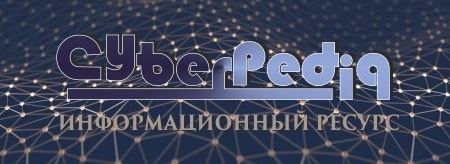
История развития хранилищ для нефти: Первые склады нефти появились в XVII веке. Они представляли собой землянные ямы-амбара глубиной 4…5 м...
Адаптации растений и животных к жизни в горах: Большое значение для жизни организмов в горах имеют степень расчленения, крутизна и экспозиционные различия склонов...
Топ:
История развития методов оптимизации: теорема Куна-Таккера, метод Лагранжа, роль выпуклости в оптимизации...
Характеристика АТП и сварочно-жестяницкого участка: Транспорт в настоящее время является одной из важнейших отраслей народного...
Генеалогическое древо Султанов Османской империи: Османские правители, вначале, будучи еще бейлербеями Анатолии, женились на дочерях византийских императоров...
Интересное:
Средства для ингаляционного наркоза: Наркоз наступает в результате вдыхания (ингаляции) средств, которое осуществляют или с помощью маски...
Лечение прогрессирующих форм рака: Одним из наиболее важных достижений экспериментальной химиотерапии опухолей, начатой в 60-х и реализованной в 70-х годах, является...
Мероприятия для защиты от морозного пучения грунтов: Инженерная защита от морозного (криогенного) пучения грунтов необходима для легких малоэтажных зданий и других сооружений...
Дисциплины:
![]() |
![]() |
5.00
из
|
Заказать работу |
|
|
Первичная аттестация. При вводе в эксплуатацию испытательное оборудование подвергается первичной аттестации, которая должна осуществляться ответственным подразделением в соответствии с положениями ГОСТ Р 8.568.
Первичная аттестация испытательного оборудования заключается в:
- экспертизе документации на него;
- экспериментальном определении его технических характеристик (допускается выборочно);
- подтверждении пригодности.
Первичная аттестация испытательного оборудования проводится комиссией, которая назначается руководителем предприятия, в составе представителей подразделения, использующего данное испытательное оборудование; метрологической службы предприятия, органов государственной метрологической службы.
Представители органов государственной метрологической службы включаются в состав комиссии в случае использования оборудования для испытаний при обязательной сертификации, а также на соответствие обязательным требованиям технических регламентов или национальных стандартов.
На первичную аттестацию испытательного оборудования должны быть представлены эксплуатационные документы по ГОСТ 2.601, программа и методика проведения первичной аттестации, методика проведения периодической аттестации (если она не изложена в эксплуатационных документах).
Результаты первичной аттестации испытательного оборудования оформляются протоколом. При положительных результатах аттестации испытательного оборудования оформляется аттестат.
Данные о проведении первичной аттестации регистрируются в формуляре или журнале, которые должны содержать номер и дату выдачи аттестата, полученные значения характеристик, срок последующей периодической аттестации, периодичность ее проведения.
|
Периодическая аттестация испытательного оборудования. В процессе эксплуатации испытательное оборудование подвергается периодической аттестации через интервалы времени, установленные в эксплуатационной документации или при его первичной аттестации, а также в случае его ремонта или модернизации. Периодическая аттестация испытательного оборудования должна осуществляться ответственным подразделением в соответствии с ГОСТ Р 8.568.
Периодическая аттестация испытательного оборудования осуществляется: 1) на плановой основе; 2) в соответствии с графиком.
Выполнение графика контролирует ответственный руководитель. Не допускается проведение работ с использованием испытательного оборудования, не прошедшего периодическую аттестацию в установленные графиками сроки.
Периодическую аттестацию испытательного оборудования проводят в сроки и в объемах, установленных в акте первичной аттестации. Номенклатура проверяемых характеристик устанавливается исходя из:
- нормированных технических характеристик оборудования;
- характеристик конкретной продукции, которые должны определяться при испытаниях на данном испытательном оборудовании.
Периодическая аттестация испытательного оборудования проводится комиссией в составе сотрудников подразделения, в котором установлено оборудование и (или) представителей метрологической службы предприятия.
Результаты периодической аттестации испытательного оборудования оформляются протоколом.
При положительных результатах периодической аттестации подтверждается возможность использования испытательного оборудования по назначению, оформляется аттестат или делается соответствующая отметка в паспорте (формуляре), испытательное оборудование идентифицируется с указанием дат проведенной и следующей аттестаций.
При отрицательных результатах периодической аттестации испытательное оборудование отстраняется от эксплуатации, в протоколе указываются корректирующие мероприятия по доведению характеристик испытательного оборудования до требуемых значений.
|
Поверка средств измерений. Средства измерений подвергаются первичной, периодической, внеочередной и инспекционной поверке. Обеспечение поверки осуществляется ответственным подразделением. Поверку проводят органы государственной метрологической службы или иные аккредитованные юридические лица в соответствии с ГОСТ 8.513 и ПР 50.2.006-94.
Первичная поверка производится на контрольно-поверочных пунктах на предприятиях, выпускающих и ремонтирующих средства измерений. Первичной поверке подлежат средства измерений утвержденных типов при выпуске из производства и ремонта, при ввозе по импорту.
Периодической поверке подлежат средства измерений, находящиеся в эксплуатации или на хранении, через определенные межповерочные интервалы. Первый межповерочный интервал устанавливается при утверждении типа. Перечни средств измерений, подлежащих поверке, составляют их владельцы по согласованию с органами государственной метрологической службы, которые контролируют их полноту и правильность. Периодическую поверку:
- должен проходить каждый экземпляр средств измерений;
- могут не проходить средства измерений, находящиеся на длительном хранении.
Внеочередная поверка проводится при эксплуатации (хранении) средств измерений при:
- повреждении знака поверительного клейма;
- утрате свидетельства о поверке;
- вводе в эксплуатацию после длительного хранения;
- нерегламентированном воздействии на средство измерений;
- неудовлетворительной работе.
Инспекционная поверка проводится для выявления пригодности средств измерений к применению при осуществлении государственного метрологического надзора.
Органы государственной метрологической службы осуществляют поверку средств измерений на основании согласованных графиков, составляемых ответственным подразделением предприятия. Сроки представления графиков устанавливают органы государственной метрологической службы. При согласовании графиков определяется место, сроки, объем поверки, оплата работ.
Средства измерений должны представляться на поверку расконсервированными, вместе с техническим описанием и инструкцией по эксплуатации; методикой проверки и паспортом (свидетельством) о последней поверке; необходимыми комплектующими устройствами.
|
Если средство измерения признается пригодным к применению, то на него или техническую документацию наносится оттиск поверительного клейма или выдается свидетельство о поверке.
Если средство измерений признано непригодным к применению:
• оттиск поверительного клейма гасится;
• свидетельство о поверке аннулируется;
• делается соответствующая запись в технической документации или выписывается извещение о непригодности.
Калибровка средств измерений. Работы по калибровке средств измерений осуществляются метрологическими службами юридических лиц, аккредитованных на право проведения указанных работ, или органами государственной метрологической службы в соответствии с ГОСТ 8.513 и ПР 50.2.016-94.
Аккредитация метрологических служб юридических лиц осуществляется органами государственной метрологической службы. При проведении аккредитации устанавливаются: 1) область деятельности метрологической службы по проведению калибровочных работ; 2) средства калибровки; 3) государственные эталоны; 4) нормативные документы по организации и проведению калибровочных работ; 5) требования к помещениям и персоналу.
Средства измерений принимаются на калибровку в соответствии с графиком калибровки. Если калибровка проводится органами государственной метрологической службы, предприятие заключает с ними договор на проведение этой работы. График и договор готовит метрологическая служба депо.
Если средство измерения признается пригодным к применению, то на него или техническую документацию наносится калибровочный знак или выдается сертификат о калибровке; соответствующая запись вносится ответственным подразделением в эксплуатационные документы на средство измерений.
Если средство измерений признается непригодным к применению, то калибровочный знак гасится, сертификат о калибровке аннулируется, соответствующая запись вносится ответственным подразделением в эксплуатационные документы на средство измерений.
|
Срок хранения документации с результатами калибровки должен составлять не менее срока, назначенного до следующей калибровки. Если этот срок не установлен, документация хранится не менее года. Документация хранится в ответственном подразделении.
Хранение. Условия хранения временно не используемых или резервных средств измерений и испытательного оборудования должны обеспечивать их сохранность в работоспособном состоянии, защиту от утраты, повреждений, вредных воздействий, преждевременного износа.
Хранение обеспечивается ответственным подразделением, если иное (например, для крупногабаритного испытательного оборудования) не определено руководством предприятия.
Стандартизированные средства измерений и испытательное оборудование должны храниться в условиях, установленных в нормативных документах на них.
2.5. Метрологическое обеспечение вагоносборочного участка
при ремонте тормозного оборудования и колесных пар
Метрологическое обеспечение включает в себя комплекс организационно-технических мероприятий, направленных на выполнение требований настоящего технологического процесса и нормативно-технической документации, указанной в приложении № 9, проводимых метрологической службой вагонного депо согласно Положению о метрологической службе депо. Организация и общее руководство работами по обеспечению единства и требуемой точности измерений в депо возложены на главного инженера ремонтного вагонного депо, проводящего эту работу через метролога депо.
Для обеспечения качественного осмотра, ремонта тормозного оборудования вагонов используются средства измерений (СИ) и средства допускового контроля (СДК), для испытания тормозного оборудования применяются системы диагностики.
Ответственным за обеспечение цеха поверенным измерительным инструментом является метролог депо.
На производственных участках цеха должен находится исправный и поверенный (калиброванный) измерительный инструмент в номенклатуре и количестве, предусмотренными настоящим технологическим процессом.
Периодическая поверка (калибровка) СИ и СДК производится по соответствующим методикам в сроки, установленные графиком поверки (калибровки), первичная - при наличии признаков неисправности, после ремонта.
Положительные результаты поверки (калибровки) СИ и СДК удостоверяются паспортом, выданным метрологом депо, с указанием даты и места проведения контроля. На манометрах наносится калибровочный знак (клеймо) с указанием даты проведения контроля.
При отрицательных результатах поверки делается отметка в паспорте «подлежит ремонту» или «подлежит списанию». Основной документ (паспорт или свидетельство о поверке (калибровке)), выданный организацией, проводившей поверку (калибровку), находится у метролога депо.
|
Аттестация испытательного оборудования состоит из первичной, периодической и при необходимости внеочередной аттестации.
Периодической аттестации подвергаются все испытательное оборудование в процессе его эксплуатации. Периодическая аттестации проводится в сроки, установленные в графике аттестации испытательного оборудования по программам и методикам аттестации. Средства измерений, встроенные в испытательное оборудование, а также принимаемые при его аттестации, должны быть поверены. Результаты аттестаций оформляются протоколом и находятся у метролога депо.
При положительных результатах аттестации на испытательное оборудование наносится бирка с указанием даты очередной аттестации. Испытательное оборудование, признанное неисправным по результатам периодической аттестации или не прошедшее аттестацию в установленный срок, к эксплуатации не допускается.
Техническое обслуживание пневматических стендов для испытания тормозных приборов производится через каждые 3 месяца. Порядок осмотра и требования по герметичности соединений такие же, как для тормозного оборудования вагонов. После осмотра и ремонта стенд должен принять мастер. На видном месте на стенде наносится надпись с указанием даты выполнения периодического осмотра. Результаты осмотра оформляются в журнале.
Техническое обслуживание автоматических стендов УКВР-2, УКАР-2М, УКРП-1, установки для испытания пружин 1110/2.5, ремонтных столов для главной СГВР-1 и магистральной СМВР-1 частей воздухораспределителей проводится один раз в смену перед началом работы.
Мастер цеха АКП является ответственным лицом, отвечающим за правильную эксплуатацию средств измерений и средств допускового контроля, их хранение.
2.6. Система контроля параметров технологического процесса
и КШМ
Основным техническим базисом для проведения контроля параметров технологического процесса и горячештамповочного модуля (комплекса) являются информационно-измерительные системы, представляющие совокупность различного типа датчиков и устройств, объединяемых в одно целое - систему контроля на основе единого метрологического, информационного и программного обеспечения и обладающих необходимой для получения достоверных результатов степенью системной совместимости друг с другом.
В общем случае получение информации состоит из следующих этапов.
1. Первичное измерительное преобразование физического (неэлектрического) параметра в электрический сигнал (датчики).
2. Вторичное преобразование информативной составляющей электрического сигнала к виду, удобному для последующей регистрации и обработки (сопутствующая аппаратура для датчиков, фильтры, модуляторы, устройства).
3. Предварительная обработка и регистрация результатов измерения
(функциональные и масштабные преобразователи, аналого-цифровые преобразователи (АЦП), специализированные вычислительные устройства, регистраторы и накопители информации в аналоговом и цифровом виде).
4. Конечная обработка и получение результатов для передачи в системы диагностики, принятия решений и прогнозирования, оперативного управления.
Первые три этапа составляют процесс сбора информации о параметрах ГПМ ОМД, последний - обработку.
Сбор информации может осуществляться с помощью устройств контроля, которые подразделяются на: 1) датчики непосредственного получения информации, например, концевые выключатели и сигнализаторы предельных значений и т.д.; 2) измерительные функциональные преобразователи (датчики), например, преобразователи параметров измерений, преобразователи вида сигналов и т.д.
Датчик преобразует измеренную величину в отображаемый сигнал, а преобразователь – отображаемый сигнал в выходной. Выходной сигнал в сопрягаемых устройствах единой измерительной системы является одновременно и принятым унифицированным сигналом. Преобразование в требуемый унифицированный сигнал может происходить в несколько ступеней. При этом удлиняется измерительная цепь и увеличивается количество возможных источников помех. Применение инвариантных волоконно-оптических измерительных функциональных преобразователей позволит повысить точность, стабильность измерений (рис. 5). Ввод результатов измерения в систему контроля может производиться непрерывно или периодически (с постоянной или переменной частотой).
В некоторых случаях возможен разовый опрос, например, ввод результатов измерений по определению химсостава проката перед резкой на мерные заготовки (заготовительный модуль).
а) б)
в) г)
Рис. 5. Волоконно-оптические датчики (функциональные преобразователи)
перемещений, усилий, деформаций ВП:
а) угловых; б) линейных; в) последовательное соединение световодных датчиков с коэффициентом передачи Ф; г) физическая модель чувствительного элемента волоконно-оптического датчика
Частота опроса ограничивается скоростью преобразования в АЦП, быстродействием микропроцессора и продолжительностью последующей обработки введенной информации. Наиболее распространенная частота опроса составляет 8-100 Гц. В некоторых случаях частота опроса зависит от величины показателя работоспособности (опрос с переменной частотой). Это вызвано тем, что по мере износа штампового инструмента размеры поковки приближаются к зоне риска, т.е. к нижней границе допуска. Изменение частоты опроса (частоты измерений) целесообразно тогда, когда скорость изменения показателя работоспособности растет по мере приближения к границам зоны риска. Организация опроса зависит от вида контроля. Так для контроля, не зависящего от обрабатываемой заготовки и осуществляемого всегда при работе модуля, применяется отдельная программа контроля, постоянно хранящаяся в памяти системы контроля.
При контроле, определяемом технологией обработки конкретной заготовки (поковки), периодичность измерений должна задаваться программой контроля, составленной для данного изделия.
Наибольшее распространение получили следующие виды контроля:
1) контроль заготовки (температура, масса, химический состав и т.д.);
2) контроль состояния штампового инструмента (износ, температура нагрева штампов, размеры и т.д.);
3) контроль поковки;
4) контроль положения заготовки;
5) контроль системы диагностического управления (СДУ) КШМ, ГПМ.
В тех случаях, когда не может быть получена необходимая частота измерения, применяют метод аппаратного сравнения аналоговых величин. При этом методе сравнение с эталоном выполняется вне микропроцессора. Процессор формирует код эталона для получения на выходе цифро-аналогового преобразователя (ЦАП) эталонного (опорного) напряжения U оп, которое подается в схему сравнения. При достижении U и³ U оп, где U и- измеренное напряжение, поступающее от датчика, схема вырабатывает сигнал отклонения от нормы. Поступающий на соответствующий вход процессора сигнал обрабатывается программой прерывания. Данный метод используется в известных системах управления ВП.
При разработке специализированных систем контроля часто объединяются с первыми также и средства обработки, особенно если результаты испытаний достаточно представлять только в алфавитно-цифровой форме, что является характерным для операций контроля и диагностирования. Вo многих случаях оценку параметров ГПМ ОМД необходимо проводить одновременно в режиме проведения измерений.
Общую задачу обработки измерений параметров ВП и ГПМ(К) на его основе условно можно разбить на три этапа.
1. Первичная обработка. Включает в себя нормировку измерений, приведение к единой выбранной системе отсчета, первичную статистическую обработку, фильтрацию и т.д., т.е. цель первого этапа – получение первичных результатов по известным стандартным методикам.
2. Идентификация модели измерений. Этот этап определяет параметры и модель канала измерений, т.е. устанавливает функциональную связь между количественными значениями измеряемой величины и аргументом:
где Z - значение измерения, x - аргумент, e - ошибка измерения, B - оператор функциональной связи, y - искомый параметр.
3. Идентификация модели канала динамики. Этот этап определяет параметры и модель канала динамики, т.е. устанавливает функциональную связь между оценкой значения искомого параметра, измерением и аргументом
,
где - оценка искомого параметра, d - ошибка неточности значения функциональной зависимости, А - оператор функциональной связи.
Контроль (оценка) достоверности должен определять доверительность исходных данных (параметров). Он заключается в проверке наличия возможных ошибок в аппаратуре, в контроле очевидных ошибок. Например, дефектов датчиков, грубых ошибок измерений. Причинами возникновения ошибок могут являться как долговременные явления (обрыв проводников, старение датчиков, загрязнение контактов и т.д.), так и кратковременные (импульсы помех в линиях связи, обусловленные индуктивными и емкостными наводками, короткое замыкание и т.д.).
В обычных устройствах индикации высокочастотные составляющие импульсов помех подавляют за счет инерционности, свойственной механическим устройствам. Кратковременные помехи при этом остаются незамеченными. Однако высокочастотные напряжения помех воспринимаются за счет быстрого считывания измеренных значений. При этом ошибки аппаратуры могут подавляться и не проявиться при повторном опросе.
Система контроля (СК) должна разрабатываться по функционально-модульной структуре, для которой должно быть характерно четкое разделение программных и аппаратных уровней. Модульная структура позволяет легко добавлять функции к системе, а также изменять или удалять часть системы.
В зависимости от места в структуре СУ ГПМ ОМД вытекают требования к датчикам (функциональным преобразователям), основными из которых являются:
- бесконтактность, инвариантность преобразования разнородных физических величин в единую физическую величину, связанную с входными параметрами определенной функциональной зависимостью;
- универсальность - воспроизведение практически любых функциональных зависимостей без изменения конструкции преобразователя, а также возможность применения волоконно-оптических элементов в качестве первичного преобразователя-датчика;
- точность, повторяемость и стабильность воспроизведения заданной функции в широком диапазоне изменения входных параметров;
- надежность;
- быстродействие;
- технологичность конструкции; чувствительность к информативным параметрам; габаритно-массовые и эксплуатационные показатели;
- унификация; работа в реальном режиме времени; минимизация затрат.
Характеристики точности и быстродействия являются основными характеристиками датчиков (устройств), определяющими его качество. Если задача повышения точности является издавна традиционной, то требование повышения быстродействия, возможности работы в реальном режиме времени - отличительная черта современного этапа развития средств контроля.
В условиях ГПС быстродействие оказывается, иногда, даже более важным параметром, чем точность, так как часто результат функционального преобразования необходимо получить с фиксированной, наперед заданной точностью, но через минимально возможный отрезок времени. Например, быстродействие исполнительного органа КШМ (ВП), контроль температуры, массы, химсостава заготовки перед штамповкой, контроль зазора в направляющих ползуна и пары винт-гайка и т.д.
В наибольшей степени этим требованиям удовлетворяют цифровые бесконтактные датчики, не требующие тарировки в процессе работы и не имеющие изнашиваемых частей (рис. 6). Диагностирование состояния инструмента (температура, деформация, износ) позволяет предупредить поломку инструмента и выход размеров заготовки за пределы поля допуска. По температуре инструмента можно судить о стабильности процесса деформирования и макроструктуре поковок и предупредить возможную потерю устойчивости системы (норма, риск, отказ).
Рис.6. Обобщенная структурная схема
первичного функционального преобразователя (датчика)
Контроль энергетических и кинематических параметров подвижных частей кузнечной машины дает возможность определить запасенную энергию и усилие деформирования. Диагностирование состояния механической системы кузнечной машины (например, измерение напряжений в станине пресса) может предупредить перегрузку и поломку базовых деталей, а также позволяет косвенно судить о состоянии деформируемой заготовки. Контроль параметров КШМ ударного действия связан с трудностями обеспечения надежной и безотказной работы датчиков на различных этапах машинного цикла, продолжительность которого составляет несколько долей секунды. Ускорение, которое испытывает ударная масса в начальный период деформирования, может достигать 1000g, что затрудняет установку на ней средств контроля.
Рассмотрим существующие методы и устройства контроля основных параметров КШМ и технологического процесса, которые можно использовать при разработке и создании систем активного контроля и диагностики.
При штамповке на КШМ силовой режим отражает колебания параметров технологического процесса, а по величине изменения усилий деформирования можно судить об отклонении некоторых из них от заданного значения.
Для контроля силового режима, развиваемого кузнечной машиной, используют магнитоупругие датчики, которые служат для контроля динамических нагрузок с частотами от 1 до 2 кГц, и тензодатчики. Точность измерений не превышает 10 %. Метод применяется в основном для научных исследований.
Для измерения кинематических параметров пресса (рис. 7) могут использоваться фотоэлектрические, энергетические, параметрические датчики, использующие тот или иной метод измерения.
Наибольший интерес представляют бесконтактные датчики измерения. Отсутствие механической связи с подвижными частями пресса повышает их надежность, долговечность при требуемой точности измерений.
Известны бесконтактные датчики измерений перемещений рабочих частей пресса с использованием фотоэлектрического метода измерения, обладающие рядом преимуществ перед контактными.
Для измерения скорости рабочих частей пресса могут использоваться датчики скорости, которые в зависимости от того, какой метод использован при их разработке, подразделяются на контактные (генераторные) и бесконтактные (емкостные, индуктивные, магнитоэлектрические).
Рис. 7. Классификация методов измерений параметров КШМ
Для контроля температуры заготовок, штампового инструмента применяют контактные и бесконтактные способы и устройства.
К контактным относятся различного рода термопары, точность измерения которых достаточно высока. Термопары позволяют контролировать в широком диапазоне температуру нагрева заготовок штамповой оснастки, тепловые деформации инструмента. Однако, низкая стабильность показаний, инерционность не позволяют создавать системы контроля с быстрой обратной связью.
Особый интерес представляют собой устройства бесконтактного контроля температуры с использованием методов радиационной пирометрии.
Из функциональной зависимости (рис. 8) следует, что часть излучения находится в инфракрасной области спектра, другая - в видимой. При измерении необходимо учитывать характеристики пропускания воздуха (рис. 9). При измерении температуры заготовка может облучаться окружающей средой (рис. 10). Суммарное излучение Wc в этом случае будет Wc=W+(1-e)W¢ где W - спектральное излучение абсолютно черного тела; W¢ - излучение окружающей среды; e - коэффициент лучеиспускания. Влияние e на Wc может быть минимальным при проведении измерений на коротких длинах волн l. В большинстве устройств для контроля температуры принят метод измерения суммарного потока излучения, что вынуждает при измерении вносить поправки.
Рис. 8. Зависимость спектральной излучательной способности от длины волны l
Рис.9. Пропускание измеряемых лучей атмосферой
Рис. 10. Суммарное излучение поверхности с коэффициентом лучеиспускания e
Разработанные на основе этого метода устройства контроля температуры в процессе эксплуатации недостаточно удовлетворяют требованиям на производстве, предъявляемым к ним. Низкая точность и стабильность показаний, инерционность, сложность тарировки не позволяют создать системы контроля с быстрой обратной связью.
При разработке новых устройств следует уделить особое внимание разделению этих компонентов излучения от объектов и по возможности уменьшить до малых значений. Этого можно достигнуть, используя метод спектрального (цветового) распределения плотности энергии в потоке излучения или метод измерения интенсивности излучения в узком спектральном диапазоне, который заключается в том, что температура измеряется на строго определенном участке спектрального излучения. Использование этого метода позволит не только измерять температуру на расстоянии и тем самым устранить термическое воздействие на датчик температуры, увеличить срок его службы, но и повысить точность измерения температуры.
Для точного измерения температуры требуются малоинерционные бесконтактные датчики температуры, работающие на определенных участках спектра. Процесс измерения требует взаимодействия излучения с материалом датчика, в результате которого образуется электрический выходной сигнал, подлежащий измерению.
Применяется два типа взаимодействий, соответствующие двум различным типам датчиков: термические и фотонные (квантовые).
У термических датчиков быстродействие относительно мало, постоянная времени у них измеряется миллисекундами, тогда как у фотонных – микросекундами.
Фотонные датчики являются селективными - они реагируют на излучение только в определенных участках спектра. Использование данной особенности позволяет точно и быстро измерить температуру быстродвижущейся или находящейся в штампе пресса (нагревательном устройстве) заготовки. Это позволяет создать системы контроля и диагностики технологических процессов горячей объемной штамповки с обратной связью.
Ответственным элементом при создании как систем управления КШМ, так и ГПМ ОМД является устройство для контроля температуры нагрева заготовок перед штамповкой. От точности измерения, стабильности показаний, надежности и долговечности его работы зависит качество поковок, надежность и стабильность работы как пресса, так и модуля, долговечность штампового инструмента.
Устройства контроля температуры заготовок (типа ИРТ), как правило, работают в следующих условиях: вибрации с ускорениями до 25 g в диапазоне частот 8-90 Гц; ударные нагрузки при длительности 2-20 мл/с; влажность до 80 % при 40 °С; наличие в окружающей среде графитовой пыли высокой концентрации, а также окалины на горячей заготовке; время непрерывной работы 8-16 ч.
Для работы в этих условиях к ним предъявляются следующие требования:
1. Допустимая погрешность определения температуры заготовки - 1 %.
2. Диапазон измерения температуры – 700-1250 °С.
3. Обеспечивать работоспособность при температуре 5-55 °С.
4. Иметь выходы на системы диагностики и управления энергией КШМ.
5. Иметь регулируемый уровень по заданному температурному диапазону штамповки с визуальным контролем.
6. Обеспечивать наработку на отказ не менее 1000 ч с устранением неисправности в течение 15-20 мин.
При оценке каждого метода контроля массы объема заготовок необходимо учитывать, что суммарная погрешность дозирования не должна превышать 1,5-2,5 %. Вследствие этого точность датчика должна быть не ниже ± 0,5 %.
Известны устройства, обеспечивающие дозирование массы (объема) заготовки с точностью ± 1,0 % (рис. 11, 12). Использование метода вихревых токов позволяет контролировать химический состав материала заготовки, его твердость, структурное состояние, внутренние напряжения, дефекты в поковках и размеры их сечений. Внутренние дефекты в поковках определяют также ультразвуковым методом.
Рис. 11. Устройство дозирования объема заготовок с гидравлическим датчиком
Рис. 12. Устройство для бесконтактного контроля массы и автоматической сортировки металлических штучных заготовок:
1 – индукционный чувствительный элемент; 2 – измерительный блок; 3 – усилитель;
4 – генератор высокой частоты; 5 – сортировочный управляющий механизм;
6 – блок цифровой индикации; 7- бункер заготовок
В условиях современного кузнечного производства эффективность технологического процесса в значительной степени зависит от вида применяемой заготовки. Известны случаи, когда экономический эффект автоматизированного технологического процесса сводился на нет из-за применения нерациональной заготовки. В настоящее время подавляющее число поковок штампуют с облоем. На облой расходуется не менее 20 % материала, перерабатываемого в кузнечных цехах. Вес облоя у большинства поковок достигает 15-20 %, а у мелких - 50-70 % от веса штампованной детали.
Значительная экономия металла может быть получена при переходе от обычной штамповки с облоем на точную штамповку в закрытых штампах. Однако широкое внедрение штамповки в закрытых штампах без дозирования заготовок по массе (объему) невозможно, так как избыток металла в заготовке влечет за собой чрезмерные удельные давления, интенсивный износ штампов, перегрузку оборудования, снижение точности поковок и т.д.
В последние годы для получения относительно точных поковок используют холоднотянутый прокат, а также применяют штампы с компенсаторами. Однако это не обеспечивает экономичного решения проблемы вследствие дороговизны.
Исходя из особенностей технологического процесса точной объемной штамповки, устройства контроля и дозирования массы (объема) заготовок должны удовлетворять следующим основным требованиям:
1) автоматически регулировать длину продвижения прутка для отрезания последующей заготовки на основе результатов контроля массы ранее отрезанных заготовок;
2) производительность должна быть не менее чем у КШМ при высокой стабильности показаний;
3) бесконтактно обеспечивать выходной сигнал в систему контроля, диагностики и управления КШМ;
4) быть универсальным по отношению к различным профилям проката и маркам материала;
5) обеспечивать точность измерения до 2,5 % при массе заготовок до 2 кг, до 1,5 % - у заготовок весом 2-5 кг, до 1 % - у заготовок весом более 5 кг;
6) обеспечивать высокий коэффициент эксплуатационной надежности.
С учетом вышеизложенного, для контроля и диагностики температуры нагрева заготовок перед штамповкой рекомендуется применять устройство типа ИРТ (А.с. 801931, А.с. 1300439, А.с. 1323152, А.с. 1303207), а для контроля и диагностики параметров КШМ рекомендуется применять многофункциональное волоконно-оптическое устройство для контроля максимальной деформации и усилия деформирования кузнечно-штамповочных машин (А.с. 1696914).
|
|
Эмиссия газов от очистных сооружений канализации: В последние годы внимание мирового сообщества сосредоточено на экологических проблемах...
История создания датчика движения: Первый прибор для обнаружения движения был изобретен немецким физиком Генрихом Герцем...
Своеобразие русской архитектуры: Основной материал – дерево – быстрота постройки, но недолговечность и необходимость деления...
Адаптации растений и животных к жизни в горах: Большое значение для жизни организмов в горах имеют степень расчленения, крутизна и экспозиционные различия склонов...
© cyberpedia.su 2017-2024 - Не является автором материалов. Исключительное право сохранено за автором текста.
Если вы не хотите, чтобы данный материал был у нас на сайте, перейдите по ссылке: Нарушение авторских прав. Мы поможем в написании вашей работы!