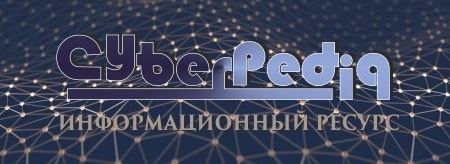
Особенности сооружения опор в сложных условиях: Сооружение ВЛ в районах с суровыми климатическими и тяжелыми геологическими условиями...
Таксономические единицы (категории) растений: Каждая система классификации состоит из определённых соподчиненных друг другу...
Топ:
Характеристика АТП и сварочно-жестяницкого участка: Транспорт в настоящее время является одной из важнейших отраслей народного...
Определение места расположения распределительного центра: Фирма реализует продукцию на рынках сбыта и имеет постоянных поставщиков в разных регионах. Увеличение объема продаж...
Когда производится ограждение поезда, остановившегося на перегоне: Во всех случаях немедленно должно быть ограждено место препятствия для движения поездов на смежном пути двухпутного...
Интересное:
Мероприятия для защиты от морозного пучения грунтов: Инженерная защита от морозного (криогенного) пучения грунтов необходима для легких малоэтажных зданий и других сооружений...
Инженерная защита территорий, зданий и сооружений от опасных геологических процессов: Изучение оползневых явлений, оценка устойчивости склонов и проектирование противооползневых сооружений — актуальнейшие задачи, стоящие перед отечественными...
Лечение прогрессирующих форм рака: Одним из наиболее важных достижений экспериментальной химиотерапии опухолей, начатой в 60-х и реализованной в 70-х годах, является...
Дисциплины:
![]() |
![]() |
5.00
из
|
Заказать работу |
|
|
Сплавы алюминия с магнием именуются магналиями. АМг6 - это магналий высокой пластичности, но средней прочности. Он обладает хорошей коррозионной стойкостью, хорошей обрабатываемостью резаньем и хорошо обрабатывается давлением. Однако, в ряду прочих широко известных магналиев этот сплав занимает первое место по прочности и твёрдости, но последнее место по коррозионной стойкости и последнее место по пластическим свойствам. Хотя он хорошо сваривается, но сварной шов АМг6 более пористый чем у того же АМг3 и часто требует дополнительной обработки. Это один из самых лёгких сплавов алюминия с плотностью 2,65 г/см². Из АМг6 выпускают широкий спектр металлопроката с различным состоянием материала. Сплав относится к деформируемым, но не термоупрочняемым. [8]
Таблица 1. Химический состав АМг6 по ГОСТ 4784-97. [9]
Массовая доля элементов, % | ||||||
Кремний Si | Железо Fe | Медь Cu | Марганец Mn | Магний Mg | Цинк Zn | Алюминий Al |
0,4 | 0,4 | 0,1 | 0,5-0,8 | 5,8-6,8 | 0,2 | 91.1 - 93.68 |
Таблица 2. Механические свойства сплава АМг6 при Т=20oС
Прокат | Толщина или диаметр, мм | σв, (МПа) | σ0,2, (МПа) | δ5, (%) | σсж, МПа |
Лист плакированный отожженный | |||||
Лист плакированный нагартованный 20% | |||||
Лист плакированный нагартованный 30% | |||||
Плита нагартованная 16% | |||||
Профиль горячекатаный отожженный | 20,5 | ||||
Профиль горячекатаный без термообработки | 19,5 |
Алюминий хрупок в нагретом состоянии, однако, главным затруднением при сварке алюминия является лёгкая его окисляемость с образованием весьма тугоплавкого и механически прочного окисла Al2O3, который плавится при температуре 2050°C, что превышает температуру кипения алюминия (°C). Окись алюминия представляет собой чрезвычайно прочное химическое соединение, которое плохо поддаётся действию флюсующих материалов, ввиду своего химически нейтрального характера. Образование окиси алюминия является основным затруднением при сварке этого металла. Алюминий можно сваривать как плавлением, газопламенной дугой, так и давлением на электрических контактных сварочных машинах. Наиболее распространена газовая ацетиленокислородная сварка алюминия. [10]
|
Подготовка под сварку заключается в освобождении Al от консервирующей смазки гальваническим или механическим путем, разделки кромок (если необходимо), обезжиривание и удаление толстой оксидной пленки Al2O3, с температурой плавления 2050○С. [11]
При точечной и шовной сварке полное разрушение и удаление поверхностных пленок, как правило, более тугоплавких, чем основной металл, происходит в жидком металле за счет электродинамических сил. Действие этих сил приходит к интенсивному перемешиванию расплавленного металла. В результате взаимодействия тока с собственным магнитным потоком при постоянной плотности тока действует элементарная сила, которая в жидком ядре давление распределяет по параболическому закону. Подобное распределение давления вызывает циркуляцию жидкости от центра к периферии.
Таким образом частицы пленок, образовавшиеся в результате механического разрушения на 1 этапе, увлекаются потоком металла и замешиваются в ядре, а под действием элементарной силы частицы перемещаются от центра к периферии ядра. [12]
В данной курсовой работе большой объём производства: 20000 изделий в год.
Поскольку контактная шовная сварка обладает достаточно быстрой скоростью выполнения сварочных работ, , остальное время будет производится подготовка свариваемого металла под сварку, а именно: механическая обработка мелкой наждачной бумагой и обезжиривание.
Выбор способа сварки.
|
Контактная сварка - это процесс образования соединения в результате нагрева металла проходящим через него электрическим током и пластической деформации зоны соединения под действием сжимающего усилия. ГОСТ 15878-79 «Контактная сварка. Соединения сварные. Конструктивные элементы».
Преимущества контактной сварки перед другими способами:
- Высокая производительность (время сварки одной точки или стыка составляет 0,02... 1,0 с)
- Малый расход вспомогательных материалов (воды, воздуха)
- Высокое качество и надежность сварных соединений при небольшом числе управляемых параметров режима, что снижает требования к квалификации сварщика
Недостатки: относительная сложность оборудования, трудность неразрушающего контроля сварных соединений.
Основные способы контактной сварки - это точечная, шовная (роликовая) и стыковая сварка.
Машины для контактной сварки бывают стационарными, передвижными и подвесными (сварочные клещи). По роду тока в сварочном контуре могут быть машины переменного или постоянного тока от импульса тока, выпрямленного в первичной цепи сварочного трансформатора или от разряда конденсатора. По способу сварки различают машины для точечной, рельефной, шовной и стыковой сварки.
Любая машина для контактной сварки состоит из электрической и механической частей, пневмо- или гидросистемы и системы водяного охлаждения (рис. 4).
Электрическая часть включает в себя силовой сварочный трансформатор 1 с переключателем ступеней 2 его первичной обмотки, с помощью которого регулируют вторичное напряжение, вторичный сварочный контур 3 для подвода сварочного тока к деталям, прерыватель 4 первичной цепи сварочного трансформатора 1 и регулятор 5 цикла сварки, обеспечивающий заданную последовательность операций цикла и регулировку параметров режима сварки.
Рис. 4. Типовые схемы машин для контактной точечной (а), шовной (б) и стыковой (в) сварки:
1 - трансформатор; 2 - переключатель ступеней; 3 - вторичный сварочный контур; 4 - прерыватель первичной цепи; 5 - регулятор; 6 - привод сжатия; 7- привод зажатия деталей; 8 - привод осадки деталей; 9 - привод вращения роликов; 10- аппаратура подготовки; 11 - орган включения
Механическая часть состоит из привода сжатия 6 точечных и шовных машин, привода 7 зажатия деталей и привода 8 осадки деталей стыковых машин. Шовные машины снабжены приводом 9 вращения роликов.
|
Пневмогидравлическая система состоит из аппаратуры 10 подготовки (фильтры, лубрикаторы, которые смазывают движущиеся части), регулирования (редукторы, манометры, дросселирующие клапаны) и подвода воздуха к приводу 6 (электропневматические клапаны, запорные вентили, краны, штуцера).
Система водяного охлаждения включает в себя штуцера разводящей и приемной гребенок, охлаждаемые водой полости в трансформаторе 1 и вторичном контуре 3, разводящие шланги, запорные вентили и гидравлические реле, отключающие машину, если вода отсутствует или ее мало.
Все машины снабжены органом включения 11. У точечных и шовных машин это ножная педаль с контактами, у стыковых - это комплект кнопок. С органов управления поступают команды на сжатие "С" электродов или зажатие "3" деталей, на включение "Т" и отключение "О" сварочного тока, на вращение "В" роликов, на включение "а" регулятора цикла сварки. Эти команды отрабатываются соответствующими блоками машины, обеспечивая выполнение операций цикла сварки.
Кроме универсальных применяются специальные машины, приспособленные для сварки конкретных конструкций и типов размеров изделий. Примером могут служить машины для контактной точечной сварки кузовов автомобилей, встроенные в автоматические линии, машины для стыковой сварки оплавлением продольных швов труб в прокатном производстве.
Электроды в контактной сварке служат для замыкания вторичного контура через свариваемые детали. Кроме этого при шовной сварке электроды-ролики перемещают свариваемые детали и удерживают их в процессе нагрева и осадки.
Важнейшая характеристика электродов - стойкость, способность сохранять исходную форму, размеры и свойства при нагреве рабочей поверхности до температуры 600○ С и ударных усилиях сжатия до 5 кг/мм2. Электроды для точечной сварки - это быстроизнашивающийся сменный инструмент сварочной машины. Для изготовления электродов используют медь и жаропрочные медные сплавы - бронзы. Это может быть хромоциркониевая бронза БрХЦрА; кадмиевая БрКд1; хромистая БрХ; бронза, легированная никелем, титаном и бериллием БрНТБ или кремний-никелевая бронза БрКН-1-4. Последние две бронзы обладают повышенной износостойкостью, из них можно изготавливать электроды-губки стыковых машин. Материалы для электродов должны обладать также высокой электро- и теплопроводностью, чтобы их нагрев в процессе сварки был меньше. Температура разупрочнения бронз не превышает 0,5 их температуры плавления, а рабочая поверхность электрода нагревается до 0,6 ТПЛАВ. При таких условиях электродные бронзы относительно быстро разупрочняются. Повысить износостойкость электродов можно, используя технологические факторы. Сварку алюминиевых и магниевых сплавов лучше производить на конденсаторных машинах, а не на машинах переменного тока. Вместо механической зачистки нужна химическая очистка поверхности, травление и пассивация. Расстояние l от рабочей поверхности до дна охлаждающего канала не должно превышать 10...12 мм, увеличение его до 15 мм повышает износ электрода в 2 раза. При сварке черных металлов стойкость электродов можно повысить в 3...4 раза только за счет сферической заточки электрода и снижения темпа сварки до 40...60 точек в минуту.
|
Электрод должен иметь минимальную массу, удобно и надежно устанавливаться на сварочной машине. Диаметр D должен обеспечивать устойчивость электрода против изгиба при сжатии его усилием сварки, а также возможность захвата инструментом для снятия. Внутренний диаметр должен обеспечивать ввод трубки с охлаждающей водой и выход воды, обычно d0 = 8 мм. Длина конусной части для крепления электрода в свече машины l1 <= 1,2 D. Угол конусности 1:10 при D <25 мм и 1: 5 при D> 32 мм. Диаметр рабочей части электрода выбирают в зависимости от толщины кромок свариваемых деталей dЭ = 3S. Стойкость электродов с наружным посадочным конусом обычно не превышает 20 000 сварок.
Электроды-ролики шовных машин имеют форму дисков. Ширина рабочей поверхности ролика В и его толщина Н зависят от толщины S свариваемой детали.
При подготовке поверхностей к контактной сварке должны выполняться три основных требования: в контактах электрод-деталь должно быть обеспечено как можно меньшее электрическое сопротивление КЭ-Д —> min), в контакте деталь-деталь сопротивление должно быть одинаковым по всей площади контакта. Сопрягаемые поверхности деталей должны быть ровными, плоскости их стыка при сварке должны совпадать.
Выбор конкретного способа подготовки поверхностей определяется материалом деталей, исходным состоянием их поверхностей, характером производства. Для штучного и мелкосерийного производства необходимо предусмотреть операции правки, рихтовки, обезжиривания, травления или зачистки, механической обработки. В условиях крупносерийного и массового производства, где обеспечивается высокое качество исходных материалов в заготовительном и штампопрессовом производствах, подготовку поверхностей перед сваркой можно не делать. Исключение составляют детали из алюминиевых сплавов, требующих обработки поверхности не ранее чем за 10 ч до сварки.
|
Критерием качества подготовки поверхности является величина контактных сопротивлений RЭ-Д и RД-Д. Для их измерения детали зажимают между электродами сварочной машины, но сварочный ток не включают. Сопротивление измеряют микроомметром при помощи щупов. Для сталей сопротивление более 200 мкОм свидетельствует о плохом качестве поверхности. Высокое RЭ-Д приводит к перегреву электродов и подплавлению поверхности деталей, вследствие чего происходит наружный и внутренний выплеск металла и образуется чрезмерная вмятина под электродами.
Шовная сварка – способ, при котором детали, образующие нахлесточные соединения, свариваются в месте соприкосновения. При перекрытии точек образуется прочноплотный шов, а без перекрытия – прочный шов или ряд точек. Шовной контактной сваркой обычно соединяют детали толщиной 0,5–6 мм. Основной тип соединения – нахлесточное. При его выборе следует учитывать свариваемость материала, номинальные размеры ядра точек, шаг между ними и величину нахлестки. Технологический процесс изготовления конструкций способом шовной контактной сварки состоит из следующих операций: предварительная сборка, подготовка поверхности, окончательная сборка, прихватка, сварка точек, антикоррозионная защита, правка и механическая доработка. В зависимости от конкретных условий некоторые операции могут быть исключены.
При шовной сварке образование соединения происходит по схеме,
состоящей из трех этапов I–III (рис. 4.1).
Рис. 4.1. Этапы образования соединения при шовной сварке
Первый этап начинается с момента обжатия деталей, вызывающего пластическую деформацию микронеровностей в контактах электрод-деталь. Последующее включение тока и нагрев металла облегчают выравнивание микрорельефа, разрушение поверхностей пленок и формирование электрического контакта. Нагретый металл деформируется преимущественно в зазор между деталями, и образуется уплотняющий поясок.
Второй этап характеризуется расплавлением металла и образованием ядра. По мере прохождения тока ядро растет до максимальных размеров – по высоте и диаметру. При этом происходит перемешивание металла, удаление поверхностных пленок и образование металлических связей в жидкой фазе. Продолжается процесс пластической деформации и тепловое расширение металла. К концу этого этапа отмечается почти полная осадка рельефа.
Третий этап начинается с выключения тока, сопровождающегося охлаждением и кристаллизацией металла. Образуется общее для деталей литое ядро. При охлаждении уменьшается объем металла и возникают остаточные напряжения. Для снижения уровня этих напряжений и предотвращения усадочных трещин и раковин требуются значительные усилия.
При шовной сварке за счет теплопередачи от предыдущих точек процессы пластической деформации при сварке второй и последующих точек на всех трех этапах облегчается. Снижается также скорость кристаллизации ядра, что приводит к уменьшению остаточных напряжений.
Конструктивные элементы сварного соединения при шовной сварке показаны на рис. 4.2.
Рис. 4.2. Конструктивные элементы соединений при шовной сварке:
d – диаметр ядра; h (h1) – величина проплавления; g (g1) – глубина вмятины от электрода; tш – шаг между точками – расстояние между центрами точек; U – величина нахлёстки
Важнейшим условием получения качественного шовного сварного соединения является выбор оптимального режима сварки.
Рекомендуемые режимы, как правило, требуют корректировки в конкретных условиях.
Нарушение параметров технологического процесса приводит к образованию следующих групп дефектов:
· изменение размеров ядра или полное его отсутствие (непровары);
· выплески (выбросы) металла из зоны контактов деталей с деталями и деталей с электродами;
· нарушение сплошности металла ядра или околошовной зон (трещины, раковины, рыхлоты);
· переход металла электродов на поверхность сварных соединений;
· изменение структуры и свойств металла ядра и околошовной зоны.
Для своевременного обнаружения и принятия технических и организационных мер по предупреждению дефектов должен проводиться систематический контроль всех звеньев производства сварной конструкции, а именно: на стадии проектирования, а также при выполнении вспомогательных операций, собственно сварочных операций и сварочного оборудования.
Шовная сварка, выполняемая при непрерывном движении деталей и непрерывном протекании сварочного тока, называется непрерывной. Такую сварку редко применяют из-за сильного перегрева поверхности деталей, контактирующей с роликами. Наибольшее распространение имеет прерывистая шовная сварка, при которой детали перемещаются непрерывно, а ток включается и выключается на определенные промежутки времени и при каждом включении (импульсе) тока образуется единичная литая зона. Перекрытие литых зон, необходимое для герметичности шва, достигается при определенном соотношении скорости вращения роликов и частоты импульсов тока.
Применяют также шаговую сварку, при которой детали перемещаются прерывисто (на шаг), а сварочный ток включается только во время их остановки, что улучшает охлаждение металла в контактах ролик - деталь по сравнению с непрерывным движением свариваемых деталей. Шовная сварка в большинстве случаев производится с наружным водяным охлаждением, что также уменьшает перегрев внешних слоев металла.
Разнообразные виды шовной сварки, встречаемые на практике, в основном различаются способом подвода сварочного тока (односторонний или двусторонний) и расположением роликов относительно свариваемых деталей (рис. 5). Двусторонняя шовная сварка аналогична двусторонней точечной (рис. 5, а-е). Вместо одного из роликов может быть применена оправка, плотно контактирующая с внутренней деталью (рис. 5, г). Для сварки неподвижных деталей кольцевым швом на плоскости служит верхний ролик, который вращается вокруг своей оси, а также вокруг оси шва (рис. 5)
Рис. 5. Способы шовной сварки
Нижняя деталь контактирует с электродом, имеющим форму чашки. Иногда свариваемые детали устанавливают на медную шину; при этом подвод тока может быть двусторонним или односторонним. При сварке на шине возможны варианты подвижной (рис. 4, ж) и неподвижной (рис.4, з) шин, когда два ролика, к которым подведен ток, вращаются вокруг своих осей и катятся по деталям. При односторонней шовной сварке, как и при точечной, наблюдается шунтирование тока в деталь, контактирующую с роликами.
Рис.6. Циклограммы шовной сварки
а - непрерывное выключение тока; б - импульсное включение тока; I - сварочный ток; Р - давление; S - перемещение роликов; t - время.
Шовную сварку применяют при изготовлении различных емкостей с толщиной стенки 0,3 - 3 мм, где требуются герметичные швы - бензобаки, трубы, бочки, сильфоны и др. [2]
|
|
Типы сооружений для обработки осадков: Септиками называются сооружения, в которых одновременно происходят осветление сточной жидкости...
Опора деревянной одностоечной и способы укрепление угловых опор: Опоры ВЛ - конструкции, предназначенные для поддерживания проводов на необходимой высоте над землей, водой...
Папиллярные узоры пальцев рук - маркер спортивных способностей: дерматоглифические признаки формируются на 3-5 месяце беременности, не изменяются в течение жизни...
Поперечные профили набережных и береговой полосы: На городских территориях берегоукрепление проектируют с учетом технических и экономических требований, но особое значение придают эстетическим...
© cyberpedia.su 2017-2024 - Не является автором материалов. Исключительное право сохранено за автором текста.
Если вы не хотите, чтобы данный материал был у нас на сайте, перейдите по ссылке: Нарушение авторских прав. Мы поможем в написании вашей работы!