в качестве целого, так и полупродукта в составе различных композиционных материалов.
1 Технико-экономическое обоснование
Метода производства
Технико-экономическое сравнение существующих методов
Производства
Технология получения полиэфиров и на их основе – нового класса высокомолекулярных соединений – полиуретанов, превосходящих по износостойкости все известные полимерные материалы, разработана в 1959- 1962 гг. Опытное производство полиуретанов освоено на производственной базе ВНИИСК. Промышленное производство полиэфиров по непрерывной технологии организовано на «Казанском заводе синтетического каучука» в 1966 г., а в 1979г. введено в действие производство полиэфира ПБА.
Сложные полиэфиры адипиновой кислоты и различных гликолей (П-6, ПС, П6-БА, ПБА, ЭДА-50, П-9А) используются для получения полиуретанов методом литья, для вальцуемых полиуретановых каучуков, отличающихся высокими прочностными показателями, сочетанием высокой твердости с эластичностью, уникальной стойкостью к истиранию, растворителям, маслам, топливам, агрессивным средам, для получения компонент в клеевых композициях в обувной промышленности, машиностроении, при изготовлении магнитных лент, а также для изготовления заливочных и лакокрасочных материалов.
|
|
Механическое удерживание земляных масс: Механическое удерживание земляных масс на склоне обеспечивают контрфорсными сооружениями различных конструкций...
Биохимия спиртового брожения: Основу технологии получения пива составляет спиртовое брожение, - при котором сахар превращается...
Адаптации растений и животных к жизни в горах: Большое значение для жизни организмов в горах имеют степень расчленения, крутизна и экспозиционные различия склонов...
Индивидуальные и групповые автопоилки: для животных. Схемы и конструкции...
© cyberpedia.su 2017-2024 - Не является автором материалов. Исключительное право сохранено за автором текста.
Если вы не хотите, чтобы данный материал был у нас на сайте, перейдите по ссылке: Нарушение авторских прав. Мы поможем в написании вашей работы!